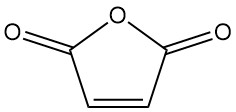
Was ist Maleinsäureanhydrid?
Maleinsäureanhydrid, auch bekannt als 2,5-Furandion, ist eine organische Verbindung mit der Formel C4H2O3. Es ist ein farbloser oder weißer Feststoff mit einem starken, reizenden Geruch, der industriell wichtiger ist als Maleinsäure.
Inhaltsverzeichnis
1. Physikalische Eigenschaften von Maleinsäureanhydrid
Maleinsäureanhydrid bildet orthorhombische Nadelkristalle. Es ist löslich in Wasser, Aceton, Ethanol, Xylol, Ethylacetat, Chloroform, Benzol, Toluol, Tetrachlormethan und vielen anderen organischen Lösungsmitteln.
Maleinsäureanhydrid ist hygroskopisch und entflammbar und kann mit Luft explosive Gemische bilden. Es kann sublimieren. Der pH-Wert von Maleinsäureanhydrid-Wasserlösungen beträgt 2,42 bei 1×10-2 M, 2,62 bei 5×10-3 M und 3,10 bei 1×10-4 M.
Die wichtigsten physikalischen Eigenschaften von Maleinsäureanhydrid sind in der folgenden Tabelle zusammengefasst.
Eigenschaft | Wert |
---|---|
CAS-Nummer | 108-31-6 |
Chemische Formel | C4H2O3 |
Molekularmasse | 98,06 g/mol |
Schmelzpunkt | 52,85 °C |
Siedepunkt (101,3 kPa) | 202,0 °C |
Dichte | 1,48 g/cm3 |
Dampfdichte | 3,40 |
Verbrennungswärme | -1391,2 kJ/mol |
Spezifische Wärmekapazität (Flüssigkeit) | -1,67 kJ mol-1 K-1 |
Verdampfungswärme | 54,8 kJ/mol |
Schmelzwärme | 13,66 kJ/mol |
Flammpunkt | 102 °C (geschlossener Tiegel) 110 °C (offener Tiegel) |
Selbstentzündungstemperatur | 477 °C |
2. Reaktionen von Maleinsäureanhydrid
Maleinsäureanhydrid weist aufgrund der Anwesenheit einer Doppelbindung und seiner Anhydridgruppe eine hohe Reaktivität auf.
Maleinsäureanhydrid hydrolysiert leicht mit Wasser zu Maleinsäure. Diese Reaktion ist exotherm.
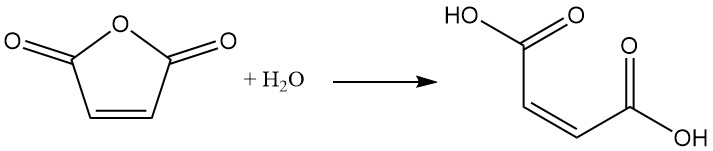
Die Reaktion mit Alkoholen in Gegenwart eines Katalysators führt zur Bildung von Maleinsäureestern. Die Wahl des Katalysators und die Reaktionstemperatur bestimmen das Produkt. Bei niedrigeren Temperaturen bilden sich Halbester, während höhere Temperaturen die Diesterbildung unter Wasserabspaltung begünstigen.

Maleinsäureanhydrid reagiert mit Ammoniak oder Aminen zu den entsprechenden Halbamiden. Durch weitere Dehydratation entstehen zyklische Imide.

An die Doppelbindung des Maleinsäureanhydrids gehen Halogene Additionsreaktionen ein. Je nach Reaktionsbedingungen können mono- oder dihalogenierte Maleinsäureanhydride bzw. dihalogenierte Bernsteinsäureanhydride entstehen.

Bei der Hydrierung von Maleinsäureanhydrid entstehen je nach Reaktionsbedingungen unterschiedliche Produkte. Dazu zählen beispielsweise Bernsteinsäureanhydrid, 1,4-Butandiol, Tetrahydrofuran oder Butyrolacton.

Die Addition von Olefinen führt zur Bildung von Alkenylbernsteinsäureanhydriden.
Maleinsäureanhydrid nimmt an Diels-Alder-Reaktionen mit konjugierten Dienen teil.
Maleinsäureanhydrid kann Homopolymerisations- und Copolymerisationsreaktionen eingehen.
Unter bestimmten Bedingungen kann Maleinsäureanhydrid dimerisieren und Cyclobutantetracarbonsäuredianhydrid (CBTA) bilden, das bei der Herstellung von Polyimiden verwendet wird.
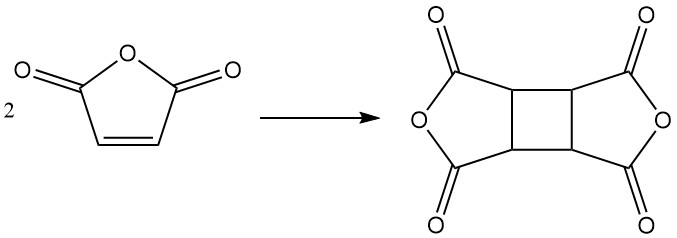
3. Herstellung von Maleinsäureanhydrid
Maleinsäureanhydrid wird durch die katalytische Oxidation geeigneter Kohlenwasserstoffe in der Gasphase hergestellt. Traditionell war Benzol der primäre Rohstoff. In den letzten Jahren haben jedoch C4-Kohlenwasserstoffe (wie Butan) zunehmend an Bedeutung gewonnen.
3.1. Herstellung von Maleinsäureanhydrid durch Oxidation von Benzol
Zur Herstellung von Maleinsäureanhydrid (Abbildung 1) wird Benzol vorgewärmt und mit einem Luftstrom vermischt, um eine homogene Mischung zu bilden. Es werden Rohrreaktoren mit vertikalen Rohren verwendet, die mit einem Katalysator wie Vanadium- und Molybdänoxiden auf einem inerten Träger gefüllt sind.
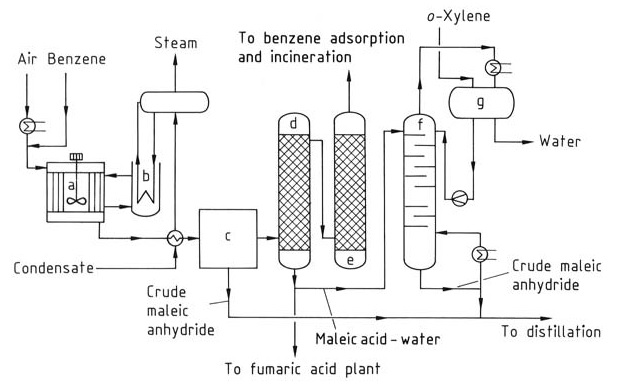
a) Reaktor; b) Salzbadkühler; c) Partialkondensator; d) Säurewäscher; e) Alkaliwäscher; f) Entwässerungskolonne; g) Phasentrenner
Die Reaktion ist exotherm und erfordert eine Kontrolle der Betriebstemperatur und eines Drucks zwischen 0,15 und 0,25 MPa, um die Ausbeute an Maleinsäureanhydrid zu optimieren und die Verbrennung zu CO2 und CO zu minimieren. Die während der Reaktion erzeugte Wärme (etwa 27 MJ pro Tonne Benzol) wird mithilfe von zirkulierenden geschmolzenen Salzen abgeführt, die anschließend mit Wasser gekühlt werden.
Die folgende Reaktion stellt die Produktion von Maleinsäureanhydrid dar:
C6H6 + 4,5 O2 → C4H2O3 + 2 CO2 + 2 H2O (ΔH = -1875 kJ/mol)
Es kommt jedoch auch zu unerwünschter Verbrennung. Nicht umgesetztes Benzol kann mithilfe von Techniken wie Adsorption zurückgewonnen und im Prozess wiederverwendet werden. Obwohl es Patente für Verfahren gibt, bei denen ein größerer Teil des Reaktionsgases nach der Maleinsäureanhydrid-Abtrennung recycelt wird, sind diese Verfahren noch nicht weit verbreitet.
Abtrennung von rohem Maleinsäureanhydrid
Der Reaktorausfluss wird zunächst gekühlt, um die Kondensation von Maleinsäureanhydrid und Wasser zu verhindern. Anschließend können zwei Methoden zur weiteren Verarbeitung verwendet werden:
- Partielle Kondensation: Das Gasgemisch wird auf etwa 55 °C gekühlt, wodurch Maleinsäureanhydrid kondensieren und als Flüssigkeit abgetrennt werden kann. Längerer Kontakt mit dem wasserhaltigen Gas kann jedoch zur Bildung von Maleinsäure führen. Bei diesem Ansatz werden normalerweise 40–60 % des Maleinsäureanhydrids zurückgewonnen.
- Wasserwäsche: Bei dieser Methode wird das gesamte Maleinsäureanhydrid im Reaktionsgas als Maleinsäurelösung aufgefangen. Der anschließende Dehydratisierungsschritt zur Rückgewinnung von Maleinsäureanhydrid ist jedoch energieintensiv und wird nur bei Reaktionsgasen mit hohem Wassergehalt (wie bei denen aus der C4-Oxidation) bevorzugt.
3.2. Herstellung von Maleinsäureanhydrid durch Dehydratisierung wässriger Maleinsäurelösungen
Maleinsäureanhydrid kann aus den durch Waschen des Reaktionsgases mit Wasser erhaltenen Maleinsäurelösungen gewonnen werden.
Bei Temperaturen über 150 °C können selbst Spuren von Alkali in der Waschlösung die Decarboxylierung von Maleinsäureanhydrid verursachen. Daher ist alkalifreies Waschwasser erforderlich.
Die Dehydratisierung von Maleinsäure erfordert Temperaturen über 100 °C (ΔH = +34,88 kJ/mol). Um jedoch eine industriell relevante Reaktionsrate zu erreichen, sind Temperaturen über 130 °C erforderlich. Dieses System mit höheren Temperaturen fördert auch die unerwünschte Isomerisierung von Maleinsäure zu Fumarsäure.
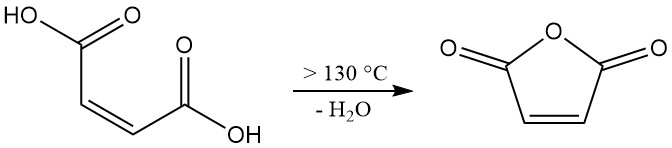
Obwohl Fumarsäure selbst unterhalb von 230 °C nicht nennenswert zu Maleinsäureanhydrid zerfällt, verringert ihre Anwesenheit die Gesamtausbeute des gewünschten Produkts. Um die Isomerisierung zu minimieren, ist während des Dehydratisierungsprozesses eine kurze Verweilzeit bei erhöhten Temperaturen entscheidend.
Zur Dehydratisierung wässriger Maleinsäurelösungen werden zwei Hauptverfahren eingesetzt: das Schleppmittelverfahren und das thermische Verfahren ohne Schleppmittel.
3.2.1. Schleppmittelverfahren
Bei diesem Verfahren wird die wässrige Maleinsäurelösung in den oberen Abschnitt einer Destillationskolonne eingespeist, wo sie sich mit einer siedenden Mischung aus Maleinsäureanhydrid und einem Schleppmittel wie Xylol vermischt.
Das Schleppmittel (Xylol) bildet mit Wasser ein azeotropes Gemisch, sodass beide als Dampfstrom über Kopf aus der Kolonne entfernt werden können. Dieser Dampfstrom wird dann in einem Dekanter in organische und wässrige Phasen getrennt.
Die organische Phase, die das Xylol enthält, wird in den oberen Teil der Destillationskolonne zurückgeführt, während die wässrige Phase in den Reaktionsgaswäscher der Oxidationsanlage zurückgeführt wird.
Der Sumpfproduktstrom der Destillationskolonne, der Maleinsäureanhydrid (10–40 %), Xylol (1–5 %), Maleinsäure (1–3 %) und Fumarsäure (1–3 %) enthält, wird einer weiteren Destillation unterzogen, um reines Maleinsäureanhydrid zu isolieren. Dieser Prozess kann kontinuierlich oder in Chargen durchgeführt werden.
3.2.2. Thermisches Verfahren ohne Schleppmittel
Diese Methode verwendet die Dünnschichtverdampfungstechnologie, um eine thermische Dehydratisierung der wässrigen Maleinsäurelösung zu erreichen. Die Technik ermöglicht eine effiziente Wasserentfernung als Dampf bei gleichzeitiger Minimierung der Verweilzeit der Maleinsäure bei hohen Temperaturen (150–200 °C). Diese kurze Einwirkzeit hilft, die Isomerisierung zu Fumarsäure (nur 1–3 %) zu unterdrücken.
Mehrere Dünnschichtverdampfereinheiten werden oft in Reihe geschaltet. Das aus dem Partialkondensator gewonnene flüssige Maleinsäureanhydrid kann auch der zweiten Stufe dieses Systems zugeführt werden, um die verbleibende Maleinsäure (1–5 %) zu dehydratisieren.
Dieser kontinuierliche Prozess erzeugt nach einem letzten Destillationsschritt hochreines Maleinsäureanhydrid (99 %). Das Sumpfprodukt des letzten Verdampfers enthält Fumarsäure und hochsiedende Rückstände, die verworfen werden.
Diese kontinuierlich betriebenen Anlagen erfordern regelmäßige Abschaltungen zur Reinigung.
3.3. Herstellung von Maleinsäureanhydrid durch Oxidation von C4-Kohlenwasserstoffen
In den letzten Jahren hat sich die Oxidation von C4-Kohlenwasserstoffen, hauptsächlich unter Verwendung von paraffinreichen n-Butan- oder n-Butan-n-Buten-Gemischen, als bedeutende Alternative zur traditionellen Benzoloxidation für die Herstellung von Maleinsäureanhydrid herausgestellt.

Es wurden verschiedene Arten von Verfahren entwickelt, wie Festbett-, Fließbett- und Transportbettverfahren.
3.3.1. Festbettverfahren
Das Festbettverfahren ist eine kommerziell etablierte Methode, bei der Vanadium-Phosphoroxid-Katalysatoren (V-P-O) in Rohrreaktoren gepackt werden, ähnlich der Benzoloxidation. Die Reaktion ist stark exotherm.
C4H10 + 3,5 O2 → C4H2O3 + 4 H2O (ΔH = -1260 kJ/mol)
Im Vergleich zur Benzoloxidation werden jedoch niedrigere Umwandlungsraten von 80 % und Selektivitäten (70 %) beobachtet. Die Rückgewinnung nicht umgesetzter C4-Kohlenwasserstoffe ist schwieriger als bei Benzol.
3.3.2. Wirbelschichtverfahren
Das Wirbelschichtverfahren bietet eine gleichmäßigere Temperaturkontrolle im Reaktor, minimiert „Hot Spots“ und verbessert potenziell die Reaktionsselektivität. Allerdings ist mit dem Wirbelschichtverfahren auch eine intensive Produktummischung verbunden, die den Vorteil zunichte machen kann.
Eine weitere Herausforderung ist die mechanische Belastung des V-P-O-Katalysators durch Abrieb und Erosion. Trotz dieser Nachteile können Wirbelschichten aufgrund ihrer Wirksamkeit als Flammenbarrieren bei höheren C4-Konzentrationen (innerhalb des Explosionsbereichs) betrieben werden.
Das ALMA-Verfahren (Alusuisse, Lummus) ist ein Beispiel für einen Wirbelschichtreaktor, der mit einer nicht-wässrigen Verarbeitungseinheit gekoppelt ist.
3.3.3. Transportbettverfahren
Dieses Verfahren wurde von Monsanto und DuPont entwickelt und verwendet zwei Reaktoren. Der bei der C4-Oxidation verbrauchte V-P-O-Katalysator wird im ersten Reaktor mit Sauerstoff regeneriert. Der regenerierte Katalysator reagiert dann im zweiten Reaktor unter nahezu stöchiometrischen Bedingungen mit minimalem Sauerstoff in der Atmosphäre mit n-Butan.
Mit diesem Verfahren wird eine hohe Selektivität bei der Bildung von Maleinsäureanhydrid (75 Mol-%) erreicht, während die Neuvermischung des Produktgases minimiert wird. Es befindet sich jedoch noch in der Entwicklung.
Aufgrund der im Vergleich zur Benzoloxidation erhöhten Wasserbildung ist die direkte Verflüssigung von Maleinsäureanhydrid aus C4-Reaktionsgas durch partielle Kondensation begrenzt. Ein größerer Anteil (65-70 %) muss durch Wasserwäsche und anschließende Dehydratisierung als Maleinsäure zurückgewonnen werden.
Eine alternative Reinigungsmethode verwendet die Absorption von Maleinsäureanhydrid aus dem Reaktionsgas durch organische Lösungsmittel, wodurch eine Trennung ohne nennenswerte Maleinsäurebildung möglich ist. Das Lösungsmittel-Maleinsäureanhydrid-Gemisch wird dann einer fraktionierten Destillation unterzogen, um reines Maleinsäureanhydrid zu isolieren.
3.4. Reinigung von rohem Maleinsäureanhydrid
Es gibt zwei Hauptmethoden zur Reinigung von rohem Maleinsäureanhydrid: diskontinuierliche Destillation und kontinuierliche Destillation.
3.4.1. Batchweise Destillation
Die batchweise Destillation wird zur Verarbeitung von direkt abgetrenntem Maleinsäureanhydrid oder Gemischen verwendet, die durch Schleppmitteldehydratation erhalten wurden. Das rohe Maleinsäureanhydrid wird in eine Batch-Destillationskolonne gegeben und zunächst unter Rückflussbedingungen erhitzt. Dadurch wird eine vollständige Dehydratation aller verbleibenden Maleinsäure erreicht.
Die geringe Menge Wasser, die während der Dehydratation abgespalten wird, kondensiert und wird vom rezirkulierenden Schleppmittel (normalerweise Xylol) getrennt. Das Xylol wird dann durch Destillation entfernt. Schließlich wird das gereinigte Maleinsäureanhydrid durch Destillation unter Vakuum gewonnen.
Batch-Destillierapparate mit Kapazitäten von 50 bis 150 Kubikmetern und Destillationskolonnen mit 10–20 Böden werden üblicherweise für diesen Prozess verwendet.
3.4.2. Kontinuierliche Destillation
Die kontinuierliche Destillation ist für großtechnische Maleinsäureanhydrid-Produktionsanlagen wirtschaftlicher.
Bei diesem Verfahren (Abbildung 2) wird ein kontinuierlicher Strom der rohen Maleinsäureanhydridmischung dem Destillationssystem zugeführt. Restliches Xylol wird zunächst in einer speziellen Kolonne (f) entfernt. Schließlich wird reines Maleinsäureanhydrid durch Destillation vom Kopf einer zweiten Kolonne (g) isoliert.

a) Kondensator; b) Trennbehälter; c) Kolonne; d) Nachentwässerung; e) Zwischenbehälter; f) o-Xylol-Kolonne; g) Säule für reines Maleinsäureanhydrid; h) Kühler; i) Kolorimeter; j) Behälter für reines Maleinsäureanhydrid
4. Verwendung von Maleinsäureanhydrid
Die einzigartigen Eigenschaften von Maleinsäureanhydrid als Dicarbonsäureanhydrid mit einer Doppelbindung machen es zu einem vielseitigen Baustein für verschiedene industrielle Anwendungen.
Maleinsäureanhydrid wird hauptsächlich zur Herstellung von Polyestern und Alkydharzen verwendet, die bei der Herstellung von glasfaserverstärkten Kunststoffen für Bauwesen, elektrische Anwendungen, Rohrleitungen und Schiffsbau verwendet werden. Es wird auch bei der Formulierung von Schmiermitteln und Weichmachern verwendet.
Maleinsäureanhydrid nimmt leicht an Copolymerisationsreaktionen teil. Einige industriell wichtige Beispiele sind Maleinsäureanhydrid-Styrol-Copolymere, die für technische Kunststoffe verwendet werden, und Maleinsäureanhydrid-Acrylsäure-Copolymere, die in der Waschmittelindustrie verwendet werden.
Maleinsäureanhydrid geht mit Dienen wie Butadien Diels-Alder-Reaktionen ein und bildet Tetrahydrophthalsäureanhydrid (1). Weitere Hydrierung ergibt Hexahydrophthalsäureanhydrid (2), das ein wertvolles Härtungsmittel für Epoxidharze ist. Ein ähnliches Verfahren unter Verwendung von Isopren ergibt Methylhexahydrophthalsäureanhydrid für die gleiche Anwendung.
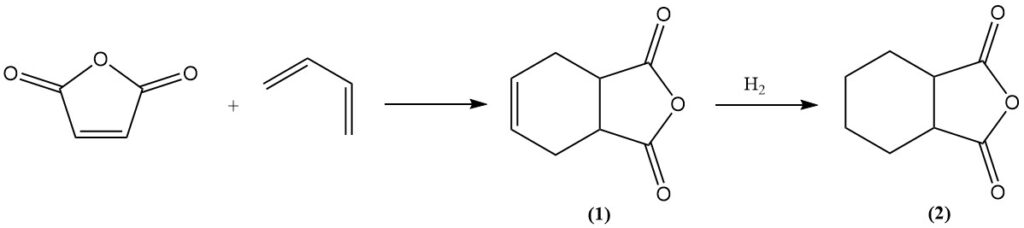
Kleinere Mengen Maleinsäureanhydrid werden bei der Herstellung von Pestiziden wie Captan und Malathion sowie Wachstumshemmern wie Maleinsäurehydrazid verwendet.
Maleinsäureester können durch Reaktionen mit Natriumhydrogensulfit in Tenside umgewandelt werden.
Maleinsäureanhydrid kann als Trocknungsbeschleuniger verwendet werden, wenn es zu trocknenden Ölen hinzugefügt wird, wodurch die Qualität von Lacken verbessert wird.
5. Toxikologie von Maleinsäureanhydrid
Maleinsäureanhydrid kann in Wasser zu Maleinsäure hydrolysieren, daher werden seine toxikologischen Eigenschaften durch die Anwesenheit von Maleinsäure beeinflusst.
Maleinsäureanhydrid zeigt eine mäßige akute Toxizität basierend auf LD50-Werten (481 mg (Ratte, oral), 465 mg (Mäuse, oral), 2620 mg (Kaninchen, perkutan) und 390 mg (Meerschweinchen, oral) pro Kilogramm Körpergewicht).
Die primäre akute toxische Wirkung ist die lokale Reizung und Ätzwirkung auf Haut, Schleimhäute und Augen. Bereits bei Konzentrationen von 1,5–2 ppm kann es zu Reizungen kommen, bei über 2,5 ppm treten starke Reizungen auf.
Das Einatmen von Maleinsäureanhydrid in Konzentrationen über 1,2 ppm über einen längeren Zeitraum kann asthmatische Symptome auslösen.
Maleinsäureanhydrid ist ein starker Sensibilisator, d. h. wiederholter Kontakt kann bei Menschen und Tieren zu allergischen Reaktionen führen.
Tierstudien haben keine Hinweise auf karzinogene, teratogene (Geburtsfehler) oder reproduktionstoxische Wirkungen durch den Kontakt mit Maleinsäureanhydrid ergeben. Allerdings wurden nur bis zu einem Expositionsniveau von 2,4 ppm keine systemischen Effekte beobachtet, sodass Effekte bei höheren Konzentrationen nicht völlig ausgeschlossen werden können.
Aufgrund der reizenden und sensibilisierenden Eigenschaften wurden Arbeitsplatzgrenzwerte festgelegt:
- MAK (Deutsche Kommission zur Prüfung gesundheitlicher Gefahren von Arbeitsstoffen): 0,2 ppm
- TLV-TWA (American Conference of Governmental Industrial Hygienists Threshold Limit Value—Time-Weighted Average): 0,25 ppm
Referenzen
- Maleic and Fumaric Acids; Ullmann’s Encyclopedia of Industrial Chemistry. – https://onlinelibrary.wiley.com/doi/10.1002/14356007.a16_053
- https://pubchem.ncbi.nlm.nih.gov/compound/Maleic-Anhydride
- Method for producing cyclobutane tetracarboxylic acid derivative. – https://patents.google.com/patent/WO2015108168A1/en