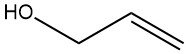
Allyl alcohol is an organic compound with the chemical formula C3H6O. It is a clear, colorless liquid with a pungent, garlic-like odor and is classified as both a primary alcohol and an unsaturated alcohol due to the presence of a double bond in its molecular structure.
The double bond is located between the second and third carbon atoms in the molecule, and the hydroxyl (-OH) group is attached to the first carbon atom.
Table of Contents
1. Physical Properties of Allyl Alcohol
Allyl alcohol (IUPAC name: prop-2-en-1-ol) is a colorless, mobile liquid with an irritating odor. It has a molecular formula of C3H6O and a molar mass of 58.08 g/mol. The melting point is -129 °C and the boiling point is 96.9 °C (101.3 kPa). Allyl alcohol is miscible with water and organic solvents.
Property | Value |
---|---|
Relative density |
|
Refractive index |
|
Critical temperature | Tcrit = 271.9 °C |
Heat of vaporization at 101.3 kPa | 39.98 kJ/mol |
Specific heat capacity of vapor | Cp (g), (20 °C and 101.3 kPa) = 2.428 kJ/kg.K |
Specific heat capacity of liquid | Cp (l), (20.5 – 95.5 °C) = 2.784 kJ/kg.K |
Heat of combustion at constant p | 1853.8 kJ/mol |
Viscosity |
|
Surface tension |
|
Dipole moment | 1.63 D |
Dielectric constant | at 16.2 °C, λ = 60 cm : 20.3 |
Ignition limits in air | at 100 °C, 101.3 kPa = 2.5 – 18.0 vol % |
Flash point (closed cup) | 22.2 °C |
Allyl alcohol is miscible with water and organic solvents in all proportions at 20 °C.It forms binary azeotropes with water, benzene, diallyl ether, allyl chloride, trichloroethylene and ternary azeotropes with (water, benzene) and (water,diallyl ether).
2. Chemical Reactions of Allyl Alcohol
Allyl alcohol is a versatile compound that can undergo a variety of reactions, including oxidation, reduction, hydrogenation, condensation, and addition reactions.
At room temperature, allyl alcohol is stable in the form of a liquid substance. However, heating allyl alcohol to temperatures exceeding 100 °C results in the creation of water-soluble polymers (polyallyl alcohols), which react with alkenoic acids to yield drying oils.
It also can be grafted to polyimides or copolymerized with styrene in the presence of oxygen.
Flame-resistant polyurethane foams are produced by condensation reaction between allyl alcohol and methyl glucoside polyethers, followed by bromination and subsequent addition of isocyanates.
Allyl alcohol can be hydroxylated with hydrogen peroxide in the presence of tungsten acid to form glycerol. This reaction is commercially important for the production of glycerol.

The hydroxylation using organic hydroperoxides with a vanadium catalyst yields glycidol (oxiranylmethanol), which can also be obtained via the reaction of allyl alcohol with peracids.
Dehydrogenation in gas phase with air in the presence of catalysts such as palladium, silver, or copper leads to the formation of acrolein.
Liquid-phase oxidation of allyl alcohol using a palladium catalyst produces acrylic acid and acrolein with a selectivity of 83%.
The catalytic hydrogenation of allyl alcohol gives 1-propanol.
Chlorination of allyl alcohol in an aqueous solution produces mono- and dichlorohydrins of glycerol which can be further hydrolyzed to yield glycerol.
Bromination in an aqueous solution buffered by calcium chloride results in the formation of yielding 2,3-dibromo-1-propanol, a compound utilized in flame-resistant materials.
The reaction of allyl alcohol with allyl chloride produces diallyl ether (boiling point: 94 °C), while with methallyl chloride yields allyl methallyl ether.
Allyl alcohol can add to carbon tetrachloride by radical initiation to form 2,4,4,4-tetrachloro-1-butanol (intermediate used in flame-retardant).
It can be hydroformylated in the presence of cobalt carbonyl to form 4-hydroxybutyraldehyde. With rhodium-complex catalysts, the 4-hydroxybutyraldehyde yield is improved to 80 %. The aldehyde can then be hydrogenated to 1,4-butanediol which is a valuable monomer for the synthesis of polyurethanes.
If hydroformylation of allyl alcohol occurs in the vapor phase using rhodium triphenylphosphine complexes supported on porous carriers, a high yield of tetrahydro-2-furanol is achieved (94%).
Allyl alcohol can be carbonylated in acetic acid solution with a palladium chloride catalyst to form 3-butenoic acid.
3. Production of Allyl Alcohol
Allyl alcohol is typically produced from propene, which is a gaseous hydrocarbon. There are a variety of ways to produce allyl alcohol from propene, but the two most common methods are: the allyl chloride process and the propylene oxide process.
3.1. Hydrolysis of Allyl Chloride
The hydrolysis of allyl chloride is a commercial process for producing allyl alcohol. Allyl chloride is reacted with a dilute sodium hydroxide solution at 150 °C and 1.3 – 1.4 MPa, yielding 85 – 95 % allyl alcohol.

Byproducts are diallyl ether (5 – 10 %), chloropropenes, propionaldehyde, and high-boiling material.
The allyl chloride and the aqueous alkaline solution must be mixed thoroughly to maintain a constant pH value. The allyl chloride must be converted nearly quantitatively because it is corrosive and cannot be economically recovered. The reaction is therefore carried out in a recycle reactor, with nickel being the most suitable reactor material.
A commercial plant for the production of allyl alcohol by continuous allyl chloride hydrolysis is shown in Figure 1. Water is removed from the raw allyl alcohol by azeotropic distillation with diallyl ether as an entrainer. The raw allyl alcohol – water azeotrope (72 % allyl alcohol) may be used without further purification for some reactions.
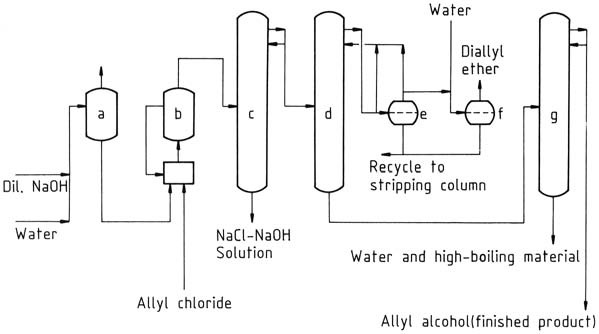
a) Preheater; b) Hydrolysis reactor with recycle system; c) Stripping column; d) Dehydration column; e) Separator; f) Diallyl ether washing tank; g) Allyl alcohol purification column
Here are some additional details about the hydrolysis of allyl chloride:
- The reaction is exothermic, so it is important to control the temperature to prevent the formation of byproducts.
- The reaction is also corrosive, so it is important to use corrosion-resistant materials for the reactor and piping.
- The byproducts of the reaction can be recycled or sold as by-products.
- The azeotropic distillation step is used to remove water from the raw allyl alcohol. This step is necessary to obtain a high purity allyl alcohol product.
3.2. Isomerization of Propene Oxide
The catalytic rearrangement of propene oxide is now more widely used in commercial production than the hydrolysis of allyl chloride. The preferred catalyst for this reaction is lithium phosphate.

In the vapor-phase process, propene oxide vapor is directed over a lithium phosphate catalyst, with temperatures ranging from 250 to 350 °C. This catalyst is composed of up to 30% inert material in a fixed-bed structure. Conversions is around 70 – 75%, accompanied by an allyl alcohol selectivity of 97%.
The resulting space-time yields is 0.5 kg of allyl alcohol per liter of catalyst per hour. Olin Mathieson employs a lithium phosphate catalyst incorporating 1% alkali hydroxide; however, this catalyst needs to be regenerated after 40 hours by acetone washing.
A distinct catalyst, formulated by Chemische Werke Hüls, contains 73.6% lithium phosphate and 17.5% silica, requiring no regeneration. Remarkably, even after 1200 hours, it maintains an allyl alcohol selectivity of 97.3%.
While lithium arsenate has been suggested as an isomerization catalyst, it offers no substantial advantage over lithium phosphate. An earlier method, catalyzed by chromium oxide and developed by Wyandotte Chemical Corp., demonstrates significantly lower conversions and selectivities.
In the liquid-phase process, the Progil process uses a finely ground lithium phosphate catalyst suspended in high-boiling solvents such as terphenyl or alkyl benzenes. Propene oxide is introduced into the suspension at 280 °C.
This variant achieves a conversion rate of 60%, an allyl alcohol selectivity of 92%, and a space-time yield of 1 kg of allyl alcohol per liter per hour. Catalyst lifetimes span 500 – 1000 hours.
A comparable technique, patented by Jefferson Chemical Co., utilizes a solvent mixture of biphenyl and diphenyl ether.
3.3. Hydrolysis of Allyl Acetate
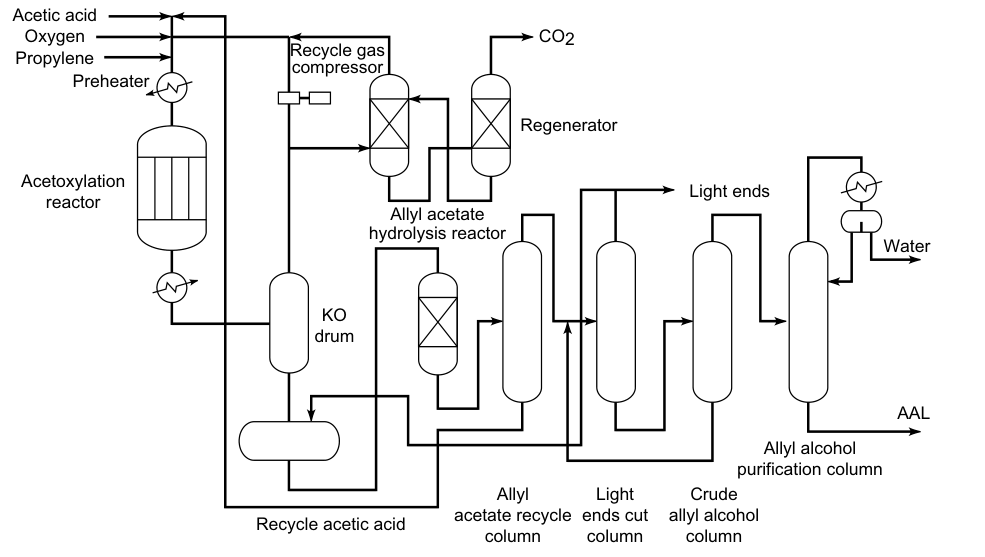
Propene, acetic acid, and oxygen react in the gas phase over palladium catalysts to form allyl acetate:
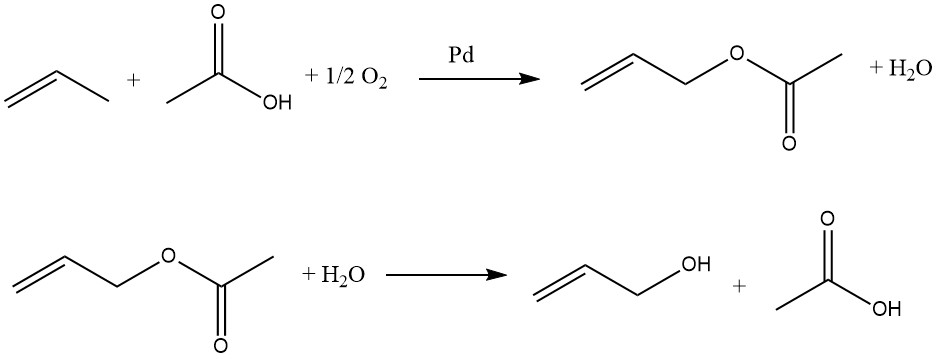
This reaction is exothermic, so the temperature of the reactor must be controlled. The allyl acetate is then hydrolyzed to allyl alcohol in a separate reactor. The acetic acid is recovered and reused in the oxidation of propene. Therefore, only propene and oxygen are required as raw materials for the preparation of allyl alcohol.
This process does not require chlorine, which makes it more environmentally friendly than other methods of producing allyl alcohol. Allyl acetate can be hydrolyzed by heating it to about 230 °C and 3 MPa.
In the Bayer process, hydrolysis is carried out catalytically over an acid cation exchanger (sulfonated polystyrene) at 100 °C. The overall yield of allyl alcohol is 90%.
3.4. Hydrogenation of Acrolein
Allyl alcohol is synthesized by catalytic hydrogenation of acrolein in the vapor phase. By using cadmium-zinc catalysts, a yield of up to 70% can be attained, and similar results can be obtained using silver-cadmium alloys supported on inert carriers like alumina or silica.

Alternatively, acrolein can be reduced by ethanol or isopropyl alcohol in the presence of a mixture of magnesium oxide and zinc oxide. This reaction occurs in the vapor phase at 400°C, resulting in allyl alcohol yields as high as 80%.
4. Uses of Allyl Alcohol
The uses of allyl alcohol are as follows:
- Glycerol Production: Allyl alcohol was initially employed as a raw material in the manufacturing of glycerol by companies such as Daicel Chemical Company.
- Monomer for Diethylene Glycol Bis(allyl Carbonate): Before 1985, allyl alcohol was utilized as a monomer in the production of diethylene glycol bis(allyl carbonate), which is utilized in the creation of plastic optical lenses.
- Epichlorohydrin Production: Showa Denko K.K. began utilizing allyl alcohol as a precursor in the production of epichlorohydrin, a compound used in various applications. Other epichlorohydrin manufacturers also considered transitioning to the allyl alcohol process.
- 1,4-Butanediol Production: ARCO Chemical Company established a significant allyl alcohol production plant and employed allyl alcohol as a raw material in the manufacturing of 1,4-butanediol. This is a notable application, marking the first cace of industrially producing 1,4-butanediol using allyl alcohol.
- Production of Allyl Esters: Allyl alcohol serves as a primary raw material for producing allyl esters, specifically diallyl phthalates and allyl methacrylate.
- Production of Allyl Ether: Allyl alcohol is also used in the production of allyl ether, specifically allyl glycidyl ether.
- Styrene-Allyl Alcohol Copolymer: A styrene-allyl alcohol copolymer is manufactured by Monsanto Chemical Company. This copolymer finds applications in water-soluble paints, alkyd resins, and urethanes as polyols.
- Allyl alcohol undergoes copolymerization reactions with other monomers to produce intermediates used in the fabrication of flame-resistant materials or as a nematocide, fungicide, or preservative.
5. Toxicology and Occupational Health
Allyl alcohol has been extensively studied for its irritating and toxic effects. Its odor can be perceived at approximately 0.8 ppm.
Concentrations between 6 and 12 ppm cause nasal irritation, while 25 ppm induces severe eye irritation with symptoms like tearing, sensitivity to light, blurred vision, and eye pain.
Higher concentrations can lead to corneal necrosis and temporary blindness. Sensitive individuals may experience eye irritation at concentrations as low as 2 to 5 ppm.
In animal studies, daily inhalation of allyl alcohol vapor at concentrations of 2 to 7 ppm for 7 hours per day over 6 months was tolerated by dogs, rabbits, guinea pigs, and rats.
The threshold limit value (TLV) and maximum allowable concentration (MAK) for allyl alcohol are both set at 2 ppm. The short-term exposure limit is higher, at 4 ppm.
Allyl alcohol has shown hepatotoxic effects, with liver cell necrosis observed in rats after oral and intraperitoneal administration. Single oral applications caused liver necrosis in rats, leading to fatalities. The LD50 for rabbits is between 50 and 80 mg/kg, and for rats, it is 64 mg/kg.
Skin contact with allyl alcohol poses a risk of systemic intoxication due to its high absorption rate. Even small amounts, like a single drop (approximately 50 mg), can cause systemic effects alongside local irritation.
Rats exposed to 50 ppm of allyl alcohol in their drinking water for 15 weeks showed tolerance without noticeable adverse effects.
These findings highlight the toxic and irritating nature of allyl alcohol, with various concentration thresholds and potential effects on different routes of exposure. Occupational safety guidelines and the potential risks associated with skin exposure are significant considerations when handling this compound.
References
- Allyl Compounds; Ullmann’s Encyclopedia of Industrial Chemistry. – https://onlinelibrary.wiley.com/doi/10.1002/14356007.a01_425
Allyl Alcohol and Monoallyl Derivatives; Kirk-Othmer Encyclopedia of Chemical Technology. – https://onlinelibrary.wiley.com/doi/10.1002/0471238961.0112122514010701.a01.pub2
FAQ
The common name for allyl alcohol is “propenol“.
Allyl alcohol is used as a precursor for the production of glycerol, allyl esters, and other chemicals. It’s also used in the synthesis of polymers, flame-resistant materials, and pharmaceuticals.
Yes, allyl alcohol is toxic and can be harmful if ingested, inhaled, or absorbed through the skin. It can cause irritation to the eyes, skin, and respiratory tract.
Allyl alcohol is primarily an industrially synthesized compound and is not commonly found in natural sources. It is typically produced by chemical processes in controlled environments.
Allyl alcohol is produced by the hydrolysis of allyl chloride or allyl acetate, and the rearrangement of propene oxide. These processes involve chemical reactions that convert precursor compounds into allyl alcohol.
Yes, allyl alcohol is miscible in water to some extent due to its hydrophilic hydroxyl group.