
Butanol, also known as n-butanol or butan-1-ol, is a primary alcohol with the chemical formula C4H9OH. It’s a colorless liquid with a strong, unpleasant odor, similar to that of burnt whiskey.
Butanol exists naturally in bound forms and concentrated in fermentation-derived fusel oils. Its industrial production began in 1912 with the discovery of Clostridium acetobutylicum Weizmann, a bacterium coaxing carbohydrates into primarily acetone and 1-butanol.
Increasing demand for 1-butanol spurred the development of novel production methods, including:
- Hydrogenation of crotonaldehyde: Formed via acetaldehyde aldolization.
- Reppe synthesis (propene carbonylation).
- Hydrogenation of n-butyraldehyde: Easily obtained by propene hydroformylation which is the current dominant method.
Table of Contents
1. Physical Properties of 1-Butanol
n-Butanol is colorless liquid with a characteristic odor. Its vapors irritate mucous membranes and become narcotic at high concentrations. It is completely miscible with common organic solvents.
Table 1 compiles the major characteristic physical properties of n-butanol.
Property | Value |
---|---|
Molar mass | 74.12 g/mol |
Melting point | -89.3 °C |
Boiling point | 117.7 °C |
Density (20°C) | 0.8098 g/cm³ |
Refractive index (20°C) | 1.3991 |
Viscosity (20°C) | 3.0 mPa·s |
Specific heat (30–80°C) | 2.437 J g⁻¹ K⁻¹ |
Heat of vaporization | 591.64 J/g |
Heat of fusion | 125.2 J/g |
Heat of combustion | 36.111 kJ/g |
Critical pressure | 44.2 hPa |
Critical temperature | 289 °C |
Surface tension (room temp.) | 22.3 mN/m |
Dielectric constant (room temp.) | 17.8 |
Evaporation number (ether = 1) | 33 |
Solubility in water (20°C, wt%) | 7.7 wt% |
Solubility in water (30°C, wt%) | 7.08 wt% |
Solubility of water in 1-butanol (20°C, wt%) | 20 wt% |
Solubility of water in 1-butanol (30°C, wt%) | 20.62 wt% |
Flash point | 34 °C |
Ignition limits in air, vol% | 1.4–11.3 |
Ignition temperature | 380 °C |
2. Chemical Properties of 1-Butanol
As a primary alkohol, 1-butanol is a reactive chemical that serves as starting material for a wide range of reactions.
2.1. Dehydration of 1-butanol
1-Butanol can be dehydrated to a mixture of butenes (1-butene, cis-2-butene, and trans-2-butene) using catalysts like γ-Al2O3 at high temperatures (300-350 °C). At lower temperature and in the presence of dehydration catalysts dibutyl ether is produced.

2.2. Oxidation of 1-butanol
1-Butanol can be dehydrogenated to 1-butanal (butanal) using oxidizing agents such as manganese (IV) oxide in sulfuric acid, nitric acid, chromic acid, or selenium dioxide at low temperature or with only suitable catalysts at high temperatures.
Oxidation of n-butanol to carboxylic acid can be accomplished by reaction with sodium hydroxide at 275 °C, forming the sodium salt of butyric acid together with hydrogen and 2-ethylhexanol.
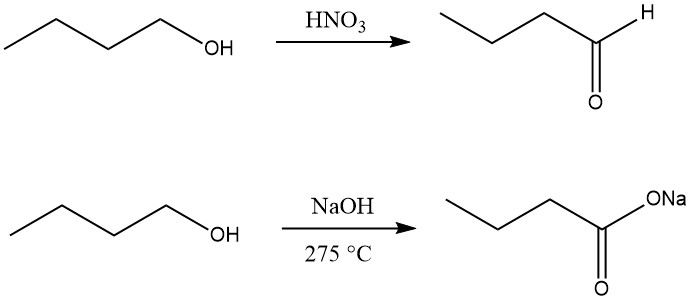
2.3. Alkylation
1-Butanol can be used in various alkylation reactions to produce N-alkyl-, N,N-dialkyl-, or N,N,N-trialkylamines with ammonia and amines. It can also be used in ring alkylation of aromatic hydrocarbons with Friedel–Crafts catalysts.
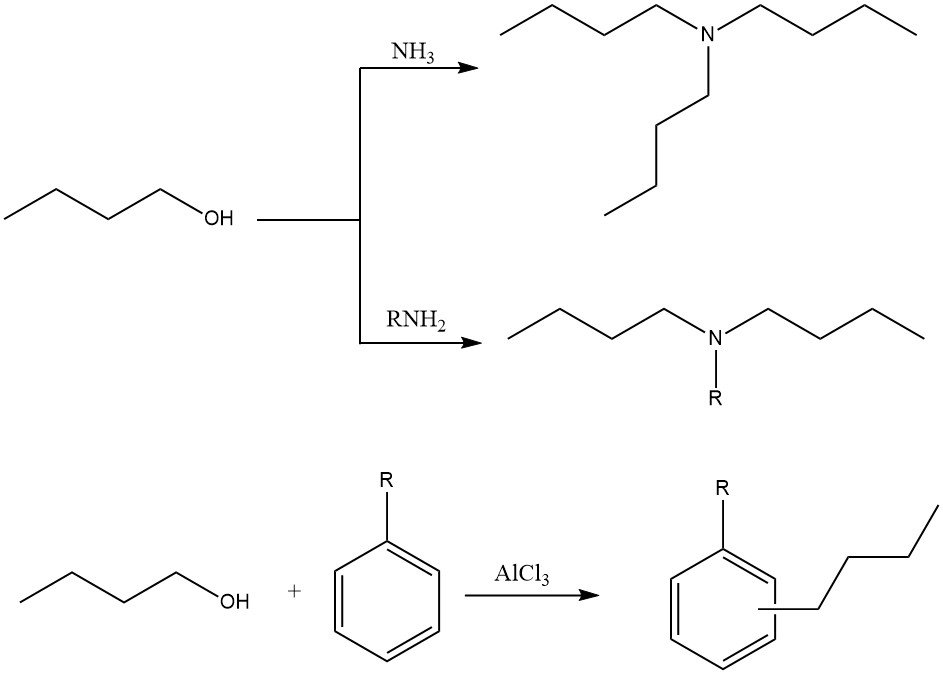
2.4. Esterification of 1-butanol
1-Butanol reacts with inorganic and organic acids to form butyl esters, typically catalyzed by acids. it can also produce esters with with acid chlorides and acid anhydrides.
3. Production of 1-Butanol
Amongst various routes to produce 1-butanol, the following three dominate industry:
- Propene hydroformylation (oxo synthesis)
- Reppe synthesis
- Hydrogenation of crotonaldehyde
3.1. Production of 1-Butanol by Oxo Synthesis
The primary method employed in the production of 1-butanol is the hydroformylation of propene, followed by hydrogenation of the resulting aldehydes. In the hydroformylation, carbon monoxide and hydrogen are added to the double bond of propene in the liquid phase using catalysts such as hydrocarbonyls or substituted hydrocarbonyls of Co, Rh, or Ru.

This initial step yields aldehydes with one additional C-atom compared to the original olefins. Isomeric mixtures of aldehydes are typically obtained, such as 1-butanal and 2-methylpropanal in the case of propene.
Various hydroformylation processes exist with different reaction conditions (pressure, temperature) and catalyst systems.
The traditional high-pressure method, existing until the early 1970s, operates at pressures of 20–30 × 106 Pa CO/H2 and temperatures of 100–180 °C, using Co as the catalyst. This process yields approximately 75% 1-butanol and 25% 2-methyl-1-propanol.
Recent advancements have led to novel process variations. Lower pressure methods (1–5 × 106 Pa) employing modified Rh-catalysts result in isomeric ratios of about 92:8 or 95:5 for 1-butanol to 2-methyl-1-propanol. However, the use of unmodified Rh can increase the percentage of 2-methyl-1-propanol to around 50%.
The catalytic hydrogenation of aldehydes is the subsequent step, leading to the formation of the corresponding alcohols. In 2010, major producers of butanol included BASF, Oxea Group, and the Dow Chemical Company.
3.2. Production of 1-Butanol by Reppe Process
An alternative method for the production of 1-butanol is the carbonylation of propene, a technique invented by REPPE in 1942. In this process, olefins, carbon monoxide, and water undergo a reaction under pressure in presence of catalyst such as the tertiary ammonium salt of polynuclear iron carbonyl hydrides.

This process uses different reaction conditions than conventional Co-catalyzed hydroformylation. At a lower temperature (approximately 100 °C) and reduced pressure (0.5–2 × 106 Pa), butanol is directly formed from the propene.
Similar to the oxo synthesis, carbon monoxide can be added to both C-atoms of the double bond. Consequently, when propene is used as the starting material, 1-butanol and 2-methyl-1-propanol are obtained in a ratio of 86:14.
The catalyst employed, carbonyl triferrate, is sensitive to both air and elevated temperatures. In the presence of water and CO2, it decomposes into iron carbonate.
To maintain sufficient reaction rates, the catalyst needs to be present in concentrations of approximately 10% in the reaction solution, a condition achieved by the use of dissolving agents such as N-alkylpyrrolidine.
Despite favorable n-iso ratios in the resulting products and milder reaction conditions, the Reppe process has not achieved the same level of success as propene hydroformylation with Co catalysts because of the elevated cost of the process technology involved.
3.3. Production of 1-Butanol by Hydrogenation of Crotonaldehyde
Until the mid-20th century, the production of 1-butanol from crotonaldehyde was the preferred method, but it has lost its importance due to the development of more competitive processes.

This process involved multi-step reactions, as follows:
- Aldol condensation: Acetaldehyde undergoes aldol condensation at ambient temperature and pressure, yielding acetaldol with ~95% selectivity and ~60% conversion. Unreacted acetaldehyde can be recovered for further use.
- Dehydration: Acidification of acetaldol with acetic acid or phosphoric acid promotes water elimination and crotonaldehyde formation. This step achieves near-quantitative yield of crotonaldehyde as the primary distillate.
- Hydrogenation: Various gas- and liquid-phase processes use copper catalysts for the efficient hydrogenation of crotonaldehyde to 1-butanol. A yield of ~1000 kg 1-butanol per 1350 kg acetaldehyde is achievable.
The economic viability of this route depends on the raw material costs. As crude oil, the primary feedstock for the oxo synthesis, becomes scarce and expensive, ethanol derived from fermentation may emerge as a competitive alternative.
The abundance and affordability of biomass in tropical countries and developing nations lacking oil reserves make this route particularly appealing. Ethanol can be dehydrogenated to acetaldehyde, serving as the starting material for this process.
3.4. Production of 1-Butanol by Fermentation of Biomass
The production of 1-butanol via biomass fermentation was a prominent industrial process that dominated the 20th century. Starting with Chaim Weizmann’s isolation of Clostridium acetobutylicum in 1914, the so-called ABE fermentation (acetone, butanol, ethanol) became the second-largest biotechnological process, surpassed only by ethanol fermentation.
Other butanol-producing Clostridium strains, like C. beijerinckii and C. saccharoperbutylacetonicum, also emerged and were used.
The classical ABE fermentation employed a batch process lasting 40-60 hours, using starch-containing biomass like corn mash or molasses as substrates. Products were recovered and fractionated by distillation, giving total yields of 25-33 kg/100 kg substrate.
Solvent concentrations reached 12-20 g/L, with a maximum butanol concentration of 14 g/L. However, low crude oil prices and high substrate costs in the late 20th century led to the decline of industrial ABE fermentation, with the last plants closing in South Africa and China by 2004.
However, increasing interest in biofuels and chemicals started a commercial interest in ABE fermentation, particularly for butanol. New fermentation plants have sprung up in Brazil and China, while companies like Gevo and Butamax are actively researching butanol production from renewable feedstocks.
Research efforts focus on maximizing butanol yield as the sole fermentation product, enhancing the production organism’s butanol tolerance, and exploring alternative, non-food substrates like cellulose and hemicellulose.
Theoretically, C. acetobutylicum can generate 0.41 g butanol per gram of glucose based on its fermentation pathways. Researchers are investigating improved strains and growth conditions to boost the butanol/acetone ratio, utilizing metabolic engineering and gene transfer to enhance butanol production in other organisms like E. coli.
Additionally, overcoming the low butanol tolerance of C. acetobutylicum involves strain selection and fermentation modifications like gas stripping or absorption.
The past success and recent resurgence of ABE fermentation highlight its potential for sustainable butanol production. Ongoing research to optimize yields, tolerance, and substrate utilization paves the way for a renewed bio-based butanol industry.
4. Uses of 1-Butanol
In the US, ~85% of 1-butanol is used primary into surface coatings. It serves directly as a solvent for varnishes or is converted into derivative solvents or monomers. It is mixed with toluene, ethanol, or specific esters for the production of nitrocellulose lacquers and used alone as a thinner.
1-Butanol is added in a concentration of 5-10% to prevent “blushing” (unwanted white opacity) caused by thinners, especially volatile ones.
It helps regulate viscosity and improves flow properties of varnishes, and reduces streaking in spirit-soluble gum/resin paints and lacquers.
1-Butanol is used as a mixure of up to 20% to dilute common solvents (mainly saturated carboxylic acid esters, particularly acetates) for polystyrene and chlorinated rubber.
1-Butanol acrylic ester is a key component of latex paints that has gained significant importance since the 1990s due to its durability and cost-effectiveness.
Butyl esters of phthalic, adipic, sebacic, oleic, azelaic, stearic, and phosphoric acids serve as plasticizers and additives in surface coatings, with di-1-butyl phthalate (DBP) being the most significant. However, DBP consumption has stagnated or slightly declined since 2000 in some countries.
1-Butanol is used in butylamines production, particularly in the US, Germany, and Belgium. It also acts as a coagulation bath for spinning acrylic fibers and in dyeing poly(vinyl alcohol) fibers.
5. Toxicology of 1-Butanol
Acute Toxicity:
- 1-butanol exhibits moderate toxicity, with the lowest reported lethal doses being 790 mg/kg (oral, rat) and 3400 mg/kg (dermal, rabbit).
- Inhalation of high concentrations can cause respiratory and eye irritation, incoordination, and narcosis. The lowest published lethal concentration is 24.3 mg/L (rats, inhaled, 4 hours).
- Direct eye contact with 1-butanol causes severe corneal irritation.
- Skin irritation is slight to moderate in rabbits.
- Genetic tests (Ames test) indicate non-mutagenic properties.
Chronic Effects:
- Occupational exposure to 1-butanol vapors at 200 ppm and above has been linked to corneal inflammation, burning sensation, blurred vision, and hearing loss.
- Repeated exposure at 100 ppm may cause mild eye irritation.
- Lower concentrations (25 ppm) have been reported to cause mild irritation and headaches in some individuals.
- Dermatitis of the fingers and hands can occur with direct skin contact.
Exposure Limits:
- Threshold Limit Value (TLV) ceiling limit: 50 ppm (skin) [ACGIH]
- Maximum Allowable Concentration (MAK value): 100 mL/m³ [German Commission for the Determination of Hazardous Substances]
- TRGS 900 value: 100 mL/m³ [German Technical Rules for Hazardous Substances]
References
- Butanols; Ullmann’s Encyclopedia of Industrial Chemistry. – https://onlinelibrary.wiley.com/doi/10.1002/14356007.a04_463.pub3
- Butyl Alcohols; Kirk-Othmer Encyclopedia of Chemical Technology. – https://onlinelibrary.wiley.com/doi/abs/10.1002/0471238961.0221202502091212.a01.pub2