
1,4-Butanediol (souvent abrégé en 1,4-BDO) est un composé chimique avec la formule moléculaire C4H10O2. C’est un liquide incolore et inodore qui appartient à la famille des diols, qui sont des composés contenant deux groupes hydroxyle (OH).
Table des matières
1. Propriétés physiques du 1,4-butanediol
Le 1,4-butanediol (masse molaire : 90,12 g/mol) est un liquide transparent avec une odeur minimale, présentant des propriétés hygroscopiques. Il se dissout facilement dans l’eau, les alcools, les cétones, les éthers de glycol et les acétates d’éther de glycol.
Cependant, sa solubilité dans l’éther diéthylique et les esters est plus faible, et il n’est pas soluble dans les hydrocarbures aliphatiques et aromatiques ainsi que dans les hydrocarbures chlorés.
Tableau 1. Propriétés physiques du 1,4-butanediol
Propriété | Valeur |
---|---|
Point de fusion (Mp) | 20,2 °C |
Point d'ébullition (Bp) | 230,5 °C (à 101,3 kPa) |
Densité (𝜚) | 1,017 g/cm³ (à 20°C); 1.0154 g/cm³ (à 25°C) |
Température critique (tc) | 446 °C |
Pression critique (pc) | 41,2 bars |
Viscosité (𝜂) | 91,56 mPa·s (à 20 °C) ; 71,5 mPa·s (à 25 °C) |
Indice de réfraction (nD) | 1,4460 (à 20°C); 1.4446 (à 25 °C) |
Constante diélectrique (𝜀) | 31.4 |
Point d'éclair | 134 °C |
2. Réaction chimique du 1,4-butanediol
Le 1,4-butanediol subit facilement une cyclisation lorsqu’il est exposé à un milieu acide, produisant du tétrahydrofurane.
Lorsqu’il est soumis à une déshydrogénation en phase gazeuse et à l’aide de catalyseurs à base de cuivre, il forme de la 𝛾-butyrolactone.
De plus, le 1,4-butanediol réagit avec les acides monocarboxyliques, donnant des diesters. L’estérification avec des acides dicarboxyliques et leurs dérivés conduit à la formation d’esters polymères thermoplastiques linéaires partiellement cristallins.
Vers 200°C, le 1,4-butanediol réagit avec l’ammoniac ou une amine à l’aide de catalyseurs au nickel ou au cobalt et en présence d’hydrogène, donnant de la pyrrolidine ou des dérivés de pyrrolidine.
Le phosgène réagit avec le 1,4-butanediol à -5∘C, produisant le bis(chloroformiate) de butanediol.
De plus, l’acrylonitrile s’ajoute au 1,4-butanediol à des températures comprises entre 20 et 100∘C, avec la présence de quantités catalytiques d’alcali, conduisant au 1,4-bis(2-cyanoéthoxy)butane.
Semblable à d’autres alcools, le 1,4-butanediol peut également subir une vinylation, entraînant la formation d’éther mono ou divinylique.
3. Production de 1,4-butanediol
Depuis les années 1990, diverses technologies alternatives ont été développées pour la production de 1,4-butanediol. La technologie Reppe, qui repose sur l’acétylène et le formaldéhyde, reste la méthode la plus répandue.
De plus, d’autres procédés utilisent le benzène ou le butane via l’anhydride maléique, le propylène, le butadiène et les sucres comme voies alternatives pour sa fabrication.
3.1. 1,4-butanediol à partir de 2-butyne-1,4-diol
Le 1,4-butanediol est fabriqué à grande échelle industriellement par hydrogénation continue du 2-butyne-1,4-diol. Ce procédé utilise principalement des catalyseurs au nickel modifiés. Le processus d’écoulement en deux étapes est effectué dans la plage de température de 80-170∘C et à une pression de 250-300 bar.

Le processus commence avec une solution aqueuse de 2-butyne-1,4-diol (30-50%), avec de l’hydrogène sans monoxyde de carbone et un mélange réactionnel recyclé, agissant comme un milieu de dissipation de la chaleur.
Ce mélange traverse un catalyseur à lit fixe de type nickel réduit dans le réacteur de tête, où plus de 99 % de la réaction a lieu.
La température initiale est d’environ 80°C et ne doit pas dépasser 170°C pour éviter les réactions de décomposition indésirables. La circulation de l’hydrogène assure une meilleure distribution des liquides. Le deuxième réacteur ou réacteur de finition achève la conversion des composés insaturés.
Différents procédés utilisés dans le commerce diffèrent principalement par le catalyseur utilisé. BASF et Invista Technologies décrivent le Ni supporté sur des oxydes de zirconium ou d’aluminium, tandis que le nickel de Raney, utilisé comme catalyseur à lit fixe, est utilisé et licencié par Invista.
Une autre variante consiste en une hydrogénation basse pression à environ 20 bars à l’aide d’un catalyseur au nickel de Raney en suspension, suivie d’une hydrogénation à 120-140∘C et 140-210 bars catalysée par un contact en lit fixe (par Ineos).
Le produit brut obtenu contient du méthanol, du propanol et du butanol comme sous-produits, ainsi que des traces de 2-méthyl-1,4-butanediol, 4-hydroxybutyraldéhyde, 𝛾-butyrolactone, acétals et triols.
Pour obtenir du 1,4-butanediol pur, l’effluent du réacteur subit une distillation fractionnée. Initialement, l’eau et les monoalcools comme le méthanol, le propanol et le butanol sont éliminés. Par la suite, le 1,4-butanediol est séparé des produits à point d’ébullition élevé tels que les triols et les sels, ainsi que des impuretés telles que la 𝛾-butyrolactone, les acétals, le 2-méthyl-1,4-butanediol et le 4-hydroxybutyraldéhyde.
Le 1,4-butanediol pur peut être isolé davantage dans une colonne supplémentaire, qui sépare le 4-hydroxybutyraldéhyde, les acétals et la 𝛾-butyrolactone en tant que bouilleurs légers.
3.2. 1,4-butanediol à base de benzène ou de butane via l’anhydride maléique
L’oxydation en phase gazeuse du benzène ou du n-butane avec de l’oxygène conduit à la production d’anhydride maléique. Cet anhydride maléique peut être adsorbé à partir du gaz de dégagement d’oxydation par de l’eau, donnant de l’acide maléique, ou par des composés organiques à point d’ébullition élevé tels que le phtalate de dibutyle.
La solution d’acide maléique dans l’eau peut être hydrogénée dans un procédé à haute pression pour donner du 1,4-butanediol, avec la présence de catalyseurs au charbon actif dopé à base de Re. Les dopants utilisés dans ces catalyseurs sont principalement Pd et Pt.
Cependant, le procédé génère des sous-produits tels que le n-butanol, le n-propanol, le méthanol et le tétrahydrofuranne. Malgré sa simplicité, le catalyseur d’hydrogénation est coûteux en raison de la forte teneur en métaux précieux.
Par conséquent, une seule production commerciale de ce procédé a été réalisée jusqu’à présent, menée par Lima aux États-Unis.
Une approche commerciale plus courante implique l’hydrogénation en phase gazeuse des diesters maléiques, qui sont dérivés de l’anhydride maléique.
Ce procédé a été développé par Kvaerner Process Technology (KPT, Londres, aujourd’hui Johnson Matthey Davy Technologies (JM Davy)) dans les années 1980. La première étape consiste à produire du maléate de diméthyle à partir d’anhydride maléique et de méthanol, en utilisant une résine échangeuse d’ions fortement acide comme catalyseur.
Le maléate de diméthyle résultant est ensuite hydrogéné en phase gazeuse à l’aide d’un système catalytique contenant du Cu à une pression de 2-8 MPa et à des températures de 150-250°C.
Ce procédé donne un mélange de 1,4-butanediol, de tétrahydrofurane, de butyrolactone, d’une petite quantité du succinate de diméthyle intermédiaire et, comme sous-produit principal, de n-butanol.
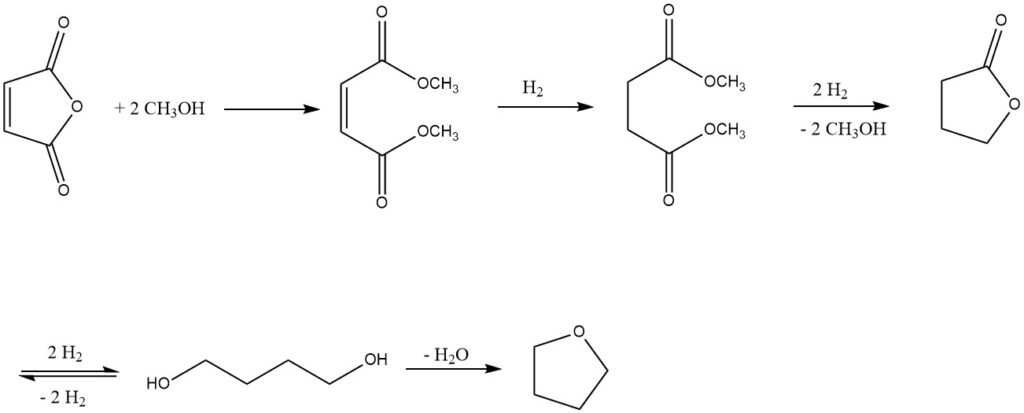
La butyrolactone et le succinate de diméthyle peuvent être récupérés sous forme d’azéotrope et recyclés vers l’étape d’hydrogénation pour obtenir une conversion complète en 1,4-butanediol et tétrahydrofurane.
JM Davy a autorisé ce processus à plusieurs reprises pour établir des usines de butanediol/butyrolactone/tétrahydrofurane dans divers endroits en Asie, notamment en Arabie saoudite, en Malaisie, en Corée et en Chine.
3.3. 1,4-butanediol de propylène
Une autre matière première pour le 1,4-butanediol est le propylène, qui peut être obtenu via l’alcool allylique. Dairen à Taïwan et en Chine, ainsi que Lyondell aux États-Unis et aux Pays-Bas, utilisent ce procédé.
Pour obtenir de l’alcool allylique, le propylène est d’abord oxydé en oxyde de propylène, qui est ensuite isomérisé (Lyondell) ou hydrolysé en alcool allylique. L’hydrolyse implique l’acétoxylation du propylène en phase gazeuse avec de l’oxygène, conduisant à la formation d’acétate d’allyle, qui est ensuite hydrolysé pour donner de l’alcool allylique (Dairen).
L’étape suivante consiste en une hydroformulation d’alcool allylique dans un solvant avec un catalyseur homogène à base de rhodium, produisant du 4-hydroxybutyraldéhyde. Un sous-produit majeur de cette étape est le 3-hydroxy-2-méthyl-propionaldéhyde.
Après extraction des aldéhydes, ceux-ci sont soumis à une hydrogénation utilisant le nickel de Raney comme catalyseur, conduisant au 1,4-butanediol, qui est ensuite purifié par distillation.

Cependant, l’un des principaux sous-produits de cette réaction est le 2-méthyl-1,3-propanediol. De plus, d’autres sous-produits formés au cours de ce processus comprennent le n-propanol et l’isobutyraldéhyde.
3.4. 1,4-butanediol de butadiène
Mitsubishi utilise un procédé en trois étapes pour produire le 1,4-butanediol :
- Le butadiène et l’acide acétique subissent une réaction catalytique pour donner du 1,4-diacétoxy-2-butène.
- L’hydrogénation ultérieure du 1,4-diacétoxy-2-butène donne le 1,4-diacétoxybutane.
- Enfin, l’hydrolyse du 1,4-diacétoxybutane conduit à la formation de 1,4-butanediol.
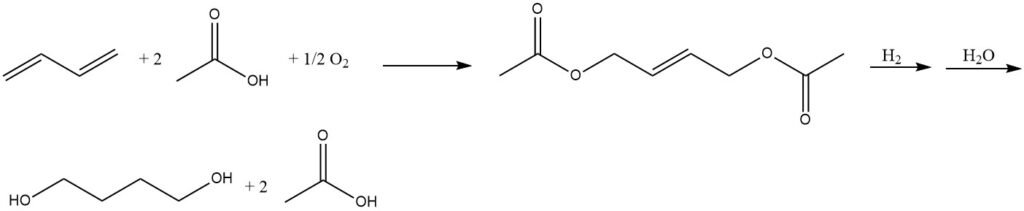
L’hydrolyse du diacétate peut également donner du tétrahydrofurane en raison des conditions de réaction très acides.
BASF a breveté un procédé similaire, où l’acide acétique s’ajoute d’abord au butadiène, et le produit résultant s’isomérise en 1,4-diacétoxy-2-butène.
Le procédé de Toyo Soda implique l’ajout de chlore au butadiène pour former un mélange de 1,4-dichloro-2-butène et de 3,4-dichloro-1-butène. Ce mélange réagit avec l’acétate de sodium pour produire du 1,4-diacétoxy-2-butène, qui est ensuite directement hydrogéné en 1,4-butanediol.
Dans un brevet décrit par Shell, le butadiène réagit avec l’hydroperoxyde de tert-butyle en utilisant un catalyseur au cobalt pour former du 1,4-di(tert-butylperoxy)butène-2, qui est ensuite converti en 1,4-butanediol par hydrogénation. En tant que sous-produit, le 1,2-butanediol est formé.
Eastman a un processus différent qui commence avec le butadiène comme matière première. Tout d’abord, le butadiène est oxydé par l’oxygène en présence d’un catalyseur à l’argent pour former du 1,2-époxy-3-butène. L’époxyde subit ensuite un réarrangement pour donner du 2,5-dihydrofurane, qui est ensuite isomérisé en 2,3-dihydrofurane.
Après addition d’eau catalysée par un acide jusqu’à un équilibre de 2-hydroxytétrahydrofuranne et de 4-hydroxybutyraldéhyde, suivie d’une hydrogénation, du 1,4-butanediol est généré. En variante, la conversion du 2,5-dihydrofurane en 1,4-butanediol peut être réalisée sous la forme d’une synthèse en un seul pot.
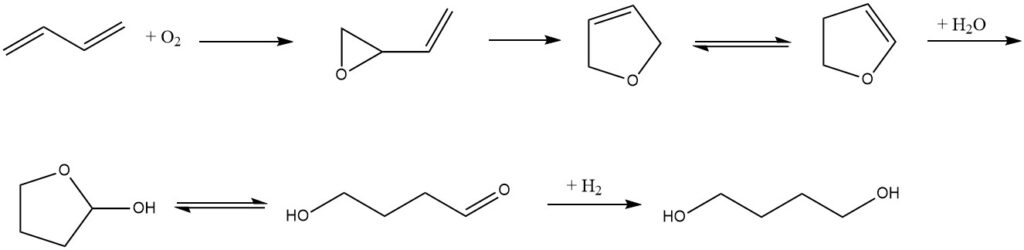
3.5. 1,4-Butanediol issu de la biomasse
Au cours des deux dernières décennies, des efforts importants ont été déployés pour produire du 1,4-butanediol et ses dérivés à partir de sources de biomasse.
L’une des premières approches consistait à utiliser du furfural, qui peut être décarbonylé en furane.
BASF a développé une méthode prometteuse dans laquelle le furane est hydrogéné en présence d’eau et d’un catalyseur à base de rhénium à pression élevée, entraînant la formation de 1,4-butanediol. La 𝛾-butyrolactone et le n-butanol sont des sous-produits.
Shell a également travaillé sur l’optimisation du procédé en utilisant des catalyseurs à base de rhénium. Avec un catalyseur Re/Pd sur carbone, Shell a obtenu un rendement élevé de tétrahydrofurane et de 1,4-butanediol comme produits principaux.
Certaines entreprises utilisent des méthodes de fermentation à base de sucre pour obtenir directement du 1,4-butanediol ou ses précurseurs. Genomatica a développé un procédé pour produire du 1,4-butanediol en faisant fermenter du glucose à l’aide de bactéries Escherichia coli génétiquement modifiées. Après fermentation, le bouillon contient du 1,4-butanediol dilué dans de l’eau, ainsi que de la biomasse et des sels.
Un processus de distillation sépare l’eau, et après une filtration approfondie et l’élimination des sels, le 1,4-butanediol brut subit une hydrogénation pour éliminer les impuretés qui peuvent affecter la stabilité de la couleur.
Une purification supplémentaire est effectuée par des étapes de distillation supplémentaires. Le procédé Genomatica est mis en œuvre commercialement dans une usine (capacité de 30 ×103 t, Novamont) en Italie depuis 2016.
Une autre approche consiste à faire fermenter des sucres en acide succinique, qui sert de précurseur pour la production de 1,4-butanediol. Des entreprises comme BioAmber, Myriant, Reverdia et Succinity ont été impliquées dans la commercialisation de ce processus de fermentation.
La fermentation directe des sucres en acide succinique nécessite un contrôle du pH en raison du faible pH résultant du bouillon de fermentation. Des matériaux basiques comme l’ammoniac ou les hydroxydes alcalins/alcalis de terre sont utilisés pour le contrôle du pH.
Le succinate de diammonia résultant peut être traité avec de l’acide sulfurique pour libérer l’acide succinique. L’acide succinique peut ensuite être converti en 1,4-butanediol par hydrogénation en phase gazeuse sous forme d’anhydride ou de diester à l’aide de catalyseurs à base de Cu ou par hydrogénation en phase liquide à l’aide de catalyseurs à base de métaux précieux.
La fermentation des sucres peut également conduire à la 𝛾-butyrolactone. Metabolix a développé une méthode pour convertir les sucres dans un processus de fermentation en poly(4-hydroxybutyrate) (poly(butyrolactone)), qui peut être dépolymérisé en butyrolactone en présence d’un catalyseur à des températures supérieures à 200∘C.
Les meilleurs résultats sont obtenus avec de l’hydroxyde de calcium comme catalyseur, et la biomasse résiduelle est convertie en combustible solide. Cependant, aucune usine commerciale n’a encore été établie pour ce processus.
4. Utilisations du 1,4-butanediol
Le 1,4-butanediol joue un rôle crucial en tant qu’intermédiaire polyvalent dans l’industrie chimique et sert de précurseur pour la 𝛾-butyrolactone et le tétrahydrofurane.
Son application la plus importante réside dans la production de polyuréthanes et de polyesters, tels que le poly(téréphtalate de butylène), communément appelé PBT. Ces matériaux ont diverses utilisations dans diverses industries.
Les polyuréthanes dérivés du 1,4-butanediol sont utilisés dans la production d’élastomères cellulaires et compacts, qui trouvent de nombreuses applications en raison de leur élasticité et de leur résilience.
Le poly(téréphtalate de butylène) est largement traité pour créer des matériaux plastiques et des adhésifs thermofusibles. De plus, il est utilisé dans la production de films plastiques et de fibres, ce qui en fait un matériau polyvalent utilisé dans différents produits et industries.
Les références
- Butanediols, Butenediol, and Butynediol, Ullmann’s Encyclopedia of Industrial Chemistry. – https://onlinelibrary.wiley.com/doi/10.1002/14356007.a04_455.pub2
-
Organic Acids: Succinic and Malic Acids. – https://www.sciencedirect.com/science/article/abs/pii/B9780444640468001592
- https://www.industrialchemicals.gov.au/sites/default/files/1-4-Butanediol.pdf
FAQ
Le 1,4-butanediol (BDO) est un composé chimique de formule moléculaire C4H10O2. C’est un liquide incolore, inodore et hygroscopique avec une large gamme d’applications dans diverses industries.
Le 1,4-butanediol peut être produit par plusieurs méthodes. Le procédé industriel le plus courant est l’hydrogénation du 2-butyne-1,4-diol, de l’anhydride maléique ou de l’acide maléique. D’autres méthodes incluent la réaction catalytique du butadiène et de l’acide acétique ou la fermentation de sucres à l’aide de bactéries génétiquement modifiées.
Le 1,4-butanediol a diverses utilisations dans différentes industries. Certaines de ses principales applications incluent:
– Production de polyuréthanes et de polyesters, dont le poly(téréphtalate de butylène).
– Solvant dans la fabrication de plastiques, de résines et de revêtements.
– Agent nettoyant et dégraissant dans les produits industriels et ménagers.
– Intermédiaire chimique dans la synthèse de la γ-butyrolactone (GBL) et du tétrahydrofuranne (THF).
Le 1,4-butanediol est également connu sous son abréviation « BDO ». C’est un raccourci couramment utilisé dans l’industrie chimique pour désigner ce composé.