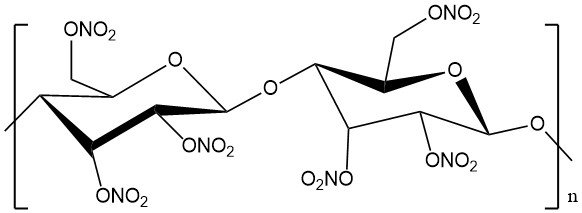
Cellulosenitrat, auch bekannt als Nitrozellulose, Flash-Papier, Schießbaumwolle oder Zelluloid, ist ein chemisches Produkt, das aus dem natürlichen Polymer Zellulose gewonnen wird. Es ist eine weiße, geruch- und geschmacklose Substanz. Seine Eigenschaften hängen vom Grad der Substitution ab.
Inhaltsverzeichnis
1. Physikalische Eigenschaften von Cellulosenitrat
Die Dichte hängt stark vom Nitrierungsgrad ab; sie nimmt mit zunehmendem Substitutionsgrad zu. Im Handel erhältliche, angefeuchtete Cellulosenitrat-Baumwolltypen weisen Schüttdichten im Bereich von 0,25–0,60 kg/L auf, die auf 0,15–0,40 kg/L (Trockenmasse) sinken.
Cellulosenitrat-Chips mit mindestens 18 % Dibutylphthalat erreichen eine Dichte von 1,45 g/cm³, bei einer Schüttdichte von 0,3-0,65 kg/L.
Die Feinheit hat einen erheblichen Einfluss auf die spezifische Oberfläche. Das Rossin-Gerät liefert genaue Messungen und zeigt Werte zwischen 1850 und 4700 cm²/g an. Die mit der BET-Methode bestimmte innere Oberfläche weist eine Abhängigkeit von der Molmasse auf. Allerdings erhöht die Senkung der Entgasungstemperatur aufgrund der Entflammbarkeit von Cellulosenitrat die Unsicherheit über die vollständige Desorption.
Thermodynamische Eigenschaften: Tabelle 1 fasst die wichtigsten Werte zusammen.
Eigenschaft | Wert |
---|---|
Verbrennungswärme | 12 kJ/g |
Schmelzwärme | 15 J/g |
Spezifische Wärmekapazität | 1,5 J/(g·K) |
Wärmeleitfähigkeit | 0,2 W/(m·K) |
Glasübergangstemperatur | 50-60 °C |
Zersetzungstemperatur | 180 °C |
Elektrische Eigenschaften: Gemessen auf Zelluloid (30 Gew.-% Kampfer in Zellulosenitrat), sind unten aufgeführt:
Dielektrizitätskonstante:
- bei 50–60 Hz: 7,0–7,5
- bei 10⁶ Hz: 6,0–6,5
Verlustfaktor (tan δ):
- bei 50–60 Hz: 0,09–0,12
- bei 10⁶ Hz: 0,06–0,09
Spezifischer Widerstand: 10¹¹–10¹² Ω⋅cm
Die Spannungs-Dehnungs-Kurve zeigt die Abhängigkeit von Dehnung und Zugfestigkeit von der Molekülgröße (ausgedrückt als Viskosität). Eine höhere Molekularmasse führt zu elastischeren Filmen mit erhöhter Zugfestigkeit.
Optische Eigenschaften: Die kristalline Struktur macht Cellulosenitratfilme optisch anisotrop. Farben im polarisierten Licht verschieben sich mit Stickstoffgehalt:
- 11,4 % N: schwach rot
- 11,5-11,8 % N: gelb
- 12,0-12,6 % N: blau bis grün
Der Brechungsindex beträgt 1,51, die maximale Lichtdurchlässigkeit liegt bei 313 nm.
Lichtstabilität: Sonnenlicht, insbesondere ultraviolette Strahlung, verfärbt und versprödet Cellulosenitratfilme. Lösungsmittel, Weichmacher und Harze können das Ausmaß der Vergilbung beeinflussen.
2. Chemische Eigenschaften von Cellulosenitrat
Cellulosenitrat wird durch teilweise oder vollständige Nitrierung hergestellt der drei Hydroxylgruppen der Cellulose und weist je nach Nitrierungsgrad einen unterschiedlichen Stickstoffgehalt auf.
- Cellulosemononitrat: 6,75 % N
- Cellulosedinitrat: 11,11 % N
- Cellulosetrinitrat: 14,14 % N
Nitrozellulose mit 10,8–12,6 % N ist aufgrund ihrer Löslichkeit in organischen Lösungsmitteln für Lacke geeignet, ab 12,3 % N wird sie vor allem in Sprengstoffen eingesetzt.
Der Stickstoffgehalt steht in direktem Zusammenhang mit dem Substitutionsgrad und bestimmt die Löslichkeit in organischen Lösungsmitteln.
- Alkohollösliche Nitrozellulose (A-Typen): ~10,9–11,3 % N (gut löslich in Alkoholen, Estern und Ketonen)
- Mäßig lösliche Nitrozellulose (AM-Typen): ~11,4–11,7 % N (löslich in Estern, Ketonen, Glykolethern und ausgezeichnete Löslichkeit mit Alkoholen)
- In Estern lösliches Cellulosenitrat (E-Typen): 11,8–12,2 % für Lackbaumwolle, bis zu 13,7 % für Schießbaumwolle (leicht löslich in Estern, Ketonen und Glykol). Ether).
Die Grenzviskosität spiegelt die durchschnittliche Moleküllänge (Polymerisationsgrad) wider und kann über die Staudinger-Mark-Houwink-Gleichung mathematisch mit der Molekülmasse verknüpft werden.
Polymolekulare Daten, einschließlich Polymerisationsgrad und Molekularmassenverteilung, Komplementviskosität und Löslichkeit, sind wichtig für das Verständnis mechanischer Eigenschaften und Alterungsprozesse. Die Gelpermeationschromatographie isoliert Polymere effizient anhand ihrer Molekularmasse.
Cellulosenitrat ist sehr gut verträglich mit zahlreichen Stoffen, die in Nitrolacken vorkommen, wie Alkydharze, Maleinharze, Ketonharze, Harnstoffharze, Polyacrylate und verschiedene Weichmacher.
Starke Säuren, Basen und organische Amine können Cellulosenitrat schnell abbauen oder zersetzen, was möglicherweise zu einer Verpuffung führt. Die Esterbindungen tragen zu seiner inhärenten Instabilität bei, die von der Temperatur, der Probenform und dem Vorhandensein oder Fehlen von Zersetzungsprodukten beeinflusst wird.
Gemischte Schwefelsäureester, die während der Produktion eingebracht werden, führen zu weiterer Instabilität und erfordern einen Stabilisierungsschritt mit schwach saurem Wasser.
Über 100 °C unterliegt Cellulosenitrat einer thermischen Zersetzung durch eine Reihe exothermer Oxidationsreaktionen, die durch NO2-Radikale ausgelöst werden, was möglicherweise zu einer spontanen Verpuffung führt.
Stabilisatoren wie Diphenylamin oder schwache Säuren können intermediäre Stickoxide binden und diese autokatalytische Kettenreaktion verhindern. Die Deflagrationstemperatur, beeinflusst durch den Stabilisierungs- und Plastifizierungsgrad, dient als Schlüsselmaß für die thermische Stabilität.
Der Bergmann-Junk-Test und der Warmlagerungstest bieten zusätzliche Methoden zur Bewertung der Stabilität von Cellulosenitrat.
3. Nitrozellulose-Rohstoffe
Die bei der Herstellung von Cellulosenitrat verwendeten Rohstoffe sind Cellulose und Nitrierungsmittel.
3.1. Zellulose
Vor dem Ersten Weltkrieg wurden aufgrund ihrer überlegenen Ausbeute und Klarheit nur hochreine Baumwoll-Linters (gebleichte Flocken oder Krepp) zur Nitrierung verwendet.
Die Knappheit an Linters führte zu Experimenten mit anderen Quellen wie Holzzellulose, sogar ungebleicht, und einjährigen Pflanzenfasern. Allerdings führten diese zu minderwertigen Lacken mit Mattheit und schlechten mechanischen Eigenschaften aufgrund des hohen Pentosangehalts.
Die Fortschritte bei der Reinigung von Zellstoff in chemischer Qualität mit heißen oder kalten Alkalibehandlungen (R18-Werte > 92 %) ermöglichten jedoch seine Verwendung zur Nitrierung ähnlich wie bei Linters. Hochraffinierte vorhydrolysierte Sulfatzellstoffe (R18 > 96 %) sind besonders geeignet und ermöglichen eine Viskositätskontrolle durch die anfängliche Wahl der Cellulose.
Ein niedriger Asche- und Kalziumgehalt in der Zellulose ist wichtig, um die Ausfällung von Kalziumsulfat während der industriellen Nitrierung zu verhindern.
Studien zeigen, dass die morphologischen und chemischen Eigenschaften von Cellulose zusammen mit dem Vorhandensein von Hemicellulose und Lignin die Nitrierungsfähigkeit und die Endprodukteigenschaften beeinflussen. Linters weisen im Vergleich zu Zellstoff (bis zu 300 %) ein besseres Säurerückhaltevermögen (110–130 %) auf, was sich auf die Beibehaltung der Fasermasse während der Verarbeitung auswirkt.
Eine spezielle Maschine misst die Kompression und Entspannung des Faserstapels, um festzustellen, ob ein Rohmaterial für die Nitrierung geeignet ist.
Ungefähr 3,4 % (150.000 Tonnen) der weltweiten Chemiezellstoffproduktion werden für die Herstellung von Cellulosenitrat verwendet.
3.2. Nitrierungsmittel
Das Salpetersäure/Schwefelsäure/Wasser-System von Schönbein bleibt das bevorzugte industrielle Nitrierungsmittel. Der maximal erreichbare Substitutionsgrad (DS 2,7, 13,4 % N) erfordert wasserfreie Salpetersäure und ein Molverhältnis von 1:2 von HNO3 zu H2SO4 Monohydrat.
Die optimale Nitriermischung enthält 21,36 % HNO3, 66,44 % H2SO4 und 12,20 % H2O.
Der Wassergehalt beeinflusst die erreichbare Nitrierung erheblich und führt zu einem Ertragsrückgang von über 12 %. Die gewünschten Veresterungsgrade werden durch Variation der Nitriersäuremischung eingestellt (Tabelle 2), wobei industrielle Prozesse HNO3 bei 25–26 % halten.
Nitrozellulose-Typ | % HNO3 | % H2SO4 | % H2O | N Inhalt, % | DS |
---|---|---|---|---|---|
Lack Baumwolle A | 25 | 55,7 | 19.3 | 10,75 | 1,90 |
Zelluloid-Baumwolle | 25 | 55,8 | 19.2 | 10,90 | 1,95 |
Lackbaumwolle AM | 25 | 56,6 | 18.4 | 11.30 | 2,05 |
Dynamit-Baumwolle | 25 | 59,0 | 16,0 | 12.10 | 2,30 |
Lack Baumwolle E | 25 | 59,5 | 15,5 | 12.30 | 2,35 |
Puderbaumwolle | 25 | 59,8 | 15.2 | 12,60 | 2,45 |
Waffenbaumwolle | 25 | 66,5 | 8,5 | 13.40 | 2,70 |
Das ternäre System HNO3/H2SO4/H2O wurde mit der Phase ausführlich untersucht Diagramm, das drei verschiedene Zonen zeigt:
- Technische Nitrierzone: Geeignet für Nitrierung (10–100 % Salpetersäure, 0–80 % Schwefelsäure, 0–20 % Wasser).
- Lösungsbereich: Keine nennenswerte Nitrierung; Es kommt zum Zelluloseabbau (0–10 % Salpetersäure, 60–100 % Schwefelsäure, 0–40 % Wasser).
- Quellzone: Erhöhter Wassergehalt führt zu verringerter Nitrierung (Salpetersäuregehalt variiert, Schwefelsäure 60–100 %, Wasser nimmt zu).
Bei einem weniger verbreiteten Verfahren wird Magnesiumnitrat anstelle von Schwefelsäure als Dehydratisierungsmittel verwendet, was Potenzial für eine kontinuierliche Verarbeitung und Abfallreduzierung bietet.
4. Herstellung von Cellulosenitrat
Cellulosenitrat wird durch Behandlung von Cellulose, meist Baumwoll-Linters, mit einer Mischung aus konzentrierter Salpeter- und Schwefelsäure hergestellt. Der Nitrierungsgrad wird durch Anpassung der Temperatur, der Säurekonzentration und der Reaktionszeit gesteuert.

Das Flussdiagramm (Abbildung 1) zeigt die industrielle Herstellung von Nitrocellulose nach dem Mischsäureverfahren. Die Viskosität des Endprodukts wird durch die Wahl der Ausgangszellulose und der Nitrierungsgrad durch die Zusammensetzung der Mischsäure bestimmt. Die endgültige Viskosität wird während des Druckkochschritts eingestellt.
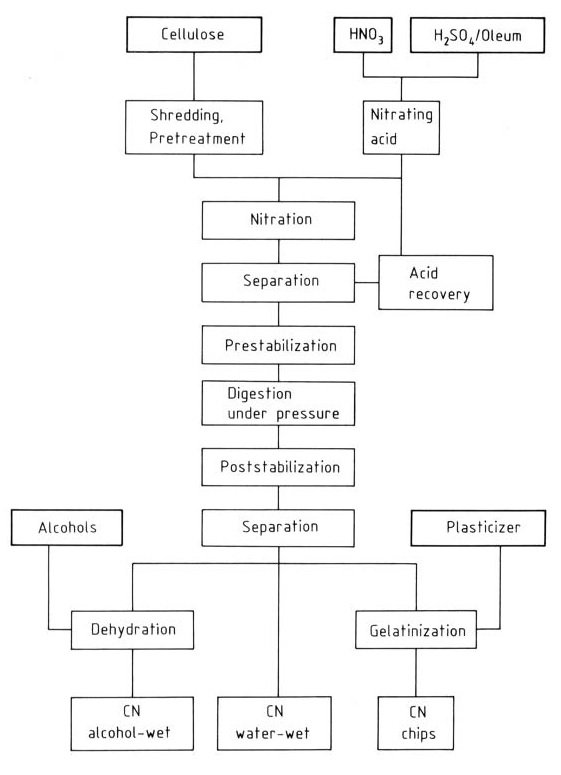
4.1. Cellulosepräparation
Die Verarbeitung von Zellulose spielt eine wichtige Rolle für eine schnelle und gleichmäßige Nitrierung. Traditionell wurden Baumwoll-Linters mit niedrigem Feuchtigkeitsgehalt (<7 %) mechanisch desintegriert, um eine homogene Fasermasse zu erhalten. Dieser Prozess war jedoch mühsam und von begrenztem Umfang.
Gepresste Zellstoffblätter boten eine Alternative, mussten jedoch in kleine Stücke zerkleinert werden, um eine effiziente Nitrierung zu ermöglichen. Früher wurde für diesen Zweck mit 20 % Natriumhydroxid vorbehandelte Fichten- oder Buchenzellulose (Merzerisierung) verwendet, häufig in der Form von leichtem Krepppapier (25 g/m³).
Um die kostspielige Umwandlung von Papierbögen zu vermeiden, wurden Versuche unternommen, Zellstoffe direkt in lose, linterartige Fasern aufzulösen. Ein Feuchtigkeitsgehalt von 50 % erwies sich als optimal für die Nitrierung und das anschließende Auswaschen mit Säure, erforderte jedoch eine Trocknung vor der Nitrierung, was einen weiteren Verarbeitungsschritt bedeutete.
Der Stern-Zerkleinerer stellte einen bedeutenden Fortschritt dar, da er Zellstoffblätter riss statt schnitt, wodurch die Faserkompression minimiert und die Nitrierungsgleichmäßigkeit verbessert wurde.
Moderne Cellulose zur Nitrierung wird hauptsächlich in Form von Flusen, Schnitzeln oder Chips verwendet. Die Packungsdichte und das Kompressionsverhalten dieser Formen beeinflussen maßgeblich die Quell- und Nitrierungskinetik sowie das Säurerückhaltevermögen. Die Optimierung dieser Faktoren ist entscheidend für effiziente und kontrollierte Nitrierungsprozesse.
4.2 Nitrierung von Cellulose
Das vorherrschende industrielle Verfahren zur Cellulosenitrierung ist immer noch ein 1922 von DuPont entwickeltes Batch-System. Die Ausrüstung besteht aus Edelstahl. Die vorgewärmte Nitriersäure wird in den zellulosehaltigen Rührreaktor gegeben.
Ein großer Säureüberschuss (1:20 bis 1:50) sorgt für Rührbarkeit und Wärmeabfuhr. Die Nitrierungstemperatur liegt zwischen 10 °C (Dynamit) und 36 °C (Zelluloid).
Nach 5 Minuten ist die Reaktion abgeschlossen und die Mischung verbleibt aufgrund der Temperaturempfindlichkeit 30 Minuten im Reaktor. Oberhalb von 40 °C beginnt der hydrolytische Abbau mit erheblichen Ertragseinbußen.
Theoretische Ausbeuten für gängige Nitrozellulosetypen (TS 1,8–2,7, N-Gehalt 10,4–13,4 %) erreichen 150–176 %, bezogen auf Zellulose, die praktischen Ausbeuten liegen jedoch aufgrund der Zelluloseart und -reinheit, Temperatur und Dauer um 15 % niedriger.
Verluste entstehen durch den vollständigen Zelluloseabbau zu Oxalsäure durch Oxidation von Oligosacchariden und Monosacchariden mit Salpetersäure. Auch mechanische Verluste bei der anschließenden Trennung (insbesondere kurze Hartholzfasern) tragen dazu bei.
Die Reaktionsmischung wird bei hoher Geschwindigkeit zentrifugiert, um überschüssige Säure abzutrennen und wiederzuverwerten. Durch die Aufrechterhaltung der Feuchtigkeit wird eine Entzündung oder Verpuffung verhindert.
Aus wirtschaftlichen Gründen ist die Säureretention durch das Produkt wichtig. Linters (100–130 % Retention) übertreffen Holzzellulose deutlich (bis zu einem 3-fach höheren Verhältnis von Zellulosenitrat zu Säure), je nach Holz- oder Zelluloseart und Verarbeitung.
Das säurefeuchte Produkt wird sofort mit überschüssigem Wasser (Konsistenz 1 %) verdünnt, um anhaftende Säure schnell zu verdrängen und die Verseifung von Cellulosenitrat zu verhindern.
Kontinuierliche Nitrierungsverfahren wurden in den 1960er Jahren entwickelt und bieten wirtschaftliche Vorteile, eine gleichmäßige Produktqualität und eine verbesserte Sicherheit. Das System verwendet zwei oder mehr kaskadenverbundene gerade Tanks oder Rohre, die mit Förderern (Schnecken- oder Turbulenzmischer) ausgestattet sind, um die Reaktionsmischung voranzutreiben.
In diesem Kaskadensystem vermischt sich aufbereitete Zellulose kontinuierlich mit zugesetzter Nitriersäure. Wichtig ist, dass die Zellulose zügig zugegeben und sofort mit Säure bedeckt wird. Die Verweilzeit beträgt 30–55 Minuten, ein neuerer Druckreaktor in Schlaufenform benötigt jedoch nur 6–12 Minuten.
Der Reaktant gelangt dann in eine kontinuierliche Zentrifuge, um gleichzeitig überschüssige Säure abzutrennen und Wasser zu verdünnen. Die kurze Verweilzeit (nur wenige Sekunden) minimiert die Gefahr einer Verpuffung und Verseifung.
Abbildung 2 zeigt das Schema des kontinuierlichen Hercules-Prozesses.
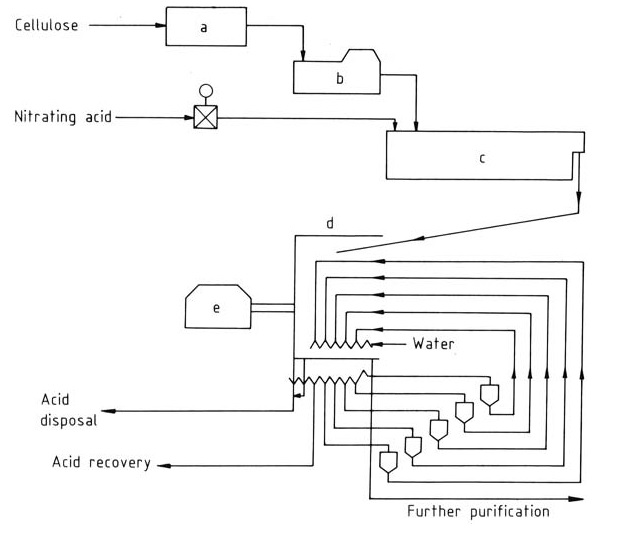
a) Vorkonditionierung; b) Automatische Waage; c) Reaktor; d) Waschzone; e) Zentrifuge
Vorkonditionierte Cellulose gelangt über automatische Waagen in den kontinuierlichen Reaktor, anschließend wird das Reaktionsprodukt zentrifugiert und in Wasserzonen im Gegenstrom gewaschen. Das nahezu säurefreie Produkt verlässt die Zentrifuge, während die gewaschene Säure mit minimalem Verlust recycelt werden kann.
4.3. Stabilisierung und Viskositätsanpassung von Cellulosenitrat
Nach dem Vorwaschen wird das Cellulosenitrat durch wiederholtes Waschen und Kochen mit Wasser, das 0,5–1 % Säurerückstände enthält, weiter gereinigt. Dieses Batch-Verfahren erfordert viel Platz, Wasser und Energie, wobei die Kochzeiten zwischen 6 Stunden für Zelluloid und 40 Stunden für Schießbaumwolle variieren. Es wurden auch automatisierte kontinuierliche Prozesse entwickelt.
Durch die Vorstabilisierung wird der größte Teil der verbleibenden Schwefelsäure entfernt, die die Zersetzung von Cellulosenitrat katalysiert. Die Säure bindet durch Adsorption und Veresterung. Schwach nitriertes Cellulosenitrat behält 1–3 % Gesamtsulfat, davon 70–85 % als saure Halbester.
Hoch nitriertes Cellulosenitrat enthält nur 0,2–0,5 % Sulfat, wovon 15–40 % Ester sein können. Halbester werden leicht verseift und durch kochendes Wasser ausgewaschen. Die Existenz von „resistentem“ Sulfat als neutraler Ester oder adsorbierte Säure bleibt unklar.
Druckkochen (Aufschluss) bei 6–8 % Konsistenz und 130–150 °C stellt die endgültige Cellulosenitratviskosität durch kontrollierten Polymerabbau ein. Die verbleibende Spur Schwefelsäure fördert die Hydrolyse bei dieser Temperatur und diesem Druck. Beispielsweise kann eine 3-stündige Behandlung bei 132 °C die Viskosität auf 1/10 ihres ursprünglichen Wertes reduzieren.
Dieses Verfahren ermöglichte die Entwicklung von High-Solid-Beschichtungen und schützenden Nitrolacken. Die Stabilisierung von Schießbaumwolle profitiert vom Druckkochen, während Dynamitwolle dies normalerweise umgeht.
Der Kettenabbau führt zu weiteren Produktverlusten in Form löslicher Fragmente und Oxalsäure. Nitrose Gase (NOx) aus der Salpetersäurereduktion werden kontinuierlich entfernt, um die Zersetzung von Cellulosenitrat zu verhindern.
Druckkochen kann diskontinuierlich in Autoklaven oder kontinuierlich in Rohrreaktoren (z. B. 1500 m lang, 100 mm Durchmesser) unter Verwendung von Direktdampf durchgeführt werden. Es gibt einen Eintopfprozess, der Vorstabilisierung, Druckkochen und Nachstabilisierung in einem einzigen Arbeitsgang kombiniert.
Zusätzliches Waschen und Kochen entfernt nahezu die restliche Schwefelsäure. Zelluloid und Lackzellulosenitrat werden in flockiger oder faseriger Form veredelt, während Schießbaumwolle gemahlen werden muss. Dies geschieht in Hollander-Motoren bei einer Konsistenz von 12–15 % oder kontinuierlich in Kegelrefinern, wobei das Material über Stufen hinweg allmählich von 3 % auf 10 % konzentriert wird.
Hydrozyklone während der Endwäsche erleichtern die Sortierung. Das Mahlen unterstützt die Diffusion und entfernt die letzten Rückstände der Faserkapillarsäure gegen den Wasserfluss. Schwache Basen (Natriumcarbonat oder Kreide) halten einen pH-Wert von 7 aufrecht, und Stabilisatoren (organische Säuren) können zugesetzt werden.
5. Verwendung von Cellulosenitrat
Cellulosenitrat wird zur Herstellung von Sprengstoffen, Lacken, Dispersionen und Celluloid verwendet.
1. Sprengstoffe
Je nach Verwendungszweck kann es sich bei Sprengstoffen um Sprengstoffe, Treibmittel, Zünder, Anzünder oder Pyrotechnik handeln.
Cellulosenitrate werden in Treibmitteln und Schießpulver verwendet und werden in folgende Kategorien eingeteilt:
- Monobasisch: Rein basierend auf Cellulosenitrat.
- Dibasic: Enthält zusätzliche Energieträger wie Nitroglycerin oder Diglycoldinitrat.
- Tribasic: Enthält eine dritte Komponente wie Nitroguanidin, die für eine geringere Verbrennungswärme und eine längere Lebensdauer des Waffenlaufs sorgt.
Je nach Stickstoffgehalt werden bestimmte Arten von Cellulosenitrat verwendet:
- CP I (Schießbaumwolle): enthält 13,3–13,5 % N, hoch nitrierte Zellulose, die als Treibmittel verwendet wird.
- CP II (Collodium): enthält 12,0–12,7 % N und wird hauptsächlich für rauchfreies Pulver verwendet.
- PE (Pulverstandard): enthält 11,5–12,0 % N, ist weniger nitriert und wird für kleinere Arme verwendet.
Aromatische Amine wie Diphenylamin werden als Stabilisatoren in Schießpulver verwendet, indem sie bei der Zersetzung entstehende nitrose Gase binden. Mischungen aus CP I und CP II bieten den gewünschten Energiegehalt und können ebenfalls verwendet werden.
Granulat aus Cellulosenitrat, das in Schießpulver verwendet wird, ist mit Graphit beschichtet, um elektrostatische Aufladungen zu verhindern. Seine Hauptanwendungsgebiete sind Kleinwaffenmunition, großkalibrige Geschütze und Panzer.
2. Lacke
Die filmbildenden Fähigkeiten von Cellulosenitrat, die durch physikalische Trocknung erreicht werden, sind die Grundlage seiner vielfältigen Lackanwendungen. Es ist mit einer Vielzahl von Harzen, Weichmachern, Pigmenten und Additiven kompatibel und ermöglicht die Herstellung von Lacken mit spezifischen Eigenschaften.
Lösungsmittelmischungen spielen eine wichtige Rolle bei der Filmbildung und beeinflussen die Trocknungszeit und andere Lackeigenschaften. Cellulosenitratlacke werden industriell in der Holz-, Metall-, Papier-, Folien- (einschließlich Heißsiegel-) und Lederindustrie sowie in anderen Anwendungen wie Klebstoffen, Spachtelmassen und Druckfarben eingesetzt.
Auftragstechniken wie Sprühen, Gießen, Rollen, Rakeln und Tauchen bieten Flexibilität je nach Substrat und gewünschtem Ergebnis. Die Anpassung der Viskosität und Löslichkeit des gewählten Cellulosenitrattyps an die spezifische Anwendung gewährleistet eine optimale Leistung.
Endlich stehen für bestimmte Anwendungen umweltfreundliche wässrige Dispersionen mit reduziertem Gehalt an organischen Lösungsmitteln zur Verfügung, die Nachhaltigkeitsbedenken berücksichtigen.
3. Dispersionen
Herkömmliche Lacke auf Basis von Cellulosenitrat enthalten viele organische Lösungsmittel (60–90 %). Diese Lösungsmittel werden beim Trocknen des Lacks in die Luft freigesetzt und tragen zur Luftverschmutzung und potenziellen Gesundheitsrisiken bei. Sie sind außerdem teuer und können Probleme bei der Entsorgung mit sich bringen.
Wässrige Cellulosenitrat-Dispersionen ersetzen die organischen Lösungsmittel durch Wasser. Obwohl sie Vorteile bieten, stellen diese Dispersionen auch einige Herausforderungen dar:
- Cellulosenitrat selbst löst sich nicht in Wasser auf und erfordert die Zugabe spezieller Chemikalien, sogenannter Koaleszenzmittel, damit es beim Auftragen einen Film bildet.
- Derzeit sind wässrige Dispersionen nicht so weit verbreitet und vielseitig wie herkömmliche Lacke auf Lösungsmittelbasis. Sie eignen sich am besten für bestimmte Materialien wie Leder, Holz, Folie und Metall.
Beispiele für kommerziell erhältliche wässrige Dispersionen sind Isoderm (Bayer AG), Coreal (BASF) und spezielle Typen von Waloran N (Wolff Walsrode AG).
4. Celluloid
Eine besondere Verwendung von Cellulosenitrat ist die Herstellung von Zelluloid, das durch Mischen von Cellulosenitrat (10,5–11,0 % N) mit Weichmachern wie Kampfer und Lösungsmitteln in einem Kneter hergestellt wird.
Zelluloid wurde weitgehend durch synthetische Materialien ersetzt, wird aber immer noch für Kämme, Haarschmuck, Toilettenartikel, Bürobedarf, Tischtennisbälle und bestimmte Anwendungen verwendet.
6. Toxikologie von Cellulosenitrat
Bei der Herstellung von Zellulosenitrat werden gefährliche Chemikalien eingesetzt, die besondere Sicherheitsmaßnahmen und Vorschriften erfordern.
Vorläuferchemikalien
- Schwefelsäure: Konzentrierte Säure (5-15 % und mehr) fällt unter die EG-Nr. 016-020-01-5 bzw. 016-020-00-8 und unterliegt der kennzeichnungspflichtigen Arbeitsstoffverordnung.
- Salpetersäure: Konzentrierte und gemischte Nitriersäuren sind ähnlich wie Schwefelsäure unter der EG-Nr. 007-004-01-9 und 007-004-00-1, kennzeichnungspflichtig und unter Einhaltung der Arbeitsstoffverordnung.
Darüber hinaus erfordern ihre oxidierenden Eigenschaften Vorsicht beim Umgang mit organischen Materialien. Die MAK-Werte (maximale Arbeitsplatzkonzentration) sind auf 10 ml/m³ (ppm) für Salpetersäuredämpfe und 5 ml/m³ (ppm) für Stickoxide (NO2) festgelegt, was regelmäßige Kontrollen der Mitarbeiter auf mögliche obstruktive Atemwegserkrankungen erforderlich macht.
Cellulosenitrat
Im Gegensatz zu seinen Vorläufern ist Cellulosenitrat selbst weder giftig noch gesundheitsgefährdend. Potenzielle Gesundheitsrisiken entstehen jedoch durch:
- Dämpfungsmittel: Das Einatmen von Dämpfungsmitteln wie Zellulosenitrat und nitrosen Gasen, die beim Verbrennen oder Schwelen freigesetzt werden, kann schädlich sein.
- Phlegmatisierungsmittel: Während handelsübliches Cellulosenitrat für die Lackherstellung (Stickstoffgehalt < 12,6 %) mindestens 18 % gelbildenden Weichmacher enthält, bestehen widersprüchliche Vorschriften.
Die Arbeitsstoffverordnung stuft es als gefährlichen Stoff ein, der eine besondere Verpackung und Kennzeichnung erfordert, und lehnt sich an ähnliche EG-Vorschriften (1982) an.
Feuchtmittel wie Ethanol und 2-Propanol unterliegen jedoch nicht diesen Vorschriften, und Butanol fällt nur in die Kategorie II d und stellt keine gesundheitlichen Bedenken dar, wenn es in gedämpften Gemischen in einer Konzentration von maximal 35 % vorhanden ist.
Referenz
- Cellulose Esters; Ullmann’s Encyclopedia of Industrial Chemistry. – https://onlinelibrary.wiley.com/doi/10.1002/14356007.a05_419.pub2