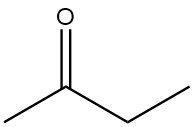
Butanone also known as methyl ethyl ketone, MEK, is an aliphatic ketone and, next to acetone, the most important commercially produced ketone. It is a is a colorless, low-viscosity, flammable liquid with a characteristic ketone-like odor similar to that of acetone.
Butanone is primarily synthesized by the dehydrogenation process of 2-butanol, similar to the production of acetone through dehydrogenation of gaseous isopropyl alcohol using copper, zinc, or bronze catalysts at temperatures ranging from 400 to 550 °C.
The 2-butanol conversion reaches 80 to 95% and the selectivity of butanone exceeds 95%. Byproducts include butenes formed through dehydration and higher ketones resulting from auto condensation. Global production of methyl ethyl ketone (MEK) reached approximately 1 million tons in 2005.
Table of Contents
Since the 1980s, there has been a growing interest in utilizing 2-butanone as a solvent in paints and adhesives. MEK, in particular, is seen as a competitor to ethyl acetate, especially when used as a low-boiling solvent.
Its versatility as a solvent extends to various applications such as nitrocellulose, cellulose acetate-butyrate, ethyl cellulose, acrylic resins, vinyl acetates, and vinyl chloride-vinyl acetate copolymer, primarily in the preparation of synthetic surface coatings.
Its suitability as a lacquer solvent is attributed to its low viscosity, high solids concentration, and wide range of compatible diluents.
The removal of MEK from the hazardous air pollutant (HAP) list in 2005 played a significant role in maintaining the market position of butanone in the United States. Additionally, butanone finds utility as an activator in oxidative reactions, a selective extractive agent, a specialized solvent for dewaxing mineral oil fractions, and a chemical intermediate.
1. Physical Properties of Butanone
Butanone is low-boiling, fast evaporating solvent With a boiling point of 79.6 °C. It is only partially miscible with water, whereas it is completely miscible with most organic solvents.
MEK forms binary and ternary azeotropic mixtures in combination with water and several organic compounds.
Physical properties of butanone include:
- Molar mass = 72.1 g/mol
- melting point = -86.7 °C
- Liquid density at 25 °C = 0.7995
- Refractive index at 25 °C = 1.736
- Liquid viscosity at 25 °C = 0.395 mPa.s
- Solubility at 20 °C in water = 27.5 %
2. Chemical Reactions of Butanone
Under normal conditions and in the absence of atmospheric oxygen, butanone is stable. Care must be taken after prolonged storage because methyl ethyl ketone peroxide forms in the presence of oxygen. Explosions may occur because of instantaneous decomposition of the peroxides.
2-Butanone is unsaponifiable and heat- and light-resistant. However it decomposes after prolonged UV exposure to give ethane, methane, carbon monoxide, ethylene, and diacetyl.
Diacetyl is formed by oxidation of MEK with air in the presence of special catalysts.
Methyl ethyl ketone peroxide a polymerization catalyst, is formed by oxidation of butanone with a solution of hydrogen peroxide.
Nitric acid and other strong oxidants oxidize butanone to a mixture of formic acid and propionic acid.
2-Butanol is obtained by catalytic reduction of butanone with hydrogen, by electrolytic reduction in sodium acetate solution or reduction with ammonium amalgam or lithium aluminum hydride.
Other reduction product is 3,4-Dimethyl-3,4-hexanediol wich is obtained by electrolytic reduction of MEK in an acidic medium or by reduction with magnesium amalgam.
Methyl ethyl ketone exhibits reactivity towards hydrogen cyanide, sodium and potassium hydrogen sulfites, resulting in the formation of addition products.
Under alkaline conditions, 2-butanone undergoes condensation reactions with aldehydes, leading to the production of higher unsaturated ketones. Notably, when formaldehyde is used, methyl isopropyl ketone is produced as an intermediate for subsequent syntheses, presenting a specific area of interest.
During base-catalyzed autocondensation in the liquid phase or gase-phase condensation on alkalinized copper catalysts, the carbonyl group in the molecule reacts with the methyl group. Conversely, in acid-catalyzed condensation, the methylene group adjacent to the carbonyl group becomes the site of attack.
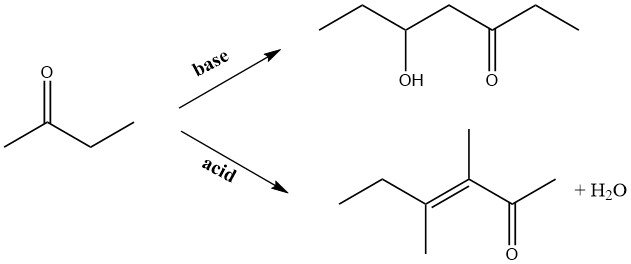
The condensation of butanone and citral results in the formation of methylpseudoionone, which can subsequently undergo cyclization to yield methylionone. This compound is employed in the production of synthetic violet perfumes.
In the presence of low-molecular aldehydes, specifically during base-catalyzed and acid-catalyzed aldolization, the α-position of the carbonyl group is primarily involved in the reaction.
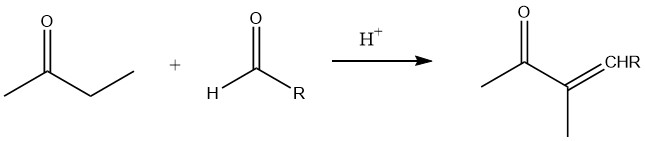
Thus, employing less than stoichiometric amounts of formaldehyde in base-catalyzed aldolization leads to the formation of 2-methyl butane-1-ol-3-one. Furthermore, exhaustive hydroxymethylation accompanied by reduction of the carbonyl group (crossed Cannizzaro reaction) produces desoxyanhydroeneaheptite.
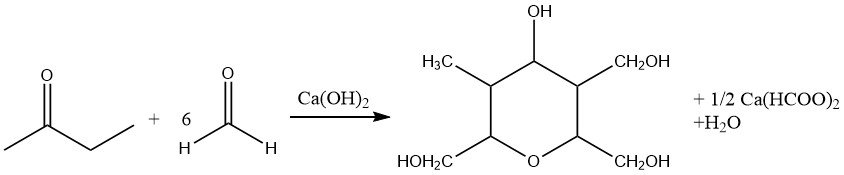
When methyl ethyl ketone reacts with primary and secondary alcohols, it yields higher ketones. The reaction with sec-butyl alcohol specifically results in the formation of ethyl amyl ketone.
Methyl ethyl ketone exhibits reactivity towards polyoxy compounds or epoxides, leading to the formation of cyclic products.
Amyl nitrite selectively attacks the CH2 group in α-position to the carbonyl group, giving the monooxime of diacetyl.

The keto group undergoes reaction with amino groups, resulting in the elimination of water. In combination with hydroxylamine, this reaction yields methyl ethyl ketoxime, an antiskinning agent.
The condensation of butanone with aliphatic esters and anhydrides produces β-diketones.
Phenols undergo reactions with methyl ethyl ketone, forming oxyphenylene compounds. When reacted with phenol, 2,2-hydroxyphenyl butane, a homolog of hydroxyphenyl propane (Bisphenol A), is obtained. Bisphenol A is an important material used in the production of synthetic resins.
Methyl ethyl ketone can be subjected to halogenation at the α-position. Additionally, it reacts with Grignard compounds, resulting in the formation of tertiary alcohols.
In the presence of acetylene and sodium amide, 3-methyl-1-pentyn-3-ol is synthesized. By combining 2-butanone with N-methylformamide, N-Methyl-formyl-aminobutane can be obtained. Furthermore, the Reformatzky reaction enables the production of β-oxyesters using monobromine-substituted esters.
3. Production of Butanone
The primary method for the production of butanone involves the dehydrogenation of 2-butanol (sec-butyl alcohol, SBA). This process technique is employed in approximately 92% of global production capacities, as reported in 2006.
2-butanol can be readily obtained through a two-step process of hydrating n-butenes derived from petrochemical C4-raffinates. Liquid sulfuric acid is utilized as a catalyst in this process. Alternatively, a single-step procedure involves the direct addition of water to a stabilized acidic ion exchange resin, which serves as the catalyst.
The remaining 8% of methyl ethyl ketone is produced through a fatal production method via Fischer-Tropsch synthesis or by catalytic oxidation of liquid n-butane, resulting in the production of acetic acid and MEK as a byproduct.
3.1. Catalytic Dehydrogenation of sec-Butyl Alcohol in the Gaseous Phase
The dehydrogenation of sec-butyl alcohol (SBA) using copper, zinc, or bronze catalysts is an endothermic reaction with a heat change (ΔH) of -51 kJ/mol. Increasing the temperature leads to an elevation in the concentration of butanone in the reaction mixture, which stabilizes at approximately 350 °C, assuming no subsequent reactions occur.
In gas-phase dehydrogenation, copper is the preferred catalyst, while zinc or bronze catalysts typically require higher dehydrogenation temperatures (400 °C).
Zinc oxide catalysts often exhibit lower selectivity due to a side-reaction involving the dehydration of SBA to n-butenes. For the dehydrogenation of SBA, catalysts such as platinum on alumina, copper or chromium, and copper and zinc on alumina are recommended, especially when SBA contains significant amounts of water.
Commercial catalysts are reactivated by oxidation with air after 3-6 months of use. Reactivation becomes necessary when the alcohol conversion rate decreases over time due to contamination of the active catalytic sites by water, deposits of butene oligomers, and di-sec-butyl ether. Higher temperatures and oxidation are employed to remove these contaminants.
Typically, commercial catalysts exhibit a lifetime of several years or more. Deutsche Texaco has developed a process technology for MEK production based on the dehydrogenation of anhydrous sec-butyl alcohol using a copper-based precipitation catalyst at temperatures of 240-260 °C under normal pressure.
In this technology, sec-butyl alcohol is produced through the direct hydration of n-butenes catalyzed by a temperature-stabilized acidic ion-exchange resin. Despite this improved heterogeneous procedure, concentrated sulfuric acid remains the main catalyst worldwide for SBA production through an indirect route.
In the indirect route, the resulting intermediate mono- or di-sec-butyl sulfate from the first reaction step is hydrolyzed in a subsequent reaction step.
The liquid sec-butyl alcohol is vaporized in an evaporator and the resulting gaseous alcohol stream is directed to a multitube reactor, where dehydrogenation takes place on a copper catalyst. The gaseous product stream exits the reactor and, after cooling to ambient temperature, is separated into a liquid phase of crude methyl ethyl ketone and a gaseous hydrogen phase.
The liquid stream still contains some unconverted SBA, along with 5-methyl-3-heptanone, higher ketones, and water, in addition to the desired MEK. The formation of 5-methyl-3-heptanone, higher ketones, and water occurs through autocondensation of two or more MEK molecules.
The 2-butanone is purified through three consecutive distillation steps under atmospheric pressure. In the first step, an azeotropic butanone-water stream is collected as an overhead product, which is further purified in a separate batch distillation column.
The second column yields the desired pure MEK (typically with a purity exceeding 99%) along with SBA mixed with higher ketones as a bottom product. In the final distillation step, the unconverted SBA is distilled off as an overhead product and returned to the process feed tank. The bottom products of this step consist of the higher ketones formed as byproducts during the synthesis process.
3.2. Butanone as a Byproduct of the Fischer-Tropsch Coal-to-Liquid Process
In the Fischer-Tropsch process, a catalytic conversion of carbon monoxide and hydrogen, known as synthesis gas, takes place to produce liquid hydrocarbons. This process yields a wide range of hydrocarbon chain lengths and a significant amount of various byproducts.
Originally developed in the 1920s by German researchers Franz Fischer and Hans Tropsch, the Fischer-Tropsch process has been commercially utilized and further improved by SASOL Ltd., a South African company, since 1955 for the production of synthetic fuels from coal.
The process involves a two-step technique. Initially, mineral coal is gasified to generate synthesis gas, which then undergoes thorough purification through absorption in scrubber systems, utilizing Rectisol technology. The purified synthesis gas is subsequently catalytically converted into hydrocarbons.
In addition to the primary products such as olefins, synthetic fuel, and waxes, a wide range of water-soluble oxygenates are produced as byproducts, accounting for approximately 3-6% selectivity in the water stream during the reaction.
Traditional separation technologies are employed to purify these oxygenates, which include alcohols, organic acids, aldehydes, butanone, and other ketones, into high-value solvent products.
3.3. Liquid-Phase Oxidation of n-Butane
In the liquid-phase oxidation of n-butane to acetic acid, 2-butanone is a reaction byproduct. This process involves the auto-oxidation or direct oxidation of n-butane in the liquid phase through a radical reaction pathway.
The initial oxidation produces MEK as an intermediate product, which, upon further oxidation, forms MEK hydroperoxide. The MEK hydroperoxide is subsequently cleaved into two molecules, resulting in the desired acetic acid as the final product.
Union Carbide Corp. has developed a continuous plug-flow process that allows for the partial collection of the intermediate butanone. This process involves noncatalyzed liquid-phase oxidation at 180 °C and 5.3 MPa, with some back-mixing. Through this process, both MEK and acetic acid are obtained.
Under continuous oxidation conditions with plug-flow at 150 °C, 6.5 MPa, and a residence time of 2.7 minutes, methyl ethyl ketone and acetic acid are formed at mass ratios of up to 3/1.
Celanese Corp. utilizes acetic acid as a solvent, employing a homogeneously dissolved oxidation catalyst system consisting of cobalt acetate and sodium acetate. This batch process is conducted at temperatures between 160 and 165 °C and at a pressure of 5.7 MPa. The resulting products are butanone and acetic acid, with a mass ratio of 0.4/1.0.
3.4. Oxidation of sec-Butylbenzene
The Hock Phenol Synthesis Shell’s SPAM technology, which combines phenol, acetone, and butanone, is based on the oxidation of a mixture of sec-butylbenzene and cumene to their respective hydroperoxide compounds. These hydroperoxides are then conventionally cleaved using an inorganic acid, preferably sulfuric acid, resulting in a mixture of phenol, MEK, and acetone as the desired products.
In the process, the crude ketone stream is separated from phenol through distillation and subsequently purified to obtain the desired pure ketone components. The catalytic cleavage of sec-butylbenzene hydroperoxide (sBHP) with an inorganic acid to produce phenol and butanone has been a well-known process for many years.
However, despite the industrial significance of 2-butanone compared to acetone, this alternative route has not been commercialized due to a major challenge encountered during the oxidation step. The rate of the autocatalytic oxidation of sec-butylbenzene is several times slower than that of cumene, leading to undesired side reactions that negatively affect the overall yield of the desired products.
According to Shell’s research, the decrease in the reaction rate during the oxidation of sec-butylbenzene is attributed to the formation of cleaved products acting as radical scavengers in the reaction mixture, present in parts per million (ppm) concentrations. These scavenger acids include formic acid, acetic acid, and phenol.
To overcome the negative impact on the reaction rate, the following options have been suggested:
1. Using a mixture of sec-butylbenzene and cumene to establish initial amounts of cumene hydroperoxide (CHP) in the first reaction step, which acts as an initiator.
2. Reducing the formation of methanol or ethanol as cleaved products in recycle streams, thereby minimizing the production of the aforementioned scavenger acids.
3. Introducing an aqueous solution of ammonia to a certain extent, allowing the acids to form their ammonium salts while ensuring that phase splitting is avoided.
3.5. Direct Oxidation of n-Butenes (Hoechst-Wacker Process)
The Hoechst-Wacker process involves the direct oxidation of n-butenes, where oxygen is transferred in a homogeneous phase using a redox salt pair, PdCl2/2CuCl. Subsequently, the salt pair undergoes reoxidation.
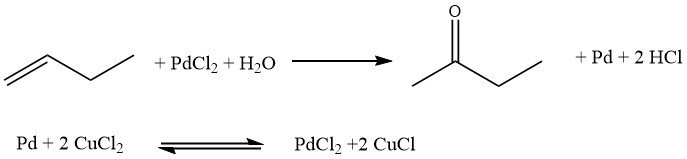
However, this process has certain drawbacks. It leads to the formation of chlorinated butanones and n-butanal, which are undesirable byproducts. Additionally, corrosion issues may arise due to the presence of free acids.
In this process, oxygen is transferred using an aqueous solution of palladium sulfate and ferric sulfate. Similar oxygen transfer principles have been employed in other processes developed by the Consortium for Electrochemistry and Eastman Kodak.
4. Uses of Butanone
Butanone, also known as methyl ethyl ketone (MEK), is a valuable solvent with similar properties to acetone. It offers several advantages compared to other solvents with similar evaporation rates:
- High dissolution power: Butanone exhibits a strong ability to dissolve various substances.
- High ratio of dissolved matter to viscosity: It can dissolve a large amount of material while maintaining a favorable viscosity.
- Miscibility with hydrocarbons: Butanone can mix with numerous hydrocarbons without affecting solids content or viscosity.
- Favorable volume-to-mass ratio: Due to its low density, it provides an advantageous balance between volume and mass.
2-Butanone has the capability to dissolve a wide range of natural substances, plastics, and resins, including rosin, ester resins, nitrocellulose, cellulose derivatives (such as cellulose acetate and cellulose acetobutyrate), epoxy resins, alkyd resins, phenolic resins, vinyl acetate polymers, and many others.
However, it cannot dissolve cellulose triacetate, high-molecular cellulose acetate, poly(vinyl chloride), poly(vinyl butyral), polysulfide rubber, and shellac only partially.
The solvent finds applications in various industries such as paint, lacquer, and varnish production, as well as in paint thinners, adhesives, cements, sealants, magnetic tapes, artificial leather, transparent paper, printing inks, electronic equipment cleaners, cosmetics, pharmaceuticals, degreasing of metal surfaces, and extraction processes.
Butanone is also used as a synthetic flavoring agent in foods and pharmaceuticals, a sterilizer for surgical instruments and dental equipment, and in the manufacturing of smokeless powder.
Although its primary use is as a solvent, butanone has limited importance as a chemical feedstock. However, it can undergo various reactions, such as condensation with formaldehyde to produce methyl isopropenyl ketone, autocondensation to form ethyl amyl ketone, and mixed condensation with acetone to obtain methyl amyl ketone.
MEK is utilized in the production of perfumes, antioxidants, catalysts, peroxides, and diacetals. Methyl ethyl ketoxime in a minor application is employed as an antiskinning agent in lacquers.
Moreover, butanone peroxide serves as a polymerization initiator for unsaturated polyesters.
In the perfume industry, 2-butanone reacts with citral to produce fragrance components like methylpseudoionone. Additionally, it has been approved as an alcohol denaturant in the Federal Republic of Germany since 1962 (as decreed by the Bundesmonopolverwaltung in Offenbach).
Reference
- 2-Butanone, Ullmann’s Encyclopedia of Industrial Chemistry. – https://onlinelibrary.wiley.com/doi/10.1002/14356007.a04_475.pub2