Industrially, several vital alcohols hold significant importance. These include methanol, ethanol, 1-propanol, 1-butanol, and 2-methyl-1-propanol (also known as isobutyl alcohol).
Also, plasticizer alcohols (ranging from C6 to C11) and fatty alcohols (C12–C18) are extensively used in the production of detergents. These alcohols are obtained primarily through different processes: synthesis gas (methanol), oxo synthesis of olefins, or the Ziegler process.
Besides the mentioned applications, alcohols serve as effective solvents and diluents for paints, mainly utilizing C1–C6 alcohols. They also act as essential intermediates in the production of esters and various organic compounds. Alcohols find applications as flotation agents, lubricants, and fuel additives, including methanol, ethanol, and tert-butyl alcohol.
For industrial applications, isomeric mixtures are often preferred due to cost considerations since pure alcohols can be expensive. Additionally, mixtures with varying carbon atom numbers can offer advantages for specific purposes. As a result, the market availability of alcohol mixtures is comparable to that of pure individual alcohols.
Table of Contents
Introduction
Production of aliphatic alcohols occurs by various industrial processes, some of which are listed below:
- Synthesis from carbon monoxide and hydrogen (C1)
- Oxo synthesis, often accompanied by hydrogenation of initially formed aldehydes (C3 – C20)
- Hydrogenation of aldehydes, carboxylic acids, or esters
- Aldol condensation of lower aldehydes followed by hydrogenation of the alkenals (C3 → C6, C4 → C8, C8 → C16)
- Oxidation of trialkylaluminum compounds (Ziegler process)
- Oxidation of saturated hydrocarbons
- Hydration of olefins (C2–C4)
- Homologation of alcohols
- Hydrocarbonylation by the Reppe process
- Hydrocarboxymethylation
- Fermentation processes (C2–C5)
- Guerbet process
Among these processes, methanol and ethanol synthesis are of paramount importance, with annual productions of approximately 49 × 106 t and 99 × 106 t, respectively. The oxo synthesis also holds significant industrial relevance, accounting for about 6.3 × 106 t of annual production.
Additionally, the hydration of ethylene and propene to yield ethanol and 2-propanol, as well as the oxidation of trialkylaluminum compounds (Alfol process or Ziegler process), have gained substantial commercial significance.
Furthermore, fermentation processes, especially for ethanol production, have regained importance in specific regions due to the rise in oil prices.
1. Synthesis from Carbon Monoxide and Hydrogen
Only methanol is commercially produced from synthesis gas. In the past, processes like Synol, isobutylol, and oxyl were used, leading to mixtures of oxygen-containing compounds with alcohols as the main components. However, these methods are no longer utilized in the Western World. More recent developments either generate oxygen-containing compounds or alcohol mixtures.
One such process is the IFP (Inst. Français du Pétrole) method for higher alcohols. It employs highly activated catalysts under low-pressure methanol synthesis conditions. The catalyst consists of mixed oxides of copper and cobalt, combined with at least one other metal (Al, Ce, Cr, Fe, La, Mn, Pr, Nd, Y, or Zn), as well as at least one Group I or II metal compound.
By adjusting the catalyst composition, the higher alcohol content in the product can be varied between 20–50 wt%. However, this process results in the formation of several byproducts, such as hydrocarbons, esters, and ketones.
Despite these advancements, none of the newer processes mentioned above are currently employed in the industry. However, small quantities of higher alcohols are produced as byproducts in the Fischer-Tropsch synthesis.
2. Oxo Synthesis
The oxo synthesis is a method used to prepare alcohols in the range of C3–C20. In this process, olefins (unsaturated hydrocarbons) react with synthesis gas (a mixture of carbon monoxide and hydrogen) to form aldehydes. Subsequently, these aldehydes are hydrogenated to produce the desired alcohols.
A specific version of the oxo synthesis is known as the Shell process, employing the catalyst HCo(CO)3PR3, which exhibits strong hydrogenating activity. This catalyst facilitates the direct hydrogenation of the initially formed aldehyde within the oxo reactor.

The Shell process was first commercially applied using propene in 1963 for the production of 1-butanol and 2-ethylhexanol. Later, in 1965, it was further developed to manufacture detergent alcohols. Its primary application is in the production of higher alcohols.
One significant advantage of the Shell process is its ability to hydroformylate olefins with internal double bonds. The reaction conditions promote isomerization of the double bond, leading to the formation of α-olefins.
For instance, the ω-olefin fractions obtained from ethylene through Shell’s “SHOP process” can be converted to alcohols using synthesis gas. The resulting alcohol mixtures consist of up to 80% linear compounds and find use in the plasticizer and detergent industries.
3. Hydrogenation of Aldehydes, Carboxylic Acids, and Esters
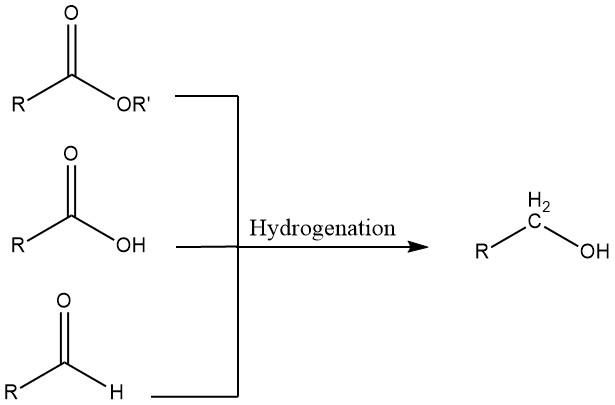
Aldehydes can undergo hydrogenation using either homogeneous or heterogeneous catalysts. Homogeneous systems are advantageous when starting materials contain sulfur, which would poison heterogeneous catalysts, or when the hydrogen used for the hydrogenation contains carbon monoxide.
However, in most cases, heterogeneous catalysts are preferred. These catalysts are effective in both gas-phase reactions at temperatures of 90–180°C and pressures of 25 bar, and liquid-phase reactions at 80–220°C and pressures up to 300 bar. The hydrogenation temperature used in industrial processes is chosen as a compromise between optimal energy utilization and a long catalyst lifetime.
For continuous processes, fixed-bed systems with catalysts are favored. The aldehyde, either in vapor form diluted with excess hydrogen or in liquid form with hydrogen, is passed through the high-pressure pipe containing the catalyst bed.
To dissipate the heat generated by the reaction, hydrogen is circulated through a heat exchanger. The hydrogenation of 2-ethyl-2-hexenal, an especially important reaction, is typically carried out in a single step using a nickel-containing catalyst.
Similar one-step processes have been proposed. However, two-step processes are also common, where the primary hydrogenation occurs in the gas phase (e.g., using copper-containing catalysts), and the secondary hydrogenation occurs in the liquid phase or trickle-bed process (e.g., with nickel-containing catalysts).
These catalysts are typically supported on aluminum oxide or silica gel. In addition to nickel and copper, successful catalysts have been developed using zinc, chromium, and combinations of these metals.
For the production of fatty alcohols, the corresponding carboxylic acid esters are hydrogenated. Natural fats and oils serve as starting materials, which are initially transesterified to form methyl esters and then reduced to alcohols, either using sodium (Bouveault–Blanc reduction) or catalytic hydrogenation.
The sodium reduction allows the preparation of unsaturated fatty alcohols from the esters of unsaturated fatty acids.
The hydrogenation of fatty acids and fatty acid esters requires more severe conditions compared to aldehyde hydrogenation. The process can be conducted continuously or discontinuously using copper-chromium oxide catalysts (Adkins catalysts), either in suspension or fixed bed.
Reaction temperatures of 240–300°C and pressures of 200–300 bar are typical. By modifying the catalysts (e.g., by adding cadmium), unsaturated fatty acid esters can be directly converted to unsaturated fatty alcohols.
4. Aldol Condensation of Lower Aldehydes and Hydrogenation of the Alkenals
In industrial processes, the oxo synthesis is the sole source of aldehydes used for aldol condensation.
After the removal of isoaldehydes and byproducts, the condensation reaction is catalyzed by either acids or bases. The reactivity of each aldehyde is influenced by its chain length and degree of branching, requiring specific reaction conditions tailored to each individual compound.
The aldols formed in the condensation undergo dehydration, resulting in the formation of alkenals. These alkenals are subsequently hydrogenated using heterogeneous catalysts. Typically, the same catalysts employed for the hydrogenation of oxo aldehydes are used for this process.
Through this method, 2-ethylhexanol, 2-methylpentanol, and limited quantities of highly branched isomeric C16 and C18 alcohols can be prepared.
However, the aldox process, which involves subjecting the aldehyde mixture formed in the oxo synthesis to aldol condensation within the oxo reactor, has not gained widespread acceptance due to the presence of mixed aldols in the final products. Nevertheless, certain mixed aldols, such as those of acetaldehyde with higher aldehydes, hold importance in specific applications.
5. Oxidation of Trialkylaluminum Compounds
Ethylene has the capability to undergo addition with triethylaluminum, resulting in a mixture of trialkylaluminum compounds with higher molecular mass. These products can be subjected to oxidation with air, leading to the formation of the corresponding aluminum alkoxides.
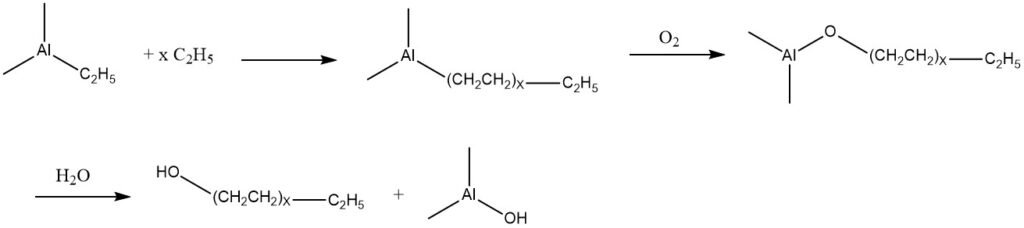
Subsequently, these alkoxides undergo hydrolysis, producing a mixture of linear primary alcohols that possess the same number of carbon atoms as the alkyl groups present in the trialkylaluminum components.
Based on this reaction, known as the Ziegler process, two commercial processes have been developed. One is by Conoco, which has been operational in the United States since 1962 and in Germany by Condea Chemie (Conoco and Deutsche Texaco) since 1964.
The other is by the Ethyl Corp., which has been in operation since 1965. The main differences between the two processes lie in the chain-length distribution and linearity of the resulting alcohols, as well as the technical characteristics involved in generating and controlling this distribution.
In the Alfol alcohol process (Conoco process), the chain-growth reaction is conducted at the lowest possible temperature to avoid displacement reactions that could lead to olefin formation. The resulting alcohols show a chain-length distribution resembling a Poisson curve and are practically 100% linear.
The Alfol alcohol process typically yields a broad range of alcohols (C2–C28), and although adjustments can be made to increase or decrease the chain lengths of the manufactured alcohols, the distribution pattern remains consistent.
On the other hand, the Ethyl Corp. has successfully developed a process with controlled linear chain growth, which predominantly yields C12 and C14 alcohols. These alcohols are up to 95% linear in structure.
6. Oxidation of Saturated Hydrocarbons
The Bashkirov Oxidation involves the oxidation of aliphatic hydrocarbons with air in the presence of boric acid, resulting in high yields of boric acid esters.
These esters are then hydrolyzed in a subsequent step, producing secondary alcohols where the hydroxyl groups are distributed statistically along the molecular chain. The reaction proceeds via an intermediate secondary hydroperoxide.
The oxidation is typically carried out in the liquid phase at temperatures between 150–170°C, with the presence of 4–5 wt% metaboric acid. A nitrogen-oxygen mixture (approximately 3.5% O2) is utilized at normal or slightly elevated pressure.
Some newer plants incorporate amines as co-catalysts. To achieve economically acceptable selectivities of 80–85%, the conversion level is kept below 20%.
Flash evaporation is used to remove starting materials and oxidation byproducts, followed by cleaning in alkaline and water scrubbers, with n-hydrocarbons being recycled.
The metaboric acid esters or boroxines obtained are resistant to oxidation and thermally stable. After fractional distillation, alcohols with a purity greater than 98% are obtained.
The process concludes with “hydrofinishing” (hydrogenation over heterogeneous nickel catalysts) to eliminate colored and odorous substances.
Orthoboric acid in the aqueous solution is converted to metaboric acid by dehydration, and recovery can also be achieved through crystallization.
In some recent variants of the process, the boric acid concentrate is mixed with the n-hydrocarbons, and the mixture is dehydrated to prevent agglomerations and stoppages. The dried slurry is then returned to the oxidation reactor.
Bashkirov originally developed the German work into a commercial process in the 1950s. The first plant started production in Shebekino/Belgorod, USSR, in 1959. Plants were also operated in the Soviet Union and Japan. However, the Union Carbide (UCC) plant in the United States closed in 1977.
The secondary alcohols produced in this process are usually converted into alkylphenol ethoxides and used as detergents. However, due to the costly recirculation of hydrocarbons and boric acid, as well as disadvantages in the application of secondary alcohols, this process has not gained significant importance in the Western World.
Apart from the Bashkirov Oxidation, another significant use of boric acid-catalyzed oxidation is in the preparation of cyclohexanol and cyclohexanone from cyclohexane, as intermediate products in the manufacture of caprolactam, adipic acid, and phenol.
Additionally, it is used in the synthesis of cyclododecanol (an intermediate product in the nylon 12 synthesis) and cyclododecanone from cyclododecane. The process involves oxidation with alkyl hydroperoxides, where iron porphyrins serve as useful catalysts.
Alcohols can be obtained from fatty acids through the esterification of fractionated raw acids (primarily in the C10–C15 range) with methanol or butanol, followed by hydrogenation. When linear hydrocarbons are used as starting materials, linear alcohols can be produced.
However, depending on the specific hydrocarbon, catalyst, and reaction conditions, the alcohol mixture may contain 5–15% branched-chain alcohols. Due to impurities present in the fatty acids, the alcohols derived from them may contain odorous substances, limiting their range of applications.
7. Hydration of Olefins
The hydration of alkenes is a common method for the production of lower alcohols. According to Markovnikov’s rule, secondary and tertiary alcohols are formed in this reaction (except in the case of ethylene).
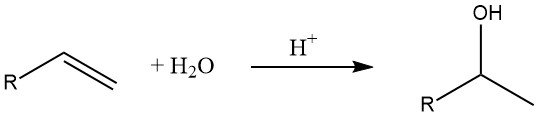
The rate of the hydration reaction depends on the stability of the intermediate carbenium ion, with tertiary carbenium ions being more stable than secondary and primary ones.
Therefore, the hydration of isobutene occurs readily at room temperature in the presence of low H⁺ ion concentrations due to the relative stability of the intermediate tertiary carbenium ion. On the other hand, the hydration of ethylene requires elevated temperatures and pressures.
In industrial settings, two variants of the hydration reaction are used. In the indirect process, the liquid-phase reaction occurs in two steps. Initially, the olefin reacts with sulfuric acid to form mono- and dialkylsulfates, which are then hydrolyzed to produce the alcohol after dilution with water. However, this process requires a costly reconcentration step to recycle the sulfuric acid.
In the direct process, hydration takes place in the gas phase. As the reaction is exothermic and leads to a reduction in volume (2 moles of reactant form 1 mole of product), alcohol formation is favored by high pressure and low temperature.
Due to incomplete conversion, a costly gas recycle is necessary in this process. Efficient catalysts for the direct hydration reaction include phosphoric acid containing materials like celite, although ion exchangers are also increasingly being used.
Direct hydration is primarily employed in the production of ethanol from ethylene and isopropyl alcohol from propene. It also plays an important role in the manufacturing of 2-butanol from a mixture of 1-butene and 2-butene (raffinate II) and tert-butyl alcohol from isobutene.
8. Homologation of Alcohols
Homologation is a chemical reaction where alcohols react with synthesis gas in the presence of complex, multicomponent catalyst systems. Depending on the specific reaction conditions, the products obtained can be either aldehydes or alcohols with one additional CH2 group compared to the starting materials.

Originally, this reaction was developed for the synthesis of ethanol from methanol. However, its applications have been extended to include the production of homologous aldehydes (such as acetaldehyde from methanol), carboxylic acids (e.g., propionic acid from acetic acid), carboxylic acid esters (e.g., ethyl acetate from methyl acetate), and even the synthesis of styrene (by homologation of benzyl alcohol to 2-phenylethanol, followed by dehydration).
Despite significant progress in this area, the homologation process has not been implemented on an industrial scale due to several challenges. The conversion and selectivity achieved so far are still insufficient for practical industrial use, and there are difficulties associated with recycling the complex homologation catalysts. As a result, industrial-scale application of the homologation reaction remains limited.
9. Reppe Process
The Reppe hydrocarbonylation process involves the reaction of olefins with carbon monoxide and water, using ammonium salts of tetracarbonyldihydrido iron as a catalyst, to produce alcohols. Similar to the oxo synthesis, this process also yields branched-chain products, resulting in a molar ratio of linear to branched-chain alcohols of approximately 9:1.

For instance, propene reacts at temperatures of 90–110°C and pressures between 5 and 20 bar to produce butanols with a high yield of 90%. Around 4% of the propene is hydrogenated to form propane. However, the conversion of higher olefins requires more severe reaction conditions.
Despite its potential, the Reppe hydrocarbonylation process cannot compete with hydroformylation in terms of industrial significance. The only known plant utilizing this process to manufacture butanol from propene (Japan Butanol Co., with a capacity of 30,000 t/a) ceased operations in the early 1980s.
10. Hydrocarboxymethylation
Hydrocarboxymethylation is a variation of the Reppe process in which higher olefins undergo a reaction with carbon monoxide and methanol, employing a cobalt-pyridine catalyst.
The resulting products are esters of carboxylic acids that have one more carbon atom in the parent chain compared to the original olefin feedstock. These esters can be further hydrogenated to yield the corresponding alcohols.
However, despite its potential, the process has not gained significant industrial importance due to economic considerations. At the present time, the products can be prepared more cost-effectively using natural raw materials. As a result, hydrocarboxymethylation has not yet achieved widespread significance in industrial applications.
11. Fermentation
Fermentation, which is believed to be one of the oldest methods for producing ethanol, is still widely practiced on a large scale. On a smaller scale, pentanols are recovered from fusel alcohols.
Recently, there has been increasing significance in the butanol–acetone fermentation of carbohydrate raw materials.
Companies like Gevo and Butamax (a joint venture between BP and DuPont) have undertaken extensive research on the production of butanol from renewable feedstocks. This signifies a growing interest in using fermentation processes to manufacture butanol from sustainable sources.
12. Guerbet Alcohols
In the Guerbet process, saturated primary alcohols are dimerized to produce α-branched primary alcohols. Typically, the reaction is conducted by refluxing the alcohol in the presence of an alkaline condensation agent and a hydrogenation-dehydrogenation catalyst, as shown below:

The water and small amounts of hydrogen generated during the reaction are continuously removed. If heating is prolonged, trimeric α-branched primary alcohols can also be formed.
The yield of dimeric alcohols in the Guerbet process is approximately 80%. This yield can be enhanced by recycling the residues and adding fresh catalyst incrementally. While various substances, including metallic sodium, have been proposed as condensation agents, alkali metal hydroxides are commonly preferred for industrial applications.
Short-chain alcohols with chain lengths shorter than cetyl alcohol (C16) are preferably dimerized at higher pressure. Using this process, it is possible to convert short-chain alcohols into C10–C20 alcohols. For example, 2-hexyldecanol and 2-octyldodecanol are produced, which find application in cosmetics as oily components with beneficial solvent properties.
However, the Guerbet reaction has not gained industrial significance as alcohols with typical α-branching are more easily prepared using other methods. For instance, 2-ethyl-1-hexanol can be obtained by hydroformylation of propene to produce butanal, followed by an aldol condensation step.
Due to the availability of alternative processes for synthesizing α-branched alcohols, the Guerbet reaction has not been established as a large-scale industrial process.
13. Other Processes
The epoxidation of linear α-olefins followed by subsequent hydrogenating cleavage is of significant commercial interest. This process leads to the production of plasticizer alcohols (C6–C10) or detergent alcohols (C10–C16).
For the hydrogenating cleavage step, various catalysts can be used. The selectivity towards primary alcohols can be influenced by the choice of catalyst, the conditions of the hydrogenation process, and the use of solvents.
Additionally, the hydrolysis of carboxylic acid esters holds some importance in industrial applications.
Reference
- Alcohols, Aliphatic; Ullmann’s Encyclopedia of Industrial Chemistry. – https://onlinelibrary.wiley.com/doi/10.1002/14356007.a01_279.pub2