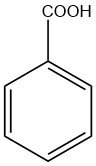
Die Bezeichnung „Benzoesäure“ leitet sich von Benzoeharz ab, einer harzigen Substanz, die aus der in Südasien beheimateten Styrax-Pflanze gewonnen wird.
Benzoesäure wurde erstmals 1775 von SCHEELE extrahiert und ihre chemische Struktur wurde anschließend 1832 von LIEBIG und WÖHLER aufgeklärt.
Die ersten Ansätze zur Herstellung von Benzoesäure wurden im späten 19. Jahrhundert entwickelt und nutzten entweder die Hydrolyse von Benzotrichlorid oder die Decarboxylierung von Phthalsäureanhydrid.
Die derzeit am häufigsten verwendete Methode zur Herstellung von Benzoesäure ist die Oxidation von Toluol mit Luft, ein Prozess, der die früheren Techniken der Dichromat- und Salpetersäureoxidation ersetzt hat
Inhaltsverzeichnis
1. Herstellung von Benzoesäure
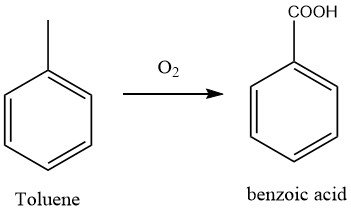
Die Flüssigphasenoxidation von Toluol mit molekularem Sauerstoff wurde während des Zweiten Weltkriegs von I.G. Farbenindustrie in Deutschland. Die Anlage nutzte einen Blasensäulen-Oxidationsreaktor aus mit Aluminium ausgekleidetem Stahl, der über ein Lufteinlassrohr, einen Abscheider und einen Absorber zur Toluolrückgewinnung verfügte.
Die Reaktion wurde mit Kobaltnaphthenat (0,1 %) katalysiert und der Reaktor war mit Wärmetauscherschlangen ausgestattet, um die während der Reaktion entstehende Wärme abzuleiten. Die Reaktion wurde bei 140 °C und ca. 0,2 MPa für 30 Stunden, was zu einer 50 %igen Toluolumwandlung führte, von der 80 % in Benzoesäure umgewandelt wurden.
Das Vorhandensein von Schwefelverbindungen, Stickstoffverbindungen, Phenolen und Olefinen als Verunreinigungen war entscheidend, da sie die Oxidationsreaktion hemmten. Als Katalysatoren wurden auch andere öllösliche Kobaltsalze verwendet.
Nach der Oxidationsreaktion wurde das Rohprodukt mit Natriumcarbonat neutralisiert, um Natriumbenzoat zu erhalten, und das nicht umgesetzte Toluol wurde durch Destillation zurückgewonnen. Der Oxidationsprozess war ein Kettenprozess freier Radikale und Peroxide waren Reaktionszwischenprodukte.
Während sich Kobalt und Mangan als Katalysatoren ähnlich verhielten, beeinflusste Kupfer die Reaktion negativ. Hohe Drücke verlangsamten die Reaktion ebenfalls, insbesondere bei niedrigeren Katalysatorkonzentrationen. Bei Temperaturen über 130 °C wurde die Reaktionsgeschwindigkeit durch die Sauerstoffdiffusion bestimmt, und während der Reaktion sammelten sich nach und nach phenolische Verbindungen an, die sie schließlich hemmten.
In modernen Verfahren wird die Oxidation bei 165 °C und 0,9 MPa durchgeführt und die Reaktionswärme durch externe Zirkulation des Reaktorinhalts abgeführt.
Der Druck der aus dem Reaktor abgelassenen Flüssigkeit wird auf Atmosphärendruck reduziert und nicht umgesetztes Toluol wird zurückgewonnen.
Benzoesäure wird durch Rektifikation gereinigt und der Bodenrückstand wird extrahiert, um den Kobaltkatalysator zurückzugewinnen. Das Abgas wird gekühlt, um den größten Teil des Toluols zurückzugewinnen, gereinigt und entlüftet.
Der Oxidationsreaktor kann eine Blasensäule oder ein Rührkessel sein, wobei Edelstahl als bevorzugtes Konstruktionsmaterial verwendet wird.
Das Produkt ist durch geringe Mengen an Phthalsäure, Kohlenmonoxid und Kohlendioxid im Abgas verunreinigt, und die Ausbeute an Benzoesäure variiert mit der Toluolumwandlung, wobei die Selektivität für Benzaldehyd und Benzylalkohol bei niedrigeren Umsätzen über 10 % liegt.
Um höherwertige Produkte herzustellen, sind weitere Verarbeitungen wie Sublimation, Rekristallisation und Neutralisation erforderlich.
Methylbiphenyle sind für den Geruch des Produkts verantwortlich und es wurde vorgeschlagen, sie zu entfernen, zu extrahieren und in einem Inertgasstrom zu behandeln.
Die katalytische Oxidation alkylaromatischer Kohlenwasserstoffe kann durch Zugabe von Bromverbindungen zum Kobaltkatalysator in Essigsäure verstärkt werden.
Dieses Verfahren wird heute häufig bei der Herstellung von Terephthalsäure eingesetzt und ist auch auf das Benzoesäureverfahren anwendbar.
Eine andere Art von Kobaltkatalysatoraktivator ist eine leicht oxidierbare Carbonylverbindung wie Methylethylketon oder Acetaldehyd. Diese Additive ermöglichen zwar eine erhebliche Senkung der Reaktionstemperatur, aufgrund ihres hohen Verbrauchs scheint die Technologie jedoch nicht praktikabel zu sein.
Ein weiterer möglicher Prozess ist die Dampfphasenoxidation von Toluol bei höheren Temperaturen, bei der verschiedene Katalysatoren wie Vanadium, Wolfram, Uran, Molybdän und Silber zum Einsatz kommen. Allerdings waren die Ausbeuten nicht mit denen des Flüssigphasenverfahrens vergleichbar.
2. Chemische Reaktionen von Benzoesäure
Die Stabilität von Benzoesäure gegenüber üblichen Oxidationsmitteln wie Luft, Permanganat, Chromsäure, Hypochlorit und verdünnter Salpetersäure ist gut dokumentiert.
Bei Temperaturen über 220 °C reagiert Benzoesäure mit Kupfer(II)-Salzen zu Phenol und seinen Derivaten. Diese Reaktion mit anschließender Kupfer(II)-Regeneration auf Basis von molekularem Sauerstoff ist die Grundlage für die industrielle Herstellung von Phenol aus Benzoesäure.
Unter ähnlichen Bedingungen reagiert Benzoesäure mit Ammoniak zu Anilin.
Beim Erhitzen auf 150 °C kommt es zur Dehydratisierung, was zur Bildung von Benzoesäureanhydrid führt.
Beim Erhitzen auf über 370 °C oder auf bis zu 245 °C in Gegenwart von Katalysatoren kommt es zur Decarboxylierung, die zur Bildung von Benzol und einer kleinen Menge Phenol führt. Die Verwendung von Kupfer- und Cadmiumpulver katalysiert den Decarboxylierungsprozess.
Wenn Kaliumbenzoat mit Kohlendioxid reagiert, disproportioniert es mithilfe von Cadmium- und Zinksalzen als Katalysatoren zu Terephthalat und Benzol.
Es wurde gezeigt, dass geschmolzenes Kaliumhydroxid Benzoesäure in Hydroxybenzoesäuren umwandelt.
Benzoesäure kann direkt mit molekularem Wasserstoff hydriert werden, wodurch Benzaldehyd in quantitativer Ausbeute entsteht. Die Reaktion wird durch Zirkonium und andere Metalloxide katalysiert.
Bei der Hydrierung an Edelmetallkatalysatoren entsteht Cyclohexancarbonsäure (Hexahydrobenzoesäure).
Darüber hinaus entsteht durch Chlorierung 3-Chlorbenzoesäure, durch Nitrierung entsteht 3-Nitrobenzoesäure und durch Sulfonierung entsteht 3-Sulfobenzoesäure.
3. Verwendung von Benzoesäure
Der überwiegende Teil der Benzoesäure wird intern zur Herstellung von Phenol verbraucht, nur ein kleiner Teil gelangt auf den freien Markt.
Im Jahr 2006 machte die Verwendung von Natrium- und Kaliumbenzoat als Lebensmittelkonservierungsmittel 41 % des weltweiten Benzoesäureverbrauchs aus.
Benzoesäure wird auch bei der Herstellung von Benzoat-Weichmachern, Alkydharzen und Benzylchlorid eingesetzt.
Von Benzoesäure abgeleitete Glykolester werden als Weichmacher in Vinylharzen verwendet, wobei die Nachfrage in den USA aufgrund ihres Ersatzes von Butylbenzylphthalat in Poly(vinylacetat)-Emulsionsklebstoffen steigt.
Natriumbenzoat ist ein wichtiger Markt für Konservierungsmittel und Korrosionsschutzmittel.
Benzoesäure findet Anwendung in modifizierten Alkydharzen zur Verbesserung der Oberflächeneigenschaften von Autoreparaturlacken.
Darüber hinaus wird es als Zwischenprodukt für die Herstellung von Parfüms, Pharmazeutika und Kosmetika verwendet.
Referenz
- „Benzoic Acid and Derivatives“, Ullmann’s Encyclopedia of Industrial Chemistry. – https://onlinelibrary.wiley.com/doi/10.1002/14356007.a03_555