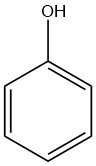
Phenol, also known as hydroxybenzene, is an organic compound with the chemical formula C6H5OH. It is a white crystalline solid at room temperature, but technical grade phenol can be a liquid due to impurities. It has a distinct odor, often described as sickeningly sweet and tarry.
Phenol was initially discovered in 1834 by RUNGE, who successfully isolated it from coal tar and designated it as carbolic acid.
Subsequently, LAURENT obtained it in crystalline form in 1841, determined its composition, and initially named it phenolic acid, which was later shortened to phenol.
In 1858, KEKULE proposed the molecular structure of phenol. Prior to the end of the 1800s, all phenol was recovered from coal and primarily employed as a disinfectant.
In 1897, HOFFMANN accomplished the first synthesis of acetylsalicylic acid from phenol in a pure and stable form. In the 1900s, the demand for phenol surged with the commercialization of phenolic resins after World War I, bisphenols following World War II, and polycarbonates in the 1960s.
Table of Contents
1. Production of phenol
Phenol is produced industrially by the Hock process, which involves the oxidation of cumene. It is the most widely used synthetic pathway, accounting for a production rate of over 6.7 million t/a of phenol and approximately 4.1 million t/a of the coproduct acetone. It is an economically competitive process, supported by the demand for acetone.
Since the demand for phenol is anticipated to grow more robustly in the future, there is a continued commercial interest in discovering new, coproduct-free techniques for phenol synthesis, such as the direct oxidation of benzene to phenol.
The oxidation of toluene with benzoic acid as an intermediate product is currently employed for phenol production.
Despite this, roughly 300,000 t of phenol is still retrieved from coal tar.
Solutia has developed the direct oxidation of benzene to phenol using nitrous oxide since around 1995, although this approach has yet to be commercialized.
The conventional synthetic routes, such as the benzene sulfonation process and hydrolysis of chlorobenzene with caustic soda, are no longer economically important.
1.1. Production of phenol by Cumene Oxidation (Hock Process)
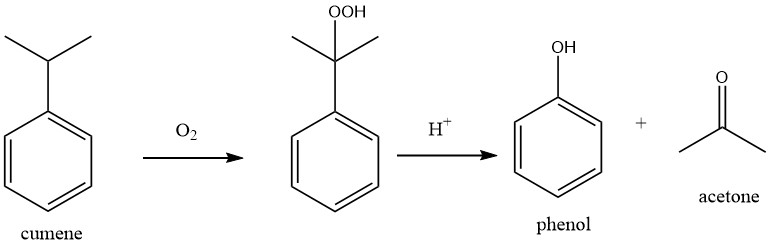
The process comprises two fundamental chemical reactions: cumene is initially subjected to oxidation with oxygen to produce cumene hydroperoxide (CHP), which is subsequently cleaved to form phenol and acetone by using a strong mineral acid as a catalyst.
Both reactions are characterized by high exothermicity, with heats of reaction of -117 kJ/mol for the oxidation of cumene and -252 kJ/mol for the cleavage of the peroxide.
H. HOCK and S. LANG first described these reactions in 1944. The industrial cumene oxidation process was subsequently developed and commercialized by The Distillers Co. in Great Britain and the Hercules Powder Company in the USA after World War II. In 1952, the first plant with a capacity of 8000 t/a was established in Shawinigan, Canada.
1.2. Production of Phenol by Toluene Oxidation
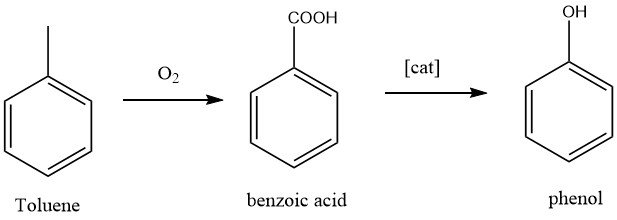
The California Research Corporation and Dow Chemical developed a two-step process for the production of phenol. In the first step, toluene is oxidized to benzoic acid, which is a well-known reaction. In the second step, benzoic acid is further oxidized to phenol.
The conversion of toluene to phenol is a complete oxidation of the methyl group, resulting in the byproducts carbon dioxide and water.
The oxidation of toluene is carried out in the liquid phase at a temperature range of 100 – 150 °C and a gauge pressure of about 2 bar, using atmospheric oxygen. The soluble catalyst used is cobalt naphthenate at concentrations between 0.1 and 0.3 %.
The reaction mechanism of the oxidation of toluene to benzoic acid is complex, with benzyl alcohol and benzaldehyde as intermediates. Byproducts such as benzylbenzoate and biphenyl are formed, as well as formic acid, acetic acid, carbon dioxide, and carbon monoxide.
For the oxidation of benzoic acid in the second step, molten benzoic acid is used as the reactant and solvent medium at a temperature of around 230 –240°C at atmospheric pressure. Atmospheric oxygen, steam, and soluble copper(II) benzoate are used as catalysts, with magnesium salts added as a promotor.
The net result of the simultaneous reactions in the system is the formation of phenol.
Copper(II) benzoate thermally decomposes to copper(I) benzoate and benzoylsalicylic acid, which is subsequently hydrolyzed to benzoic acid and salicylic acid in the presence of water or steam. The salicylic acid decarboxylates rapidly to give phenol and carbon dioxide.
The Dow process was commercialized with the first plant starting up in the early 1960s in Landar, British Columbia, followed by a second plant in Kalama, Washington, and a third in Rosenburg, Netherlands, operated by DSM. In 1991, Nippon Phenol brought a new plant online in Japan.
The Lummus Company introduced a new process for the oxidation of benzoic acid in 1978, conducted in the vapor phase over a copper-containing catalyst in a heterogeneous reactor.
According to Lummus, the reaction does not produce tars or nonvolatile residues, likely due to the rapid removal of phenol from the reaction zone.
1.3. Phenol from Coal
The recovery of “natural” phenol from coal has been a commercial process for producing phenol for a long time and is still being practiced. However, this process has become insignificant as a source of phenol nowadays.
Phenol, as well as many other aromatic compounds, are retrieved from the vapors of coal carbonization, where coal is subjected to temperatures above 900 °C with the absence of air in a coke oven, leaving coke as the solid residue and condensable hydrocarbons and gases as vapors.
The vapors are condensed to form coal tar, which can be washed with aqueous sulfuric acid or phosphoric acid to recover ammonia, or washed with a wash oil to remove benzene. The remaining gas is utilized as fuel on-site and consists of hydrogen and methane.
Continuous distillation is used to further process the coal tar. In the first column, light oil containing benzene, toluene, and xylenes is separated along with water. In the second column, carbolic oil, which includes phenol and phenolic compounds, is separated as the overhead, and naphthalene oil is taken as a side cut.
The bottom product from the second column is further fractionated to produce wash oil for benzene recovery from the off-gas, methylnaphthalene oil, anthracene oil, and pitch. High reflux ratios and a high degree of thermal integration are utilized with plate columns or columns with random packings.
The carbolic oil, which constitutes around 2-3% of the coal tar and contains about 30-35% of phenolic compounds such as phenol and cresols, is subjected to 8-9% caustic soda in an extraction unit. Phenol and cresols, known as tar acids, are extracted as salts into the aqueous phase. The crude phenolate lye is steam distilled to separate residual hydrocarbons and pyridine bases.
The phenolate lye is then treated with carbon dioxide to liberate the acid tars from their salts in the column. The aqueous phase containing sodium carbonate is further treated to remove dissolved phenol.
The organic phase is fractionated into pure phenol (bp 181.8 °C), o-cresol (bp 191.0 °C), a mixture of m- and p-cresoles (bp 202.0 – 203.0 °C), and a xylenol fraction (bp up to 210 °C) by batch distillation.
2. Chemical reactions of phenol
The chemical properties of phenol are characterized by the mutual influence of the hydroxyl group and the aromatic ring upon each other.
2.1. Reactions Involving the O-H Bond
In contrast to aliphatic alcohols, phenol is a weak acid and forms soluble salts with strong bases, which is useful for its recovery from organic solvents such as coal tar. Its pKa value in an aqueous solution is 10.0. The phenolate anion is stabilized by the aromatic ring system.
Phenol can be liberated from its salts even at room temperature, by treatment with carbon dioxide. Near its boiling point, phenol can displace carboxylic acids from their salts to form phenolates.
The hydroxyl group can be easily esterified (e.g., to phenyl acetate) or etherified (e.g., diphenyl ether).
2.2. Reactions of the Aromatic Ring
The electron pair in phenol is delocalized over the aromatic ring, causing its acidity. The excess electrons in the ortho and para positions make phenol highly susceptible to electrophilic substitution. For example, bromine in aqueous solution reacts with phenol to produce 2,4,6-tribromophenol in high yield.
The Kolbe reaction is another important reaction, involving the coupling of carbon dioxide with sodium phenoxide at 125 °C to give sodium salicylate. At 125 °C, carbon dioxide substitutes in the ortho position, whereas at temperatures above 250 °C, the para isomer is favored.
Other reactions following electrophilic substitution include chlorination, sulfonation, and nitration.
2.3. Liquid-Phase Oxidation
Oxidation of organic substances by molecular oxygen generates various intermediate products, such as cumene hydroperoxide. These processes follow a complex radical mechanism.
Phenol can inhibit such reactions by reacting with free radicals to form phenoxy radicals, which are relatively stable and do not propagate the chain mechanism. Therefore, any ingress of phenol into oxidation processes must be avoided.
3. Uses of phenol
The global production capacity of phenol exceeds 9 million tonnes. Bisphenol A, a major derivative of phenol, accounts for approximately 37% of the worldwide output.
Bisphenol A is commonly utilized in the manufacturing of high-quality polycarbonates for automotive applications, compact discs, and glazing, as well as in the production of epoxy resins.
The second largest application of phenol is in the production of phenolic resins with formaldehyde. These resins are primarily used for underseal applications in the automotive industry.
Additionally, phenol is employed for the synthesis of caprolactam by using of the cyclohexanol–cyclohexanone route.
Several other derivatives of phenol are produced, including alkylphenols, diphenols, aniline, and salicylic acid.
As the automotive sector is a significant consumer of phenol derivatives, such as polycarbonates and phenolic resins, the demand for phenol is still largely tied to this market, which tends to be cyclical.
Reference
- Phenol; Ullmann’s Encyclopedia of Industrial Chemistry. – https://onlinelibrary.wiley.com/doi/10.1002/14356007.a19_299.pub3