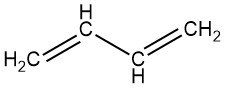
1,3-Butadien ist ein farbloses Gas mit einem benzinähnlichen Geruch. Es ist das einfachste Mitglied der Reihe konjugierter Diene, die die Struktur C=C-C=C enthalten, wobei C Kohlenstoff ist.
Butadien bezieht sich typischerweise auf 1,3-Butadien (106-99-0), einen hochbedeutsamen ungesättigten C4-Kohlenwasserstoff. Sein thermodynamisch weniger stabiles Gegenstück, 1,2-Butadien (590-19-2), hat eine vernachlässigbare industrielle Relevanz.
1,3-Butadien: CH2=CH–CH=CH2
1,2-Butadien: CH2=C=CH–CH3
Butadien gilt als wichtige Petrochemikalie mit einer weltweiten Produktion von über 10 Millionen Tonnen pro Jahr.
Inhaltsverzeichnis
1. Physikalische Eigenschaften von Butadien
Butadien ist unter normalen Bedingungen ein farbloses Gas. Einige physikalische Eigenschaften sind in der folgenden Tabelle zusammengefasst:
Eigenschaft | Wert |
---|---|
Siedepunkt bei 101,3 kPa | -4,4 °C |
Schmelzpunkt bei 101,3 kPa | -108,9 °C |
Kritische Temperatur | 425 K |
Kritischer Druck | 4,32 MPa |
Kritisches Molvolumen | 221 cm³/mol |
Dichte (Flüssigkeit, 0 °C) | 0,646 g/cm³ |
Dichte (flüssig, 25 °C) | 0,616 g/cm³ |
Dichte (flüssig, 50 °C) | 0,582 g/cm³ |
Gasdichte (relativ zu Luft) | 1,87 |
Dampfdruck (-4,4°C) | 101,3 kPa |
Dampfdruck (0 °C) | 120,0 kPa |
Dampfdruck (25 °C) | 273,6 kPa |
Dampfdruck (50 °C) | 537,9 kPa |
Dampfdruck (75 °C) | 986,7 kPa |
Dampfdruck (100 °C) | 1733 kPa |
Viskosität (flüssig, 0 °C) | 0,25 mPa·s |
Viskosität (flüssig, 50 °C) | 0,20 mPa·s |
Verdampfungsenthalpie (25 °C) | 20,86 kJ/mol |
Verdampfungsenthalpie (-4,4 °C) | 22,47 kJ/mol |
Bildungsenthalpie (gasförmig, 298 K, 101,3 kPa) | 110,0 kJ/mol |
Freie Bildungsenthalpie (gasförmig, 298 K, 101,3 kPa) | 151,5 kJ/mol |
Verbrennungsenthalpie (gasförmig, 298 K, 101,3 kPa) | 2541,5 kJ/mol |
Hydrierungsenthalpie zu Butan (gasförmig, 298 K, 101,3 kPa) | 235,7 kJ/mol |
Bildungsentropie (Flüssigkeit, 298 K, 101,3 kPa) | 199,0 J·mol⁻¹·K⁻¹ |
Schmelzenthalpie (164,2 K, 101,3 kPa) | 7,988 kJ/mol |
Butadien ist in Wasser nur begrenzt löslich. Es ist in Methanol und Ethanol löslich. und in hochsiedenden polaren Lösungsmitteln wie Methylpyrrolidon gut löslich.
Mehrere technische Eigenschaften sind entscheidend für den sicheren Umgang mit Butadien. Dazu gehören:
- Flammpunkt: -85 °C
- Zündtemperatur: 415 °C
Unstabilisiertes oder unzureichend stabilisiertes Butadien kann mit Luftsauerstoff unter Bildung explosiver Peroxide reagieren.
2. Chemische Eigenschaften von Butadien
Butadien, das über zwei konjugierte Doppelbindungen verfügt, nimmt an verschiedenen Reaktionen teil, darunter 1,2- und 1,4-Additionen mit sich selbst (Polymerisation) und anderen Reagenzien, linearer Dimerisierung, Trimerisierung und Ringbildung.
Polymerisation:
Die bedeutendste Reaktion für Butadien ist die Polymerisation durch 1,2- und 1,4-Addition, die zu einer Vielzahl von Polymeren führt. Die Art dieser Polymere hängt von den Herstellungsmethoden und dem verwendeten Katalysatorsystem ab und führt zu industriell wichtigen synthetischen Kautschuken und Polymerharzen.
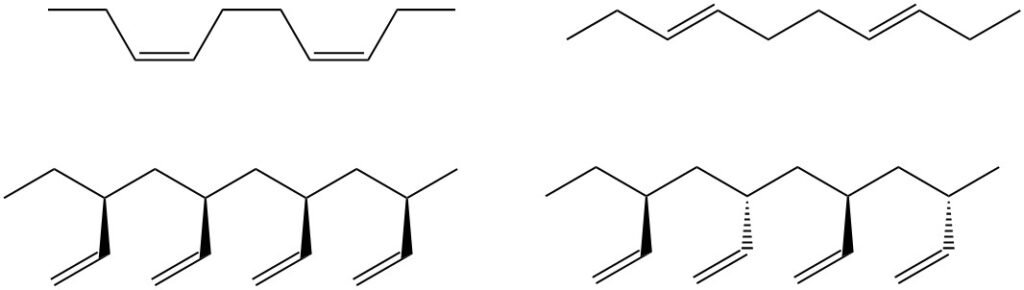
Andere Additionsreaktionen:
Butadien unterliegt einer 1,2- oder 1,4-Addition mit verschiedenen Reagenzien, wobei die Anteile der Additionsprodukte von den Reaktionsbedingungen abhängen. Diese Additionsprodukte dienen als entscheidende Zwischenprodukte bei der Herstellung von Stoffen wie Chloropren und Hexamethylendiamin.
Spezifische Reaktionen:
1. Chlorierung (Chloropren-Herstellung): In einem typischen Beispiel einer elektrophilen Addition reagiert Butadien mit Chlor zu Chloropren (1), einer Verbindung mit vielfältigen industriellen Anwendungen.
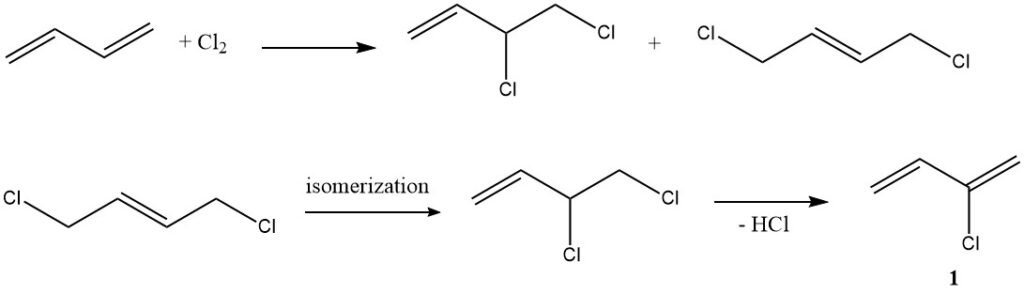
2. Hydrocyanierung (Adiponitril-Herstellung): Unter Verwendung eines von Du Pont entwickelten dreistufigen Prozesses wird Butadien einer Hydrocyanierung unterzogen, um eine Mischung aus isomeren linearen und verzweigten Pentennitrilen zu bilden. Anschließende Isomerisierung und weitere Hydrocyanierung führen zu Adiponitril (2).
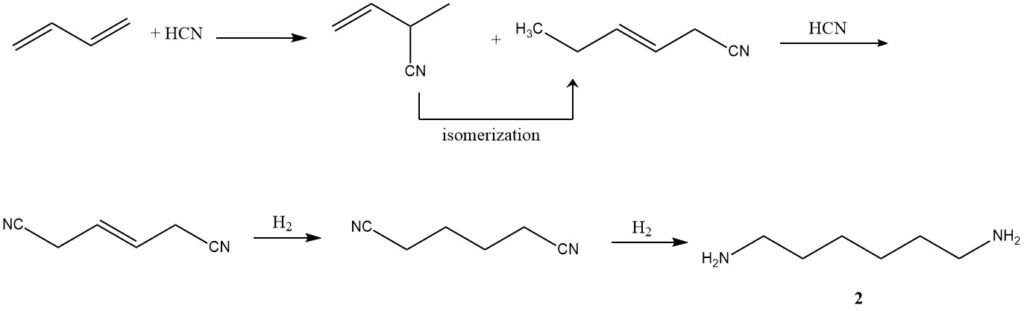
3. Carboalkoxylierung (ε-Caprolactam-Produktion): DSM und Du Pont haben ein alternatives Verfahren zur ε-Caprolactam-Produktion aus Butadien untersucht. Dieser mehrstufige Prozess umfasst Carboalkoxylierung, Hydroformylierung und reduktive Aminierung. Obwohl es noch nicht im industriellen Maßstab umgesetzt wurde, stellt es einen vielversprechenden Weg für die zukünftige Entwicklung dar.
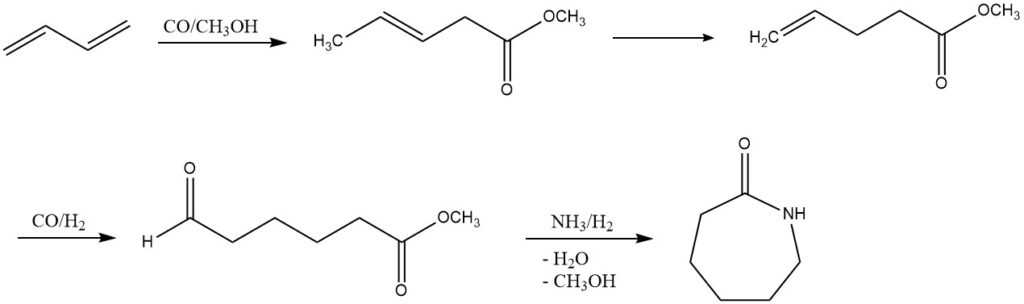
4. Acetoxylierung (1,4-Butandiol- oder Tetrahydrofuran-Herstellung): Durch Acetoxylierung führt Butadien zur Synthese von 1,4-Diacetoxy-2-buten, das in einem mehrstufigen Mitsubishi-Prozess in 1,4-Butandiol oder Tetrahydrofuran. Diese Prozesse unter dem Einfluss spezifischer Katalysatoren zeigen das Potenzial für vielfältige chemische Umwandlungen.
5. Andere Oxidationsreaktionen: Innovative Verfahren wie das Toyo-Soda-Verfahren und die Direktoxidation mit Luft oder Sauerstoff stellen wirtschaftliche Methoden zur Herstellung verschiedener C4-Derivate dar. Die Einführung von 3,4-Epoxy-1-buten durch Oxidation eröffnet Möglichkeiten für die Herstellung wertvoller chemischer Zwischenprodukte.
6. Diels-Alder-Reaktion: Eine der bekanntesten Reaktionen von Butadien, die Diels-Alder-Reaktion, spielt eine entscheidende Rolle in industriellen Prozessen zur Herstellung von Styrol. Die Dimerisierung von Butadien und die anschließende Umwandlung in Styrol unterstreichen die Vielseitigkeit dieser Reaktion bei der Synthese wertvoller chemischer Verbindungen.

7. Cyclodimerisierung, Cyclotrimerisierung: Zwei Moleküle Butadien können cyclodimerisiert werden, um 1,5-Cyclooctadien zu erzeugen, während drei Moleküle zu 1,5,9-Cyclododecatrien führen. Diese zyklischen Verbindungen dienen, unterstützt durch spezielle Katalysatoren, als Zwischenprodukte bei der Herstellung höherer Polyamide.
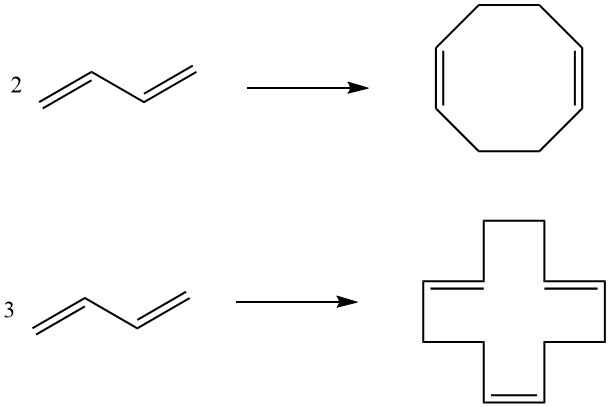
8. 1,4-Cycloaddition: Die reversible 1,4-Addition von Butadien mit Schwefeldioxid führt zur Bildung des cyclischen Sulfons 2,5-Dihydrothiophen-1,1-dioxid, das weiter in Sulfolan umgewandelt wird. Dieses Verfahren demonstriert die Anpassungsfähigkeit von Butadien bei der Synthese hochpolarer Lösungsmittel.

9. Lineare Dimerisierung und Trimerisierung; Telomerisierung: Unter dem Einfluss von Ni-, Co-, Pd- oder Fe-Katalysatoren erfährt Butadien eine lineare Dimerisierung oder Trimerisierung. Die resultierenden linearen Oligomere, getrennt nach Kettenlänge, bieten vielfältige Verbindungen, wie beispielsweise 1,3,7-Octatrien.
Bei der Telomerisierungsreaktion handelt es sich um die Di- und Oligomerisierung eines 1,3-Diens unter Zugabe einer nukleophilen Verbindung. Es wird durch Pd, Ni oder Pt katalysiert und liefert je nach verwendetem Nukleophil ein breites Spektrum an Produkten.
10. Hydrierung: Die selektive Hydrierung von Butadien erzeugt 1-Buten oder 2-Buten, und eine sorgfältige Anpassung der Reaktionsbedingungen gewährleistet eine ausreichende Umwandlung ohne Überhydrierung zu n-Butan. Kommerzielle Prozesse von Unternehmen wie Axens, UOP und Lummus bieten maßgeschneiderte Ansätze zur Maximierung der Ausbeute spezifischer Buten-Isomere.
11. Bildung von Komplexen: Butadien bildet Komplexe mit verschiedenen Metallverbindungen, wie zum Beispiel Cu(I)-Salzen. Obwohl es früher bei der Extraktion von Butadien eingesetzt wurde, haben moderne extraktive Destillationstechniken diese Methode weitgehend ersetzt.
Komplexe mit anderen Übergangsmetallen wie Fe, Ni, Co, Pd und Pt sind gut etabliert und tragen zu mechanistischen Studien in der Alpha-Olefin-Polymerisationskatalyse bei.
3. Herstellung von Butadien
Historisch gesehen gab es verschiedene Methoden zur Butadienproduktion. Heute gibt es noch vier Hauptpfade:
- Naphtha-Cracken: Dieser vorherrschende Weg fängt Butadien als Nebenprodukt der Ethylenproduktion ein.
- Butan/Buten-Dehydrierung: Dieser Prozess spielt je nach Rohstoff- und Butadienpreisen eine untergeordnete, kampagnenbasierte Rolle.
- Ethanolproduktion: Diese Methode hat an Bedeutung verloren.
- Acetylenproduktion: Dieser Weg ist kommerziell nicht mehr realisierbar.
Neue biobasierte Ansätze werden derzeit erforscht.
Die Wirtschaftlichkeit der Butadienproduktion wird stark von der gekoppelten Produktion von Ethylen und Propylen beeinflusst. Wenn diese C2- und C3-Olefine kostengünstig sind, wird die gezielte Butadienproduktion aus Butenen und Butan attraktiver.
3.1. Herstellung aus Acetylen
In der Vergangenheit wurden zwei Wege genutzt, um Butadien aus Acetylen herzustellen. Beide sind mittlerweile veraltet, da die Acetylenproduktion energieintensiv und teuer ist. Nur die ersten Schritte des Reppe-Prozesses, die zu 1,4-Butandiol und Tetrahydrofuran führen, bleiben kommerziell relevant.
3.2. Herstellung aus Ethanol
Das später von LEBEDEW modifizierte IPATJEW- und OSTROMISLENSKY-Verfahren diente während des Zweiten Weltkriegs einst als wichtige Butadienquelle, insbesondere in Deutschland und Osteuropa. Dieser Vorgang wird durch die Reaktion veranschaulicht:
2 CH3CH2OH → CH2=CHCH=CH 2 + 2 H2O + H2
und bei Temperaturen im Bereich von 370 bis 450 °C unter Verwendung von MgO – SiO2 oder SiO2 – betrieben. Mit Al2O3-Katalysatoren werden Selektivitäten von bis zu 70 % erreicht.
Obwohl es für die Produktion im großen Maßstab nicht mehr konkurrenzfähig ist, könnte es in Regionen mit billigem Ethanol oder überschüssigem Agraralkohol immer noch realisierbar sein.
3.3. Dehydrierung von Butan und Butenen
Die Dehydrierung von Butan und Butenen zur Herstellung von Butadien stellt aufgrund seiner endothermen Natur einzigartige Herausforderungen dar. Um die Ausbeute und Selektivität zu maximieren, müssen mehrere wichtige Überlegungen berücksichtigt werden:
Le Chateliers Prinzip: Durch die Senkung des Partialdrucks der gewünschten Produkte Butadien und Wasserstoff wird die Reaktion vorangetrieben. Dies kann durch Vakuumbetrieb oder durch Zugabe von Dampf zur Reaktionsmischung erreicht werden.
Vorteile von Steam:
- Dampf hilft, die Desaktivierung des Katalysators zu mildern, indem er die Koksbildung auf der Katalysatoroberfläche verhindert.
- Die endotherme Natur der Dehydrierungsreaktion erfordert eine externe Wärmezufuhr. Dampf kondensiert leicht und setzt erhebliche Wärme frei, um die Reaktion voranzutreiben.
- Der kondensierte Dampf kann leicht vom Produktstrom abgetrennt werden, wodurch eine minimale Kontamination gewährleistet wird.
Während höhere Temperaturen die Butadienbildung begünstigen, erhöhen sie auch das Risiko unerwünschter Nebenreaktionen wie Cracken, Isomerisierung und Polymerisation. Es ist entscheidend, das optimale Temperaturgleichgewicht zwischen Ausbeute und Selektivität zu finden.
Verbindungen, die für die oben genannten Nebenreaktionen anfällig sind, werden vor dem Dehydrierungsprozess entfernt, um ihren Einfluss zu minimieren.
Da die Dehydrierungsreaktion nicht vollständig abläuft, muss der Produktstrom getrennt werden, um Butadien zu isolieren. Nicht umgesetzte Ausgangsmaterialien werden zur Maximierung der Effizienz wieder in den Prozess zurückgeführt.
Durch die sorgfältige Steuerung dieser Aspekte kann die Dehydrierung von Butan und Butenen für eine effiziente und selektive Butadienproduktion optimiert werden.
3.3.1. Dehydrierung von n-Butan
Es gibt zwei bekannte Methoden zur Dehydrierung von n-Butan zu Butadien:
1. Houdry-Catadien-Prozess:
Dieses etablierte einstufige Verfahren wird seit 1943 kommerziell betrieben. Mehrere parallel angeordnete Festbettreaktoren werden im Kreislauf zwischen Reaktions- und Regenerationsphase geschaltet. Ein Aluminiumoxidkatalysator mit 20 % Chromoxid ermöglicht die Dehydrierung von reinem n-Butan oder seiner Mischung mit n-Butenen bei 550–650 °C und 10–25 kPa.
Hohe Temperaturen begünstigen die Butadienproduktion, erzeugen aber auch unerwünschte Nebenprodukte wie C1-C3-Kohlenwasserstoffe, Wasserstoff und den Katalysator verschmutzenden Koks.
Nach jedem Reaktionszyklus (5–15 Minuten) wird der Reaktor regeneriert: Durch die Verbrennung der Koksablagerung wird im Katalysator und im Inertmaterial gespeicherte Wärme für die nächste Reaktionsphase freigesetzt.
Dieser Prozess führt zu einer Butadienkonzentration von 15–18 % am Reaktorausgang. Nachfolgende Rückgewinnungsschritte, einschließlich Abschrecken, Komprimieren, Strippen und Trennen, erhöhen die Butadienkonzentration auf 30–50 %. Aus 1000 Tonnen n-Butan werden etwa 550 Tonnen Butadien gewonnen. Reines Butadien kann durch Extraktivdestillation isoliert werden.
2. Phillips Petroleum-Prozess:
Dieses zweistufige Verfahren bietet Vorteile wie eine längere Katalysatorlebensdauer und höhere Butadienausbeuten.
- Dehydrierung zu Buten: n-Butan wird bei 600°C und 1 bar auf einer Cr2O3– katalytischen Dehydrierung zu Buten dehydriert. Na2O-Al2O3-Katalysator.
- Buten-Abtrennung: n-Butene werden mit Hilfsstoffen wie Aceton, Acetonitril oder Furfural extrahiert.
- Butadienbildung: Abgetrennte n-Butene werden in einem isothermen Rohrreaktor zu Butadien dehydriert. Der Reaktor wird durch Rauchgas auf 600 °C erhitzt und arbeitet bei 1 bar Druck mit Heißdampfzugabe über einem Fe2O3-K2O-Al2O3-Katalysator.
- Butadien-Rückgewinnung und -Reinigung: Durch extraktive Destillation mit den oben genannten Hilfsmitteln wird Butadien zurückgewonnen und gereinigt.
Das Phillips-Verfahren zeichnet sich durch längere Laufzeiten (keine Katalysatorregeneration) und eine Butadienausbeute von 65 % basierend auf n-Butan aus, was seine Effizienz und verbesserte Selektivität im Vergleich zum Houdry-Catadiene-Verfahren unter Beweis stellt.
3.3.2. Dehydrierung von n-Butenen
n-Butene, die häufig in gekracktem Benzin, der Olefinproduktion und der LPG-Dehydrierung vorkommen, sind häufig als Teil eines C4-Kohlenwasserstoffgemisches vorhanden.
Während C4-Paraffine durch extraktive Destillation (wie bei der Butadienrückgewinnung) von C4-Olefinen getrennt werden können, stellt die Trennung von Isobuten und n-Buten aufgrund ihrer nahe beieinander liegenden Siedepunkte eine besondere Herausforderung dar.
Mehrere Methoden beseitigen diese Trennungshürde:
1. BASF-Verfahren: Verwendet 40–45 % H2SO4, um Isobuten selektiv in tert-Butanol umzuwandeln, was eine einfachere Trennung ermöglicht.
2. Isobuten kann zur weiteren Verarbeitung und Trennung in Methyl-tert-butylether oder Isobuten-Oligomere umgewandelt werden.
3. Destillation mit Hydroisomerisierung: Verfahren wie Isopure von Axens und CD DeIB von CD-Tech kombinieren Destillation mit Hydroisomerisierung von 1-Buten zu 2-Buten. Da 2-Buten einen anderen Siedepunkt als Isobuten aufweist, ist eine Destillation möglich.
4. Dow-Prozess: Verwendet die Dehydrierung von n-Butenen mit Wasserdampf über einem Ca/Ni-Phosphatkatalysator, der mit Cr2O3 stabilisiert ist. Überhitzter Dampf liefert die nötige Wärme für die Reaktion und erreicht eine Butenumwandlung von 50 % und eine Butadienselektivität von bis zu 90 %.
5. Parallelreaktor-Ansatz: Da der Dow-Prozess eine Katalysatorregeneration nach 15 Minuten erfordert, werden Parallelreaktoren eingesetzt, die einen kontinuierlichen Betrieb ermöglichen.
Ähnliche Verfahren wurden auch von Shell und Phillips Petroleum entwickelt und zeigen die vielfältigen Ansätze zur n-Buten-Dehydrierung und Butadienproduktion.
3.3.3. Oxidative Dehydrierung von n-Butenen
Die oxidative Dehydrierung (ODH) bietet mehrere Vorteile gegenüber herkömmlichen Dehydrierungsverfahren für die Butadienproduktion. Durch die Entfernung von Wasserstoff aus dem Gleichgewicht durch Oxidation verbessert ODH die Umwandlung und Selektivität erheblich:
2 C4H8 + O2 → 2 C4H6 + 2 H2O
Diese exotherme Reaktion liefert Wärme für die endotherme Dehydrierung, wodurch der Energiebedarf weiter gesenkt wird. Darüber hinaus trägt die Anwesenheit von Sauerstoff und Dampf dazu bei, die Verkokung des Katalysators zu minimieren.
Historische ODH-Prozesse:
- Oxo-D-Verfahren (Petro-Tex): Dieses seit 1965 angewandte Verfahren nutzt einen Ferritkatalysator und arbeitet unter mildem Druck. Zu den Vorteilen gehören ein geringer Dampf- und Heizenergieverbrauch, eine hohe Umwandlung/Selektivität, eine lange Katalysatorlebensdauer und keine Regenerationserfordernis.
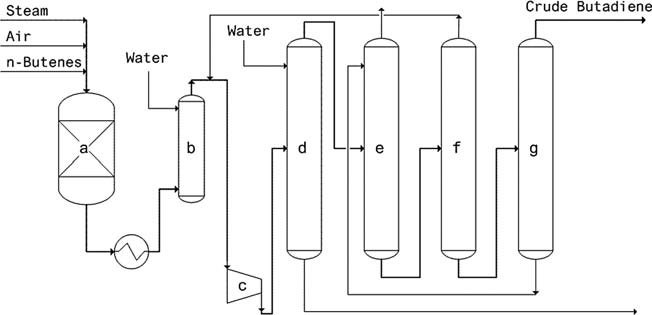
- O-X-D-Prozess (Phillips): Dieser seit 1976 in Betrieb befindliche Prozess verwendet einen Li-Sn-P-O-Katalysator und erreicht eine Butenumwandlung von 75–80 % mit einer Butadienselektivität von 88–92 %.
Neuere Entwicklungen in ODH:
- Nippon-Zeon-Prozess: Dieser Prozess verwendet eine Mischung aus n-Buten/Butan und Luft/Abgas als Beschickung und bietet Flexibilität bei der Beschickungszusammensetzung. Ein Mischmetalloxidkatalysator erreicht eine Butadienausbeute von 85 %, bezogen auf die Butene.
- Chemischer Prozess von Mitsubishi: Dieser Prozess nutzt einen Mo/Bi/Co-Katalysator und wandelt eine C4-Mischung, die 70 % n-Buten enthält, mit Luft, Dampf und Stickstoff um. Die Zugabe von Stickstoff ermöglicht ein hohes Sauerstoff/Butan-Verhältnis und minimiert so die Verkokung. Die Butadienumwandlung übersteigt 80 % bei einer Selektivität von über 90 %.
- Andere Entwicklungen: Asahi Kasai und Mitsui Chemicals haben ebenfalls ODH-Prozesse mit vielversprechenden Ergebnissen entwickelt, darunter Wirbelschichtreaktoren und Strategien zur Umwandlung von Ethylen in Butadien.
Allgemeine Vorteile von ODH:
- Höhere Umwandlung und Selektivität im Vergleich zu herkömmlichen Dehydrierungsprozessen.
- Reduzierter Energiebedarf aufgrund der exothermen Oxidationsreaktion.
- Reduziert die Verkokung des Katalysators.
- Potenzial für die Verwendung gemischter C4-Ströme als Ausgangsmaterial.
Einschränkungen:
- ODH-Prozesse sind im Allgemeinen komplexer als herkömmliche Dehydrierung.
- Die erforderlichen hohen Temperaturen können bei der Verwendung von Sauerstoff mit Butan zur Bildung unerwünschter Nebenprodukte führen
3.4. Isolierung von Butadien aus C4-Steam-Cracker-Fraktionen
Butadien wird hauptsächlich aus C4-Fraktionen isoliert, die beim Dampfcracken von Kohlenwasserstoffen entstehen. Die Wahl des Ausgangsmaterials, wie beispielsweise Naphtha in Westeuropa und LPG in den Vereinigten Staaten, spielt eine wichtige Rolle im Prozess, während der Crackgrad in erster Linie die Zusammensetzung der C4-Fraktion beeinflusst.
Die Abtrennung von Butadien aus dieser Mischung stellt aufgrund seines azeotropen Verhaltens mit Butan eine Herausforderung dar. Daher sind spezielle Techniken erforderlich.
Das Kupfer-Ammoniumacetat-Verfahren nutzt seine Fähigkeit, mit Butadien einen Komplex zu bilden, und löst dieses Problem bei Fraktionen mit niedrigem Butadien- und C4-Acetylengehalt. Höhere Acetylengehalte erfordern jedoch eine Vorbehandlung mittels selektiver Hydrierung.
Die extraktive Destillation erweist sich als bevorzugte Methode zur Butadien-Isolierung. Diese Technik nutzt die unterschiedlichen Affinitäten verschiedener Komponenten gegenüber bestimmten organischen Lösungsmitteln basierend auf ihrem Ungesättigtheitsgrad.
Beliebte Lösungsmittel sind Acetonitril (von Shell/KBR und LyondellBasell), N-Methylpyrrolidon (von BASF), Dimethylformamid (von Nippon Zeon Chemicals) und Furfural (von ConocoPhillips)).
Diese Prozesse, die einen oder zwei extraktive Destillationsschritte in Verbindung mit konventioneller Destillation umfassen, trennen Butadien und andere hochaffine Komponenten von weniger löslichen Butanen und Butenen. Weitere Reinigungsschritte entfernen verbleibende Verunreinigungen, um Butadien-Reinheit zu erreichen.
Das BASF-Verfahren, das NMP als Lösungsmittel verwendet, zeichnet sich durch Korrosionsfreiheit und hohe Butadienausbeuten aus, während das Nippon-Zeon-DMF-Verfahren ähnliche Vorteile aufweist.
Zu den jüngsten Fortschritten in diesem Bereich gehören die Trennwandtechnologie, die Kombination zweier Destillationsschritte in einer Einheit zur Steigerung der Effizienz sowie verbesserte Destillationsinterna und Prozesssteuerung zur Steigerung der Kapazität und Leistung bestehender Einheiten.
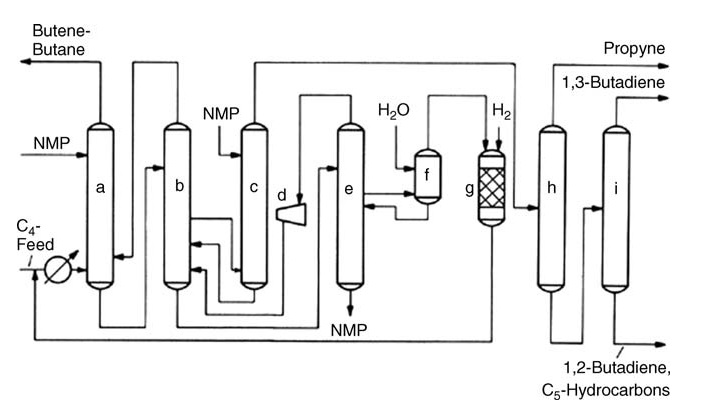
a) Hauptwäscher; b) Gleichrichter; c) Nach der Waschmaschine; d) Radialkompressor; e) Entgasungsturm; f) Wasserwäscher; g) Hydrierungsreaktor; h) Erste Destillation; i) Zweite Destillation
Alternative Ansätze wie die selektive Hydrierung von C4-Acetylenen bieten verschiedene Vorteile. Das KLP-Verfahren von UOP entfernt Acetylene vor der Extraktion, was den Prozess vereinfacht und die Butadienausbeute erhöht. Der CDHYDRO-Prozess von CDTECH bietet Flexibilität, indem er unterschiedliche Grade der Acetylenumwandlung ermöglicht und so den Butadienverlust minimiert.
3.5. Butadien aus biobasierten Ressourcen
Der wachsende Trend zur Nutzung erneuerbarer Ressourcen für die petrochemische Produktion erstreckt sich auch auf Butadien. Obwohl es verschiedene Wege gibt, sind Wege mit Bioalkoholen die vielversprechendsten.
Bioethanolproduktion, etabliert durch Fermentierung von Zuckerrohr, Mais oder Lignozellulosehaltiges Material erreichte im Jahr 2011 weltweit 68 Millionen Tonnen. Bestehende Technologien können Bioethanol in Butadien umwandeln.
Obwohl es derzeit keine großtechnische Produktion von Biobutadien gibt, treibt das zunehmende Interesse von Biobutanol als Kraftstoffadditiv die laufende Prozessentwicklung voran. Dehydratisierung und Dehydrierung von Biobutanol zu n-Buten.
Ein weiterer möglicher Weg ist die Gasvergärung von Kohlenmonoxid, das aus der Vergasung organischer Stoffe oder Industrieabgasen gewonnen wird. Bei diesem bakteriellen Prozess entsteht 2,3-Butandiol, eine Vorstufe von Butadien. Allerdings steckt diese Technologie noch in den Kinderschuhen.
Derzeit ist die biobasierte Butadienproduktion im Vergleich zur petrochemischen Route wirtschaftlich nicht konkurrenzfähig. Allerdings könnten steigende Öl- und Erdgaspreise in Verbindung mit weiteren technologischen Fortschritten in Zukunft Biotransformationswege begünstigen.
4. Verwendung und wirtschaftliche Bedeutung von Butadien
Butadien wird hauptsächlich als Monomer oder Comonomer bei der Herstellung von Synthesekautschuk verwendet. Es trägt zu Styrol-Butadien-Kautschuk (SBR), Polybutadien-Kautschuk (BR), Acrylnitril-Butadien-Kautschuk (NBR) und Chloropren-Kautschuk (CR) bei.
Über die Kautschukproduktion hinaus spielt Butadien in mehreren Kunststoffen eine entscheidende Rolle. Es bildet das Rückgrat von schlagfestem Polystyrol, einem Zweiphasensystem aus Polystyrol und Polybutadien. Darüber hinaus trägt Butadien zu ABS-Polymeren bei, einer Mischung aus Acrylnitril, Butadien und Styrol sowie MBS-Copolymeren , als Modifikatoren für Polyvinylchlorid verwendet.
Darüber hinaus dient Butadien als Zwischenprodukt in verschiedenen chemischen Synthesen.
In den Vereinigten Staaten, Japan und Westeuropa ist die Automobilindustrie der Hauptabnehmer von Butadienkautschuk.
Die Butadienpreise erlebten Anfang der 1990er Jahre aufgrund des Überangebots aufgrund erhöhter Crackkapazitäten einen deutlichen Rückgang. Dies führte zur Hydrierung von Butadien und zur Verwendung als Cracker-Ausgangsmaterial.
Seit Ende der 1990er Jahre führte die steigende Nachfrage nach Gummiprodukten und Polymeren, insbesondere in Asien, zu einem exponentiellen Anstieg der Butadiennachfrage und einem stetigen Preisanstieg.
Die globale Wirtschaftsrezession im Jahr 2008 führte zu einem dramatischen Rückgang der Butadiennachfrage, gefolgt von einer Erholung. Die Butadienpreise übertrafen die Ethylenpreise, was selten vorkam, bis die Volatilität zu Spitzenwerten von über 2.000 Euro pro Tonne führte.
Diese Preisschwankungen sind auf die Einführung von Ethan-basierten Crackern im Nahen Osten und die Verlagerung von US-Crackern auf leichtere Gasrohstoffe zurückzuführen. Diese Änderungen führen trotz steigender weltweiter Nachfrage zu einer geringeren Butadienausbeute.
5. Toxikologie von Butadien
Exposition und Toxizität:
- Die berufsbedingte Exposition gegenüber Butadien ist in der Petrochemie, der Butadienreinigungs- und -verarbeitungsindustrie sowie bei der Herstellung von Gummi- und Kunststoffprodukten am höchsten.
- Butadien gelangt hauptsächlich durch Einatmen in den Körper, Hautkontakt kommt seltener vor.
- Eine außerberufliche Exposition kann in der Nähe von Punktquellen wie Bränden, Zigarettenrauch und Fahrzeugemissionen auftreten, allerdings in viel geringeren Mengen als in beruflichen Umgebungen.
Tierstudien:
- Butadien weist eine geringe akute Toxizität auf, wobei hohe Dosen eine Narkose verursachen, der Erregung und Hyperventilation vorausgehen.
- Wiederholte kurzfristige Exposition bei hohen Konzentrationen (4000-8000 ppm) führt bei Ratten zu Speichelfluss, hat jedoch keinen Einfluss auf Wachstum, Nahrungsaufnahme oder andere Parameter.
- Mäuse, die ähnlichen Konzentrationen ausgesetzt waren, zeigten im Vergleich zu Ratten ein geringeres Körpergewicht und eine erhöhte Sterblichkeit sowie eine höhere Empfindlichkeit gegenüber Butadien.
- Eine Langzeitexposition bei Ratten (bis zu 111 Wochen) führt bei der höchsten Konzentration (8000 ppm) zu vorübergehender Nasensekretion, Ataxie und früher Mortalität. Es erhöht auch das Lebergewicht und deutet auf die Möglichkeit einer Metaplasie in der Lunge und eine höhere Inzidenz einiger Tumoren hin.
- Mäuse, die 60–61 Wochen lang niedrigeren Konzentrationen (625–1250 ppm) ausgesetzt waren, zeigten toxische und proliferative Läsionen in der Nasenhöhle, Lebernekrose und Atrophie der Fortpflanzungsorgane . Bemerkenswert ist, dass sie verschiedene Tumoren, einschließlich bösartiger Erkrankungen, früher und häufiger entwickeln als Kontrollpersonen.
- Eine zweijährige Studie mit noch niedrigeren Konzentrationen (6,25-625 ppm) zeigt die frühe Entwicklung ausgedehnter Lymphome, ungewöhnlicher Herztumoren und Lungentumoren bei Mäusen.
Metabolismus und Mutagenität:
- Butadien wird in der Leber zu Epoxid-Zwischenprodukten metabolisiert, die vermutlich die Hauptursache für seine Toxizität und Karzinogenität sind.
- Die Bildung dieser Metaboliten ist bei Mäusen stärker ausgeprägt als bei Ratten und Menschen.
- Butadien zeigt im Ames-Test nur in Gegenwart von Enzymen Mutagenität, was auf die Bildung eines mutagenen Zwischenprodukts schließen lässt.
Menschendaten:
- Zu den Auswirkungen der Butadien-Exposition liegen nur begrenzte menschliche Daten vor.
- Freiwillige, die einer sehr hohen Konzentration (8000 ppm) ausgesetzt waren, erlebten vorübergehende Reizungen, verschwommenes Sehen und Atemwegsbeschwerden, es wurden jedoch keine kumulativen Auswirkungen beobachtet.
- Hämatologische Studien an Arbeitern, die durchschnittlich 20 ppm Butadien ausgesetzt waren, zeigten keine signifikanten Anomalien.
- Frühe Sterblichkeitsstudien an Arbeitern in der Styrol-Butadien-Kautschuk-Industrie deuteten nicht auf ein erhöhtes Krebsrisiko hin.
- Neueste Übersichten epidemiologischer Studien liefern Hinweise auf ein erhöhtes Risiko für hämatolymphatische Malignome, insbesondere Leukämie, bei erhöhter Butadien-Exposition.
Einstufung und Grenzwerte für die Exposition am Arbeitsplatz:
- Basierend auf Tier- und Humandaten wird Butadien von der Internationalen Agentur für Krebsforschung (IARC) als Karzinogen der Gruppe 1 eingestuft.
- Die Grenzwerte für die berufsbedingte Exposition variieren geringfügig zwischen verschiedenen Aufsichtsbehörden und liegen zwischen 0,5 und 4,4 mg/m3.
- Kontinuierliche Anstrengungen werden unternommen, um die Belastung an Arbeitsplätzen mit Butadien zu reduzieren.
Referenz
- Butadiene; Ullmann’s Encyclopedia of Industrial Chemistry. – https://onlinelibrary.wiley.com/doi/10.1002/14356007.a04_431.pub2