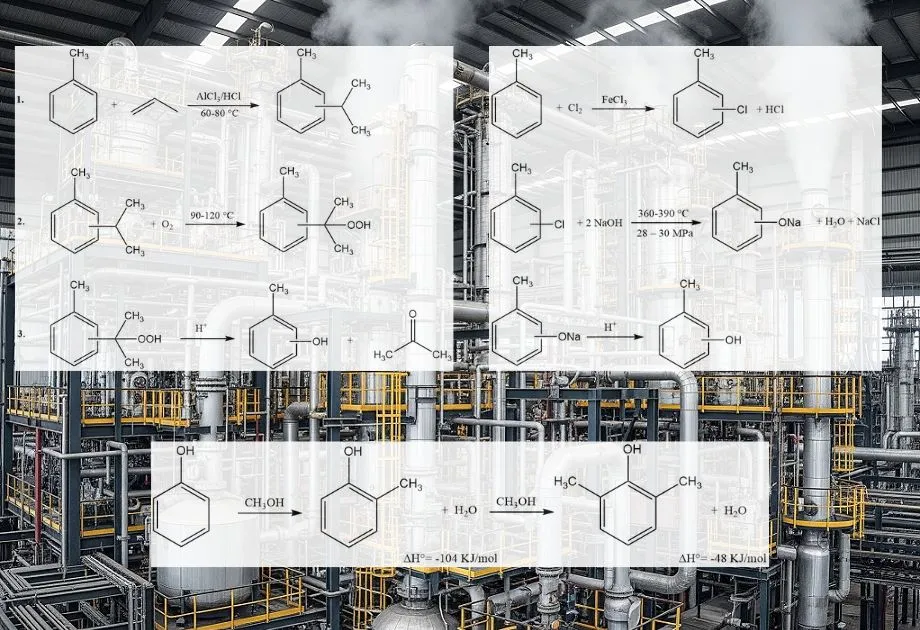
Seit 1965 hat die synthetische Kresolproduktion stark zugenommen und aufgrund der steigenden Nachfrage die Gewinnung aus Kohlenteer und Raffinerieätzmitteln abgelöst. Kresole werden hauptsächlich durch verschiedene Verfahren hergestellt, wie z. B. die alkalische Fusion von Toluolsulfonaten, die alkalische Chlortoluolhydrolyse, die Spaltung von Cymolhydroperoxid und die Dampfphasenmethylierung von Phenol.
Die ersten drei Verfahren verwenden Toluol als Ausgangsstoff und sind Erweiterungen etablierter Phenolsynthesemethoden. Die Phenolmethylierung ist jedoch ein spezieller Weg zur Kresol- und Xylenolproduktion.
Jedes Verfahren erzeugt eine eigene Kresol-Isomerenverteilung, und alle sind von individueller Bedeutung.
Inhaltsverzeichnis
1. Herstellung von Kresol durch alkalische Fusion von Toluolsulfonaten
Die alkalische Fusion ist ein wichtiges industrielles Verfahren, das hauptsächlich zur Synthese von p-Kresol eingesetzt wird. Der Prozess umfasst vier verschiedene Reaktionsschritte:
1. Sulfonierung von Toluol: Toluol reagiert bei 120–130 °C unter Normaldruck mit konzentrierter Schwefelsäure. Um einen vollständigen Verbrauch der Schwefelsäure zu gewährleisten, wird das entstehende Reaktionswasser azeotrop mit überschüssigem Toluoldampf entfernt.
2. Neutralisation: Das entstehende Toluolsulfonsäuregemisch wird mit Natriumsulfit oder Natriumhydroxid neutralisiert.
3. Alkalische Fusion: Das Natriumtoluolsulfonat wird anschließend bei 330–350 °C mit überschüssigem Natriumhydroxid geschmolzen.
4. Ansäuerung: Das geschmolzene Produkt wird in Wasser gelöst und unlösliches Natriumsulfit abfiltriert. Die wässrige Phase wird anschließend mit Schwefeldioxid (aus Schritt 2 recycelt) oder Schwefelsäure angesäuert.
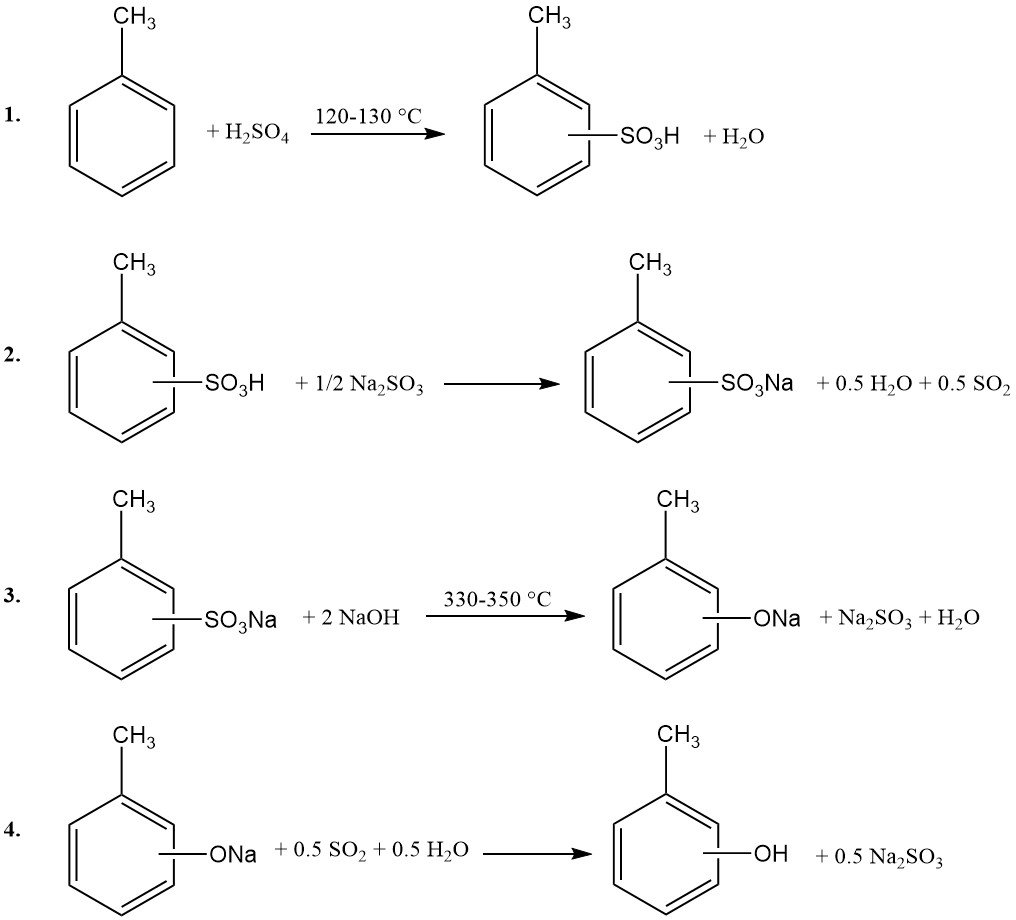
Der Ansäuerungsschritt ergibt eine wässrige Natriumsulfitlösung, die zur Neutralisationseinheit zurückgeführt wird, sowie eine Rohkresolphase. Dieses Rohkresol wird durch azeotrope Destillation dehydratisiert. Die Anlagen- und Prozesskonfiguration ähnelt stark denen, die zuvor für die Phenol-Synthese mittels alkalischer Fusion von Natriumbenzolsulfonat verwendet wurden.
Die fraktionierte Destillation des dehydratisierten Rohkresols liefert Phenol, o-Kresol, ein m-/p-Kresolgemisch und einen Rückstand, der Ditolylsulfone, Xylenole und andere höhere Phenole enthält. Ditolylsulfone sind Nebenprodukte der Sulfonierung, während Phenole und Xylenole in geringen Mengen bei der alkalischen Fusion entstehen.
Die Kresol-Isomerenverteilung wird maßgeblich von den Sulfonierungsbedingungen beeinflusst. Typische Zusammensetzungen umfassen 6–12 % o-Kresol, 6–12 % m-Kresol und 80–85 % p-Kresol. Nach destillativer Entfernung des o-Kresols kann p-Kresol mit einer Reinheit von ca. 90 % erhalten werden.
Eine weitere Reinigung auf einen m-Kresolgehalt von ca. 1 % ist durch Schmelzkristallisation möglich. Eine Kresolausbeute von 80 %, bezogen auf Toluol, ist möglich, wobei die Ausbeute mit steigendem m-Kresolgehalt abnimmt.
Kinetisch kontrollierte (milde) Sulfonierungsbedingungen in Verbindung mit einer milden Alkalischmelze können Kresolgemische mit reduziertem m-Kresolgehalt erzeugen. Beispielsweise wurde berichtet, dass die Sulfonierung mit Chlorschwefelsäure bei 33–45 °C ein m-kresolfreies Produkt mit einer Ausbeute von 90 % und einem o-/p-Kresol-Verhältnis von 15:85 liefert.
Ähnlich führt die Toluolsulfonierung mit Schwefeltrioxid-Schwefeldioxid-Gemischen bei 25–50 °C zu Toluolsulfonsäuregemischen, die praktisch frei vom meta-Isomer sind und ein o-/p-Isomerenverhältnis von nur 3:97 aufweisen.
Der Betrieb in einem Schleifenreaktor bei 0 °C mit gasförmigem SO3, verdünnt mit einem Inertgas (oder unter Vakuum), kann den o- und m-Isomerengehalt auf 0,5 % reduzieren. Die Sulfonierung mit Oleum oder Schwefelsäure in einem Rotationsfilmreaktor mit kurzen Verweilzeiten ermöglicht ebenfalls eine meta-freie Sulfonierung, die hauptsächlich p-Toluolsulfonsäure liefert.
Im Gegensatz dazu erzeugt die thermodynamisch kontrollierte Sulfonierung (hohe Temperatur, lange Reaktionszeit, niedriger Wassergehalt) ein Gleichgewichtsgemisch mit etwa 5 % o-, 54 % meta- und 41 % para-Toluolsulfonsäure. Die alkalische Fusion solcher Gemische ergibt anschließend eine Isomerieverteilung von etwa 5 % o-Kresol, 56 % m-Kresol und 39 % p-Kresol.
Technisches m-Kresol kann durch die Reaktion von Wasserdampf bei 165 °C mit einem meta-isomerenreichen Toluolsulfonsäuregemisch unter thermodynamisch kontrollierten Bedingungen (anschließend mehrstündige Isomerisierung bei 190–200 °C) hergestellt werden.
Bei diesem Verfahren werden ortho- und para-Toluolsulfonsäuren selektiv zu Schwefelsäure und Toluol hydrolysiert. Das freigesetzte Toluol wird mit Wasserdampf abdestilliert, wobei neben Schwefelsäure m-Toluolsulfonsäure mit einer Reinheit von über 90 % zurückbleibt.
Nebenreaktionen während der Isomerisierung und Hydrolyse können durch Zugabe von 5–10 Mol-% Natriumsulfat zum Sulfonierungsansatz unterdrückt werden. Diese Zugabe erleichtert zudem die Abtrennung der bei der Hydrolyse gebildeten Schwefelsäure als untere Phase bei 140–150 °C.
Das Hydrolysegemisch kann mit konzentrierter Natronlauge neutralisiert werden, wobei Natriumsulfat und Natrium-m-Toluolsulfonat entstehen. Die resultierende Natrium-m-Toluolsulfonat-Lösung wird anschließend mit einer Natriumhydroxidschmelze (enthält 10–15 % Kaliumhydroxid) bei einer Anfangstemperatur von 330 °C umgesetzt und anschließend zur Schmelze auf 340 °C erhitzt.
Die Destillation der nach der Ansäuerung erhaltenen Rohkresolphase liefert m-Kresol mit einer Reinheit von bis zu 98 % und einer Ausbeute von ca. 65 % bezogen auf umgesetztes Toluol.
Das Toluolsulfonierungsverfahren für p-Kresol wird von PMC (USA, ca. 18.000 t/a), Inspec Fine Chemicals (Großbritannien, ca. 12.000 t/a), Beraton (Russland, ca. 3.000 t/a) und Konan Chemicals (Japan, ca. 4.000 t/a) eingesetzt.
Die Honshu Chemical Industry Co. (Japan) betreibt eine Reserveanlage (ca. 2.500 t/a), die entweder m- oder p-Kresol produzieren kann. Eine Anlage von Gujarat Aromatics in Indien, die auf dem Honshu-Verfahren basiert, produziert Berichten zufolge jährlich 3.000–5.000 t p-Kresol oder m-Kresol.
Das Toluolsulfonsäure-Kresol-Verfahren erfordert zwar eine relativ einfache Anlage, sein Hauptnachteil ist jedoch die unvermeidliche Bildung von wässrigem Natriumsulfit.
2. Herstellung von Kresol durch alkalische Chlortoluolhydrolyse
Kresole können industriell durch alkalische Chlortoluolhydrolyse hergestellt werden, wobei ein Isomerengemisch mit hohem m-Kresolgehalt entsteht. Die Bayer AG in Deutschland, ein führender Hersteller synthetischer Kresole mit einer Kapazität von über 30.000 t/a, nutzt dieses Verfahren.
Der erste Schritt ist die Chlorierung von Toluol. Ein Mol Toluol reagiert mit einem Mol Chlor in Gegenwart von Eisen(III)-chlorid und Dischwefeldichlorid zu einem Gemisch aus o- und p-Chlortoluol. Je nach FeCl3 und Cokatalysatorsystem können die o/p-Verhältnisse zwischen 3:1 und 1:2 liegen.
Anschließend wird dieses Chlortoluolgemisch mit einem Überschuss an Natronlauge (2,5–3,5 mol/mol Chlortoluol) hydrolysiert. Diese Reaktion erfolgt bei hohen Temperaturen (360–390 °C) und Drücken (280–300 bar, 28–30 MPa).
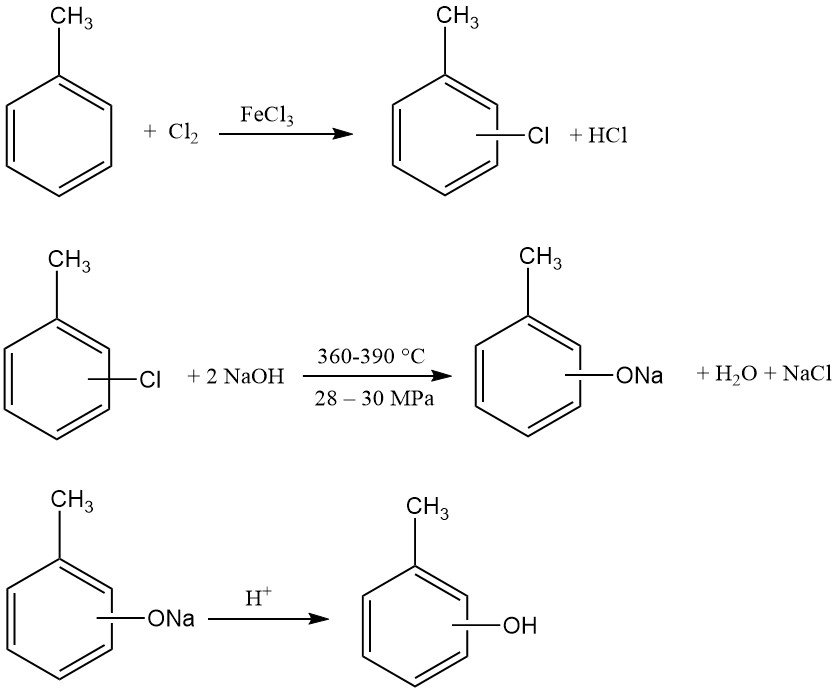
Die exotherme Hydrolyse wird kontinuierlich in langen Hochdruckrohren aus Nickelstahl durchgeführt, um dem korrosiven Reaktionsgemisch standzuhalten. Hohe Strömungsgeschwindigkeiten mit häufigen Richtungswechseln gewährleisten die Homogenität der Reaktionsmasse und verhindern eine Trennung der Komponenten.
Die entstehende Natriumkresolatlösung wird anschließend neutralisiert, um die Kresole freizusetzen. Die im ersten Chlorierungsschritt entstehende Salzsäure kann für diese Neutralisation genutzt werden. Nebenproduktiv produziertes Natriumchlorid kann einer Chlor-Alkali-Elektrolyseanlage zugeführt werden.
Aus wirtschaftlichen Gründen ist die gemeinsame Ansiedlung von Ausgangsstoffproduktion und Hydrolyseanlage erforderlich, um den Transport über Rohrleitungen zu ermöglichen. Die zugrundeliegende Technologie dieses Prozesses ähnelt weitgehend der Chlorbenzol-zu-Phenol-Hydrolyse von Dow-Bayer. Bei der Kresolproduktion entstehen jedoch mehr Nebenprodukte.
Zu diesen Nebenprodukten gehören Ditolylether (Bis(methylphenyl)ether), Tolylkresole (Methyl(methylphenyl)phenole) sowie geringe Mengen Toluol, Phenol, Benzoesäure und Crackabgase (Methan, Wasserstoff). Phenol kann beispielsweise durch azeotrope Destillation mit Chlortoluol entfernt werden.
Während die Bildung von Tolylkresol schwer zu kontrollieren ist, lässt sich die Bildung von Ditolylether durch Anpassung von Temperatur, Verweilzeit und Natronlaugekonzentration steuern. Das Recycling von Ditolylethern minimiert zudem deren Anreicherung aufgrund ihrer Hydrolysierbarkeit, wenn auch langsamer als bei Diphenylether.
Eine optimale Reaktionskontrolle ermöglicht Kresolausbeuten von ca. 80 % bezogen auf Chlortoluol.
Da Ditolylether ein wertvolles chemisches Produkt ist, das als Wärmeträger (z. B. Diphyl DT), elektrischer Isolator (z. B. Baylectrol 4800, ein PCB-Ersatz) und Vorstufe für Gerbstoffe verwendet wird, wird er oft nicht recycelt. Manchmal müssen die Prozessbedingungen sogar angepasst werden, um seine selektive Bildung zu verbessern.
Die alkalische Chlortoluolhydrolyse liefert hochreine Kresole mit minimalen Anteilen anderer Verbindungen.
Ein o/p-Chlortoluol-Eingangsverhältnis von 1:1 führt typischerweise zu einem o-, m- und p-Kresol-Isomerenverhältnis von etwa 1:2:1. Dieses veränderte Verhältnis im Vergleich zum Chlortoluol-Eingangsverhältnis deutet auf eine Isomerisierung über Arin-Zwischenprodukte unter den anspruchsvollen Hydrolysebedingungen hin. Nach der o-Kresol-Destillation wird ein m-/p-Kresol-Gemisch mit etwa 70 % m-Kresol erhalten.
Die Anlage kann auch mit reinem o-Chlortoluol oder p-Chlortoluol betrieben werden. Die Hydrolyse von p-Chlortoluol ergibt ein 1:1-M-/p-Kresolgemisch, während die Hydrolyse von o-Chlortoluol ein 1:1-M-/m-Kresolgemisch erzeugt. Reines m-Kresol kann aus letzterem durch Abdestillieren des o-Kresols technisch isoliert werden.
Die Hydrolyse von Chlortoluol ohne signifikante Isomerisierung ist unter milderen Bedingungen (200–350 °C) mit Alkalimetallhydroxiden, Alkalimetallcarbonaten, Ammoniumhydroxid oder Alkalimetallacetat-/-propionatlösungen in Gegenwart von Kupfer oder Kupferverbindungen möglich.
Diese alternativen Verfahren sind aufgrund geringerer Ausbeuten bei niedrigeren Temperaturen im Allgemeinen industriell nicht rentabel.
3. Kresolherstellung durch Cymolhydroperoxidspaltung
Das Cymol-Kresol-Verfahren, auch als Cymolhydroperoxid-Synthese bekannt, ermöglicht die Herstellung von m- oder p-Kresol aus den entsprechenden Isopropyltoluol-(Cymol-)Isomeren. Für die o-Kresolsynthese ist dieses Verfahren nicht geeignet. Der Prozess umfasst drei Hauptschritte:
- Toluolpropylierung und Cymolisomerisierung: Toluol reagiert mit Propen zu Cymolisomeren, deren Isomerisierung anschließend zur gewünschten Isomerenverteilung führt.
- Cymoloxidation: Cymol wird zu Cymolhydroperoxid oxidiert.
- Peroxidspaltung: Das Cymolhydroperoxid wird säurekatalysiert gespalten, wobei Kresol und Aceton entstehen.
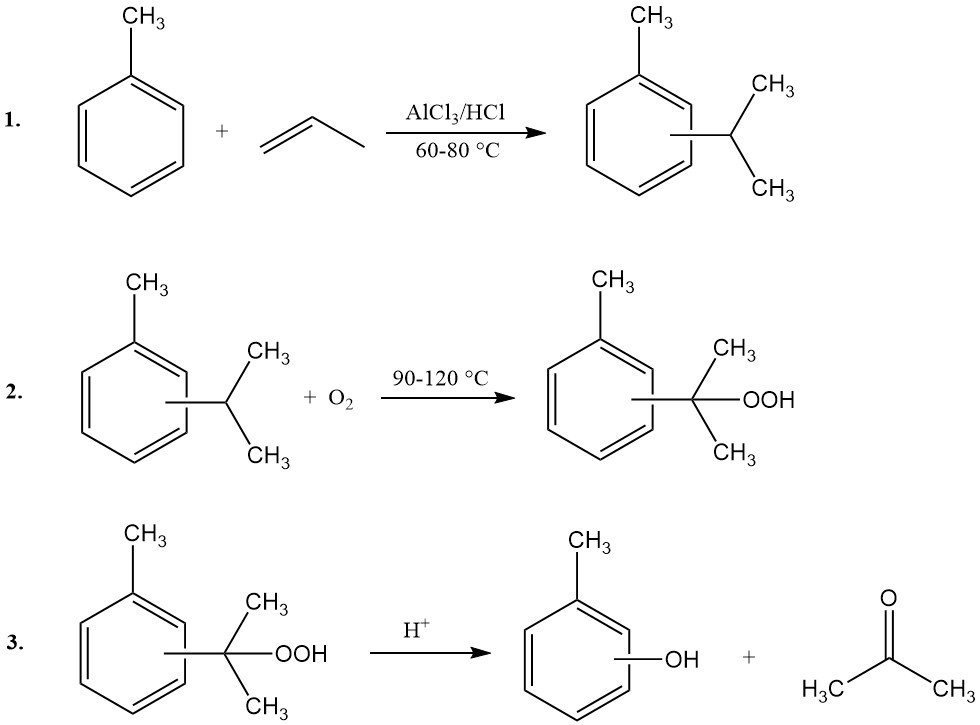
Das Cymol-Kresol-Verfahren weist im Vergleich zum Hock-Cumol-Verfahren mehrere betriebliche und wirtschaftliche Nachteile auf. Dazu gehören geringere Raum-Zeit-Ausbeuten, komplexe Destillationsanforderungen, anspruchsvolles Abwassermanagement und reduzierte Produktausbeuten (20–30 % niedriger).
Hauptfaktoren für diese Einschränkungen sind die Isomerieverteilung bei der Propylierung, eine suboptimale Oxidationskinetik, Methylgruppenoxidation und Formaldehyd-Nebenreaktionen sowie eine komplexe Nebenproduktabtrennung.
1. Die Toluolpropylierung liefert ortho-, meta- und para-Cymol-Isomere. ortho-Cymol hemmt die Oxidation anderer Cymole und wird selbst nur schlecht oxidiert. Die Aufrechterhaltung eines o-Cymol-Gehalts unter 10 % ist für eine kontinuierliche Oxidation entscheidend.
Um dies zu erreichen, sind aufwendige Recycling- und Isomerisierungsschritte erforderlich. Dabei wird häufig Aluminiumchlorid eingesetzt, um das thermodynamische Gleichgewicht herzustellen (z. B. 3 % o-, 64 % m- und 33 % p-Cymol). Auch Diisopropyltoluol-Nebenprodukte werden zur Isomerisierung recycelt.
2. Cymol oxidiert langsamer als Cumol, und der maximal erreichbare Peroxidgehalt ist niedriger (ca. 20 % gegenüber > 30 % bei Cumol). Dies erfordert höhere Recyclingquoten für nicht umgesetztes Cymol und führt bei höheren Oxidationsgraden zu einer erhöhten Nebenproduktbildung (z. B. Dimethyl(tolyl)methanol, Methylacetophenon).
3. Die Oxidation der Cymolmethylgruppe ist eine bedeutende Nebenreaktion. Dabei entstehen primäre Peroxide, die weniger stabil sind und Nebenprodukte (z. B. Isopropylbenzylalkohol, Cuminsäure) liefern. Die anschließende Säurespaltung erzeugt Formaldehyd, der mit Kresol zu Harzen reagieren kann, was die Kresolausbeute erheblich reduziert und die Produktreinigung erschwert.
Verfahren zur Minderung der Formaldehydbildung oder ihrer Auswirkungen umfassen die selektive Zersetzung/Hydrierung primärer Peroxide, Extraktion oder die alkalische In-situ-Auflösung saurer Nebenprodukte.
4. Das Reaktionsgemisch nach der Spaltung ist hochkomplex und enthält zahlreiche Nebenprodukte mit ähnlichen Siedepunkten und azeotropen Tendenzen. Dies macht die Trennung kostspielig. Die selektive Hydrierung primärer Peroxide und die anschließende Rehydrierung des konzentrierten Spaltgemisches können die Kresolausbeute durch Rückbildung von Cymol erhöhen.
Industrielle Cymol-Kresol-Anlagen mit gemischten Cymol-Einspeisungen sind seit 1969 in Betrieb (z. B. Sumitomo und Mitsui in Japan mit einer Kapazität von jeweils 22.000 t/a). Sie produzieren typischerweise m-/p-Kresol mit einer Reinheit von über 99,5 % und einem m/p-Verhältnis von 60:40. Hochwertiges Aceton wird zusätzlich produziert.
Die Verwendung von reinem p- oder m-Cymol als Ausgangsmaterial macht die Rückgewinnung und Isomerisierung von o-Cymol überflüssig und vereinfacht so die direkte Produktion reiner Isomere. Beispiele hierfür sind die frühere p-Kresol-Produktion aus natürlichen Terpenen (Hercules Powder Co., USA) und aktuelle Anlagen, die das Cymex-Verfahren von UOP nutzen, das p-Cymol selektiv mithilfe von Molekularsieben isoliert.
4. Herstellung von Kresol durch Methylierung von Phenol
Synthetische Kresole, insbesondere o-Kresol, und Xylenole werden hauptsächlich durch Methylierung von Phenol mit Methanol hergestellt. Dieser Prozess erfolgt in Gegenwart verschiedener Katalysatoren. 2,6-Xylenol wird fast ausschließlich auf diese Weise hergestellt.
Diese Synthese umfasst einen einzigen Reaktionsschritt. Allerdings wird Phenol verwendet, ein vergleichsweise teurer Rohstoff. Zudem ist die Abtrennung der Produkte vom Reaktionsgemisch aufgrund der nahe beieinander liegenden Siedepunkte mehrerer Komponenten und der strengen Reinheitsanforderungen für bestimmte Produkte kostspielig.
Die Methylierungsreaktion kann sowohl in der Dampf- als auch in der Flüssigphase durchgeführt werden.
4.1. Methylierung von Phenol in der Dampfphase
Die Dampfphasenmethylierung von Phenol mit Methanol ist ein wichtiger industrieller Weg zur Herstellung von hochreinem o-Kresol und/oder 2,6-Xylenol, wobei letzteres fast ausschließlich auf diese Weise hergestellt wird.
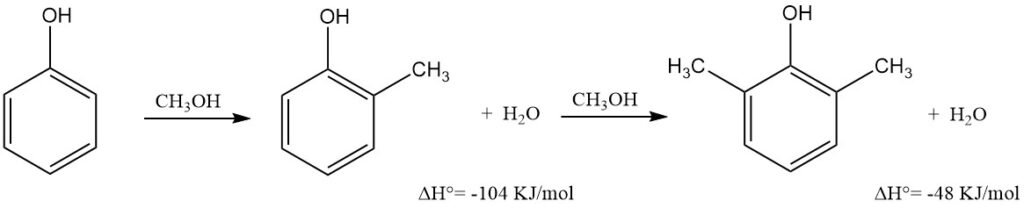
Bei diesem Verfahren wird ein überhitztes Gemisch aus Phenol, Methanol und Wasserdampf bei 300–460 °C und atmosphärischem oder leicht erhöhtem Druck über einen festen Metalloxidkatalysator in einem Edelstahl-Rohrbündelreaktor geleitet.
Die Flüssigkeitsraumgeschwindigkeit (LHSV) liegt typischerweise zwischen 1 und 2 h⁻¹. Die Reaktionstemperatur ist katalysatorabhängig und kann an die gewünschte Produktzusammensetzung angepasst werden. Die Reaktionswärme wird über siedende organische Wärmeträger, zirkulierende Salzschmelzen oder Hochdruckdampferzeugung zugeführt.
Der Verlust der Katalysatoraktivität im Laufe der Zeit wird durch Temperaturerhöhungen und regelmäßiges Entfernen der Kohlenstoffablagerungen durch Verbrennen ausgeglichen. Wasser im Ausgangsgemisch unterdrückt die Methanolzersetzung, verlängert die Regenerationszyklen und verlängert die Katalysatorlebensdauer.
Der Reaktoraustrag tauscht Wärme mit dem Ausgangsmaterial aus und kondensiert anschließend. Nicht kondensierbare Methanolzersetzungsprodukte (H2, CH4, CO2 und CO) werden als Brenngas für die Dampferzeugung verwendet. Wässriges Methanol wird aus dem flüssigen Produkt destilliert und recycelt. Die Trennung in Methanol, phenolhaltiges Wasser und Phenole kann in einer einzigen Destillationskolonne oder durch Dekantieren mit anschließender Harzadsorption der Phenole erfolgen.
Das verbleibende Wasser wird durch azeotrope Destillation mit Toluol oder als Azeotrop mit nicht umgesetztem Phenol entfernt, wobei im letzteren Fall eine Phenolstrippung aus dem Abwasser erforderlich ist.
Das entwässerte Gemisch wird einer kontinuierlichen fraktionierten Vakuumdestillation in Hochleistungskolonnen unterzogen, um Phenolether, Phenol, hochreines o-Kresol (99,5 %) und 2,6-Xylenol zu gewinnen. Die Phenolether-Phenol-Fraktion wird recycelt.
Destillationsrückstände, die andere Xylenole und Trimethylphenole enthalten, werden typischerweise als Brennstoff verwendet. Wenn der Katalysator eine hohe Orthoselektivität aufweist, ist 99,5 % reines 2,6-Xylenol direkt erhältlich. Andernfalls oder unter erschwerten Bedingungen kann die 2,6-Xylenol-Fraktion m- und p-Kresol enthalten, was eine weitere Reinigung erforderlich macht.
Das Verhältnis von o-Kresol zu 2,6-Xylenol lässt sich durch Anpassung des Methanol-Phenol-Verhältnisses steuern; durch Rückführung von o-Kresol kann 2,6-Xylenol zum alleinigen Produkt werden. Die Gesamtausbeute (Selektivität) an o-Kresol und 2,6-Xylenol, bezogen auf umgesetztes Phenol, liegt zwischen 90 und 98 %.
Bei der Dampfphasenmethylierung von Phenol werden hauptsächlich Metalloxidkatalysatoren eingesetzt. Diese Katalysatoren beeinflussen Reaktionstemperatur, Produktverteilung und Selektivität.
Magnesiumoxidkatalysatoren erzielen eine hohe Orthoselektivität und minimieren die m- und p-Kresolbildung selbst bei erhöhten Temperaturen (420–460 °C). Ihre Leistung kann durch Kombination mit anderen Metalloxiden (z. B. Alkalimetallen, Mangan, Kupfer) gesteigert werden.
Niedrigere Reaktionstemperaturen sind mit anderen Katalysatorsystemen erreichbar. Manganoxid- oder Chromoxid-Katalysatoren arbeiten bei etwa 390 °C, während Vanadiumoxid- oder Eisenoxid-Katalysatoren bei 320–350 °C eingesetzt werden.
Diese werden häufig mit verschiedenen anderen Oxiden (z. B. Cer, Aluminium, Silizium) gemischt, um den Umsatz und die Selektivität für 2,6-Xylenol/o-Kresol zu verbessern. Diese Mischoxidsysteme tragen zudem dazu bei, die Katalysatorlebensdauer zu verlängern und die Methanolzersetzung zu reduzieren.
γ-Aluminiumoxid katalysiert die Reaktion bei 300–320 °C mit minimaler Methanolzersetzung und guter Stabilität. Aufgrund der begrenzten Phenolumwandlung ist jedoch ein erheblicher Produktrücklauf zur Kontrolle der Nebenproduktbildung erforderlich, und es sind komplexe Reinigungsschritte für 2,6-Xylenol erforderlich.
Katalysatoren mit stark sauren Zentren, wie Aluminiumoxide, Siliciumdioxid-Aluminiumoxid, Zeolithe, Aluminiumphosphate und Phosphorsäure-Kieselgur, fördern die Isomerisierung und Transmethylierung. Sie führen typischerweise zu Produkten mit höherem m/p-Kresol-Gehalt, insbesondere bei erhöhten Temperaturen.
Formselektive Zeolithe (z. B. Typ HKY) und Phosphorsäure-Kieselgur, die bei 250–300 °C reagieren, können eine hohe Selektivität für p-Kresol aufweisen, was zu m-/p-Kresol-Gemischen mit ca. 77–85 % p-Kresol führt. Modifizierte Pentasil-Zeolithe weisen ebenfalls Paraselektivität auf.
Alternative Methylierungsmittel sind Methylbenzole, Dimethylether, Methylamin, Methan, Kohlenmonoxid-Wasserstoff-Gemische und Formaldehyd-Wasserstoff-Gemische.
Die Dampfphasenmethylierung wird weltweit von Unternehmen wie General Electric Co. (USA, Niederlande), Inspec Fine Chemicals (Großbritannien), Chemopetrol (Tschechische Republik), Nippon Crenol (Japan), GEM Polymers (Japan), Mitsubishi Gas Chemical Company (Japan) und Honshu Chemical Industry Co. (Japan) eingesetzt.
4.2. Methylierung von Phenol in der Flüssigphase
Die Flüssigphasenmethylierung bietet eine Alternative zu Dampfphasenmethoden zur Synthese von Kresolen und Xylenolen. Bei diesem Verfahren werden typischerweise Oxidkatalysatoren wie γ-Al2O3 eingesetzt, die in einem Phenol-Methanol-Gemisch in einem Autoklaven bei 300–400 °C oder über einem Festbett in einem Rohrreaktor (z. B. 350 °C, 35 bar) suspendiert sind.
Ein bemerkenswertes industrielles Verfahren, das vom Chemischen Werk Löwi angewendet wird, reagiert Phenol mit einer äquimolaren Menge Methanol bei 350–400 °C unter Verwendung von Aluminiummethylat als Katalysator. Mit diesem Verfahren wird eine Ausbeute von ca. 80 % an Kresolen und Xylenolen aus ca. 60 % umgesetztem Phenol erreicht.
Neben o-Kresol als Hauptprodukt entstehen auch andere Isomere und Trimethylphenole, wobei die Produktverhältnisse über die Reaktionsparameter einstellbar sind. Die Gegenwart von Basen erhöht den Umsatz, während Säuren p-Kresol und 2,4-Xylenol begünstigen.
Ein weiteres bedeutendes Verfahren, das Biller-Verfahren (ehemals Union Rheinische Kraftstoff AG), nutzte wässrige Zinkhalogenid-Halogenwasserstoff-Lösungen als Katalysatoren unter milderen Bedingungen (200–240 °C, ca. 25 bar). Dieses Verfahren lieferte bis zu 98 % Kresol aus umgesetztem Phenol, produzierte jedoch größere Mengen an p-Kresol und 2,4-Xylenol, wobei p-Kresol unter optimierten Bedingungen nahezu m-Kresol-frei war.
Dieses Verfahren erforderte aufgrund des Katalysatorsystems hochkorrosionsbeständige Materialien.
Beide Flüssigphasenverfahren sind mit Herausforderungen verbunden, darunter die Rohstoffkosten (Phenol) und die komplexe Produkttrennung aufgrund ähnlicher Siedepunkte und strenger Reinheitsanforderungen.
4.3. Transmethylierung und Isomerisierung
Transmethylierungs- und Isomerisierungsprozesse ermöglichen die Umwandlung weniger erwünschter Methylphenol-Nebenprodukte und -Rückstände in wertvollere Kresol-Isomere, insbesondere o-Kresol und m-/p-Kresol-Gemische.
Diese Reaktionen erfolgen typischerweise durch Zugabe von Phenol zu Methylphenolrückständen (aus Phenolmethylierung oder anderen Quellen) oder zu ungenutzten Xylenolen. Der Prozess läuft entweder in der Dampfphase oder in der Flüssigphase bei Temperaturen zwischen 400 und 500 °C ab. Zu den gängigen Katalysatoren für diese Reaktionen gehören Aluminiumoxid, Chromoxid-Aluminiumoxid, Siliciumdioxid-Aluminiumoxid, Metalloxid-Eisenoxid und Magnesiumoxid-Wolframoxid.
Bei 2,6-Xylenol können die Transmethylierung und die damit verbundene Isomerisierung ohne Katalysator erfolgen. Diese nichtkatalytische Umwandlung kann in der Dampfphase bei 550–600 °C oder diskontinuierlich in der Flüssigphase bei 420–470 °C durchgeführt werden. Diese Verfahren können die Gesamtausbeute an o-Kresol aus der Phenolmethylierung steigern.
Chiyoda Chemical Engineering Construction Co. entwickelte ein Isomerisierungs-Transalkylierungsverfahren für Kresol-Isomerengemische. Dabei werden Kresolgemische mit Phenol an Siliciumdioxid-Aluminiumoxid-Katalysatoren bei 400 °C unter Normaldruck umgesetzt.
Das resultierende Gemisch kann rektifiziert werden, um reines o-Kresol zu isolieren, wobei alle anderen Phenolkomponenten recycelt werden.
Versuche, o-Kresol aufgrund schwankender Nachfrage mit Katalysatoren wie Aluminiumchlorid, Aluminiumfluorid, Bortrifluorid, Aluminiumsilikaten oder Aluminiumoxid zu m- und p-Kresol zu isomerisieren, waren bisher weitgehend unbefriedigend. Diese Methoden führten häufig zu unerwünschten Nebenreaktionen wie Verharzung und Disproportionierung zu Phenol und Dimethylphenolen.
Eine Isomerisierung ohne nennenswerte Disproportionierung ist jedoch mit Silica-Alumina-Zeolithen der ZSM-Gruppe möglich. Bei ca. 400 °C und o-Kresolumsätzen von 40–50 % erreichen diese Katalysatoren m-/p-Kresol-Selektivitäten von 90 % und ein m:p-Verhältnis von 7:3.
5. Weitere Kresol-Produktionsverfahren
Neben den primären industriellen Verfahren wurden verschiedene alternative Synthesen für Kresole erforscht, die häufig auf Isomereselektivität abzielen. Diese Verfahren werden in der Regel noch nicht im industriellen Maßstab eingesetzt.
5.1. Oxychlorierung von Toluol
Dieses Verfahren beinhaltet die Oxychlorierung von Toluol mit wässriger Salzsäure und Sauerstoff, katalysiert durch Salpetersäure und ein Palladium- oder Kupfersalz, bei ca. 100 °C. Es liefert hauptsächlich o- und p-Chlortoluol mit hoher Selektivität.
Die anschließende Dampfphasenhydrolyse des Chlortoluols erzeugt Kresol, wobei die freigesetzte Salzsäure recycelt wird. Dieses Verfahren zur Toluol-Oxychlorierung ist zwar effizient und bietet hohe Umsätze und Selektivitäten, erfordert aber umfangreiche Recyclingmöglichkeiten und korrosionsbeständige Anlagenmaterialien.
5.2. Oxidative Decarboxylierung von Methylbenzoesäuren
Methylbenzoesäuren können durch Einleiten eines Luft-Dampf-Gemisches durch ihre Schmelze bei 200–240 °C zu Kresolen decarboxyliert werden, katalysiert durch Kupfer- und Magnesiumsalze.
Die Dampfphasenoxidation mit Sauerstoff-Stickstoff-Gemischen an Mischkatalysatoren bei etwa 300 °C zeigt bessere Ergebnisse, wobei meta-Methylbenzoesäure selektiv m-Kresol liefert. Diese Methode ist komplexer als die Phenolherstellung und birgt Herausforderungen hinsichtlich Teerbildung und Nebenproduktbildung.
5.3. Baeyer-Villiger-Oxidation von p- oder o-Methylbenzaldehyd
Dieses Verfahren erzeugt p-Kresol aus p-Methylbenzaldehyd (oder o-Kresol aus o-Methylbenzaldehyd). Dabei reagiert Methylbenzaldehyd mit Perameisensäure (hergestellt aus Wasserstoffperoxid und Ameisensäure) zu Tolylformiat, das anschließend zu Kresol und Ameisensäure hydrolysiert wird. Das Verfahren liefert hohe Ausbeuten, wobei die Ameisensäure größtenteils recycelt wird.
5.4. Kernhydroxylierung von Toluol
Hierbei handelt es sich um die direkte Hydroxylierung von Toluol (oder Xylol) unter Verwendung verschiedener Oxidationsmittel (z. B. Sauerstoff, Wasserstoffperoxid, organische Peroxide) und Katalysatorsysteme (z. B. Friedel-Crafts-Katalysatoren, Übergangsmetallverbindungen, Mikroorganismen).
Obwohl umfassend erforscht, bestehen Herausforderungen in der Isolierung von Kresolen aus verdünnten Lösungen und der Notwendigkeit eines umfangreichen Recyclings teurer Hilfsstoffe. Beispielsweise können bestimmte Mikroorganismen regioselektiv p-Kresol produzieren, und bestimmte Systeme, die Wasserstoffperoxid mit starken Säuren oder titanmodifizierte Zeolithe verwenden, liefern o- und p-Kresolgemische.
5.5. Oxidative Methylierung von Toluol
Dieses Verfahren beinhaltet die adiabatische Oxidation von Toluol mit Sauerstoff, Methan und Wasserdampf bei hohen Temperaturen (700–750 °C) in einem Rohrreaktor. Es entsteht ein Gemisch aromatischer Verbindungen, darunter Ethylbenzol, Styrol, Benzol, Phenol und Kresol. Dies deutet auf ein Potenzial für die Kresolproduktion im petrochemischen Maßstab hin.
5.6. Hock-Reaktion von Toluolderivaten
Ähnlich wie beim Cymol-Kresol-Verfahren können auch andere Toluolderivate peroxidiert und gespalten werden, wobei Kresol und die entsprechende Carbonylverbindung entstehen. Beispiele hierfür sind Ethylidenbis(p-methylbenzol) und 4-Methylcyclohexylbenzol, die zur Herstellung von p-Kresol modifiziert werden können.
Die Oxidation von Xylol in Gegenwart von Essigsäure kann ebenfalls Kresylacetat ergeben, das anschließend zu Kresol hydrolysiert wird.
5.7. Hydrierung von N,N‘-Dialkylaminomethylphenolen
Bei dieser Methode reagiert Phenol mit Paraformaldehyd und einem sekundären Amin (z. B. Piperidin) zu Aminomethylphenolen, die anschließend über einem Palladium-Kohlenstoff-Katalysator hydriert werden. Dabei entstehen typischerweise o-Kresol und p-Kresol im Molverhältnis 1:2 mit hohen Ausbeuten bezogen auf umgesetztes Phenol.
5.8. Diels-Alder-Ringschluss von Isopren und Vinylacetat
Diese dreistufige Syntheseroute erzeugt selektiv p-Kresol. Isopren reagiert mit Vinylacetat in einer Diels-Alder-Cycloaddition zu 1-Methylcyclohexen-4-ylacetat, das anschließend verseift wird. Das entstehende 1-Methylcyclohexen-4-ol wird anschließend katalytisch zu p-Kresol dehydriert.
Referenzen
- Cresols and Xylenols; Ullmann’s Encyclopedia of Industrial Chemistry. – https://onlinelibrary.wiley.com/doi/abs/10.1002/14356007.a08_025
- Methylation of phenols. – https://patents.google.com/patent/US3446856A/en
- Synthesis method of o-cresol and m-cresol. – https://patents.google.com/patent/CN103992210A/en