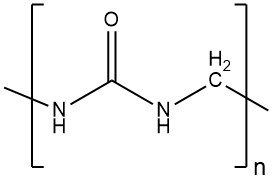
All urea–formaldehyde condensates containing the recurring unit urea-methyl, from monomolecular to high molecular products. During the 1970s, multiple revelations emerged regarding the composition of urea–formaldehyde resins.
The progress of industrial applications relied on empirical approaches. By application of diverse analytical methods, such as 1H NMR and 13C NMR spectroscopy, elemental analyses including C, H, N, and O, quantification of hydroxymethyl groups, as well as determination of total formaldehyde content was possible.
However, the interrelation between the technical characteristics of amino resins, or materials derived from these resins, and the distribution of structural units, remains largely difficult in most cases.
Table of Contents
1. Pure Urea–Formaldehyde Resins
The molar ratio of formaldehyde to urea, viscosity, and gelling time are important macroscopic parameters of pure urea-formaldehyde resins. Resins with a molar ratio of 1 usually give insoluble polymethylene ureas that do not possess any adhesive properties.
However, if the molar ratio is reduced from a relatively high value gradually or stepwise during the course of the reaction, the resultant resin possesses adhesive properties. These properties improve as the molar ratio increases, but the undesirable release of formaldehyde increases simultaneously.
The highly viscous resin solutions obtainable by prolonged industrial condensation of urea and formaldehyde are low molecular mass products. They contain about six to eight urea units. This also applies to the completely insoluble powdered or glassy condensates.
During storage, the concentration of methylene groups increases at the expense of the hydroxymethyl groups. The viscosity also increases, initially slowly and virtually linearly, and then, after a critical time, rather steeply.
Some or all of the hydroxymethyl groups can be blocked by etherification, and the shelf life of the amino resin is thus extended. In principle, the same reactions take place when the resin is hardened by the user, but they are substantially more rapid. However, a residual amount of hydroxymethyl groups remains after hardening.
Because they are susceptible to hydrolysis, even the cured urea resins are more water sensitive than the phenol or melamine resins.
The gelling time or reactivity of the resin is an important parameter for the user. This time can be determined relatively precisely, and is the time in which the resin changes from a fluid to a virtually immobile solid following the addition of a certain amount of hardener at a particular temperature.
The reactivity increases with increasing molar ratio, content of hydroxymethyl groups, and content of free formaldehyde.
2. Mixed Condensates
Industrial amino resins are mixtures of various condensates and co-condensates. Amino resin solutions are always polymeric mixtures with different degrees of condensation and distributions of functional groups.
The term “mixed condensates” is loosely applied to resins that are formed in the condensation of urea and formaldehyde when the reaction is carried out using substances that also form resins with formaldehyde. These substances include melamine, phenol, organic acid amides, sulfonamides, and carbamates.
For example, in the presence of melamine or phenol, it is possible to prepare urea resins with improved strength and swelling properties for the manufacture of particle board, such as weather-resistant particle board.
Modification with melamine gives resin glues that can be used to produce good-quality particle board even when the molar ratio of formaldehyde to urea is low.
Mixed resins with other resin formers, such as acrylic acid, acrylates, and acrylamide, are also sometimes advantageous. These are also mixtures of polymers, of co-condensates, or of homologous polymers and co-condensates.
3. Condensation of Urea with other Aldehydes
Urea can be condensed with other aldehydes besides formaldehyde. For example, it can be condensed with isobutyraldehyde, acetaldehyde, or crotonaldehyde to produce sparingly soluble nitrogen fertilizers. These fertilizers are also known as controlled-release fertilizers because they release nitrogen slowly over time.
Urea can also be condensed with glyoxal to produce products that can be used as textile auxiliaries. Textile auxiliaries are substances that are used to improve the properties of textiles, such as their strength, color, or luster.
Products obtained by the subsequent condensation of urea-formaldehyde resins with glyoxal are also used for textile finishing. Textile finishing is the process of applying chemicals to textiles to improve their properties.
4. Resins from Urea Derivatives
The condensation with urea derivatives or their substitution is a well-known. However, these reactions have industrial significance primarily in the creation of auxiliary agents for textiles and paper.
Reactions involving aldehydes depend on the existence of remaining hydrogen atoms at the nitrogen sites. However, the inclination to engage in condensation significantly decreases as the number and size of substituents increase.
Reacting a symmetrically disubstituted urea derivative, such as N,N’-dimethylurea or dihydroxymethylurea dimethyl ether, in conjunction with formaldehyde in an acidic milieu, yields cyclic urea derivatives of urones.
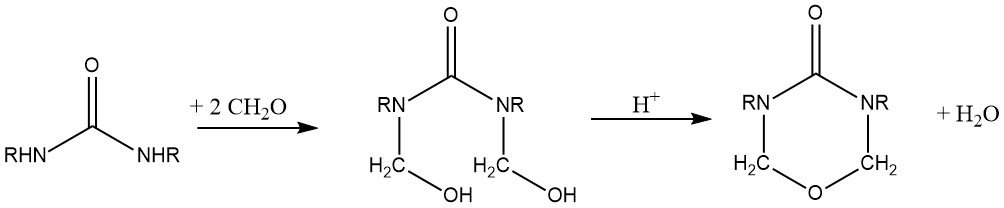
Of industrial utility is dihydroxymethylurone dimethyl ether, specifically bis(methoxymethyl)urone, which makes cellulose fabrics wrinkle-resistant. Its reactivity and resilience to hydrolysis is realatively good.
Urones react with cellulose, yet they generate minimal quantities of self-cross-linked resins, similar to urea–formaldehyde compounds.
When sulfur (S) substitutes the oxygen (O) in urea, the result is thiourea. This thiourea exhibits all principal condensation reactions attributed to urea. In a mildly alkaline milieu, N-hydroxymethyl compounds as well as S-hydroxymethyl compounds are formed.
For the latter, the initial postulation adopts the tautomeric structure NH2–C(SH)=NH. Thiourea–formaldehyde condensates surpass their urea counterparts in water resistance. Several thiourea condensates are hypothesized to form a cyclic molecular arrangement.
5. Modified Urea Resins
Amino resins can be modified in many ways with different fonctional groups.
5.1. Reactions with Alcohols
Amino resins can be modified by etherifying the hydroxymethyl groups with alcohols in an acidic medium.

The equilibrium constant for the etherification of monohydroxymethylurea and dihydrox-ymethylurea with methanol and ethanol has been measured. The enthalpy of reaction is ΔH= -6 to -8 kJ/mol. The equilibrium constants (K) differ depending on the substitution:
As the number of C atoms in the alcohol increases, the equilibrium is shifted to the left and the reaction rate reduced so that the etherification becomes more difficult.
The ethers of the low-boiling alcohols can be transetherified with higher boiling alcohols by heating the mixture in weakly acidic solution and distilling the more volatile alcohols.
Frequently only some of the hydroxymethyl groups of resin glues and impregnating resins undergo etherification with monohydric or polyhydric alcohols of less than five carbon atoms. As a result, some of the hydroxymethyl groups are protected against condensation, and the resins have a longer shelf life.
In the starting materials for surface coatings, 20–100% of the hydroxymethyl groups undergo etherification, depending on the type. The amino resins etherified with butyl groups are the most important for wood coatings, e.g., parquet coating.
Where complete etherification takes place, the reaction is carried out using an entraining agent – the alcohol it-self, toluene, or xylene – and the water is distilled azeotropically.
Ethers of one- to three-carbon alcohols with low molecular mass hydroxymethyl compounds of urea, ethylene urea (imidazolidinone), propylene urea (1,3-bis(hydroxymethyl) tetrahydro-2-(1H)-pyrimidinone), and melamine have achieved some importance in the field of textile auxiliaries.
These compounds are precondensates having relatively low molecular masses of about 600.
Urea resins etherified with butyl groups can be employed as starting materials for making surface coatings. However, when baked alone, they give brittle and water-sensitive films.
Therefore, they cannot be used alone as binders. In combination with nitrocellulose, or with alkyd, epoxy, or acrylate resins, they give excellent baked finishes.
5.2. Ammonia and Amines Reactions
Amines display high reactivity when reacting with hydroxymethyl compounds from urea and formaldehyde. Ammonia, in particular, reacts with the hydroxymethyl group, resulting in the formation of either an amino or imino group, accompanied by the elimination of water:
-NH-CH2OH + NH3 → -NH-CH2NH2 + H2O
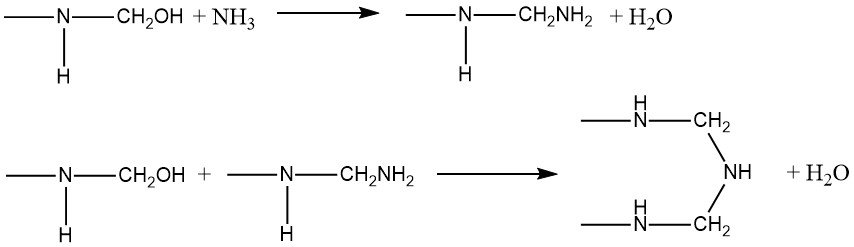
The reaction between ammonia and formaldehyde is exothermic (ΔH = -57 kJ/mol), generating hexamethylenetetramine. This process has found industrial application in capturing formaldehyde from waste gases, such as those emanating from particle board production. When urea and aldehydes are combined with primary amines, they yield cyclic compounds, referred to as triazines of type (1), where R’ can be hydroxymethyl, its methyl, or ethyl ethers.
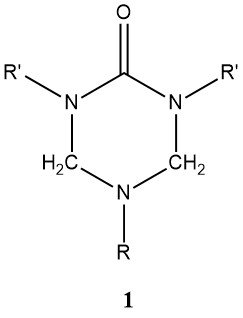
Ammonia, primary or secondary amines, or polyamines having two or more primary amino groups, are used in the production of amino-modified resins. These modified resins exhibit greater stability in the presence of water when compared to unchanged resins produced by similar processes.
Ammonia and amines can react with hydroxymethyl groups in urea, under weakly acidic or alkaline conditions, to yield N-aminomethyl groups. In strongly acidic solutions, these groups eliminate the amine substituents to produce condensates.
Even highly condensed urea resins retain the capacity to bind substantial quantities of ammonia and amines because a portion of the formaldehyde persists in the form of hydroxymethyl groups. This industrial application is employed in the deodorization of resins or particle board.
The condensation of the resin molecule with an amine results in a resin with a cationic character. This characteristic increases the resin’s affinity for cellulose fibers, rendering it valuable as an auxiliary agent in textiles or paper production. These basic urea resins enhance the wet tensile strength of paper.
5.3. Reaction with Sulfites
The hydroxymethyl groups of amino resins can react with hydrogen or other sulfites to form an aminomethanesulfonate, which imparts an anionic character to the resins. The pH of the solution controls the sulfite content.
R-NH-CH2OH + [HSO3]– → [R-NH-CH2SO3]– + H2O
To produce resins of this type, the reaction of urea and formaldehyde is begun in a neutral or alkaline medium to achieve hydroxymethylation. After the desired degree of conversion has been reached, condensation is carried out using sulfite or hydrogen sulfite in a slightly acidic solution.
The resin can react with hydrogen sulfite because there are still many hydroxymethyl groups present. Even water-insoluble resins can be made soluble by treating them with hydrogen sulfite after the reaction is complete.
Anionic amino resins are of particular industrial importance in the field of water-soluble or water-dispersible adhesives. Other uses include textile auxiliaries, paper auxiliaries, leather auxiliaries, and deodorants.
In addition to modification with sulfite, patents mention many other modifiers, such as aldehydes and triazines. The affinity of anionic resins for cellulose is lower than that of cationic resins, so the fibers must be posttreated with aluminum sulfate to fix the resins.
The modification of urea–formaldehyde resin glues with ligninsulfonic acid has also been mentioned. The products are dark resin solutions that have been used from time to time in the woodworking industry.
Lignin contains phenolic groups, and the incorporation of lignin components imparts relatively high water resistance. However, the lignins are of different origins and compositions, so the production process must be adapted empirically to the different lignin varieties. This fact and the dark coloration have prevented more extensive use of lignin wastes from wood pulp production.
Reference
- Amino Resins; Ullmann’s Encyclopedia of Industrial Chemistry. – https://onlinelibrary.wiley.com/doi/10.1002/14356007.a02_115.pub2