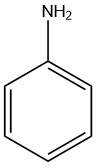
Aniline, also known as aminobenzene, is an aromatic amine with the chemical formula C6H5NH2. It is a flammable colorless to slightly yellow liquid with a sweet, amine-like odor, and it turns brown upon exposure to air and light.
Its isolation dates back to the early 19th century, and its structure was conclusively established by A. W. Von Hofmann in 1843 through the reduction of nitrobenzene.
The initial industrial method for synthesizing aniline was established as early as 1854. In the past 145 years, aniline has emerged as one of the top 100 essential building blocks in the field of chemistry.
Aniline serves as an essential intermediate in a wide variety of applications, such as in isocyanates, rubber processing agents, dyes and pigments, agricultural chemicals, and pharmaceuticals.
Table of Contents
1. Properties of Aniline
1.1. Physical Properties of Aniline
Aniline is partially soluble in water and miscible with most organic solvents (e.g. ethanol, acetone, and benzene).
Important physical properties of aniline are as follows:
- Molecular mass (Mr) = 93.13 g/mol
- Boiling point (101.3 kPa) = 184.4 °C
- Solidification point = -6.2 °C
- Flash point (DIN 51758) = 76 °C
- Ignition temperature (DIN 51758) = 540 °C
- Odor threshold = 0.5 mL/m3
- Density liquid (20 °C) = 1.022 g/cm3
- Solubility (20 °C) Aniline in water =3.6 %
- pH value (3.6 g aniline per liter, 20 °C) = 8.8
1.2. Chemical Reactions of Aniline
The chemistry of aniline is determined by the primary amino group (Figure 1) and by the activated benzene nucleus (Figure 2).
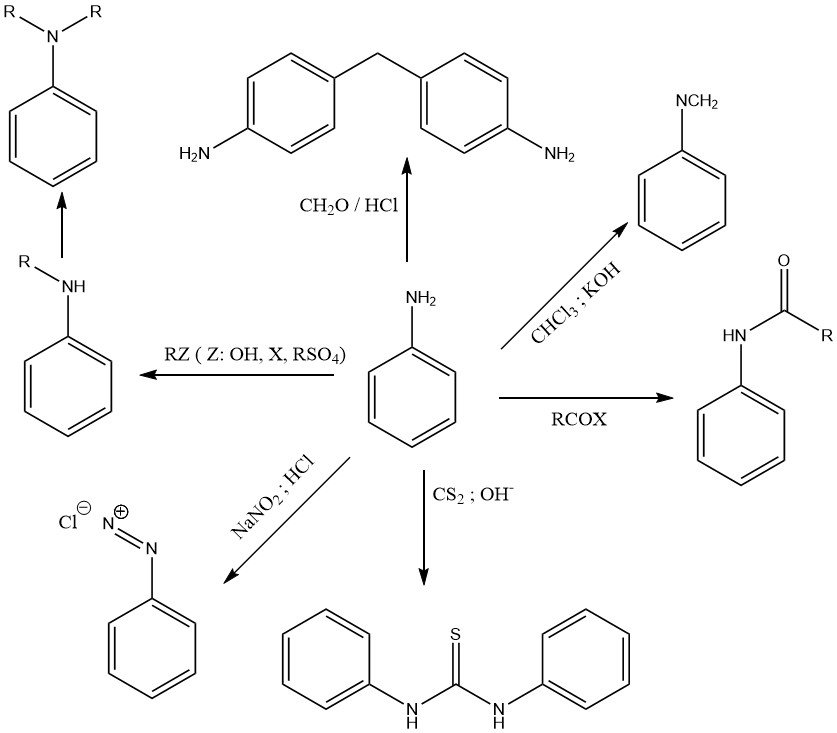
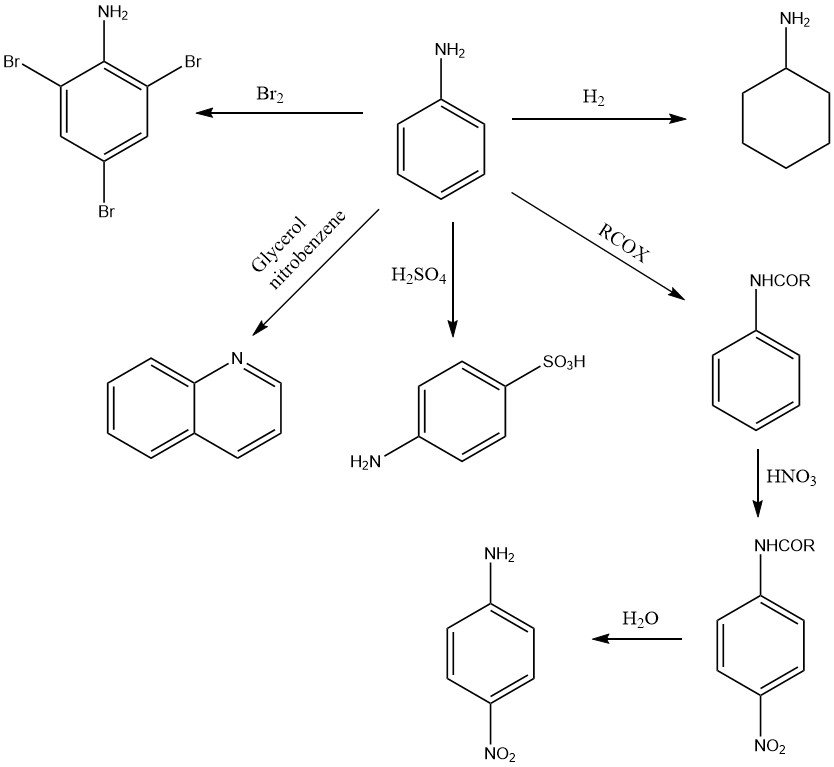
The lone electron pair on the nitrogen of the amino group is partially delocalized to the aromatic ring system. Therefore aniline is only a weak base (pKa = 4.60) as compared with aliphatic amines such as cyclohexylamine (pKa= 10.64).
Nevertheless aniline forms stable, water-soluble salts with strong mineral acids (e.g., hydrochloric or sulfuric acid). The formation of aniline sulfate can be used to protect the amino group of aniline against oxidation during subsequent synthesis steps.
Various alkylating agents (like alcohols, alkylhalides, alkylsulfates, and olefins) alkylate the amino group to form N-alkyl and N,N-dialkylaniline in Lewis acid catalyzed reactions at elevated temperature and pressure.
The reaction of aniline with chloroform in a caustic potash solution produces phenylisocyanide.
N,N-Diphenylthiourea is the product of the reaction of aniline and carbon disulfide in an alkaline alcohol solution.
A characteristic reaction of primary aromatic amines like aniline is the formation of diazonium salts with nitrous acid.
Aniline undergoes condensation reactions with alkylaldehydes. The most important reaction is the formation of 4,4′-methylenedianiline (MDA) by condensation of aniline with formaldehyde in the presence of hydrochloric acid.
Aniline reacts with organic acids and acid derivatives to form amides.
Aniline undergoes a variety of oxidation reactions, depending on the oxidizing agent and the conditions. Mononuclear products like p-benzoquinone (MnO2, H2SO4), bimolecular compounds such as azobenzene (air) or polymeric substances like aniline black (Cu or V, Na2Cr2O7 or NaClO3) may be formed (see Figure 2).
The aromatic ring of aniline is catalytically hydrogenated to give cyclohexylamine and/or dicyclohexylamine at elevated temperature and pressure, depending on conditions and type of catalyst.
The presence of the amino group activates the ortho and para positions of the aromatic ring and, as a result, aniline reacts readily with electrophilic substances. For example, the bromation of aniline with bromine yields 1,3,5-tribromoaniline under mild conditions.
The reaction with sulfuric acid at high temperature forms almost exclusively 4-aminobenzene sulfonic acid (4-sulfanilic acid).
Nitration of aniline (after protecting the amino group against oxidation by the formation of acetanilide) forms the 4-nitro compound.
Numerous N-heterocyclic compounds can be obtained from aniline. For example quinoline is produced in the Skraup synthesis by condensation of aniline with glycerol or acrylaldehyde (acrolein) in nitrobenzene.
2. Production of Aniline
The majority of aniline synthesis processes used in commercial applications initiate from benzene.
Although there have been attempts to directly aminate benzene, the process requires high temperature and pressure, as well as an excess of ammonia, which has hindered the development of an economically viable method.
Instead, DuPont and Mitsui Toatsu have investigated the oxidative amination of benzene, which generates water as a byproduct.
Currently, all global manufacturers, with the exception of Mitsui Petrochemicals Ind. (Japan), utilize nitrobenzene as a raw material for aniline production.
Mitsui Petrochemicals Ind. additionally employs phenol as a starting material, whereas Aristech Chemical Corp. (United States) exclusively uses the phenol route.
2.1. Catalytic Hydrogenation of Nitrobenzene
The highly exothermic catalytic hydrogenation (DH = -544 kJ/mol at 200 °C) of nitrobenzene is performed both in the vapor and in the liquid phase in commercially used processes.
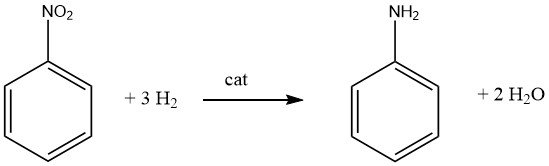
Efficient heat exchange and utilization of the heat of reaction is a crucial aspect for any process that employs nitrobenzene as a raw material.
2.1.1. Catalytic Vapor-Phase Hydrogenation
Nitrobenzene can be converted to aniline with high yields using hydrogenation processes.
Fixed-bed or fluidized-bed vapor-phase techniques are typically employed, with the most effective catalysts being copper or palladium supported on activated carbon or an oxidic substrate, in combination with modifiers or promoters such as Pb, V, P, or Cr to enhance activity and selectivity.
In the Lonza process, which is operated by First Chemical Corp., a homogenized mixture of hydrogen and nitrobenzene is passed over a fixed-bed catalyst of copper on pumice.
Nitrobenzene is sprayed into a heated circulating gas stream of fresh hydrogen at a fixed position to ensure homogenization.
The molar ratio of nitrobenzene feed to total hydrogen is around 1:100 at the reactor inlet, and the reaction products exit the reactor with a temperature above 300°C. The heat generated by hydrogenation is used for steam production and to warm the recycle gas stream.
Excess hydrogen, crude aniline, and water are separated by cooling the reactor outlet in a condenser, and aniline is purified by distillation.
Bayer utilizes conventional fixed-bed reactors employing a palladium catalyst on an alumina support modified by the addition of vanadium and lead.
The process claims adiabatic hydrogenation of nitrobenzene over a fixed-bed catalyst of 1.5 to 4 wt % palladium on coke with 0.1 to 2 wt % lead as a modifier.
The mixture of vaporized nitrobenzene and hydrogen in a molar ratio of 1:120 to 1:200 is fed to the adiabatic reactor at a pressure of 100 – 700 kPa and an inlet temperature of 250 – 350 °C.
The catalyst bed in the reactor is 0.1 to 1.0 m in height, and the reaction products exit the reactor without cooling at a maximum temperature of 460 °C.
After cooling, crude aniline, crude wastewater, and recycled hydrogen are separated under pressure. The crude aniline is purified by distillation.
BASF employs a vapor-phase, fluidized-bed process, where nitrobenzene is partially evaporated by atomization with a hot gas stream primarily composed of hydrogen.
The stream of gas is circulated in the presence of a fluidized catalyst, and the reaction products are condensed, and aniline is separated from the crude reaction products. Copper supported on silica with chromium, zinc, and barium promoters is a preferred catalyst.
The two-phase mixture of nitrobenzene and hydrogen is injected through nozzles at various heights in the fluidized bed, and the hydrogenation occurs in the presence of excess hydrogen at 250 – 300 °C and 400 – 1000 kPa. The reaction heat is used for steam production, and the hot product gas is cooled in a heat exchanger.
After catalyst regeneration, the organic material deposited on the catalyst surface is burned off at 200 to 250 °C with air, and the catalyst is activated again by reducing the copper oxide to copper with hydrogen at 200 to 300 °C.
2.1.2. Catalytic Liquid-Phase Hydrogenation
The hydrogenation processes for aniline employed by ICI and DuPont are conducted in the liquid phase. These processes are typically operated at temperatures ranging from 90 to 200 °C and pressures of 100 to 600 kPa.
The liquid-phase reaction may be carried out using slurry or fluidized-bed reactors. The conversion of nitrobenzene to aniline is typically complete after a single reactor pass with yields of 98 to 99%.
In the 1960s, ICI developed a continuous hydrogenation process that used aniline as the solvent, comprising over 95 wt % of the liquid phase.
The process operates near or at the boiling point of the solvent (usually at pressures below 100 kPa), allowing the reaction mixture to evaporate and dissipate some or all of the heat of the reaction.
Water is removed along with the effluent vapors, while sufficient aniline is returned to the reactor to maintain steady-state conditions. The process employs finely divided nickel on kieselguhr as a preferred catalyst.
DuPont, on the other hand, employs a liquid-phase hydrogenation process for nitrobenzene using a platinum-palladium catalyst on a carbon support with iron as a modifier.
The modifier provides good catalyst life, high activity, and protection against hydrogenation of the aromatic ring. The process employs a plug-flow reactor that achieves nearly quantitative yields, with the product exiting the reactor virtually free of nitrobenzene.
Comparing the catalytic liquid-phase and vapor-phase hydrogenation of nitrobenzene reveals no significant differences in yield and product quality for both processes.
The liquid-phase process, however, has a higher space-time yield and does not require a recycle gas loop, resulting in lower energy requirements.
Conversely, the vapor-phase process effectively utilizes the heat of reaction, producing steam without the need for product-catalyst separation and resulting in longer catalyst life.
2.2. Reduction of Nitrobenzene with Iron and Iron Salts
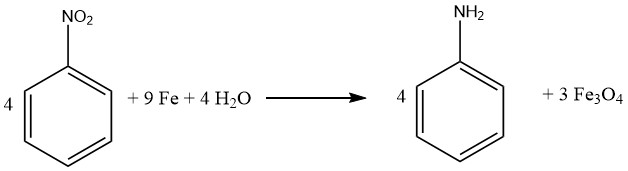
The Bechamp process is a historical method for reducing nitrobenzene, which employs iron and iron (II) chloride. Despite being more than a century old, the process is still used in two Bayer aniline plants to produce colored iron oxide pigments as byproducts.
To carry out the Bechamp process, nitrobenzene is reduced in an agitated reaction vessel with a solution of iron(II) chloride and ground iron fillings.
The reactor is filled with water, including aniline water from aniline distillation, as well as 20% of the iron, the required amount of catalyst, and approximately 5-10% of the total nitrobenzene feed.
The reaction mixture is heated to reflux with intense agitation, and after the reduction has begun, the remaining nitrobenzene and iron are slowly added to prevent excessive temperature and pressure buildup.
The reaction is completed in about 8-10 hours by heating the vessel to 100°C for an additional two hours after the iron/nitrobenzene addition. Following neutralization with lime, the reaction mixture is transferred to a separator, and the organic phase containing aniline is withdrawn.
The aniline is then recovered from the organic phase through water stripping and distillation. Any remaining aniline is recovered from the material remaining in the separator before the iron oxide powder slurry is processed into a fine particle, colored pigment.
The color of the iron oxide byproduct can be manipulated by altering the reaction medium with additives, using different types of iron, and by controlling the calcination conditions.
2.3. Amination of Phenol

Halcon developed a commercial phenol route in which phenol is subjected to amination in the vapor phase using ammonia along with a silica-alumina catalyst.
Due to the exothermic and reversible nature of the reaction (ΔH = -8.4 kJ/mol), high conversion rates can only be achieved using excess ammonia (mole ratio of 20:1) and low reaction temperatures to reduce ammonia dissociation.
Diphenylamine, triphenylamine, and carbazole are impurities produced as byproducts. The use of excess ammonia also inhibits the formation of these impurities. The yield based on phenol and ammonia are ≥ 96% and 80%, respectively.
The process includes vaporizing phenol and fresh and recycled ammonia separately to avoid yield losses. They are then combined in the amination reactor containing the silica-alumina catalyst.
After the reaction, the gas is cooled and partially condensed, and the excess ammonia is recovered in a separation column, compressed and recycled.
The condensation product passes through a drying column to remove water and then through a finishing column in vacuum (less than 80 kPa) to separate aniline from residual phenol and impurities. The phenol containing some aniline (azeotropic mixture) is recycled.
Compared to the nitrobenzene route that starts from benzene, the phenol route involves four steps (cumene to phenol via the intermediate cumene hydroperoxide), while the nitrobenzene route involves only two steps.
The nitrobenzene route has an overall advantage in yield and lower total energy requirements, whereas the phenol route has an advantage in prolonged catalyst life and product quality.
The phenol route is preferred if low-cost phenol is available from phenol producers.
3. Uses of Aniline
Aniline is used in more than 300 different end products, the most important one being the polyurethane building block 4,4-methylene-di-paraphenylene isocyanate (MDI).
3.1 Methylene Diphenylene Isocyanate (MDI)
MDI is a crucial isocyanate that is combined with alcohols, such as polyols and polyetherols, to form polyurethanes (PU). The MDI-based PU systems are widely employed in the construction, furniture, automotive, and insulation industries.
These applications, as well as new fields of application, are predicted to fuel strong growth for MDI-PU, particularly in emerging markets.
A typical commercial MDI process involves the preparation of a mixture of polymeric methylenephenylamines by condensing aniline with formaldehyde in the presence of HCl.
The reaction results in intermediate formation of amine hydrochlorides, which are neutralized with caustic soda. The reaction usually takes place at subatmospheric pressure and temperatures between 70 and 105°C, with an excess of aniline. The yield is approximately 96%.
The polyamine product is then reacted with phosgene in a solvent to produce a crude mixture of isocyanates. The reaction temperature is about 120°C, and the pressure is 345 kPa, with a yield of approximately 97%.
Chlorobenzene is removed by distillation, and the crude is separated by vacuum distillation into pure MDI and polymeric MDI, with the production of hydrogen chloride as a byproduct of the reaction.
3.2 Rubber Processing Chemicals
In the first decade of this century, pure aniline was utilized as a vulcanization accelerator. The call for higher effectiveness and safer handling led to the development of aniline-based mercaptothiazole and sulfenic amide accelerators, which currently account for approximately 80% of all vulcanization accelerators used worldwide.
Aniline’s greater importance within the rubber processing chemicals sector lies in antidegradants such as paraphenylenediamines (PPD), quinolines, and diphenylamine.
Aniline is the feedstock for around 70% of all antidegradants consumed globally. Future demand for aniline in the rubber industry is expected to grow by 2–3% per year, consistent with the global growth in demand for synthetic and natural rubber.
3.3 Dyes and Pigments
Aniline serves as a raw material for intermediates for dyes and pigments, which make up more than 50% of all known formulations. However, most of these formulations are of minor significance. The largest classes are the mono-, di-, and triazo compounds.
Production of dyes and pigments has shifted toward Asian countries, such as China and India. Nevertheless, some world-scale dyes and pigments plants in Europe and NAFTA (United States, Canada, Mexico) still utilize aniline, e.g., for the production of indigo.
Since BASF’s industrial realization of the chemical indigo syntheses in the late 19th century, indigo has become the most critical dye based on aniline.
Worldwide growth for this application is expected to remain low, at a rate of 1–2% per year.
3.4 Agricultural Chemicals
More than 40 active substances for pesticides (herbicides, fungicides, and insecticides) use aniline as raw material. Most importantly, amide and urea herbicides. Companies located in NAFTA account for over 50% of the world’s aniline consumption for agricultural chemicals.
Aniline-based active substances are primarily in the later stages of their life cycle and are about to be replaced. Global consumption is predicted to decline by 1–2% per year.
3.5 Pharmaceuticals
Aniline is a stable, albeit minor, source for the preparation of analgesics, antipyretics, antiallergics, and vitamins. Although the production of aniline is expected to increase in the next five years for pharmaceuticals, there will be a corresponding decrease in its use for vitamin production due to the growing popularity of fermentation technology.
3.6 Cyclohexylamine/Dicyclohexylamine
During the 1990s, aniline became the preferred raw material for the production of cyclohexylamine and dicyclohexylamine. These amines are mainly utilized as intermediates for sulfenamide vulcanization accelerators. Cyclohexylamine is also used in large quantities as a corrosion inhibitor and a feedstock for cyclamates.
The use of these amines in accelerators and water treatment is projected to increase by approximately 3-4% annually, while the demand for cyclohexylamine for the production of cyclamates has fluctuated considerably and is difficult to forecast. If the FDA lifts the ban on cyclamates as artificial sweeteners in the United States, an increase in demand can be expected.
3.7 Miscellaneous
Among a variety of other uses (such as alkylaniline production, optical brighteners, sulfonic acids, etc.), it is worth mentioning the consumption of aniline for the synthesis of aramid fibers.
Aramids are versatile and can be used as substitutes for steel, with equivalent reinforcement properties at a significantly lower weight. Aramids have healthy growth rates due to their application in various industries, such as the replacement of asbestos in brake linings.
Reference
- Aniline; Ullmann’s Encyclopedia of Industrial Chemistry. – https://onlinelibrary.wiley.com/doi/10.1002/14356007.a02_303.pub2