
1,4-Butaandiol is een chemische verbinding met de moleculaire formule C4H10O2. Het is een kleurloze en geurloze vloeistof die behoort tot de familie van diolen, verbindingen die twee hydroxyl (OH) groepen bevatten.
Inhoudsopgave
1. Fysische eigenschappen van 1,4-butaandiol
1,4-butaandiol (molaire massa: 90,12 g/mol) is een transparante vloeistof met minimale geur, die hygroscopische eigenschappen vertoont. Het lost gemakkelijk op in water, alcoholen, ketonen, glycolethers en glycoletheracetaten. De oplosbaarheid in di-ethylether en esters is echter lager en het is niet oplosbaar met alifatische en aromatische koolwaterstoffen en gechloreerde koolwaterstoffen.
Eigenschap | Waarde |
---|---|
Smeltpunt | 20,2°C |
Kookpunt | 230,5 °C (bij 101,3 kPa) |
Dichtheid (𝜚) | 1,017 g/cm³ (bij 20 °C) 1,0154 g/cm³ (bij 25 °C) |
Kritische temperatuur | 446 °C |
Kritische druk | 41,2 bar |
Viscositeit (𝜂) | 91,56 mPa s (bij 20 °C) 71,5 mPa s (bij 25 °C) |
Breukindex | 1,4460 (bij 20 °C) 1,4446 (bij 25 °C) |
Diëlektrische constante (𝜀) | 31,4 |
Flits Punt | 134 °C |
2. Chemische reactie van 1,4-butaandiol
1,4-butaandiol ondergaat gemakkelijk cyclisatie wanneer het wordt blootgesteld aan een zuur medium, waarbij tetrahydrofuraan wordt geproduceerd.
Wanneer het wordt onderworpen aan dehydrogenering in de gasfase en met behulp van kopergebaseerde katalysatoren, vormt het 𝛾-butyrolacton.
Bovendien reageert 1,4-butaandiol met monocarbonzuren, waarbij di-esters worden gevormd. Verestering met dicarbonzuren en hun derivaten resulteert in de vorming van gedeeltelijk kristallijne, lineaire, thermoplastische polymere esters.
Rond 200 °C reageert 1,4-butaandiol met ammoniak of een amine met behulp van nikkel- of kobaltkatalysatoren en in aanwezigheid van waterstof, waarbij pyrrolidine of pyrrolidinederivaten worden geproduceerd.
Fosgeen reageert met 1,4-butaandiol bij -5 °C, waarbij het bis(chloorformiaat) van butaandiol wordt geproduceerd.
Bovendien voegt acrylonitril zich bij temperaturen tussen 20 en 100 °C toe aan 1,4-butaandiol, met de aanwezigheid van katalytische hoeveelheden alkali, wat leidt tot 1,4-bis(2-cyanoethoxy)butaan.
Net als andere alcoholen kan 1,4-butaandiol ook vinylering ondergaan, wat resulteert in de vorming van mono- of divinylether.
3. Productie van 1,4-butaandiol
Sinds de jaren negentig zijn verschillende alternatieve technologieën ontwikkeld voor de productie van 1,4-butaandiol. De Reppe-technologie, die afhankelijk is van acetyleen en formaldehyde, blijft de meest voorkomende methode.
Daarnaast gebruiken andere processen benzeen of butaan via maleïnezuuranhydride, propyleen, butadieen en suikers als alternatieve routes voor de productie ervan.
3.1. Productie van 1,4-Butaandiol uit 2-Butyn-1,4-diol
1,4-Butaandiol wordt op grote industriële schaal geproduceerd door continue hydrogenering van 2-butyn-1,4-diol. Dit proces maakt voornamelijk gebruik van gemodificeerde nikkelkatalysatoren. Het tweetrapsstroomproces wordt uitgevoerd binnen het temperatuurbereik van 80-170 °C en bij een druk van 250-300 bar.

Het proces start met een waterige oplossing van 2-butyn-1,4-diol (30-50%), samen met koolmonoxidevrije waterstof en gerecycled reactiemengsel, dat fungeert als een warmteafvoerend medium.
Dit mengsel passeert een gereduceerde nikkel-type vaste-bed katalysator in de loodreactor, waar meer dan 99% van de reactie plaatsvindt.
De begintemperatuur is ongeveer 80 °C en mag niet hoger zijn dan 170 °C om ongewenste ontledingsreacties te voorkomen. Waterstofcirculatie zorgt voor een betere vloeistofverdeling. De tweede of afsluitende reactor voltooit de omzetting van onverzadigde verbindingen.
Verschillende commercieel gebruikte processen verschillen voornamelijk in de gebruikte katalysator. BASF en Invista Technologies beschrijven Ni ondersteund op oxiden van zirkonium of aluminium, terwijl Raney-nikkel, gebruikt als een vaste-bed katalysator, wordt gebruikt en gelicentieerd door Invista.
Een andere variatie betreft lagedrukhydrogenering bij ongeveer 20 bar met behulp van een gesuspendeerde Raney-nikkelkatalysator, gevolgd door hydrogenering bij 120-140∘C en 140-210 bar gekatalyseerd door een vastbedcontact (door Ineos).
Het verkregen ruwe product bevat methanol, propanol en butanol als bijproducten, samen met sporen van 2-methyl-1,4-butaandiol, 4-hydroxybutyraldehyde, 𝛾-butyrolacton, acetalen en triolen.
Om zuivere 1,4-butaandiol te verkrijgen, ondergaat het reactoreffluent fractionele destillatie. Eerst worden water en monoalcoholen zoals methanol, propanol en butanol verwijderd. Vervolgens wordt 1,4-butaandiol gescheiden van hoogkokende verbindingen zoals triolen en zouten, samen met onzuiverheden zoals 𝛾-butyrolacton, acetalen, 2-methyl-1,4-butaandiol en 4-hydroxybutyraldehyde.
Zuivere 1,4-butaandiol kan verder worden geïsoleerd in een extra kolom, die 4-hydroxybutyraldehyde, acetalen en 𝛾-butyrolacton scheidt als lichtkokende verbindingen.
3.2. 1,4-butaandiol op basis van benzeen of butaan via maleïnezuuranhydride
De gasfaseoxidatie van benzeen of n-butaan met zuurstof leidt tot de productie van maleïnezuuranhydride. Dit maleïnezuuranhydride kan worden geadsorbeerd uit het oxidatiegas door water, wat resulteert in maleïnezuur, of door organische hoogkokende verbindingen zoals dibutylftalaat.
De maleïnezuuroplossing in water kan worden gehydrogeneerd in een hogedrukproces om 1,4-butaandiol te verkrijgen, met de aanwezigheid van gedoteerde Re-based actieve koolstofkatalysatoren. De dopanten die in deze katalysatoren worden gebruikt, zijn voornamelijk Pd en Pt.
Het proces genereert echter bijproducten zoals n-butanol, n-propanol, methanol en tetrahydrofuraan. Ondanks de eenvoud is de hydrogeneringskatalysator duur vanwege het hoge gehalte aan edelmetalen.
Bijgevolg is er tot nu toe slechts één commerciële productie van dit proces gerealiseerd, uitgevoerd door Lima in de VS.
Een meer gebruikelijke commerciële aanpak omvat de gasfasehydrogenering van maleïnezuurdiësters, die zijn afgeleid van maleïnezuuranhydride.
Dit proces werd in de jaren 80 ontwikkeld door Kvaerner Process Technology (KPT, Londen, nu Johnson Matthey Davy Technologies (JM Davy)). De eerste stap omvat het produceren van dimethylmaleïnezuur uit maleïnezuuranhydride en methanol, met behulp van een sterk zure ionenuitwisselingshars als katalysator.
Het resulterende dimethylmaleïnezuur wordt vervolgens gehydrogeneerd in de gasfase met behulp van een Cu-bevattend katalysatorsysteem bij een druk van 2-8 MPa en temperaturen van 150-250 °C.
Dit proces levert een mengsel op van 1,4-butaandiol, tetrahydrofuraan, butyrolacton, een kleine hoeveelheid van het intermediaire dimethylsuccinaat en, als het belangrijkste bijproduct, n-butanol.
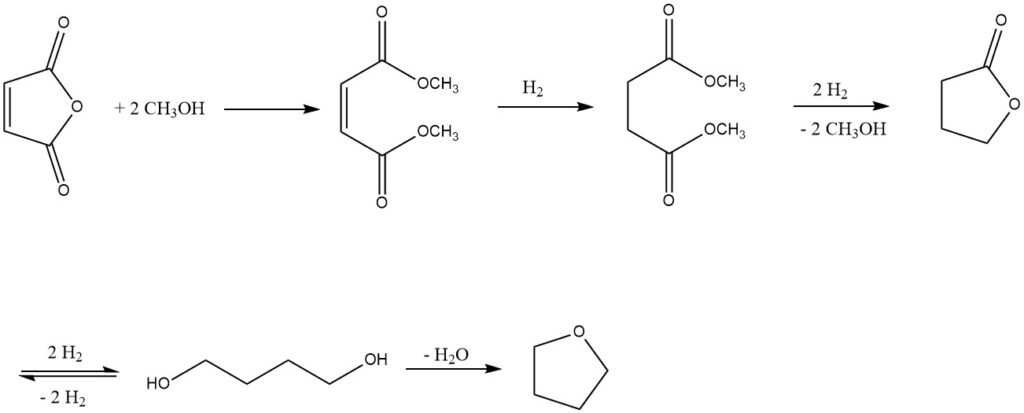
Butyrolacton en dimethylsuccinaat kunnen worden teruggewonnen als een azeotroop en worden gerecycled naar de hydrogeneringsfase om volledige omzetting naar 1,4-butaandiol en tetrahydrofuraan te bereiken.
JM Davy heeft dit proces meerdere keren gelicentieerd om butaandiol/butyrolacton/tetrahydrofuraanfabrieken op te zetten op verschillende locaties in Azië, waaronder Saoedi-Arabië, Maleisië, Korea en China.
3.3. Productie van 1,4-butaandiol uit propyleen
Een alternatieve grondstof voor 1,4-butaandiol is propyleen, dat kan worden verkregen via allylalcohol. Dairen in Taiwan en China, evenals Lyondell in de VS en Nederland, maken gebruik van dit proces.
Om allylalcohol te verkrijgen, wordt propyleen eerst geoxideerd tot propyleenoxide, dat vervolgens wordt geïsomeriseerd (Lyondell) of gehydrolyseerd tot allylalcohol. De hydrolyse omvat acetoxylering van propyleen in de gasfase met zuurstof, wat leidt tot de vorming van allylacetaat, dat vervolgens wordt gehydrolyseerd om allylalcohol (Dairen) te verkrijgen.
De volgende stap omvat hydroformulering van allylalcohol in een oplosmiddel met een homogene rhodium-gebaseerde katalysator, wat 4-hydroxybutyraldehyde oplevert. Een belangrijk bijproduct in deze stap is 3-hydroxy-2-methyl-propionaldehyde.
Na extractie van de aldehyden worden ze onderworpen aan hydrogenering met Raney-nikkel als katalysator, wat resulteert in 1,4-butaandiol, dat vervolgens wordt gezuiverd door destillatie.

Een van de belangrijkste bijproducten in deze reactie is echter 2-methyl-1,3-propaandiol. Daarnaast zijn er tijdens dit proces andere bijproducten gevormd, zoals n-propanol en isobutyraldehyde.
3.4. Productie van 1,4-butaandiol uit butadieen
Mitsubishi gebruikt een proces in drie stappen om 1,4-butaandiol te produceren:
- Butadieen en azijnzuur ondergaan een katalytische reactie om 1,4-diacetoxy-2-buteen te produceren.
- Vervolgens levert hydrogenering van 1,4-diacetoxy-2-buteen 1,4-diacetoxybutaan op.
- Ten slotte leidt hydrolyse van 1,4-diacetoxybutaan tot de vorming van 1,4-butaandiol.
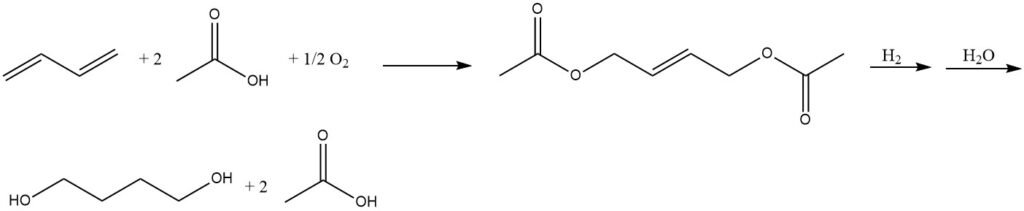
De hydrolyse van het diacetaat kan ook tetrahydrofuraan opleveren vanwege de zeer zure reactieomstandigheden.
BASF heeft een soortgelijk proces gepatenteerd, waarbij azijnzuur eerst wordt toegevoegd aan butadieen en het resulterende product isomeriseert tot 1,4-diacetoxy-2-buteen.
Toyo Soda’s proces omvat de toevoeging van chloor aan butadieen om een mengsel van 1,4-dichloor-2-buteen en 3,4-dichloor-1-buteen te vormen. Dit mengsel reageert met natriumacetaat om 1,4-diacetoxy-2-buteen te produceren, dat vervolgens direct wordt gehydrogeneerd tot 1,4-butaandiol.
In een patent beschreven door Shell reageert butadieen met tert-butylhydroperoxide met behulp van een kobaltkatalysator om 1,4-di(tert-butylperoxy)buteen-2 te vormen, dat vervolgens wordt omgezet in 1,4-butaandiol door hydrogenering. Als bijproduct wordt 1,2-butaandiol gevormd.
Eastman heeft een ander proces dat begint met butadieen als grondstof. Eerst wordt butadieen geoxideerd door zuurstof in aanwezigheid van een zilverkatalysator om 1,2-epoxy-3-buteen te vormen. Het epoxide ondergaat vervolgens een herschikking om 2,5-dihydrofuraan te produceren, dat vervolgens wordt geïsomeriseerd tot 2,3-dihydrofuraan.
Na zuurgekatalyseerde toevoeging van water aan een evenwicht van 2-hydroxytetrahydrofuraan en 4-hydroxybutyraldehyde, gevolgd door hydrogenering, wordt 1,4-butaandiol gegenereerd. Als alternatief kan de omzetting van 2,5-dihydrofuraan naar 1,4-butaandiol worden uitgevoerd als een one-pot synthese.
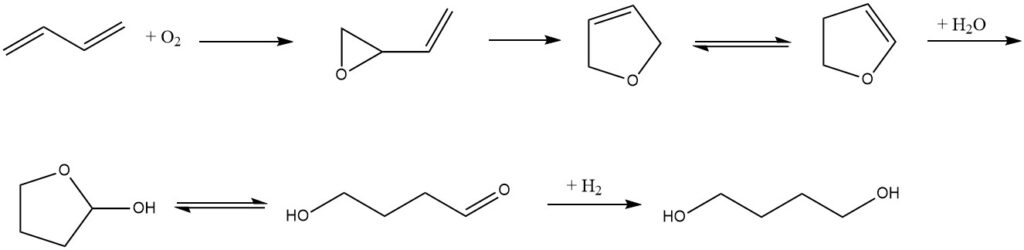
3.5. Productie van 1,4-butaandiol uit biomassa
De afgelopen twee decennia zijn er grote inspanningen geleverd om 1,4-butaandiol en zijn derivaten te produceren uit biomassabronnen.
Een van de eerste benaderingen betrof het gebruik van furfural, dat kan worden gedecarbonyleerd tot furaan.
BASF ontwikkelde een veelbelovende methode waarbij furaan wordt gehydrogeneerd in aanwezigheid van water en een op rhenium gebaseerde katalysator bij verhoogde druk, wat resulteert in de vorming van 1,4-butaandiol. 𝛾-Butyrolacton en n-butanol worden geproduceerd als bijproducten.
Shell werkte ook aan het optimaliseren van het proces met behulp van op rhenium gebaseerde katalysatoren. Met een Re/Pd op koolstofkatalysator behaalde Shell een hoge opbrengst van tetrahydrofuraan en 1,4-butaandiol als belangrijkste producten.
Sommige bedrijven gebruiken fermentatie methoden op basis van suiker om direct 1,4-butaandiol of zijn voorlopers te verkrijgen. Genomatica ontwikkelde een proces om 1,4-butaandiol te produceren door glucose te fermenteren met behulp van genetisch gemodificeerde Escherichia coli bacteriën. Na fermentatie bevat de bouillon 1,4-butaandiol verdund in water, samen met biomassa en zouten.
Een distillatieproces scheidt water en na grondige filtratie en verwijdering van zouten ondergaat de ruwe 1,4-butaandiol hydrogenering om onzuiverheden te verwijderen die de kleurstabiliteit kunnen beïnvloeden.
Verdere zuivering wordt uitgevoerd door extra distillatiestappen. Het Genomatica-proces is sinds 2016 commercieel geïmplementeerd in één fabriek (30 ×103 t capaciteit, Novamont) in Italië.
Een andere aanpak omvat het fermenteren van suikers tot barnsteenzuur, dat dient als een precursor voor de productie van 1,4-butaandiol. Bedrijven als BioAmber, Myriant, Reverdia en Succinity zijn betrokken geweest bij de commercialisering van dit fermentatieproces.
De directe fermentatie van suikers tot barnsteenzuur vereist pH-regeling vanwege de resulterende lage pH van de fermentatiebouillon. Basismaterialen zoals ammoniak of alkali-/aardalkalihydroxiden worden gebruikt voor pH-regeling.
Het resulterende diammoniak-succinaat kan worden behandeld met zwavelzuur om barnsteenzuur vrij te maken. Barnsteenzuur kan vervolgens worden omgezet in 1,4-butaandiol door hydrogenering in de gasfase als een anhydride of diester met behulp van op koper gebaseerde katalysatoren of door hydrogenering in de vloeibare fase met behulp van op edelmetaal gebaseerde katalysatoren.
Suikerfermentatie kan ook leiden tot 𝛾-butyrolacton. Metabolix ontwikkelde een methode om suikers in een fermentatieproces om te zetten in poly(4-hydroxybutyraat) (poly(butyrolacton)), dat kan worden gedepolymeriseerd tot butyrolacton in aanwezigheid van een katalysator bij temperaturen boven 200 °C.
De beste resultaten worden bereikt met calciumhydroxide als katalysator en de resterende biomassa wordt omgezet in vaste brandstof. Er is echter nog geen commerciële fabriek voor dit proces opgezet.
4. Toepassingen van 1,4-butaandiol
1,4-butaandiol speelt een cruciale rol als veelzijdig tussenproduct in de chemische industrie en dient als een voorloper voor 𝛾-butyrolacton en tetrahydrofuraan.
De belangrijkste toepassing ligt in de productie van polyurethanen en polyesters, zoals poly(butyleentereftalaat), dat algemeen bekend staat als PBT. Deze materialen hebben diverse toepassingen in verschillende industrieën.
Polyurethanen afgeleid van 1,4-butaandiol worden gebruikt in de productie van cellulaire en compacte elastomeren, die vanwege hun elasticiteit en veerkracht een breed scala aan toepassingen vinden.
Poly(butyleentereftalaat) wordt uitgebreid verwerkt om plastic materialen en smeltlijmen te maken. Daarnaast wordt het gebruikt in de productie van plastic films en vezels, waardoor het een veelzijdig materiaal is dat wordt gebruikt in verschillende producten en industrieën.
Referenties
- Butanediols, Butenediol, and Butynediol, Ullmann’s Encyclopedia of Industrial Chemistry. – https://onlinelibrary.wiley.com/doi/10.1002/14356007.a04_455.pub2
- Organic Acids: Succinic and Malic Acids. – https://www.sciencedirect.com/science/article/abs/pii/B9780444640468001592
- https://www.industrialchemicals.gov.au/sites/default/files/1-4-Butanediol.pdf