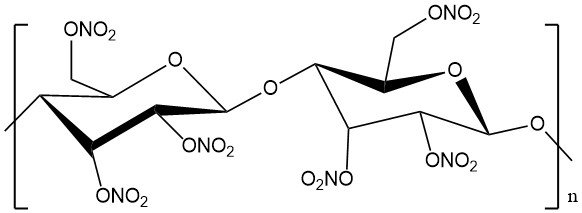
Cellulosenitraat, ook bekend als nitrocellulose, flash paper, guncotton of celluloid, is een chemisch product afgeleid van het natuurlijke polymeer cellulose. Het is een witte, geurloze en smaakloze substantie. De eigenschappen ervan zijn afhankelijk van de mate van substitutie.
Inhoudsopgave
1. Fysieke eigenschappen van cellulosenitraat
De dichtheid is sterk afhankelijk van de mate van nitrering; deze neemt toe naarmate de mate van substitutie toeneemt. Commercieel verkrijgbare, bevochtigde cellulosenitraatkatoensoorten vertonen bulkdichtheden binnen 0,25-0,60 kg/l, afnemend tot 0,15-0,40 kg/l (droge massa).
Cellulosenitraatchips met ten minste 18% dibutylftalaat bereiken een dichtheid van 1,45 g/cm³, met een bulkdichtheid van 0,3-0,65 kg/l.
Fijnheid heeft een aanzienlijke invloed op het specifieke oppervlak. Het Rossin-apparaat levert nauwkeurige metingen en onthult waarden tussen 1850 en 4700 cm²/g. Het binnenoppervlak, bepaald via de BET-methode, is afhankelijk van de molaire massa. Het verlagen van de ontgassingstemperatuur vanwege de ontvlambaarheid van cellulosenitraat leidt echter tot onzekerheid over volledige desorptie.
Thermodynamische eigenschappen: Tabel 1 vat de belangrijkste waarden samen.
Eigenschap | Waarde |
---|---|
Verbrandingswarmte | 12 kJ/g |
Smeltwarmte | 15 J/g |
Soortelijke warmtecapaciteit | 1,5 J/(g·K) |
Thermische geleidbaarheid | 0,2 W/(m·K) |
Glasovergang temperatuur | 50-60 °C |
Ontledingstemperatuur | 180 °C |
Elektrische eigenschappen: Gemeten op celluloid (30 gew.% kamfer in cellulosenitraat), worden hieronder vermeld:
Diëlektrische constante:
- bij 50-60 Hz: 7,0-7,5
- bij 106 Hz: 6,0-6,5
Dissipatiefactor (tan δ):
- bij 50–60 Hz: 0,09–0,12
- bij 106 Hz: 0,06-0,09
Specifieke weerstand: 1011–1012 Ω⋅cm
De spanning-rekcurve onthult de afhankelijkheid van rek en treksterkte van moleculaire grootte (uitgedrukt als viscositeit). Een hogere moleculaire massa vertaalt zich naar elastischere films met verhoogde treksterkte.
Optische eigenschappen: De kristallijne structuur maakt cellulosenitraatfilms optisch anisotroop. Kleuren in gepolariseerd licht verschuiven met stikstofgehalte:
- 11,4% N: zwak rood
- 11,5-11,8% N: geel
- 12,0-12,6% N: blauw naar groen
De brekingsindex is 1,51, met een pieklichttransmissie bij 313 nm.
Lichtstabiliteit: Zonlicht, met name ultraviolette straling, verkleurt en verbrost cellulosenitraatfilms. Oplosmiddelen, weekmakers en harsen kunnen de mate van vergeling beïnvloeden.
2. Chemische eigenschappen van nitrocellulose
Cellulosenitraat wordt geproduceerd door gedeeltelijke of volledige nitratie van de drie hydroxylgroepen van de cellulose en vertoont een wisselend stikstofgehalte op basis van de mate van nitratie.
- Cellulosemononitraat: 6,75% N
- Cellulosedinitraat: 11,11% N
- Cellulose trinitraat: 14,14% N
Nitrocellulose met 10,8–12,6% N is geschikt voor lakken vanwege de oplosbaarheid in organische oplosmiddelen, en boven de 12,3% N wordt het voornamelijk gebruikt in explosieven.
Het stikstofgehalte is direct gerelateerd aan de mate van substitutie, wat de oplosbaarheid in organische oplosmiddelen bepaalt.
- In alcohol oplosbare nitrocellulose (type A): ~10,9–11,3% N (zeer oplosbaar in alcoholen, esters en ketonen)
- Matig oplosbare nitrocellulose (type AM): ~11,4–11,7% N (oplosbaar in esters, ketonen, glycolethers en uitstekende oplosbaarheid met alcoholen)
- Cellulosenitraat oplosbaar in esters (type E): 11,8–12,2% voor lakkatoen, tot 13,7% voor schietkatoen (goed oplosbaar in esters, ketonen en glycolethers).
Intrinsieke viscositeit weerspiegelt de gemiddelde moleculaire lengte (polymerisatiegraad) en kan wiskundig worden gekoppeld aan moleculaire massa via de Staudinger-Mark-Houwink-vergelijking.
Polymoleculaire gegevens, waaronder polymerisatiegraad en moleculaire massaverdeling, complementviscositeit en oplosbaarheid, zijn belangrijk voor het begrijpen van mechanische eigenschappen en verouderingsprocessen. Gelpermeatiechromatografie isoleert polymeren efficiënt op basis van hun moleculaire massa.
Cellulosenitraat is zeer compatibel met talrijke stoffen die in nitrolakken voorkomen, zoals alkydharsen, maleïneharsen, ketonharsen, ureumharsen, polyacrylaten en verschillende weekmakers.
Sterke zuren, basen en organische aminen kunnen cellulosenitraat snel afbreken of ontleden, wat mogelijk tot deflagratie kan leiden. De esterbindingen dragen bij aan de inherente instabiliteit, die wordt beïnvloed door temperatuur, monstervorm en de aanwezigheid of afwezigheid van ontledingsproducten.
Gemengde zwavelzuuresters, die tijdens de productie worden geïntroduceerd, zorgen voor verdere instabiliteit, waardoor een stabilisatiestap met zwak zuur water nodig is.
Boven 100 °C ondergaat cellulosenitraat thermische ontleding via een reeks exotherme oxidatiereacties die worden geïnitieerd door NO2-radicalen, wat mogelijk leidt tot spontane deflagratie.
Stabilisatoren zoals difenylamine of zwakke zuren kunnen intermediaire stikstofoxiden binden en deze autokatalytische kettingreactie voorkomen. Deflagratietemperatuur, beïnvloed door stabilisatie- en plasticisatieniveaus, dient als een belangrijke maatstaf voor thermische stabiliteit.
De Bergmann-Junk-test en de warm storage-test bieden aanvullende methoden voor het evalueren van de stabiliteit van cellulosenitraat.
3. Nitrocellulose-grondstoffen
De grondstoffen die worden gebruikt bij de productie van cellulosenitraat zijn cellulose en nitreermiddelen.
3.1. Cellulose
Vóór de Eerste Wereldoorlog werden alleen katoenlinters met een hoge zuiverheid (gebleekte vlokken of crêpe) gebruikt voor nitratie vanwege hun superieure opbrengst en helderheid.
De schaarste aan linters leidde tot experimenten met andere bronnen zoals houtcellulose, zelfs ongebleekt, en vezels van eenjarige planten. Deze resulteerden echter in inferieure lakken met dofheid en slechte mechanische eigenschappen vanwege het hoge pentosangehalte.
De vooruitgang in chemische zuivering van houtpulp met warme of koude alkalibehandelingen (R18-waarden > 92%) maakte het echter mogelijk om het te gebruiken voor nitratie, vergelijkbaar met linters. Zeer geraffineerde, voorgehydrolyseerde sulfaatpulpen (R18 > 96%) zijn bijzonder geschikt en maken viscositeitscontrole mogelijk via de initiële cellulosekeuze.
Een laag as- en calciumgehalte in cellulose is belangrijk om calciumsulfaatneerslag tijdens industriële nitrering te voorkomen.
Uit onderzoek blijkt dat de morfologische en chemische eigenschappen van cellulose, samen met de aanwezigheid van hemicellulose en lignine, het nitreringsvermogen en de eigenschappen van het eindproduct beïnvloeden. Linters vertonen een superieure zuurretentiecapaciteit (110–130%) vergeleken met houtpulp (tot 300%), wat van invloed is op de retentie van vezelmassa tijdens de verwerking.
Een gespecialiseerde machine meet de compressie en relaxatie van de vezelstapel om te bepalen of een grondstof geschikt is voor nitrering.
Ongeveer 3,4% (150.000 ton) van de wereldwijde productie van chemische pulp wordt gebruikt voor de productie van cellulosenitraat.
3.2. Nitreringsmiddelen
Het salpeterzuur-/zwavelzuur-/watersysteem van Schöenbein blijft het favoriete industriële nitreringsmiddel. De maximaal haalbare substitutiegraad (DS 2,7, 13,4% N) vereist watervrij salpeterzuur en een molaire verhouding van 1:2 van HNO3 tot H2SO4 monohydraat.
Het optimale nitreringsmengsel bevat 21,36% HNO3, 66,44% H2SO4 en 12,20% H2O.
Het watergehalte heeft een aanzienlijke invloed op de haalbare nitrering, met een daling van de opbrengst boven de 12%. De gewenste veresteringsniveaus worden aangepast door het nitreringszuurmengsel te variëren (Tabel 2), waarbij industriële processen HNO3 op 25–26% houden.
Nitrocellulosetype | % HNO3 | % H2SO4 | % H2O | N-gehalte, % | DS |
---|---|---|---|---|---|
Lakkatoen A | 25 | 55,7 | 19,3 | 10,75 | 1,90 |
Celluloid katoen | 25 | 55,8 | 19,2 | 10,90 | 1,95 |
Lakkatoen AM | 25 | 56,6 | 18,4 | 11,30 | 2,05 |
Dynamietkatoen | 25 | 59,0 | 16,0 | 12,10 | 2,30 |
Lakkatoen E | 25 | 59,5 | 15,5 | 12,30 | 2,35 |
Poederkatoen | 25 | 59,8 | 15,2 | 12,60 | 2,45 |
Gunkatoen | 25 | 66,5 | 8,5 | 13,40 | 2.70 |
Het ternaire systeem HNO3/H2SO4/H2O is uitgebreid bestudeerd, waarbij het fasediagram drie verschillende zones onthult:
- Technische nitratiezone: Geschikt voor nitratie (10-100% salpeterzuur, 0-80% zwavelzuur, 0-20% water).
- Oplossingszone: Geen significante nitratie; celluloseafbraak vindt plaats (0–10% salpeterzuur, 60–100% zwavelzuur, 0–40% water).
- Zwellingzone: Een verhoogd watergehalte leidt tot een verminderde nitrering (salpeterzuurgehalte varieert, zwavelzuur 60–100%, water neemt toe).
Een minder gebruikelijk proces gebruikt magnesiumnitraat in plaats van zwavelzuur als dehydratiemiddel, wat potentieel biedt voor continue verwerking en afvalreductie.
4. Productie van cellulosenitraat
Cellulosenitraat wordt geproduceerd door cellulose, meestal katoenlinters, te behandelen met een mengsel van geconcentreerd salpeterzuur en zwavelzuur. De mate van nitrering wordt geregeld door de temperatuur, zuurconcentraties en reactietijd aan te passen.

Het stroomdiagram (Figuur 1) toont de industriële productie van nitrocellulose door het gemengde zuurproces. De viscositeit van het eindproduct wordt bepaald door de keuze van de initiële cellulose, en de mate van nitrering wordt bepaald door de samenstelling van het mengzuur. De uiteindelijke viscositeit wordt aangepast tijdens de drukkookstap.
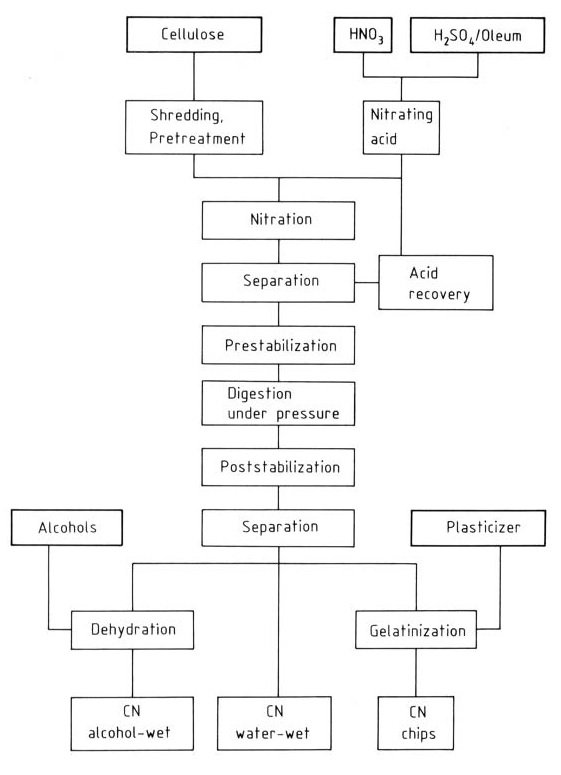
4.1. Cellulosebereiding
De verwerking van cellulose speelt een belangrijke rol bij het bereiken van snelle, uniforme nitratie. Traditioneel werden katoenlinters met een laag vochtgehalte (<7%) mechanisch uiteengevallen om een homogene vezelmassa te verkrijgen. Dit proces was echter arbeidsintensief en beperkt in omvang.
Geperste pulpvellen boden een alternatief, maar moesten in kleine stukjes worden versnipperd om efficiënte nitratie mogelijk te maken. Voor dit doel werd van oudsher sparren- of beukencellulose gebruikt, voorbehandeld met 20% natriumhydroxide (mercerisatie), vaak in de vorm van lichtgewicht crêpepapier (25 g/m³).
Om de kostbare papiervelconversie te vermijden, werden pogingen gedaan om pulpen direct te desintegreren in losse, pluisachtige vezels. Een vochtgehalte van 50% bleek optimaal voor nitratie en daaropvolgende zuuruitwassing, maar vereiste droging vóór nitratie, wat een extra verwerkingsstap opleverde.
De Stern-shredder vertegenwoordigde een aanzienlijke vooruitgang door pulpvellen te scheuren in plaats van te snijden, waardoor de vezelcompressie werd geminimaliseerd en de uniformiteit van de nitratie werd verbeterd.
Moderne cellulose voor nitratie wordt voornamelijk gebruikt in de vorm van pluis, snippers of chips. De pakkingsdichtheid en het compressiegedrag van deze vormen hebben een aanzienlijke invloed op de zwellings- en nitratiekinetiek, evenals op de zuurretentiecapaciteit. Het optimaliseren van deze factoren is cruciaal voor efficiënte en gecontroleerde nitratieprocessen.
4.2 Nitratie van cellulose
Het dominante industriële proces voor cellulosenitratie is nog steeds een batchsysteem dat in 1922 door DuPont werd ontwikkeld. De apparatuur is gemaakt van roestvrij staal. Het voorverwarmde nitreerzuur wordt toegevoegd aan de roerreactor met cellulose.
Een grote zuurovermaat (1:20 tot 1:50) zorgt voor roerbaarheid en warmteafvoer. De nitreringstemperatuur varieert van 10 °C (dynamiet) tot 36 °C (celluloid).
Na 5 minuten is de reactie voltooid en blijft het mengsel 30 minuten in de reactor vanwege de temperatuurgevoeligheid. Hydrolytische afbraak met aanzienlijke opbrengstverliezen begint boven 40 °C.
Theoretische opbrengsten voor veelvoorkomende nitrocellulosetypen (DS 1,8–2,7, N-gehalte 10,4–13,4%) bereiken 150–176% op basis van cellulose, maar praktische opbrengsten zijn 15% lager vanwege het type en de zuiverheid van cellulose, temperatuur en duur.
Verliezen ontstaan door volledige ontleding van cellulose tot oxaalzuur door oxidatie van oligosachariden en monosachariden met salpeterzuur. Mechanische verliezen tijdens daaropvolgende scheiding (met name korte hardhoutvezels) dragen ook bij.
Het reactiemengsel wordt met hoge snelheid gecentrifugeerd om overtollig zuur te scheiden en te recyclen. Het vasthouden van vocht voorkomt ontbranding of deflagratie.
Zuurretentie door het product is belangrijk om economische redenen. Linters (100-130% retentie) presteren aanzienlijk beter dan houtcelluloses (tot een 3x hogere cellulosenitraat-tot-zuurverhouding), afhankelijk van het type hout of cellulose en de verwerking.
Het zuurvochtige product wordt onmiddellijk verdund in overtollig water (1% consistentie) om snel aanhechtend zuur te verdringen en cellulosenitraatverzeping te voorkomen.
Continue nitreringsprocessen, ontwikkeld in de jaren 60, bieden economische voordelen, uniforme productkwaliteit en verbeterde veiligheid. Het systeem maakt gebruik van twee of meer cascade-gekoppelde, direct-run tanks of buizen die zijn uitgerust met transportbanden (schroef- of turbulentiemengers) om het reactiemengsel te laten vorderen.
Bereide cellulose mengt continu met toegevoegd nitrerend zuur in dit cascadesysteem. Het is belangrijk dat de cellulose snel wordt toegevoegd en onmiddellijk wordt bedekt met zuur. De verblijftijd is 30-55 minuten, maar een nieuwere lusvormige drukreactor heeft slechts 6-12 minuten nodig.
De reactant gaat vervolgens een continue centrifuge in voor gelijktijdige afscheiding van overtollig zuur en verdunning van water. De korte verblijftijd (slechts een paar seconden) minimaliseert de deflagratie- en verzepingsrisico’s.
Figuur 2 illustreert het schema van het continue Hercules-proces.
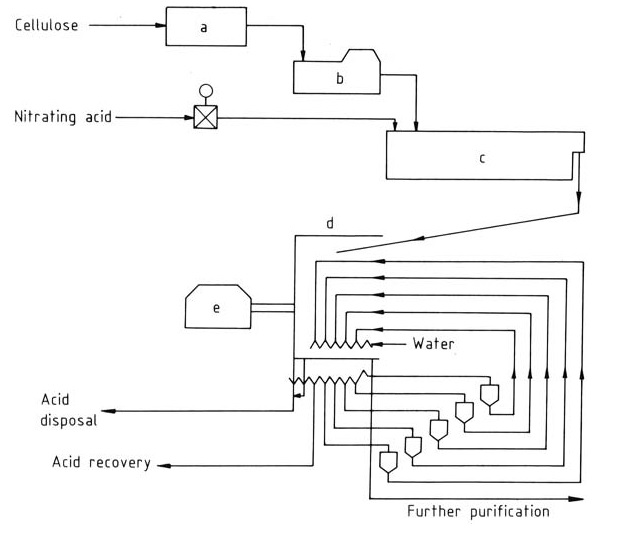
a) Preconditionering; b) Automatische weegschaal; c) Reactor; d) Waszone; e) Centrifuge
Voorgeconditioneerde cellulose komt via automatische weegschalen de continue reactor binnen en vervolgens wordt het reactieproduct gecentrifugeerd en tegenstrooms gewassen in waterzones. Het bijna zuurvrije product verlaat de centrifuge, terwijl het gewassen zuur met minimaal verlies kan worden gerecycled.
4.3. Stabilisatie en viscositeitsaanpassing van nitrocellulose
Na het voorwassen zuivert herhaald wassen en koken met water met 0,5-1% zuurresidu het cellulosenitraat verder. Deze batchmethode vereist aanzienlijke ruimte, water en energie, met kooktijden variërend van 6 uur voor celluloid tot 40 uur voor schietkatoen. Er zijn ook geautomatiseerde continue processen ontwikkeld.
Voorstabilisatie verwijdert het grootste deel van het resterende zwavelzuur, wat de ontleding van cellulosenitraat katalyseert. Het zuur bindt zich door adsorptie en verestering. Zwak genitreerd cellulosenitraat behoudt 1-3% totaal sulfaat, met 70-85% als zure semi-esters.
Sterk genitreerd cellulosenitraat heeft slechts 0,2-0,5% sulfaat, waarvan 15-40% esters kunnen zijn. Semi-esters worden gemakkelijk verzeept en weggespoeld door kokend water. Het bestaan van “resistent” sulfaat als neutrale ester of geadsorbeerd zuur blijft onduidelijk.
Drukkoken (digestie) bij 6-8% consistentie en 130-150 °C past de uiteindelijke viscositeit van cellulosenitraat aan door gecontroleerde polymeerafbraak. Het resterende spoor zwavelzuur bevordert hydrolyse bij deze temperatuur en druk. Bijvoorbeeld, een behandeling van 3 uur bij 132 °C kan de viscositeit verlagen tot 1/10e van de oorspronkelijke waarde.
Dit proces vergemakkelijkte de ontwikkeling van high-solid coatings en beschermende nitrolakken. Schietkatoenstabilisatie profiteert van drukkoken, terwijl dynamietwol dit meestal omzeilt.
Ketenafbraak genereert verdere productverliezen als oplosbare fragmenten en oxaalzuur. Nitreuze gassen (NOx) van salpeterzuurreductie worden continu verwijderd om ontleding van cellulosenitraat te voorkomen.
Drukkoken kan batchgewijs worden uitgevoerd in autoclaven of continu in buisreactoren (bijv. 1500 m lang, 100 mm diameter) met behulp van directe stoom. Er bestaat een eenpotsproces dat prestabilisatie, drukkoken en poststabilisatie in één bewerking combineert.
Extra wassen en koken elimineren bijna het resterende zwavelzuur. Celluloid en lakcellulosenitraat worden afgewerkt in schilferige of vezelachtige vorm, terwijl schietkatoen moet worden gemalen. Dit gebeurt in Hollander-motoren met een consistentie van 12-15% of continu in kegelraffinaderijen, waarbij het materiaal geleidelijk wordt geconcentreerd van 3% tot 10% over de fasen.
Hydrocyclonen tijdens de laatste wasbeurt vergemakkelijken het sorteren. Maalproces helpt bij diffusie, waarbij de laatste vezelcapillaire zuurresten tegen de waterstroom worden verwijderd. Zwakke basen (natriumcarbonaat of krijt) handhaven een pH van 7 en stabilisatoren (organische zuren) kunnen worden toegevoegd.
5. Toepassingen van cellulosenitraat
Cellulosenitraat wordt gebruikt bij de productie van explosieven, lakken, dispersies en celluloid.
1. Explosieven
Afhankelijk van het gebruik kunnen explosieven springstoffen, voortstuwingsgassen, detonatoren, ontstekers of pyrotechniek zijn.
Cellulosenitraten worden gebruikt in voortstuwingsgassen en buskruit en worden gecategoriseerd als:
- Monobasisch: Puur gebaseerd op cellulosenitraat.
- Dibasisch: Bevat extra energiedragers zoals nitroglycerine of diglycoldinitraat.
- Tribasisch: Bevat een derde component zoals nitroguanidine, wat zorgt voor een lagere verbrandingswarmte en een langere levensduur van de loop.
Specifieke soorten cellulosenitraat worden gebruikt op basis van stikstofgehalte:
- CP I (Guncotton): bevat 13,3–13,5% N, sterk genitreerde cellulose die wordt gebruikt voor voortstuwingsgassen.
- CP II (Collodium): bevat 12,0-12,7% N en wordt voornamelijk gebruikt voor rookloos kruit.
- PE (Powder Standard): bevat 11,5–12,0% N, is minder genitreerd en wordt gebruikt voor kleinere wapens.
Aromatische aminen zoals difenylamine worden gebruikt als stabilisatoren in buskruit door stikstofgassen te binden die ontstaan tijdens de ontleding. Mengsels van CP I en CP II bieden de gewenste energie-inhoud en kunnen ook worden gebruikt.
Korrels van cellulosenitraat die in buskruit worden gebruikt, zijn gecoat met grafiet om elektrostatische ladingen te voorkomen. De belangrijkste toepassingen zijn in munitie voor kleine wapens, grootkaliber geweren en tanks.
2. Lakken
De filmvormende eigenschappen van cellulosenitraat, bereikt door fysieke droging, vormen de basis van de diverse laktoepassingen. Het is compatibel met een breed scala aan harsen, weekmakers, pigmenten en additieven, waardoor lakken met specifieke eigenschappen kunnen worden gemaakt.
Oplosmiddelmengsels spelen een belangrijke rol bij de filmvorming en beïnvloeden de droogtijd en andere lakeigenschappen. Cellulose nitraat lakken worden industrieel gebruikt in de hout-, metaal-, papier-, folie- (inclusief hete seal) en leerindustrie, evenals in andere toepassingen zoals lijm, plamuur en drukinkt.
Toepassingstechnieken zoals spuiten, gieten, rollen, doktersmescoating en dompelen bieden flexibiliteit op basis van het substraat en het gewenste resultaat. Door de viscositeit en oplosbaarheid van het gekozen cellulose nitraat type af te stemmen op de specifieke toepassing, wordt optimale prestatie gegarandeerd.
Ten slotte zijn er voor bepaalde toepassingen milieuvriendelijke waterige dispersies met minder organische oplosmiddelen beschikbaar, waarmee duurzaamheidszorgen worden aangepakt.
3. Dispersies
Traditionele lakken gemaakt met cellulose nitraat bevatten veel organische oplosmiddelen (60–90%). Deze oplosmiddelen komen vrij in de lucht als de lak droogt, wat bijdraagt aan luchtvervuiling en mogelijke gezondheidsrisico’s. Ze zijn ook duur en kunnen een uitdaging vormen voor de verwijdering.
Waterige cellulosenitraatdispersies vervangen de organische oplosmiddelen door water. Hoewel ze voordelen bieden, brengen deze dispersies ook enkele uitdagingen met zich mee:
- Cellulosenitraat lost zelf niet op in water, waardoor speciale chemicaliën, coalescentiemiddelen genaamd, moeten worden toegevoegd om een film te vormen bij het aanbrengen.
- Momenteel worden waterige dispersies niet zo veel gebruikt of zijn ze niet zo veelzijdig als traditionele lakken op basis van oplosmiddelen. Ze zijn het meest geschikt voor specifieke materialen zoals leer, hout, folie en metaal.
Voorbeelden van commercieel verkrijgbare waterige dispersies zijn Isoderm (Bayer AG), Coreal (BASF) en speciale soorten Waloran N (Wolff Walsrode AG).
4. Celluloid
Celluloidnitraat wordt speciaal gebruikt bij de productie van celluloid, dat wordt geproduceerd door cellulosenitraat (10,5-11,0% N) te mengen met weekmakers zoals kamfer en oplosmiddelen in een kneder.
Celluloid is grotendeels vervangen door synthetische materialen, maar wordt nog steeds gebruikt voor kammen, haarversieringen, toiletartikelen, kantoorbenodigdheden, pingpongballen en specifieke toepassingen.
6. Toxicologie van cellulosenitraat
De productie van cellulosenitraat omvat gevaarlijke chemicaliën die specifieke veiligheidsmaatregelen en -voorschriften vereisen.
Precursorchemicaliën
- Zwavelzuur: Geconcentreerd zuur (5-15% en hoger) valt onder EG-nr. 016-020-01-5 en 016-020-00-8, respectievelijk, en is onderworpen aan de Arbeitsstoffverordnung (werkstofverordening) die correcte etikettering vereist.
- Salpeterzuur: Net als zwavelzuur worden geconcentreerde en gemengde nitrerende zuren geclassificeerd onder EG-nr. 007-004-01-9 en 007-004-00-1, die etikettering vereisen en zich aan de Arbeitsstoffverordnung moeten houden.
Bovendien vereisen hun oxiderende eigenschappen voorzichtigheid bij het omgaan met organische materialen. MAK-waarden (maximale werkplekconcentratie) zijn vastgesteld op 10 ml/m³ (ppm) voor salpeterzuurdampen en 5 ml/m³ (ppm) voor stikstofoxiden (NO2), wat regelmatige controles van werknemers op mogelijke obstructieve luchtwegaandoeningen vereist.
Cellulose Nitraat
In tegenstelling tot zijn voorlopers is cellulose nitraat zelf niet inherent giftig of gevaarlijk voor de gezondheid. Mogelijke gezondheidsrisico’s ontstaan echter door:
- Bevochtigingsmiddelen: Inademing van bevochtigingsmiddelen zoals cellulose nitraat en nitreuze gassen die vrijkomen bij verbranding of smeulen kan schadelijk zijn.
- Flegmatiseringsmiddelen: Hoewel commercieel verkrijgbaar cellulose nitraat voor lakproductie (stikstofgehalte < 12,6%) ten minste 18% gelatinerende weekmaker bevat, bestaan er tegenstrijdige regelgevingen.
De Arbeitsstoffverordnung classificeert het als een gevaarlijke stof die specifieke verpakking en etikettering vereist, wat overeenkomt met soortgelijke EEG-regelgeving (1982). Dempingsmiddelen zoals ethanol en 2-propanol vallen echter niet onder deze regelgeving, en butanol valt alleen onder categorie II d zonder gezondheidsrisico’s wanneer het aanwezig is in gedempte mengsels in een maximale concentratie van 35%.
Referentie
- Cellulose Esters; Ullmann’s Encyclopedia of Industrial Chemistry. – https://onlinelibrary.wiley.com/doi/10.1002/14356007.a05_419.pub2