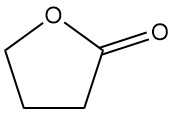
γ-Butyrolactone (CAS 96-48-0), also known as γ-hydroxybutyric acid lactone, is a simple organic compound with the formula C4H6O2. It is a hygroscopic and colorless liquid with a faint odor, might seem unremarkable at first glance.
Its industrial production started in the 1940s as a result of the work of Reppe and colleagues at BASF. The Reppe process remains the dominant method for large-scale γ-butyrolactone synthesis.
Table of Contents
1. Physical Properties of Butyrolactone
γ-Butyrolactone exists as a colorless, slightly hygroscopic liquid with a faint odor. It is miscible with water, alcohols, esters, ethers, ketones, and aromatic hydrocarbons. While it has a limited miscibility with linear and cyclic aliphatic hydrocarbons, it is used as a solvent for numerous polymers and lower hydrocarbons.
Some physical properties of γ-butyrolactone are listed in the table below:
Property | Value |
---|---|
Molar Mass | 86.09 g/mol |
Melting Point | -43.5°C |
Boiling Point | 204-206°C (at 101.3 kPa) |
Density (0°C) | 1.15 g/cm³ |
Density (20°C) | 1.13 g/cm³ |
Density (40°C) | 1.11 g/cm³ |
Critical Temperature | 436.5°C |
Critical Pressure | 3.35 MPa |
Vapor Pressure (20°C) | 0.04 kPa |
Vapor Pressure (50°C) | 0.3 kPa |
Vapor Pressure (100°C) | 3.6 kPa |
Vapor Pressure (150°C) | 22.5 kPa |
Vapor Pressure (205°C) | 101.3 kPa |
Heat of Vaporization (206°C) | 535 kJ/kg |
Heat of Solution in Water | 2500 J/mol |
Specific Heat Capacity (cp) - Liquid (25°C) | 1680 J kg⁻¹ K⁻¹ |
Specific Heat Capacity (cp) - Liquid (100°C) | 1850 J kg⁻¹ K⁻¹ |
Specific Heat Capacity (cp) - Liquid (200°C) | 2200 J kg⁻¹ K⁻¹ |
Specific Heat Capacity (cp) - Gas (100°C) | 1275 J kg⁻¹ K⁻¹ |
Specific Heat Capacity (cp) - Gas (200°C) | 1575 J kg⁻¹ K⁻¹ |
Specific Heat Capacity (cp) - Gas (300°C) | 1820 J kg⁻¹ K⁻¹ |
Flash Point | 100-101°C |
Ignition Temperature | 455°C |
Heat of Combustion | 234 kJ/g |
Explosion Limits - Lower | 2.7 vol% |
Explosion Limits - Upper | 15.6 vol% |
Refractive Index (20°C) | 1.4352 |
Viscosity (20°C) | 1.90 mPa s |
Viscosity (50°C) | 1.25 mPa s |
Viscosity (80°C) | 0.86 mPa s |
Viscosity (110°C) | 0.63 mPa s |
Viscosity (140°C) | 0.49 mPa s |
Viscosity (170°C) | 0.40 mPa s |
Surface Tension (20°C) | 44.6 x 10⁻⁵ N/cm |
Dielectric Constant (20°C) | 39.1 |
Thermal Conductivity (25-65°C) | 0.276 J m⁻¹ s⁻¹ K⁻¹ |
Conductivity | 0.7 μS/cm |
2. Chemical Properties of Butyrolactone
In an aqueous solution, the isomerization between the lactone form and the free hydroxybutyric acid form is a temperature-dependent equilibrium. At 0 °C, the lactone form predominates completely, while at 100 °C, approximately 80% exists as the lactone.
Strong alkaline conditions (one molar equivalent of alkali) shift the equilibrium entirely towards the hydroxybutyric acid form. This property allows for the titrimetric determination of butyrolactone. At a neutral pH (7), butyrolactone is very stable.
Butyrolactone undergoes ring-cleavage reactions with various reagents, yielding derivatives of γ-hydroxybutyric acid. Examples include reactions with bases, hydrogen halides, and alcohols (under acidic conditions).
It also undergoes reactions in the α position without ring cleavage. These include reactions with ammonia, amines, carbonyl compounds, and halogenation. For example, its condensation with ethyl acetate forms α-acetobutyrolactone, an important intermediate in vitamin B1 synthesis.
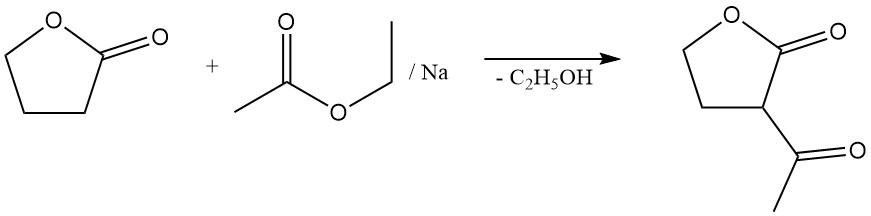
The lactone ring cleavage reaction allows for the preparation of valuable γ-substituted butyric acid derivatives. For example, the reaction with sodium sulfide yields the rubber additive thiodibutyric acid,

while reaction with phenol produces phenoxybutyric acid.
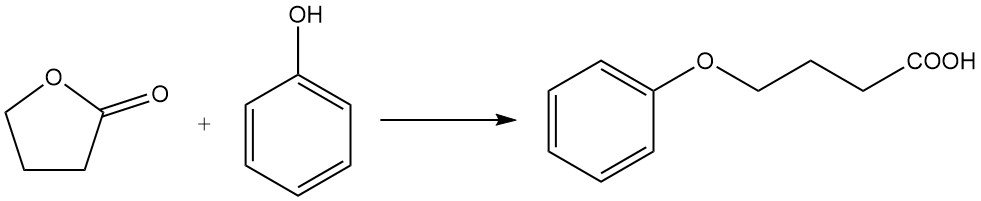
Replacing the ring oxygen atom with nitrogen is an industrial reaction used for the synthesis of pyrrolidone derivatives. As an example, butyrolactone reacts with methylamine to produce N-methylpyrrolidone (NMP), a key industrial solvent.
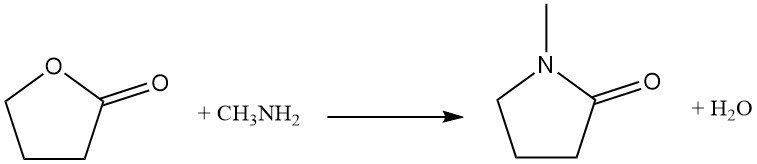
Direct homopolymerization of butyrolactone requires high pressure (2000 MPa), but alternative routes, such as fermentation of sugars, can give a similar product.
3. Production of Butyrolactone
3.1. Production of Butyrolactone by Dehydrogenation of 1,4-Butanediol
The Reppe process is the predominant industrial route for butyrolactone synthesis, achieved by the gas-phase endothermic dehydrogenation of 1,4-butanediol. This multi-step reaction proceeds via γ-hydroxybutyraldehyde and 2-hydroxytetrahydrofuran intermediates.

Major manufacturers employing this process include BASF, Ashland, and Lyondell.
Preheated 1,4-butanediol vapor is combined with a hot circulating hydrogen stream and passed over a copper catalyst bed at atmospheric pressure and temperatures ranging from 180 to 300°C (Figure 1). This reaction delivers a high yield of approximately 95% butyrolactone.
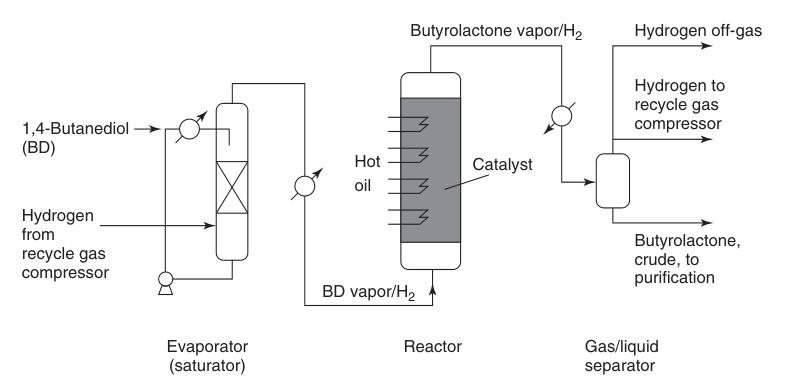
The generated hydrogen byproduct requires minimal purification for potential reuse, typically involving catalytic methanization to remove carbon monoxide impurities.
Crude butyrolactone which is separated from the recycled gas stream contains minor impurities like unreacted 1,4-butanediol, butyric acid, and high-boiling compounds. These are removed via distillation to obtain pure butyrolactone.
Butyrolactone itself is non-corrosive and compatible with carbon steel equipment. However, components exposed to hot crude product containing butyric acid, such as parts of the synthesis or distillation vessels and piping, necessitate the use of stainless steel for enhanced durability.
3.2. Production of Butyrolactone by Hydrogenation of Maleic Anhydride
An alternative route to butyrolactone involves catalytic hydrogenation of maleic anhydride. In this process, preheated molten maleic anhydride is introduced into a circulating stream of hydrogen under pressure (6-12 MPa) and temperature (160-280 °C). A nickel-based catalyst promotes the reaction, which proceeds exothermically with a ΔH of -211 kJ/mol:

The reaction pathway involves intermediate succinic anhydride, and depending on the chosen conditions, can be further directed towards tetrahydrofuran production. Complete hydrogenation of succinic anhydride, however, inevitably leads to co-formation of tetrahydrofuran.
The excess hydrogen is recycled after water washing to remove impurities. Byproducts formed during butyrolactone synthesis, including propanol, butanol, propionic acid, and butyric acid, are separated from the circulating gas stream. Subsequent distillation purifies the butyrolactone stream.
Due to the presence of acidic byproducts, both the synthesis and distillation equipment require stainless steel construction. Mitsubishi Chemical Corporation is a manufacturer employing this method.
3.3. Production of Butyrolactone by Hydrogenation of Maleic Esters
Emerging in the 1980s, several processes utilizing dimethyl maleate as an intermediate offer alternative routes to 1,4-butanediol and tetrahydrofuran (THF). These methods also present the opportunity to isolate butyrolactone, an intermediate in the reaction sequence.
One notable process, developed by Kvaerner Process Technology (now Johnson Matthey Davy Technologies), uses dimethyl maleate as the initial product obtained from maleic anhydride and methanol using a strong acidic ion exchange catalyst.
Subsequent gas-phase hydrogenation over a copper-based catalyst system, under pressures of 2-8 MPa and temperatures of 150-250°C, yields a mixture of desired products: 1,4-butanediol, THF, butyrolactone, trace amounts of dimethyl succinate (intermediate), and n-butanol as a major byproduct.

Butyrolactone and dimethyl succinate form an azeotropic mixture, allowing for their recovery and recycling back to the hydrogenation stage. This recycling strategy promotes complete conversion towards 1,4-butanediol and THF. Alternatively, the azeotrope can be refined by distillation to isolate pure butyrolactone.
The butyrolactone yield is directly influenced by the operating pressure and temperature during hydrogenation, which dictate the equilibrium between 1,4-butanediol and butyrolactone. Under the reported conditions, yields can range from 5% to 50%.
This innovative process has gained significant commercial interest, with KPT and JM Davy securing licenses for building multiple butanediol-butyrolactone-THF plants in Saudi Arabia, Malaysia, Korea, and China.
3.4. Production of Butyrolactone by Biobased Process
Metabolix (now, Yield10 Bioscience, Inc.) developed a fermentation process to produce poly(4-hydroxybutyrate) (polybutyrolactone) from sugars. This polymer can be depolymerized to butyrolactone at temperatures exceeding 200 °C, with calcium hydroxide achieving optimal results. The remaining biomass is converted into solid fuel. As of 2019, no commercial plant using this method exists.
BioAmber proposed a bio-based route where sugars are fermented to succinic acid diammonium salt. Subsequent ammonia removal yields succinic acid, which can be hydrogenated in the presence of a precious metal catalyst to produce butyrolactone, alongside 1,4-butanediol and tetrahydrofuran. This process has not yet reached commercial application.
While not commercially significant, research has explored various alternative pathways for butyrolactone synthesis from tetrahydrofuran, dihydrofuran, acetylene, butynediol, olefins, butadiene or by carbonylation.
4. Uses of Butyrolactone
Butyrolactone’s versatility extends far beyond its role as a simple chemical intermediate. Its applications span diverse fields, from pharmaceutical formulations to polymer science and even emerging technologies in electronics.
Butyrolactone serves as a crucial building block for various chemicals, including N-methylpyrrolidone (NMP) and pyrrolidone, both with their own significant uses. It is also used in the synthesis of phenoxy herbicides like MCPB (γ-2-methyl-4-chlorophenoxybutyric acid) and growth regulators.
It is an intermediate in the production of α-acetobutyrolactone, a vital step in vitamin B1 synthesis. Butyrolactone is also used for the production of thiodibutyric acid, a valuable additive in rubber manufacturing.
It is a solvant that can dissolve various polymers, facilitating their processing and manipulation. Additionally,it is a valuable catalyst for specific polymerization reactions.
Butyrolactone contributes to the formulation of hair-wave compositions, sun lotions, other personal care products and in pharmaceuticals.
Other applications of butyrolactone include: as a solvent in inkjet printing ink, an extractant in the petroleum industry, as a stabilizer for chlorohydrocarbons and phosphorus-based pesticides and as a nematocide.
Its unique properties make it a promising co-solvent for capacitor electrolytes in the electronics industry and has a potential use in photoresists.
5. Toxicology and Occupational Health
Absorption and Metabolism:
- Butyrolactone readily absorbs through the intestine and skin. Its oral half-life in rats is around 20 minutes.
- Metabolism and excretion are rapid, primarily yielding γ-hydroxybutyric acid as the main metabolite.
- In humans, studies report (S)-3,4-dihydroxybutyrate, glycolic acid, and other metabolites in urine after ingestion.
Acute Toxicity:
- Butyrolactone exhibits low acute toxicity, with LD50 values between 800 and 1800 mg/kg in rodents and 500-1700 mg/kg in guinea pigs.
- Dermal LD50 in guinea pigs is 5600 mg/kg.
- The inhalative LC50 (rat, 4-h) exceeds the highest non-lethal concentration tested (>5.1 mg/L).
- Inhalation at room temperature saturation shows no adverse effects in rats [BASF, (1960) unpublished results].
Neurological Effects:
- Butyrolactone’s central nervous system (CNS) depression occurs through its metabolite, γ-hydroxybutyric acid, with additional peripheral nervous system anesthetic effects.
- Doses of 2500 mg in adult humans induced temporary sleep.
- Doses of 66 mg/kg in children for anesthesia resulted in deep sleep with occasional respiratory depression.
- Higher accidental oral doses in adults and infants caused CNS depression-induced unconsciousness, occasionally coma, bradycardia, and respiratory depression. Patients recovered fully within 24h with supportive care.
Local and Skin Effects:
- Butyrolactone is non-irritating to skin but moderately irritating to eyes in rabbits [BASF, (1960) unpublished results].
- No skin sensitization observed in guinea pigs.
- Patch testing in 200 volunteers found no skin reactions.
- Lotions containing butyrolactone are well-tolerated for topical application.
- It has served as a successful topical analgesic for musculoskeletal pain, headaches, and migraines.
Chronic and Carcinogenicity Studies:
- Prolonged oral administration at 3 g/kg daily for four weeks led to CNS depression in rats but no further significant effects.
- Repeated-dose studies showed slightly higher toxicity compared to gavage with possible bolus effects.
- Numerous mutagenicity and genotoxicity studies indicate no genotoxic potential.
- Long-term carcinogenicity studies in rats and mice at high doses found no evidence of tumorigenic potential.
- Early dermal and oral studies also did not show carcinogenic effects.
- Overall, evidence suggests no significant carcinogenic risk associated with butyrolactone.
Developmental and Reproductive Effects:
Prenatal exposure in rats and rabbits via oral and inhalation routes showed no substance-related developmental effects (BASF AG, (1993) unpublished results).
Occupational Exposure:
Specific occupational exposure limits for butyrolactone are not established in Europe or the USA.
Environmental Impact:
Acute toxicity data and rapid biodegradability suggest minimal environmental risk.
Reference
- Butyrolactone; Ullmann’s Encyclopedia of Industrial Chemistry. – https://onlinelibrary.wiley.com/doi/10.1002/14356007.a04_495.pub2