Le caprolactame, l’ingrédient clé du nylon-6, peut être produit par plusieurs voies. La méthode la plus courante est la conversion de la cyclohexanone en oxime de cyclohexanone par des procédés d’ammoximation ou de peroxyde d’hydrogène. Cette oxime subit ensuite un réarrangement de Beckmann pour former du caprolactame.
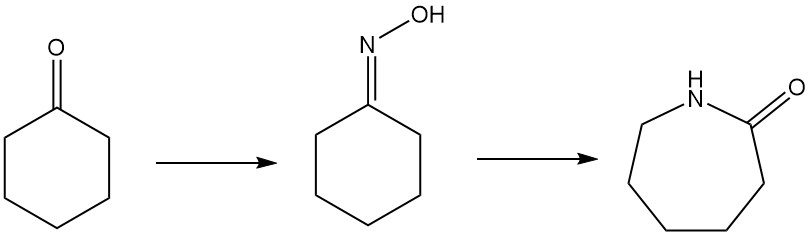
D’autres procédés incluent la production par photooximation et par voie à base de toluène ou sont récupérés à partir de déchets de nylon-6. Des procédés innovants émergent, notamment la voie ALTAM utilisant des méthodes à base de butadiène ou d’adiponitrile dérivées de ressources renouvelables comme le furfural ou la biomasse.
Les usines modernes de caprolactame sont des opérations complexes à plusieurs étapes, avec des capacités actuelles d’une seule ligne atteignant le chiffre impressionnant de 200 000 tonnes par an pour la technologie Fibrant HPO, largement autorisée.
Bien que la cyclohexanone domine comme matière première (> 98 %), le cyclohexane et le toluène peuvent également être utilisés. Notamment, l’hydrogénation du phénol et diverses voies d’oxydation du cyclohexane sont utilisées pour obtenir l’intermédiaire clé. L’efficacité combinée de la conversion de la cyclohexanone en caprolactame est d’environ 98 %.
Table of Contents
1. Production de caprolactame via le procédé cyclohexanone
La production moderne de caprolactame repose sur le benzène extrait des flux de BTX comme matière première principale. Tous les procédés commerciaux sauf un utilisent l’oxime de cyclohexanone comme intermédiaire. Cette oxime est formée par la réaction de la cyclohexanone avec l’hydroxylamine, générée par diverses méthodes telles que :
- Processus Raschig
- NO hydrogénation dans le processus à l’acide sulfurique
- Procédé Fibrant HPO
- Processus d’ammoximation
1.1. Cyclohexanone Oxime par Raschig Process
Dans ce processus, l’oxime de cyclohexanone est produite par la réaction de la cyclohexanone et du sulfate d’hydroxylamine, et l’ammoniac est utilisé pour neutraliser le sel d’oxime. Le sulfate d’ammonium est produit comme sous-produit de cette réaction.
Plusieurs améliorations, connues sous le nom de procédés Raschig, ont été mises en œuvre pour améliorer le rendement en oxime de cyclohexanone et minimiser la production de sels de sulfate. Les procédés Raschig modifiés, les seuls encore en activité, génèrent exclusivement du sulfate d’ammonium comme sous-produit.
Dans le procédé Raschig modifié, les matières premières (ammoniac, CO2, SO2, eau et air) réagissent d’abord pour former du sulfate d’hydroxylamine via l’équation (1 ). Ensuite, le sulfate d’hydroxylamine réagit avec la cyclohexanone pour produire de l’oxime de cyclohexanone (Équation (2)).
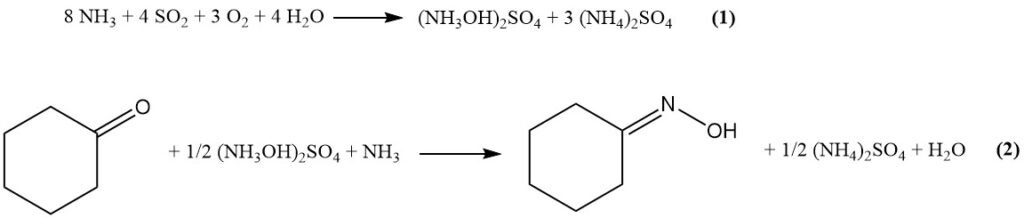
Les principales étapes du processus impliquées sont répertoriées ci-dessous :
L’ammoniac absorbe le CO2 présent dans l’eau pour former une solution de carbonate/bicarbonate d’ammonium.
L’ammoniac brûle avec l’air (catalyseurs Pt/Rh) à ~850°C pour générer du NOx et de l’eau. Les gaz chauds sont refroidis, récupérant la chaleur d’oxydation exothermique et condensant le sous-produit dilué de l’acide nitrique.
Le mélange gazeux nitreux et la solution de carbonate/bicarbonate d’ammonium réagissent à <10°C et à pH 15 pour former du nitrite d’ammonium.
La combustion du soufre produit du SO2 (10 à 20 % en volume) avec récupération de chaleur pour la génération de vapeur.
- Le SO2 réagit avec un mélange aqueux de nitrite d’ammonium et d’hydroxyde d’ammonium pour former de l’acide hydroxyimidodisulfurique. La température et le rapport NH4OH/NH4NO2 sont des paramètres importants pour minimiser les sous-produits.
L’acide hydroxyimidodisulfurique subit une hydrolyse et une neutralisation pour former du sulfate d’hydroxylamine via le N-hydroxysulfamate d’ammonium.
L’oximation de la cyclohexanone avec du sulfate d’hydroxylamine à un pH de 4,5 et entre 50 et 100 °C donne de l’oxime de cyclohexanone.
L’ammoniac aqueux neutralise l’acide sulfurique libéré et le sulfate d’ammonium coproduit est récupéré par cristallisation par évaporation.
Les autres sous-produits du procédé Raschig sont les gaz nitreux présents dans les gaz résiduaires de formation de nitrite, l’azote gazeux provenant de la décomposition du nitrite d’ammonium et le gaz N2O provenant de diverses réactions de décomposition.
1.2. NO hydrogénation dans le processus d’acide sulfurique
Pour minimiser la coproduction de sulfate d’ammonium, BASF, Cyclopol et Inventa développé des procédés de réduction catalytique du NO avec de l’hydrogène en sulfate d’hydroxylamine dans de l’acide sulfurique dilué. Le NO lui-même est généré par oxydation catalytique de l’ammoniac avec de l’oxygène pur et de la vapeur.
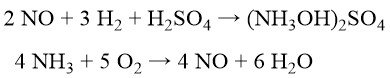
La production ultérieure d’oxime est similaire au processus Raschig (équation (2)). Cette voie, avec la neutralisation de l’excès de H2SO4, génère encore ~0,7 kg de sulfate d’ammonium par kg d’oxime de cyclohexanone. Les risques d’explosion sont atténués par la composition contrôlée du gaz lors de la synthèse du sulfate d’hydroxylamine. Une purification approfondie des matières premières et des traitements complexes du catalyseur sont nécessaires.
Un mélange d’ammoniac d’environ 14 %, d’un rapport O2/NH3 d’environ 1,34 et de vapeur passe sur un catalyseur Pt/Rh à environ 850 °C pour former principalement du NO et d’autres oxydes d’azote. Le gaz chaud se refroidit dans une chaudière à chaleur résiduelle (générant de la vapeur), puis refroidit davantage pour condenser l’eau et diluer l’acide nitrique.
Le NO2 restant est éliminé dans des tours consécutives avec de l’acide nitrique dilué et une solution de soude caustique, atteignant une pureté d’environ 95 %.
La synthèse de l’hydroxylamine comprend plusieurs lignes de 5 à 7 réacteurs bien agités de 20 m3 fonctionnant en continu. Chaque réacteur reçoit une solution d’acide sulfurique purifié à 20 % en poids avec environ 35 g/L de catalyseur Pt-graphite finement dispersé (~ 0,5 % en poids). Tous les réacteurs reçoivent du NO purifié et de l’hydrogène en excès. La température de réaction est d’environ 45°C.
Bien que la pression atmosphérique soit utilisée, une pression élevée peut être avantageuse. Une solution de sulfate d’hydroxylamine d’environ 25 % en poids contenant le catalyseur sort du dernier réacteur et subit une filtration. La suspension concentrée de catalyseur est recyclée dans le premier réacteur.
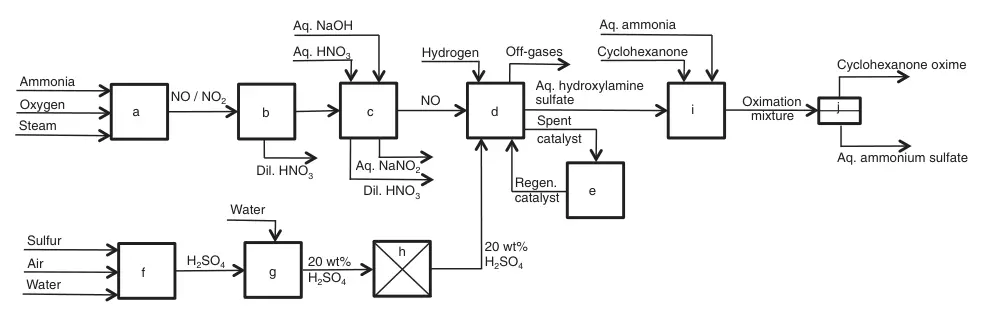
a) Combustion d'ammoniac ; b)Condensations ; c) PAS de lavage ; d) AUCUNE réduction ; e) Régénération du catalyseur ; f) Combustion du soufre ; g) Dilution ; h) Purification ; i) oximation de la cyclohexanone ; j) Séparation oxime de cyclohexanone/sulfate d'ammonium aqueux
Les mélanges réactionnels extrêmement corrosifs et la sensibilité du catalyseur nécessitent une sélection minutieuse des matériaux. Inventa a proposé des revêtements en caoutchouc/résine synthétique et BASF a suggéré des types d’acier spéciaux sans cuivre.
La solution de sulfate d’hydroxylamine produite réagit avec la cyclohexanone à une température (85-90 °C) dépassant le point de fusion de l’oxime de la cyclohexanone aqueuse. La phase aqueuse de sulfate d’ammonium résultante se sépare de la phase organique contenant de l’eau à environ 7 % en poids, et les deux sont traitées séparément.
L’oxime de cyclohexanone est extraite de la phase de sulfate d’ammonium avec de la cyclohexanone, récupérée ensuite par distillation. La cristallisation par évaporation de la solution restante donne environ 0,7 kg de sulfate d’ammonium cristallin par kg d’oxime de cyclohexanone. Après séchage partiel, l’oxime contenant de l’eau est prête pour le réarrangement de Beckmann pour produire du caprolactame.
1.3. Processus Fibrant HPO®
Développé par Fibrant dans les années 1960, le procédé HPO (hydroxylamine phosphate oxime) offre une approche unique de la production d’oxime de cyclohexanone basée sur du nitrate sélectif. hydrogénation des ions/oxydes d’azote.
Cette voie de synthèse combinée d’hydroxylamine et d’oxime élimine le sous-produit sulfate d’ammonium. Le procédé HPO permet une boucle fermée entre les synthèses d’hydroxylamine et d’oxime en évitant la libération d’acide sulfurique lors de la formation d’oxime.
Il s’articule autour du recyclage de deux flux : un tampon d’acide phosphorique aqueux et une phase de traitement organique. Plusieurs réactions et opérations clés se produisent au sein de ce système.

L’hydrogénation catalytique sélective des ions nitrate avec de l’hydrogène gazeux dans la solution tampon d’acide phosphorique génère de l’hydroxylamine. Au pH de la réaction ~ 2, l’hydroxylamine résultante devient protonée, formant du phosphate d’hydroxylammonium. Le Pd/Pt supporté sur du carbone ou de l’alumine est utilisé comme catalyseur.
Un système unique de réacteur à colonne à bulles triphasé combine un contact gaz-liquide-solide optimal avec une évacuation efficace de la chaleur. L’hydrogène n’ayant pas réagi est recyclé après séparation de la suspension de catalyseur. La solution tampon d’acide phosphorique hydroxylammonium passe à la section d’oximation.
Le tampon aqueux hydroxylamine-acide phosphorique réagit avec une phase organique toluène-cyclohexanone convertit la cyclohexanone en oxime de cyclohexanone et libère de l’acide phosphorique. Cette étape d’oximation fonctionne à pH ~ 2, permettant des conversions quasi quantitatives de l’hydroxylamine et de la cyclohexanone.
La phase organique formée (cyclohexanone oxime-toluène) est séparée du tampon aqueux, lavée à l’eau, puis le toluène est distillé. L’oxime sèche est déplacée vers la section de réarrangement Beckmann, tandis que le toluène distillé est recyclé vers le réacteur d’oximation.
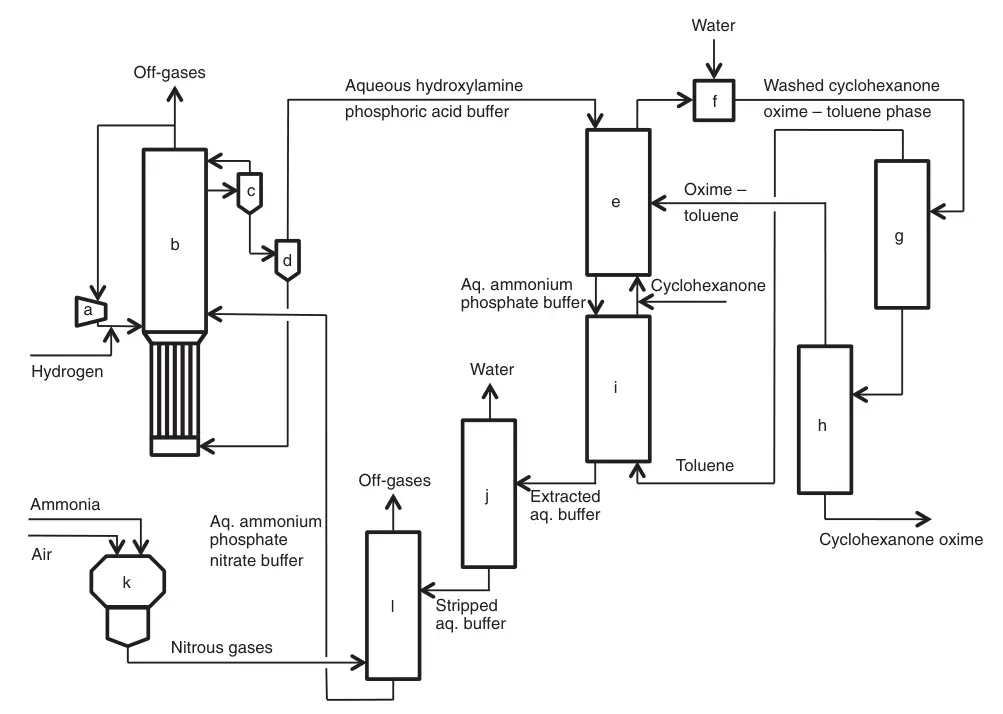
a) Compresseur ; b) Réacteur d'hydrogénation des nitrates ; c) Séparateur gaz-liquide ; d) Filtration catalytique ; e) Oxymation ; f) Lavage ; g) distillation du toluène ; h) purification de l'oxime de cyclohexanone ; i) Extraction ; j) Décapage à la vapeur ; k) Combustion d'ammoniac ; l) Décomposition de l'ammoniac et absorption des gaz nitreux
Le développement continu du processus HPO a conduit au processus HPOplus intensifié, caractérisé par des flux de processus concentrés, une consommation réduite de matières premières/d’énergie et une capacité d’oxime sur une seule ligne considérablement augmentée (> 200 000 t/a).
1.4. Processus d’ammoximation
La réaction de la cyclohexanone avec l’ammoniac et le peroxyde d’hydrogène offre une voie alternative à la synthèse de l’oxime de la cyclohexanone en phase liquide sans générer de sous-produit de sulfate d’ammonium.

Le succès initial de cette approche est survenu en 1960 avec l’utilisation de catalyseurs au tungstène et à l’étain dans de l’ammoniac aqueux à une température de 10 à 30 °C, permettant d’obtenir des rendements d’oxime élevés (> 90 %). Cependant, les problèmes d’extraction et de récupération du catalyseur ont entravé la commercialisation.
À la fin des années 1970, un matériau synthétique poreux (la silicalite de titane (TS-1)) a été développé, conduisant à de nouveaux procédés d’oxydation catalytique. En 1987, Montedipe a mis en œuvre le TS-1 pour l’ammoximation au cyclohexanone, suivi par des processus similaires de Sinopec.
L’ammoniac réagit avec le peroxyde d’hydrogène sur les centres de titane du catalyseur, formant l’hydroxylamine intermédiaire, qui réagit ensuite avec la cyclohexanone pour donner l’oxime souhaitée.
Le rapport molaire d’alimentation H2O2/cyclohexanone est de 1,0 à 1,1 et il s’agit d’un alcool tertiaire stable (par exemple, alcool tert-butylique) à raison de 2 à 4 fois le poids de la cyclohexanone est utilisé comme solvant.
La réaction est opérée à une température d’environ 85 °C et une pression supérieure à 0,25 MPa pendant environ 1,5 h pour obtenir une conversion de cyclohexanone en oxime jusqu’à 98 %.
La première usine commerciale basée sur cette technologie a été construite par Sumitomo Chemical en 2003. Plusieurs usines chinoises de caprolactame utilisent cette technologie, certaines avec des variantes TS-1.
Une description simplifiée du processus est présentée dans la Figure 3 :
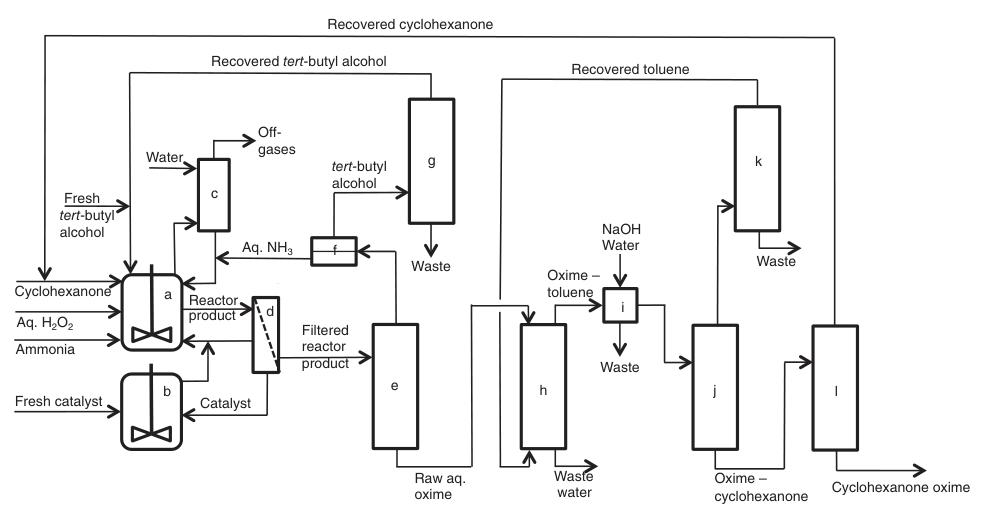
a) Réacteurs d'ammoximation ; b) Préparation/purification du catalyseur ; c) épuration des gaz dégagés ; d) Filtration ; e) Récupération d'ammoniac/alcool tert-butylique ; f) séparation L/L ; g) distillation de l'alcool tert-butylique ; h) Extraction ; i) Lavage ; j) Récupération de solvant ; k) Distillation du solvant ; l) Récupération de cyclohexanone
Le processus commence par un flux continu de matière première contenant du peroxyde d’hydrogène dilué, de la cyclohexanone, de l’ammoniac, de l’alcool tert-butylique (frais et recyclé) et un catalyseur (frais ou recyclé) entrant dans les réacteurs d’ammoximation agités.
Les gaz d’échappement générés au cours de cette étape, qui contiennent de l’ammoniac n’ayant pas réagi, sont lavés avec de l’eau pour récupérer et recycler l’ammoniac.
Le mélange de produits résultant subit ensuite une filtration et est envoyé vers une colonne de récupération pour séparation et purification. À ce stade, deux voies alternatives peuvent être utilisées :
1. Extraction avec toluène :
L’ammoniac n’ayant pas réagi et l’alcool tert-butylique contenant de l’eau sont récupérés et purifiés pour être réutilisés. L’oxime de cyclohexanone et la cyclohexanone n’ayant pas réagi sont extraites à l’aide de toluène, suivies d’un lavage à l’eau et d’une séparation supplémentaire par distillation.
2. Réextraction à contre-courant :
Une étape continue de réextraction à contre-courant utilise de l’eau déminéralisée pour former des phases aqueuses séparées d’oxime et de cyclohexanone. Ces phases sont ensuite soumises à une purification supplémentaire par distillation.
1.5. Réarrangement Beckmann de la cyclohexanone oxime en caprolactame
Le caprolactame, un précurseur clé du nylon-6, est principalement produit à partir de l’oxime de cyclohexanone via le réarrangement de Beckmann. Cette réaction hautement exothermique se produit à la fois en phase liquide et gazeuse.
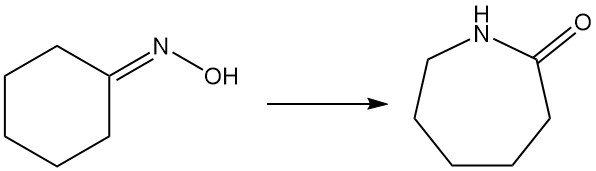
La conversion de l’oxime en caprolactame implique le réarrangement traditionnel de Beckmann en phase liquide avec de l’acide sulfurique fumant, générant du sulfate d’ammonium comme coproduit. Sumitomo Chemical, cependant, utilise un processus unique de réarrangement de Beckmann en phase vapeur.
Un prix déprimé du sulfate d’ammonium rend sa coproduction indésirable, motivant le développement de procédés le minimisant ou l’éliminant. Cependant, le sulfate d’ammonium peut également bénéficier à la production de caprolactame lorsqu’il est utilisé comme engrais dans des conditions de sol spécifiques, en fournissant de l’azote, du soufre et un ajustement du pH.
1.5.1. Réarrangement de Beckmann en phase liquide
La méthode industrielle dominante utilise de l’acide sulfurique ou de l’oléum fumant comme catalyseur et solvant. Il atteint une conversion élevée en oxime et le rendement en caprolactame est de près de 100 %, mais il génère du sulfate d’ammonium comme sous-produit.
Les paramètres de réaction tels que la température, la concentration d’acide et le mélange ont un impact significatif sur la pureté et la couleur du produit. Un réarrangement en plusieurs étapes avec une alimentation en oléum distribuée réduit la production de sulfate d’ammonium.
La purification finale du caprolactame implique l’extraction par solvant, la distillation et le lavage.
1.5.2. Réarrangement en phase gazeuse (réarrangement catalytique hétérogène)
Le réarrangement en phase gazeuse a été développé pour éviter la génération de sulfate d’ammonium associée aux méthodes en phase liquide. Les premières tentatives utilisant des catalyseurs d’élimination de l’eau se sont heurtées à une faible sélectivité et à une désactivation du catalyseur.
Sumitomo Chemical a obtenu un succès industriel avec des zéolites à haute teneur en silice en présence d’eau et de méthanol.
Ce processus implique l’évaporation d’un mélange humide oxime/méthanol. L’oxime est ensuite convertie en caprolactame sur un catalyseur zéolitique MFI à 350-380°C. Le catalyseur est régénéré en continu avec de l’air à 500°C dans un système à lit fluidisé.
Les impuretés du caprolactame résultant sont éliminées par distillation. Une purification plus poussée du caprolactame par cristallisation à partir d’un solvant mixte et via hydrogénation et distillation en plusieurs étapes donne un produit très pur.
Sumitomo Chemical est le seul producteur commercial utilisant le réarrangement en phase gazeuse sans générer de sulfate d’ammonium.
2. Production de caprolactame par photooximation
Dans les années 1950, Toray a développé un procédé photochimique unique pour produire du caprolactame. Cette méthodologie, appelée photonitrosation (PNC), contourne la synthèse conventionnelle d’oxime par conversion directe du cyclohexane en dichlorhydrate de cyclohexanone oxime, suivie d’un réarrangement ultérieur de Beckmann en caprolactame.
Le cyclohexane réagit avec le chlorure de nitrosyle pour donner le chlorhydrate de cyclohexanone oxime, en suivant les réactions ci-dessous :
1. Formation d’acide nitrosylsulfurique : Les gaz nitreux obtenus à partir de la combustion de l’ammoniac réagissent avec l’acide sulfurique pour produire de l’acide nitrosylsulfurique (NOHSO4).
2 H2SO4 + NON + NO2 → 2 NOHSO4 + H2O
2. Production de NOCl : NOHSO4 réagit avec le chlorure d’hydrogène (HCl) pour produire du NOCl, avec régénération simultanée de l’acide sulfurique.
NOHSO4 + HCl → NOCl + H2SO4
3. Conversion photochimique :

Le procédé PNC est basé sur la réaction photochimique du cyclohexane avec NOCl en présence d’un excès de HCl. Cette transformation est facilitée par des lampes LED haute performance émettant de la lumière actinique et conduit à la formation sélective de dichlorhydrate de cyclohexanone oxime sous forme de couche inférieure huileuse.
Notamment, les lampes LED offrent une efficacité énergétique supérieure (0,4 kg d’oxime par kWh) et une sélectivité molaire (86 %) par rapport aux précédentes alternatives de lampes au mercure.
Le dichlorhydrate d’oxime récupéré subit un réarrangement de Beckmann en utilisant de l’oléum, donnant du caprolactame. Le cyclohexane n’ayant pas réagi est recyclé, tandis que le chlorure d’hydrogène dégagé est récupéré par un processus aqueux d’absorption et de concentration.
La solution brute de caprolactame est neutralisée avec de l’ammoniac et soumise à une purification supplémentaire via un traitement chimique, un séchage et une distillation. Ce procédé génère 1,55 tonne de sulfate d’ammonium par tonne de caprolactame.
3. Récupération du caprolactame à partir des déchets de nylon-6
Les déchets de nylon 6, générés tout au long de leur cycle de vie, depuis la production jusqu’à l’élimination du produit final, présentent une opportunité de valorisation des ressources. Les processus de dépolymérisation récupèrent le précieux caprolactame de ces flux de déchets, offrant ainsi des avantages à la fois environnementaux et économiques.
Les déchets solides de nylon-6 sont dépolymérisés en caprolactame dans un réacteur à bouilloire à haute pression en utilisant de la vapeur surchauffée avec un catalyseur de craquage (généralement de l’acide phosphorique). Cette conversion peut également se produire sans catalyseur sous une pression de vapeur élevée.
Le mélange vapeur-caprolactame résultant subit une condensation et une concentration partielles. Ensuite, un agent oxydant purifie le concentré, suivi d’une purification finale du caprolactame par distillation.
Les eaux de lavage provenant de la production de copeaux de nylon 6 contiennent des oligomères de caprolactame aux côtés du monomère. La préconcentration via évaporation en couche mince précède la dépolymérisation en utilisant la même méthodologie que les déchets solides.
La solution aqueuse de caprolactame résultante subit une purification chimique et une distillation pour produire de l’eau, des fractions à bas point d’ébullition et le produit de caprolactame souhaité.
Des méthodes alternatives abordent également la dépolymérisation des oligomères. Une approche consiste à concentrer l’eau de lavage pour maintenir la solubilité des oligomères et à introduire la solution caprolactame-oligomère dans un réacteur à lit fixe ou à lit fluidisé.
Un catalyseur spécialisé à l’oxyde d’aluminium craque les oligomères à 275-350 °C, atteignant un rendement de 95 % par rapport à la charge d’alimentation. Les méthodes de purification conventionnelles récupèrent ensuite le caprolactame.
Plusieurs technologies établies traitent les déchets de nylon-6 post-consommation, en particulier les tapis mis au rebut. Ces processus nécessitent la collecte, le tri et le déchiquetage mécanique avant la dépolymérisation en caprolactame de qualité vierge.
Des exemples notables incluent le programme « 6ix Again » de BASF, qui utilise un réacteur semi-continu avec de l’acide phosphorique et de la vapeur surchauffée pour une dépolymérisation à haute température (250-300°C). Une purification ultérieure avec un agent oxydant et une distillation sous vide récupèrent le caprolactame du distillat.
Un autre procédé est le recyclage du nylon Evergreen, qui est une méthode de dépolymérisation non catalysée en deux étapes qui utilise un système de réacteur à haute pression et de la vapeur surchauffée pour hydrolyser les matériaux déchiquetés. Il récupère 90 à 95 % du nylon-6 initial sous forme de caprolactame, adapté à la production de tapis.
4. Processus à base de toluène
Développé par Snia Viscosa en 1960 et utilisé en Italie jusqu’au début des années 1990, ce procédé à base de toluène offre une voie alternative à la production de caprolactame. Le processus comprend trois étapes clés :
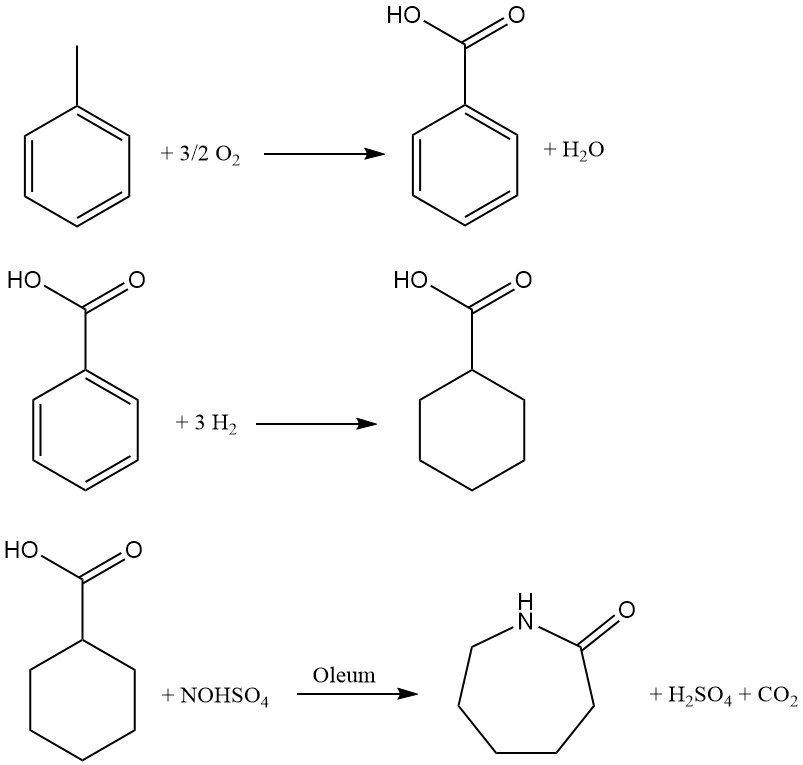
1. Oxydation catalytique : Le toluène subit une oxydation à l’air en phase liquide à l’aide d’un catalyseur au cobalt à 160-170°C et sous une pression de 0,8-1 MPa. La récupération du toluène n’ayant pas réagi par refroidissement garantit un rendement optimal.
Le produit liquide résultant, contenant environ 30 % d’acide benzoïque ainsi que des intermédiaires et des sous-produits, nécessite une distillation en plusieurs étapes pour la purification.
2. Hydrogénation : L’acide benzoïque est converti en acide cyclohexanecarboxylique par hydrogénation en phase liquide à l’aide d’un catalyseur Pd/C. Une série de réacteurs agités fonctionnant à environ 170°C et à une pression de 1 à 1,7 MPa facilitent une transformation efficace. Une distillation ultérieure sous pression réduite purifie l’acide résultant.
3. Nitrosodecarboxylation et réarrangement : Cette étape cruciale combine la nitrosation de l’acide cyclohexanecarboxylique avec le réarrangement de Beckmann pour générer directement du caprolactame. Une solution d’acide nitrosylsulfurique à 73 % dans l’acide sulfurique, préparée par absorption conventionnelle de NO dans l’oléum, est utilisée dans la réaction dans un réacteur à plusieurs étages.
Le maintien du taux de conversion autour de 50 % nécessite que le processus se déroule dans du cyclohexane bouillant sous pression atmosphérique. Les acides sulfoniques se forment comme sous-produits inévitables.
Suite au réarrangement-nitrosation combiné, le flux de produit subit une hydrolyse avec de l’eau à basse température. L’extraction de l’acide cyclohexanecarboxylique n’ayant pas réagi permet son recyclage dans le processus.
La solution acide de caprolactame, contenant un excès d’acide sulfurique, passe ensuite à l’étape de neutralisation. La cristallisation sous pression réduite avec de l’ammoniac donne deux couches liquides distinctes : une solution de sulfate d’ammonium et une solution aqueuse de caprolactame. Une purification plus poussée implique :
- L’extraction au toluène sépare le caprolactame des sous-produits solubles dans l’eau.
- L’extraction à contre-courant avec de l’eau récupère le caprolactame de la solution toluénique.
- La distillation donne du caprolactame pur à partir de la solution aqueuse concentrée.
5. Processus alternatifs
Au-delà du processus conventionnel d’ammoximation au cyclohexanone, plusieurs voies alternatives au caprolactame ont émergé :
5.1. Processus au peroxyde d’hydrogène
- Procédé Inventa : L’oxydation de la cyclohexylamine avec du peroxyde d’hydrogène génère de l’oxime de cyclohexanone.
- Procédé 1,1´-Peroxydicyclohexylamine : La cyclohexanone et le peroxyde d’hydrogène réagissent pour former un peroxyde, qui se transforme ensuite en caprolactame et régénère la cyclohexanone.
5.2. Oxydation de la cyclohexylamine avec l’oxygène élémentaire :
L’oxydation directe de la cyclohexylamine avec de l’oxygène produit de l’oxime de cyclohexanone.
5.3. Oxymation directe de la cyclohexanone :
L’ammoniac, l’air et la cyclohexanone réagissent directement sur divers catalyseurs pour former de l’oxime de cyclohexanone.
5.4. Processus Bis(nitrosocyclohexane) :
La décharge électrique déclenche la réaction du cyclohexane avec l’oxyde nitrique ou des composés apparentés, formant du bis (nitrosocyclohexane), qui se réorganise en oxime de cyclohexanone.
5.5. Procédé acide ε-hydroxycaproïque/ε-caprolactone :
L’oxydation de la cyclohexanone avec l’air génère de l’acide ε-hydroxycaproïque et de l’acide adipique (sous-produit). Les deux peuvent être convertis en caprolactame par différentes voies.
5.6. Procédé 2-Nitrocyclohexanone :
Une séquence unique de réactions impliquant l’acétylation, la nitration, le clivage du cycle, l’hydrogénation et la cyclisation convertit la cyclohexanone en caprolactame sans sous-produits. .
5.7. Procédé 3,3-pentaméthylèneoxaziridine :
L’hypochlorite réagit avec la cyclohexanone dans l’ammoniaque pour former de l’isoxime de cyclohexanone, qui se réorganise ensuite en caprolactame sous l’effet de la chaleur.
5.8. Désacétylation catalytique du N-acétylcaprolactame :
L’O-acétylcyclohexanone oxime subit une désacétylation sur des catalyseurs pour donner du caprolactame.
5.9. Processus basés sur le butadiène :
- Procédé ALTAM : développé par DSM et d’autres, ce processus en plusieurs étapes utilise du butadiène pour finalement produire du caprolactame avec une sélectivité élevée.
- Procédés à base d’adiponitrile : BASF et Rhône-Poulenc ont développé des procédés indépendants pour la production de caprolactame à partir d’adiponitrile, obtenu à partir de diverses voies, dont le butadiène.
5.10. Itinéraires biorenouvelables :
Avec les préoccupations croissantes en matière de durabilité, les ressources biologiques gagnent du terrain en tant que matières premières pour la production de caprolactame. Plusieurs itinéraires prometteurs sont en cours de développement, axés sur :
- Produits chimiques à ajouter : benzène d’origine biologique, phénol, acrylonitrile, ou HMF, peut être facilement intégré dans les processus de caprolactame existants.
- Voies chimiques : Acide lévulinique ou furfural, obtenu à partir de la biomasse, peut être converti en intermédiaires menant au caprolactame.
- Voies fermentaires (partiellement) : Synthèse microbienne de lysine ou directe fermentation des glucides offrent des voies potentielles vers les précurseurs du caprolactame.
Bien qu’ils ne soient actuellement pas économiquement compétitifs par rapport aux méthodes traditionnelles, les processus biorenouvelables sont prometteurs pour une future production durable de caprolactame.
Référence
- Caprolactam; Ullmann’s Encyclopedia of Industrial Chemistry. – https://onlinelibrary.wiley.com/doi/10.1002/14356007.a05_031.pub3