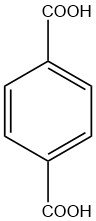
Terephthalsäure ist im Handel in Form eines frei fließenden Pulvers erhältlich, das aus abgerundeten Kristallen besteht. Beim langsamen Umkristallisieren bildet es Nadeln.
Die von WHINFIELD und DICKSON in den 1940er Jahren in Großbritannien durchgeführten Forschungsarbeiten brachten Terephthalsäure in den Vordergrund der wissenschaftlichen Gemeinschaft.
In den Vereinigten Staaten hatten CAROTHERS und seine Kollegen bereits das Potenzial zur Herstellung linearer Polyester mit hohem Molekulargewicht durch die Reaktion von Disäuren mit Diolen nachgewiesen. Allerdings hatten sie aliphatische Disäuren und Diole eingesetzt, die zu Polyestern führten, die für das Spinnen zu Fasern ungeeignet waren.
WHINFIELD und DICKSON entdeckten, dass symmetrische aromatische Disäuren hochschmelzende, kristalline und faserbildende Materialien ergeben. Infolgedessen entwickelte sich Poly(ethylenterephthalat) zur am häufigsten hergestellten synthetischen Faser.
Im Jahr 1992 belegten Terephthalsäure und Dimethylterephthalat hinsichtlich der Tonnage aller weltweit hergestellten Chemikalien etwa den 25. Platz und bei organischen Chemikalien etwa den zehnten Platz.
Inhaltsverzeichnis
1. Herstellung von Terephthalsäure
p-Xylol ist ein wichtiger Rohstoff für die Herstellung von Terephthalsäure und Dimethylterephthalat, die für die Herstellung von Polyesterfasern, -folien und -harzen unerlässlich sind.
Es wurden eine Reihe von Oxidationskatalysatoren und -bedingungen entwickelt, die zu einer nahezu quantitativen Oxidation der in p-Xylol vorhandenen Methylgruppen führen, wobei der Benzolring praktisch unberührt bleibt.
Diese Katalysatoren basieren im Allgemeinen auf Kobalt, Mangan und Brom oder Kobalt mit einem Cooxidationsmittel wie Acetaldehyd. Das in allen Prozessen verwendete Oxidationsmittel ist Sauerstoff, und Essigsäure wird in allen Prozessen bis auf einen als Reaktionslösungsmittel verwendet.
1.1. Amoco-Oxidation
Der von Scientific Design entdeckte Amoco-Oxidationsprozess macht etwa 70 % des weltweit produzierten Terephthalat-Rohstoffs aus. Es ist das am weitesten verbreitete Katalysatorsystem und wird in fast allen Neuanlagen eingesetzt.
Mitsui Petrochemical, jetzt Mitsui Sekka, entwickelte ebenfalls ein kommerzielles Verfahren und war ein früher Lizenznehmer von Mid-Century, und Amoco hat das Verfahren ebenfalls lizenziert.
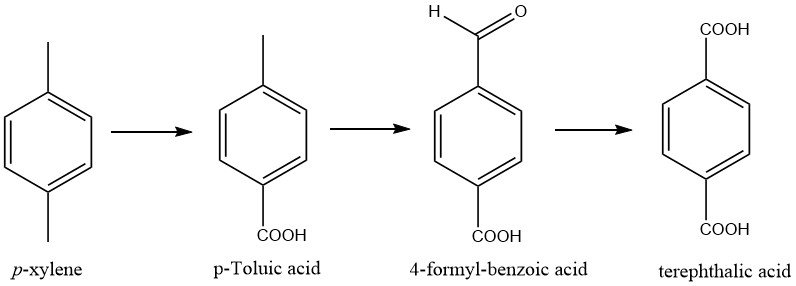
Bei der Herstellung von Terephthalsäure und Dimethylterephthalat wird p-Xylol als Ausgangsstoff verwendet. Dieses Ausgangsmaterial wird mithilfe eines löslichen Kobalt-Mangan-Brom-Katalysatorsystems oxidiert, was zu einer nahezu quantitativen Oxidation der Methylgruppen mit minimalen Xylolverlusten führt.
Die Reaktion wird mit Essigsäure als Lösungsmittel und Druckluft als Oxidationsmittel durchgeführt. Es können verschiedene Kobalt- und Mangansalze verwendet werden, und die Bromquelle kann HBr, NaBr oder Tetrabromethan sein.
Aufgrund der stark korrosiven Brom-Essigsäure-Umgebung erfordert der Prozess in einigen Teilen den Einsatz von mit Titan ausgekleideten Geräten.
Das Einsatzgemisch, bestehend aus p-Xylol, Essigsäure, Katalysator und Wasser, wird kontinuierlich dem Oxidationsreaktor zugeführt. Der Reaktor wird bei Temperaturen zwischen 175 und 225 °C und Drücken zwischen 1500 und 3000 kPa betrieben.
Über den stöchiometrischen Bedarf hinaus wird Druckluft zugeführt, um einen messbaren Sauerstoffpartialdruck bereitzustellen und eine hohe p-Xylol-Umwandlung zu erreichen.
Die Reaktion ist stark exotherm und setzt Wasser und Wärme frei. Die Reaktion von 1 Mol p-Xylol mit 3 Mol Disauerstoff führt zur Bildung von 1 Mol Terephthalsäure und 2 Mol Wasser.
Nur vier Wasserstoffatome, die etwas mehr als 2 Gew.-% des p-Xylol-Moleküls ausmachen, sind nicht in Terephthalsäure eingebaut.
Terephthalsäure ist im Lösungsmittel nicht gut löslich, was dazu führt, dass sie bei ihrer Bildung ausfällt. Dadurch entsteht ein Dreiphasensystem bestehend aus festen Terephthalsäurekristallen, Lösungsmittel mit etwas gelöster Terephthalsäure und Dampf aus Stickstoff, Essigsäure, Wasser und einer kleinen Menge Sauerstoff.
Die Reaktionswärme wird durch Verdampfen des Lösungsmittels entfernt, und es wird eine Verweilzeit von bis zu 2 Stunden verwendet. Die Ausbeute an Terephthalsäure beträgt über 95 Mol-%, wobei über 98 % des p-Xylols reagieren.
Durch die vollständige Oxidation zu Kohlenoxiden gehen jedoch geringe Mengen an p-Xylol und Essigsäure verloren, und im Reaktorabfluss sind Verunreinigungen wie Oxidationszwischenprodukte vorhanden.
Die hervorragende Ausbeute und der geringe Lösungsmittelverlust in einem einzigen Reaktordurchgang machen diese Technologie für neue Anlagen universell einsetzbar.
Die Oxidation der Methylgruppen in p-Xylol erfolgt schrittweise, wobei während des Prozesses zwei Zwischenprodukte, p-Toluylsäure und 4-Formylbenzoesäure, gebildet werden.
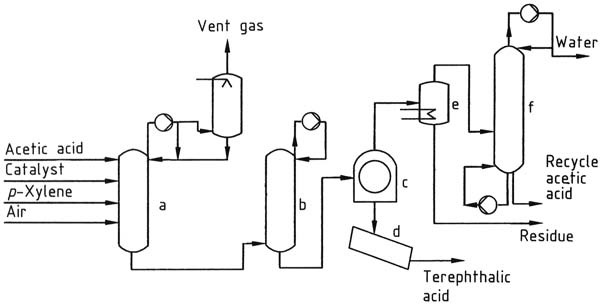
a) Oxidationsreaktor; b) Druckausgleichsgefäß; c) Filter; d) Trockner; e) Rest noch vorhanden; f) Dehydrationskolonne
1.2. Mehrstufige Oxidation
Zahlreiche Unternehmen in Japan haben Methoden entwickelt, um die Konzentration von 4-Formylbenzoesäure durch die Einführung strengerer Oxidationsverfahren auf 200–300 ppm zu senken.
Solche Verfahren haben es ermöglicht, einen separaten Reinigungsschritt wegzulassen, da die Konzentration von 4-Formylbenzoesäure ausreichend niedrig ist, um Terephthalsäure als Ausgangsmaterial für einige Polyesterprodukte zu verwenden, die keine hohe Reinheit des Ausgangsmaterials erfordern.
Diese Kategorie von Terephthalsäure wird allgemein als Terephthalsäure mittlerer Reinheit bezeichnet, die etwa 11 % der insgesamt produzierten Terephthalsäure ausmacht.
Bei den meisten dieser Verfahren kommt das von Scientific Design entdeckte Katalysatorsystem zum Einsatz.
Mitsubishi Kasei und seine Lizenznehmer produzieren den Großteil der mittelreinen Terephthalsäure. Sie haben dieses Produkt Q-PTA genannt, das im Allgemeinen eine 4-Formylbenzoesäure-Konzentration von etwa 290 ppm aufweist.
Mitsubishi hat außerdem einen intensiveren Oxidationsprozess eingeführt, der den Gehalt an 4-Formylbenzoesäure weiter reduziert. Dieses Produkt trägt den Namen S-QTA.
Um p-Xylol in Essigsäure mit einem Kobalt-Mangan-Brom-Katalysator zu oxidieren, ähnelt die Methode der Amoco-Oxidation.
Die Aufschlämmung wird auf 235 – 290 °C erhitzt und in einem weiteren Reaktor weiter oxidiert. In Verbindung mit einer Temperaturerhöhung kann mehr Katalysator eingeführt werden.
Erhitzen führt zu einer verbesserten Löslichkeit von Terephthalsäure, was zur Freisetzung von 4-Formylbenzoesäure und farbigen Verunreinigungen führt, wenn sich die Kristalle auflösen.
Obwohl Terephthalsäure bei höheren Temperaturen nicht vollständig löslich ist, können Kristalle aufgeschlossen werden. Der Aufschluss ist ein dynamischer Gleichgewichtsprozess, bei dem sich Kristalle weiter auflösen und neu formieren, wodurch die Freisetzung von 4-Formylbenzoesäure in die Lösung erhöht wird, wo die Oxidation abgeschlossen werden kann.
Während die Notwendigkeit eines separaten Reinigungsprozesses entfällt, ist für den Oxidationsprozess ein zusätzlicher Reaktor erforderlich.
Darüber hinaus neigt Essigsäure bei höheren Temperaturen dazu, stärker zu Kohlenoxiden und Wasser zu oxidieren. Das Mitsubishi-Verfahren umfasst die Fest-Flüssigkeits-Trennung und Trocknung, um das pulverförmige Produkt zu erhalten.
Die Essigsäure muss entwässert und zur Verwendung im Prozess recycelt werden.
2. Verwendung von Terephthalsäure
Gesättigte Polyester werden hauptsächlich unter Verwendung von Terephthalsäure und Dimethylterephthalat hergestellt. Poly(ethylenterephthalat), ein alternierendes Copolymer aus Terephthalsäure und 1,2-Ethandiol, ist der vorherrschende Typ und deckt über 90 % der Nachfrage mit einem weltweiten Verbrauch von mehr als 12 Millionen Tonnen.
Polyester werden hauptsächlich in Textil- und Industriefasern verwendet, die 75 % des Marktes ausmachen. Polyester ist derzeit die volumenmäßig größte synthetische Faser, für die sie verwendet wird.
Das am schnellsten wachsende Segment des Polyestermarktes sind Lebensmittel- und Getränkebehälter, auf die 13 % der Nachfrage entfallen. Filme für Audio, Video und Fotografie machen 7 % des Marktes aus.
Poly(butylenterephthalat) ist ein Hochleistungsformharz, das durch die Reaktion von Terephthalsäure mit 1,4-Butandiol hergestellt wird. Es findet Verwendung in speziellen Industriebeschichtungen, lösungsmittelfreien Beschichtungen, Elektroisolierlacken, Aramidfasern und Klebstoffen.
Eine kleine Menge Bis(2-ethylhexyl)terephthalat wird als Weichmacher hergestellt, während ein Teil Dimethylterephthalat ringhydriert wird, um das Cyclohexan-Analogon 1,4-Cyclohexandicarbonsäure für Spezialpolyester und Beschichtungen herzustellen.
Referenz
- Terephthalic Acid, Dimethyl Terephthalate, and Isophthalic Acid; Ullmann’s Encyclopedia of Industrial Chemistry. – https://onlinelibrary.wiley.com/doi/10.1002/14356007.a26_193.pub2