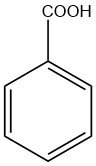
Le nom acide benzoïque provient de la gomme benjoin, une résine balsamique obtenue à partir d’une plante sud-asiatique appelée styrax.
L’extraction de l’acide benzoïque a été réalisée par SCHEELE en 1775. Sa structure a été déterminée par LIEBIG et W€OHLER en 1832.
Les premières méthodes de production ont été développées à la fin des années 1800. Ils étaient basés sur l’hydrolyse du benzotrichlorure ou la décarboxylation de l’anhydride phtalique.
Aujourd’hui, l’acide benzoïque est produit par oxydation du toluène avec de l’air, ce qui a remplacé les processus d’oxydation par dichromate ou acide nitrique.
Table des matières
1. Production d'acide benzoïque
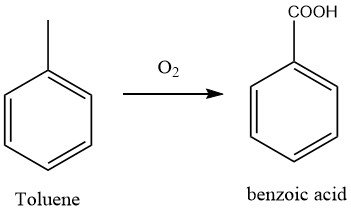
Oxydation en phase liquide du toluène avec de l’oxygène moléculaire. Ce procédé a été développé par I.G. Farben industrie en Allemagne pendant la Seconde Guerre mondiale et a fonctionné jusqu’à la fin de la guerre.
L’installation était constituée d’un réacteur d’oxydation à colonne à bulles en acier revêtu d’aluminium et équipé d’un tube d’entrée d’air, d’un séparateur et d’un absorbeur pour récupérer le toluène.
Le réacteur contenait des serpentins d’échange de chaleur pour éliminer la grande quantité de chaleur générée lors de la réaction. La pureté du toluène était critique car les composés soufrés, les composés azotés, les phénols et les oléfines inhibent la réaction d’oxydation.
La réaction a été effectuée à 140°C et env. 0,2 MPa avec un catalyseur au naphténate de cobalt (0,1 %) pendant 30 h.
Une conversion d’environ 50 % du toluène a été obtenue, dont 80 % ont formé de l’acide benzoïque. D’autres sels de cobalt solubles dans l’huile ont également été utilisés comme catalyseurs.
Le produit d’oxydation brut a été neutralisé avec du carbonate de sodium pour produire du benzoate de sodium. Le toluène n’ayant pas réagi a été récupéré de la phase d’huile usée par distillation.
Le mécanisme élémentaire de cette oxydation est un processus en chaîne radicalaire. Le catalyseur au cobalt raccourcit la période d’induction de la réaction et retarde l’accumulation d’inhibiteurs.
Les peroxydes sont des intermédiaires de réaction. Le manganèse se comporte de la même manière que le cobalt en tant que catalyseur, mais ses performances sont plus faibles.
Le cuivre affecte négativement l’oxydation. Des pressions élevées retardent la réaction, en particulier à des concentrations de catalyseur plus faibles. Au-dessus de 130 °C, la vitesse de réaction est déterminée par la diffusion d’oxygène.
Les composés phénoliques s’accumulent progressivement au cours de la réaction et finissent par l’inhiber.
Dans un procédé moderne typique, l’oxydation est effectuée à 165 °C et 0,9 MPa. La chaleur de réaction est évacuée par circulation externe du contenu du réacteur. La pression du liquide évacué du réacteur est ramenée à la pression atmosphérique et le toluène n’ayant pas réagi est récupéré.
L’acide benzoïque est purifié par rectification. Le résidu de fond est extrait pour récupérer le catalyseur au cobalt. Les gaz d’échappement sont refroidis pour récupérer la majeure partie du toluène, purifiés et ventilés. Le réacteur d’oxydation peut être une colonne à bulles ou une cuve agitée.
L’acier inoxydable est généralement utilisé comme matériau de construction. L’évacuation de la chaleur reste un problème sérieux, et la distribution d’air dans le réacteur est essentielle pour empêcher une réaction d’emballement. La teneur en oxygène des gaz d’échappement doit être strictement surveillée pour éviter une explosion.
Sous-produits du processus d’oxydation
Le benzaldéhyde se forme en quantités assez importantes, en particulier à des conversions plus faibles. Il peut être récupéré par distillation.
Une quantité limitée d’alcool benzylique est formée, mais sa récupération n’est pas pratique en raison de l’estérification inévitable avec l’acide benzoïque.
Le benzoate de benzyle peut être récupéré au fond de la colonne d’acide benzoïque.
D’autres esters, y compris le formiate de benzyle et l’acétate de benzyle, sont également présents. Les biphényles et les méthylbiphényles se forment en plus petites quantités. Parce que leurs pressions de vapeur sont proches de celle de l’acide benzoïque, ils jouent un rôle dans la rectification de l’acide benzoïque.
Le produit est contaminé par de petites quantités d’acide phtalique. Le monoxyde de carbone et le dioxyde de carbone sont détectés dans les gaz d’échappement.
Le rendement en acide benzoïque est d’environ 90 %, mais il varie avec la conversion du toluène. Aux conversions inférieures, la sélectivité pour le benzaldéhyde et l’alcool benzylique dépasse 10 %.
L’acide benzoïque de qualité technique conventionnel est généralement de qualité rectifiée. Un traitement supplémentaire est nécessaire pour les produits de qualité supérieure.
Des procédés de sublimation, de recristallisation et de neutralisation ont été proposés. Un traitement thermique sous atmosphère inerte est tenté.
Pour éliminer l’acide phtalique, dont la présence n’est pas autorisée pour les usages alimentaires ou pharmaceutiques, des traitements aux amines et des méthodes de rinçage ont été rapportés.
Les méthylbiphényles sont responsables de l’odeur du produit. Pour leur élimination, une extraction et un traitement dans un courant de gaz inerte ont été proposés.
Les réactions d’oxydation des hydrocarbures alkylaromatiques sont considérablement améliorées en ajoutant des composés de brome au catalyseur au cobalt dans l’acide acétique.
Cette méthode est maintenant largement utilisée dans la production d’acide téréphtalique et est également applicable au procédé à l’acide benzoïque.
Sous certaines conditions, l’acide benzoïque lui-même peut être utilisé comme solvant. Le manganèse a un effet synergique sur le catalyseur au cobalt.
Ce processus peut réaliser des vitesses de réaction élevées et une meilleure conversion du toluène, ainsi que l’élimination de l’inhibition de la réaction.
Cependant, pour éviter la corrosion, l’équipement doit être construit en titane coûteux. Un autre type d’activateur de catalyseur au cobalt est un composé carbonylé facilement oxydable tel que la méthyléthylcétone ou l’acétaldéhyde.
Ces additifs permettent une réduction considérable de la température de réaction, mais du fait de la forte consommation de ces activateurs, cette technologie ne semble pas pratique.
L’oxydation catalytique du toluène dans de l’hydroxyde de sodium aqueux donne directement du benzoate de sodium. Ce processus a été essayé depuis les années 1940, mais des rendements satisfaisants n’ont pas été atteints.
L’oxydation en phase vapeur du toluène à des températures plus élevées est un autre processus potentiel. Divers catalyseurs (vanadium, tungstène, uranium, molybdène, argent, etc.) ont été étudiés, mais les rendements n’étaient pas comparables à ceux du procédé en phase liquide.
2. Réactions chimiques de l’acide benzoique
L’acide benzoïque est stable vis-à-vis des agents oxydants courants. L’air, le permanganate, l’acide chromique, l’hypochlorite et l’acide nitrique dilué ne l’affectent pas. Cependant, au-dessus de 220 °C, il réagit avec les sels de cuivre (II) pour former du phénol et ses dérivés.
Cette réaction, suivie d’une régénération du cuivre (II) avec de l’oxygène moléculaire, est à la base de la production commerciale de phénol à partir de l’acide benzoïque. L’acide benzoïque réagit avec l’ammoniac dans des conditions similaires pour former de l’aniline. Lors du chauffage à 150 ° C, une certaine déshydratation a lieu pour former de l’anhydride benzoïque.
La décarboxylation se produit lorsque l’acide benzoïque est chauffé au-dessus de 370 °C ou aussi bas que 245 °C en présence de catalyseurs, formant du benzène et une petite quantité de phénol. La poudre de cuivre et de cadmium accélère la décarboxylation.
Lorsque le benzoate de potassium est chauffé dans du dioxyde de carbone, il se disproportionne en téréphtalate et en benzène. Les sels de cadmium et de zinc catalysent cette réaction.
L’acide benzoïque est converti en acides hydroxybenzoïques par l’hydroxyde de potassium fondu.
L’acide benzoïque peut être directement hydrogéné avec de l’hydrogène moléculaire pour donner du benzaldéhyde avec un rendement quantitatif. Le zirconium et d’autres oxydes métalliques catalysent la réaction.
L’hydrogénation sur des catalyseurs de métaux nobles donne l’acide cyclohexanecarboxylique (acide hexahydrobenzoïque).
La chloration donne principalement de l’acide 3-chlorobenzoïque.
La nitration de l’acide benzoique forme l’acide 3-nitrobenzoïque et la sulfonation forme l’acide 3-sulfobenzoïque.
3. Utilisations de l’acide benzoïque
La majorité de l’acide benzoïque est utilisée en captivité pour produire du phénol.
Les boissons et les applications alimentaires représentaient 41 % de la consommation mondiale d’acide benzoïque sous forme de benzoate de sodium et de potassium en 2006.
Les autres applications majeures comprennent les plastifiants au benzoate, les résines alkydes et le chlorure de benzyle.
Les esters glycoliques de l’acide benzoïque sont utilisés comme plastifiants pour les résines vinyliques. La demande a augmenté aux États-Unis en remplacement du phtalate de butyle et de benzyle dans les adhésifs en émulsion de poly(acétate de vinyle).
Un autre marché important est le benzoate de sodium pour les conservateurs et les anticorrosifs.
L’acide benzoïque est utilisé dans les résines alkydes modifiées pour les émaux de finition automobile afin d’améliorer les propriétés de surface.
L’acide benzoïque est également utilisé comme intermédiaire pour les parfums, les produits pharmaceutiques et les cosmétiques.
Les références
-
« Benzoic Acid and Derivatives », Ullmann’s Encyclopedia of Industrial Chemistry. – https://onlinelibrary.wiley.com/doi/10.1002/14356007.a03_555