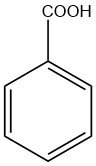
Benzoic acid is a white crystalline solid organic compound with the chemical formula C6H5COOH. The name “benzoic acid” is derived from gum benzoin, a resinous substance obtained from the styrax plant indigenous to South Asia.
Benzoic acid is found naturally in some fruits and vegetables, such as cranberries, prunes, plums, apples, cinnamon, and cloves. It was first extracted by SCHEELE in 1775, and its chemical structure was subsequently elucidated by LIEBIG and W€OHLER in 1832.
The initial methods for producing benzoic acid were developed during the late 1800s, using either the hydrolysis of benzotrichloride or the decarboxylation of phthalic anhydride.
At present, the most commonly used method for manufacturing benzoic acid is the oxidation of toluene with air, a process that has supplanted the former dichromate and nitric acid oxidation techniques.
Table of Contents
1. Production of benzoic acid
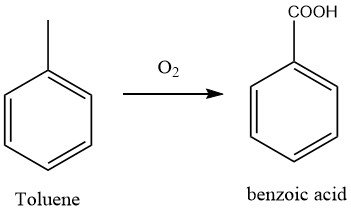
After the oxidation reaction, the crude product was neutralized with sodium carbonate to obtain sodium benzoate, and the unreacted toluene was recovered through distillation. The oxidation process was a free-radical chain process, and peroxides were reaction intermediates.
While cobalt and manganese behaved similarly as catalysts, copper adversely affected the reaction. High pressures also retarded the reaction, especially at lower catalyst concentrations. At temperatures above 130 °C, the reaction rate was determined by oxygen diffusion, and phenolic compounds gradually accumulated during the reaction, inhibiting it eventually.
In modern processes, the oxidation is conducted at 165 °C and 0.9 MPa, and the reaction heat is removed by external circulation of the reactor’s contents.
The pressure of the liquid discharged from the reactor is reduced to atmospheric, and unreacted toluene is recovered.
Benzoic acid is purified by rectification, and the bottom residue is extracted to recover the cobalt catalyst. The exhaust gas is cooled to recover most of the toluene, purified, and vented.
The oxidation reactor can be a bubble column or a stirred tank, with stainless steel as the preferred construction material.
The product is contaminated by small amounts of phthalic acid, carbon monoxide, and carbon dioxide in the exhaust gas, and the yield of benzoic acid varies with toluene conversion, with selectivity for benzaldehyde and benzyl alcohol exceeding 10% at lower conversions.
To produce higher grade products, further processing such as sublimation, recrystallization, and neutralization are necessary.
Methylbiphenyls are responsible for the odor of the product, and for their removal, extraction and treatment in an inert gas stream have been proposed.
The catalytic oxidation of alkylaromatic hydrocarbons can be enhanced by adding bromine compounds to the cobalt catalyst in acetic acid.
This method is now widely used in the production of terephthalic acid and is also applicable to the benzoic acid process.
Another type of cobalt catalyst activator is a readily oxidizable carbonyl compound such as methyl ethyl ketone or acetaldehyde. These additives allow for a considerable reduction in reaction temperature, but because of their high consumption, the technology does not seem to be practical.
Vapor-phase oxidation of toluene at higher temperatures is another potential process, using various catalysts such as vanadium, tungsten, uranium, molybdenum, and silver. However, yields were not comparable to those of the liquid-phase process.
2. Chemical reactions of benzoic acid
The stability of benzoic acid towards common oxidizing agents such as air, permanganate, chromic acid, hypochlorite, and dilute nitric acid has been well documented.
At temperatures exceeding 220 °C, benzoic acid reacts with copper (II) salts to yield phenol and its derivatives. This reaction, which is followed by molecular oxygen-based copper(II) regeneration, is the basis for the industrial production of phenol from benzoic acid.
Under similar conditions, benzoic acid reacts with ammonia to produce aniline.
Upon heating to 150 °C, dehydration occurs, resulting in the formation of benzoic anhydride.
When heated above 370 °C or as low as 245 °C in the presence of catalysts, decarboxylation occurs, leading to the formation of benzene and a small quantity of phenol. The use of copper and cadmium powder catalyses the decarboxylation process.
When potassium benzoate is reacted with carbon dioxide, it disproportionates to terephthalate and benzene, with the aid of cadmium and zinc salts as catalysts.
Fused potassium hydroxide has been shown to convert benzoic acid into hydroxybenzoic acids.
Benzoic acid can be hydrogenated directly using molecular hydrogen, resulting in the production of benzaldehyde in a quantitative yield. The reaction is catalyzed by zirconium and other metal oxides.
Hydrogenation on noble metal catalysts leads to the formation of cyclohexanecarboxylic acid (hexahydrobenzoic acid).
Furthermore, chlorination yields 3-chlorobenzoic acid, nitration forms 3-nitrobenzoic acid, and sulfonation forms 3-sulfobenzoic acid.
3. Uses of benzoic acid
The vast majority of benzoic acid is consumed internally for the production of phenol, with only a small amount entering the open market.
In the year 2006, the use of sodium and potassium benzoate as food preservatives accounted for 41% of the global consumption of benzoic acid.
Benzoic acid is also employed in the manufacture of benzoate plasticizers, alkyd resins, and benzyl chloride.
Glycol esters derived from benzoic acid are used as plasticizers in vinyl resins, with increased demand in the USA due to their replacement of butyl benzyl phthalate in poly(vinyl acetate) emulsion adhesives.
Sodium benzoate serves as a major market for preservatives and anti-corrosives.
Benzoic acid finds application in modified alkyd resins for improving the surface properties of automotive refinishing enamels.
Furthermore, it is utilized as an intermediate for manufacturing perfumes, pharmaceuticals, and cosmetics.
Reference
- “Benzoic Acid and Derivatives”, Ullmann’s Encyclopedia of Industrial Chemistry. – https://onlinelibrary.wiley.com/doi/10.1002/14356007.a03_555