Cellulose ethers are typically white to yellowish powders or granules that are safe to use and have the ability to dissolve in water. While there are cellulose ethers that do not readily dissolve in water, their sales are minimal compared to the water-soluble varieties.
The production of cellulose ethers involves a chemical reaction between cellulose and low-molecular alkoxylating agents, which can facilitate the incorporation of additional functional groups.
The initial documentation of the manufacturing process for cellulose ethers can be traced back to an article published by W. SUIDA in 1905. The first patents associated with their industrial production were granted as early as 1918.
During the period between 1920 and 1930, carboxymethyl cellulose emerged as the first cellulose ether to gain significant economic importance. This was followed by the introduction of methyl celluloses and hydroxyethyl cellulose approximately a decade later. These three categories of cellulose ethers continue to dominate the market in the present day.
Table of Contents
1. Carboxymethyl Cellulose (CMC)
Carboxymethyl celluloses (CMC) hold the highest market share in terms of sales volume. They are offered in different levels of purity, ranging from “unpurified” to “highly purified,” specifically for food-grade purposes. Within the CMC group, there are also mixed ethers containing hydroxyalkyl substituents, which exhibit predominantly ionic characteristics.
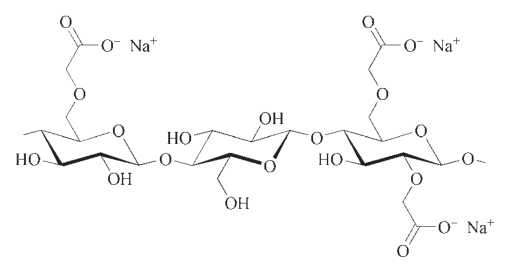
1.1. Applications of Carboxymethyl celluloses (CMC)
The market for CMC can be divided into two segments: “purified” and “unpurified.” However, the definitions of these terms may vary depending on the region and supplier. Generally, CMC products with active content ranging from 55% to 85% are considered “unpurified,” those with 85% to 95% are “semi-purified,” around 98% are “purified,” and those with an active content greater than 99.5% are classified as “highly purified” or high-purity grades.
Annual global sales of CMC amount to approximately 230,000 tons, with purified CMC accounting for 130,000 tons and unpurified CMC totaling 100,000 tons.
Compared to other cellulose ethers, CMC can be produced with less technological input, which explains why there are a relatively large number of manufacturers (over 20) in the market.
Initially, CMC found application in detergents as a soil carrier and in deep-well drilling for oil and water, where it acted as a flotation aid in drilling mud. Unpurified grades were, and in some cases still are, used in these applications.
Purified CMC products are used in various technical areas, such as surface coatings and the paper industry, where they enhance fiber retention, improve filler/pigment/dye yield, strength, printability, and smoothness of paper.
CMC, when combined with gelatin, is used as a coacervate to encapsulate ink in the production of non-carbon copy papers. High-purity grades find applications in the cosmetics and pharmaceutical industries, where CMC serves as a fat-free ointment base or tablet disintegrant.
In the food and pet food production sectors, CMC enhances consistency, acts as a low-calorie substitute for starch and proteins, and controls functions like freeze-thaw stability in frozen products or creaminess in ice cream.
1.2. Synthesis of CMC
CMC is synthesized using a Williamson ether synthesis method from alkali cellulose, sodium chloroacetate, or chloroacetic acid. In the process, chloroacetic acid reacts with caustic soda in situ to form the corresponding salt.
This synthesis occurs in an aqueous or aqueous-alcoholic medium, typically in the form of a slurry. The alcohols commonly employed include ethanol, isopropanol, tert-butanol, or their mixtures.
Alkalinization occurs at room temperature, and the reaction proceeds within a temperature range of 50 °C to the boiling point of the slurry medium under suitable system pressure. It is important to note that the reaction is exothermic, meaning it releases heat during the process.
The reaction is highly temperature-dependent, with an activation energy of 87.9 kJ/mol. The yield of the reaction, relative to chloroacetic acid, typically ranges from 65% to 80%. However, hydrolysis of chloroacetic acid can occur as a side reaction, resulting in the formation of glycolate.
Commercially available CMCs are produced with a degree of substitution ranging from 0.2 to 1.5. Carboxymethylation mainly occurs at the C2 position, followed by C6 and C3 substitution of the anhydroglucose unit, although there is a slight preference for C2 substitution.
1.3. Industrial Processes
During the early stages of CMC production, the cellulose was activated by soaking in alkaline steeping tanks. Once excess caustic soda solution was pressed out, the alkali cellulose was shredded into fibers.
The reaction took place in a kneader, where sodium chloroacetate was added, and temperatures reached 30-35 °C. Subsequently, the reaction was completed in a tumbling drum at 50 °C. The resulting material was washed with a methanol and water mixture, filtered, ground, and finally dried.

a) Cellulose shredding; b) Cellulose buffer; c) Slurry medium dosing vessel; d) Caustic soda dosing vessel; e) Chloroacetic acid dosing vessel; f) Reaction mixer; g) Washing vessel; h) Filtration equipment; i) Dryer; j) Comminuting; k) Screening equipment; l) Slurry medium recycling
The first continuous process, introduced by Wyandotte Chem. Corp. in 1947, involved a rotating drum where sodium hydroxide solution and monochloroacetic acid were added to the ground cellulose. After a dwell time of 3 hours, the product was allowed to “ripen” for 10 hours in drums. However, this process lacked a washing stage, making it suitable only for unpurified CMC.
In contemporary CMC production processes, ground cellulose is typically processed in batches. For low mass fractions of cellulose, it is processed as a suspension, whereas for higher mass fractions, mixers are used with the presence of “inert” media.
Short-chain alcohols are employed as mass-transfer and heat-exchanging media or as suspending agents. Ethanol is commonly used as a slurry medium for processes with a high mass fraction, while isopropanol is utilized in suspension-type processes. By employing multiple sets of equipment in parallel or series, a quasi-continuous operation can be achieved during the activation and reaction stages.
The starting materials, suspension or slurry media, can be solid or liquid at normal room and reaction temperatures, allowing for operation at ambient pressure.
Depending on the desired product purity, the product is washed with alcohol-water mixtures, preferably using the same alcohol used in the reaction. Water cannot be used for washing due to the water-solubility of the products.
To meet purity requirements, it is necessary to remove the alcohols from the product after the washing stage and prior to the grinding and drying processes.
Suspension agents and washing liquids are collected and reprocessed through distillation, extraction, or membrane processes.
2. Methyl and Hydroxyalkyl Methyl Celluloses
Methyl cellulose is a term used to collectively refer to pure methyl cellulose (MC) and hydroxyalkyl methyl celluloses (HAMC). However, pure methyl cellulose constitutes only a small portion of the market share.
In contrast, the mixed ethers hydroxyethyl methyl cellulose (HEMC) and hydroxypropyl methyl cellulose (HPMC) have gained significant recognition, especially in technical applications.
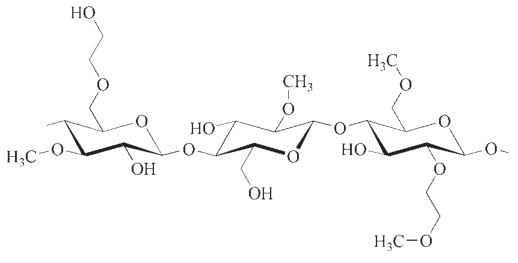
2.1. Applications
The market size for methyl cellulose and hydroxyalkyl methyl celluloses was approximately 120,000 tons in 2003. The Dow Chemical Company emerged as the market leader, closely followed by Shin-Etsu Chemical and Wolff Cellulosics.
High-purity grades of these substances are marketed for applications in the food, pharmaceutical, and cosmetics sectors, while purified products find use in the building materials and industrial domains. The building material sector represents the largest application field by a significant margin.
Specific applications and the types of methyl cellulose products used in the building materials sector vary across regions due to different construction methods and traditions, particularly in dry mortars.
In the United States, joint compounds account for the largest segment, whereas in Europe, MC and HAMC find widespread use in plasters, renders, and tile adhesives.
The efficient application methods employed in modern construction rely on the utilization of methyl celluloses. These substances regulate properties such as water retention, open time, wet adhesion, initial thickening, and setting behavior with low additive contents ranging from 0.01 to 2 wt% relative to the building material system. As a result, cellulose ethers must meet stringent quality requirements.
In the life science sectors, only nonhydroxyalkylated methyl cellulose (modified vegetable gum) and hydroxypropyl methyl cellulose (carbohydrate gum) are employed.
The pharmaceutical industry uses methyl celluloses as tablet bases and in coatings for controlled-release drugs.
In the food and cosmetics industries, the thickening and emulsifying properties of methyl celluloses are exploited to achieve desired consistency and texture.
Notably, highly methylated hydroxypropyl methyl cellulose is employed as a protective colloid in the polymerization of vinyl chloride.
2.2. Synthesis of hydroxyalkyl methyl cellulose
The synthesis of hydroxyalkyl methyl cellulose combines principles of synthesis employed in industrial cellulose ether production. Methylation follows the Williamson ether synthesis, involving the reaction of alkali cellulose with gaseous or liquid methyl chloride, with a stoichiometric amount of NaOH solution consumed.
Side reactions occur, leading to the hydrolysis of methyl chloride into methanol and subsequent etherification of methanol by methyl chloride to form dimethyl ether. These reactions take place within the temperature range of 70 to 120 °C, and methylation is an exothermic process with an activation energy of 80 kJ/mol.
The produced grades exhibit a degree of substitution between 1.7 and 2.3. In the case of pure methylation, the substituent demonstrates a preference for the C2 position, followed by the C6 and C3 positions of the anhydroglucose unit.
During the production of hydroxyalkyl methyl cellulose, alkoxylation of cellulose occurs prior to or concurrently with methylation. Both the cellulose and the formed alkoxy groups can be methylated and alkoxylated, leading to a wide range of different products with tailored properties to meet specific application requirements.
2.3. Industrial Processes
The initial processes developed for the production of methyl cellulose and hydroxyalkyl methyl celluloses operated at ambient pressure and involved gas circulation. In these methods, cellulose underwent activation through a steeping process, followed by shredding and contact with reagents in a mixer.
Continuous extraction of nonreacted gaseous feed materials and byproducts occurred, with the byproducts condensed out and the gas flow recycled back into the reactor. The resulting product underwent washing, filtration, compression, grinding, and drying.
The most widely used process today for batchwise or semibatchwise production of hydroxyalkyl methyl celluloses is the slurry process, conducted at pressures of up to 30 bar.
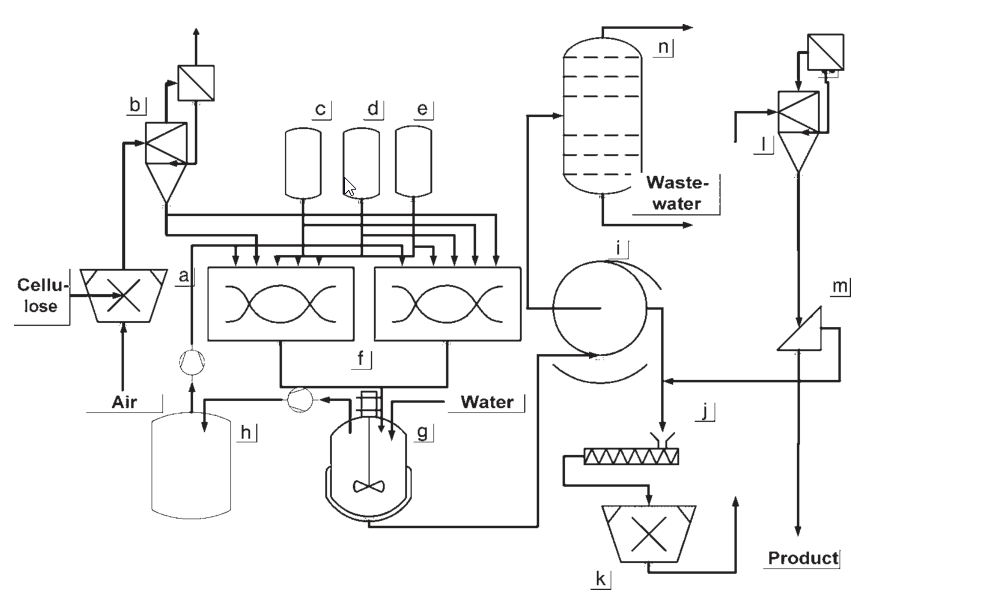
a) Cellulose shredding; b) Cellulose buffer; c) Caustic soda dosing vessel; d) Alkoxylation agent dosing vessel; e) Methyl chloride dosing vessel; f) Reaction mixer; g) Washing vessel; h) Gas buffer; i) Filtration equipment; j) Conditioning equipment; k) Comminuting; l) Stream dryer; m) Screening equipment; n) Slurry medium recycling
Patented processes from the 1950s suggested the use of pressure-resistant reactors without additional inert slurry media, while more recent patents proposed the inclusion of inert slurry media, primarily ethers.
The slurry medium served as a heat transfer medium, evaporating and condensing in a dome-shaped condenser.
The reagents were added to the ground cellulose in a specific sequence depending on the desired product characteristics. The slurry medium had to be added before etherification due to the heat generated during the exothermic reactions.
Upon completion of the reaction, low-boiling slurry media were extracted by reducing the pressure and collected for reuse, while byproducts were discharged. High-boiling slurry media were separated during the washing stage and subsequently reprocessed.
Suspension-type processes were mentioned in various patents, offering advantages in terms of simple process engineering but presenting disadvantages in the more complex preparation of the suspension agent.
The flocculation point of methyl cellulose and hydroxyalkyl methyl celluloses allowed the products to be washed with water above this point. This involved transferring the contents of the reactor to a stirred tank filled with hot water or suspending them in the reaction mixer, where salts formed during the reaction dissolved and any unreacted activation reagents were neutralized with acid.
The suspension was then separated in a solid-liquid separating unit. Additional washing stages might be necessary depending on the product specifications to ensure compliance with byproduct content restrictions.
Depending on the specific product, the hydroxyalkyl methyl cellulose underwent conditioning for the grinding and drying stage. Drying and grinding could be conducted consecutively or in combined milling and drying units.
Achieving the required fineness of grind, often with a particle size of less than 63 mm in over 50 wt% of the product, typically involved screening and sifting stages, with coarse-grained material recycled.
3. HydroxyethylCellulose(HEC)
Hydroxyethyl celluloses occupy a significant position as the third largest product group in the market. These cellulose derivatives are characterized as non-ionic and exhibit solubility in both cold and hot water.
The manufacturing process for hydroxyethyl celluloses was initially documented in 1920 through a patent awarded to Farbenfabriken Bayer.
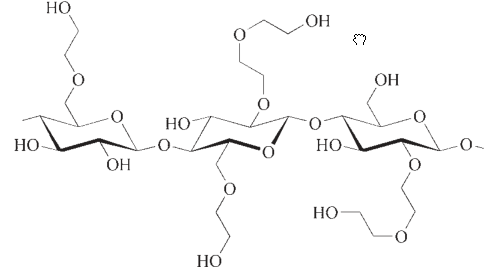
3.1. Applications of HydroxyethylCellulose (HEC)
The hydroxyethyl cellulose (HEC) market is primarily dominated by Hercules Incorporated/Aqualon and Dow Chemical Company.
With annual sales reaching approximately 60,000 tons, the majority of HEC is used in the construction industry, specifically in surface coatings.
HEC also finds applications in cosmetics, where it competes with derivatives of hydroxypropyl methyl cellulose (HPMC).
Additionally, HEC is employed in drilling fluids and serves as a protective colloid in emulsion polymerization processes.
In the paint industry, HEC holds the largest market share among cellulose ether product groups. Although HEMC, HPMC, and CMC-based products have smaller shares, they are well-established in these applications due to technical advantages and cost considerations.
In addition to pure HEC, this product group encompasses mixed cellulose ethers similar to HEC, such as ethyl hydroxyethyl cellulose (EHEC) and hydrophobically modified (hm) variants of HEC.
The hydrophobic properties of hm-HEC are achieved through secondary substitution, typically with long-chain alkyl residues (ranging from C12 to C24).
The hydrophobically modified grades, similar to purely synthetic associative thickeners, offer additional effects by interacting with particle surfaces, particularly the binder in latex paints, and by forming micelles and mixed micelles with other surfactants present in the paint formulation. T
hese features are especially beneficial in high-quality paint formulations, reducing spattering during roller application, and improving brush resistance and leveling properties.
3.2. Synthesis of HydroxyethylCellulose (HEC)
Hydroxyethyl cellulose (HEC) is produced by the reaction of cellulose with ethylene oxide, a process known as ethoxylation. This ethoxylation reaction only requires small amounts of alkaline solution as a catalyst.
During the ethoxylation process, both the cellulose alcoholate and the hydroxyl ions present can react with ethylene oxide or with the glycolates formed during the reaction.
Excessive alkali can reduce the yield of the main reaction, but a minimum amount of caustic soda solution is necessary to break down the cellulose.
The ethoxylation reaction occurs in the presence of an “inert” solvent such as isopropanol, tert-butanol, 1,2-dimethoxyethane, or acetone. It starts at a low temperature (around 30 °C) and is highly exothermic.
The degree of substitution in HECs is controlled by the amount of ethylene oxide added, resulting in molar substitutions of 1.5 and 3.5. The yield of the reaction typically ranges from 40% to 75% relative to the amount of ethylene oxide used.
The reaction of ethylene oxide follows a preferred order of reactivity, with alkoxy groups being most reactive, followed by C6 positions, and then C2 and C3 positions (with some distance between them).
The reaction rates can be influenced by adjusting the alkali concentration, such as through partial neutralization. After the completion of the reaction, any excess alkali added must be neutralized.
3.3. Industrial Processes
The production of hydroxyethyl cellulose (HEC) typically involves suspension processes conducted at pressures higher than ambient pressure. Stirred pressure vessels are commonly used for the reaction.
In the production process, the ground cellulose is suspended in a suspending medium and mixed with the alkalizing agent. Liquid ethylene oxide is then added to the suspension, and the reaction is allowed to proceed for approximately 2 hours.
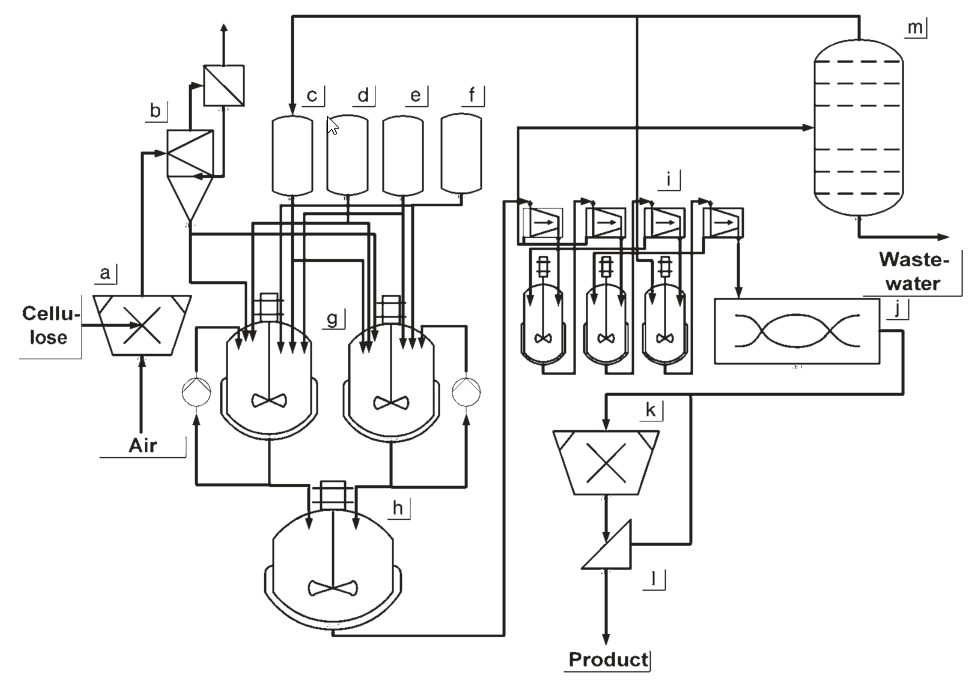
a) Cellulose shredding; b) Cellulose buffer; c) Slurry medium dosing vessel; d) Caustic soda dosing vessel; e) Acid dosing vessel; f) Alkoxylation agent dosing vessel; g) Stirred reaction tank; h) Washing vessel; i) Washing and filtration process; j) Stream dryer; k) Comminuting; l) Screening equipment; m) Slurry medium recycling
After the reaction, it is necessary to wash out salts and byproducts from the HEC. This requires suitable equipment for washing and solid-liquid separation, either in a series or a combined unit. Since HEC does not have a flocculation point, mixtures of water and an organic solvent are used for the washing process. Then, the HEC undergoes drying and grinding steps.
Simultaneously, the suspension medium and any extracting agents used in the process need to be regenerated and recycled. Distillation is typically employed as the chosen method for regeneration.
4. Hydroxypropyl Cellulose (HPC)
Among the various cellulose ethers used worldwide, hydroxypropyl celluloses (HPC) represent the smallest product group.
These cellulose ethers exhibit a range of properties, including simple swellability, solubility in cold water, and enhanced thermoplasticity, which allows them to be processed in melt extruders.
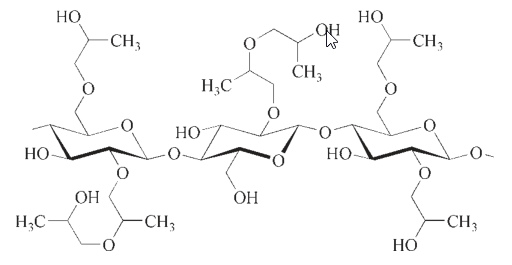
The introduction of hydroxypropyl cellulose in the market dates back to the late 1960s when it was first launched in the USA.
4.1. Applications of Hydroxypropyl Cellulose (HPC)
The global market for hydroxypropyl cellulose is relatively small, with an annual volume of less than 10,000 metric tons.
The primary industries that uses hydroxypropyl cellulose are pharmaceuticals and cosmetics.
High-purity grades of hydroxypropyl cellulose are specifically designed for food and pharmaceutical applications, while purified grades are supplied to the cosmetics industry and for technical applications.
4.2. Synthesis of Hydroxypropyl Cellulose (HPC)
The synthesis of hydroxypropyl cellulose (HPC) is similar to that of hydroxyethyl cellulose (HEC). Before the reaction with propylene oxide takes place, the cellulose is activated using caustic soda solution.
The reaction of cellulose with propylene oxide has a higher activation energy and requires a higher reaction temperature compared to the reaction with ethylene oxide in HEC synthesis. This means that the reaction conditions for HPC synthesis are slightly more demanding.
During the reaction, propylene glycol and polypropylene glycols are produced as byproducts. These byproducts, along with the salts formed during the neutralization stage, need to be removed in one or several washing stages. The washing process is essential to eliminate impurities and achieve the desired purity of the HPC product.
4.3. Industrial Processes
The production processes for hydroxypropyl cellulose (HPC) are largely similar to those used for hydroxyethyl cellulose (HEC). The reaction for HPC is typically conducted in a slurry, similar to HEC.
Various slurry media have been described in the literature, including hexane, toluene, tetrahydrofuran, dioxane, and common alcohols. Additionally, the gas-phase method, which produces high-quality grades with a high degree of substitution, can also be employed for HPC production.
One notable difference between HPC and HEC is that highly substituted HPC has a thermal flocculation point. This characteristic allows for washing with hot water, which is not possible with HEC. This provides an advantage in the washing process for HPC, facilitating the removal of salts and byproducts from the product.
5. Uses of Cellulose ethers
Cellulose ethers find applications in a wide range of industries and fields, including oil drilling, industrial processes such as polymerization, surface coatings, construction materials, healthcare, cosmetics, food, and pharmaceuticals. However, not all types of cellulose ethers are equally suitable for every application.
Even though the required quantity of cellulose ethers in many applications is relatively small, typically between 0.02 and 2%, they play an important role in imparting specific properties such as water-binding capacity, film formation, thickening, and control of rheological properties. Many modern products and processing techniques rely on the use of cellulose ethers.
Each field of application has its specific requirements, often necessitating modifications to the cellulose ether product. Once the appropriate product category is selected, parameters such as the type of substitution, viscosity range, product purity, and physical state (forming) need to be fine-tuned.
This fine-tuning process requires expertise in understanding the properties of cellulose ethers and their application in different systems and methods.
Many suppliers of cellulose ethers offer not only the products themselves but also technical expertise and additional services to assist customers in finding the right solutions for their specific needs. This includes knowledge of the properties of cellulose ethers, their customization, and support in application-related issues.
Reference
- Cellulose Ethers; Ullmann’s Encyclopedia of Industrial Chemistry. – https://onlinelibrary.wiley.com/doi/10.1002/14356007.a05_461.pub2
FAQ: Cellulose Ethers
Cellulose ethers are versatile materials used in various industries and applications. They are primarily employed for their properties such as thickening, water-binding capacity, film formation, and control of rheological properties. Common applications include surface coatings, construction materials, pharmaceuticals, cosmetics, food, oil drilling, and industrial processes.
Cellulose ethers encompass a range of derivatives. Some examples include:
1. Methyl cellulose (MC)
2. Hydroxyethyl cellulose (HEC)
3. Hydroxypropyl cellulose (HPC)
4. Ethyl hydroxyethyl cellulose (EHEC)
5. Hydroxypropyl methyl cellulose (HPMC)
6. Carboxymethyl cellulose (CMC)
The primary raw material for cellulose ether production is cellulose, which is typically derived from plant sources such as wood pulp or cotton. Chemical modifications are carried out on cellulose using specific reagents to create different types of cellulose ethers.
Cellulose ethers are synthesized through chemical reactions involving cellulose and various reagents. The most common method involves activating cellulose with an alkaline solution, followed by reacting it with an etherifying agent such as methyl chloride (for methyl cellulose) or ethylene oxide (for hydroxyethyl cellulose). The reaction conditions, including temperature and reaction time, vary depending on the specific cellulose ether being produced.
Cellulose ethers are manufactured through industrial processes by companies specializing in cellulose chemistry. They are produced in dedicated facilities using cellulose as the raw material and employing specific synthesis methods to achieve the desired cellulose ether product.
Cellulose ethers serve as components in a wide range of products. Some examples include:
1. Paints and coatings: They improve viscosity, provide film formation, and enhance brushability.
2. Construction materials: They contribute to mortar and tile adhesives, cement-based renders, and gypsum products, improving workability and water retention.
3. Pharmaceuticals: They are used as binders, thickeners, and film-formers in tablets, ointments, and suspensions.
4. Cosmetics: They are utilized in personal care products like lotions, creams, and shampoos for their thickening, stabilizing, and emulsifying properties.
5. Food: They act as stabilizers, thickeners, and texture modifiers in food products such as sauces, dressings, and dairy items.
6. Oil drilling: They aid in controlling rheology and fluid loss in drilling fluids.
7. Industrial processes: They find applications in polymerization reactions, emulsion polymerization, and as protective colloids.