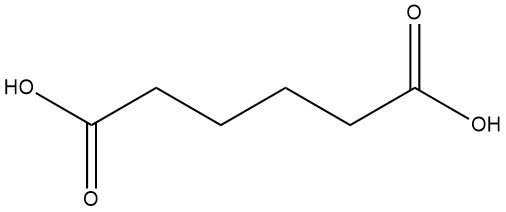
L’acide adipique, également appelé acide hexanedioïque ou acide 1,4-butanedicarboxylique, a la formule chimique C6H10O4 et une masse molaire de 146,14 g/mol. Il revêt une importance significative en tant qu’acide dicarboxylique aliphatique largement utilisé.
Bien que sa présence dans la nature soit limitée, elle est globalement synthétisée à grande échelle. L’application principale de ce composé est dans la production de polyamide nylon 66 qui a été découvert par W. H. Carothers de DuPont au début des années 1930.
Depuis lors, la fabrication de la fibre polyamide nylon 66 est devenue un processus dominant dans l’industrie des fibres synthétiques à l’échelle mondiale.
Table des matières
1. Propriétés physiques de l’acide adipique
L’acide adipique est obtenu sous forme de cristaux incolores et inodores au goût acide caractéristique. Il démontre une solubilité élevée dans le méthanol et l’éthanol, et il est également soluble dans l’eau et l’acétone.
Cependant, sa solubilité dans le cyclohexane et le benzène est assez limitée. Une fois cristallisé, l’acide adipique forme des prismes monocliniques lors de l’utilisation d’eau, d’acétate d’éthyle ou d’acétone/éther de pétrole comme solvants.
Voici quelques-unes de ses propriétés physiques :
Propriété | Valeur |
---|---|
mp, °C | 152.1 |
pb, °C à 101,3 kPa | 337,5 |
pb, °C à 13,3 kPa | 265 |
pb, °C à 2,67 kPa | 222 |
pb, °C à 0,67 kPa | 191 |
pb, °C à 0,133 kPa | 159,5 |
Densité relative (170 °C) | 1.085 |
Densité apparente, kg/m³ | 600 - 700 |
Solubilité, g/100 g d'eau à 15 °C | 1.42 |
Solubilité, g/100 g d'eau à 40 °C | 4.5 |
Solubilité, g/100 g d'eau à 60 °C | 18.2 |
Solubilité, g/100 g d'eau à 80 °C | 73 |
Solubilité, g/100 g d'eau à 100 °C | 290 |
Constantes de dissociation k1 | 4,6 × 10-5 |
Constantes de dissociation k2 | 3,6 × 10-6 |
Chaleur spécifique du liquide (200 °C), kJ kg⁻¹ K⁻¹ | 2.719 |
Chaleur spécifique de la vapeur (300 °C), kJ kg⁻¹ K⁻¹ | 1.680 |
Chaleur de fusion, kJ/kg | 115 |
Chaleur de vaporisation, kJ/kg | 549 |
Chaleur de la solution dans l'eau, kJ/kg à 10 - 20 °C | -214 |
Chaleur de la solution dans l'eau, kJ/kg à 90 - 100 °C | -241 |
Viscosité à l'état fondu, mPa · s à 160 °C | 4.54 |
Viscosité à l'état fondu, mPa · s à 193 °C | 2.64 |
2. Réactions chimiques de l’acide adipique
L’acide adipique présente une stabilité dans les conditions atmosphériques, mais lors du chauffage de l’acide fondu au-delà de 230 à 250 ° C, un certain degré de décarboxylation se produit, conduisant à la formation de cyclopentanone, avec un point d’ébullition de 131 ° C.
Cette réaction est notamment catalysée par des sels métalliques, dont le fer, le calcium et le baryum.
Par rapport aux acides glutarique ou succinique, l’acide adipique présente une tendance bien moindre à former des anhydrides cycliques par perte d’eau.
L’acide adipique présente une réactivité au niveau d’un ou des deux groupes d’acide carboxylique, s’engageant dans la formation de sels, d’esters, d’amides, de nitriles et d’autres composés.
Il résiste généralement à l’action de la plupart des agents oxydants, comme en témoigne sa production dans l’acide nitrique, mais lorsqu’il est exposé à l’acide nitrique au-dessus de 180 ° C, l’acide adipique subit une attaque autocatalytique, produisant du dioxyde de carbone, de l’eau et des oxydes d’azote.
3. Fabrication de l’acide adipique
Dans les premières étapes de la production commerciale d’acide adipique, un processus en deux étapes impliquait l’oxydation à l’air du cyclohexane. La première étape était l’oxydation du cyclohexane en cyclohexanol et cyclohexanone à faible conversion, suivie d’un processus de conversion élevée qui oxydait à l’air le mélange pour donner de l’acide adipique.
Cependant, depuis l’an 2000, toute la fabrication à grande échelle d’acide adipique utilise l’oxydation à l’acide nitrique du cyclohexanol, de la cyclohexanone ou d’un mélange des deux substances connu sous le nom d’huile cétone-alcool (KA).
Les principales différences entre ces procédés commerciaux résident dans la méthode de production de l’huile KA. Typiquement, les six atomes de carbone formant le squelette de l’acide adipique proviennent du benzène, qui est hydrogéné en cyclohexane, ou du phénol, qui est hydrogéné en cyclohexanol.
Ensuite, le cyclohexane est oxydé avec de l’air pour produire l’huile KA. Au cours des deux dernières décennies, il y a eu une évolution notable vers le procédé à base de cyclohexane plus rentable.
3.1. Oxydation de l’acide nitrique du cyclohexanol
3.1.1. Mécanisme de réaction
La deuxième étape du procédé de production d’acide adipique conventionnel, développé par DuPont à la fin des années 1940, implique l’oxydation du cyclohexanol, de la cyclohexanone ou d’un mélange des deux à l’aide d’acide nitrique. L’acide adipique est obtenu avec un rendement supérieur à 90 %.
Au cours de ce processus, du dioxyde de carbone, des oxydes d’azote et certains acides dicarboxyliques de masse moléculaire inférieure sont formés comme sous-produits majeurs. De plus, certains sous-produits provenant d’impuretés présentes dans l’huile KA de départ sont également détectés.
Le mécanisme chimique de cette réaction a été initialement discuté en 1956, y compris des considérations de cinétique et de conception du réacteur. La figure 1 présente un résumé des conclusions de ces enquêtes.
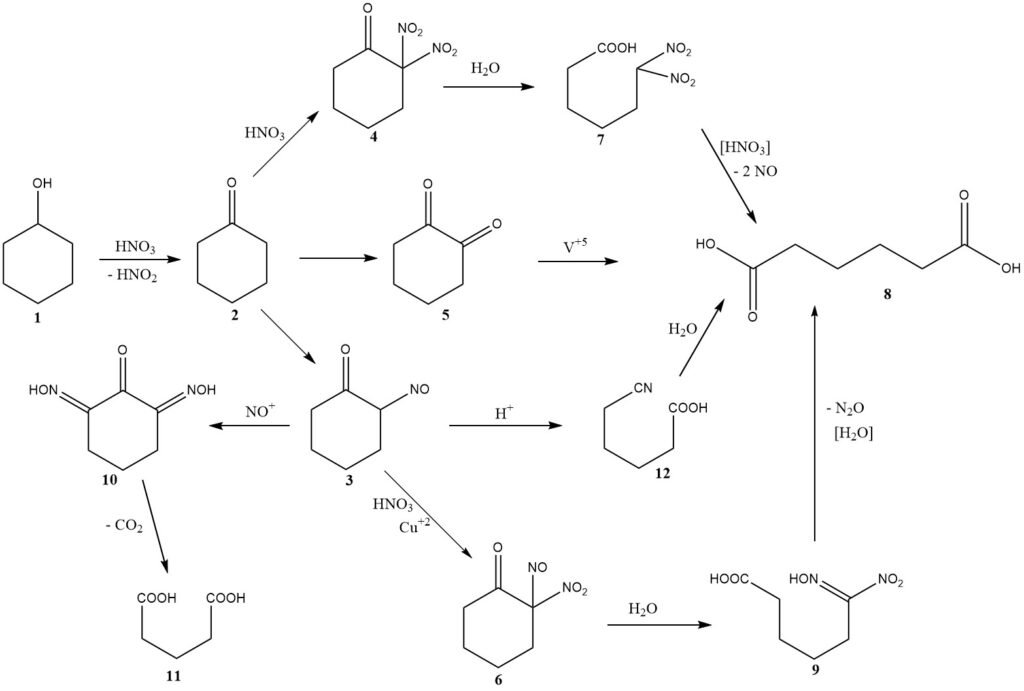
L’oxydation du cyclohexanol (1) produit de la cyclohexanone (2) tout en générant de l’acide nitreux. Ensuite, la cyclohexanone subit l’une des trois voies possibles conduisant à la formation d’acide adipique (8).
La voie principale implique la nitrosation pour produire la 2-nitrosocyclohexanone (3), qui réagit ensuite avec l’acide nitrique pour former la 2-nitro-2-nitrosocétone (6).
Le clivage hydrolytique de cet intermédiaire donne l’acide 6-nitro-6-hydroximinohexanoïque, également connu sous le nom d’acide nitrolique (9), qui se décompose davantage pour donner de l’acide adipique et de l’oxyde nitreux, les principaux produits de réduction de l’acide nitrique non récupérés.
Typiquement, 2,0 moles d’acide nitrique sont converties en protoxyde d’azote pour chaque mole d’acide adipique produit.
A des températures plus élevées, une deuxième voie devient significative, impliquant la nitration, conduisant à la formation de dinitrocétone (4).
Les premiers chercheurs ont proposé une troisième voie, impliquant la formation intermédiaire de 1,2-dicétone (5) ou de son dimère, où l’utilisation d’un catalyseur au vanadium est nécessaire pour obtenir un bon rendement en acide adipique. La présence de vanadium suggère sa contribution significative au rendement global.
La nitrosocétone intermédiaire (3) peut subir deux réactions secondaires importantes. La nitrosation multiple conduit à un intermédiaire (10), qui perd du dioxyde de carbone pour produire de l’acide glutarique (11) ou de l’acide succinique par réaction ultérieure avec l’acide nitrique.
Du cuivre métallique est ajouté à l’acide nitrique pour inhiber ces réactions. Dans des conditions spécifiques avec une concentration à l’état d’équilibre relativement élevée de la nitrosocétone (3) ou de l’oximinocétone tautomère, un réarrangement de type Beckmann se produit, conduisant à la formation mineure d’acide 5-cyanopentanoïque (12), qui est lentement hydrolysé en acide adipique .
3.1.2. Procédés commerciaux d’oxydation de l’acide nitrique
Le processus d’oxydation de l’acide nitrique pour convertir le cyclohexanol-cyclohexanone (KA) en acide adipique reste similaire à la littérature des premiers brevets, mais des progrès ont été réalisés dans l’élimination des sous-produits, la récupération du catalyseur et de l’acide nitrique et la réduction des émissions d’oxyde nitreux, un gaz à effet de serre qui était traditionnellement libéré dans l’atmosphère.
En raison de la nature corrosive de l’acide nitrique, les usines de fabrication sont construites avec des matériaux comme l’acier inoxydable (type 304L ou mieux) ou le titane dans les zones à forte exposition.
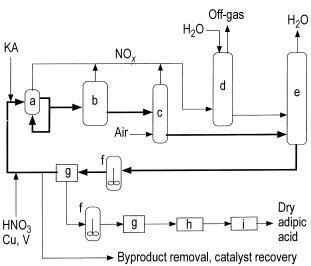
Le procédé implique généralement un réacteur (a), fonctionnant comme un grand échangeur de chaleur, fonctionnant à 60 – 80 °C et à une pression de 0,1 – 0,4 MPa. Le réacteur reçoit la liqueur mère d’acide nitrique recyclée (NML), le matériau d’alimentation KA, l’acide d’appoint avec 50 à 60 % d’acide nitrique et un catalyseur cuivre-vanadium.
Le temps de séjour dans le réacteur est inférieur à 5 minutes. Certaines installations utilisent un second réacteur (b) à température élevée (110 – 120 °C) pour terminer la réaction et réduire les impuretés avant de procéder à la cristallisation.
La réaction est hautement exothermique (6280 kJ/kg) et des conceptions de réacteur innovantes ont été brevetées pour contrôler la chaleur de réaction et minimiser la consommation d’énergie. Un excédent de flux d’alimentation de NML recyclé en KA est maintenu (au moins 3:1 jusqu’à 1000:1) pour contrôler la réaction et améliorer le rendement.
Le flux de produit subit plusieurs étapes, notamment le passage dans un blanchisseur (c) pour éliminer les oxydes d’azote dissous en excès, qui sont ensuite récupérés sous forme d’acide nitrique dans l’absorbeur (d).
Le gaz de dégagement de l’absorbeur peut être utilisé pour initier l’oxydation à des températures plus basses en le faisant passer à travers le courant d’alimentation en KA avant de l’amener à l’oxydant. L’eau produite dans le procédé est éliminée dans un alambic de concentration (e) fonctionnant sous vide.
Le flux de produit concentré est soit recyclé vers le réacteur avec une partie détournée pour la récupération du produit, soit envoyé directement vers la récupération du produit avant le recyclage du filtrat NML. L’acide adipique brut est extrait de la boucle NML par cristallisation (f) puis filtré ou centrifugé (g).
Ce courant d’effluent, contenant des concentrations plus élevées d’acide glutarique, d’acide succinique et de sous-produits, est ensuite traité pour récupérer les catalyseurs au vanadium et au cuivre et éliminer les acides sous-produits. La récupération des métaux est généralement réalisée par échange d’ions.
L’acide adipique brut issu du premier cristallisoir (g) subit une ou plusieurs étapes de recristallisation avant de passer dans un sécheur (h) et un refroidisseur (i). Alternativement, si l’acide adipique sec n’est pas nécessaire, les cristaux de la centrifugeuse/filtre (g) peuvent être dissous dans de l’eau et ajoutés à une solution aqueuse de 1,6-hexanediamine pour produire du sel de nylon.
Des améliorations supplémentaires au procédé classique ont été décrites, notamment concernant la séparation et la récupération des sous-produits d’acide dibasique.
Selon l’utilisation finale, l’acide adipique brut peut être raffiné à différents degrés, mais la recristallisation dans l’eau est une approche courante. Il a été affirmé que le reflux de l’acide adipique brut dans de l’acide nitrique à 60% avec du vanadium dissous produisait un produit de haute qualité.
3.2. Routes à base de butadiène
Au début des années 1970, BASF a lancé un vaste programme de recherche pour produire de l’adipate de diméthyle, un diester qui pourrait ensuite être hydrolysé en acide adipique. Le processus impliquait la carbométhoxylation du butadiène à l’aide de monoxyde de carbone et de méthanol, catalysée par du cobalt et de la pyridine sous haute pression.
Cette réaction a donné du 3-penténoate de méthyle, qui a été séparé des sous-produits par distillation. Par la suite, une deuxième étape de carbométhoxylation à plus basse pression, avec un rapport pyridine sur cobalt réduit, a entraîné la formation d’adipate de diméthyle.
L’hydrolyse du diester en acide adipique et en méthanol a été réalisée par un procédé catalytique à haut rendement. Dans l’ensemble, le procédé a présenté un rendement approximatif d’environ 70 % à partir du butadiène. Bien que démontré à l’échelle d’une usine pilote, il n’a pas encore été commercialisé.
Au milieu des années 1980, DuPont s’est également lancé dans un programme important impliquant une voie à base de butadiène vers l’acide adipique. Contrairement à l’approche diester de BASF, la méthode de DuPont impliquait la dihydrocarboxylation directe du butadiène en acide adipique (comme le montre la figure 3).
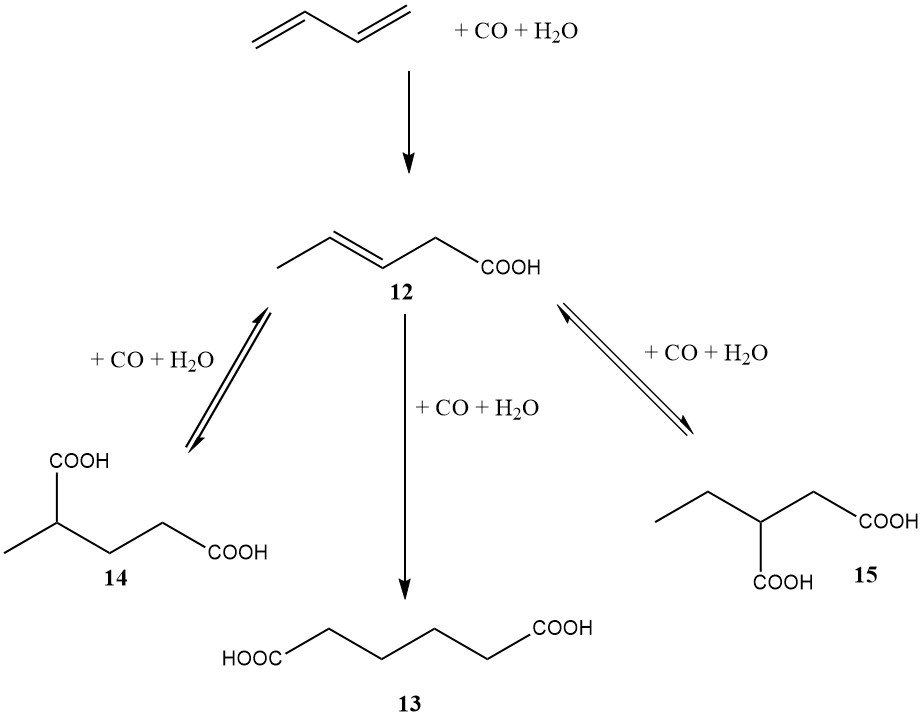
La première étape, catalysée par le palladium, le rhodium ou l’iridium, a conduit principalement à l’acide 3-penténoïque. La deuxième étape, catalysée par le rhodium ou l’iridium, a entraîné la formation d’acide adipique (13), d’acide 2-méthylglutarique (14) et d’acide 2-éthylsuccinique (15).
L’avantage de ce procédé était la capacité d’isomériser les acides 2-méthylglutarique et 2-éthylsuccinique en acide adipique en utilisant le même système catalytique. Le catalyseur nécessitait un promoteur d’halogénure, tel que l’acide iodhydrique.
L’acide pentanoïque, un acide carboxylique saturé et un sous-produit du procédé, servait généralement de solvant. Depuis la fin des années 1980, de nombreuses grandes entreprises chimiques ont obtenu de nombreux brevets pour des variantes de ces voies à base de butadiène.
3.3. Autres itinéraires
Outre l’oxydation classique en deux étapes air/acide nitrique du cyclohexane et la carboxylation/carbométhoxylation du butadiène, divers autres procédés ont été explorés pour la production d’acide adipique.
Monsanto a mené des recherches sur la dicarbonylation catalysée par l’halogénure de palladium des 2-butènes 1,4-disubstitués. Ce procédé implique la production d’acide adipique à partir de 1,4-diméthoxy-2-butène, de monoxyde de carbone et de chlorure de palladium à 100 ° C, suivie d’une hydrogénation et d’une hydrolyse de l’ester diméthylique insaturé résultant.
L’oxydation en une étape du cyclohexane à l’aide d’acide nitrique, de dioxyde d’azote ou d’air a également été étudiée. L’oxydation tout air en une étape du cyclohexane est particulièrement attrayante sur le plan économique et a fait l’objet de recherches approfondies.
Les premières études ont été menées par Gulf Research and Development, Asahi Chemical Industries et d’autres groupes. Par exemple, le cyclohexane peut être oxydé en une étape en acide adipique avec un rendement de 70 à 75 % en présence d’un catalyseur d’acétate de cobalt dans de l’acide acétique comme solvant.
Récemment, cette approche a suscité un regain d’intérêt, ce qui a donné lieu à plusieurs brevets délivrés à des sociétés telles que Redox Corporation et Bayer.
L’acide adipique peut également être produit par ozonolyse du cyclohexène ou en ajoutant un acide carboxylique au cyclohexène et en oxydant ensuite l’ester résultant avec de l’acide nitrique.
De plus, la formation de dérivés d’acide adipique via le couplage électrolytique d’acrylates a été décrite.
Ces processus alternatifs représentent des efforts de recherche en cours pour développer de nouvelles méthodes de synthèse de l’acide adipique.
4. Utilisations de l’acide adipique
Environ 80 % de la consommation mondiale d’acide adipique est destinée à la production de fibres et de résines de nylon 66.
Une plus petite quantité d’acide adipique est encore utilisée en captivité pour produire de l’adiponitrile.
Des quantités importantes d’acide adipique sont transformées en esters pour diverses applications telles que les plastifiants, les lubrifiants et une gamme de résines polyuréthanes.
Les esters monomères sont des plastifiants essentiels pour le poly(chlorure de vinyle) et d’autres résines, tandis que les esters polymères sont utilisés lorsque des niveaux de plastifiant exceptionnellement élevés sont requis.
Les résines de polyuréthane qui incorporent de l’acide adipique sont créées à partir de polyisocyanates et de polyols de polyester (adipates) et trouvent une utilisation dans diverses applications.
L’acide adipique sert également d’acidulant dans les gélatines et les confitures et agit comme agent tampon ou neutralisant dans d’autres produits alimentaires.
De plus, il est utilisé pour modifier les propriétés des polyesters insaturés à utiliser dans les plastiques renforcés et les revêtements alkydes.
L’acide adipique est utilisé dans les résines polyamide-épichlorhydrine pour améliorer la résistance à l’état humide des produits en papier.
D’autres applications diverses incluent son utilisation dans les adhésifs, les insecticides, le tannage, la teinture et les industries textiles. De plus, l’acide adipique et les acides dibasiques mixtes (DBA) sont utilisés comme tampons dans le traitement de désulfuration des gaz de combustion dans les centrales électriques.
5. Toxicologie et santé au travail
L’acide adipique présente une irritation mineure et une faible toxicité orale. Les doses létales publiées (LDLo) sont de 3600 mg/kg (rat, oral), LD50 275 mg/kg (rat ou souris, i.p.) et LD50 1900 mg/kg (souris, oral).
Certains tests d’alimentation chronique ont montré des augmentations retardées du poids corporel, des altérations de certaines enzymes et des modifications des taux d’urée et de chlorure dans le sang. Cependant, aucune activité tératogène n’a été observée dans les études impliquant des souris gravides.
Des études de métabolisme sur des rats nourris avec de l’acide adipique marqué au 14C ont révélé la présence d’acide adipique inchangé et de produits métaboliques normaux dans l’urine.
L’exposition à l’acide adipique peut provoquer une irritation des muqueuses telles que les yeux et les voies respiratoires, tandis qu’une exposition prolongée de la peau peut entraîner un dessèchement ou une irritation.
En cas de déversement ou de fuite, le personnel doit être protégé contre l’inhalation ou le contact excessif avec la peau. Le dépoussiérage doit être contrôlé et des mesures doivent être prises pour éviter les étincelles d’électricité statique. En cas de déversement, la zone peut être rincée à grande eau.
Bien qu’il n’y ait pas de valeur TLV (Threshold Limit Value) ou MAK (Maximal Concentration Value) établie, l’exposition atmosphérique à l’acide adipique doit être maintenue en dessous de celle d’une poussière organique nuisible : l’ACGIH (1979) recommande une TWA (Time-Weighted Average Average) de 8 heures. ) de 10 mg/m3 pour les poussières totales et de 5 mg/m3 pour les poussières respirables. La TLV OSHA pour la poussière totale est de 15 mg/m3.
6. Dérivés d’acide adipique
6.1. Adiponitrile
Le principal dérivé de l’acide adipique est l’adiponitrile, également appelé 1,6-hexanedinitrile ou 1,4-dicyanobutane, Mr 108,14, point d’ébullition 298 – 300 °C (à 101,3 kPa), 154 °C (à 1,3 kPa), et point de congélation 2,4 °C.
L’adiponitrile sert d’intermédiaire dans la production du principal composant du nylon 66, la 1,6-hexanediamine. Les méthodes de production antérieures impliquaient la conversion de l’acide adipique en dinitrile par déshydratation en phase liquide ou vapeur du sel d’ammonium, à l’aide d’acide phosphorique ou d’un catalyseur bore-phosphore. Cependant, ces méthodes ne sont plus utilisées par les principaux producteurs de nylon 66.
Diverses voies ont été utilisées pour la production d’adiponitrile, y compris les procédés de Celanese, qui ont produit de la 1,6-hexanediamine à partir de l’ammonolyse du 1,6-hexanediol, obtenu par hydrogénation de l’acide adipique.
6.2. Sels d’acide adipique
L’acide adipique forme des sels de métaux alcalins et d’ammonium solubles dans l’eau, ainsi que des sels alcalino-terreux modérément solubles.
Leurs solubilités dans 100 g d’eau sont les suivantes : sel de diammonium 40 g (14 °C), sel disodique 59 g d’hémihydrate (14 °C), sel dipotassique 65 g (15 °C), sel de calcium 4 g de monohydrate ( 13 °C), et 1 g de sel anhydre (100 °C).
Le sel le plus courant est le poly(hexanedioate de 1,6-hexanediammonium), produit par réaction de l’acide adipique avec la 1,6-hexanediamine. Ce sel soluble dans l’eau, un précurseur du nylon 66, peut être facilement expédié ou stocké avant la polyamidation finale, au cours de laquelle l’eau est éliminée.
6.3. Esters et polyesters d’acide adipique
Les esters et polyesters d’acide adipique constituent le plus grand marché non polyamide pour l’acide adipique. Les esters dérivés d’alcools à longue chaîne sont utilisés comme plastifiants et lubrifiants, tandis que ceux d’alcools à chaîne courte servent principalement de solvants.
Le reflux de l’acide adipique avec du méthanol en présence d’un catalyseur acide donne de l’adipate de monométhyle, ainsi que le diester. L’électrolyse du sel du monoester (synthèse Kolbe) génère du sébacate de diméthyle, autre précurseur du polyamide.
Les esters se dissolvent facilement dans la plupart des solvants organiques, l’adipate de diméthyle étant le solvant le plus couramment utilisé et l’adipate de di-2-éthylhexyle étant le plastifiant le plus largement utilisé. D’autres plastifiants adipates simples comprennent les esters de n-octyle, de n-décyle, d’isodécyle et d’isooctyle.
Les plastifiants polymères plus complexes, préparés à partir de glycols, représentent un peu moins de la moitié des plastifiants à base d’acide adipique. Des polyols de polyester de faible masse moléculaire ayant des groupes terminaux hydroxyle sont utilisés avec des polyisocyanates pour produire des résines de polyuréthane.
6.4. Anhydrides d’acide adipique
L’anhydride d’acide adipique est généralement obtenu en déshydratant l’acide adipique, ce qui entraîne la formation de la forme polymère linéaire. La distillation de l’anhydride polymère peut produire la forme cyclique monomère, qui est hautement instable et se transforme facilement en anhydride polymère linéaire.
6.5. Amide d’acide adipique
Le diamide de l’acide adipique a un point de fusion de 228 °C et est pratiquement insoluble dans l’eau froide. Traditionnellement, il a été préparé en traitant l’ester diméthylique avec de l’hydroxyde d’ammonium concentré ou en chauffant le sel diammonium de l’acide adipique dans un courant d’ammoniac. Divers amides substitués peuvent être synthétisés à partir d’amines en utilisant des méthodes de synthèse standard.
Référence
Adipic Acid; Ullmann’s Encyclopedia of Industrial Chemistry. – https://onlinelibrary.wiley.com/doi/10.1002/14356007.a01_269
FAQ
L’acide adipique est un composé organique cristallin blanc de formule chimique C6H10O4. Il appartient à la classe des acides dicarboxyliques aliphatiques et est souvent appelé acide hexanedioïque. L’acide adipique est commercialement important et largement utilisé dans diverses industries en raison de ses propriétés polyvalentes.
L’acide adipique a diverses applications dans toutes les industries. Son utilisation principale et la plus importante est dans la production de polyamide nylon 66, un matériau crucial pour la fabrication de fibres et de résines. En outre, l’acide adipique est utilisé dans la production d’esters, de résines de polyuréthane, de plastifiants, de lubrifiants et comme acidulant ou agent tampon dans l’industrie alimentaire. Il est également employé dans la synthèse de divers dérivés chimiques.
L’acide adipique peut être produit par plusieurs méthodes. Les procédés commerciaux les plus courants impliquent l’oxydation air/acide nitrique en deux étapes du cyclohexane ou l’hydrocyanation directe du butadiène. La première méthode commence par l’oxydation du cyclohexane pour produire du cyclohexanol et de la cyclohexanone, suivie de leur oxydation avec de l’acide nitrique pour obtenir de l’acide adipique. Cette dernière méthode implique l’hydrocyanation du butadiène pour produire de l’adiponitrile, qui est ensuite hydrogéné et hydrolysé pour donner de l’acide adipique.
L’acide adipique présente une solubilité dans divers solvants. Il est soluble dans le méthanol, l’éthanol, l’eau et l’acétone. Cependant, sa solubilité est relativement plus faible dans le cyclohexane et le benzène.
L’acide adipique est généralement considéré comme sûr lorsqu’il est utilisé conformément aux directives et aux concentrations recommandées. C’est un irritant mineur et a une faible toxicité orale. La dose létale pour les rats (LDLo) est relativement élevée (3600 mg/kg), mais il faut faire preuve de prudence pour éviter une inhalation excessive ou un contact avec la peau. L’acide adipique n’est pas connu pour être tératogène et ses produits métaboliques sont excrétés dans l’urine.
La formule chimique de l’acide adipique est C6H10O4.
L’acide adipique est également connu sous le nom « acide hexanedioïque ».