
What is propionic acid?
Propionic acid, also known as propanoic acid, is a naturally occurring short-chain carboxylic acid with the formula CH3CH2COOH. It is a colorless liquid with a pungent odor, often described as resembling sweat or cheese.
Propionic acid was first described by J. Gottlieb in 1844 and classified as a fatty acid by J.J. Dumas in 1848. Its name originates from the Greek words “protos” (first) and “pion” (fat), reflecting its position as the first fatty acid isolable from an aqueous solution by salting out.
Propionic acid exists naturally, primarily as esters within essential oils. It can also form as a free acid through various enzymatic and fermentation processes. It is a product of anaerobic carbohydrate fermentation in the ruminant stomach. Propionic acid derivatives are used as intermediates in several physiological cycles.
Propionic acid is used in the production of cellulose esters, plastic dispersions, and herbicides, and it finds limited use in pharmaceuticals, flavors, and fragrances.
It is also used as a food preservative because of its fungicidal and bactericidal properties, and it is increasingly used to prevent mold and bacterial spoilage in forage cereals, animal feeds, bakery products, and cheese.
Table of Contents
1. Physical Properties of Propionic Acid
Propionic acid is a colorless liquid with a pungent odor. Solid propionic acid crystallizes in the monoclinic system and expands by 12.2% volume when melted. Similar to its lower homologs, acetic acid and formic acid, a significant portion of propionic acid molecules dimerize in both the liquid and gas phases.
Propionic acid is miscible with water and most organic solvents in all proportions. It forms azeotropic mixtures with various liquids, including water (82.3 wt% water, boiling point 99.98 °C at 101.3 kPa).
Tables 1, 2, and 3 provide temperature-dependent data for propionic acid, including vapor pressure, density, and dynamic viscosity, respectively.
Temperature (°C) | Pressure (kPa) |
---|---|
0.7 | 0.1 |
13.5 | 0.25 |
24.0 | 0.5 |
35.0 | 1.0 |
50.8 | 2.5 |
64.5 | 5.0 |
79.3 | 10.0 |
100.9 | 25 |
120.1 | 50 |
140.9 | 100 |
159.5 | 200 |
185.7 | 500 |
203.0 | 1000 |
219.7 | 2000 |
Temperature (°C) | Density (g/cm³) |
---|---|
-20 | 1.038 |
-10 | 1.027 |
0 | 1.016 |
10 | 1.005 |
20 | 0.9935 |
30 | 0.9827 |
40 | 0.9719 |
50 | 0.9611 |
60 | 0.9503 |
70 | 0.9395 |
80 | 0.9286 |
90 | 0.9176 |
100 | 0.9066 |
110 | 0.8954 |
120 | 0.8841 |
130 | 0.8726 |
140 | 0.8609 |
150 | 0.849 |
160 | 0.8367 |
170 | 0.8241 |
Temperature (°C) | Viscosity (mPa·s) |
---|---|
0 | 154.1 |
20 | 109.4 |
50 | 73.8 |
100 | 45.0 |
150 | 31.0 |
Other physical properties of propionic acid are listed in the following table:
Property | Value |
---|---|
CAS | [79-09-4] |
Formula | CH3CH2COOH |
Molecular Weight | 74.08 g/mol |
Melting Point | -20.8 °C |
Boiling Point | 141.3 °C |
Refractive Index | 1.3865 |
Surface Tension toward Air at | |
20 °C | 26.7 × 10-3 N/m |
90 °C | 19.7 × 10-3 N/m |
Thermal Conductivity at | |
0 °C | 153 W m-1 K-1 |
20 °C | 150 W m-1 K-1 |
50 °C | 144 W m-1 K-1 |
100 °C | 136 W m-1 K-1 |
Electrical Conductivity at 2 °C | 10-4 μS/cm |
Dynamic Dielectric Constant at | |
10 °C | 3.30 |
40 °C | 3.44 |
Electric Dipole Moment, μ | 1.75 D ± 5% |
Dissociation Constant in H2O at | |
0 °C | 1.274 × 10-5 mol/L |
20 °C | 1.338 × 10-5 mol/L |
40 °C | 1.284 × 10-5 mol/L |
60 °C | 1.160 × 10-5 mol/L |
Ionization Potential | 10.24 ± 0.03 eV |
Heat of Fusion | 101.65 kJ/kg |
Heat of Vaporization | 418.7 kJ/kg |
Heat of Formation | -164.5 kJ/mol |
Heat of Combustion | -1528.3 kJ/mol |
Specific Heat (Liquid), at | |
0 °C | 2.077 kJ kg-1 K-1 |
50 °C | 2.299 kJ kg-1 K-1 |
100 °C | 2.516 kJ kg-1 K-1 |
Specific Heat (Vapor), at | |
100 °C | 2.823 kJ kg-1 K-1 |
200 °C | 3.245 kJ kg-1 K-1 |
300 °C | 3.647 kJ kg-1 K-1 |
Isentropic Compressibility at 20 °C | 0.750 GPa |
Critical Temperature | 338.9 °C |
Critical Pressure | 5.37 MPa |
Critical Volume | 0.322 kg/L |
Flash Point | 50 °C |
Ignition Temperature | 485 °C |
Explosion Limits in Air at 20 °C | 2.1–12.0 vol% |
2. Reactions of Propionic Acid
Propionic acid is the third member of the aliphatic monocarboxylic acid series, which has the reactivity characteristic of these acids. It readily forms salts, amides, acid halides, and anhydrides.
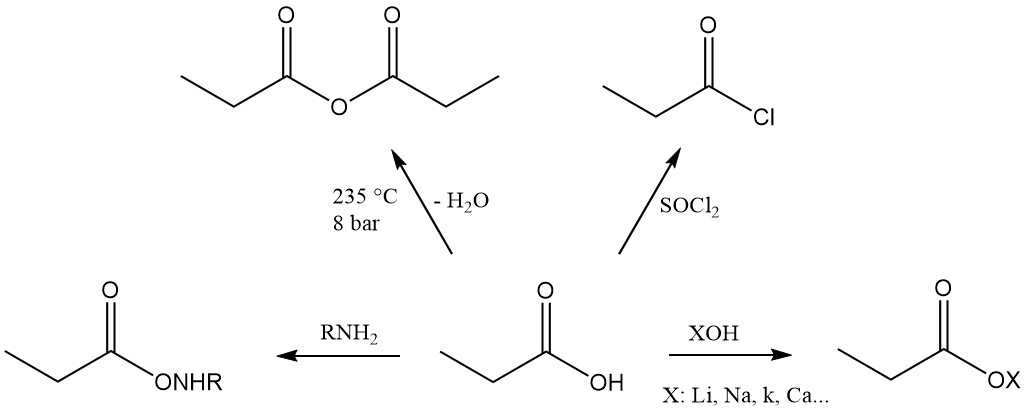
Propionic acid esters are formed by reaction with alcohols and olefins, while the reaction with acetylenes yields corresponding vinyl esters.


The reactivity of propionic acid is different from that of acetic acid due to the methylene group’s inductive effect. This makes propionic acid more susceptible to attack by alkaline permanganate solutions compared to acetic acid. The degradation process is non-selective, resulting in a mixture of carbon dioxide, oxalic acid, and lactic acid.

Ionic substitution reactions also display a preference for the methylene group. Chlorination using halogen-transfer reagents, such as PCl3, leads to the formation of α-chloropropionic acid, while radical chlorination induced by peroxides or UV radiation yields β-chloropropionic acid. Both products are used as intermediates in the production of herbicides and pharmaceuticals.
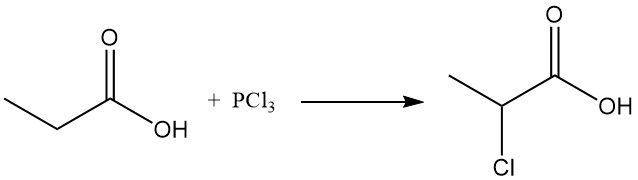

Thermal decomposition of calcium propionate or propionic acid vapor passed over metal oxides at 300–400 °C produces diethyl ketone, a widely used industrial solvent.

3. Industrial Production of Propionic Acid
Propionic acid is industrially produced by the carbonylation of ethylene or the oxidation of propanal.
It can also be produced as byproducts from hydroxylamine salt synthesis from 1-nitropropane, from wood distillation, by nitric acid oxidation of 1-propanol, by alkali melting of n-propanol and isopropanol mixtures, and by carbonylation of ethanol and acetic acid. However, all these methods are obsolete.
Other potential, but economically nonviable, sources of propionic acid include:
- Byproduct formation: Propionic acid can be formed as a byproduct during processes like methanol carbonylation and n-butene oxidation, but the yield is relatively low.
- Direct ethylene reaction: The direct reaction of ethylene, carbon monoxide, and water over specific catalysts has potential but is not yet competitive.
- C1-Processes: Two-step reactions using synthesis gas and rhodium catalysts have been described for propionic acid production, but current resource availability makes them less attractive.
For applications requiring “natural” propionic acid, particularly in flavors and fragrances, microbiological and enzymatic processes based on fermenting starch or sugars have been developed. However, the high production cost limits its use to specialized applications.
3.1. Production of Propionic Acid by Carbonylation of Ethylene (BASF Process)
The BASF process for propionic acid production uses the Reppe synthesis. This reaction involves the reaction of ethylene with carbon monoxide and water under high pressure, using Ni(CO)4 as a catalyst.
C2H4 + CO + H2O → CH3CH2COOH
This process offers several advantages, such as low raw material costs, high conversion and yield of propionic acid, and a simple workup procedure.
A simple industrial process description is shown in Figure 1.
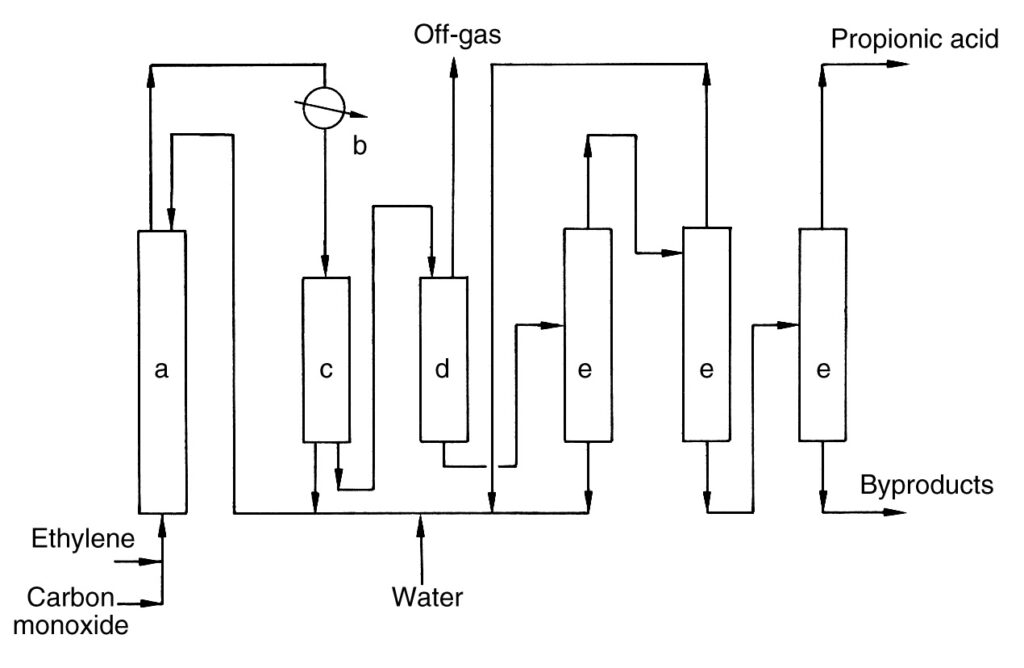
a) High-pressure reactor; b) Heat exchanger; c) Separator; d) Expansion vessel; e) Distillation column
Ethylene and carbon monoxide are compressed and continuously fed along with a recycle stream into the high-pressure reactor (a). The reaction proceeds at 100–300 bar and 250–320 °C. Crude propionic acid is formed and withdrawn from the reactor head.
The crude product is cooled in a heat exchanger (b), generating steam. A portion of the cooled product is recycled to the reactor (c) for temperature control, while the main stream is depressurized (d).
The depressurized stream separates into an off-gas stream and a crude acid stream. Nickel catalyst is recovered from the off-gas and recycled back to the reactor. The off-gas is incinerated with heat recovery.
The crude acid is dehydrated and further purified via multiple distillation columns (e). Nickel salts formed during the process are recycled. The final distillation yields pure propionic acid, and the product residue is removed from the process.
Boric acid is reported to enhance the reaction rate and prevent catalyst salt precipitation.
3.2. Production of Propionic Acid by Oxidation of Propanal
Propionic acid is produced commercially by propanal oxidation. This process involves two steps: propanal production and catalyzed carbonylation.
Propanal is formed as an intermediate during n-propanol production via ethylene hydroformylation. Unlike higher aldehydes, n/iso isomer mixtures are not formed. It is produced industrially by high-pressure cobalt-catalyzed carbonylation or by low-pressure rhodium/iridium-catalyzed carbonylation.
The readily obtained propanal is then selectively oxidized to propionic acid under mild conditions (40–50 °C).
This two-step method ensures the use of existing plants for both propanal production and subsequent oxidation. Companies like Dow (formerly Union Carbide) and Eastman in the United States employ this method for propionic acid production.
3.3. Production of Propionic Acid by Direct Oxidation of Hydrocarbons
Historically, a significant portion of propionic acid was produced via the direct oxidation of hydrocarbons, primarily naphtha. This process, primarily used for acetic acid production, also generated formic acid, propionic acid, a mixture of butyric acid isomers, and methyl ethyl ketone as byproducts.
While this method offered advantages in terms of raw material cost, the process presented significant challenges:
- Complex Product Mixture: The oxidation process yielded a complex mixture of various organic acids, requiring a sophisticated and expensive separation process.
- Limited Product Control: The reaction conditions offered minimal control over the specific ratios of products formed, making it difficult to adapt to fluctuating market demands.
- High Energy Consumption: The separation process associated with this technology results in high energy consumption.
These drawbacks ultimately led to the complete abandonment of this technology. By 2009, all operational plants using this process had been shut down, with the last one being the Celanese plant in Pampa, Texas.
A description of the BP Chemicals process (Figure 2), a historical example of direct hydrocarbon oxidation, is provided for reference purposes.
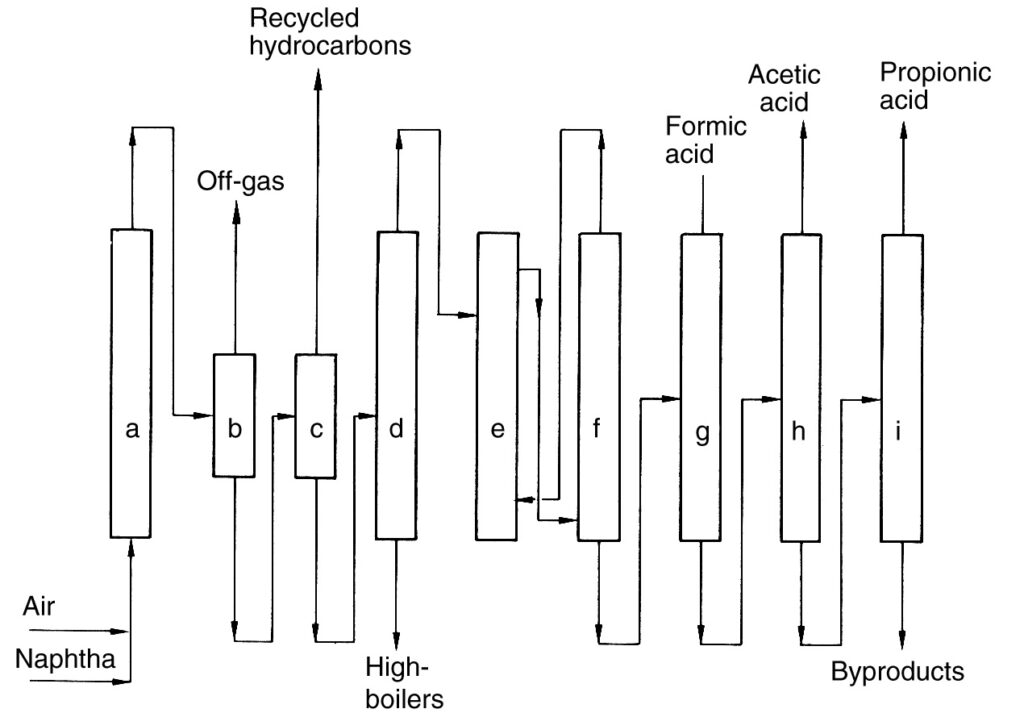
a) Reactor; b) Gas–liquid separator; c) Liquid–liquid separator; d) Distillation column; e) Extraction; f) Separation of extracting agent; g) Formic acid distillation; h) Acetic acid distillation; i) Propionic acid distillation
In this process, naphtha was preheated and then oxidized with air at elevated pressure (40–45 bar) within a series of reactors (a). The reaction generated heat, which was utilized for steam production.
The cooled reactor effluent was separated from the reaction off-gas in a separator (b). The recovered liquid was recycled back to the reactors, while the off-gas was incinerated. The remaining liquid product was then separated into an organic phase (unreacted hydrocarbons) and an aqueous phase containing the product mixture (c). Unreacted hydrocarbons were recycled.
The aqueous phase underwent separation of low- and high-boiling components, followed by extraction dehydration (e) to obtain the crude acid. Finally, fractional distillation steps (g)–(i) were used to isolate C1- to C4-carboxylic acids.
3.4. Production of Propionic Acid by Fermentation
While petrochemical processes dominate industrial propionic acid production, fermentation using Propionibacterium species offers a bio-based alternative. These gram-positive, non-motile, rod-shaped bacteria are generally recognized as safe (GRAS), making the resulting propionic acid suitable for applications like food, feed, pharmaceuticals, and cosmetics.
Propionibacteria use the dicarboxylic acid pathway to convert glucose (or other carbon sources) to propionic acid. This pathway involves pyruvate as a key intermediate. Pyruvate can either be carboxylated to oxaloacetate, leading to propionic acid biosynthesis, or decarboxylated to acetyl-CoA, leading to acetic acid biosynthesis.
The co-production of propionic and acetic acids maintains redox balance.
Theoretically, 1.5 mol of glucose can yield 2 mol of propionate, 1 mol of acetate, and 1 mol of CO2 through the Embden-Meyerhof-Parnas (EMP) pathway. This translates to a maximum propionic acid yield of 0.548 g/g glucose and a propionic acid-to-acetic acid ratio of 2.
The pentose phosphate pathway (HMP) can lead to higher propionic acid yields (up to 0.68 g/g) with less acetic acid produced. Succinic acid is a common byproduct in this process.
The actual propionic acid yield depends heavily on the chosen substrate and fermentation conditions.
Propionic acid fermentation typically occurs under anaerobic conditions (purged with nitrogen gas) at 30–32 °C and pH 6.0–7.0. The fermentation medium requires buffering (e.g., CaCO3) or addition of base (e.g., ammonium hydroxide) to neutralize the acids produced, as propionibacteria growth ceases below pH 4.5.
The medium typically includes a carbon source (e.g., glucose), nitrogen source (e.g., ammonia), minerals, and vitamins. Propionibacteria can use various carbon sources, including sugars, lactate, glycerol, and sorbitol.
Industrial processes often employ low-cost feedstocks like whey permeate, molasses, or biodiesel waste glycerol, supplemented with nitrogen sources like yeast extract.
Propionic acid itself acts as a fermentation inhibitor, reducing growth and production rates at concentrations exceeding 10 g/L. Conventional fermentation processes usually take 3 days to reach around 20 g/L propionic acid with a yield of 0.4 g/g glucose or less.
Extensive research has focused on improving yield, concentration, and production rate through strain development and process optimization.
4. Uses of Propionic Acid
4.1. Uses of Propionic Acid as Food and Feed Preservative
Propionic acid and its salts (propionates) are widely used as preservatives due to their ability to inhibit bacteria, fungi, insects, viruses, and mites.
The exact mechanism of action is still under investigation, but the undissociated form of propionic acid (dominant at acidic pH) is believed to be responsible for the preservative effect. This form penetrates cells like a nutrient and disrupts essential carbohydrate metabolism enzymes.
Propionates require hydrolysis to release the active acid form, making them slower and less effective than propionic acid itself.
Propionic acid shows a broad spectrum of activity against various microorganisms, with a minimum inhibitory concentration (MIC) of 0.05–0.50 wt% against fungi, 0.25–0.50 wt% against bacteria, and 0.10–1.0 wt% against yeasts.
It is effective against spoilage molds in food and feed and more effective against Gram-negative bacteria (e.g., E. coli, Salmonella). It also inactivates viruses like the Vaccinia virus at concentrations above 1.0 wt% and kills mites and corn beetles in cereals.
Propionic acid has a strong odor, which limits its use in food preservation. Propionates (calcium, sodium, and ammonium salts) are preferred in food due to their nearly neutral taste and smell.
Both forms are used in feed preservation, with animals often preferring the acidic taste of propionic acid-preserved feed.
Propionic acid and its salts are generally recognized as safe (GRAS) for various food applications in the US and Europe. The FAO/WHO has no specific limitations on their daily intake.
4.2. Other Uses
Propionic acid is used in other industries such as rubber, polymers, solvents, flavors, fragrances, pharmaceuticals and herbicides.
Zinc, cadmium, lead, and mercury propionates can be used as vulcanization regulators, influencing the process of strengthening rubber during production.
Propionic acid is used as an intermediate, often in its anhydride form, for the production of valuable esters such as cellulose acetate propionate and vinyl propionate.
Methyl, ethyl, propyl, and butyl propionates are used as solvents for resins and paints, and various propionate esters possess characteristic fruity aromas, making them valuable ingredients in flavor and fragrance formulations.
Small amounts of propionic acid are converted to propionyl chloride, a reactive molecule used to introduce the “propionyl group” during the synthesis of certain pharmaceuticals.
Until the late 1980s, a significant portion of propionic acid was used to produce chlorinated herbicides. However, the development of more potent and versatile herbicides has led to a decline in this application.
5. Toxicology of Propionic Acid
Propionic acid shows low acute toxicity and is rapidly metabolized in the body. However, it has irritant/corrosive effects on skin and eyes. Chronic exposure at high concentrations can cause local changes in the forestomach epithelium of some animal species.
Propionic acid, or its activated form, propionyl-CoA, is a natural intermediate in human metabolism. It’s readily absorbed and metabolized by the liver.
Propionic acid has low oral and inhalation toxicity. Sodium and calcium propionates are even less toxic. Skin contact can cause irritation or corrosion.
Long-term exposure to high concentrations (>0.4%) in rats can cause changes in the forestomach lining. However, beagle dogs, which lack a forestomach, did not show these effects.
Studies have not shown any evidence of propionic acid or propionates causing genetic mutations. Studies on pregnant animals did not reveal any developmental abnormalities caused by propionic acid exposure.
Limited human studies suggest propionic acid is well tolerated orally at low doses. Sodium propionate solutions have been used safely for eye treatment.
Reference
- Propionic Acid and Derivatives; Ullmann’s Encyclopedia of Industrial Chemistry. – https://onlinelibrary.wiley.com/doi/10.1002/14356007.a22_223.pub4