Die Friedel-Crafts-Alkylierung
Die Friedel-Crafts-Alkylierung aromatischer Verbindungen beinhaltet eine säurekatalysierte elektrophile Substitution, bei der eine Alkylgruppe einen aromatischen Wasserstoff ersetzt. Zu diesem Zweck werden üblicherweise verschiedene Alkylierungsmittel wie Olefine, Alkylhalogenide und Alkohole eingesetzt.
Diese Reaktion kann auf verschiedene aromatische Substrate angewendet werden, einschließlich heteroaromatischer Verbindungen und sogar Verbindungen wie Ferrocen. Diese Reaktionen sind typischerweise schnell und exotherm und werden oft unter milden Bedingungen in der flüssigen Phase durchgeführt.
In einigen Fällen werden jedoch für bestimmte Substrate Dampfphasenverfahren mit strengeren Bedingungen eingesetzt. Bei der Verwendung von Olefinen, Alkylhalogeniden und Alkoholen als Alkylierungsmittel laufen die Gesamtreaktionen wie folgt ab:
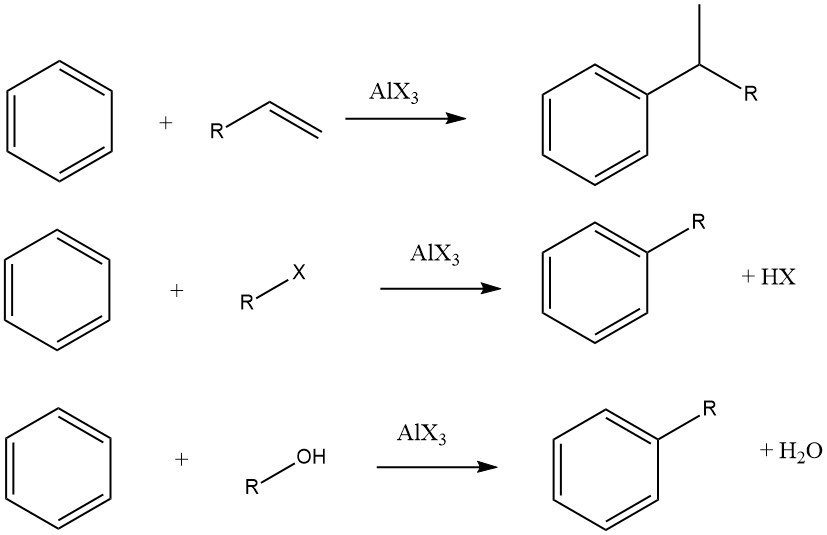
Inhaltsverzeichnis
Der Grad der Isomerisierung der Alkyleinheit und die Einhaltung der Markownikow-Regel während des Additionsprozesses variieren je nach Säuregehalt des Katalysators.
1.1. Katalysatoren für die Friedel-Crafts-Alkylierung
Die im Friedel-Crafts-Alkylierungsprozess verwendeten Katalysatoren sind sauer und ihre Wirksamkeit hängt von verschiedenen Faktoren ab, darunter Reaktionsbedingungen, Alkylierungsmittel und aromatische Substrate. Sowohl Lewis-Säuren als auch Brønsted-Säuren können als aktive Katalysatoren wirken, und häufig verwendete Katalysatoren werden anhand ihrer chemischen Struktur klassifiziert.
Gruppe | Beispiele | Art der Säure |
---|---|---|
Säurehalogenide | AlCl3, AlBr3, SnCl4, SbCl5, FeCl3 | Lewis-Säuren |
Metallalkyle und -alkoxide | AlR3, BR3, ZnR2, Al(OPh)3 | Lewis-Säuren |
Protonensäuren | HCl, HCl – AlCl3, H2SO4, HF, H3PO4 | Brønsted-Säure |
Säureoxide und Derivate | Zeolithe, Mischoxide und feste Supersäuren, Tone, Heteropolysäuren | Brønsted/Lewis-Säure |
Unterstützte Säuren | H3PO4 – SiO2, BF3 – Al2O3 | Brønsted/Lewis-Säure |
Kationenaustauscherharze | Permutit Q, Amberlite IR 112, Dowex 50, Nafion – Kieselsäure, Deloxan | Brønsted-Säure |
Traditionell werden häufig saure Halogenide wie AlCl3 oder AlBr3 und Protonensäuren wie HCl, HF oder H2SO4 auf Kieselgur als Träger verwendet. Aufgrund ihrer Umweltfreundlichkeit, einfachen Handhabung und geringeren Kostenauswirkungen bei der Prozessgestaltung zeichnet sich jedoch eine Verschiebung hin zur Substitution dieser Katalysatoren durch Zeolithe und anorganische Oxide ab.
Die Anwesenheit von Basen, insbesondere organischen Stickstoffverbindungen, verringert den Säuregehalt und die Effizienz des Katalysators. Selbst bei Konzentrationen von nur 20 ppm kann Sauerstoff zur Bildung schwerer harziger Materialien auf dem Katalysator führen. Diene wie Butadien in einer Butenbeschickung tragen ebenfalls zur Bildung harziger oder teerartiger Substanzen auf dem Katalysator bei.
Interessanterweise können Spuren von Feuchtigkeit oder anderen Protonenlieferanten die katalytische Aktivität insbesondere bei Lewis-Säuren steigern. Höhere Mengen dieser Verbindungen beeinträchtigen jedoch die Leistung des Katalysators.
In einigen Fällen werden absichtlich milde Katalysatorgifte wie organische Nitroverbindungen eingesetzt, um den Säuregehalt des Katalysators zu senken und Nebenreaktionen wie Isomerisierung zu verhindern. Diese organischen Nitroverbindungen bilden mit Lewis-Säuren stöchiometrische Komplexe, was zu saubereren Alkylierungsprozessen mit moderaten Ausbeuten führt.
Darüber hinaus wirken bestimmte Addukte wie BF3·OEt2 oder BF3·C6H5OH als milde Friedel-Crafts-Katalysatoren. Verunreinigungen in Katalysatoren, wie das Vorhandensein von Eisenchlorid in Aluminiumchlorid, können die Produktausbeute erheblich verringern und den Verlauf der durch Lewis-Säuren katalysierten Reaktion beeinflussen.
1.2. Isomerisierung der Alkylierungsmittel
Aufgrund der sauren Natur der Reaktionsbedingungen bei der Friedel-Crafts-Alkylierung unterliegen Alkylierungsreagenzien häufig Umlagerungen und neigen dazu, in das am stärksten verzweigte Isomer umgewandelt zu werden, das möglich ist. Dies zeigt sich an Reaktionen von Benzol mit Propylchlorid, wobei Isopropylbenzol das Hauptprodukt ist, und mit n-Butylchlorid, was zur Bildung von sek.-Butylbenzol führt.
In diesen Fällen wird die Isomerisierung des Alkylierungsmittels durch die Wanderung eines Wasserstoffatoms und nicht durch direkte Kohlenstoffumlagerungen eingeleitet. Die treibende Kraft hinter dieser Isomerisierung ist die Bildung des stabilsten Carbokations, das dem üblichen Trend folgt: primär < sekundär < tertiär.
Wenn beispielsweise Benzol mit langkettigen linearen 1-Olefinen alkyliert wird, führt die Reaktion nicht nur zur Bildung von 2-Alkylbenzol, sondern in den meisten Fällen auch zu einer zufälligen Verteilung des Phenylsubstituenten entlang der Alkylkette.
Dieser Effekt könnte auch auf die Isomerisierung der alkylierten Reaktionsprodukte zurückgeführt werden, da n-Butylbenzol in Gegenwart eines Friedel-Crafts-Katalysators wie AlCl3 in sek.-Butylbenzol umgewandelt wird.
Unter bestimmten Reaktionsbedingungen kann die Alkylierung von Benzol mit tertiären Alkylhalogeniden zur Bildung sekundärer Alkylbenzole statt tertiärer Alkylbenzole führen.

Beispielsweise entsteht bei der Alkylierung von Benzol mit 2-Chlor-2,3-dimethylbutan aufgrund der Isomerisierung des Primärprodukts tert-Hexylbenzol überwiegend 2,2-Dimethyl-3-phenylbutan. Die Isolierung des Primärprodukts tert-Hexylbenzol ist nur möglich, wenn weniger aktive Katalysatoren wie Eisenchlorid eingesetzt werden.
1.3. Reaktivität aromatischer Substrate
Die elektrophile Substitution aromatischer Verbindungen bei der Friedel-Crafts-Alkylierung wird durch das Vorhandensein von Substituenten am aromatischen Substrat beeinflusst. Elektronenschiebende Substituenten wie Alkyl, NR2 oder OR (wobei R eine Alkylgruppe ist) erhöhen die Reaktivität und bewirken, dass der neue Substituent vorzugsweise in die ortho- oder para-Position eindringt.
Als Ergebnis entsteht bei der Alkylierung von Benzol mit Olefinen monosubstituiertes Benzol. Dieses monosubstituierte Benzol reagiert jedoch schneller mit einem anderen Olefinmolekül als Benzol selbst, was zu einer komplexen Mischung aus mono- und polyalkylierten Benzolen führt.
Der Grad der Polysubstitution wird durch die Reaktionsbedingungen beeinflusst und durch sterische Hinderung durch sperrige Alkylgruppen verringert. Sperrige Olefine wie Cyclohexen oder lineare C6-C18-Olefine ermöglichen gute Ausbeuten der Monoalkylierung in Benzol.
Ethylen oder Propen können durch Recycling polyalkylierter Produkte und sorgfältige Wahl der Reaktionsbedingungen monoalkyliert werden, wie dies bei der industriellen Synthese von Ethylbenzol und Cumol der Fall ist.
Bei der Alkylierung einfach substituierter Benzole überwiegen zunächst ortho- und para-Isomere. Die anschließende Isomerisierung führt jedoch häufig zu einer Gleichgewichtsmischung, die reicher an Metaprodukt ist.
Ortho-Substitution wird nur dann bevorzugt, wenn sie sterisch gehindert ist. Beispielsweise entstehen bei der durch HF katalysierten Reaktion von Benzol und 4-Methylcyclohexen 75 % Monoalkylderivate und 25 % Dialkylderivate, wobei 75 % das Para-Isomer und nur 25 % das Meta-Isomer sind.
In ähnlicher Weise ergibt die Cumol-Alkylierung mit 2-Buten über BF3-H3PO4 91 % para-Produkt, und die Dialkylierung von Benzol mit Propen über Siliciumdioxid-Aluminiumoxid ergibt vorzugsweise p-Diisopropylbenzol, das für die Synthese von Terephthalsäure und Hydrochinon geeignet ist.
Der Ersatz von Benzol durch Halogenide deaktiviert die Reaktion. Phenole oder Phenylether reagieren bei der Alkylierung aufgrund der deutlich erhöhten Elektronendichte in ortho- und para-Position deutlich schneller als Benzol.
In mikroporösen Materialien hängen Reaktivitäten, Produktselektivitäten und Isomerpräferenzen weitgehend von der Art, Anzahl und Stärke der Säurezentren und der Geometrie der Zeolithporen ab. Die Alkylierung mit festen Katalysatoren erfordert im Allgemeinen höhere Temperaturen, mit Ausnahme sehr starker fester Säuren, wie z. B. fester Supersäuren.
1.4. Dealkylierung und Transalkylierung
Viele der zur Alkylierung aromatischer Verbindungen verwendeten Katalysatoren können insbesondere bei höheren Temperaturen auch die Rückreaktion der Alkylierung fördern. Wenn beispielsweise Alkylbenzole mit AlCl3 erhitzt werden, entstehen durch umgekehrte Alkylierung Mischungen aus Benzol und polyalkylierten Benzolen.
Die Neigung alkylaromatischer Verbindungen zur Disproportionierung hängt auch von der Struktur des Alkylsubstituenten ab, und zwar in der Reihenfolge: tert-C4H9 > iso-C3H7 > n-C3H7 > C2H5 > CH3.
Disproportionierung und Transalkylierung von Methylbenzolen erfolgen bei 300 – 450 °C in Gegenwart fester Säurekatalysatoren wie SiO2 – Al2O3, während Disproportionierung und Transalkylierung von Ethylbenzolen und Isopropylbenzolen unter 100 °C mit typischen Friedel-Crafts-Katalysatoren stattfinden.
Der intermolekulare Alkylgruppentransfer (Transalkylierung) wird in verschiedenen industriellen Prozessen genutzt. Beispielsweise reagiert bei der Synthese von Ethylbenzol das unerwünschte Dialkylierungsprodukt mit einem Überschuss an frischem Benzol, um eine hohe Umwandlung von Ethylen in Ethylbenzol zu erreichen.
In Gegenwart eines Überschusses an BF3 – HF führt die Disproportionierung von Monoalkylbenzolen überwiegend zum Meta-Isomer. Dies ist auf die hohe Stabilität des Komplexes [m-Et2C6H5]+[BF4]− zurückzuführen. Ein ähnlicher Komplextyp wird kommerziell zur selektiven Extraktion von m-Xylol aus Mischungen aromatischer C8-Verbindungen verwendet.
Das Gleichgewicht zwischen Alkylierungs- und Dealkylierungsreaktionen erklärt die Produktverteilung bei der Alkylierung substituierter aromatischer Verbindungen. Zunächst entstehen ortho- und para-Isomere, die mit kurzen Reaktionszeiten isoliert werden können (kinetische Kontrolle). Bei längeren Reaktionszeiten isomerisieren diese Isomere jedoch zu den stabileren Meta-Isomeren (thermodynamische Kontrolle).
Kommerziell werden Dealkylierungsverfahren verwendet, um Toluol in Benzol umzuwandeln, m-Xylol zu den gewünschten ortho- und para-Derivaten zu isomerisieren und Toluol zu Benzol und Xylolen zu disproportionieren. Diese Prozesse machen sich das Gleichgewichtsverhalten der alkylaromatischen Verbindung zunutze.
2. Alkylierung von Benzol
Die Alkylierung von Benzol findet drei wichtige kommerzielle Anwendungen:
1. Alkylierung mit Ethylen zur Herstellung von Ethylbenzol, das als Zwischenprodukt für die Styrolproduktion dient. Die weltweite Produktionskapazität für Ethylbenzol betrug 1991 etwa 20 Millionen Tonnen pro Jahr.
2. Alkylierung mit Propen zur Herstellung von Cumol, einem Zwischenprodukt für die Phenol produktion, mit Aceton als Nebenprodukt. Die weltweite Produktionskapazität für Cumol betrug 1992 rund 7,5 Millionen Tonnen pro Jahr.
3. Alkylierung mit langkettigen Olefinen mit 10 – 18 Kohlenstoffatomen zur Herstellung von Alkylbenzolen, die anschließend zu oberflächenaktiven Verbindungen sulfoniert werden. Die Produktionskapazität für lineare Alkylbenzolsulfonate (LAB) betrug 1992 etwa 180.000 Tonnen pro Jahr.
2.1. Alkylierung von Benzol mit Ethylen
Die Alkylierung von Benzol mit Ethylen führt zur Bildung von Ethylbenzol, einer Reaktion, die schnell und exotherm ist.

Bei diesem Prozess entstehen als Nebenprodukte erhebliche Mengen an Polyethylbenzolen. Die Alkylierung kann sowohl in der Flüssigphase als auch in der Dampfphase durchgeführt werden.
In Flüssigphasenprozessen ist AlCl3 der am häufigsten verwendete Katalysator, aber auch andere Katalysatoren wie BF3, FeCl3, ZrCl4, SnCl4, H3PO4 und Erdalkaliphosphate werden verwendet. Die Reaktion wird typischerweise bei Atmosphärendruck und Temperaturen im Bereich von 85 bis 95 °C durchgeführt.
Die Dampfphasen-Alkylierung von Benzol ist vor allem in den Vereinigten Staaten weit verbreitet. Sie wird üblicherweise bei etwa 300 °C und 40 – 65 bar unter Verwendung saurer heterogener Katalysatoren wie Al2O3-SiO2 oder H3PO4-SiO2 durchgeführt.
Um die Selektivität der Monoalkylierung zu verbessern, wird ein niedriges Ethylen-Benzol-Verhältnis (0,2:1,0) verwendet. Das von Universal Oil Products entwickelte Alkar-Verfahren wird in mehreren Anlagen kommerziell eingesetzt und verwendet Bortrifluorid auf modifiziertem wasserfreiem Aluminiumoxid als nichtkorrosiven Katalysator.
Das Alkar-Verfahren ermöglicht einen weiten Bereich der Ethylenkonzentration (5 – 95 %) im Einsatzgas und ermöglicht so die Verwendung von Abgasen aus dem katalytischen Cracken oder Demethanizer-Überkopf oder hochreinem Ethylen. Die Prozessbedingungen umfassen typischerweise Temperaturen um 300 °C und Drücke um 60 bar, was zu einer vollständigen Umwandlung von Ethylen führt.
Die unter Verwendung des Alkar-Katalysators für die Benzol-Alkylierung mit Ethylen erhaltene Isomerenverteilung ist wie folgt:
Diethylbenzole:
1,2- (26 %);
1,3- (49 %); Und
1,4- (25 %).
Triethylbenzole:
1,2,3- (3 %);
1,2,4- (35 %); Und
1,3,5- (62 %).
Zeolithkatalysatoren haben für die Benzolethylierung großes Interesse gefunden. Mobil Oil und Badger führten einen Festbett-Dampfphasenprozess mit proprietären ZSM-5-Zeolithen ein, der bei 420–430 °C und 15–20 bar durchgeführt wurde.
Als Ausgangsmaterial kann nach der Reinigung reines oder verdünntes Ethylen verwendet werden. Polyalkylbenzole können zur Transalkylierung recycelt werden, was zu einer hohen Endausbeute an Ethylbenzol (98 – 99 Mol-%) führt. Katalysatoren auf Zeolithbasis haben Vorteile gegenüber flüssigen Brønsted- oder Lewis-Säure-Katalysatoren, da sie nicht korrodierend und umweltfreundlich sind und Konstruktion, Handhabung und Entsorgung vereinfachen.
Ein weiterer Prozess auf Zeolithbasis namens EBMax-Prozess, der Mobils proprietären MCM-22-Zeolithkatalysator verwendet, arbeitet in der flüssigen Phase. Darüber hinaus wird ein von Unocal entwickelter Katalysator auf Zeolithbasis in einer von Lummus/Unocal/UOP lizenzierten Festbett-Flüssigphasen-Alkylierungstechnologie eingesetzt.
2.2. Alkylierung von Benzol mit Propen
Die Alkylierung von Benzol mit Propen führt zur Bildung von Cumol, einer exothermen Reaktion. Cumol ist eine essentielle Verbindung, die hauptsächlich bei der Synthese von Phenol mit Aceton als Nebenprodukt verwendet wird. Ein kleiner Teil des Cumols wird auch bei der Herstellung von α-Methylstyrol verwendet.
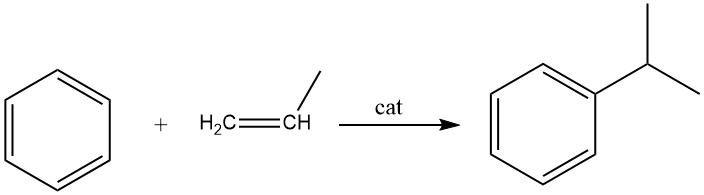
Für die Synthese von Cumol werden sowohl Flüssigphasen- als auch Dampfphasenverfahren kommerziell eingesetzt. Das weit verbreitete Flüssigphasenverfahren von Universal Oil Products nutzt einen festen Phosphorsäurekatalysator (SPA) auf Kieselgur.
Die Reaktion wird bei 15 – 35 bar und Temperaturen von 200 – 250 °C durchgeführt. Um eine Polyalkylierung zu verhindern und eine hohe Propenumwandlung (ca. 94 %) zu erreichen, ist ein Molverhältnis von Benzol zu Propen von 5:1 erforderlich. Die Umwandlung sinkt auf 70 %, wenn ein Benzol-Propen-Zufuhrverhältnis von 4:1 verwendet wird.
Steigender Druck und steigende Temperatur erhöhen eher die Umwandlung als die Cumolausbeute. Neben dem SPA-Katalysator werden auch Schwefelsäure und AlCl3 zur Cumol-Herstellung eingesetzt.
Neuartige Cumol-Produktionstechnologien auf Basis von Zeolithkatalysatoren wurden von verschiedenen Unternehmen wie Mobil/Raytheon, UOP, CDTech, Dow/Kellogg und Enichem entwickelt. Diese Prozesse umfassen typischerweise zwei Reaktoren und eine Destillationseinheit.
Der erste Reaktor führt die Alkylierung durch, während der zweite Reaktor schwere Endprodukte (Tri- und Polyisopropylbenzole) mit frischem Benzol transalkyliert.
Der MCM-22-Zeolith von Mobil, der proprietäre Zeolith von UOP im QMax-Prozess, der hoch entaluminierte Mordenit-Zeolith von Dow und der BEA-Zeolith-Katalysator von Enichem sind Beispiele für Zeolithe, die in diesen Prozessen verwendet werden.
Darüber hinaus kann Cumol mit Propen unter Verwendung eines vorbehandelten Aluminiumsilikatkatalysators in der flüssigen Phase unter Druck bei 150 – 250 °C weiter alkyliert werden. Dies führt zur Produktion von hauptsächlich p-Diisopropylbenzol und m-Diisopropylbenzol, mit nur Spuren des ortho-Isomers.
Die Isomere können durch Destillation getrennt werden und die Mischung aus m-Diisopropylbenzol und o-Diisopropylbenzol kann isomerisiert werden, um durch Transalkylierung mit Benzol weiter p-Diisopropylbenzol herzustellen. Die Diisopropylbenzole sind auch wichtige Zwischenprodukte bei der Herstellung von Hydrochinon oder Resorcin.
2.3. Alkylierung von Benzol mit höheren Olefinen
Monoalkylbenzole mit 10 – 14 Kohlenstoffatomen in der Alkylkette, wie z. B. Dodecylbenzol, spielen eine wichtige Rolle als Zwischenprodukte bei der Herstellung von Alkylbenzolsulfonaten, die häufig in anionischen kommerziellen Waschmitteln (Tensiden) verwendet werden.
Bis etwa 1965 war das für diese Reaktion verwendete primäre Olefin Propentetramer. Aufgrund von Umweltbedenken im Zusammenhang mit der biologischen Abbaubarkeit von Detergenzien auf Propentetramerbasis verlagerte sich die Industrie jedoch auf lineare Alkylbenzolsulfonate.
Heutzutage werden lineare Olefine mit 10 – 14 Kohlenstoffatomen als Ausgangsstoffe für die Herstellung von Alkylbenzolsulfonaten verwendet. Die Reaktion wird typischerweise durch flüssiges HF, H2SO4 oder AlCl3 katalysiert und geeignete Reaktionsbedingungen sind wie folgt:
1. HF: 0 – 10 °C, Molverhältnis Benzol zu Alken 4 – 10 und 2 – 3 kg Alken pro Kilogramm HF.
2. H2SO4: 10 – 30 °C, Molverhältnis Benzol zu Alken 4 – 5 und 2 Volumina Alken pro Volumen 96 – 98 % H2SO4.
3. AlCl3: 55 – 60 °C, Molverhältnis Benzol zu Olefin 3 – 4 und 25 Mol Alken pro Mol AlCl3.
Das HF-Verfahren gilt hinsichtlich des Katalysatorverbrauchs als das wirtschaftlichste. Es wird in flüssiger Phase bei Atmosphärendruck und 10 °C durchgeführt. Effektives Rühren und Kühlen sind notwendig, um die exotherme Reaktion zu kontrollieren und die Reaktionszeiten zu bestimmen.
Das Produkt wird in einem Absetzbehälter von der Säure getrennt, gewaschen und dann bei Atmosphärendruck destilliert, um Benzol zurückzugewinnen, und bei reduziertem Druck, um die Alkylbenzole zu isolieren.
Kürzlich wurden in der Literatur einige feste Alkylierungskatalysatoren beschrieben, aber aufgrund der geringeren Nachfrage nach linearen Alkylbenzolen (LAB) in industrialisierten Regionen hat nur das Detal-Verfahren von UOP eine neue Technologie kommerzialisiert, bei der ein nichtkorrosiver Katalysator als Ersatz für HF verwendet wird. Dieser Prozess nutzt einen fluoridierten Siliciumdioxid-Aluminiumoxid-Katalysator und arbeitet in der flüssigen Phase bei etwa 130 °C, wodurch eine hohe Linearität und Umwandlung erreicht wird.
Die Wascheigenschaften von Alkylbenzolsulfonaten werden durch den Verzweigungsgrad in der Alkylseitenkette beeinflusst, wobei drei bis fünf Methylgruppen im Dodecylbenzol optimal sind. Auch die Position der Phenylgruppe an der Alkylkette beeinflusst die Waschmitteleigenschaften.
Die Friedel-Crafts-Alkylierung führt zu einer Gleichgewichtsproduktmischung mit einer zufälligen Verteilung des Phenyls über die Alkylkette. Die Produktzusammensetzung wird durch die Art des Katalysators beeinflusst, wobei verschiedene Katalysatoren unterschiedliche Isomere von Monoalkylbenzolen bevorzugen.
Lewis-Säuren wie AlCl3 sind in der Lage, die gebildeten Phenylalkane zu isomerisieren, während Protonensäuren vor der endgültigen Alkylierung von Benzol nur die Olefine isomerisieren.
2.4. Alkylierung von Benzol mit Alkylchloriden
Kommerziell ist die Alkylierung von Benzol mit Alkylchloriden eine weitere Methode zur Herstellung von Waschmittelalkylaten. Das aus der Chlorierung von Paraffinen gewonnene Alkylchlorid enthält etwa 70 % Paraffin. Diese Mischung wird mit einem großen Überschuss an Benzol in einem emaillierten Alkylierungsturm unter Verwendung von AlCl3 als Katalysator bei 80 °C umgesetzt.
Während der Reaktion entsteht Chlorwasserstoff entsteht in stöchiometrischen Mengen, sorgt für eine gute Durchmischung der Reaktanten und wird am Kopf des Reaktors abgetrennt.
Die Produkte werden dann in einem Absetzbehälter vom Katalysator getrennt, neutralisiert, gewaschen und destilliert, um Benzol und Paraffin zurückzugewinnen, die recycelt werden. Die Alkylate werden durch Destillation unter vermindertem Druck weiter gereinigt.
Eine Herausforderung bei diesem Verfahren ist die Bildung erheblicher Mengen an Indan- und Tetralin-Derivaten als Nebenprodukte aufgrund der Anwesenheit von Dichloralkan-Verunreinigungen im Alkylchlorid.
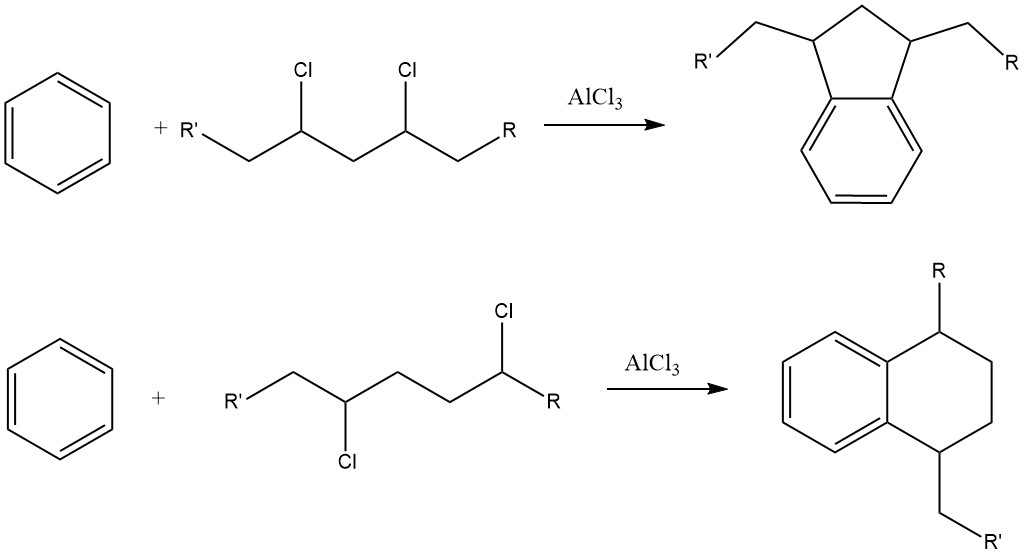
Alkylbenzole mit mehr als 15 Kohlenstoffatomen in der Seitenkette führen zu Alkylbenzolsulfonaten, die in Wasser nahezu unlöslich, in organischen Medien wie Mineralölen jedoch gut löslich sind.
Diese Lösungen in Mineralöl finden in der metallverarbeitenden Industrie als Bohr- und Schneidflüssigkeiten oder in der Textilindustrie als Spinn- oder Batchflüssigkeiten Verwendung. Darüber hinaus werden Alkylbenzolsulfonate dieses Typs zunehmend als Flutungsmittel in verbesserten Erdölrückgewinnungsprozessen eingesetzt.
2.5. Verschiedene Alkylierungen von Benzol
Benzol kann mit einer Vielzahl von Verbindungen alkyliert werden, darunter verschiedene lineare, verzweigte, zyklische, Aryl- oder anderweitig substituierte Olefine, Alkylhalogenide, Alkohole, Ether, Alkine und Diene.
Einige dieser Reaktionen wurden erfolgreich kommerzialisiert, beispielsweise die Synthese von tert-Butylbenzol aus Benzol und Isobuten. Tert-Butylbenzol findet Anwendung bei der Herstellung von Parfüms.
3. Cycloalkylierung
Ein Beispiel für intermolekulare Cycloalkylierungen ist die Reaktion von Dichlormethan und Benzol, die zur Bildung von 9,10-Dihydroanthracen zusammen mit etwas Diphenylmethan führt. Bei dieser Reaktion entstehen auch Anthracen-Derivate.

Eine intramolekulare Cycloalkylierung ist für alkylierte aromatische Verbindungen möglich, die in ihrer Seitenkette eine Doppelbindung oder eine funktionelle Gruppe, beispielsweise eine Halogen- oder Hydroxygruppe, tragen. Beispielsweise wird 3-Phenyl-1-propen in Gegenwart von AlCl3 zu Indan isomerisiert.

BASF entwickelte eine Synthese für Anthrachinon auf Basis der Cycloalkylierung. Dabei erfolgt die Dimerisierung von Styrol in flüssiger Phase zu 1-Methyl-3-phenylindan unter Verwendung von Phosphorsäure als Katalysator. Die resultierende Verbindung wird dann einer katalytischen Dampfphasenoxidation unterzogen, um Anthrachinon herzustellen.
3.1. Arylierung aromatischer Verbindungen
Die Arylierung aromatischer Verbindungen kann mit verschiedenen Methoden erreicht werden, einschließlich der Reaktion mit Arylhalogeniden, der Reaktion mit Diazoniumhalogeniden und der dehydrierenden Kondensation.
Arylhalogenide wie Fluorbenzol, Chlorbenzol und Brombenzol können als Arylierungsmittel bei Friedel-Crafts-Arylierungen verwendet werden. Allerdings ist ihre Reaktivität relativ gering, wobei Fluorbenzol am reaktivsten ist, gefolgt von Chlorbenzol und Brombenzol.
Durch Arylierung mit Fluorbenzol können Biphenyle als Produkte entstehen, während die Zersetzung von Aryldiazoniumtetrafluorboraten in aromatischen Lösungsmitteln zusammen mit Fluorbenzol zu ringarylierten Produkten führen kann.
Die Scholl-Reaktion ist eine dehydrierende Kondensation einer aromatischen Verbindung in Gegenwart von Friedel-Crafts-Katalysatoren. Durch diese Reaktion kann beispielsweise Naphthalin in Perylen und Pyridin in 2,2′-Dipyridyl umgewandelt werden. Mit der Scholl-Reaktion können auch hochmolekulare polykondensierte aromatische Verbindungen gebildet werden.
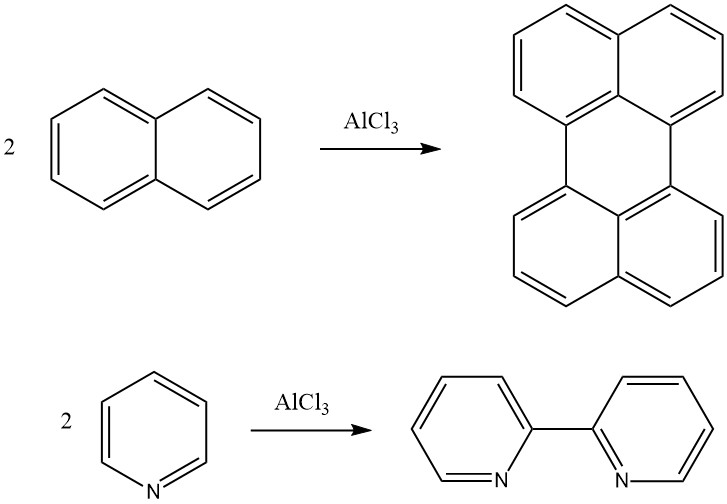
4. Alkylierung substituierter Benzole
Die Alkylierung von Benzol führt typischerweise zu einer Mischung aus monoalkylierten, dialkylierten und polysubstituierten Verbindungen. Die Reaktivität und Orientierung im zweiten Substitutionsschritt hängen von den elektronischen und sterischen Eigenschaften des ersten Substituenten und der Größe des Alkylierungsmittels ab.
Dialkylierte Benzole haben erhebliche kommerzielle Bedeutung. Diethylbenzole werden beispielsweise zur Erhöhung der Oktanzahl von Kraftstoffen verwendet und fallen als Nebenprodukte bei der Herstellung von Ethylbenzol an.
Dialkylbenzole können zu Divinylbenzolen dehydriert werden, die für die Vernetzung von Polyolefinen wie Polystyrol bei der Herstellung von Ionenaustauscherharzen von entscheidender Bedeutung sind.
Ethylmethylbenzol, das durch Ethylierung von Toluol entsteht, ist als Ausgangsmaterial für Styrole mit Methylsubstitutionen im aromatischen Ring industriell wertvoll. Ein weiteres Beispiel ist die Herstellung von Diisopropylbenzol durch die Reaktion von Propen mit Cumol (Alkylierung von Benzol mit Propen).
4.1. Die Alkylierung von Toluol mit Propen
Der industrielle Prozess der Alkylierung von Toluol mit Propen zur Herstellung von Cymol wird von Unternehmen wie Sumitomo Chemicals durchgeführt. Das resultierende Cymolgemisch besteht hauptsächlich aus Meta- und Para-Isomeren und wird dann einer Oxidation unterzogen, um Aceton und Kresole zu ergeben.
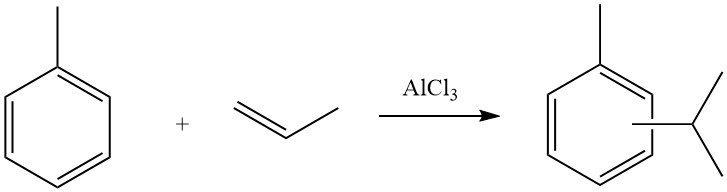
Diese Kresole bestehen zu etwa 39,5 % aus Meta- und Para-Kresolen und zu 36 % aus Meta-Kresolen und dienen als wesentliche Rohstoffe für Phenolharze und Weichmacher.
Ein weiterer wichtiger Aspekt betrifft die Herstellung polymethylierter Benzole durch Prozesse wie die Disproportionierung von Toluol oder die Methylierung von Benzol oder Toluol. Diese polymethylierten Benzole können oxidiert werden, um die entsprechenden Säuren zu bilden, die in verschiedenen Polymeren wie Polyestern, Polyamiden und Polyimiden Anwendung finden.
4.2. Alkylierung höherer aromatischer Verbindungen
Die Alkylierung höherer aromatischer Verbindungen wie Biphenyl, Indan, Tetralin und mehrkerniger aromatischer Verbindungen wie Naphthalin, Acenaphthen, Anthracen, Fluoren und Phenanthren wurde dokumentiert.
Beispielsweise wird die Alkylierung von Naphthalin mit höheren Olefinen kommerziell zur Herstellung von Fluoreszenzmitteln für Schmieröle eingesetzt. Diese Flüssigphasenreaktion nutzt AlCl3 als Katalysator bei Temperaturen bis zu 180 °C.
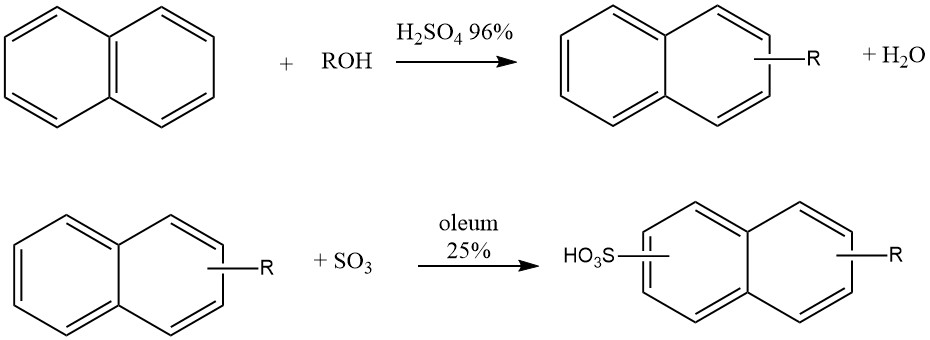
Eine weitere industrielle Anwendung der Naphthalin-Alkylierung ist die Herstellung von Waschmitteln vom Typ „Nekal“ (BASF), bei denen es sich um Alkylnaphthalinsulfonate handelt. Diese Verbindungen gehörten zu den ersten synthetischen Waschmitteln und werden auch heute noch als Tenside in der Textilindustrie verwendet.
Die Synthese dieser Alkylnaphthalinsulfonate erfolgt in einem Eintopfverfahren, bei dem Naphthalin mit Butanol, Hexanol oder Mischungen aus Propanol-Butanol in Gegenwart von 96 %iger Schwefelsäure bei 50 °C reagiert. Nach der Alkylierung wird 25 % Oleum zur Sulfonierung zugesetzt.
Darüber hinaus beinhaltet das Hock-Verfahren die Oxidation von 2-Isopropylnaphthalin, was zu 2-Naphthol führt. Um 2-Isopropylnaphthalin zu erhalten, kann eine Reaktion zwischen Naphthalin und Propen unter Verwendung von ZnCl2 oder Aluminiumsilikaten als Katalysatoren bei 150–200 °C durchgeführt werden, wobei auch geringe Mengen des 1-Isopropyl-Isomers entstehen.
Darüber hinaus haben 2,6-Dialkylnaphthaline aufgrund ihrer Umwandlung in 2,6-Naphthalindicarbonsäure, die bei der Herstellung des Hochleistungskunststoffs Poly(ethylen-2,6-naphthalindicarboxylat) (Polyethylennaphthenat, PEN) verwendet wird, großes Interesse geweckt.
Für die Alkylierung von Naphthalinen wurden verschiedene formselektive Katalysatoren, darunter Mordenit, untersucht. Alternativ hat Amoco 1995 eine weitere Route mit einer Kapazität von rund 40.000 t/a kommerzialisiert. Sie alkylieren o-Xylol mit Butadien an einem stark basischen Katalysator und ergeben o-Tolylpenten, das dann einer Cyclisierung, Dehydrierung und Isomerisierung unterliegt.
5. Alkylierung von Phenolen
Die Alkylierung von Phenolen ist eine äußerst bedeutsame industrielle Reaktion, die zur Produktion von Alkylphenolen führt, die in verschiedenen Anwendungen wie Antioxidantien, Herbiziden, Insektiziden und Polymeren weit verbreitet sind.
Aufgrund der erhöhten Elektronendichte im aromatischen Ring, der mit der nukleophilen Hydroxylgruppe verbunden ist, erfolgt die Alkylierung im Vergleich zu aromatischen Kohlenwasserstoffen unter milderen Bedingungen.
Verschiedene Faktoren, darunter Reaktionsbedingungen, Katalysatoren und Alkylierungsmittel, beeinflussen die Bildung überwiegend ortho- oder para-monoalkylierter, 2,4- oder 2,6-dialkylierter und 2,4,6-trialkylierter Phenole.
Höhere Temperaturen führen aufgrund von Sekundärreaktionen zu thermodynamisch stabileren Meta-Isomeren. Darüber hinaus können niedrige Temperaturen und Katalysatorkonzentrationen erhebliche Mengen an Alkylarylethern ergeben, während höhere Temperaturen, Katalysatorkonzentrationen und Säurestärke die überwiegende Bildung von Alkylphenolen begünstigen.
Im Alkylierungsprozess werden Alkylierungsmittel wie Olefine, Alkohole und Alkylhalogenide eingesetzt. Es wurden drei Haupttypen industrieller Verfahren zur Phenolalkylierung entwickelt:
1. Bei der Flüssigphasen-Alkylierung wird das Alkylierungsmittel zu einer Lösung oder Suspension des Katalysators im Phenol gegeben. Nach der Reaktion wird der Katalysator abgetrennt und eventuell verbleibender Katalysator durch Neutralisation zersetzt.
2. Bei Festbett-Flüssigphasenverfahren strömen die Reaktanten bei erhöhtem Druck in Rohrreaktoren über den Katalysator, die von außen gekühlt werden.
3. Bei der Dampfphasen-Alkylierung werden Phenol und das Alkylierungsmittel wie Methanol oder ein Olefin in einen Festbettreaktor geleitet, der bei 300–400 °C betrieben wird, wobei die Reaktionswärme effizient abgeführt wird.
Die Produktrückgewinnung erfolgt durch Destillation, wobei nicht umgewandelte Phenole und Alkylierungsmittel recycelt und verschiedene mono-, di- und trialkylierte Phenole abgetrennt werden. Die vollständige Entfernung saurer Katalysatorspuren ist entscheidend, um Nebenreaktionen während der Destillation wie Isomerisierung, Transalkylierung und Disproportionierung zu verhindern.
Flüssigphasenprozesse nutzen Lewis-Säure-Katalysatoren wie AlCl3, BF3 oder Al(C6H5O)3, Protonensäuren wie HF, H2SO4, H3PO4 oder p-Tolylsulfonsäure oder saure Ionenaustauscherharze wie Nafion-Harze oder sulfonierte Polystyrole.
Dampfphasenprozesse erfordern Katalysatoren mit hoher thermischer Stabilität, wie Montmorillonite, Zeolithe wie Faujasit und Metalloxide wie γ-Al2O3, MgO, CaO und Fe2O3 – CrO3.
Die Regioselektivität kann mithilfe verschiedener Katalysatoren gesteuert werden. Beispielsweise fördern HF, BF3, Al2O3·SiO2 oder saure Ionenaustauscherharze bei der Alkylierung von Phenolen mit Olefinen überwiegend p-substituierte Produkte.
Andererseits führt Al(C6H5O)3, das aus Phenol und metallischem Aluminium entsteht, insbesondere in Gegenwart von Spuren von Quecksilbersalzen, fast ausschließlich zu 2-alkylierten und 2,6-dialkylierten Produkten. Diese Selektivität für die ortho-Alkylierung wird einem sechsgliedrigen Übergangszustand zugeschrieben, an dem Aluminiumphenolat und ein Olefin beteiligt sind.
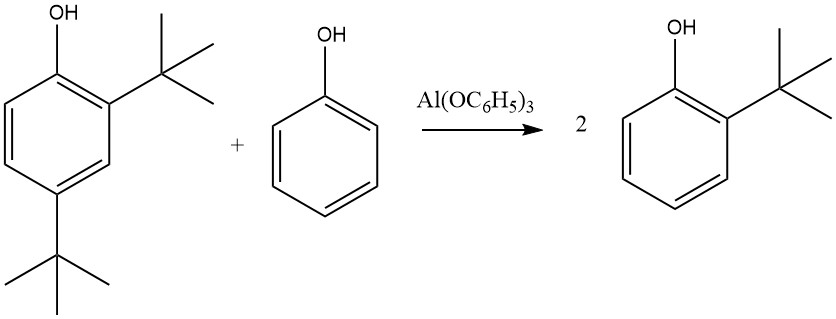
Andere Metallsalze von Phenol, darunter die von Zink, Magnesium und Kalzium, können diese Reaktion ebenfalls aktivieren, die nicht auf Phenol beschränkt ist; 2-Naphthol, 2-Kresol oder 4-Kresol können auch durch Ethylen, Propen, die Butene, Cyclohexen oder andere Olefine mit unterschiedlicher Reaktivität alkyliert werden, wobei Isobuten die höchste Reaktivität und Ethylen die niedrigste zeigt.
In Gegenwart von γ-Al2O3 als Katalysator kann eine hohe Selektivität für monoalkylierte o-Phenole erreicht werden. Dieses Verfahren läuft bei erhöhten Temperaturen von 200 – 350 °C in der Flüssigphase bei Drücken von 20 – 200 bar ab und ist für den kontinuierlichen Festbettbetrieb geeignet.
Bei den Alkylphenolprodukten werden Alkylphenole häufig im Batch-Verfahren hergestellt, was eine höhere Flexibilität bietet. Für in großen Mengen hergestellte Verbindungen wie Kresole, 2,6-Xylenol, 2-sek.-Butylphenol, 4-tert-Butylphenol, Octylphenol, Nonylphenol, Dodecylphenol, Thymol oder 2,6-Di-tert-butylphenol 4-Methylphenol wurden kontinuierliche Prozesse mit Kapazitäten von jeweils bis zu 25.000 t/a eingeführt.
5.1. Alkylierung von Phenol mit Methanol
Die Alkylierung von Phenol mit Methanol bei erhöhten Temperaturen und mit einem Katalysator ergibt hauptsächlich 2-Kresol (60 – 70 % bei 50 % Phenolumwandlung und 300 °C) und 2,6-Xylenol, begleitet von geringen Mengen an 4-Kresol, 2, 4- und 2,3-Xylenole und eine kleine Menge 3-Kresol.
Die Reaktion kann entweder in der Flüssig- oder Dampfphase durchgeführt werden. Bei Dampfphasenprozessen werden die Reaktanten bei Atmosphärendruck oder leicht erhöhtem Druck in einen Rohrreaktor mit Festbettkatalysator bei Temperaturen zwischen 300 und 450 °C eingeleitet.
Die Verwendung von aktiviertem Al2O3 bei 300 °C und MgO und CeO2 bei 540 bzw. 450 °C führt zu einer hohen Selektivität für 2-Kresol und 2,6-Xylenol. Allerdings führt die Verwendung stark saurer Katalysatoren wie Aluminiumoxid, Aluminiumsilikate, Zeolithe und Aluminiumphosphat, insbesondere bei höheren Temperaturen, zu einer Transalkylierung-Isomerisierung, was zu einer erhöhten Produktion von 3-Kresol und 4-Kresol führt.
Flüssigphasenprozesse nutzen Katalysatoren wie Al2O3, Al(OMe)3, Al(OC6H5)3 oder ZnCl2 – HCl bei erhöhten Drücken. In allen Fällen steigt das Xylenol:Kresol-Verhältnis mit dem Methanol:Phenol-Verhältnis, der Temperatur und dem Druck.
5.2. Alkylierung von Phenolen mit Olefinen
Die Alkylierung von Phenol mit Methanol erfolgt bei erhöhten Temperaturen, typischerweise zwischen 320 und 340 °C, in Gegenwart von 1 – 2 % Al(C6H5O)3 und bei 200 bar, was zur Bildung von 2-Ethylphenol führt.
Andererseits kann die Alkylierung von Phenol mit Propen zu 2-Isopropylphenol bei niedrigeren Temperaturen von 280 – 300 °C unter Verwendung von γ-Al2O3 als Katalysator erreicht werden.
Darüber hinaus wird die Propylierung von Kresolen zu Thymol oder Carvacol in kontinuierlichen Flüssigphasenprozessen unter Verwendung von γ-Al2O3, Aluminiumsilikaten oder Zeolithen durchgeführt. Unter ähnlichen Bedingungen kann 2-sec-Butylphenol aus Phenol und n-Butenen hergestellt werden.
Die Produktion von 2-tert-Butylphenol und 2,6-Di-tert-butylphenol kann bei 100 °C und Drücken bis zu 20 bar in Gegenwart von Al(C6H5O)3 erreicht werden, wobei die hohe Reaktivität von Isobuten ausgenutzt wird.
Alternativ kann 4-tert-Butylphenol bei Atmosphärendruck und Temperaturen im Bereich von 80 bis 140 °C unter Verwendung von H2SO4, H3PO4, BF3 oder vorzugsweise sauren Kationenaustauscherharzen hergestellt werden.
Das wichtige Antioxidans 2,6-Di-tert-butyl-4-methylphenol wird aus 4-Kresol und Isobuten bei 70 °C mit H2SO4 als Katalysator hergestellt. Ebenso führt die Alkylierung von Phenol mit 2-Methylbutenen bei 100 – 120 °C in Gegenwart von BF3 oder H3PO4 zu 4-tert-Amylphenol, und bei einem Überschuss an 2-Methylbutenen entsteht 2,4-Di-tert-amylphenol .
Ein wichtiger kommerzieller Prozess ist die Alkylierung von Phenol mit linearen oder verzweigten Olefinen mit 6 bis 20 Kohlenstoffatomen, was zu Alkylphenolen führt, die nach Ethoxylierung und Sulfatierung breite Anwendung als anionische Detergenzien finden.
Diisobuten, Tripropen und Tetrapropen sind bevorzugte Alkylierungsmittel, und die Reaktion wird unter milden Bedingungen (50 – 85 °C) mit BF3 in kontinuierlichen Chargen- oder Rohrreaktoren katalysiert. Saure Kationenaustauscherharze wie makroretikuläres sulfoniertes Polystyrol sind ebenfalls ausgezeichnete Katalysatoren, die die Katalysatortrennung erleichtern.
Um eine bessere Temperaturkontrolle zu erreichen, kann die Reaktion in zwei Stufen durchgeführt werden, wobei in der ersten Stufe ein Katalysator mit reduziertem Säuregehalt eingesetzt wird. Die Chemischen Werke Häüls (heute Degussa-Hüls) in Deutschland nutzen ein solches Verfahren zur Herstellung von Nonylphenol.
In der ersten Stufe dieses Festbettverfahrens steigt die Temperatur von 80 auf 120 °C und in der zweiten Stufe von 110 auf 130 °C. Auch aktivierte Aluminiumsilikate können als Katalysatoren dienen, sie erfordern jedoch höhere Reaktionstemperaturen und längere Reaktionszeiten.
Die industrielle Produktion von Alkylphenolen, Haloalkylphenolen und verwandten Verbindungen ist umfangreich und diese Verbindungen werden häufig als Oxidationsinhibitoren, Reinigungsmittel, Bakterizide, Fungizide, Insektizide und Desinfektionsmittel verwendet.
6. Alkylierung aromatischer Amine
Aufgrund der Basizität aromatischer Amine sind saure Katalysatoren für deren Alkylierung nicht gut geeignet. Beispielsweise führt der Einsatz des Friedel-Crafts-Katalysators AlCl3 bei der Reaktion von Ethylen mit Anilin überwiegend zu nicht identifizierten harzigen Produkten mit nur geringen Mengen an 2-Ethylanilin.
Allerdings erweist sich Aluminiumanilid Al(C6H5NH)3, das in situ durch Erhitzen von Aluminiumpulver in Anilin unter Wasserstoffentwicklung entsteht, als wirksamer Katalysator für diese Reaktion. Unter Bedingungen von 300 – 340 °C und 200 bar wird 2,6-Diethylanilin nach 2 – 3 Stunden erhalten, während kürzere Reaktionszeiten zur Bildung von 2-Ethylanilin führen.
Die katalytische Aktivität von Aluminiumanilid wird durch die Zugabe von Friedel-Crafts-Katalysatoren wie AlCl3, SnCl4, TiCl4, SiCl4, BF3 oder ZnCl2 weiter gesteigert. Auch Alkalimetall- und AlCl3-Gemische in Anilin zeigen Aktivität und führen selektiv zur N-Alkylierung.
Diese Reaktion wurde auf verschiedene substituierte Aniline ausgeweitet, darunter 2-, 3- und 4-Toluidin, 2,6-, 2,4- und 2,5-Xylidin, 2-Propylanilin, 2- und 3-Chloranilin. und α-Naphthylamin. Darüber hinaus können auch Diamine wie m-Phenylendiamin oder 2,4-Toluylendiamin sowie sekundäre Amine wie Diphenylamin alkyliert werden.
Beim Alkylierungsprozess mit Olefinen nimmt die Reaktivität in der Reihenfolge Ethylen > Propen > 1-Buten > Isobuten ab, was entgegengesetzt zur Reaktivitätsreihenfolge ist, die bei der Phenolalkylierung mit Al(OC6H5)3-Katalysator beobachtet wird.
Bemerkenswert ist, dass Isobuten selbst bei 200–250 °C Aktivität mit Friedel-Crafts-Katalysatoren wie AlCl3, BF3 oder Montmorillonit zeigt, während die Reaktion mit Aluminiumanilid langsam verläuft. Bei Verwendung von Montmorillonit kommt es zur selektiven Bildung von 4-tert-Butylanilin, während BF3- oder AlCl3-Katalysatoren Gemische der 2- und 4-Isomere ergeben.
Bei der Alkylierung von Anilinen mit Methanol wirken Molekularsiebe als Katalysatoren, wodurch ein komplexes Gemisch aus 2-Toluidin, 2,6- und 2,4-Xylidin sowie 2,4,6-Trimethylanilin entsteht. Industriell werden 2,6-Dialkylaniline wie 2-Ethyl-6-methylanilin als Zwischenprodukte für Herbizide und Farbstoffe hergestellt.
7. Alkylierung heteroaromatischer Verbindungen und verwandter Substrate
Verschiedene heterocyclische aromatische Verbindungen, darunter Furane, Thiophene und N-Heterocyclen, können Alkylierungsreaktionen unterzogen werden, obwohl nur begrenzte Informationen über ihre kommerziellen Anwendungen verfügbar sind.
Cyclopentadienylderivate unterliegen ebenfalls einer Friedel-Crafts-Alkylierung auf ähnliche Weise wie andere aromatische Verbindungen.
7.1. Furan
Furan weist im Vergleich zu Benzol eine höhere Reaktivität bei Friedel-Crafts-Alkylierungen auf. Allerdings neigen Furane in Gegenwart von Säuren zu einer schnellen Verharzung, was die Produkttrennung erschweren kann.
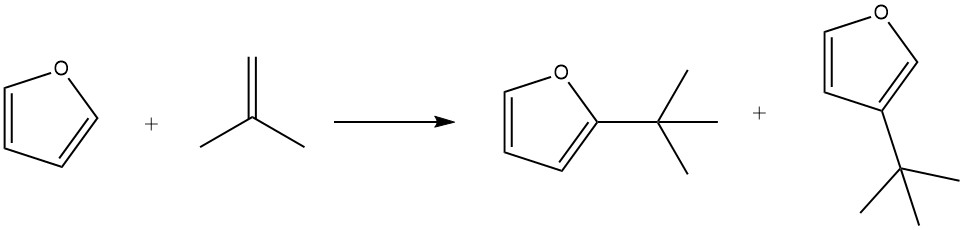
Durch die Verwendung von Phosphorsäure auf Kieselgur als Katalysator kann Furan effizient mit Isobuten bei 100 °C innerhalb von 3 Stunden alkyliert werden, was zu einer 85-prozentigen Ausbeute der Alkylate zusammen mit geringen Mengen an Isoocten führt.
Unter milden Bedingungen (z. B. 50 °C für 1 Stunde) wird die Substitution in der 2-Position bevorzugt. Längere Reaktionszeiten (7 Stunden), höhere Temperaturen (150 °C) und höhere Katalysatorkonzentrationen fördern jedoch die Bildung von Produkten, die in Position 3 substituiert sind. Darüber hinaus wurde während des Prozesses auch die Bildung von 2,5-Di-tert-butylfuran beobachtet.
7.2. Thiophen
Thiophen weist im Vergleich zu aromatischen Kohlenwasserstoffen eine deutlich höhere Reaktivität bei Friedel-Crafts-Reaktionen auf und ermöglicht die Alkylierung mit verschiedenen Olefinen, darunter Propen, 1-Buten, 2-Methylbutene, Cyclohexen und Alkoholen wie Isopropylalkohol und tert-Butylalkohol.
Erfolgreiche Ergebnisse wurden mit sauren Katalysatoren wie Phosphorsäure bei 60 °C oder Aluminiumoxid-Siliciumdioxid bei 200 °C erzielt. Allerdings führte die Verwendung von H2SO4, HF, BF3·OMe2 und AlCl3 zu Nebenreaktionen. In allen Fällen wurde das Thiophen in der 2-Position substituiert, und es entstanden auch höhersiedende Produkte, wie z. B. dialkylierte Verbindungen.
Darüber hinaus handelt es sich bei der Entfernung von Thiophen aus gekracktem Benzin während der Raffinierung mit kalter konzentrierter Schwefelsäure wahrscheinlich um eine Alkylierungsreaktion. Die im Benzin enthaltenen Olefine wirken als Alkylierungsmittel und führen zur Bildung hochsiedender Alkylthiophene, die bei der Destillation als Rückstand zurückbleiben.
7.3. N-Heterozyklen
N-Heterocyclen können in Gegenwart von Aluminiumamiden als Katalysatoren alkyliert werden. Während heterozyklische Verbindungen wie Carbazol und Indol träge mit Aluminiummetall unter Bildung des Amids reagieren, dient Aluminiumanilid als wirksamer Katalysator.
Wenn beispielsweise Carbazol mit Ethylen in Gegenwart von Anilin und Aluminiumpulver reagiert, entsteht 1-Ethylcarbazol. Diese Reaktion findet in einem Autoklaven bei 280 °C und 200 bar statt.
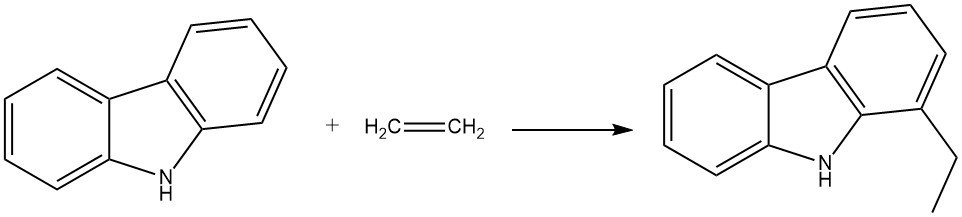
Propen kann unter ähnlichen Bedingungen auch zu 1-Isopropylcarbazol reagieren, allerdings mit einer etwas geringeren Ausbeute.
Die Kombination von Carbazol und Propen mit AlCl3 als Katalysator bei 90 – 100 °C führt zur Bildung von Diisopropylcarbazol. Eine weitere Reaktion an einem Aluminiumsilikatkatalysator bei 180 – 200 °C ergibt Tetra- und Pentaisopropylcarbazol. Darüber hinaus kann die Ethylierung von Pyrrol mit einem Aluminiumsilikat-Katalysator bei 200 – 370 °C erreicht werden.
7.4. Nichtbenzolische aromatische Verbindungen
Nichtbenzoide aromatische Verbindungen wie Ferrocene, Fulvene, Azulene, Pseudoazulene, Indolizine und Cyclazine weisen chemische Ähnlichkeiten nicht nur mit Benzoloidsystemen, sondern auch mit Olefinen auf.
Ihre elektrophilen Substitutionsreaktionen laufen im Vergleich zu Benzolderivaten typischerweise unter milderen Bedingungen ab. Aufgrund ihrer relativ geringen Stabilität ist jedoch eine sorgfältige Auswahl der Katalysatoren und Reaktionsbedingungen unerlässlich.
Ferrocen kann in Gegenwart von Lewis-Säuren wie AlCl3 mit verschiedenen Substraten, einschließlich Methanol, Ethyl-, Isopropyl-, Butyl- und Benzylhalogeniden, 1,2-Dichlorethan, Ethylen, Propen und Isobuten, alkyliert werden.
Die Reaktion führt häufig zu komplexen Mischungen homoannularer und heteroannularer Produkte (bei denen beide Ringe alkyliert sind), da das System nach dem ersten Alkylierungsschritt reaktiver wird.
Günstiger scheint die Alkylierung von Ferrocen mit Olefinen zu sein, etwa die Reaktion mit Isobuten, die bereits bei Raumtemperatur abläuft. Bei höheren Temperaturen (100 – 150 °C) wird heteroannulares Tri-tert-butylferrocen in einer Ausbeute von 44 % erhalten, zusammen mit etwas Tetra-tert-butylferrocen. Sterische Hinderung verhindert die Anbindung von mehr als zwei tert-Butylsubstituenten an denselben Cyclopentadienylring.
8. Verschiedene Alkylierungsreaktionen
Die Alkylierung aromatischer Verbindungen mit bi- oder polyfunktionellen Reagenzien führt zur Bildung einer Vielzahl wertvoller ein-, zwei- oder mehrkerniger Produkte mit bedeutenden kommerziellen Anwendungen.
8.1. Haloalkylierungen
Unter geeigneten Reaktionsbedingungen können Haloalkylierungen aromatischer Verbindungen mit bi- oder polyfunktionellen Alkylierungsmitteln primäre Haloalkylierungsprodukte erzeugen und gleichzeitig eine unerwünschte Cycloalkylierung oder Verknüpfung mehrerer Kerne vermeiden.
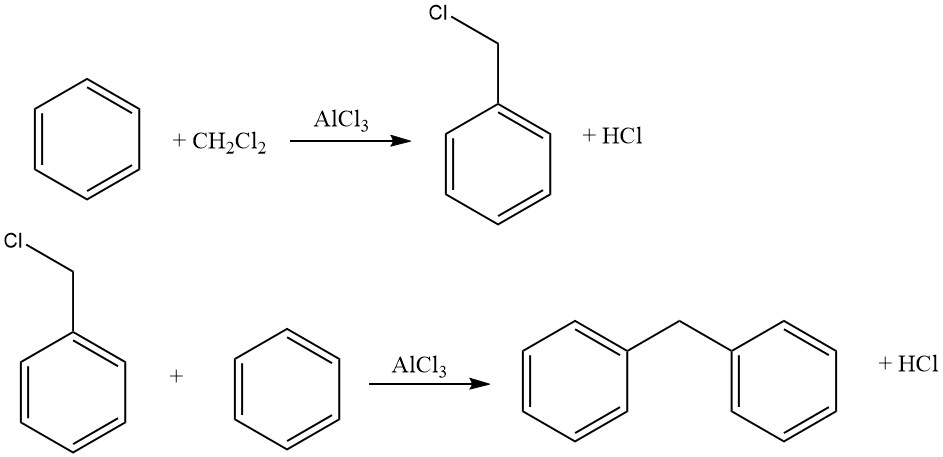
Zu den üblichen Haloalkylierungsmitteln gehören Aldehyd-Halogenwasserstoff, Haloalkylether, Haloalkohole und ähnliche Verbindungen. Dieser Prozess ermöglicht Halomethylierung, Haloethylierung, höhere Haloalkylierung sowie Bis- und Polyalkylierung.
Die Reaktion wird häufig durch Zinkchlorid katalysiert, aber auch andere Katalysatoren wie saure Halogenide (z. B. ZnCl2 – AlCl3, SnCl4, AlCl3 – Ketone, AlCl3 – Pyridin) oder Protonensäuren (HCl, H2SO4, H3PO4, p-Toluolsulfonsäure). verwendet werden.
Ein häufiges Beispiel für diese Reaktion ist die Chlormethylierung mit Formaldehyd-HCl (Blanc-Reaktion). Obwohl diese Reaktion synthetisch wertvoll ist, ist aufgrund der Bildung reaktiver Zwischenprodukte, insbesondere Chlormethylether, die stark krebserregend sind, Vorsicht geboten.

8.2. Hydroxyalkylierung
Die Hydroxyalkylierung aromatischer Verbindungen mit Aldehyden und Ketonen in Gegenwart von Säuren ist von erheblicher industrieller Bedeutung. Die den aromatischen Kern angreifenden Elektrophile entstehen durch die Reaktion von Aldehyden oder Ketonen mit Lewis- oder Protonensäuren (wobei R, R0 = H, Alkyl, Aryl).
Die Reaktion führt zur Bildung eines substituierten Benzylalkohols. Unter sauren Bedingungen reagiert dieser Alkohol mit einem anderen Molekül der aromatischen Verbindung und erzeugt ein substituiertes Diarylmethan.
Ein bemerkenswertes Beispiel für diese Reaktion ist die Hydroxyalkylierung von Phenol mit Aceton, die 2,2-Bis-(4-hydroxyphenyl)propan, allgemein bekannt als Bisphenol A, ergibt. Diese Verbindung wird industriell in kontinuierlichen Prozessen unter Verwendung von H2SO4 (oder trockener HCl im Jahr) hergestellt Hooker-Prozess) als Katalysator und Methylmercaptan als Promotor, was zu nahezu quantitativen Ausbeuten bei 50 °C führt.

Auch Kationenaustauscherharze werden aufgrund ihres vereinfachten Trennverfahrens zunehmend als Katalysatoren eingesetzt. Bisphenol A wird hauptsächlich zur Herstellung von Epoxid- und Polycarbonatharzen verwendet.
Hydroxyalkylierungen sind äußerst vielseitig und ermöglichen die Reaktion zahlreicher Alkyl- und Aryl-substituierter Aldehyde und Ketone mit verschiedenen aromatischen Verbindungen. Beispielsweise wird das Insektizid DDT aus Chloral und Chlorbenzol hergestellt. Die Reaktion von Phenol mit Formaldehyd führt zu Hydroxymethylphenolen, die bei erhöhten Temperaturen weiter zu Phenolharzen kondensieren können.
Bei der Verwendung von Oxiranen (Epoxiden) als Alkylierungsmittel werden β-Hydroxyalkylaromaten erhalten. Beispielsweise führt die Reaktion von Benzol mit Ethylenoxid in Gegenwart einer stöchiometrischen Menge AlCl3 zu einem Aluminiumalkoxid, das bei Hydrolyse β-Phenylethanol ergibt.
8.3. Amidomethylierung
Bei der Amidomethylierung, auch Tscherniac-Einhorn-Reaktion genannt, handelt es sich um einen Prozess, bei dem N-Hydroxymethylamide oder die entsprechenden Imide unter milden Bedingungen in Gegenwart von Schwefelsäure mit aromatischen Verbindungen reagieren. Diese Reaktion ermöglicht die Einführung einer Amidomethylgruppe in den aromatischen Kern.
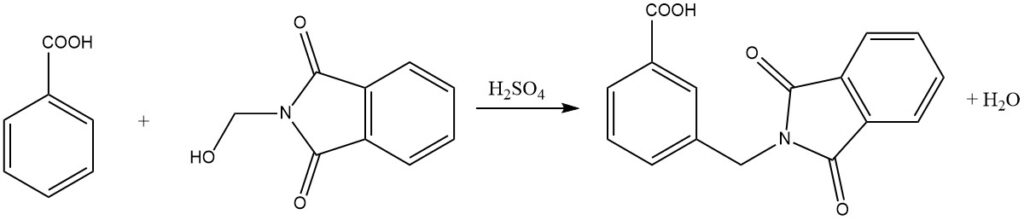
Darüber hinaus können durch diesen Prozess auch weniger reaktive aromatische Verbindungen wie Benzoesäuren einer Amidoalkylierung unterzogen werden. Bemerkenswerterweise können sogar nitrosubstituierte aromatische Verbindungen mit N-Chlormethylcarbonsäureamiden in Gegenwart von AlCl3 als Katalysator alkyliert werden.
Referenz
- Acylation and Alkylation; Ullmann’s Encyclopedia of Industrial Chemistry. – https://onlinelibrary.wiley.com/doi/10.1002/14356007.a01_185
FAQ
Die Friedel-Crafts-Alkylierung ist eine chemische Reaktion zur Einführung von Alkylgruppen (wie Methyl, Ethyl usw.) in einen aromatischen Ring. Dabei wird ein Wasserstoffatom am aromatischen Ring durch eine Alkylgruppe ersetzt, was zur Bildung alkylaromatischer Verbindungen führt.
Die Friedel-Crafts-Alkylierung hat verschiedene industrielle Anwendungen. Durch diese Reaktion hergestellte Alkylaromatenverbindungen werden als Ausgangsmaterialien bei der Synthese von Farbstoffen, Pharmazeutika, Duftstoffen und Agrochemikalien verwendet. Darüber hinaus dienen sie als Zwischenprodukte bei der Herstellung von Polymeren und anderen organischen Verbindungen.
Außer Benzol können auch andere aromatische Verbindungen wie Naphthalin, Toluol, Phenol, Anilin und verschiedene heterozyklische aromatische Verbindungen wie Furane und Thiophene Alkylierungsreaktionen eingehen. Die spezifischen Bedingungen und Reagenzien können je nach Art der aromatischen Verbindung und der gewünschten Alkylsubstitution variieren.
Ja, die Friedel-Crafts-Alkylierung weist einige Einschränkungen und Herausforderungen auf. Eine wesentliche Einschränkung ist die Möglichkeit einer Überalkylierung, die zu polyalkylierten Produkten führen kann. Auch eine sterische Hinderung in bestimmten aromatischen Verbindungen kann die Reaktion behindern. Darüber hinaus können einige Alkylierungsmittel und Lewis-Säure-Katalysatoren empfindlich gegenüber Feuchtigkeit und Luft sein, was eine sorgfältige Handhabung und Reaktionsbedingungen erfordert.
Während die Friedel-Crafts-Alkylierung ein nützliches Werkzeug für die Einführung von Alkylgruppen an aromatischen Ringen ist, ist sie aufgrund der Möglichkeit mehrfacher Substitutionsprodukte möglicherweise nicht immer für die Synthese hochkomplexer Moleküle geeignet. In solchen Fällen können selektivere oder kontrollierte Methoden erforderlich sein, um die gewünschte Synthese zu erreichen.