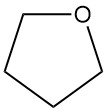
Tetrahydrofuran (THF), also known as oxolane, is a cyclic ether with the chemical formula C4H8O. It has a wide application in the chemical industry.
Table of Contents
1. Physical Properties of Tetrahydrofuran
Tetrahydrofuran (THF) is a colorless, volatile, polar liquid commercially available with a minimum purity of 99.9 wt% (when distilled). It possesses a characteristic acetone-like odor. THF is completely miscible with water, alcohols, ethers, and other common solvents.
Table 1 presents some physical properties of THF.
Property | Value |
---|---|
Molar mass | 72.1 g/mol |
Boiling point | 66 °C |
Melting point | -108.5 °C |
Critical temperature | 267 °C |
Critical pressure | 5.19 MPa |
Critical density | 0.322 g/cm3 |
Density at 20 °C | 0.886 |
Refractive index at 20 °C | 1.4073 |
Specific heat capacity | 1.765 J g-1 K-1 |
Heat of vaporization (66 °C, 101.3 kPa) | 435 J/kg |
Heat of combustion | -35,141 kJ/kg |
Explosive limits in air (25 °C) | 1.5 vol% (lower), 12.0 vol% (upper) |
Flash point (Abel-Pensky) | -22 °C |
Dipole moment | 5.84 × 10-30 C.m |
Dielectric constant (20 °C) | 7.6 |
2. Chemical Reactions of Tetrahydrofuran
Tetrahydrofuran is a valuable starting material for important reactions. These include cationic polymerization with concurrent ring-opening of THF to produce high-molecular-weight bifunctional glycol ethers with various chain lengths.
These products are of economic importance in the production of essential plastics. Additionally, ring-cleavage reactions of tetrahydrofuran are the basis for dehydration to butadiene, oxidation to succinic acid, and carboxylation to adipic acid, or γ-valerolactone.
THF is the preferred reaction medium for conducting Grignard reactions or reductions using reagents like LiAlH4. It is also used as a ligand in coordination complexes, such as those occasionally employed in stereospecific polymerizations.
Benzene reacts with tetrahydrofuran in sulfuric acid to produce tetralin (1,2,3,4-tetrahydronaphthalene).

However, THF readily reacts with oxygen (e.g., upon contact with air), forming an unstable hydroperoxide as the primary product. The addition of hydroquinone or 2,6-di-tert-butyl-p-cresol (BHT) (e.g., 250 mg/kg) can inhibit peroxide formation. Distillation of tetrahydrofuran containing peroxides concentrates the peroxides, leading to a high risk of explosion, even on a laboratory scale.
3. Production of Tetrahydrofuran
3.1. Production of Tetrahydrofuran from Acetylene and Formaldehyde
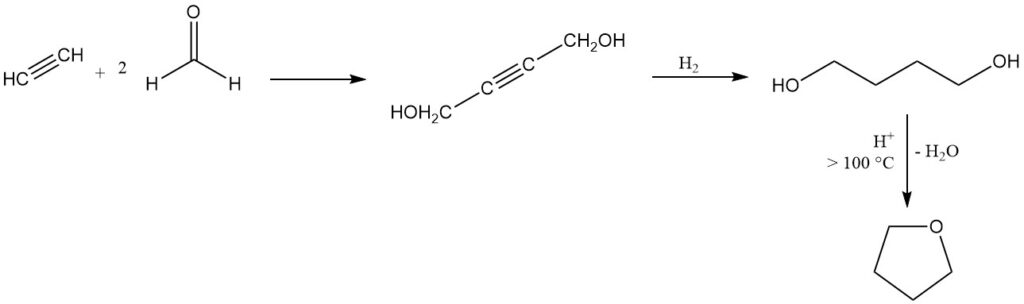
Tetrahydrofuran is produced by the Reppe process, developed in the 1930s, which remains a dominant industrial method in Europe and the United States.
In this process, acetylene reacts with formaldehyde to produce 2-butyne-1,4-diol, followed by hydrogenation to 1,4-butanediol which then undergoes acid-catalyzed cyclization with the elimination of water above 100 °C to yield THF.
Several catalysts are suitable for this cyclization, including inorganic acids, acidic aluminosilicates, and earth or rare-earth metal oxides. An almost quantitative conversion and near-100% yield can be achieved in a continuous, atmospheric pressure process using alumina as the catalyst.
This requires continuous distillation of the formed tetrahydrofuran out of the reaction mixture while simultaneously feeding pure 1,4-butanediol at a matching consumption rate. This method has high catalyst efficiency, allowing for significant THF production per unit of catalyst.
BASF had developed a medium-pressure process for selective conversion of crude butanediol to THF with minimal additional energy.
The THF-steam mixture obtained from the cyclization is first rectified to isolate the corresponding azeotrope (5.3 wt% water, boiling point 62.3 °C), which is treated with alkali hydroxide, followed by distillation to obtain anhydrous THF.
Industrial processes can overcome the formation of azeotrope mixtures by distillation under pressure.
3.2. Production of Tetrahydrofuran by Butadiene Acetoxylation
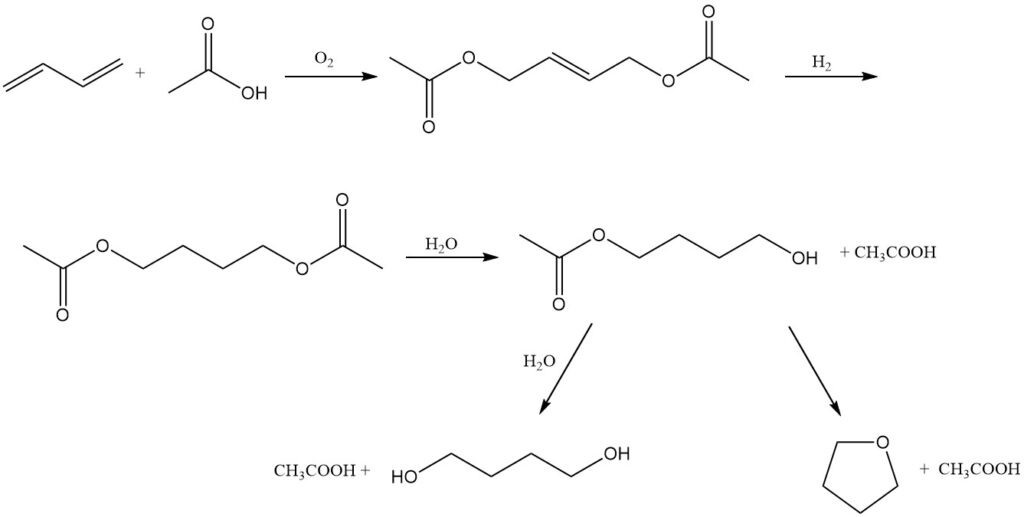
Mitsubishi-Kasei Corporation in Japan offers an alternative route for the co-production of 1,4-butanediol and tetrahydrofuran, using butadiene as the starting material. This process can be explained by the following reactions:
Oxidation: Butadiene undergoes oxidation at 3 MPa and 80 °C in the presence of a palladium-tellurium catalyst, acetic acid, and a nitrogen-oxygen mixture. This reaction yields 1,4-diacetoxy-2-butene.
Hydrogenation: The obtained 1,4-diacetoxy-2-butene is then hydrogenated to form 1,4-diacetoxybutane.
Hydrolysis: Finally, 1,4-diacetoxybutane is hydrolyzed to 1,4-butanediol or THF.
3.3. Production of Tetrahydrofuran by Propylene Oxide Process
Arco produces 1,4-butanediol through a process that involves the following steps:
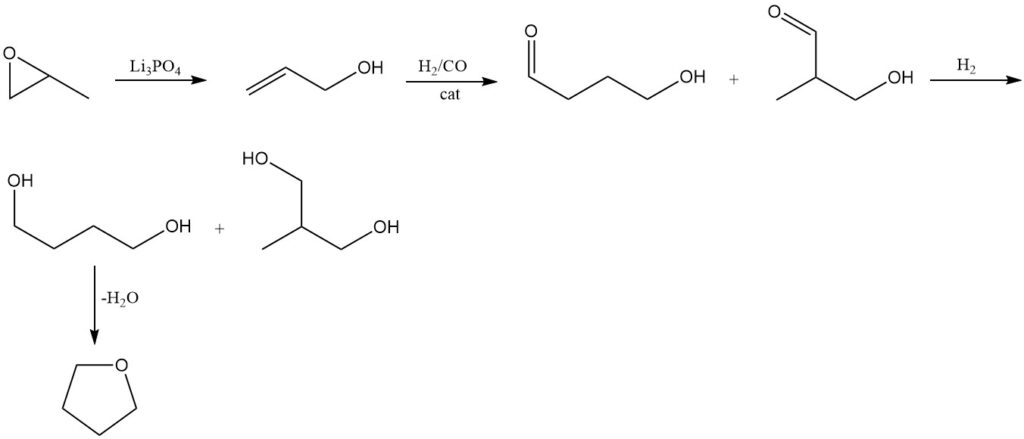
Propylene oxide is isomerized to allyl alcohol using conventional methods at 250–300 °C and 1 MPa pressure over a trilithium orthophosphate (Li3PO4) catalyst.
The resulting allyl alcohol undergoes hydroformylation using the Kuraray process. This reaction produces 4-hydroxybutyraldehyde as the primary product along with 3-hydroxy-2-methylpropionaldehyde as a byproduct.
Subsequent hydrogenation of the obtained aldehydes forms 1,4-butanediol as the major product, accompanied by the formation of 2-methyl-1,3-propanediol.
As in the previous methods, tetrahydrofuran is produced by dehydrating 1,4-butanediol using an acid catalyst.
3.4. Production of Tetrahydrofuran by Maleic Anhydride Hydrogenation

Due to its chemical structure, maleic anhydride is a promising starting material for the synthesis of butanediol, THF, and γ-butyrolactone. Mitsubishi-Kasei originally developed and implemented an industrial-scale process using maleic anhydride. However, they have since abandoned this method in favor of their newer butadiene acetoxylation process.
Several companies, including Davy-McKee Ltd., BP, Sohio, and Shinwha Petrochemical, have adopted similar processes for butanediol and tetrahydrofuran production. For example, Shinwha Petrochemical in South Korea operates a plant based on the McKee process, with a capacity of 20,000 tons of butanediol per year.
The initial step in this process is the vapor-phase hydrogenation of ethyl maleate. The reaction conditions can be manipulated to control the ratio of THF to butanediol in the final product mixture.
There is a growing interest in using maleic anhydride as a feedstock for tetrahydrofuran production, and it appears to be gaining traction as a potential replacement for the Reppe process.
3.5. Production of Tetrahydrofuran by n-Butane-Maleic Anhydride Process

Du Pont offers a novel two-stage process for tetrahydrofuran synthesis using n-butane as the starting material.
n-Butane is oxidized to maleic anhydride with a high yield (70–75%) using a unique, transportable, and abrasion-resistant oxidation catalyst.
The resulting aqueous maleic acid solution undergoes hydrogenation over a specialized rhenium-doped palladium catalyst. This step offers flexibility, allowing for the selective production of either butanediol or THF based on process requirements.
The process has been successfully piloted and was implemented in the Spanish province of Asturias, with an annual production capacity of 45,000 tons.
3.6. Production of Tetrahydrofuran by Pentosan/Furfural Processes
Interest in tetrahydrofuran production from furfural has grown due to the use of renewable resources. Pentosans, abundant in agricultural waste products, are the starting materials.
The process for THF production from furfural involves two catalytic steps:
- Furfural undergoes catalytic decarbonylation to form furan.
- The furan is then hydrogenated to yield THF.
4. Uses of Tetrahydrofuran
Tetrahydrofuran is used in a variety of sectors, with the largest volume being as a monomer for poly(tetramethylene oxide) (PTMO), also known as poly(tetramethylene ether glycol) (PTMEG) or polytetrahydrofuran (PTHF). PTMO is an important component in the production of:
- Thermoplastic polyurethanes
- Elastic fibers
- Molded elastomers
- Copolyesters
- Copolyamides
- Polyurethane coatings
Commercial PTMO is available under various trade names, including Terathane (DuPont), Polytetrahydrofuran (BASF), and Polymeg (Quaker Oats).
A smaller portion of THF is used as solvent for applications such as coatings, adhesives, and special varnishes based on materials like poly(vinyl chloride) (PVC) or polyurethanes and as cosolvent in printing inks, as an extracting agent and as reaction medium, particularly for organometallic syntheses in organic chemistry.
It is also a common laboratory reagent and an intermediate in the chemical syntheses of consumer and industrial products such as nutritionals, pharmaceuticals, and insecticides.
5. Toxicology of Tetrahydrofuran
Extensive research by BASF’s Industrial Hygiene and Pharmacology Institute suggests that THF exhibits minimal toxicity, comparable to acetone, contrasting earlier reports likely based on impure samples.
Animal studies involving chronic exposure (1 year at 1000 ppm, 2 years at 3000 ppm) to THF did not reveal significant poisoning symptoms in rats, cats, or rabbits. However, these concentrations (1000-3000 ppm) would cause severe mucous membrane irritation in humans.
Similar to ethanol, THF is rapidly metabolized by the body.
Due to its strong solvent properties, tetrahydrofuran dissolves the outer keratin layers of skin and mucous membranes, rapidly penetrating deeper tissues. This characteristic leads to severe irritation but does not cause sensitization (allergic reaction).
Peroxide formation during storage can exacerbate skin irritation, and contact with wounds or beneath fingernails can induce significant pain.
THF is readily absorbed through the skin, similar to methanol. Prolonged skin contact should be avoided, and appropriate hand protection is recommended.
The established workplace exposure limit for tetrahydrofuran is 200 ppm (mL/m³). This value is set to address local mucous membrane irritation caused by THF vapors, not its narcotic effects, which require much higher concentrations.
References
- Tetrahydrofuran, Ullmann’s Encyclopedia of Industrial Chemistry. – https://onlinelibrary.wiley.com/doi/10.1002/14356007.a26_221.pub3
- Polyethers, Tetrahydrofuran and Oxetane Polymers; Kirk-Othmer Encyclopedia of Chemical Technology. – https://onlinelibrary.wiley.com/doi/10.1002/0471238961.2005201816182103.a01
- Tetrahydrofuran; Hamilton & Hardy’s Industrial Toxicology. – https://onlinelibrary.wiley.com/doi/10.1002/9781118834015.ch70