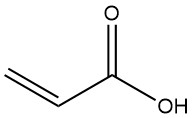
Acrylic acid, also known as 2-propenoic acid, is the simplest unsaturated carboxylic acid with the formula CH2=CHCOOH. It is a colorless liquid that is flammable, volatile and slightly toxic.
To prevent polymerization, commercial preparations typically incorporate hydroquinone or its monomethyl ether.
In the past, industrial production of acrylic acid involved various methods like acrylonitrile hydrolysis and the modified Reppe process. However, significant advancements in catalytic oxidation, particularly in converting propene to acrylic acid via acrolein, have nearly entirely supplanted these previous techniques.
Table of Contents
1. Physical Properties of Acrylic Acid
Acrylic acid is a transparent and colorless liquid with a boiling point of 141.0 °C at 101.3 kPa and a melting point of 13.5 °C, forming crystalline needles when solidified.
It exhibits high miscibility with water, alcohols, esters, and various other organic solvents, making it readily soluble in these substances.
Other important physical propertiess are listed below:
Property | Value |
---|---|
Molar Mass (Mr) | 72.06 g/mol |
Refractive Index | 1.421 |
Density | 1.05 g/cm³ |
Viscosity | 1.15 mPa.s (at 25°C) |
Critical Temperature | 380 °C |
Critical Pressure | 5.06 Mpa |
Dissociation Constant | 5.46 x 10-5 (at 25°C) |
pKa | 4.25 |
2. Chemical Reactions Of Acrylic Acid
Acrylic acid exhibits distinctive reactions characteristic of both unsaturated compounds and aliphatic carboxylic acids. Its high reactivity can be attributed to the presence of two unsaturated centers in a conjugated position.
The β-carbon atom, polarized by the carbonyl group, acts as an electrophile, enabling the addition of various nucleophiles and active hydrogen compounds to the vinyl group.
Additionally, the carbon-carbon double bond participates in radical-initiated addition reactions, Diels-Alder reactions with dienes, and polymerization reactions.
Regarding the carboxyl function, it undergoes displacement reactions typical of aliphatic acids, such as esterification.
When the vinyl and carboxyl functions jointly react, especially with bifunctional reagents, they often serve as convenient pathways to form polycyclic and heterocyclic substances.
Acrylic acid readily undergoes polymerization, which can be catalyzed by heat, light, and peroxides, but inhibited by stabilizers like the monomethyl ether of hydroquinone or hydroquinone itself.
Notably, these phenolic inhibitors are effective only in the presence of oxygen. The polymerization process of acrylic acid is highly exothermic and can be extremely vigorous.
2.1. Addition Reactions
Acrylic acid readily undergo addition reactions with various substances, such as hydrogen, hydrogen halides, and hydrogen cyanide, which are commonly added to olefins:
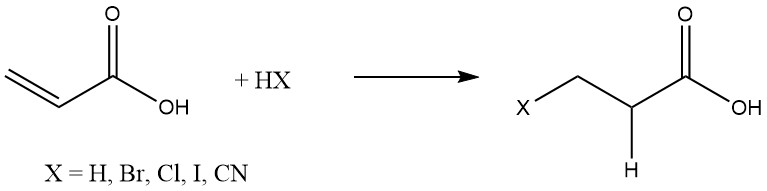
Michael additions of organic substances occur in the presence of basic catalysts like tertiary amines, quaternary ammonium salts, and alkali alkoxides.
Ammonia and amines, being sufficiently basic, can react without the need for a catalyst. The addition of a single molecule of NH3 can be achieved using an aqueous solution of ammonia and ammonium carbonate.
The addition of aromatic amines or amides and tert-alkyl primary amines is more effectively promoted by acids. Amines may attack both the vinyl and carboxyl functions, but the resulting products from such reactions decompose to give N-substituted amides.
Under basic conditions, alcohols, phenols, hydrogen sulfide, and thiols also undergo addition reactions. Hydrogen sulfide, when combined with sulfur and ammonium polysulfide or amine catalysts, gives polythiodipropionic acids. Meanwhile, additions of aromatic hydrocarbons are more efficiently promoted by Lewis acids.
If additional acidic hydrogen atoms are available in the addition product, a second (and third) molecule of acrylic acid can add. This occurs in the reaction of acrylic acid with H2S, NH3, RNH2, and pyrrole.
Heterocyclic substances are often formed through subsequent reactions of the carboxyl function, especially with bifunctional nucleophiles:
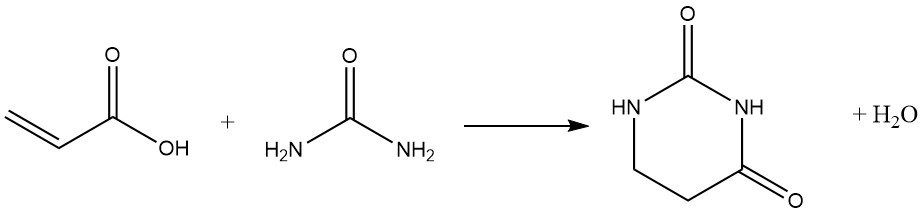
At elevated temperatures or during prolonged storage, acrylic acid dimerizes:

2.2. Reactions of the Carboxyl Group
Acrylic acid can be readily converted into its corresponding salts, transformed into acrylic anhydride by reaction with acetic anhydride, or converted into acryloyl chloride by reacting with benzoyl or thionyl chloride. The esterification of acrylic acid and transesterification of acrylic esters are economically significant reactions.
Some other examples of carboxylic group are:
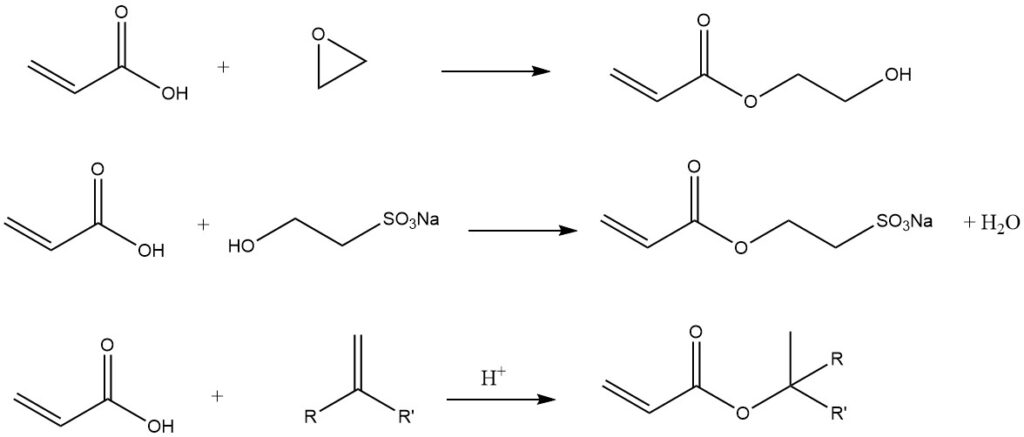
3. Production of Acrylic Acid
Commercial acrylic acid is primarily produced from propene, which is also utilized as a raw material for acrolein production. In the past, various processes were employed for the production of acrylic acid and its esters, some of which are still in use to a limited extent.
1. Processes Based on Acetylene:
Acrylic acid and its esters can be synthesized from acetylene in the presence of acid and nickel carbonyl at atmospheric pressure and 40°C:
4 C2H2 + 4 ROH + 2 HCl + Ni(CO)4 → 4 H2C=CHCOOR + NiCl2 + H2
However, this method has been abandoned due to the challenges associated with handling toxic and corrosive nickel carbonyl.
2. High-Pressure Reppe Process:
BASF employed a process using nickel bromide–copper(II) bromide catalyst at approximately 14 MPa and 200 °C to produce acrylic acid from acetylene, CO, and water. Nevertheless, this process was replaced by the more economical direct oxidation of propene.
3. Acrylonitrile Hydrolysis:
This method, which involves the hydrolysis of acrylonitrile, was found economically unattractive due to low yield and large quantities of NH4HSO4 waste. Some companies have abandoned this process, except for Asahi Chemical, which still uses it.
4. Ketene Process:

In this process, acetic acid or acetone is pyrolyzed to ketene, but it has been abandoned by companies like Celanese and B. F. Goodrich due to its many steps and the toxicity of β-propiolactone.
5. Thermal Depolymerization of Polypropiolactone:
Novomer has developed proprietary catalysts to produce polypropiolactone (PPL) as an intermediate that can be thermally depolymerized into acrylic acid or acrylate esters, addressing the challenges of transportation and reducing manufacturing complexity.
6. Ethylene Cyanohydrin Process:
Ethylene cyanohydrin is generated by adding hydrogen cyanide to ethylene oxide, and then catalytically dehydrated to produce acrylic acid using sulfuric acid. This process was used by Union Carbide and Rohm & Haas but abandoned due to handling difficulties with HCN and NH4HSO4 waste.
7. Partial Oxidation of Allyl Ether:
A catalytic system based on Li-doped mesoporous manganese oxide can catalyze the aerobic partial oxidation of diallyl ether into allyl acrylate under ambient conditions in acetonitrile solvent.
3.1. Production of Acrylic Acid by Propene Oxidation
The production of acrylic acid from propene involves heterogeneous catalytic oxidation in the vapor phase, using air and steam. The resulting product is typically absorbed in water, followed by extraction with a suitable solvent, and then distilled to obtain technical grade glacial acrylic acid.
Research on catalysts for propene oxidation to acrylic acid began in the late 1950s, with two methods for the heterogeneously catalyzed gas-phase oxidation of propene: single-step and two-step processes.
In the single-step process, the yield is limited, approximately 50-60% at best, and the catalyst’s lifetime is short due to the presence of tellurium oxide, which tends to sublime.
The two-step process involves different reaction conditions and catalysts to achieve optimum conversion and selectivity in each step. First-stage catalysts are used for acrolein-selective propene oxidation, yielding more than 85% of acrolein and acrylic acid.
Early second-stage catalysts for acrolein oxidation to acrylic acid were based mainly on cobalt-molybdenum oxides, providing yields of less than 70 mol%. However, further research showed that various multicomponent metal-oxide catalysts, including molybdenum and vanadium, along with other elements and carriers, could increase activity and yield.
Acid recovery and purification involve cooling the effluent gas and scrubbing it with water to obtain an aqueous solution of acrylic acid. This solution is then purified through extraction with an organic solvent, distillation, and inhibitor addition to prevent polymerization during distillation. The purity of the resulting acrylic acid usually exceeds 99.5 wt%, with a purified yield of around 98%.
Different purification methods, such as oligomerization and direct esterification, have been explored, but the light-solvent extraction process remains the most suitable for commercial plants due to its energy efficiency and product quality. Other methods have not been widely adopted commercially due to their high energy consumption or product quality issues.
3.2. Biobased Acrylic Acid
Biobased technologies for the production of acrylic acid involve the fermentation of biomass-derived substances, such as sugars, to produce lactic acid, 3-hydroxypropanoic acid, and 3-hydroxypropanal. Subsequently, these fermentation intermediates undergo chemical transformation to yield acrylic acid.
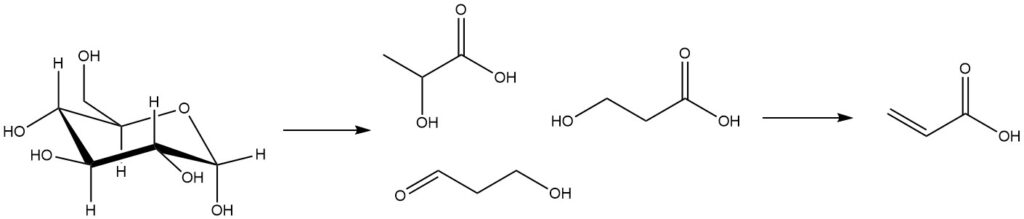
Dehydration of the intermediate lactic acid typically occurs through acetoxylation, where acetic acid is used as an azeotropic solvent.
From 2008 to 2010, several biobased technologies for acrylic acid production were initiated, utilizing feedstocks like glucose, glycol, lactic acid, and biomass.
Joint ventures and individual companies, such as Cargill/Novozymes/BASF, OPXBio/Dow, Arkema/THE, Nippon Shokubai, Geneomatica, and Choren, have been actively involved in the development of these technologies. Some of these approaches are expected to become commercialized by 2025.
Various joint ventures, including Cargill/Novozymes/BASF and OPXBio/Dow, focus on engineering enzymes or microorganisms to produce acrylic acid from renewable feedstocks like corn and sugar cane.
Arkema, in partnership with HTE, is working on developing catalysts for producing acrylic acid from glycerol via acrolein. Nippon Shokubai is exploring a gas-phase process to produce acrylic acid from glycerol obtained as a byproduct in biodiesel production from vegetable oils. The commercialization potential of these processes depends on the availability and price of glycerol.
Genomatica’s approach involves the fermentation of sugar to fumaric acid, followed by cross-metathesis with ethylene to produce acrylic acid. While this technology has been patented, there are still significant technical challenges to overcome.
The progress and success of these biobased technologies will not only depend on technological advancements but also on societal pressures and demands to produce goods and chemicals from renewable and sustainable sources.
4. Uses of Acrylic Acid
Acrylic acid serves as an intermediate in the production of acrylates. Acrylates are a group of compounds derived from acrylic acid and are widely used in various industries for their versatility and performance properties.
Additionally, acrylic acid and its sodium salts find increasing applications as flocculants and dispersants. These polymeric forms of acrylic acid, particularly the polymeric sodium salts, are gaining more industrial importance due to their effective properties in promoting flocculation (clumping of particles) and dispersion (even distribution of particles) in various processes and applications.
As of 2014, the global production capacities for acrylic acid and its esters were more than 5.2 million tons per year and 3.6 million tons per year, respectively.
China has emerged as a high-growth market for acrylic acid, surpassing the combined demand in North America and Europe. Between 2002 and 2014, China’s production capacity for acrylic acid nearly quadrupled, indicating its significant role in the industry.
In 2014, 50% of the total acrylic acid consumption was utilized as an intermediate in ester production, while the other 50% was processed to produce glacial acetic acid.
5. Toxicology and Occupational Health
Acrylic acid is moderately toxic and highly corrosive. Ingestion can lead to severe gastrointestinal burns, and its vapor is irritating to the eyes and respiratory tract. Contact with the skin may cause burns. The following physiological response data is available:
– LD50: 340 mg/kg (rat, oral)
– LC50: 3600 mg/m3 (rat, inhalation, 5 L, 4 hours)
– LD50: 280 mg/kg (rabbit, skin)
The Threshold Limit Value (TLV) for acrylic acid on a time-weighted average (TWA) is set at 10 ppm (parts per million) or 30 mg/m3. This value serves as a guideline to control exposure levels in occupational settings.
Reference
- Acrylic Acid and Derivatives; Ullmann’s Encyclopedia of Industrial Chemistry. – https://onlinelibrary.wiley.com/doi/10.1002/14356007.a01_161.pub4
Frequently Asked Questions (FAQ) about Acrylic Acid
Acrylic acid is a colorless liquid organic compound with the chemical formula CH2=CHCOOH. It belongs to the family of unsaturated carboxylic acids and has a strong, pungent odor. Acrylic acid is highly reactive due to the presence of two unsaturated centers, making it an essential building block for various chemical processes and polymerizations.
Acrylic acid is primarily used as an intermediate in the production of acrylates, a versatile group of compounds extensively employed in manufacturing paints, adhesives, coatings, and superabsorbent polymers. Additionally, acrylic acid and its sodium salts are utilized as flocculants and dispersants in various industrial applications.
Acrylic acid is typically produced through the catalytic oxidation of propene in the vapor phase, using air and steam. The two-step process involves the oxidation of propene to acrolein, followed by the further oxidation of acrolein to acrylic acid.
Acrylic acid polymer refers to the polymerization product of acrylic acid. It is commonly known as polyacrylic acid (PAA) when in its soluble form or sodium polyacrylate when in its sodium salt form. These polymers are water-soluble and possess excellent flocculation and dispersing properties, making them valuable in applications like wastewater treatment, detergent formulations, and personal care products.
Acrylic acid is considered a weak acid. In its pure form, it exhibits acidic properties, but its strength is relatively lower compared to strong mineral acids like sulfuric acid or hydrochloric acid. In aqueous solutions, acrylic acid partially dissociates to release hydrogen ions, giving it a characteristic acidic behavior.