The majority of potential pathways to obtain hydrazine are limited due to the availability of raw materials and production costs. Nitrogen and ammonia stand out as the only viable starting materials for a more straightforward process.
An evaluation of the standard free energy variation ΔF°(g) (298 K) within the gaseous system H2-N2-NH3-N2H4 indicates that the direct synthesis of hydrazine from nitrogen and hydrogen is energetically unfavorable. The formation free energy strongly favors the production of ammonia.
Despite ongoing efforts, there is currently no practical or cost-effective solution for selectively reducing nitrogen. Therefore, ammonia remains the only valuable nitrogen source for hydrazine production.
On paper, the coupling of two ammonia molecules with concurrent hydrogen production appears to be an appealing process. However, it is both endothermic and highly inefficient.
For example, various methods such as electric discharge, photolysis, or radiolysis used to decompose ammonia yield only low amounts of hydrazine. An alternative approach is the oxidizing the hydrogen atoms separated from ammonia.

In an industrial setting, only three oxidants are significant: chlorine, oxygen, and hydrogen peroxide.
An additional challenge arises from the fact that hydrazine, a much stronger reducing agent than ammonia, can also react with the oxidizing agent.
Chlorine has been extensively employed in the Raschig process, which is still in operation. To prevent further oxidation of hydrazine by chlorine, highly diluted conditions must be used, resulting in yields no greater than 60%.
The hydrolysis of azines derived from acetone and butanone under pressure offers a means to produce hydrazine while regenerating the ketone.
Bayer has significantly improved yields by introducing acetone into the Raschig process.
In the 1970s, PCUK (now Atochem) developed a new, efficient, and environmentally friendly process based on the oxidation of ammonia by hydrogen peroxide in the presence of a ketone. Currently, most hydrazine is produced through the ketazine process, involving the oxidation of ammonia by either chlorine or hydrogen peroxide.
Table of Contents
1. Raschig Process
In the Raschig process, the oxidation of ammonia is achieved using sodium hypochlorite, which is obtained by reacting chlorine with sodium hydroxide.
The oxidation occurs in two steps. In the first step, carried out at approximately 5 °C, a rapid reaction forms chloramine:

Subsequently, the reaction mixture is combined with a significant excess of ammonia (with a ratio of 40:1), and the slow reaction that leads to hydrazine takes place at temperatures between 130 and 150 °C, under a pressure of 3.0 MPa:

Several notable side reactions can occur, including:

Upon exiting the reactor, the reaction solution contains approximately 1% hydrazine hydrate and around 4% sodium chloride. The pressure is then reduced to atmospheric levels using a series of evaporators.
Ammonia is condensed, concentrated, and recycled. The solution collected at the bottom of the stripping columns undergoes salt removal in a conventional forced-circulation salting evaporator. The resulting distillate is further concentrated to obtain 100% hydrazine hydrate.
To achieve reasonable yields in this process, it is important to use dilute solutions and maintain a high ratio of ammonia to hypochlorite. However, the costs associated with evaporation remain high, even with potential steam savings.
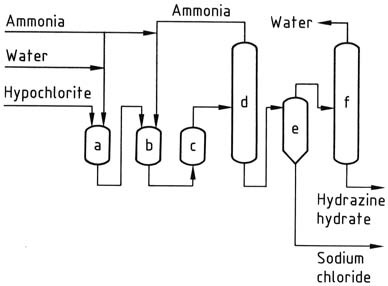
a) Chloramine reactor; b), c) Hydrazine reactors; d) Ammonia evaporator; e) Hydrazine – sodium chloride separator; f) Hydrazine hydrate concentrator
2. Olin Raschig Process
In the Olin Raschig process, for the production of anhydrous hydrazine in aerospace applications, precise control is exercised over the generation of sodium hypochlorite. A low temperature is employed to prevent decomposition and the formation of chlorate, while maintaining a minimal excess of sodium hydroxide.
The sodium hypochlorite solution is combined with three times the amount of ammonia at 5 °C to create chloramine. This chloramine is then rapidly introduced to a 30-fold excess of anhydrous ammonia under pressure (20-30 MPa) and heated to 130 °C.
The resulting reaction mixture, containing 1-2% hydrazine hydrate, undergoes treatment similar to the conventional Raschig process in order to obtain hydrazine hydrate. Anhydrous hydrazine is obtained by eliminating water through azeotropic distillation with aniline in a column operating at atmospheric pressure.
Condensation of the vapor produces a distillate with two layers, wherein the aqueous phase is removed and the aniline phase is refluxed back to the top of the column. Anhydrous hydrazine is recovered as a mixture with aniline, which can then be separated through distillation.
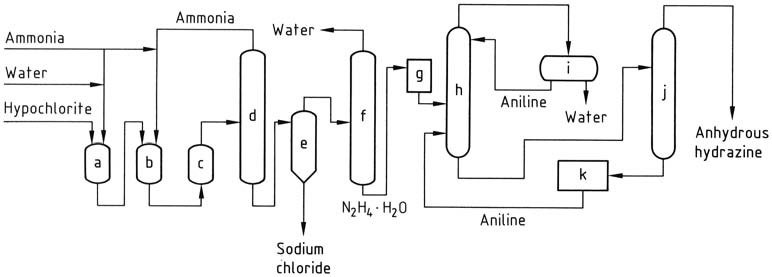
a) Chloramine reactor; b), c) Hydrazine reactors; d) Ammonia evaporator; e) Hydrazine – sodium chloride separator; f) Hydrazine hydrate concentration; g) Hydrazine hydrate storage; h) Hydrazine hydrate dehydration; i) Aniline – water decantation; j) Anhydrous hydrazine distillation; k) Aniline storage
3. Urea Process
Urea can serve as an alternative ammonia source in the Raschig process. While it is not presently employed for the commercial production of hydrazine hydrate, this approach has been utilized on a commercial scale.
Initially, it proved to be the most cost-effective method for smaller production volumes. However, as plants grew in size, the traditional Raschig process became more favorable, rendering the urea-based method obsolete.
Since 1990, significant quantities of hydrazodicarbonamide have been manufactured in Asia using the crude reaction mixture of urea and sodium hypochlorite as the hydrazine source.
However, this particular process involves the substantial generation of byproducts and requires expensive treatment of effluents. As a result, it is likely to become outdated over time.
4. Bayer Ketazine Process
The Bayer process is a modified version of the Raschig process that involves the reaction of chloramine with ammonia in the presence of acetone at a pH range of 12-14:
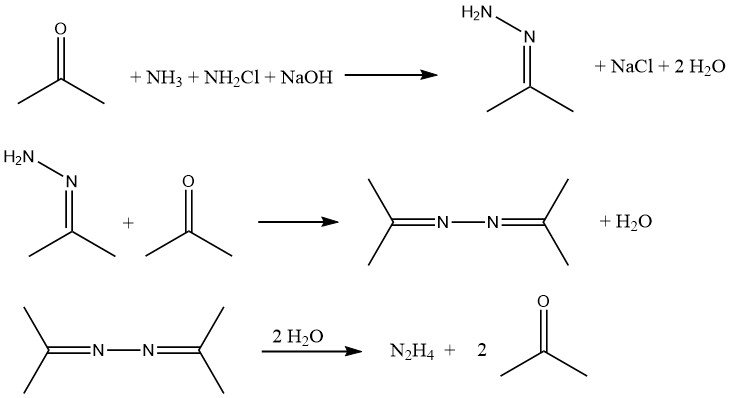
Simultaneously and continuously, sodium hypochlorite, acetone, and a 20% aqueous solution of ammonia (in a molar ratio of 1:2:20, respectively) are introduced into a reactor at approximately 35 °C and 200 kPa.
Excess ammonia is removed from the reaction mixture through stripping, then quenched with water and recycled back to the reactor as an aqueous solution.
The resulting aqueous solution containing dimethyl ketazine, with residual acetone, sodium chloride, and organic impurities, is fed into a distillation column. In this column, the dimethyl ketazine is recovered as an aqueous azeotrope (consisting of 55% dimethyl ketazine) at atmospheric pressure (boiling point of 95 °C at 101.3 kPa).
The introduction of acetone into the distillation column is intended to prevent premature hydrolysis of the ketazine. The byproduct obtained from the still is a solution of sodium chloride that contains traces of hydrazine and organic compounds. This solution requires treatment before disposal or recycling to electrolysis.
Next, the dimethyl ketazine undergoes hydrolysis in a pressurized distillation column (operating at 0.8-1.2 MPa), yielding acetone, which is recycled back to the reactor, and a 10% aqueous solution of hydrazine. The hydrazine solution is then concentrated to a hydrazine content of 64%.
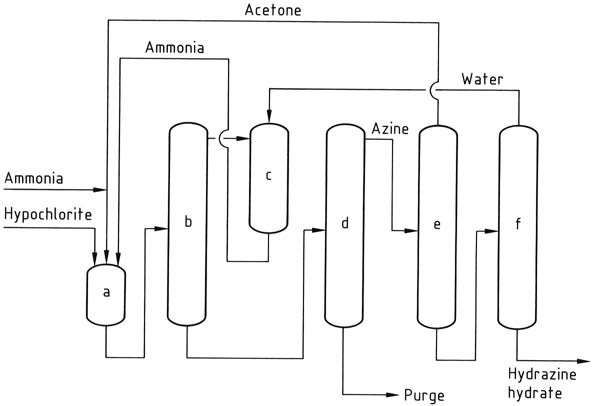
5. Fisons Process
The process, initially implemented by Whiffen and Sons, was further developed by Fisons and became operational in the 1960s. In this process, methyl ethyl ketone was employed instead of acetone to capture the hydrazine, and the hydrolysis step involved the use of sulfuric acid.
However, this particular process is no longer in operation.
6. Peroxide Process
The most recent hydrazine process, developed by PCUK and currently employed by ATOFINA in France and Mitsubishi Gas in Japan, utilizes hydrogen peroxide as the oxidizing agent. The reaction takes place at atmospheric pressure and 50 °C in the presence of methyl ethyl ketone (MEK), with a ratio of H2O2:MEK:NH3 of 1:2:4.
To activate the hydrogen peroxide, acetamide and disodium hydrogen phosphate are employed by ATOFINA, while Mitsubishi Gas uses an arsenic compound. The overall reaction leads to the formation of methyl ethyl ketazine with high yield.
The reaction mechanism involves the activation of both ammonia and hydrogen peroxide since these two reactants do not naturally react with each other, unlike ammonia and hypochlorite in the Bayer process. The reaction proceeds through the formation of an oxaziridine intermediate, which is capable of oxidizing ammonia to a hydrazine derivative.
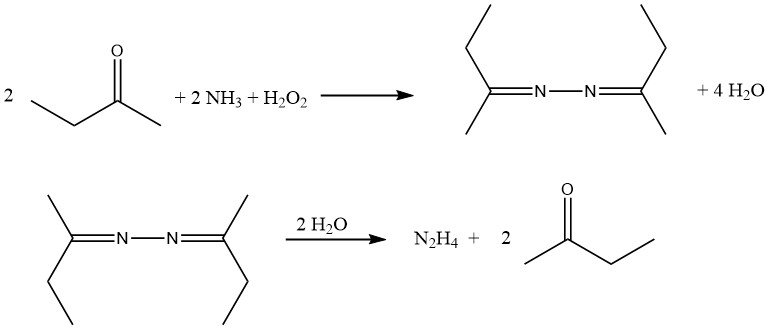
Due to the insolubility of methyl ethyl ketazine in the reaction mixture, it can be easily separated through decantation. The separated ketazine is then purified via distillation. Under pressure (0.8-10 MPa), the purified ketazine is hydrolyzed, resulting in concentrated aqueous hydrazine and overhead methyl ethyl ketone, which is recycled.
The aqueous layer containing the activator is concentrated to remove water and subsequently recycled back to the reactors after eliminating water-soluble impurities through a purge. The peroxide process offers several advantages over other methods, including the absence of salt byproducts, high yields, low energy consumption, minimal molar excess, and no requirement for aqueous effluent treatment.
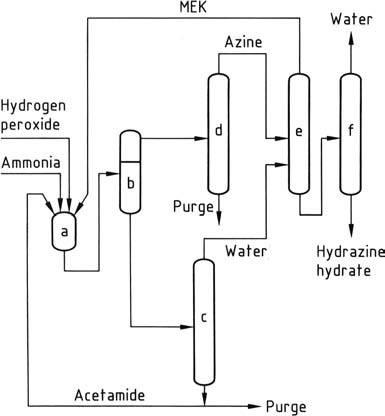
Reference
- Hydrazine; Ullmann’s Encyclopedia of Industrial Chemistry. – https://onlinelibrary.wiley.com/doi/10.1002/14356007.a13_177