
El 1,4-butanodiol (a menudo abreviado como 1,4-BDO) es un compuesto químico con la fórmula molecular C4H10O2. Es un líquido incoloro e inodoro que pertenece a la familia de los dioles, que son compuestos que contienen dos grupos hidroxilo (OH).
Tabla de contenido
1. Propiedades físicas del 1,4-butanodiol
El 1,4-butanodiol (masa molar: 90,12 g/mol) es un líquido transparente con olor mínimo y que presenta propiedades higroscópicas. Se disuelve fácilmente en agua, alcoholes, cetonas, éteres de glicol y acetatos de éter de glicol. Sin embargo, su solubilidad en éter y ésteres dietílicos es menor y no es soluble en hidrocarburos alifáticos y aromáticos ni en hidrocarburos clorados.
Tabla 1. Propiedades físicas del 1,4-butanodiol
Propiedad | Valor |
---|---|
Punto de fusión (Mp) | 20,2°C |
Punto de ebullición (Pb) | 230,5°C (a 101,3 kPa) |
Densidad (𝜚) | 1,017 g/cm³ (a 20°C); 1,0154 g/cm³ (a 25°C) |
Temperatura crítica (tc) | 446°C |
Presión crítica (pc) | 41,2 bares |
Viscosidad (𝜂) | 91,56 mPa·s (a 20°C); 71,5 mPa·s (a 25°C) |
Índice de refracción (nD) | 1,4460 (a 20°C); 1,4446 (a 25°C) |
Constante dieléctrica (𝜀) | 31,4 |
Punto de inflamación | 134°C |
2. Reacción química del 1,4-butanodiol
El 1,4-butanodiol se cicla fácilmente cuando se expone a un medio ácido, produciendo tetrahidrofurano.
Cuando se somete a deshidrogenación en fase gaseosa y utilizando catalizadores a base de cobre, forma 𝛾-butirolactona.
Además, el 1,4-butanodiol reacciona con ácidos monocarboxílicos dando diésteres. La esterificación con ácidos dicarboxílicos y sus derivados da como resultado la formación de ésteres poliméricos termoplásticos lineales, parcialmente cristalinos.
Alrededor de 200 °C, el 1,4-butanodiol reacciona con amoníaco o una amina utilizando catalizadores de níquel o cobalto y en presencia de hidrógeno, produciendo pirrolidina o derivados de pirrolidina.
El fosgeno reacciona con 1,4-butanodiol a -5∘C, produciendo el bis(cloroformiato) de butanodiol.
El acrilonitrilo sufre una reacción de adición con al 1,4-butanodiol a temperaturas entre 20 y 100 ∘C, con la presencia de cantidades catalíticas de álcali, lo que da lugar a 1,4-bis(2-cianoetoxi)butano.
Al igual que otros alcoholes, el 1,4-butanodiol también puede sufrir vinilación, lo que da como resultado la formación de éter mono o divinílico.
3. Producción de 1,4-butanodiol
Desde la década de 1990 se han desarrollado diversas tecnologías alternativas para la producción de 1,4-butanodiol. La tecnología Reppe, que se basa en acetileno y formaldehído, sigue siendo el método más utilizado.
Además, otros procesos utilizan benceno o butano mediante anhídrido maleico, propileno, butadieno y azúcares como rutas alternativas para su fabricación.
3.1. 1,4-butanodiol a partir de 2-butino-1,4-diol
El 1,4-butanodiol se fabrica a gran escala industrial mediante hidrogenación continua de 2-butino-1,4-diol. Este proceso emplea predominantemente catalizadores de níquel modificados. El proceso de flujo de dos etapas se lleva a cabo dentro del rango de temperatura de 80-170∘C y a una presión de 250-300 bar.

El proceso comienza con una solución acuosa de 2-butino-1,4-diol (30-50%), junto con hidrógeno libre de monóxido de carbono y una mezcla de reacción reciclada, que actúa como medio disipador de calor.
Esta mezcla pasa a través de un catalizador de lecho fijo de tipo níquel reducido en el reactor de plomo, donde tiene lugar más del 99% de la reacción.
La temperatura inicial es de aproximadamente 80∘C y no debe exceder los 170∘C para evitar reacciones de descomposición no deseadas. La circulación del hidrógeno garantiza una mejor distribución del líquido. El segundo reactor o reactor de acabado completa la conversión de compuestos insaturados.
Los diferentes procesos empleados comercialmente se diferencian principalmente en el catalizador utilizado. BASF e Invista Technologies describen el Ni soportado sobre óxidos de circonio o aluminio, mientras que Invista utiliza y licencia el níquel Raney, empleado como catalizador de lecho fijo.
Otra variación implica la hidrogenación a baja presión a alrededor de 20 bar utilizando un catalizador de níquel Raney suspendido, seguida de una hidrogenación a 120-140∘C y 140-210 bar catalizada por un contacto de lecho fijo (por Ineos).
El producto bruto obtenido contiene metanol, propanol y butanol como subproductos, junto con trazas de 2-metil-1,4-butanodiol, 4-hidroxibutiraldehído, 𝛾-butirolactona, acetales y trioles.
Para obtener 1,4-butanodiol puro, el efluente del reactor se somete a una destilación fraccionada. Inicialmente, se eliminan el agua y los monoalcoholes como metanol, propanol y butanol. Posteriormente, el 1,4-butanodiol se separa de los productos de alto punto de ebullición, como trioles y sales, junto con impurezas como 𝛾-butirolactona, acetales, 2-metil-1,4-butanodiol y 4-hidroxibutiraldehído.
El 1,4-butanodiol puro se puede aislar aún más en una columna adicional, que separa 4-hidroxibutiraldehído, acetales y 𝛾-butirolactona como productos de punto de ebullición ligero.
3.2. 1,4-butanodiol a base de benceno o butano mediante anhídrido maleico
La oxidación en fase gaseosa del benceno o del n-butano con oxígeno conduce a la producción de anhídrido maleico. Este anhídrido maleico puede ser absorbido a partir del gas de oxidación por agua, dando como resultado ácido maleico, o por compuestos orgánicos de alto punto de ebullición como el ftalato de dibutilo.
La solución de ácido maleico en agua se puede hidrogenar en un proceso de alta presión para producir 1,4-butanodiol, con la presencia de catalizadores de carbón activo a base de Re dopados. Los dopantes utilizados en estos catalizadores son principalmente Pd y Pt.
Sin embargo, el proceso genera subproductos como n-butanol, n-propanol, metanol y tetrahidrofurano. A pesar de su simplicidad, el catalizador de hidrogenación es caro debido al alto contenido de metales preciosos.
En consecuencia, hasta el momento sólo se ha realizado una producción comercial de este proceso, realizada en Lima en Estados Unidos.
Un enfoque comercial más común implica la hidrogenación en fase gaseosa de diésteres maleicos, que se derivan del anhídrido maleico.
Este proceso fue desarrollado por Kvaerner Process Technology (KPT, Londres, ahora Johnson Matthey Davy Technologies (JM Davy)) en los años 1980. El primer paso consiste en producir maleato de dimetilo a partir de anhídrido maleico y metanol, utilizando una resina de intercambio iónico fuertemente ácida como catalizador.
A continuación, el maleato de dimetilo resultante se hidrogena en fase gaseosa utilizando un sistema catalítico que contiene Cu a una presión de 2-8 MPa y temperaturas de 150-250 ∘C.
Este proceso produce una mezcla de 1,4-butanodiol, tetrahidrofurano, butirolactona, una pequeña cantidad del intermedio succinato de dimetilo y, como subproducto principal, n-butanol.
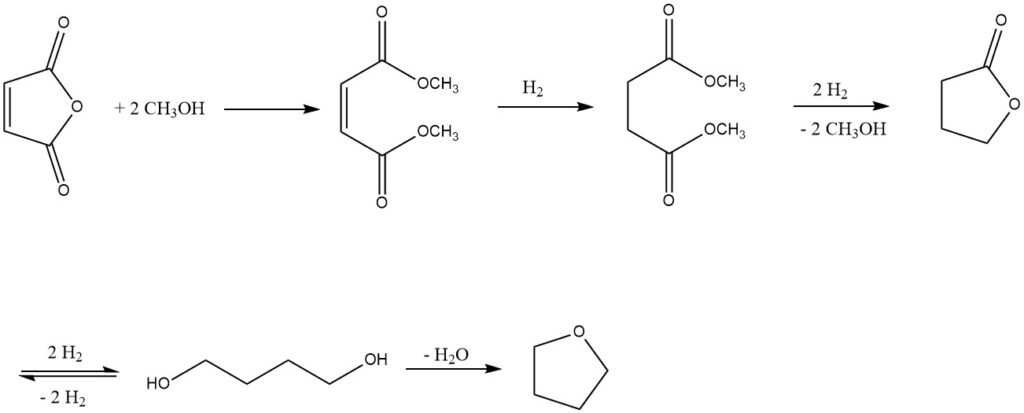
La butirolactona y el succinato de dimetilo se pueden recuperar como azeótropo y reciclarse nuevamente a la etapa de hidrogenación para lograr una conversión completa en 1,4-butanodiol y tetrahidrofurano.
JM Davy ha autorizado este proceso varias veces para establecer plantas de butanodiol/butirolactona/tetrahidrofurano en varios lugares de Asia, incluidos Arabia Saudita, Malasia, Corea y China.
3.3. 1,4-butanodiol a partir de propileno
Una materia prima alternativa para el 1,4-butanodiol es el propileno, que se puede obtener mediante alcohol alílico. Dairen en Taiwán y China, así como Lyondell en EE.UU. y Países Bajos, utilizan este proceso.
Para obtener alcohol alílico, primero se oxida el propileno a óxido de propileno, que luego se isomeriza (Lyondell) o se hidroliza a alcohol alílico. La hidrólisis implica la acetoxilación del propileno en fase gaseosa con oxígeno, lo que lleva a la formación de acetato de alilo, que posteriormente se hidroliza para producir alcohol alílico (Dairen).
El siguiente paso implica la hidroformulación de alcohol alílico en un disolvente con un catalizador homogéneo a base de rodio, produciendo 4-hidroxibutiraldehído. Un subproducto importante en este paso es el 3-hidroxi-2-metil-propionaldehído.
Después de extraer los aldehídos, se someten a hidrogenación utilizando níquel Raney como catalizador, dando como resultado 1,4-butanodiol, que luego se purifica por destilación.

Sin embargo, uno de los principales subproductos de esta reacción es el 2-metil-1,3-propanodiol. Además, otros subproductos formados durante este proceso incluyen n-propanol e isobutiraldehído.
3.4. 1,4-butanodiol a partir de butadieno
Mitsubishi emplea un proceso de tres pasos para producir 1,4-butanodiol:
- El butadieno y el ácido acético sufren una reacción catalítica para producir 1,4-diacetoxi-2-buteno.
- La hidrogenación posterior de 1,4-diacetoxi-2-buteno da 1,4-diacetoxibutano.
- Finalmente, la hidrólisis del 1,4-diacetoxibutano conduce a la formación de 1,4-butanodiol.
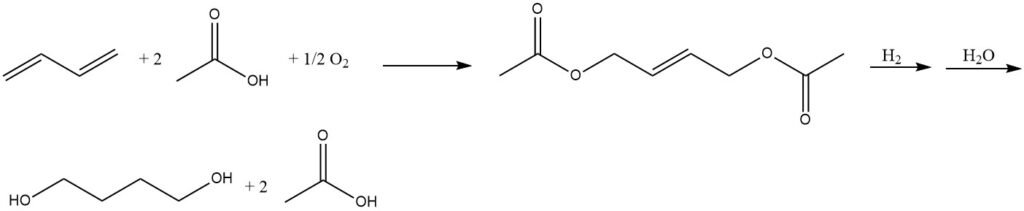
La hidrólisis del diacetato también puede producir tetrahidrofurano debido a las condiciones de reacción altamente ácidas.
BASF ha patentado un proceso similar, donde primero se agrega ácido acético al butadieno y el producto resultante se isomeriza a 1,4-diacetoxi-2-buteno.
El proceso de Toyo Soda implica la adición de cloro al butadieno para formar una mezcla de 1,4-dicloro-2-buteno y 3,4-dicloro-1-buteno. Esta mezcla reacciona con acetato de sodio para producir 1,4-diacetoxi-2-buteno, que luego se hidrogena directamente a 1,4-butanodiol.
En una patente descrita por Shell, el butadieno reacciona con hidroperóxido de terc-butilo usando un catalizador de cobalto para formar 1,4-di(terc-butilperoxi)buteno-2, que luego se convierte en 1,4-butanodiol mediante hidrogenación. Como subproducto se forma 1,2-butanodiol.
Eastman tiene un proceso diferente que comienza con butadieno como materia prima. Primero, el butadieno se oxida con oxígeno en presencia de un catalizador de plata para formar 1,2-epoxi-3-buteno. Luego, el epóxido se reordena para producir 2,5-dihidrofurano, que posteriormente se isomeriza a 2,3-dihidrofurano.
Después de la adición de agua catalizada por ácido hasta un equilibrio de 2-hidroxitetrahidrofurano y 4-hidroxibutiraldehído, seguida de hidrogenación, se genera 1,4-butanodiol. Alternativamente, la conversión de 2,5-dihidrofurano en 1,4-butanodiol se puede realizar como una síntesis en un solo recipiente.
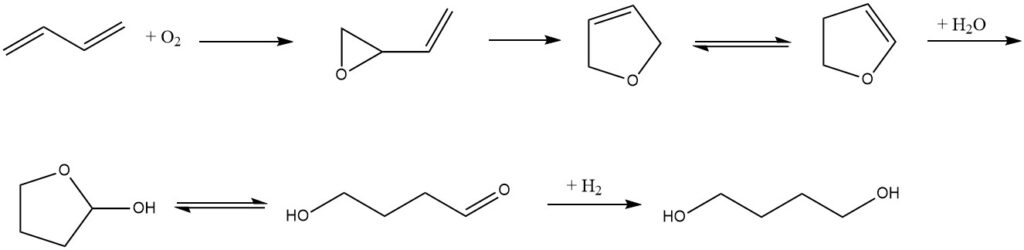
3.5. 1,4-butanodiol a partir de biomasa
En las últimas dos décadas se han realizado importantes esfuerzos para producir 1,4-butanodiol y sus derivados a partir de fuentes de biomasa.
Uno de los primeros enfoques implicó el uso de furfural, que puede descarbonilarse a furano.
BASF desarrolló un método prometedor en el que se hidrogena furano en presencia de agua y un catalizador a base de renio a presión elevada, lo que da como resultado la formación de 1,4-butanodiol. Como subproductos se producen 𝛾-butirolactona y n-butanol.
Shell también trabajó en la optimización del proceso utilizando catalizadores a base de renio. Con un catalizador de Re/Pd sobre carbono, Shell logró un alto rendimiento de tetrahidrofurano y 1,4-butanodiol como productos principales.
Algunas empresas utilizan métodos de fermentación a base de azúcar para obtener directamente 1,4-butanodiol o sus precursores. Genomatica desarrolló un proceso para producir 1,4-butanodiol fermentando glucosa utilizando la bacteria Escherichia coli genéticamente modificada. Tras la fermentación, el caldo contiene 1,4-butanodiol diluido en agua, además de biomasa y sales.
Un proceso de destilación separa el agua y, después de una minuciosa filtración y eliminación de sales, el 1,4-butanodiol crudo se hidrogena para eliminar las impurezas que pueden afectar la estabilidad del color.
La purificación adicional se lleva a cabo mediante etapas de destilación adicionales. El proceso Genomatica se ha implementado comercialmente en una planta (30 ×103 t de capacidad, Novamont) en Italia desde 2016.
Otro enfoque implica fermentar azúcares hasta obtener ácido succínico, que sirve como precursor para la producción de 1,4-butanodiol. Empresas como BioAmber, Myriant, Reverdia y Succinity han participado en la comercialización de este proceso de fermentación.
La fermentación directa de azúcares a ácido succínico requiere control del pH debido al bajo pH resultante del caldo de fermentación. Para el control del pH se utilizan materiales básicos como amoníaco o hidróxidos alcalinos/térreos.
El succinato de diamonio resultante se puede tratar con ácido sulfúrico para liberar ácido succínico. Luego, el ácido succínico se puede convertir en 1,4-butanodiol mediante hidrogenación en fase gaseosa como anhídrido o diéster utilizando catalizadores a base de Cu o mediante hidrogenación en fase líquida utilizando catalizadores a base de metales preciosos.
La fermentación de azúcares también puede dar lugar a 𝛾-butirolactona. Metabolix desarrolló un método para convertir azúcares en un proceso de fermentación en poli(4-hidroxibutirato) (poli(butirolactona)), que puede despolimerizarse en butirolactona en presencia de un catalizador a temperaturas superiores a 200 ∘C.
Los mejores resultados se logran con hidróxido de calcio como catalizador y la biomasa residual se convierte en combustible sólido. Sin embargo, aún no se ha establecido ninguna planta comercial para este proceso.
4. Usos del 1,4-butanodiol
El 1,4-butanodiol desempeña un papel crucial como intermediario versátil en la industria química y sirve como precursor de la 𝛾-butirolactona y el tetrahidrofurano.
Su aplicación más importante radica en la producción de poliuretanos y poliésteres, como el poli(tereftalato de butileno), comúnmente conocido como PBT. Estos materiales tienen diversos usos en diversas industrias.
Los poliuretanos derivados del 1,4-butanodiol se emplean en la producción de elastómeros celulares y compactos, que encuentran una amplia gama de aplicaciones debido a su elasticidad y resiliencia.
El poli(tereftalato de butileno) se procesa ampliamente para crear materiales plásticos y adhesivos termofusibles. Además, se utiliza en la producción de películas y fibras plásticas, lo que lo convierte en un material versátil utilizado en diferentes productos e industrias.
Referencias
- Butanediols, Butenediol, and Butynediol, Ullmann’s Encyclopedia of Industrial Chemistry. – https://onlinelibrary.wiley.com/doi/10.1002/14356007.a04_455.pub2
-
Organic Acids: Succinic and Malic Acids. – https://www.sciencedirect.com/science/article/abs/pii/B9780444640468001592
- https://www.industrialchemicals.gov.au/sites/default/files/1-4-Butanediol.pdf