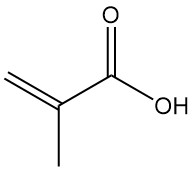
Methacrylic acid, also known as α-methylacrylic acid or 2-methylpropenoic acid, is an organic acid with the formula CH2=C(CH3)COOH. It is a colorless, moderately volatile, corrosive liquid with a strongly acrid odor.
Methacrylic acid was first produced in 1865 from ethyl methacrylate, which was prepared by dehydration of ethyl α-hydroxyisobutyrate.
Table of Contents
1. History of Methacrylic Acid and methacrylates
The scientific exploration of acrylates and methacrylates for commercial applications began with the doctoral thesis of OTTO ROEHΜ in 1901. He investigated the polymerization products of acrylic acid derivatives and envisioned their potential industrial use.
Roehml reported the synthesis of transparent, rubbery materials but lacked efficient production methods at the time. In 1907, he partnered with OTTO HAAS to establish a company focused on leather treatment enzymes.
Significant advancements in the commercial production of acrylates and methacrylates occurred in the 1920s. Following World War I, Roehml developed a process for large-scale acrylate production using ethylene cyanohydrin, an intermediate derived from ethylene chlorohydrin.
Later, he collaborated with Walter Bauer to establish a similar process for methyl methacrylate using acetone cyanohydrin. By 1931, Bauer had successfully produced a clear and transparent methyl methacrylate polymer that softened above 100 °C.
The 1930s witnessed intensive research on fabricating cast sheets from methyl methacrylate by Rohm and Haas and Du Pont (USA), Rohm and Haas AG (Germany), and ICI (England).
The first commercial production of methyl methacrylate monomer began in Darmstadt, Germany (1933), via the acetone cyanohydrin route, which involved converting the cyanohydrin to ethyl α-hydroxyisobutyrate, followed by dehydration using P2O5.
ICI secured a patent in 1934 for an alternative method that transformed acetone cyanohydrin to methacrylamide sulfate using concentrated sulfuric acid. Methacrylic acid, obtained by hydrolyzing methacrylamide sulfate, could then be esterified to form methyl methacrylate.
Recognizing the efficiency of the ICI process, Rohm and Haas AG entered into a cross-licensing agreement for cast acrylic sheet production. Subsequently, both ICI and Rohm and Haas AG initiated commercial methyl methacrylate production using the methacrylamide sulfate route in 1937.
Rohm and Haas in the United States, then an independent company since 1917, continued using the original process for several years due to licensing limitations.
The methacrylamide sulfate route remained the main commercial process for methyl methacrylate and methacrylic acid production until the introduction of isobutene oxidation processes in 1983. These processes were independently developed in Japan by Japan Catalytic Chemical and Mitsubishi Rayon.
While additional isobutene-based methacrylic acid capacity is planned in Japan and a new ethylene-based facility is under construction by BASF, the acetone cyanohydrin route is still used for a significant portion of the global methyl methacrylate demand.
Acetone-cyanohydrin-based operations primarily yield methyl methacrylate, the most important methacrylate derivative. Methacrylic acid produced by other routes is also used as an intermediate for methyl methacrylate synthesis.
Smaller quantities of other methacrylates, including ethyl methacrylate, n-butyl methacrylate, isobutyl methacrylate, and higher homologues like lauryl methacrylate and stearyl methacrylate, are manufactured by direct esterification of methacrylic acid or transesterification of methyl methacrylate.
Additionally, specialty monomers like 2-hydroxyethyl methacrylate, 2-hydroxypropyl methacrylate, aminoalkyl methacrylates (e.g., 2-dimethylaminoethyl methacrylate), and methacrylamide are commercially available. The intermediate methacrylamide sulfate is the precursor for methacrylamide production.
2. Physical Properties of Methacrylic Acid
Methacrylic acid is a weak organic acid with a pKa of 4.65. It is a clear, colorless liquid or colorless crystals with an acrid, repulsive odor. It is soluble in chloroform and miscible with water, ethanol, and ether.
The most important physical properties of methacrylic acid are listed in Table 1.
Property | Value |
---|---|
Molecular weight | 86.09 g/mol |
Melting point, °C | 15.8 |
Boiling point (101.3 kPa), °C | 162 |
Density, g/cm3 | 1.015 |
Refractive index | 1.4288 |
Vapor pressure, kPa |
at 20 °C: 0.09 at 60 °C: 1.33 |
Viscosity (24 °C), mPa·s | 1.38 |
Solubility in water | Miscible |
Critical temperature, °C | 370 |
Critical pressure, Pa | 4.70 |
Critical volume, cm3/mol | 270 |
Heat of vaporization (101.3 kPa), kJ/mol | 0.418 |
Specific heat capacity, J g-1 K-1 | 2.1 |
Flash point, °C |
Open cup: 77 Closed cup: 67 |
Autoignition temperature, °C | 400 |
3. Chemical Reactions of Methacrylic Acid
Methacrylic acid is very reactive, displaying reactions typical of both the alkene and the carboxylic acid.
The electron-withdrawing effect of the carboxylic acid polarizes the double bond and enhances its reactivity, but this reactivity is less pronounced than in acrylic acid because of the electron-donating methyl group.
As a result, nucleophilic Michael and Michael-like additions to the double bond take place only with electron-rich reagents.
3.1. Addition to the Carbon-Carbon Double Bond
Methacrylic acid reacts with hydrogen cyanide, hydrogen halides, hydrogen sulfide, mercaptans, alkyl amines, alcohols, phenols, or phosphines to produce β-substituted α-methyl propionates.
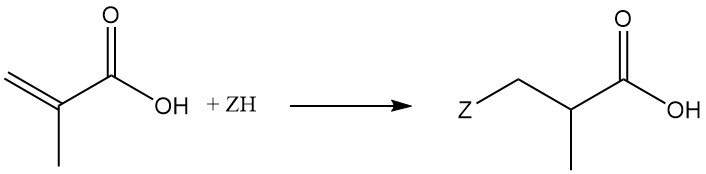
3.2. Diels-Alder Reactions
Methacrylic acid undergoes Diels-Alder reactions with dienes such as butadiene and cyclopentadiene.
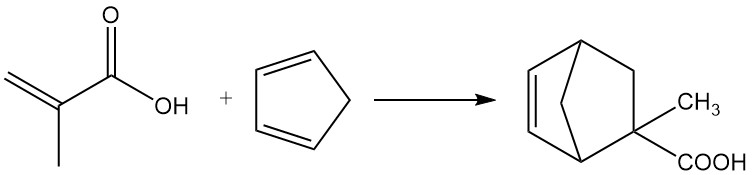
3.3. Reactions of the Carboxylic Acid Function
Esters of methacrylic acid are formed by reactions with alcohols in the presence of catalytic quantities of sulfuric or sulfonic acids. Acid-catalyzed addition of olefins also produces esters.
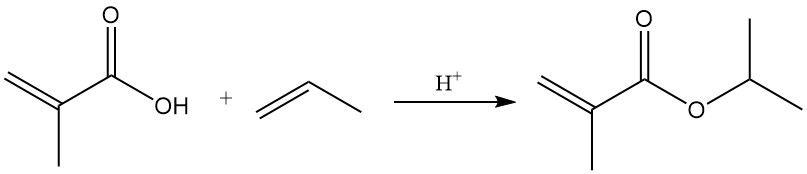
Reaction of the methacrylic acid group with epoxides in the presence of catalysts such as anion-exchange resins, ferric chloride, or lithium salts yields hydroxyethyl and hydroxypropyl methacrylates.
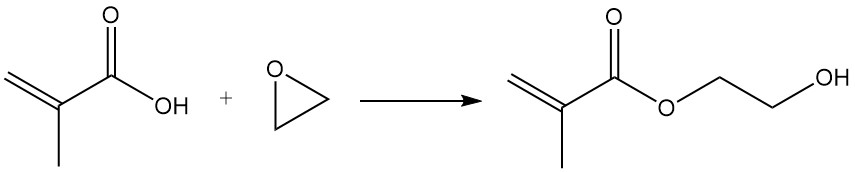
Methacryloyl chloride is synthesized by the reaction of the methacrylic acid with thionyl chloride or phosphorus trichloride.
Methacrylic acid reacts with acetic anhydride to produce methacrylic anhydride.
3.4. Polymerization
Polymers of methacrylic acid and its derivatives are readily formed upon heating in the presence of free radical initiators like peroxides, UV light, or ionizing radiation.
Common phenolic inhibitors target peroxy radicals and do not inhibit the initiated polymerization process. However, oxygen exclusion is critical during polymerization to prevent the conversion of alkyl radicals to hydroperoxy radicals.
4. Industrial Production of Methacrylic Acid
This section focuses on commercially viable methods for producing methacrylic acid. Different feedstocks are used for these processes, categorized by their carbon chain length: ethylene (C2 route), propene or acetone (C3 route), and isobutene (C4 route).
The economic feasibility of each process depends on the regional availability and pricing of raw materials. Currently, no single alternative surpasses the established acetone cyanohydrin route in economic terms, justifying the continued operation of existing cyanohydrin-based plants.
4.1. Production of Methacrylic Acid by Acetone Cyanohydrin Route
The most common method for methacrylic acid synthesis involves the hydrolysis of methacrylamide sulfate, derived from acetone cyanohydrin.
Acetone cyanohydrin is formed by reacting dry acetone with hydrogen cyanide in the presence of a basic catalyst. This intermediate then reacts with excess concentrated sulfuric acid to yield methacrylamide sulfate.

The sulfuric acid serves a dual purpose: as a reactant and as the reaction solvent. Insufficient sulfuric acid results in a difficult-to-handle reaction mixture. Both the acid and acetone cyanohydrin must be anhydrous to minimize byproduct formation.
The initial reaction, carried out in a series of stirred tank reactors, necessitates good heat transfer to manage the exothermic process. Thorough mixing is crucial to prevent the cyanohydrin decomposition into its starting materials, which can form undesired byproducts.
Following the initial reaction (80–110 °C), the mixture undergoes brief thermal cracking (125–160 °C) to convert most of the a-hydroxyisobutyramide byproduct to the desired methacrylamide sulfate, along with some acetone, carbon monoxide, and water.
The second stage involves either hydrolyzing the methacrylamide sulfate stream with excess water to produce methacrylic acid and ammonium bisulfate, or treating it with aqueous methanol in a combined hydrolysis-esterification step to yield a mixture of methyl methacrylate and methacrylic acid.
The overall yield based on acetone cyanohydrin is typically within the 80–90% range.
For methacrylic acid production, the hydrolysis results in a two-phase mixture that allows for separate purification of methacrylic acid from the upper organic layer and dilute aqueous methacrylic acid from the lower layer via distillation and steam stripping, respectively.
The desire to eliminate sulfuric acid regeneration and the associated hazards of transporting hydrogen cyanide are key drivers for exploring alternative production methods.
However, the established acetone cyanohydrin route benefits from the economic advantage of using acetone (a byproduct of phenol production) and hydrogen cyanide (a byproduct of acrylonitrile production) as feedstocks.
4.2. Production of Methacrylic Acid from Isobutene
In recent years, companies like Nihon Methacryl Monomer (a Sumitomo and Nippon Shokubai joint venture) and Mitsubishi Rayon have developed a two-stage catalytic oxidation process to produce methacrylic acid from isobutene or tert-butanol.
The process involves the oxidation of isobutene to methacrolein, which is then further oxidized to methacrylic acid.
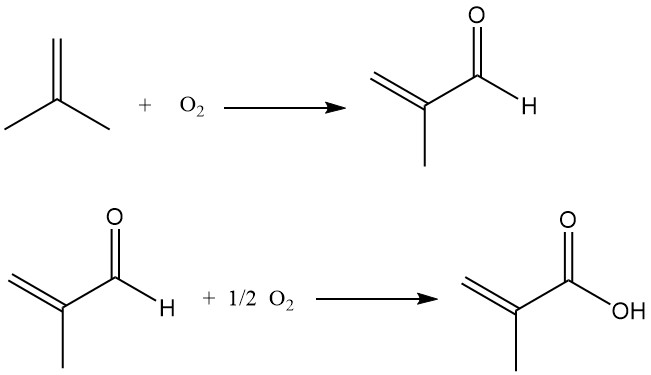
Published reports compare this process for methacrylic acid production from isobutene with a similar process for acrylic acid production from propene. The key challenge lies in maintaining high catalyst selectivity during the second oxidation stage, which typically performs best at moderate conversion rates (65–85%).
The Sumitomo-Nippon Shokubai process (Figure 1) overcomes this challenge by operating the first-stage reactor at high conversion and directly feeding its effluent to the second oxidation reactor. The second stage operates at a lower conversion rate to optimize catalyst selectivity and lifespan.
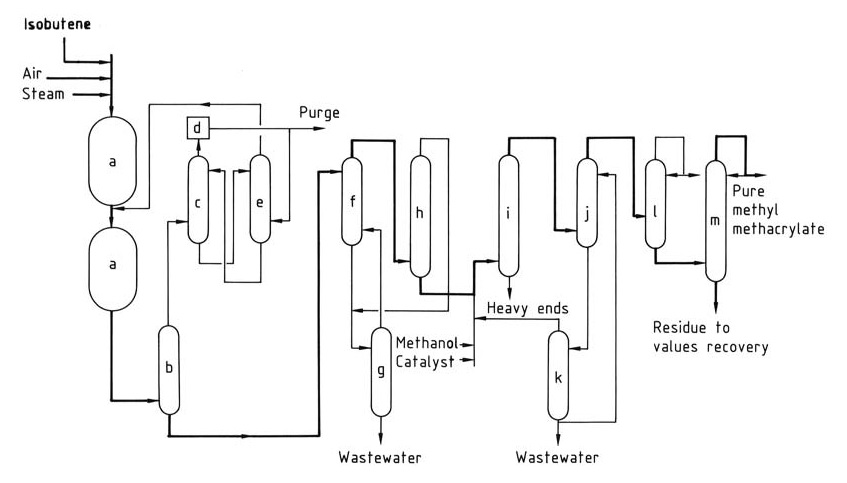
a) Oxidation reactors; b) Quencher; c) Absorber; d) Combustion unit; e) Methacrolein recovery tower; f) Solvent extraction unit; g) Solvent stripping tower; h) Solvent recovery/dehydration tower; i) Esterification reactor; j) Extractor; k) Distillation unit; l) Light ends stripper; m) Product distillation column.
Unreacted methacrolein from the second stage is then separated and recycled, achieving an overall yield of methacrylic acid from isobutene of around 65-70%.
Catalysts in the first oxidation are typically multicomponent metal oxides containing bismuth, molybdenum, and other metals to enhance activity and control selectivity. For the second oxidation, catalysts based on phosphomolybdic acid are used. Additional elements like copper and vanadium may also be present.
The second-stage oxidation reactor effluent is quenched (b) to obtain crude aqueous methacrylic acid. The remaining gaseous stream is passed through an absorber (c), where unreacted methacrolein is absorbed (usually using aqueous carboxylic acid).
Absorber off-gases are incinerated (d) before release. A portion of the incinerated gases can be recycled to the first stage as an inert diluent. The methacrolein-laden absorbent is transferred to a recovery tower (e) for recycling back to the second-stage reactor. The recovered absorbent solution is returned to the absorber.
Crude methacrylic acid undergoes solvent extraction (f) followed by dehydration in a solvent recovery/dehydration tower (h) to yield crude methacrylic acid as the bottom product.
The recycled organic solvent is returned to the extraction step, while the aqueous overhead is combined with the extractor raffinate and sent for solvent stripping (g) before wastewater treatment.
The dry, crude methacrylic acid can either be purified further or directly sent to an esterification reactor (i) with methanol and catalyst for conversion to methyl methacrylate.
Several companies, including Nippon Shokubai, Mitsubishi Rayon, Mitsui Toatsu, Kyowa Gas, Nippon Kayaku, Rohm and Haas, and Oxirane, have invested in the research, development, and commercialization of this process.
4.3. Production of Methacrylic Acid from Isobutyric Acid
An alternative method for the production of methacrylic acid is the acid-catalyzed carbonylation of propene to isobutyric acid, followed by oxidative dehydrogenation. Unlike the acetone cyanohydrin process, this process uses propene as the starting material.
While it is not yet commercially operational, several major methyl methacrylate producers are actively researching its commercialization potential.
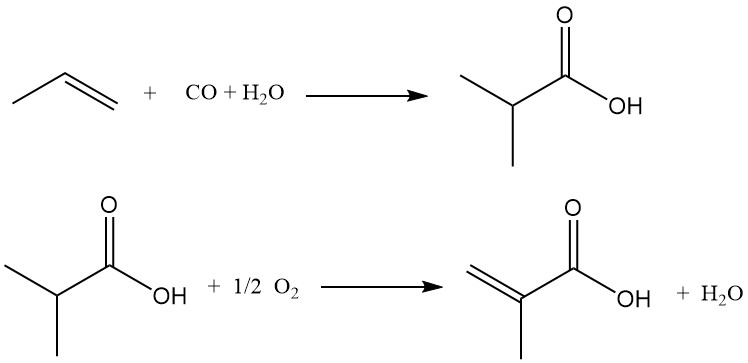
The first stage involves reacting propene, carbon monoxide, and water in the presence of a strong acid catalyst (sulfuric acid, hydrogen fluoride, or boron fluoride) to produce isobutyric acid. Controlled water addition during carbonylation allows for direct isobutyric acid synthesis.
Hydrogen fluoride can act as both a solvent and a catalyst in this process. The reaction proceeded from 30 °C at 20 MPa to 120 °C at 14 MPa, with a slight water deficiency relative to propene. Following the reaction, the product stream undergoes staged flash separation:
- Stage 1: Recovers excess carbon monoxide for recycling.
- Stage 2: Removes inert gases and any hydrogen fluoride or isopropyl fluoride through scrubbing with caustic solution.
Most of the hydrogen fluoride is then separated and recycled, with any remaining fluorine-containing materials in the bottom stream being hydrolyzed and the liberated hydrogen fluoride recycled.
A final distillation step purifies the isobutyric acid for the next stage. Byproducts from multiple propene condensations prior to carbonylation are present in the distillation bottoms, but the overall propene selectivity is reported to be 95–97%.
In the second stage, isobutyric acid, steam, and air are passed over a fixed-bed catalyst in a multitubular reactor, undergoing oxidative dehydrogenation to methacrylic acid.
The reactor effluent is quenched to obtain an aqueous methacrylic acid stream. This crude product contains byproducts like acetone and acetic acid, along with carbon monoxide, carbon dioxide, and noncondensable gases that are incinerated.
Methacrylic acid is isolated by solvent extraction and dehydration, followed by distillation. Isobutyric and acetic acids are then separated as light ends before final methacrylic acid distillation. Separating isobutyric acid from methacrylic acid is a challenge due to the close boiling points of the two acids.
Two main types of catalysts are used for isobutyric acid dehydrogenation to methacrylic acid:
- Mo-P-V mixed oxide catalysts developed by Mitsubishi Chemical Industries, R€ohm, and others. These phosphomolybdic acid derivatives, often achieve conversions of 99.8% with selectivities exceeding 74%.
- Iron phosphate catalysts by Ashland Oil. These catalysts offer selectivities of 84–85% at conversions of 85–95% but require operation at higher temperatures (400 °C) compared to phosphomolybdate catalysts.
4.4. Production of Methacrylic Acid from Ethylene
Beyond the dominant processes previously described, other alternative methods exist for methacrylic acid production. Methacrylic acid can be prepared by the condensation of formaldehyde with propionic acid or by the condensation of formaldehyde with propanal to form methacrolein, which is then oxidized to methacrylic acid.
BASF has commercialized a process based on the condensation of formaldehyde with propanal, using ethylene, synthesis gas, and formaldehyde as feedstocks. Their plant, which has been operational since 1990, has a production capacity of 40,000 metric tons per year.
In the BASF process, ethylene is hydroformylated to propanal, which undergoes condensation with formaldehyde to form methacrolein. Methacrolein is catalytically oxidized by air to methacrylic acid.
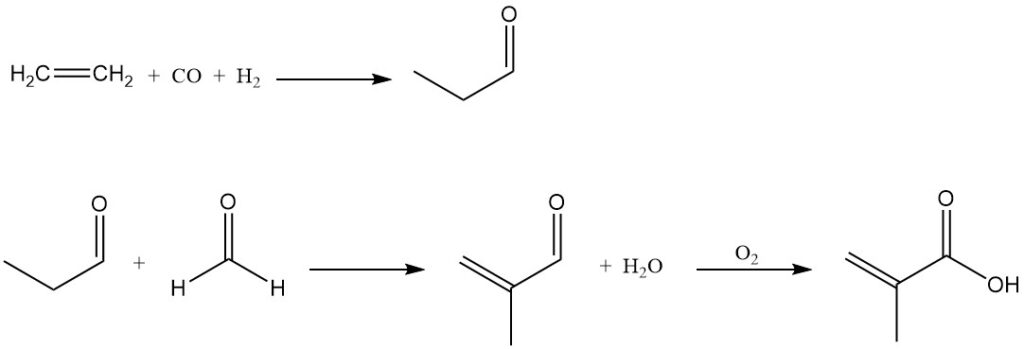
An alternative process is proposed that involves the oxidation of propanal to propionic acid, followed by its condensation with formaldehyde to directly produce methacrylic acid.
5. Uses of Methacrylic Acid
Methacrylic acid is used to prepare a wide range of polymers, including methacrylates, and to produce its esters. These polymers provide water-clear, tough plastics that are used in sheet form in glazing, signs, displays, and lighting panels.
By molding polymer pellets, automotive lighting lenses and similar products can be prepared.
Higher methacrylate polymers are used in the manufacture of oil additives, solventless inks and coatings, and binders for xerography.
Methacrylic acid is used in paints, adhesives, leather treatment agents, and as a raw material in the manufacture of ion-exchange resins.
Salts of poly(methacrylic acid) are used as additives in detergents and as water-soluble thickeners.
6. Toxicology of Methacrylic Acid
Methacrylic acid is considered slightly to moderately dangerous based on oral and dermal exposure studies in rats and rabbits.
Mucous membranes are highly sensitive to methacrylic acid. Exposure can cause irritation ranging from slight to corrosive, potentially leading to permanent eye damage or blindness. Full-eye protection is mandatory during handling.
Direct contact can cause skin redness and irritation, ranging from mild to severe, including potential corrosion. Methacrylic acid is more corrosive than its esters. Gloves and protective clothing are required.
Overexposure to methacrylic acid vapors can irritate the nose and throat, and may cause dizziness, drowsiness, or central nervous system depression.
Swallowing methacrylic acid can severely irritate the mouth, throat, esophagus, and stomach, causing discomfort, vomiting, diarrhea, dizziness, and potential collapse.
Repeated exposure to the skin can lead to allergic dermatitis (rash, itching, and swelling). Individuals may develop sensitivity after exposure, leading to reactions from subsequent exposures to the same or other acrylic monomers.
Studies on animals exposed to extremely high vapor concentrations of methacrylic acid have shown respiratory tract inflammation and degenerative changes in organs (liver, kidneys, and heart) at levels far exceeding irritation thresholds. No such effects have been reported in humans.
References
- Methacrylic Acid and Derivatives; Ullmann’s Encyclopedia of Industrial Chemistry. – https://onlinelibrary.wiley.com/doi/10.1002/14356007.a16_441.pub2
- https://www.m-chemical.co.jp/en/products/departments/mcc/mma_pmma/product/1201254_9386.html
- https://www.basf.com/global/documents/en/products-and-industries/acrylic-monomers/technical-information/TI_CP_1574_e_Methacrylic_acid_technical_190419_SCREEN_02.pdf