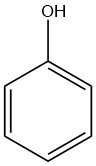
Phenol, auch Hydroxybenzol genannt, ist eine organische Verbindung mit der chemischen Formel C6H5OH. Bei Raumtemperatur ist es ein weißer kristalliner Feststoff, technisches Phenol kann jedoch aufgrund von Verunreinigungen flüssig sein. Es hat einen ausgeprägten Geruch, der oft als widerlich süß und teerig beschrieben wird.
Phenol wurde erstmals 1834 von RUNGE entdeckt, der es erfolgreich aus Kohlenteer isolierte und als Karbolsäure bezeichnete.
Anschließend erhielt LAURENT es 1841 in kristalliner Form, bestimmte seine Zusammensetzung und nannte es zunächst Phenolsäure, die später zu Phenol abgekürzt wurde.
1858 schlug KEKULE die Molekülstruktur von Phenol vor. Vor dem Ende des 19. Jahrhunderts wurde das gesamte Phenol aus Kohle gewonnen und hauptsächlich als Desinfektionsmittel eingesetzt.
Im Jahr 1897 gelang HOFFMANN die erste Synthese von Acetylsalicylsäure aus Phenol in reiner und stabiler Form. In den 1900er Jahren stieg die Nachfrage nach Phenol mit der Kommerzialisierung von Phenolharzen nach dem Ersten Weltkrieg, von Bisphenolen nach dem Zweiten Weltkrieg und von Polycarbonaten in den 1960er Jahren.
Inhaltsverzeichnis
1. Herstellung von Phenol
Der Hock-Prozess, bei dem Cumol oxidiert wird, ist der am weitesten verbreitete Syntheseweg für die Phenolproduktion und sorgt für eine Produktionsrate von über 6,7 Millionen t/a Phenol und etwa 4,1 Millionen t/a des Nebenprodukts Aceton. Es handelt sich um ein wirtschaftlich wettbewerbsfähiges Verfahren, das durch die Nachfrage nach Aceton unterstützt wird.
Da die Nachfrage nach Phenol in Zukunft voraussichtlich stärker wachsen wird, besteht weiterhin ein kommerzielles Interesse an der Entdeckung neuer, nebenproduktfreier Techniken für die Phenolsynthese, wie beispielsweise der direkten Oxidation von Benzol zu Phenol.
Zur Phenolherstellung wird derzeit die Oxidation von Toluol mit Benzoesäure als Zwischenprodukt eingesetzt.
Trotzdem werden immer noch rund 300.000 t Phenol aus Steinkohlenteer gewonnen.
Solutia hat seit etwa 1995 die direkte Oxidation von Benzol zu Phenol unter Verwendung von Lachgas entwickelt, obwohl dieser Ansatz noch nicht kommerzialisiert wurde.
Die herkömmlichen Synthesewege wie die Benzolsulfonierung und die Hydrolyse von Chlorbenzol mit Natronlauge haben keine wirtschaftliche Bedeutung mehr.
1.1. Herstellung von Phenol durch Cumol-Oxidation (Hock-Prozess)
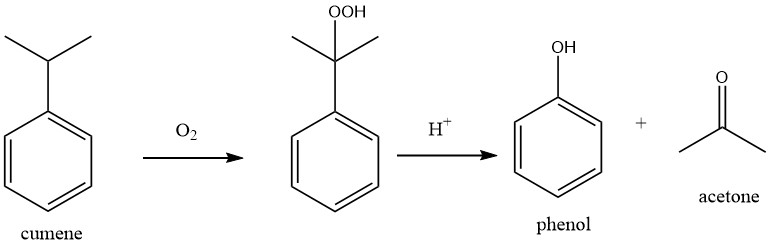
Der Prozess umfasst zwei grundlegende chemische Reaktionen: Cumol wird zunächst mit Sauerstoff oxidiert, um Cumolhydroperoxid (CHP) zu erzeugen, das anschließend unter Verwendung einer starken Mineralsäure als Katalysator in Phenol und Aceton gespalten wird.
Beide Reaktionen zeichnen sich durch eine hohe Exothermie aus, mit Reaktionswärmen von -117 kJ/mol für die Oxidation von Cumol und -252 kJ/mol für die Spaltung des Peroxids.
H. HOCK und S. LANG beschrieben diese Reaktionen erstmals 1944. Das industrielle Cumol-Oxidationsverfahren wurde anschließend nach dem Zweiten Weltkrieg von The Distillers Co. in Großbritannien und der Hercules Powder Company in den USA entwickelt und kommerzialisiert. 1952 wurde in Shawinigan, Kanada, die erste Anlage mit einer Kapazität von 8000 t/a errichtet.
1.2. Herstellung von Phenol durch Toluoloxidation
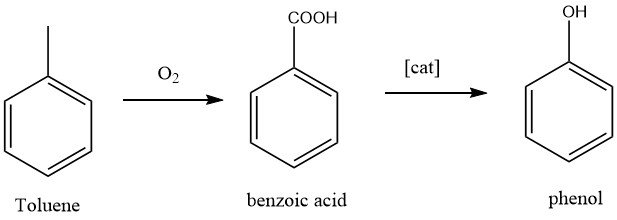
Die California Research Corporation und Dow Chemical haben ein zweistufiges Verfahren zur Herstellung von Phenol entwickelt. Im ersten Schritt wird Toluol zu Benzoesäure oxidiert, eine bekannte Reaktion. Im zweiten Schritt wird Benzoesäure weiter zu Phenol oxidiert.
Bei der Umwandlung von Toluol in Phenol erfolgt eine vollständige Oxidation der Methylgruppe, wobei die Nebenprodukte Kohlendioxid und Wasser entstehen.
Die Oxidation von Toluol erfolgt in flüssiger Phase bei einem Temperaturbereich von 100 – 150 °C und einem Überdruck von etwa 2 bar unter Verwendung von Luftsauerstoff. Als löslicher Katalysator wird Kobaltnaphthenat in Konzentrationen zwischen 0,1 und 0,3 % eingesetzt.
Der Reaktionsmechanismus der Oxidation von Toluol zu Benzoesäure ist komplex, mit Benzylalkohol und Benzaldehyd als Zwischenprodukten. Es entstehen Nebenprodukte wie Benzylbenzoat und Biphenyl sowie Ameisensäure, Essigsäure, Kohlendioxid und Kohlenmonoxid.
Für die Oxidation von Benzoesäure im zweiten Schritt wird geschmolzene Benzoesäure als Reaktant und Lösungsmittelmedium bei einer Temperatur von etwa 230–240 °C und Atmosphärendruck verwendet. Als Katalysatoren werden Luftsauerstoff, Wasserdampf und lösliches Kupfer(II)-benzoat verwendet, wobei Magnesiumsalze als Promotor zugesetzt werden.
Das Nettoergebnis der gleichzeitigen Reaktionen im System ist die Bildung von Phenol.
Kupfer(II)-benzoat zersetzt sich thermisch zu Kupfer(I)-benzoat und Benzoylsalicylsäure, die anschließend in Gegenwart von Wasser oder Dampf zu Benzoesäure und Salicylsäure hydrolysiert wird. Die Salicylsäure decarboxyliert schnell zu Phenol und Kohlendioxid.
Das Dow-Verfahren wurde kommerzialisiert, als die erste Anlage Anfang der 1960er Jahre in Landar, British Columbia, in Betrieb ging, gefolgt von einer zweiten Anlage in Kalama, Washington, und einer dritten in Rosenburg, Niederlande, die von DSM betrieben wurde. 1991 nahm Nippon Phenol in Japan eine neue Anlage in Betrieb.
Die Lummus Company führte 1978 ein neues Verfahren zur Oxidation von Benzoesäure ein, das in der Dampfphase über einem kupferhaltigen Katalysator in einem heterogenen Reaktor durchgeführt wird.
Laut Lummus entstehen bei der Reaktion keine Teere oder nichtflüchtigen Rückstände, was wahrscheinlich auf die schnelle Entfernung von Phenol aus der Reaktionszone zurückzuführen ist.
1.3. Phenol aus Kohle
Die Gewinnung von „natürlichem“ Phenol aus Kohle ist seit langem ein kommerzielles Verfahren zur Herstellung von Phenol und wird immer noch praktiziert. Allerdings ist dieses Verfahren als Phenolquelle heutzutage unbedeutend geworden.
Phenol sowie viele andere aromatische Verbindungen werden aus den Dämpfen der Kohleverkokung gewonnen, wobei Kohle unter Luftabschluss in einem Koksofen Temperaturen über 900 °C ausgesetzt wird, wobei Koks als fester Rückstand und kondensierbare Kohlenwasserstoffe und Gase zurückbleiben als Dämpfe.
Die Dämpfe werden zu Kohlenteer kondensiert, der mit wässriger Schwefelsäure oder Phosphorsäure zur Rückgewinnung von Ammoniak oder mit einem Waschöl zur Entfernung von Benzol gewaschen werden kann. Das verbleibende Gas wird vor Ort als Brennstoff genutzt und besteht aus Wasserstoff und Methan.
Zur Weiterverarbeitung des Steinkohlenteers wird eine kontinuierliche Destillation eingesetzt. In der ersten Kolonne wird Leichtöl, das Benzol, Toluol und Xylole enthält, zusammen mit Wasser abgetrennt. In der zweiten Kolonne wird Karbolöl, das Phenol und phenolische Verbindungen enthält, als Kopfprodukt abgetrennt und Naphthalinöl als Nebenprodukt entnommen.
Das Sumpfprodukt der zweiten Kolonne wird weiter fraktioniert, um Waschöl für die Benzolrückgewinnung aus dem Abgas, Methylnaphthalinöl, Anthracenöl und Pech zu erzeugen. Hohe Rückflussverhältnisse und ein hoher Grad an thermischer Integration werden mit Bodenkolonnen oder Kolonnen mit Füllkörperpackungen genutzt.
Das Karbolöl, das etwa 2–3 % des Kohlenteers ausmacht und etwa 30–35 % phenolische Verbindungen wie Phenol und Kresole enthält, wird in einer Extraktionsanlage mit 8–9 % Natronlauge behandelt. Phenol und Kresole, sogenannte Teersäuren, werden als Salze in die wässrige Phase extrahiert. Die rohe Phenolatlauge wird dampfdestilliert, um restliche Kohlenwasserstoffe und Pyridinbasen abzutrennen.
Anschließend wird die Phenolatlauge mit Kohlendioxid behandelt, um die Säureteere in der Kolonne von ihren Salzen zu befreien. Die Natriumcarbonat enthaltende wässrige Phase wird weiter behandelt, um gelöstes Phenol zu entfernen.
Die organische Phase wird in reines Phenol (Siedepunkt 181,8 °C), o-Kresol (Siedepunkt 191,0 °C), eine Mischung aus m- und p-Kresolen (Siedepunkt 202,0 – 203,0 °C) und eine Xylenolfraktion (Siedepunkt höher) fraktioniert bis 210 °C) durch diskontinuierliche Destillation.
2. Chemische Reaktionen von Phenol
Die chemischen Eigenschaften von Phenol sind durch die gegenseitige Beeinflussung der Hydroxylgruppe und des aromatischen Rings gekennzeichnet.
2.1. Reaktionen unter Beteiligung der O-H-Bindung
Im Gegensatz zu aliphatischen Alkoholen ist Phenol eine schwache Säure und bildet mit starken Basen lösliche Salze, was für die Rückgewinnung aus organischen Lösungsmitteln wie Kohlenteer nützlich ist. Sein pKa-Wert in wässriger Lösung beträgt 10,0. Das Phenolatanion wird durch das aromatische Ringsystem stabilisiert.
Phenol kann durch Behandlung mit Kohlendioxid bereits bei Raumtemperatur aus seinen Salzen freigesetzt werden. Nahe seinem Siedepunkt kann Phenol Carbonsäuren aus ihren Salzen verdrängen und Phenolate bilden.
Die Hydroxylgruppe kann leicht verestert (z. B. zu Phenylacetat) oder verethert (z. B. Diphenylether) werden.
2.2. Reaktionen des aromatischen Rings
Das Elektronenpaar im Phenol ist über den aromatischen Ring delokalisiert, was zu dessen Azidität führt. Die überschüssigen Elektronen in den ortho- und para-Positionen machen Phenol sehr anfällig für elektrophile Substitution. Beispielsweise reagiert Brom in wässriger Lösung mit Phenol und erzeugt in hoher Ausbeute 2,4,6-Tribromphenol.
Die Kolbe-Reaktion ist eine weitere wichtige Reaktion, bei der Kohlendioxid mit Natriumphenolat bei 125 °C zu Natriumsalicylat gekoppelt wird. Bei 125 °C substituiert Kohlendioxid in der ortho-Position, während bei Temperaturen über 250 °C das para-Isomer bevorzugt wird.
Andere Reaktionen nach der elektrophilen Substitution umfassen Chlorierung, Sulfonierung und Nitrierung.
2.3. Flüssigphasenoxidation
Bei der Oxidation organischer Substanzen durch molekularen Sauerstoff entstehen verschiedene Zwischenprodukte, beispielsweise Cumolhydroperoxid. Diese Prozesse folgen einem komplexen radikalischen Mechanismus.
Phenol kann solche Reaktionen hemmen, indem es mit freien Radikalen unter Bildung von Phenoxyradikalen reagiert, die relativ stabil sind und den Kettenmechanismus nicht fortsetzen. Daher muss jeglicher Eintrag von Phenol in Oxidationsprozesse vermieden werden.
3. Verwendung von Phenol
Die weltweite Produktionskapazität von Phenol übersteigt 9 Millionen Tonnen. Bisphenol A, ein Hauptderivat von Phenol, macht etwa 37 % der weltweiten Produktion aus.
Bisphenol A wird häufig bei der Herstellung hochwertiger Polycarbonate für Automobilanwendungen, CDs und Verglasungen sowie bei der Herstellung von Epoxidharzen verwendet.
Die zweitgrößte Anwendung von Phenol ist die Herstellung von Phenolharzen mit Formaldehyd. Diese Harze werden hauptsächlich für Unterbodenschutzanwendungen in der Automobilindustrie verwendet.
Darüber hinaus wird Phenol für die Synthese von Caprolactam über die Cyclohexanol–Cyclohexanon-Route eingesetzt.
Es werden mehrere andere Phenolderivate hergestellt, darunter Alkylphenole, Diphenole, Anilin und Salicylsäure.
Da der Automobilsektor ein bedeutender Abnehmer von Phenolderivaten wie Polycarbonaten und Phenolharzen ist, ist die Nachfrage nach Phenol immer noch weitgehend an diesen Markt gebunden, der tendenziell zyklisch ist.
Referenz
- Phenol; Ullmann’s Encyclopedia of Industrial Chemistry. – https://onlinelibrary.wiley.com/doi/10.1002/14356007.a19_299.pub3