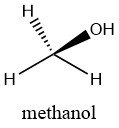
What is Methanol?
Methanol, also known as wood alcohol, is a chemical compound with the formula CH3OH. It is a colorless, flammable liquid with a distinctive alcoholic odor. Methanol is the simplest alcohol, and it is the most important alcohol industrially.
Methanol is a key chemical feedstock used in the production of a wide range of products, including plastics, paints, and pharmaceuticals. It is also used as a fuel and energy source.
Methanol was first isolated in the 17th century, but it was not until the early 20th century that it began to be produced on a commercial scale. Today, methanol is produced using a variety of processes, but the most common method involves reacting carbon monoxide and hydrogen in the presence of a copper oxide catalyst.
Methanol is a highly versatile molecule, and it can be converted into a wide range of other chemicals through a variety of chemical reactions. For example, methanol can be used to produce formaldehyde, acetic acid, and methyl methacrylate.
Methanol is also used as a fuel and energy source. It can be blended with gasoline to reduce emissions, and it can also be used in fuel cells to generate electricity.
Table of Contents
1. Physical Properties of Methanol
Methanol is a colorless liquid with high polarity and medium vapor pressure. It is a versatile solvent that can dissolve a wide range of substances, including water, alcohols, and other organic solvents. It is miscible with oils and fats to a limited extent.
Methanol has the physical properties presented in the following table:
Property | Value |
---|---|
Physical state | Liquid |
Color | Colorless |
Odor | Slightly sweet, alcoholic |
Melting point | −97.6 °C (−143.7 °F; 175.6 K) |
Boiling point | 64.7 °C (148.5 °F; 337.8 K) |
Density | 0.792 g/cm³ |
Solubility in water | Miscible |
Vapor pressure | 160 mmHg at 20 °C (68 °F) |
Flash point | 11 °C (52 °F) |
Flammable limits | 6.7–36% by volume in air |
Autoignition temperature | 455 °C (851 °F) |
2. Chemical Reactions of Methanol
Methanol is the simplest alcohol, and its reactivity is determined by the hydroxyl group. Methanol reacts by cleaving the C-O or O-H bond, and the hydrogen or hydroxyl group can be substituted. Unlike higher alcohols, methanol cannot undergo β-elimination to form a multiple bond.
Important industrial reactions of methanol include:
- Dehydrogenation and oxidative dehydrogenation
- Carbonylation
- Esterification with organic or inorganic acids and acid derivatives
- Etherification
- Addition to unsaturated bonds
- Replacement of hydroxyl groups
1. Methanol combustion: Methanol can undergo combustion, which is a chemical reaction that involves the combination of methanol with oxygen gas to produce carbon dioxide, water, and energy.
2 CH3OH + 3 O2 → 2 CO2 + 4 H2O + energy
This reaction is exothermic and produces a lot of heat, making methanol a useful fuel.
2. Esterification: Methanol can react with carboxylic acids to produce esters, which are organic compounds with a characteristic sweet odor. This reaction is catalyzed by an acid catalyst, such as sulfuric acid or hydrochloric acid.
RCOOH + CH3OH → RCOOCH3 + H2O
3. Dehydration: Methanol can undergo dehydration, which is a chemical reaction that involves the removal of water molecules from methanol to produce dimethyl ether (DME). This reaction is catalyzed by an acid catalyst, such as alumina or zeolite.
2 CH3OH → CH3OCH3 + H2O
4. Oxidation: Methanol can be oxidized to produce formaldehyde (HCHO), which is a useful intermediate compound in the production of various chemicals.
2 CH3OH + O2 → 2 HCHO + 2 H2O
This reaction is typically catalyzed by a metal catalyst, such as copper or silver.
5. Methylation: Methanol can be used as a source of methyl groups (-CH3) in various chemical reactions, such as the methylation of phenols to produce methylphenols.
C6H5OH + CH3OH → C6H4(OCH3)OH + H2O
3. Production of Methanol
Methanol is currently produced on an industrial scale using a low-pressure catalytic conversion of synthesis gas. This process has lower investment and production costs, improved operational reliability, and greater flexibility than other methods.
Methanol production can be divided into three main steps:
- Production of synthesis gas
- Synthesis of methanol
- Processing of crude methanol
3.1. Production of Synthesis Gas
Synthesis gas can be produced from a variety of carbonaceous materials, including coal, coke, natural gas, petroleum, and petroleum fractions. Natural gas is the most common feedstock for large-scale synthesis gas production for methanol synthesis.
The composition of the synthesis gas required for methanol synthesis is characterized by the stoichiometric number S, which is defined as follows:
S = (H2 – CO2)/(CO + CO2)
The stoichiometry number should be at least 2.0 for the synthesis gas mixture. Values above 2.0 indicate an excess of hydrogen, while values below 2.0 indicate a hydrogen deficiency.
A deficiency in hydrogen will reduce the selectivity to methanol, while an excess of hydrogen will increase the size of the synthesis loop. Therefore, a synthesis gas composition with a stoichiometric number slightly above 2.0 is optimal for methanol synthesis.
3.1.1. Synthesis Gas from Natural Gas
Most methanol produced worldwide is derived from natural gas, which can be cracked by steam reforming, autothermal reforming, a combination thereof, or by partial oxidation.
Steam Reforming
In steam reforming, the natural gas feedstock is catalytically cracked in the absence of oxygen with the addition of steam and possibly carbon dioxide. This produces a synthesis gas with a stoichiometric number of well above 2.0.
The stoichiometric number can be adjusted to the desired value of slightly above 2.0 by adding CO2 either up or downstream of the steam reformer. The heat required for the reaction is supplied externally.
Autothermal Reforming
In autothermal reforming, the natural gas feedstock is converted by partial oxidation with oxygen and reaction on a Ni-based catalyst. The heat for the reaction is provided by the exothermic partial oxidation reaction. The synthesis gas obtained is characterized by a deficiency in hydrogen, so hydrogen must be added before routing to the methanol synthesis loop.
Combination of Steam and Autothermal Reforming
In a combination of the two processes, only part of the natural gas stream is subjected to steam reforming. The remainder is fed together with the steam reformed gas to an autothermal reformer (ATR) filled with Ni-based catalyst.
In the ATR, the natural gas is partially oxidized with oxygen. The stoichiometric number of the synthesis gas can be adjusted to slightly above 2.0 by adjusting the split between steam and autothermal reforming and selecting the proper process parameters.
Partial Oxidation
In partial oxidation, the natural gas feedstock is cracked without a catalyst by direct oxidation with oxygen. This generates heat for the reaction.
3.1.2. Synthesis Gas from Other Raw Materials
Hydrocarbons
Higher hydrocarbons, such as liquefied petroleum gas, refinery off-gases, and naphtha, can also be used as raw materials for synthesis gas production for methanol plants. They are processed mainly by steam reforming.
Crude Oil, Heavy Oil, Tar, and Asphalt
Crude oil, heavy oil, tar, and asphalt products can also be converted into synthesis gas, but this is more difficult than with natural gas. Their sulfur content is considerably higher (0.7-1.5% H2S and COS) and must be decreased.
The produced synthesis gas also contains excess carbon monoxide and must, therefore, be subjected to shift conversion with water. The resulting excess of carbon dioxide is removed from the gas. Gas cleaning and carbon dioxide removal can be achieved, for example, within a Rectisol process.
Coal
Coal can be converted into synthesis gas with steam and oxygen by a variety of processes at different pressures (0.5-8 MPa) and temperatures (400-1500 °C). The coal-based synthesis gas must be desulfurized and subjected to shift conversion to obtain the required stoichiometry.
3.2. Synthesis of Methanol
Methanol is synthesized from synthesis gas in a reactor at 200-300 °C and 5-10 MPa. The reaction is exothermic, so heat must be removed to prevent the reactor from overheating.
The gas leaving the reactor is cooled and the methanol is condensed. The remaining gas is recycled back to the reactor, along with fresh synthesis gas. This is necessary because only 50-80% of the synthesis gas is converted to methanol in one pass.
The crude methanol is then purified and distilled. The purge gas from the recycle loop is used to heat the reformer.
Technology Development
Until 1997, the main difference between industrial low-pressure methanol processes was the reactor design. The maximum capacity of methanol plants was 2,500 to 3,000 t/d.
In 1997, Lurgi introduced the MegaMethanol process, which combines different reactor types with a large-scale synthesis gas production plant. This paved the way for methanol plants with capacities of up to 10,000 t/d per train.
Today, there are a variety of methanol synthesis technologies available, each with its own advantages and disadvantages. The major technology providers are Lurgi, JM/Davy, Topsøe, MGC, JM/Uhde, JM/Jacobs, JM/Others, and JM/Toyo.
All of these technologies are based on highly integrated concepts that include all steps from gasification and gas cleaning to synthesis and workup. This allows for high energy and carbon efficiencies of up to 67% and 83%, respectively.
3.2.1. Reactor Design
Methanol has been produced on an industrial scale since the 1960s, and there are still several different basic reactor designs in use today. The best design for a particular plant will depend on the specific requirements, such as the carbon source, availability of utilities, and heat integration.
Adiabatic Reactors
Adiabatic reactors do not remove heat during the reaction, so the temperature gradually increases along the axis of the reactor. This can be mitigated by quenching the reaction with cold gas at several points, or by using a series of reactor beds with intermediate coolers.
Quasi-Isothermal Reactors
Quasi-isothermal reactors maintain a relatively constant temperature throughout the reactor. This is typically done by using a tubular reactor with cooling by boiling water. There are also gas-cooled reactors, in which the heat of reaction is transferred to the reaction gas.
Specific Reactor Designs
Some specific methanol reactor designs include:
- Standard quasi-isothermal reactor: This reactor uses a tubular reactor with cooling by boiling water.
- Variobar reactor: This reactor uses a shell-and-tube reactor coiled in several tiers, with cooling tubes embedded in the catalyst packing.
- Gas-cooled reactor: This reactor has a catalyst bed on the shell side, and the synthesis gas flows through the catalyst bed in either an axial, radial, or axial-radial direction.
- Superconverter: This reactor uses double-walled tubes filled with catalyst in the annular space. The synthesis gas first flows through the inner tube to heat it up, and then in the reverse direction through the catalyst bed to release heat of reaction.
3.2.2. Large-Scale Methanol Synthesis Loop Designs
Methanol is a good energy carrier for remote areas because it can be easily transported. However, to be economical, methanol production plants need to be large-scale. This means that the conversion rate of synthesis gas to methanol needs to be high, so that the amount of gas flowing through the loop is minimized.
One design for a high-conversion methanol synthesis plant is the Lurgi Combined Converter Methanol Synthesis (Figure 1). This process uses two reactors in parallel: a quasi-isothermal boiling water reactor and a gas-cooled reactor.
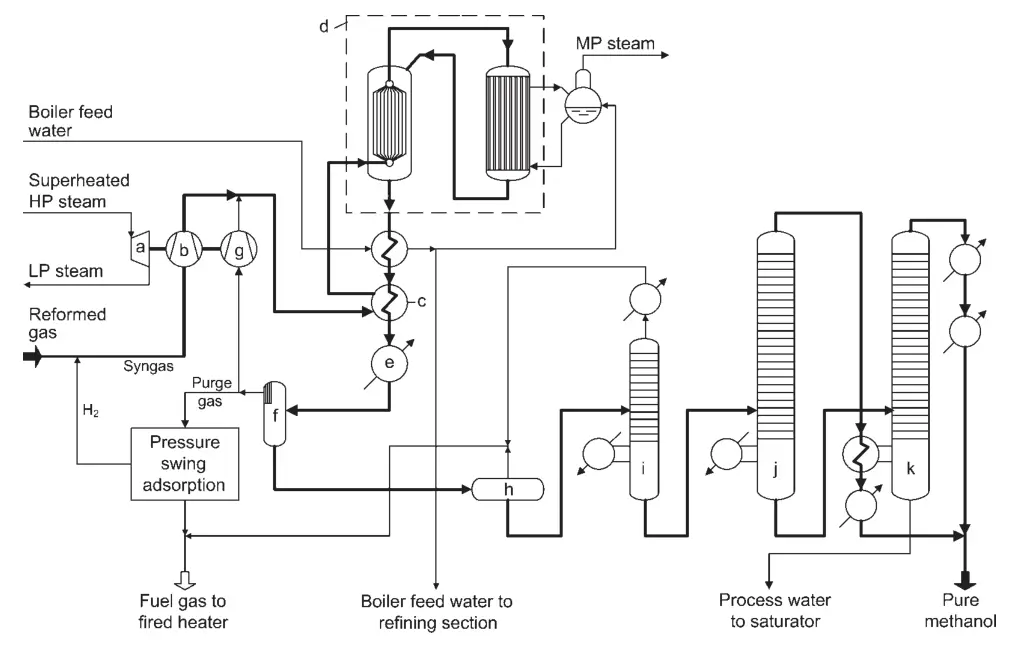
a) Turbine for synthesis gas and recycle compressor; b) Synthesis gas compressor; c) Trim heater; d) Combined converter system; e) Final cooler; f) Methanol separator; g) Recycle gas compressor; h) Expansion vessel; i) Light ends column; j) Pure methanol pressure column; k) Atmospheric methanol column
The quasi-isothermal reactor converts the most reactive part of the synthesis gas, while the gas-cooled reactor converts the remaining gas. The heat of reaction from the gas-cooled reactor is used to preheat the reactor inlet gas for the quasi-isothermal reactor.
Another design for a high-conversion methanol synthesis plant is the series loop technology of Davy Process Technology (Figure 2). This process uses two reactors in series, with the same circulation gas used twice. The driving force for the reaction is maintained by condensing methanol between the two reactors.
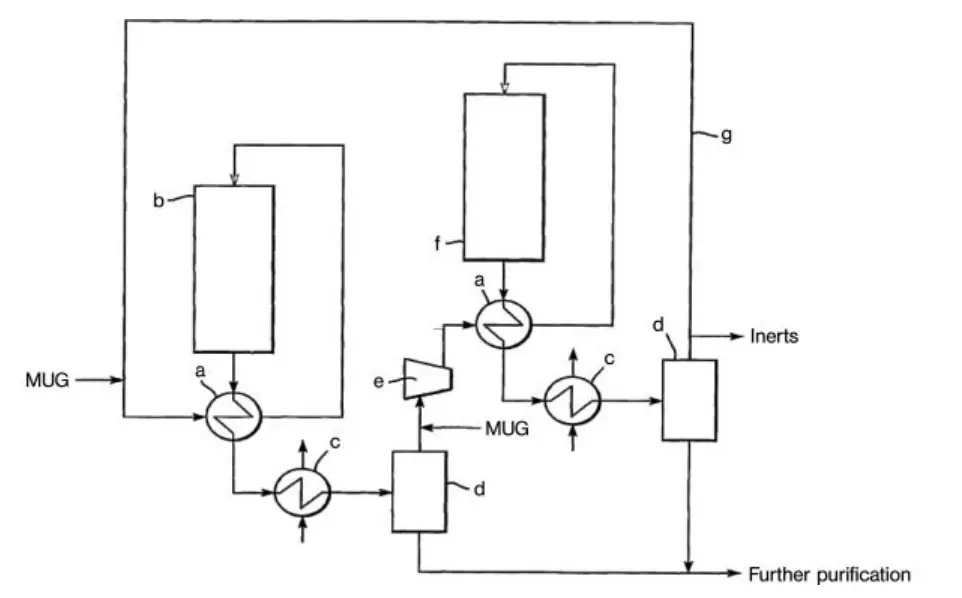
a) Interchanger; b) Reactor; c) Condenser; d) Gas–liquid separator; e) Circulator; f) Final reactor; g) Recycle gas line
3.3. Alternative Synthesis Routes of Methanol
3.3.1. CO2-to-Methanol
The chemical valorization of CO2 by hydrogenation to methanol has been studied since the early 1990s. However, it has only gained commercial interest in recent years due to increasing awareness of the need to reduce CO2 emissions and the development of government policies such as carbon taxes and cap-and-trade programs.
Several companies have developed catalyst systems and process concepts for CO2-to-methanol production. However, pilot-scale results are scarce, and the only demonstration-scale projects are by Mitsui Chemicals and Carbonrecycling, Iceland.
The basic knowledge about the CO2-to-methanol technology is already available, but the real challenges are the production of renewable hydrogen and the economical production of clean CO2 from waste gas streams.
The political, ecological, and economic drivers will decide if and when this technology comes to market.
3.3.2. Liquid Phase Methanol Synthesis
Methanol can also be produced by converting carbon monoxide with hydrogen in a liquid phase, typically methanol. When using suitable reaction conditions and catalyst systems containing alkali components, significant productivities of up to 1.3 kg kgcat⁻¹ h⁻¹ can be reached.
The reaction mechanism in the liquid phase is different from that in the gas phase. It involves the carbonylation of methanol (or a higher alcohol) to the respective methyl ester, followed by hydrogenolysis to the respective alcohol and methanol.
In the late 1990s, a demonstration-scale plant for liquid-phase methanol synthesis was put in operation by the US Department of Energy (DOE) together with Eastman and Air Products. However, it was found that the catalyst lifetimes are inferior to those of conventional processes (best case: 0.17%/d at 215 °C). Both water and CO2 have a negative effect on the catalyst performance.
Despite these challenges, research on liquid-phase methanol synthesis is ongoing. This concept is promising because it has the potential to be more efficient and less expensive than conventional gas-phase methanol synthesis.
3.3.3. Direct Oxidation of Methane
The direct oxidation of methane to methanol is a highly desirable reaction, but it is also very challenging. This is because the reaction is both kinetically and thermodynamically unfavorable.
Most catalyst systems for the direct oxidation of methane to methanol yield either low conversion (<10%) or low selectivity (<80%). However, some companies claim to have developed simple and efficient processes for this reaction, mainly for small gas sources.
One promising catalyst system is heterogeneous Pt-CTF (covalent triazine-based framework) catalysts in a sulfuric acid medium. This system has been shown to achieve high conversion and selectivity for the direct oxidation of methane to methanol.
3.4. Distillation of Crude Methanol
Crude methanol leaving the reactor contains water and other impurities, including light and heavy ends. The amount and composition of these impurities depend on the reaction conditions, feed gas, and catalyst.
To purify the crude methanol, it is first made slightly alkaline by the addition of small amounts of aqueous caustic soda to neutralize lower carboxylic acids and partially hydrolyze esters. Then, the light ends are removed in a light ends column. Finally, pure methanol is distilled overhead in one or more distillation columns.
If the distillation columns operate at different pressures, the heat of condensation of the vapors of the column operating at higher pressure can be used to heat the column at lower pressure.
In case the process water contains slight impurities, either a side draw-off or an additional column for purification is required.
Some components form azeotropic mixtures with methanol, such as acetone, ethyl formate, methyl acetate, ethyl acetate, and methyl proprionate.
4. Uses of Methanol
Methanol has a variety of uses in various industries. For detailed information, see this article: Uses of Methanol →
5. Toxicology of Methanol
Methanol is a poisonous alcohol that can be absorbed through the mouth, skin, and lungs. It is metabolized to formic acid, which can cause acidosis and other health problems.
Symptoms of methanol poisoning include abdominal pain, nausea, headache, vomiting, lassitude, blurred vision, ophthalmalgia, photophobia, and xanthopsia. In severe cases, methanol poisoning can lead to coma and death.
The lethal dose of methanol is between 30 and 100 mL/kg body weight. Sensitivity to methanol varies widely.
Treatment for methanol poisoning includes:
- Administration of ethanol to inhibit the oxidation of methanol to formic acid
- Gastric lavage
- Hemodialysis
- Treatment with alkali to control blood hyperacidity
- Administration of CNS stimulants
- Drinking larger volumes of fluid
- Eye bandage to protect the eyes against light
- Keeping the patient warm
Methanol can also cause chronic poisoning, which is characterized by damage to the visual and central nervous systems.
Reference
- Methanol; Ullmann’s Encyclopedia of Industrial Chemistry. – https://onlinelibrary.wiley.com/doi/10.1002/14356007.a16_465.pub3