The Friedel-Crafts alkylation
The Friedel-Crafts alkylation of aromatic compounds involves an acid-catalyzed electrophilic substitution, wherein an alkyl group replaces an aromatic hydrogen. A diverse range of alkylating agents, such as olefins, alkyl halides, and alcohols, is commonly employed for this purpose.
This reaction can be applied to various aromatic substrates, including heteroaromatic compounds and even compounds like ferrocene. These reactions are typically rapid and exothermic, and they are often conducted under mild conditions in the liquid phase.
However, in some cases, vapor-phase processes with more stringent conditions are utilized for certain substrates. When olefins, alkyl halides, and alcohols are used as alkylating agents, the overall reactions proceed as follows:
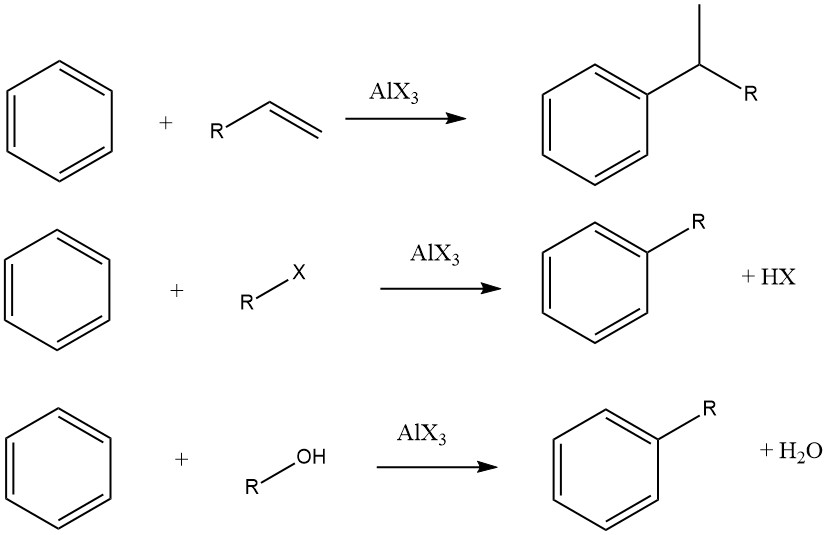
Table of Contents
The degree of isomerization of the alkyl moiety and adherence to the Markovnikov rule during the addition process vary depending on the acidity of the catalyst.
1.1. Catalysts for Friedel-Crafts alkylation
Catalysts used in the Friedel-Crafts alkylation process are acidic, and their effectiveness depends on various factors, including reaction conditions, alkylating agents, and aromatic substrates. Both Lewis acids and Brønsted acids can act as active catalysts, and frequently used catalysts are classified based on their chemical structures.
Group | Examples | Type of acid |
---|---|---|
Acidic halides | AlCl3, AlBr3, SnCl4, SbCl5, FeCl3 | Lewis acids |
Metal alkyls and alkoxides | AlR3, BR3, ZnR2, Al(OPh)3 | Lewis acids |
Proton acids | HCl, HCl – AlCl3, H2SO4, HF, H3PO4 | Brønsted acid |
Acidic oxides and derivatives | zeolites, mixed oxides and solid superacids, clays, heteropolyacids | Brønsted/Lewis acid |
Supported acids | H3PO4 – SiO2, BF3 – Al2O3 | Brønsted/Lewis acid |
Cation-exchange resins | Permutit Q, Amberlite IR 112, Dowex 50, Nafion – silica, Deloxan | Brønsted acid |
Traditionally, acidic halides like AlCl3 or AlBr3, and proton acids such as HCl, HF, or H2SO4, supported on diatomaceous earth, have been widely employed. However, a shift is occurring towards substituting these catalysts with zeolites and inorganic oxides due to their environmental friendliness, ease of handling, and lower cost implications in process design.
The presence of bases, especially organic nitrogen compounds, reduces the acidity and efficiency of the catalyst. Oxygen, even at concentrations as low as 20 ppm, can lead to the formation of heavy resinous materials on the catalyst. Dienes like butadiene in a butene feed also contribute to the production of resinous or tarry substances on the catalyst.
Interestingly, traces of moisture or other proton suppliers can enhance catalytic activity, particularly for Lewis acids. However, higher amounts of these compounds are detrimental to the catalyst’s performance.
In some cases, mild catalyst poisons, such as organic nitro compounds, are intentionally used to lower catalyst acidity and prevent side reactions like isomerization. These organic nitro compounds form stoichiometric complexes with Lewis acids, resulting in cleaner alkylation processes with moderate yields.
Additionally, certain adducts like BF3·OEt2 or BF3·C6H5OH act as mild Friedel-Crafts catalysts. Impurities in catalysts, like the presence of ferric chloride in aluminum chloride, can significantly decrease product yield and impact the course of the reaction catalyzed by Lewis acids.
1.2. Isomerization of the Alkylating Agents
Due to the acidic nature of the reaction conditions in Friedel-Crafts alkylation, alkylating reagents often undergo rearrangements and tend to be transformed into the most highly branched isomer possible. This is demonstrated in reactions of benzene with propyl chloride, where isopropylbenzene is the main product, and with n-butyl chloride, which leads to the formation of sec-butylbenzene.
In these cases, the isomerization of the alkylating agent is initiated by the migration of a hydrogen atom rather than direct carbon rearrangements. The driving force behind this isomerization is the formation of the most stable carbocation, following the usual trend: primary < secondary < tertiary.
For example, when benzene is alkylated with long-chain linear 1-olefins, the reaction leads not only to the formation of 2-alkylbenzene but also to a random distribution of the phenyl substituent along the alkyl chain in most cases.
This effect could also be attributed to the isomerization of the alkylated reaction products, as n-butylbenzene is transformed into sec-butylbenzene in the presence of a Friedel-Crafts catalyst like AlCl3.
Under certain reaction conditions, alkylating benzene with tertiary alkyl halides can result in the formation of secondary alkylbenzenes rather than tertiary alkylbenzenes.
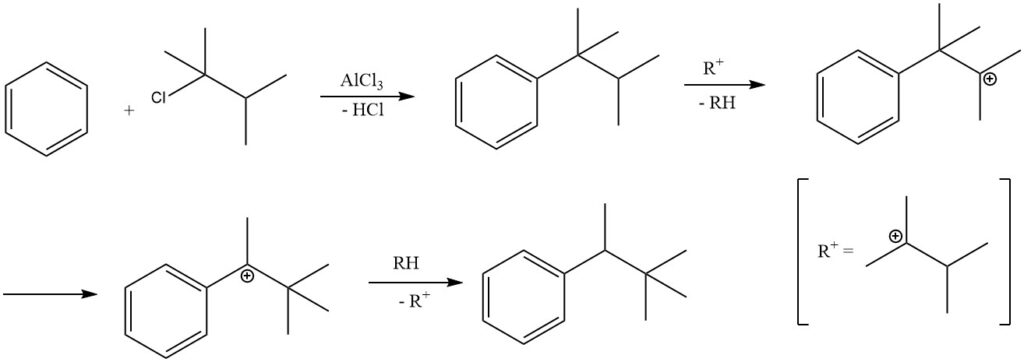
For instance, alkylating benzene with 2-chloro-2,3-dimethylbutane predominantly produces 2,2-dimethyl-3-phenylbutane due to the isomerization of the primary product tert-hexylbenzene. The isolation of the primary product, tert-hexylbenzene, is only possible when less active catalysts, such as ferric chloride, are employed.
1.3. Reactivity of Aromatic Substrates
The electrophilic substitution of aromatic compounds in Friedel-Crafts alkylation is influenced by the presence of substituents on the aromatic substrate. Electron-donating substituents like alkyl, NR2, or OR (where R is an alkyl group) increase reactivity, causing the new substituent to preferably enter the ortho or para position.
As a result, when benzene is alkylated with olefins, monosubstituted benzene is formed. However, this monosubstituted benzene reacts faster with another olefin molecule than benzene itself, leading to a complex mixture of mono- and polyalkylated benzenes.
The degree of polysubstitution is affected by reaction conditions and is reduced by steric hindrance from bulky alkyl groups. Bulky olefins like cyclohexene or linear C6 – C18 olefins allow good yields of monoalkylation in benzene.
Ethylene or propene can be monoalkylated through recycling of polyalkylated products and careful choice of reaction conditions, as seen in the industrial synthesis of ethylbenzene and cumene.
In the alkylation of monosubstituted benzenes, ortho and para isomers initially predominate. However, subsequent isomerization often results in an equilibrium mixture richer in the meta product.
Ortho substitution is favored only if sterically hindered. For instance, the reaction of benzene and 4-methylcyclohexene catalyzed by HF produces 75% monoalkyl derivative and 25% dialkyl derivative, with 75% being the para isomer and only 25% the meta isomer.
Similarly, cumene alkylation by 2-butene over BF3 – H3PO4 yields 91% para product, and dialkylation of benzene with propene over silica – alumina gives preferentially p-diisopropylbenzene, suitable for the synthesis of terephthalic acid and hydroquinone.
Substituting benzene with halides deactivates the reaction. Phenols or phenyl ethers react much faster than benzene in alkylation due to the significantly enhanced electron density in the ortho and para positions.
In microporous materials, reactivities, product selectivities, and isomer preferences largely depend on the type, number, and strength of acid sites and the geometry of zeolite pores. Alkylation using solid catalysts generally requires higher temperatures, with the exception being very strong solid acids, such as solid superacids.
1.4. Dealkylation and Transalkylation
Many of the catalysts used for alkylating aromatic compounds can also promote the reverse reaction of alkylation, especially at higher temperatures. For instance, when alkylbenzenes are heated with AlCl3, mixtures of benzene and polyalkylated benzenes are formed through reverse alkylation.
The tendency of alkylaromatic compounds to undergo disproportionation also depends on the structure of the alkyl substituent, following the order: tert-C4H9 > iso-C3H7 > n-C3H7 > C2H5 > CH3.
Disproportionation and transalkylation of methylbenzenes occur at 300 – 450 °C in the presence of solid acid catalysts like SiO2 – Al2O3, while disproportionation and transalkylation of ethylbenzenes and isopropylbenzenes take place below 100 °C with typical Friedel-Crafts catalysts.
The intermolecular alkyl group transfer (transalkylation) is utilized in various industrial processes. For instance, in the synthesis of ethylbenzene, the unwanted dialkylation product reacts with an excess of fresh benzene to achieve a high conversion of ethylene to ethylbenzene.
In the presence of an excess of BF3–HF, the disproportionation of monoalkylbenzenes predominantly yields the meta isomer. This is due to the high stability of the complex [m-Et2C6H5]+[BF4]−. A similar type of complex is used commercially to selectively extract m-xylene from mixtures of C8 aromatic compounds.
The equilibrium between alkylation and dealkylation reactions explains the product distribution in the alkylation of substituted aromatic compounds. Initially, ortho and para isomers are formed and can be isolated with short reaction times (kinetic control). However, with prolonged reaction times, these isomers isomerize to the more stable meta isomers (thermodynamic control).
Commercially, dealkylation processes are used to convert toluene to benzene, isomerize m-xylene to the desired ortho and para derivatives, and disproportionate toluene to benzene and xylenes. These processes take advantage of the alkylaromatic compound’s equilibrium behavior.
2. Alkylation of Benzene
The alkylation of benzene finds three major commercial applications:
- Alkylation with ethylene to produce ethylbenzene, which serves as an intermediate for styrene production. The global production capacity for ethylbenzene was approximately 20 million metric tons per year in 1991.
- Alkylation with propene to produce cumene, which is an intermediate for phenol production, with acetone as a byproduct. The global production capacity for cumene was around 7.5 million metric tons per year in 1992.
- Alkylation with long-chain olefins containing 10 – 18 carbon atoms to produce alkylbenzenes, which are then sulfonated to produce surface-active compounds. The production capacity for linear alkylbenzenesulfonates (LAB) in 1992 was approximately 180,000 metric tons per year.
2.1. Alkylation of Benzene with Ethylene
The alkylation of benzene with ethylene results in the formation of ethylbenzene, a reaction that is fast and exothermic.

During this process, significant amounts of polyethylbenzenes are produced as side products. The alkylation can be carried out in both the liquid phase and the vapor phase.
In liquid-phase processes, AlCl3 is the most commonly used catalyst, but other catalysts like BF3, FeCl3, ZrCl4, SnCl4, H3PO4, and alkaline-earth phosphates are also used. The reaction is typically conducted at atmospheric pressure and temperatures ranging from 85 to 95 °C.
Vapor-phase alkylation of benzene is widely practiced, especially in the United States. It is usually carried out at approximately 300 °C and 40 – 65 bar using acidic heterogeneous catalysts like Al2O3-SiO2 or H3PO4-SiO2.
To improve selectivity to monoalkylation, a low ethylene-benzene ratio (0.2 : 1.0) is used. The Alkar process, developed by Universal Oil Products, is commercially employed in several plants and uses boron trifluoride supported on modified anhydrous alumina as the noncorrosive catalyst.
The Alkar process allows a wide range of ethylene concentration (5 – 95 %) in the feed gas, enabling the use of off-gas from catalytic cracking or demethanizer overhead, or high-purity ethylene. The process conditions typically involve temperatures of around 300 °C and pressures of about 60 bar, leading to complete conversion of ethylene.
Isomer distribution obtained using the Alkar catalyst for benzene alkylation with ethylene is as follows:
Diethylbenzenes:
1,2- (26%);
1,3- (49%); and
1,4- (25%).
Triethylbenzenes:
1,2,3- (3%);
1,2,4- (35%); and
1,3,5- (62%).
Zeolite catalysts have gained significant interest for benzene ethylation. Mobil Oil and Badger introduced a fixed-bed vapor phase process using proprietary ZSM-5 zeolites, conducted at 420 – 430 °C and 15 – 20 bar.
Pure or diluted ethylene can be used as the feedstock after purification. Polyalkylbenzenes can be recycled for transalkylation, resulting in a high final yield of ethylbenzene (98 – 99 mol %). Zeolite-based catalysts have advantages over liquid Brønsted or Lewis acid catalysts, being noncorrosive and environmentally benign, simplifying construction, handling, and disposal.
Another zeolite-based process called the EBMax Process, using Mobil’s proprietary MCM-22 zeolite catalyst, operates in the liquid phase. Additionally, a zeolite-based catalyst developed by Unocal is employed in a fixed-bed, liquid-phase alkylation technology licensed by Lummus/Unocal/UOP.
2.2. Alkylation of Benzene with Propene
The alkylation of benzene with propene leads to the production of cumene, which is an exothermic reaction. Cumene is an essential compound used primarily in the synthesis of phenol with acetone as a co-product. A small portion of cumene is also utilized in the production of α-methylstyrene.
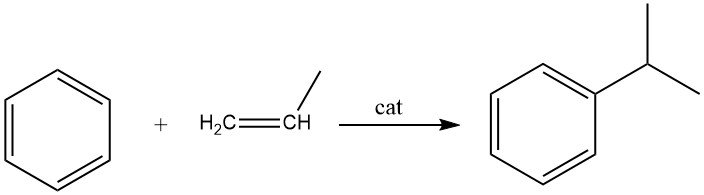
Both liquid-phase and vapor-phase processes are employed commercially for the synthesis of cumene. The widely used liquid-phase process by Universal Oil Products utilizes a solid phosphoric acid catalyst (SPA) supported on diatomaceous earth.
The reaction is conducted at 15 – 35 bar and temperatures of 200 – 250 °C. To prevent polyalkylation and achieve a high propene conversion (approximately 94%), a molar ratio of benzene to propene of 5:1 is required. The conversion decreases to 70% when a 4:1 benzene-propene feed ratio is used.
Increasing pressure and temperature enhance the conversion rather than cumene yields. In addition to the SPA catalyst, sulfuric acid and AlCl3 are also used for cumene production.
Novel cumene production technologies based on zeolite catalysts were developed by various companies such as Mobil/Raytheon, UOP, CDTech, Dow/Kellogg, and Enichem. These processes typically involve two reactors and a distillation unit.
The first reactor performs alkylation, while the second reactor transalkylates heavy ends (tri- and polyisopropylbenzenes) with fresh benzene.
Mobil’s MCM-22 zeolite, UOP’s proprietary zeolite in the QMax process, highly dealuminated mordenite zeolite by Dow, and Enichem’s BEA-zeolite catalyst are examples of zeolites used in these processes.
Furthermore, cumene can be further alkylated with propene using a pretreated aluminum silicate catalyst in the liquid phase under pressure at 150 – 250 °C. This leads to the production of mainly p-diisopropylbenzene and m-diisopropylbenzene, with only traces of the ortho isomer.
The isomers can be separated by distillation, and the mixture of m-diisopropylbenzene and o-diisopropylbenzene can be isomerized to further produce p-diisopropylbenzene by transalkylation with benzene. The diisopropylbenzenes are also important intermediates in the production of hydroquinone or resorcinol.
2.3. Alkylation of Benzene with Higher Olefins
Monoalkylbenzenes with 10 – 14 carbon atoms in the alkyl chain, such as dodecylbenzene, play an important role as intermediates in the production of alkylbenzenesulfonates, widely used in anionic commercial detergent products (surfactants).
Until around 1965, the primary olefin used for this reaction was propene tetramer. However, due to environmental concerns related to the biodegradability of detergents based on propene tetramer, the industry shifted towards linear alkylbenzenesulfonates.
Linear olefins with 10 – 14 carbon atoms are now used as feedstock for alkylbenzenesulfonate production. The reaction is typically catalyzed by liquid HF, H2SO4, or AlCl3, and suitable reaction conditions are as follows:
1. HF: 0 – 10 °C, benzene to alkene molar ratio of 4 – 10, and 2 – 3 kg of alkene per kilogram of HF.
2. H2SO4: 10 – 30 °C, benzene to alkene molar ratio of 4 – 5, and 2 volumes of alkene per volume of 96 – 98% H2SO4.
3. AlCl3: 55 – 60 °C, benzene to olefin molar ratio of 3 – 4, and 25 moles of alkene per mole of AlCl3.
The HF process is considered the most economical in terms of catalyst consumption. It is carried out in the liquid phase at atmospheric pressure and 10 °C. Effective stirring and cooling are necessary to control the exothermic reaction and determine the reaction times.
The product is separated from the acid in a settler, washed, and then distilled at atmospheric pressure to recover benzene and at reduced pressure to isolate the alkylbenzenes.
Recently, some solid alkylation catalysts have been described in the literature, but due to decreased demand for linear alkylbenzenes (LAB) in industrialized regions, only UOP’s Detal process has commercialized a new technology using a noncorrosive catalyst to replace HF. This process utilizes a fluorided silica – alumina catalyst and operates in the liquid phase at around 130 °C, achieving high linearity and conversion.
The detergent properties of alkylbenzenesulfonates are influenced by the degree of branching in the alkyl side chain, with three to five methyl groups in dodecylbenzene being optimal. The position of the phenyl group on the alkyl chain also affects detergent properties.
Friedel – Crafts alkylation leads to an equilibrium product mixture with a random distribution of the phenyl over the alkyl chain. The product composition is influenced by the nature of the catalyst, with different catalysts favoring different isomers of monoalkylbenzenes.
Lewis acids like AlCl3 are capable of isomerizing the phenylalkanes formed, while proton acids isomerize only the olefins before the final alkylation of benzene.
2.4. Alkylation of Benzene with Alkyl Chlorides
Commercially, the alkylation of benzene with alkyl chlorides is another method used for producing detergent alkylates. The alkyl chloride, obtained from the chlorination of paraffins, contains around 70% paraffin. This mixture is reacted with a large excess of benzene in an enameled alkylating tower, using AlCl3 as the catalyst, at 80 °C.
During the reaction, hydrogen chloride is formed in stoichiometric amounts, which ensures thorough mixing of the reactants and is separated at the top of the reactor.
The products are then separated from the catalyst in a settler, neutralized, washed, and distilled to recover benzene and paraffin, which are recycled. The alkylates are further purified by distillation under reduced pressure.
One challenge with this process is the formation of considerable amounts of indane and tetralin derivatives as byproducts due to the presence of dichloroalkane impurities in the alkyl chloride.
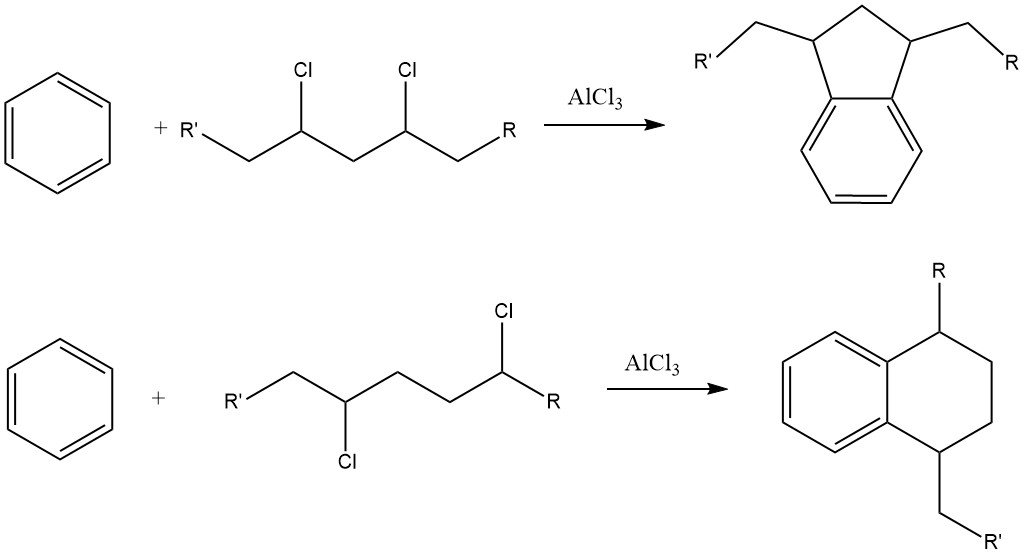
Alkylbenzenes with more than 15 carbon atoms in the side chain lead to alkylbenzenesulfonates that are nearly insoluble in water but highly soluble in organic media, such as mineral oils.
These solutions in mineral oil find use in the metal-working industry as drilling and cutting fluids or in the textile industry as spinning or batch fluids. Additionally, alkylbenzenesulfonates of this type are increasingly used as flooding agents in enhanced petroleum recovery processes.
2.5. Miscellaneous Alkylations of Benzene
Benzene can undergo alkylation with a wide range of compounds, including various linear, branched, cyclic, aryl-, or otherwise substituted olefins, alkyl halides, alcohols, ethers, alkynes, and dienes.
Some of these reactions have been successfully commercialized, such as the synthesis of tert-butylbenzene from benzene and isobutene. Tert-butylbenzene finds application in the production of perfumes.
3. Cycloalkylation
One example of intermolecular cycloalkylations involves the reaction of dichloromethane and benzene, leading to the formation of 9,10-dihydroanthracene along with some diphenylmethane. In this reaction, anthracene derivatives are also produced.

Intramolecular cycloalkylation is possible for alkylated aromatic compounds that carry a double bond or a functional group, such as a halogen or hydroxy group, in their side chain. For instance, 3-phenyl-1-propene undergoes isomerization in the presence of AlCl3 to form indane.

BASF developed a synthesis for anthraquinone based on cycloalkylation. This involves the dimerization of styrene in the liquid phase to 1-methyl-3-phenylindane, using phosphoric acid as a catalyst. The resulting compound is then subjected to catalytic vapor-phase oxidation to produce anthraquinone.
3.1. Arylation of Aromatic Compounds
Arylation of aromatic compounds can be achieved using various methods, including reaction with aryl halides, reaction with diazonium halides, and dehydrogenating condensation.
Aryl halides, such as fluorobenzene, chlorobenzene, and bromobenzene, can be used as arylating agents in Friedel-Crafts arylations. However, their reactivity is relatively low, with fluorobenzene being the most reactive followed by chlorobenzene and bromobenzene.
Arylation with fluorobenzene can yield biphenyls as products, while the decomposition of aryldiazonium tetrafluoroborates in aromatic solvents can lead to ring-arylated products along with fluorobenzene.
The Scholl Reaction is a dehydrogenating condensation of an aromatic compound in the presence of Friedel-Crafts catalysts. For example, naphthalene can be converted to perylene, and pyridine can be converted to 2,2′-dipyridyl through this reaction. High molecular weight polycondensated aromatic compounds can also be formed using the Scholl Reaction.
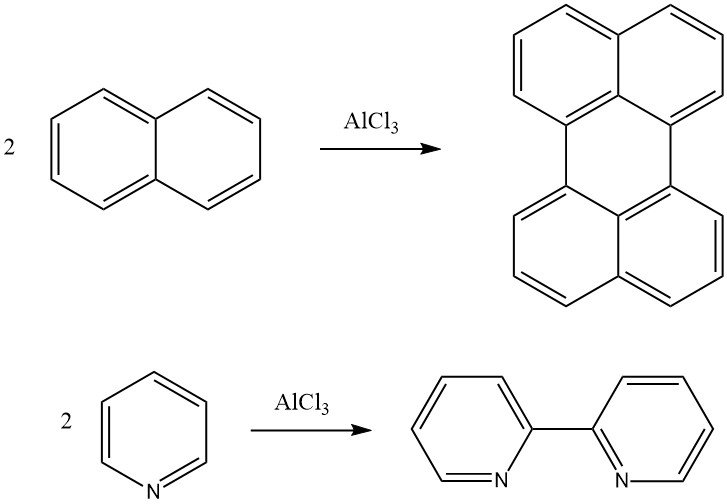
4. Alkylation of Substituted Benzenes
The alkylation of benzene typically leads to a mixture of monoalkylated, dialkylated, and polysubstituted compounds. The reactivity and orientation in the second substitution step depend on the electronic and steric properties of the first substituent and the size of the alkylating agent.
Dialkylated benzenes have significant commercial importance. For instance, diethylbenzenes are used to enhance the octane ratings of motor fuels and are obtained as byproducts in the production of ethylbenzene.
Dialkylbenzenes can be dehydrogenated to produce divinylbenzenes, which are crucial for crosslinking polyolefins like polystyrene in the manufacturing of ion-exchange resins.
Ethylmethylbenzene, formed by ethylating toluene, is industrially valuable as a starting material for styrenes that have methyl substitutions in the aromatic ring. Another example is the production of diisopropylbenzene through the reaction of propene with cumene (alkylation of benzene with propene).
4.1. The Alkylation of Toluene with Propene
The industrial process of alkylating toluene with propene to produce cymene is carried out by companies like Sumitomo Chemicals. The resulting cymene mixture mainly consists of meta and para isomers, which is then subjected to oxidation to yield acetone and cresols.

These cresols comprise approximately 39.5% meta and para-cresols and 36% meta-cresol and serve as essential raw materials for phenolic resins and plasticizers.
Another significant aspect involves the production of polymethylated benzenes by processes like disproportionation of toluene or methylation of benzene or toluene. These polymethylated benzenes can undergo oxidation to form the corresponding acids, which find applications in various polymers such as polyesters, polyamides, and polyimides.
4.2. Alkylation of Higher Aromatic Compounds
Alkylating higher aromatic compounds, such as biphenyl, indane, tetralin, and polynuclear aromatic compounds like naphthalene, acenaphthene, anthracene, fluorene, and phenanthrene, has been documented.
For instance, the alkylation of naphthalene with higher olefins is employed commercially to produce fluorescent agents used in lubricating oils. This liquid-phase reaction utilizes AlCl3 as a catalyst at temperatures up to 180 °C.
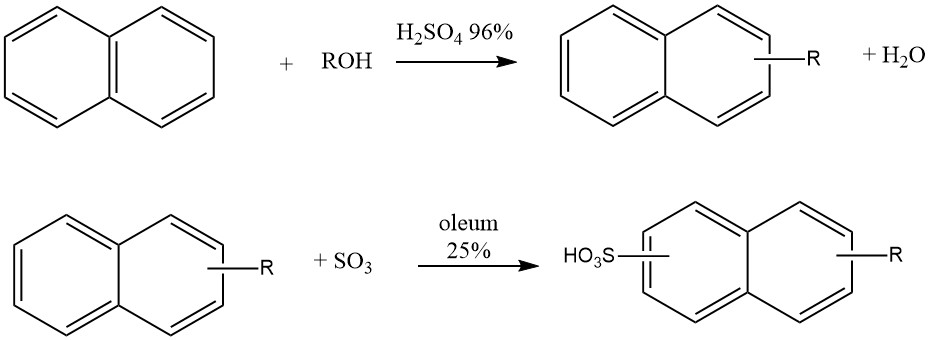
Another industrial application of naphthalene alkylation is the production of ‘Nekal’ type detergents (BASF), which are alkylnaphthalenesulfonates. These compounds were among the earliest synthetic detergents and continue to be used as surfactants in the textile industry.
The synthesis of these alkylnaphthalenesulfonates involves a one-pot process where naphthalene reacts with butanol, hexanol, or mixtures of propanol-butanol in the presence of 96% sulfuric acid at 50 °C. After alkylation, 25% oleum is added for sulfonation.
Additionally, the Hock process involves the oxidation of 2-isopropylnaphthalene, resulting in 2-naphthol. To obtain 2-isopropylnaphthalene, a reaction between naphthalene and propene using ZnCl2 or aluminum silicates as catalysts at 150 – 200 °C can be performed, yielding small amounts of the 1-isopropyl isomer as well.
Furthermore, 2,6-dialkylnaphthalenes have garnered significant interest due to their conversion to 2,6-naphthalenedicarboxylic acid, used in the production of high-performance plastic poly(ethylene-2,6-naphthalene dicarboxylate) (polyethylenenaphthenate, PEN).
Various shape-selective catalysts, including mordenite, have been studied for alkylating naphthalenes. Alternatively, Amoco commercialized another route in 1995 with a capacity of about 40,000 t/a. They alkylate o-xylene with butadiene over a strongly basic catalyst, yielding o-tolylpentene, which then undergoes cyclization, dehydrogenation, and isomerization.
5. Alkylation of Phenols
The alkylation of phenols is a highly significant industrial reaction, resulting in the production of alkylphenols extensively used in various applications, such as antioxidants, herbicides, insecticides, and polymers.
Due to the increased electron density in the aromatic ring associated with the nucleophilic hydroxyl group, alkylation occurs under milder conditions compared to aromatic hydrocarbons.
Various factors, including reaction conditions, catalysts, and alkylating agents, influence the formation of predominantly ortho- or para-monoalkylated, 2,4- or 2,6-dialkylated, and 2,4,6-trialkylated phenols.
Higher temperatures lead to thermodynamically more stable meta isomers due to secondary reactions. Additionally, low temperatures and catalyst concentrations can yield significant amounts of alkyl aryl ethers, while higher temperatures, catalyst concentrations, and acid strength favor the predominant formation of alkylphenols.
Alkylating agents like olefins, alcohols, and alkyl halides are employed in the alkylation process. Three main types of industrial processes for phenol alkylation have been developed:
1. Liquid-phase alkylation involves adding the alkylating agent to a solution or suspension of the catalyst in the phenol. After the reaction, the catalyst is separated, and any residual catalyst is decomposed through neutralization.
2. Fixed-bed liquid-phase processes operate with the reactants passing over the catalyst in tubular reactors at elevated pressures, which are externally cooled.
3. Vapor-phase alkylation entails sending phenol and the alkylating agent, such as methanol or an olefin, to a fixed-bed reactor operating at 300 – 400 °C, with efficient removal of the heat of reaction.
Product recovery involves distillation, with unconverted phenols and alkylating agents recycled, and various mono-, di-, and trialkylated phenols separated. Complete removal of acidic catalyst traces is crucial to prevent side reactions during distillation, such as isomerization, transalkylation, and disproportionation.
Liquid-phase processes utilize Lewis acid catalysts like AlCl3, BF3, or Al(C6H5O)3, proton acids like HF, H2SO4, H3PO4, or p-tolylsulfonic acid, or acidic ion-exchange resins, such as Nafion resins or sulfonated polystyrenes.
Vapor-phase processes require catalysts with high thermal stability, such as montmorillonites, zeolites like faujasite, and metal oxides like γ-Al2O3, MgO, CaO, and Fe2O3 – CrO3.
Regioselectivity can be controlled using different catalysts. For instance, HF, BF3, Al2O3•SiO2, or acidic ion-exchange resins promote predominantly p-substituted products when alkylating phenols with olefins.
On the other hand, Al(C6H5O)3, formed from phenol and metallic aluminum, especially in the presence of trace mercury salts, leads almost exclusively to 2-alkylated and 2,6-dialkylated products. This selectivity for ortho alkylation is attributed to a six-membered transition state involving aluminum phenolate and an olefin.
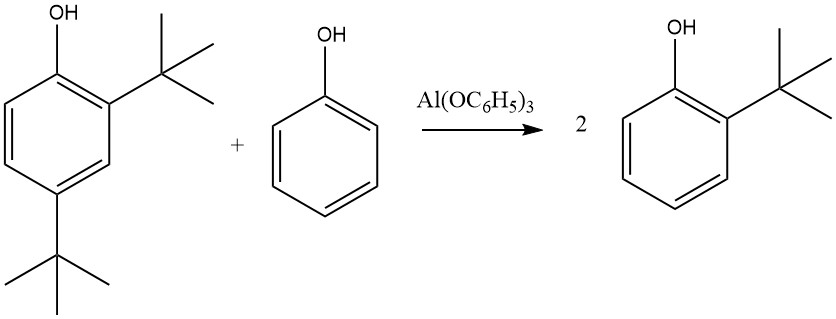
Other metal salts of phenol, including those of zinc, magnesium, and calcium, can also activate this reaction, which is not limited to phenol; 2-naphthol, 2-cresol, or 4-cresol can also be alkylated by ethylene, propene, the butenes, cyclohexene, or other olefins, with varying reactivity, where isobutene shows the highest reactivity and ethylene the lowest.
In the presence of γ-Al2O3 as a catalyst, high selectivity for monoalkylated o-phenols can be achieved. This process operates at elevated temperatures of 200 – 350 °C in the liquid phase at pressures of 20 – 200 bar and is suitable for continuous fixed-bed operation.
Regarding the alkylphenol products, alkylphenols often are produced in batch operations, offering higher flexibility. However, for compounds produced in large quantities, such as cresols, 2,6-xylenol, 2-sec-butylphenol, 4-tert-butylphenol, octylphenol, nonylphenol, dodecylphenol, thymol, or 2,6-di-tert-butyl-4-methylphenol, continuous processes with capacities of up to 25,000 t/a each have been introduced.
5.1. Alkylation of Phenol with Methanol
Alkylation of phenol with methanol under elevated temperatures and with a catalyst yields primarily 2-cresol (60 – 70% at 50% phenol conversion and 300 °C) and 2,6-xylenol, accompanied by minor amounts of 4-cresols, 2,4-, and 2,3-xylenols, and a small quantity of 3-cresol.
The reaction can be conducted in either the liquid or vapor phase. In vapor-phase processes, the reactants are introduced at atmospheric or slightly elevated pressure into a tubular reactor with a fixed-bed catalyst at temperatures ranging from 300 to 450 °C.
Using activated Al2O3 at 300 °C, and MgO and CeO2 at 540 and 450 °C, respectively, results in high selectivity for 2-cresol and 2,6-xylenol. However, using highly acidic catalysts like aluminum oxide, aluminum silicates, zeolites, and aluminum phosphate, especially at higher temperatures, leads to transalkylation-isomerization, resulting in increased production of 3-cresol and 4-cresol.
Liquid-phase processes utilize catalysts such as Al2O3, Al(OMe)3, Al(OC6H5)3, or ZnCl2 – HCl at elevated pressures. In all cases, the xylenol:cresol ratio increases with the methanol:phenol ratio, temperature, and pressure.
5.2. Alkylation of Phenols with Olefins
Alkylation of phenol with methanol is carried out at elevated temperatures, typically between 320 and 340 °C, in the presence of 1 – 2 % Al(C6H5O)3 and at 200 bar, resulting in the formation of 2-ethylphenol.
On the other hand, the alkylation of phenol with propene to produce 2-isopropylphenol can be achieved at lower temperatures of 280 – 300 °C using γ-Al2O3 as the catalyst.
Additionally, propylation of cresols to yield thymol or carvacol is carried out in continuous liquid-phase processes utilizing γ-Al2O3, aluminum silicates, or zeolites. Under similar conditions, 2-sec-butylphenol can be produced from phenol and n-butenes.
The production of 2-tert-butylphenol and 2,6-di-tert-butylphenol can be achieved at 100 °C under pressures up to 20 bar in the presence of Al(C6H5O)3, exploiting the high reactivity of isobutene.
Alternatively, 4-tert-butylphenol can be prepared at atmospheric pressure and temperatures ranging from 80 to 140 °C using H2SO4, H3PO4, BF3, or preferably acidic cation-exchange resins.
The important antioxidant 2,6-di-tert-butyl-4-methylphenol is produced from 4-cresol and isobutene at 70 °C using H2SO4 as the catalyst. Similarly, alkylation of phenol with 2-methylbutenes at 100 – 120 °C in the presence of BF3 or H3PO4 results in 4-tert-amylphenol, and with an excess of 2-methylbutenes, 2,4-di-tert-amylphenol is formed.
A important commercial process involves alkylation of phenol with linear or branched olefins containing 6 – 20 carbon atoms, leading to alkylphenols, which, after ethoxylating and sulfating, find wide application as anionic detergents.
Diisobutene, tripropene, and tetrapropene are preferred alkylating agents, and the reaction is catalyzed under mild conditions (50 – 85 °C) using BF3 in continuous-batch or tubular reactors. Acidic cation-exchange resins, such as macroreticular sulfonated polystyrene, are also excellent catalysts that facilitate the catalyst separation.
To achieve better temperature control, the reaction may be carried out in two stages, employing a catalyst of reduced acidity in the first stage. Chemische Werke H€uls (now Degussa-H€uls) in Germany utilizes a process of this kind to produce nonylphenol.
In the first stage of this fixed-bed process, the temperature increases from 80 to 120 °C, and in the second stage, it rises from 110 to 130 °C. Activated aluminum silicates can also serve as catalysts, but they require higher reaction temperatures and longer reaction times.
The industrial production of alkylphenols, haloalkylphenols, and related compounds is extensive, and these compounds are widely used as oxidation inhibitors, detergents, bactericides, fungicides, insecticides, and disinfectants.
6. Alkylation of Aromatic Amines
Due to the basicity of aromatic amines, acidic catalysts are not well-suited for their alkylation. For instance, the use of the Friedel – Crafts catalyst AlCl3 in the reaction of ethylene with aniline predominantly yields unidentified resinous products with only small quantities of 2-ethylaniline.
However, aluminum anilide, Al(C6H5NH)3, formed in situ through the heating of aluminum powder in aniline with hydrogen evolution, proves to be an effective catalyst for this reaction. Under conditions of 300 – 340 °C and 200 bar, 2,6-diethylaniline is obtained after 2 – 3 hours, while shorter reaction times lead to the formation of 2-ethylaniline.
The catalytic activity of aluminum anilide is further enhanced by the addition of Friedel – Crafts catalysts like AlCl3, SnCl4, TiCl4, SiCl4, BF3, or ZnCl2. Alkali metal and AlCl3 mixtures in aniline also display activity, leading selectively to N-alkylation.
This reaction has been extended to various substituted anilines, including 2-, 3-, and 4-toluidine, 2,6-, 2,4-, and 2,5-xylidine, 2-propylaniline, 2- and 3-chloroaniline, and α-naphthylamine. Additionally, diamines such as m-phenylenediamine or 2,4-toluylenediamine, as well as secondary amines like diphenylamine, can also undergo alkylation.
In the alkylation process with olefins, the reactivity decreases in the order of ethylene > propene > 1-butene > isobutene, which is opposite to the reactivity order observed in phenol alkylation with Al(OC6H5)3 catalyst.
Notably, isobutene demonstrates activity with Friedel – Crafts catalysts such as AlCl3, BF3, or montmorillonite even at 200 – 250 °C, but with aluminum anilide, the reaction proceeds slowly. When montmorillonite is used, selective formation of 4-tert-butylaniline occurs, while BF3 or AlCl3 catalysts yield mixtures of the 2 and 4 isomers.
In the alkylation of anilines with methanol, molecular sieves act as catalysts, resulting in a complex mixture containing 2-toluidine, 2,6- and 2,4-xylidine, and 2,4,6-trimethylaniline. Industrially, 2,6-dialkylanilines, such as 2-ethyl-6-methylaniline, are produced as intermediates for herbicides and dyes.
7. Alkylation of Heteroaromatic Compounds and Related Substrates
Various heterocyclic aromatic compounds, including furans, thiophenes, and N-heterocycles, can be subjected to alkylation reactions, although limited information is available about their commercial applications.
Cyclopentadienyl derivatives also undergo Friedel – Crafts alkylation in a manner similar to other aromatic compounds.
7.1. Furan
Furan exhibits higher reactivity in Friedel – Crafts alkylations compared to benzene. However, furans tend to undergo rapid resinification in the presence of acids, which can complicate product separation.
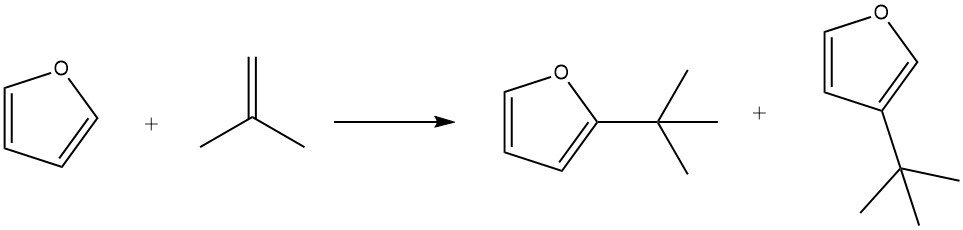
By using phosphoric acid on kieselguhr as a catalyst, furan can be efficiently alkylated with isobutene at 100 °C within 3 hours, resulting in an 85% yield of the alkylates, along with minor amounts of isooctene.
Under mild conditions (e.g., 50 °C for 1 hour), substitution in the 2 position is favored. However, longer reaction times (7 hours), higher temperatures (150 °C), and greater catalyst concentrations promote the formation of products substituted in the 3 position. Additionally, the formation of 2,5-di-tert-butylfuran has also been observed during the process.
7.2. Thiophene
Thiophene exhibits significantly higher reactivity in Friedel – Crafts reactions compared to aromatic hydrocarbons, enabling its alkylation with various olefins, including propene, 1-butene, 2-methylbutenes, cyclohexene, and alcohols like isopropyl alcohol and tert-butyl alcohol.
Successful results have been obtained using acidic catalysts such as phosphoric acid at 60 °C or alumina silica at 200 °C. However, the use of H2SO4, HF, BF3•OMe2, and AlCl3 resulted in side reactions. In all cases, the thiophene was substituted in the 2 position, and higher-boiling products, such as dialkylated compounds, were also produced.
Additionally, the removal of thiophene from cracked gasoline during refining with cold concentrated sulfuric acid is likely an alkylation reaction. The olefins present in the gasoline act as alkylating agents, leading to the formation of high-boiling alkylthiophenes, which remain as residue upon distillation.
7.3. N-Heterocycles
N-Heterocycles can undergo alkylation in the presence of aluminum amides as catalysts. While heterocyclic compounds like carbazole and indole react sluggishly with aluminum metal to form the amide, aluminum anilide serves as an effective catalyst.
For instance, when carbazole reacts with ethylene in the presence of aniline and aluminum powder, it produces 1-ethylcarbazole. This reaction occurs in an autoclave at 280 °C and 200 bar.
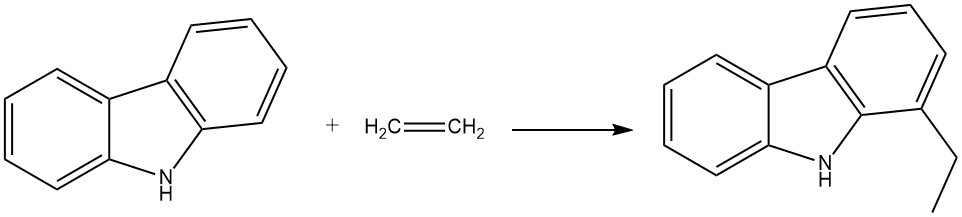
Propene can also react under similar conditions to yield 1-isopropylcarbazole, although with a slightly lower yield.
The combination of carbazole and propene with AlCl3 as the catalyst at 90 – 100 °C results in the formation of diisopropylcarbazole. Another reaction over an aluminum silicate catalyst at 180 – 200 °C gives tetra- and pentaisopropylcarbazole. Moreover, the ethylation of pyrrole can be achieved using an aluminum silicate catalyst at 200 – 370 °C.
7.4. Nonbenzenoid Aromatic Compounds
Nonbenzenoid aromatic compounds, such as ferrocenes, fulvenes, azulenes, pseudoazulenes, indolizines, and cyclazines, share chemical similarities not only with benzenoid systems but also with olefins.
Their electrophilic substitution reactions typically occur under milder conditions compared to benzene derivatives. However, due to their relatively low stability, careful selection of catalysts and reaction conditions is essential.
Ferrocene can undergo alkylation in the presence of Lewis acids, such as AlCl3, with various substrates including methanol, ethyl, isopropyl, butyl, and benzyl halides, 1,2-dichloroethane, ethylene, propene, and isobutene.
The reaction often leads to complex mixtures of homoannular and heteroannular products (where both rings are alkylated), as the system becomes more reactive after the first alkylation step.
Alkylation of ferrocene with olefins appears to be more favorable, such as the reaction with isobutene, which occurs even at room temperature. At higher temperatures (100 – 150 °C), heteroannular tri-tert-butylferrocene is obtained in a 44% yield, along with some tetra-tert-butylferrocene. Steric hindrance prevents the attachment of more than two tert-butyl substituents to the same cyclopentadienyl ring.
8. Miscellaneous Alkylation Reactions
The alkylation of aromatic compounds using bi- or polyfunctional reagents results in the formation of a diverse range of valuable mono-, di-, or polynuclear products with significant commercial applications.
8.1. Haloalkylations
Under suitable reaction conditions, haloalkylations of aromatic compounds with bi- or polyfunctional alkylating agents can produce primary haloalkylation products while avoiding undesired cycloalkylation or linkage of multiple nuclei.
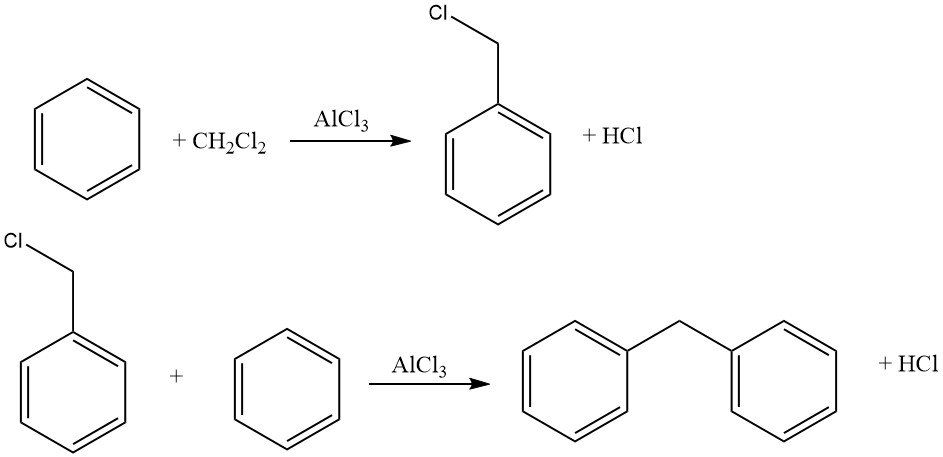
Common haloalkylating agents include aldehyde–hydrogen halide, haloalkyl ethers, haloalcohols, and similar compounds. This process allows for halomethylation, haloethylation, higher haloalkylation, as well as bis- and polyalkylation.
The reaction is often catalyzed by zinc chloride, but other catalysts such as acidic halides (e.g., ZnCl2 – AlCl3, SnCl4, AlCl3–ketones, AlCl3 – pyridine) or proton acids (HCl, H2SO4, H3PO4, p-toluenesulfonic acid) can also be used.
One common example of this reaction is the chloromethylation using formaldehyde–HCl (Blanc reaction). While this reaction is synthetically valuable, caution must be exercised due to the formation of reactive intermediates, particularly chloromethyl ethers, which are highly carcinogenic.

8.2. Hydroxyalkylation
Hydroxyalkylation of aromatic compounds using aldehydes and ketones in the presence of acids is of significant industrial importance. The electrophiles attacking the aromatic nucleus are formed by the reaction of aldehydes or ketones with Lewis or proton acids (where R, R0 = H, alkyl, aryl).
The reaction results in the formation of a substituted benzyl alcohol. Under acidic conditions, this alcohol reacts with another molecule of the aromatic compound to produce a substituted diarylmethane.
One notable example of this reaction is the hydroxyalkylation of phenol with acetone, yielding 2,2-bis-(4-hydroxyphenyl)propane, commonly known as bisphenol A. This compound is industrially produced in continuous processes using H2SO4 (or dry HCl in the Hooker process) as a catalyst and methyl mercaptan as a promoter, resulting in almost quantitative yields at 50 °C.

Cation-exchange resins are also increasingly used as catalysts due to their simplified separation process. Bisphenol A is primarily used for the production of epoxy- and polycarbonate resins.
Hydroxyalkylations are highly versatile, allowing numerous alkyl- and aryl-substituted aldehydes and ketones to react with various aromatic compounds. For instance, the insecticide DDT is produced from chloral and chlorobenzene. The reaction of phenol with formaldehyde leads to hydroxymethylphenols, which can further condense to form phenol resins at elevated temperatures.
When oxiranes (epoxides) are used as alkylating agents, β-hydroxyalkyl aromatic compounds are obtained. For example, the reaction of benzene with ethylene oxide in the presence of a stoichiometric amount of AlCl3 leads to an aluminum alkoxide, which, upon hydrolysis, yields β-phenylethanol.
8.3. Amidomethylation
Amidomethylation, also known as the Tscherniac-Einhorn reaction, is a process where N-hydroxymethylamides or the corresponding imides react with aromatic compounds under mild conditions in the presence of sulfuric acid. This reaction allows for the introduction of an amidomethyl group to the aromatic nucleus.
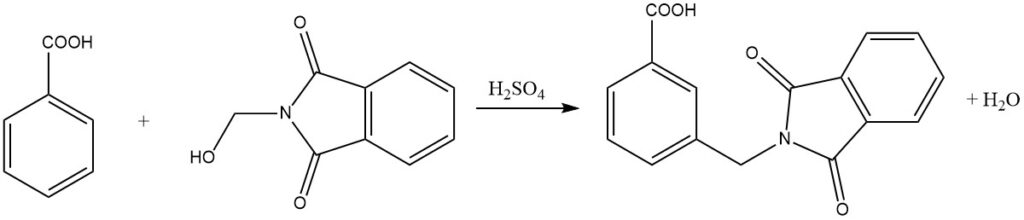
Additionally, less reactive aromatic compounds, such as benzoic acids, can also undergo amidoalkylation through this process. Remarkably, even nitro-substituted aromatic compounds can be alkylated using N-chloromethylcarboxylic acid amides in the presence of AlCl3 as a catalyst.
Reference
- Acylation and Alkylation; Ullmann’s Encyclopedia of Industrial Chemistry. – https://onlinelibrary.wiley.com/doi/10.1002/14356007.a01_185
FAQ
Friedel-Crafts Alkylation is a chemical reaction used to introduce alkyl groups (such as methyl, ethyl, etc.) onto an aromatic ring. It involves the substitution of a hydrogen atom on the aromatic ring with an alkyl group, resulting in the formation of alkylaromatic compounds.
Friedel-Crafts Alkylation has various industrial applications. Alkylaromatic compounds produced through this reaction are used as starting materials in the synthesis of dyes, pharmaceuticals, fragrances, and agrochemicals. Additionally, they serve as intermediates in the production of polymers and other organic compounds.
Apart from benzene, other aromatic compounds such as naphthalene, toluene, phenol, aniline, and various heterocyclic aromatic compounds like furans and thiophenes can undergo alkylation reactions. The specific conditions and reagents may vary depending on the nature of the aromatic compound and the desired alkyl substitution.
Yes, Friedel-Crafts Alkylation has some limitations and challenges. One major limitation is the possibility of overalkylation, which can lead to polyalkylated products. Steric hindrance in certain aromatic compounds can also hinder the reaction. Additionally, some alkylating agents and Lewis acid catalysts may be sensitive to moisture and air, requiring careful handling and reaction conditions.
While Friedel-Crafts Alkylation is a useful tool for the introduction of alkyl groups on aromatic rings, it may not always be suitable for the synthesis of highly complex molecules due to the potential for multiple substitution products. In such cases, more selective or controlled methods may be required to achieve the desired synthesis.