Acetaldehyde is produced from the following raw materials: ethanol obtained through the fermentation of carbohydrates or the hydration of ethylene, acetylene, ethylene, lower hydrocarbons, carbon monoxide and hydrogen and methanol.
The economic viability of commercial processes relies on the availability and prices of raw materials. In highly industrialized nations, where maintaining high prices for ethanol through fiscal measures was challenging or where petrochemical ethanol was unavailable (as was the case in Germany or Japan before 1939), acetylene became the preferred starting material for acetaldehyde.
The acetylene process continues to be used in some Eastern European countries and by companies that have access to inexpensive acetylene. However, in other countries, petrochemically produced ethanol became the favored raw material, while ethanol derived from fermentation was and still is used to a lesser extent in countries with a less significant chemical industry.
In Western countries, including Japan, these processes have largely been replaced by the direct oxidation process developed in the late 1950s by Wacker-Chemie and Hoechst. This shift occurred because ethylene is available at a lower cost compared to acetylene.
Even two-stage processes that employ ethanol derived from ethylene as the starting material are no longer competitive due to the diminishing importance of acetaldehyde as an organic intermediate.
In general, processes based on acetylene, ethylene, and ethanol have higher selectivity compared to the oxidation of saturated hydrocarbons. This is because, in the latter case, additional oxidation products are formed alongside acetaldehyde.
However, these processes are economically viable only in large-scale operations where all primary and secondary products obtained during the process are utilized, as the separation of the product mixture can be costly.
Table of Contents
1. Production of Acetaldehyde from Ethanol
To produce acetaldehyde, there are two methods involving ethanol: dehydrogenation and oxidation in the presence of oxygen. Between 1918 and 1939, dehydrogenation was favored due to the simultaneous production of hydrogen. However, later on, catalytic vapor-phase oxidation of ethanol became the preferred process, likely due to the extended catalyst lifespan and the potential for energy recovery.
1.1. Dehydrogenation of Ethanol
The initial studies on ethanol dehydrogenation, documented in 1886, involved passing ethanol through glass tubes at 260 °C.
CH3CH2OH → CH3CHO + H2 ΔH = +82.5 kJ/mol
Improved yields are achieved with catalysts such as platinum, copper, or zinc, nickel, or cobalt oxides. Subsequent patents mention zinc and chromium catalysts, rare earth metal oxides, and mixtures of copper and chromium oxides. Copper catalysts yield the least amount of decomposition products, but frequent catalyst regeneration is necessary.
1.1.1. Process Description
Ethanol vapor is directed through a tubular reactor containing a catalyst composed of copper sponge or copper activated with chromium oxide at temperatures of 260-290 °C. Each run results in a conversion rate of 25-50%.
Acetaldehyde and ethanol are separated from the exhaust gas, primarily composed of hydrogen, through alcohol and water washing. Pure acetaldehyde is obtained via distillation, while ethanol is separated from water and higher-boiling products through distillation and returned to the reactor.
The final acetaldehyde yield is approximately 90%. Byproducts include butyric acid, crotonaldehyde, and ethyl acetate.
1.2. Oxidation of Ethanol
The oxidation of ethanol is the oldest and most effective laboratory method for synthesizing acetaldehyde. In the commercial process, ethanol is catalytically oxidized with oxygen (or air) in the vapor phase.
CH3CH2OH + 0.5 O2 → CH3CHO + H2O ΔH = -242 kJ/mol
Copper, silver, and their oxides or alloys are commonly used catalysts.
1.3. Veba-Chemie Process
In the Veba-Chemie process, ethanol is combined with air and passed over a silver catalyst at temperatures ranging from 500 to 650 °C. The specific temperature depends on the alcohol-to-air ratio and gas flow rate through the catalyst.
Alcohol conversion ranges from 50% to 70%, while the yield varies between 97% and 99%, depending on the reaction conditions. Acetaldehyde and unconverted alcohol are separated from the waste gas through cold alcohol washing and fractional distillation.
After concentration, the alcohol returns to the reactor. Heat generated during the reaction is utilized for steam production using a waste-heat recovery system immediately after the reaction zone.
The waste gas mainly consists of nitrogen, hydrogen, methane, carbon monoxide, and carbon dioxide, and is burned as low-calorific-value lean gas in steam generators. Small amounts of acetic acid are produced as a byproduct.
2. Production of Acetaldehyde from Acetylene
The use of mercury compounds serves as the primary catalyst for the industrial water addition process (hydration) in acetylene production.
To achieve successful industrial implementation of this method, it is important to eliminate the polymerization and condensation products of acetaldehyde formed in an acidic environment.
In 1912, the Consortium für elektrochemische Industrie proposed a process that utilized excess acetylene at an elevated temperature. It involved the immediate removal of the acetaldehyde product from the reaction liquid.
Simultaneously, the heat generated during the reaction was dissipated by distilling an appropriate amount of water. Secondary reactions, such as the oxidation of acetaldehyde to form acetic acid and carbon dioxide, resulted in the reduction of Hg2+ to metallic mercury. Acetaldehyde production from acetylene has now been discontinued in Western countries.
2.1. Wet Oxidation Process (Hoechst)
The wet oxidation process offered a solution to avoid direct handling of toxic mercury compounds. It was employed by Wacker-Chemie, among others, until the switch to ethylene as the starting material in 1962.
In this method, iron(III) sulfate was added to reoxidize the mercury metal to the mercury(II) salt, ensuring adequate concentrations of the active catalyst. Acetylene reacted with the aqueous catalyst solution at 90-95 °C.
Approximately 30-50% of the injected acetylene underwent reaction in each run. The gas emerging from the reactor was cooled, leading to the separation of mainly water and traces of mercury, which were then returned to the reactor.
Acetaldehyde and water were condensed in additional coolers, and the acetaldehyde was finally washed out with water from the cooled cycle gas. This process yielded an 8-10% aqueous acetaldehyde solution.
Nitrogen was introduced with the feed gas, while carbon dioxide was produced as a byproduct. To prevent excessive accumulation, these gases were removed by withdrawing a small stream of the cycle gas.
Iron(II) sulfate was formed during the reaction and oxidized in a separate reactor with 30% nitric acid at 95 °C. Pure acetaldehyde was obtained through fractional distillation of the aqueous solution at approximately 200 kPa.
2.2. Chisso Process
The Chisso process employed a sulfuric acid/mercury sulfate solution as a catalyst. The acetylene reacted completely with the catalyst solution at 68-78 °C and a gauge pressure of 140 kPa.
A combination of pressure and vacuum process stages, conducted at low temperatures and without excess acetylene, allowed for the isolation and distillation of pure acetaldehyde, utilizing the heat generated during the reaction.
Similar to the Hoechst process, the catalyst could be regenerated with nitric acid. However, production of acetaldehyde using this method was discontinued at Chisso Corp. over a decade ago.
2.3. Production via Vinyl Ether
REPPE at BASF introduced a method using vinyl ether, completely avoiding the use of toxic mercury compounds. Methanol was added to acetylene at 150-160 °C and 1600 kPa in the presence of potassium hydroxide, resulting in the formation of methyl vinyl ether. The methyl vinyl ether was then hydrolyzed with dilute acid.
2.4. Production via Ethylidene Diacetate
The addition of acetic acid to acetylene in the presence of mercury(II) salts yielded ethylidene diacetate (CH3CH(OCOCH3)2). This compound decomposed into acetaldehyde and acetic anhydride at 130-145 °C with the aid of acid catalysts such as ZnCl2.
Although this process was initially developed by Societe Chimique des Usines du Rhone on an industrial scale in 1914, it has lost significance in recent times.
3. Production from Ethylene
Ethylene has become the primary feedstock for acetaldehyde production, with the Wacker process being the dominant method for direct oxidation of ethylene.
3.1. Direct Oxidation of Ethylene
The Wacker process, developed by Wacker-Chemie and Hoechst between 1957 and 1959, involves the following reaction:
CH4 + 0.5 O2 → CH3CHO ΔH= -244 kJ/mol
A catalyst solution containing PdCl2 and CuCl2 is used. The reaction between ethylene and aqueous palladium chloride was found to produce acetaldehyde almost quantitatively:
C2H4 + PdCl2 + H2O → CH3CHO + Pd + 2 HCl
In the Wacker-Hoechst process, metallic palladium is reoxidized by CuCl2, which is then regenerated with oxygen:
Pd + 2 CuCl2 → PdCl2 + 2 CuCl
2 CuCl + 0.5 O2 + 2 HCl → 2 CuCl2 + H2O
Therefore, only a small amount of PdCl2 is needed for ethylene conversion, and the rate-determining step is the reaction of ethylene with palladium chloride.
The process can be carried out in one or two stages. In the one-stage method, an ethylene-oxygen mixture reacts with the catalyst solution. A stationary state is established where the acetaldehyde formation and CuCl2 reduction occur at the same rate. The catalyst’s degree of oxidation, expressed as the ratio of CCu2+/(CCu2++CCu+), determines this stationary state.
In the two-stage process, ethylene and oxygen react separately in different reactors, and the catalyst solution is alternately reduced and oxidized. Air is typically used for catalyst oxidation instead of pure oxygen.
3.1.1. One-Stage Process
In the one-stage process, ethylene and oxygen are introduced into a reaction tower. The catalyst solution is circulated and mixed with the gas using the airlift principle. The reaction takes place at around 130 °C and 400 kPa.
The resulting mixture of acetaldehyde, water vapor, and unconverted gas is separated, cooled, and washed to separate the reaction products.
Unconverted gas is recycled back to the reactor, with a small portion discharged as exhaust gas to prevent inert gas accumulation. The crude acetaldehyde obtained from washing is then distilled in two stages to obtain purified acetaldehyde.
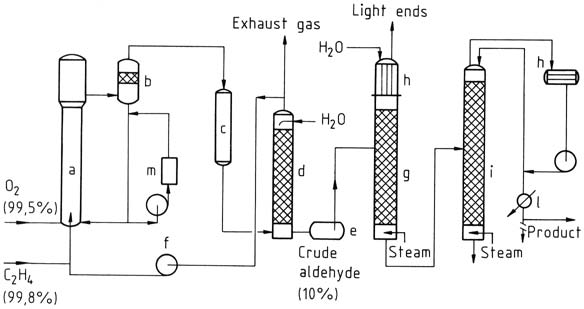
a) Reactor; b) Separating vessel; c) Cooler; d) Scrubber; e) Crude aldehyde tank; f) Cycle-gas compressor; g) Light-ends distillation; h) Condensers; i) Purification column; l) Product cooler; m) Regeneration
3.1.2. Two-Stage Process
The two-stage process involves using tubular reactors for both the reaction and oxidation steps. The gases react almost completely in the presence of the catalyst. Ethylene reacts at lower temperatures and pressures, and the catalyst solution containing acetaldehyde is then expanded in a flash tower.
The acetaldehyde-water vapor mixture is distilled, and the catalyst is recycled for the reaction with ethylene. The process water is reused, and a portion is used for scrubbing exhaust air and gas to remove impurities. The crude acetaldehyde is subjected to two-stage distillation to obtain pure acetaldehyde.
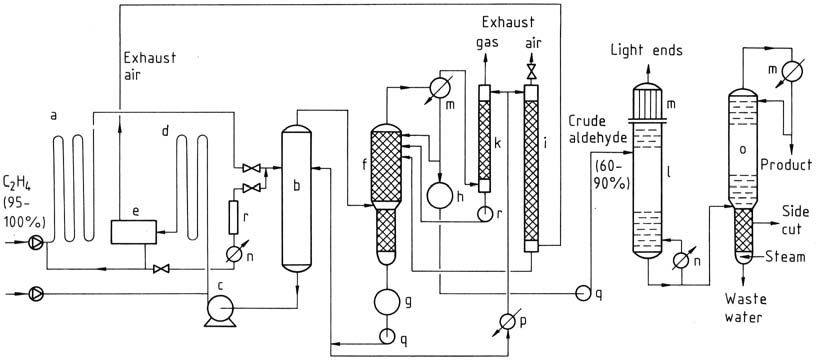
a) Reactor; b) Flash tower; c) Catalyst pump; d) Oxidation reactor; e) Exhaust-air separator; f) Crude-aldehyde column; g) Process-water tank; h) Crude-aldehyde container; i) Exhaust-air scrubber; k) Exhaust-gas scrubber; l) Light-ends distillation; m) Condensers; n) Heater; o) Purification column; p) Cooler; q) Pumps; r) Regeneration
Both the one-stage and two-stage processes have a similar acetaldehyde yield of around 95% and comparable production costs. The choice between the methods depends on factors such as raw material availability, energy considerations, and the cost of oxygen.
3.2. Formation of Acetaldehyde as a Byproduct
The generation of acetaldehyde occurs during the manufacturing process of vinyl acetate from ethylene or acetylene. Distillation is employed to separate acetaldehyde, which is subsequently converted into acetic acid for recycling purposes.
In a specific variation of the method starting from ethylene, both vinyl acetate and acetaldehyde are obtained in equal molar proportions of 1:1. This characteristic renders the process almost self-sufficient in terms of acetic acid production.
3.3. Ethylene Oxide Isomerization
Before the direct oxidation of ethylene became the preferred method, extensive research was conducted on this process. Catalysts such as Al2O3, SiO2, and acid salts derived from mineral acids like sulfuric acid, phosphoric acid, or molybdic acid were employed. Although yields of 90-95% have been reported, this approach has not gained significant industrial significance.
4. Production from C1 Sources
Following the oil price increases in 1973/74 and 1977, C1 materials garnered interest as feedstock for organic chemicals and as alternatives to petrochemicals. However, in terms of acetaldehyde production, C1 materials appear to have limited importance since most traditional acetaldehyde derivatives can be synthesized from C1 sources.
4.1. Direct Production from Synthesis Gas
Acetaldehyde is formed with relatively low selectivity, yielding approximately 30% from synthesis gas. The resulting mixture also contains acetic acid, ethanol, and saturated hydrocarbons, primarily methane. Catalysts comprising cobalt and rhodium compounds activated by iodine compounds or magnesium chloride, supported on a silicate carrier, are utilized. To date, this process has not found industrial applications.
4.2. Production via Methanol, Methyl Acetate, or Acetic Anhydride
The hydroformylation of methanol using CO/H2, known as the oxo process, has been well-established. This reaction occurs in the presence of hydroformylation catalysts such as cobalt, nickel, and iron salts (e.g., CoBr2, CoI2) or the corresponding metal carbonyls.
It is conducted at elevated temperatures (180-200 °C) and high pressure (30-40 MPa). An acetaldehyde selectivity of 80% or higher has been reported using iron-cobalt carbonyl or cobalt-nickel catalysts in conjunction with tertiary amines, phosphines, or nitriles.
Similarly, high selectivity has been claimed for the hydrocarbonylation of methyl acetate using palladium or rhodium catalysts, accompanied by tertiary phosphines and iodine compounds, or cobalt-ruthenium catalysts, in the presence of methyl and sodium iodides.
Certain patents describe the generation of acetaldehyde through the reduction of acetic anhydride with hydrogen over palladium or platinum catalysts supported on a carrier, operating at low pressures and moderate temperatures. If the future diminishes the significance of acetaldehyde as an organic intermediate, this method could prove interesting for economically producing small quantities of acetaldehyde.
5. Production from Hydrocarbons
Acetaldehyde is an incidental byproduct in the production of acrolein, acrylic acid, and propene oxide from propene. Additionally, it is formed by the oxidation of saturated hydrocarbons (e.g., propane or butane) in the gas phase, as implemented by Celanese in the United States.
Reference
- Acetaldehyde; Ullmann’s Encyclopedia of Industrial Chemistry. – https://onlinelibrary.wiley.com/doi/10.1002/14356007.a01_031.pub2