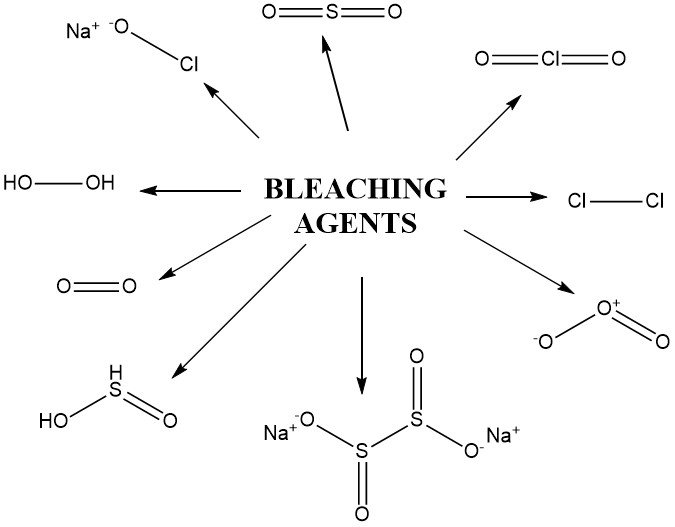
Introduction
The process of achieving a bleaching effect involves the removal of chromophores. This can be accomplished by adsorbing the colored compounds onto active surfaces such as active carbon or bleaching clays.
This method is commonly employed on an industrial scale to bleach and purify liquids like vegetable oil. Another commonly used approach in industrial settings is the chemical destruction of chromophores in organic or inorganic compounds, which is often combined with purification or cleaning processes.
This is particularly important for natural products, which often contain impurities. For instance, cotton is contaminated with seed-capsule residues, wax, fatty constituents, and inorganic compounds. By bleaching cotton, its brightness is enhanced while impurities are simultaneously removed. Bleaching can also serve as a continuation or supplement to previous processing steps.
To illustrate, in the context of chemical pulping, bleaching removes lignin from wood fibers, resulting in increased brightness and further purification of the cellulose. Achieving nearly colorless bleaching without causing damage is challenging and requires expertise. The objective of bleaching from the beginning may also be to create a more uniform hue, such as bleaching wood veneer.
In terms of volume and product value, the bleaching of fibrous materials for paper and textile production holds significant importance.
Table of Contents
1. Mechanism of Bleaching
Bleaching can be categorized into oxidative and reductive bleaching. Oxidative bleaching irreversibly destroys chromophores, while reductive bleaching can be reversible, such as through reoxidation by atmospheric oxygen.
In the case of natural products, the complete chemical composition of the colored compounds is often not known. Generally, these compounds contain conjugated carbon-carbon double bonds, such as polymethine chains, aromatic systems, or quinoid systems. Oxidative bleaching disrupts the double bonds, eliminates the conjugation, and generates chemical compounds with lower molecular weight.
Effective bleaching often involves a multi-step process. Repeating acidic oxidation and alkaline extraction allows for moderate conditions and low chemical concentrations to be maintained.
The bleaching effect is measured by the increase in brightness. Remission photometers are utilized to determine brightness relative to a standard at multiple wavelengths, with BaSO4 being the most commonly used standard. However, there are alternative methods available to assess brightness. The stability of brightness also serves as an indicator of the quality and efficiency of the bleaching process.
Excessive oxidation can lead to the formation of new chromophores or potential yellowing in the future. Yellowing occurs if the auxochrome groups in a chromophore can be reoxidized. Light and heat can cause color changes in bleached materials.
UV radiation readily breaks carbon-carbon bonds, producing radicals. The recombination of these radicals with oxygen or other parts of the molecule can generate new chromophores.
During bleaching processes, it is important to ensure that the degree of polymerization of the treated polymers is not negatively affected. A decrease in molecular weight can impact fiber strength and reduce economic value.
Therefore, bleaching should target chromophores while preserving the molecular structure. The complexity of raw materials has led to the development of various bleaching methods.
For example, bleaching cotton differs from bleaching wool. While strong alkaline conditions can be applied to bleach the carbohydrate polymer cellulose (cotton), the keratin (protein) wool fiber is highly sensitive to alkali. Alkaline bleaching cannot be used as it would result in the destruction of the polymer through the extraction of amino acids.
2. Bleaching Agents
2.1. Pretreatment
The preparation for a bleaching process involves the removal of contaminants. A common pretreatment method is washing. Sheared wool, for example, can contain a significant amount of sand and fatty material (lanolin), up to 50 wt %.
Similarly, compounds that consume or decompose the bleaching agent must be eliminated prior to the actual bleaching process. Washing with surfactants or chelating compounds is a standard procedure to achieve this.
It reduces the demand for bleaching agents and minimizes the potential for negative side reactions during bleaching. In the case of chemical pulp bleaching, this is often a crucial requirement.
Acid washing at a pH below 3 dissolves metal ions. The presence of reducing agents like sulfur dioxide, which lower the oxidation state of metals, can enhance this effect. Chelating agents such as sodium salts of diethylenetriaminepentaacetic acid (DTPA) or ethylenediaminetetraacetic acid (EDTA) are used under mildly acidic conditions (pH 5-6) to accelerate the removal of metals.
This pH range allows the elimination of transition metals while preserving magnesium and calcium ions, which serve as stabilizers in the bleaching process. For chemical pulp produced through alkaline pulping, this metals-removal stage is necessary if a totally chlorine-free (TCF) bleaching process is to be implemented.
In conventional or elemental chlorine-free (ECF) bleaching, metals are removed during the acidic chlorine dioxide stages. In acid sulfite pulping, they are solubilized during the pulping process and eliminated in brown stock washing.
During alkaline pulping of hardwood, xylan polymer double bonds are generated. These hemicellulose compounds consume electrophilic bleaching chemicals. An acid pretreatment at around 90 °C and pH below 3 is conducted to hydrolyze these compounds, producing furancarboxylic acid. This helps reduce the demand for bleaching chemicals.
Enzymes such as xylanase can be used as a pretreatment. During alkaline pulping, xylan dissolves but may precipitate again in the final stages of the cooking procedure, posing challenges for bleaching. Xylanase enzyme removes the precipitate and facilitates the bleaching process. Enzymes extracted from thermophilic bacteria with high temperature and pH tolerance are preferred for this purpose.
In textile bleaching, treatments with amylase or peroxosulfate may be necessary to remove starch.
2.2. Oxidizing Agents
In ancient times, oxidative bleaching of textiles was practiced by the Egyptians and Phoenicians using sunlight combined with a mild alkaline treatment involving potassium carbonate leached from wood ashes.
In the 1700s, a bleaching method known as “Dutch bleaching” emerged, which involved alternating treatments with potassium carbonate, sunlight exposure on grassy meadows, and sour milk. This technique reached its pinnacle near Haarlem, Netherlands.
Advancements in chemical knowledge in the late 1700s led to the discovery of a new bleaching agent, hypochlorite. Potassium hypochlorite (Eau de Javelle), sodium hypochlorite (Eau de Labarraque), and calcium hypochlorite became the most significant industrial bleaching agents for almost 150 years.
Chlorine was introduced to chemical pulp bleaching in the 1930s, followed by chlorine dioxide and hydrogen peroxide a decade later.
The industrial use of oxygen as a bleaching agent for chemical pulp began in the late 1960s, and ozone was subsequently incorporated into chemical pulp bleaching sequences.
Other oxidizing compounds employed for bleaching include hydrogen peroxide derivatives like peracetic acid, sodium perborate, peroxodisulfates (persulfates), and peroxomonosulfates (Caro’s acid). These compounds are used under specific conditions, including potassium permanganate.
2.2.1. Oxygen
The utilization of oxygen as a bleaching agent has experienced a significant rise since the early 1970s. It is employed in the bleaching of chemical pulp to sustain and intensify the degradation of lignin, which typically initiates during alkaline pulping.
Oxygen delignification requires alkaline conditions, usually with sodium hydroxide (NaOH), for the oxidation process. It also necessitates relatively high temperatures (75-100 °C) and an oxygen pressure of 0.3-0.5 MPa. Increasing the temperature, pressure, or concentration of caustic soda enhances the oxidation rate.
The process of oxygen delignification involves two simultaneous reactions: desired delignification and undesired degradation of carbohydrates. Consequently, practical limits exist for temperature increase and alkali quantity. The reduction in the degree of polymerization is partially hindered by magnesium salts.
Although the impact of oxygen on chemical pulp is limited, its treatment reduces the demand for other bleaching chemicals by 40-50%. Oxygen delignification enables the combined recovery of effluents from pulping and subsequent delignification steps, effectively reducing the total discharge of organic material from the bleaching plant.
In magnesium-based pulping processes, such as magnesium sulfite pulping, the oxygen stage can be conducted using magnesium hydroxide or oxide as the source of alkali. Typically, hydrogen peroxide is added simultaneously (at approximately 90 °C) to expedite the delignification rate.
2.2.2. Chlorine Dioxide and Sodium Chlorite
Chlorine dioxide is an exceptionally selective bleaching agent that was first utilized in the bleaching of chemical pulp in 1946.
Chlorine dioxide possesses an unpaired electron, rendering it a free radical with limited stability. It exists as a gas under standard conditions and can spontaneously explode at partial pressures exceeding 40 kPa, breaking down into chlorine and oxygen.
When exposed to heat or light, even lower concentrations of chlorine dioxide can explode, albeit with reduced violence. Consequently, pure chlorine dioxide cannot be transported or stored. Instead, it is generated on-site and typically handled as a diluted aqueous solution.
The primary industrial method for chlorine dioxide generation involves the reduction of chlorate. Historically, the Mathieson process, which employs sulfur dioxide for reduction, played a significant role. Dilute sulfuric acid and sodium sulfate or sodium hydrogen sulfate are produced as byproducts.
Alternative processes with fewer byproducts employ hydrochloric acid, methanol, or hydrogen peroxide as the reducing agent. Hydrochloric acid offers the advantage of low cost but results in a relatively high amount of chlorine present as a byproduct in the chlorine dioxide, leading to increased formation of undesired halogenated products during bleaching.
Today, the methanol and hydrogen peroxide processes are the most prominent methods. These processes generate highly pure chlorine dioxide gas, which is diluted with air or water vapor to prevent explosions.
The gas is then absorbed in cold water to achieve a concentration of 6-12 g/L. For reactions of chlorine dioxide with pulp, a pH value between 2 and 5 is typically maintained. Within this pH range, chlorine dioxide does not impact the degree of polymerization of cellulose.
The recommended reaction temperature for chlorine dioxide is between 50 and 75 °C. In the bleaching of hardwood pulp, initiating bleaching at high temperatures (> 90 °C) is favorable as it allows simultaneous oxidation of lignin and hydrolysis of hexenuronic acids.
In textile bleaching, sodium chlorite is employed as the chlorine dioxide source. Hydrochloric acid, formic acid, or acetic acid is used to liberate chlorine dioxide through the following reaction:
5 NaClO2 + 4 HCl → 4 ClO2 + 2 H2O + 5 NaCl
2.2.3. Hydrogen Peroxide and other Peroxo Compounds
Hydrogen peroxide has served as an industrial bleach since the early 1900s, primarily in the bleaching of textile fibers.
Sodium perborate, NaBO3·4 H2O, derived from sodium peroxide and borax, has been used as a bleach in laundry detergents like Persil as early as 1907. To this day, perborates and percarbonates are extensively employed in laundry detergents due to their mild bleaching effect at elevated temperatures, which is gentler on fibers compared to the harsher hypochlorites used as cold bleaches. Special coated products are applied to enhance the storage stability of pure percarbonate.
Aqueous solutions of hydrogen peroxide are commercially available in concentrations up to 90 wt %. Solutions with 35-70 wt % are commonly used in bleaching.
The most significant application of hydrogen peroxide is in the bleaching of pulp for paper production. Mechanical pulp and chemical pulp are bleached using alkaline peroxide solutions. Hydrogen peroxide is also employed for bleaching textile fibers such as cotton, flax, wool, and synthetics.
Commercial hydrogen peroxide bleaching processes generally operate under slightly to strongly alkaline conditions. Sodium hydroxide is commonly used as the alkali source. The initial reaction involves the nucleophilic addition of hydroperoxide anions to carbonyl groups. Consequently, the addition of alkali enhances the bleaching rate:
HOOH+ OH– ↔ HOO– + H2O
However, alkaline conditions also promote side reactions such as the disproportionation of hydrogen peroxide into oxygen and water:
HOO– + H2O2 → H2O + OH– + O2
The bleaching outcome depends on activation and stabilization. The reaction rate increases with temperature and alkali concentration.
However, at high temperatures, side reactions such as the thermal decomposition of hydrogen peroxide into radicals become more likely, potentially leading to yield losses and solubilization of the material being bleached. Therefore, the typical temperature range for peroxide bleaching is between 60 and 90 °C.
Stabilization of the alkaline bleaching solution may be necessary to minimize peroxide decomposition. Hydroxyl radicals, generated through peroxide decomposition, are highly unselective oxidizing agents that cause undesired side reactions.
In chemical pulp bleaching, chelation of transition metals is only necessary in TCF (totally chlorine-free) bleaching. In ECF (elemental chlorine-free) bleaching, hydrogen peroxide is typically applied following an acidic stage, which removes transition metals during the washing step.
For mechanical pulp bleaching, detrimental metals are best removed by pretreatment with a chelating agent. Commonly used chelating agents are the sodium salts of diethylenetriaminepentaacetic acid (DTPA), ethylenediaminetetraacetic acid (EDTA), or similar phosphonates with comparable or superior chelating abilities.
Stabilizers like sodium silicate and magnesium salts (mostly magnesium sulfate) are also employed. These stabilizers help precipitate or absorb detrimental compounds on colloidal silica or magnesium hydroxide.
During the bleaching process, hydrogen peroxide cleaves side chains and irreversibly destroys quinoid structures. The oxidation and destruction of quinones are crucial for achieving good brightness stability. Peroxide-bleached products exhibit lower reversion compared to other oxidants.
Peracetic acid is used in small amounts as an activation step prior to alkaline hydrogen peroxide treatment. Its application allows for a higher increase in brightness or a lower overall consumption of bleaching chemicals.
The reaction with pulp is carried out under mildly acidic conditions, predominantly involving the hydroxylation reaction of residual lignin. Peracetic acid is produced by mixing acetic acid and hydrogen peroxide.
In the presence of a strong acid (e.g., sulfuric acid), a rapid equilibrium is established among acetic acid, peracetic acid, hydrogen peroxide, and water. As the other compounds in the mixture do not contribute to the bleaching reaction of peracetic acid, the use of equilibrium peracetic acid is costly.
Distilled peracetic acid is an alternative, obtained through vacuum distillation of equilibrium peracetic acid, resulting in a relatively pure peracetic acid solution in water. Distilled peracetic acid with a content of about 35% in water should be stored below 4 °C to prevent the slow re-establishment of the equilibrium with hydrogen peroxide and acetic acid at higher temperatures.
Another option is on-site mixing, which yields a peracetic acid/peroxide mixture that can be used for an initial peracetic acid reaction followed by a subsequent peroxide bleaching step. This is achieved by adding sufficient alkali after the acidic stage.
Peracetic acid can also be generated in situ from hydrogen peroxide and tetraacetylethylendiamine (TAED) under weakly alkaline conditions. This procedure is applied in laundering agents using percarbonate or perborate as a peroxide source and is also applicable in specialty bleaching.
Potassium peroxosulfate (KHSO5) is used for bleaching polyamide and cellulose fibers, although it is primarily employed to clean wool and reduce its shrinkage.
Sodium peroxodisulfate (Na2S2O8) and ammonium peroxodisulfate ((NH4)2S2O8) are used in cotton desizing and occasionally as additives in hydrogen peroxide bleaching.
2.2.4. Ozone
Ozone is generated through a silent electrical discharge from oxygen. In the bleaching of pulp, ozone is typically produced using pure oxygen. This method allows for a high concentration of ozone in the gas (up to 12 wt %) and facilitates the mixing process.
To maintain effective bleaching, ozone is used at a pH below 4. It is important to keep the temperature below approximately 50 °C to prevent side reactions with cellulose caused by its high oxidation potential. Higher temperatures can result in less stable brightness and easy yellowing.
2.2.5. Chlorine and Hypochlorites
Historically, chlorine was widely utilized for lignin oxidation (delignification) in chemical pulp bleaching. Chlorination involves substitution and oxidation of the aromatic rings in lignin, resulting in the production of dicarboxylic acid and chlorinated lignin fragments.
Around 10% of the applied chlorine is found as halogenated compounds in the effluent, including chlorinated phenols and polyhalogenated dibenzodioxins and dibenzofurans.
These compounds are analyzed quantitatively using an extractive method with activated carbon, and the measurement is expressed as adsorbable halogenated organic compounds (AOX).
Some of these compounds are mutagenic, leading to a phase-out of chlorine application in most regions after the identification of these substances in the effluent.
Currently, hypochlorite is primarily used as a stain remover, known as “cold bleach” in laundering. In chemical pulp bleaching, its application is limited to small amounts for controlled reduction of the degree of polymerization of dissolving pulp.
Hypochloric acid (HOCl) has a higher oxidation potential (+1.50 V) compared to chlorine (+1.35 V) or hypochlorite (OCl–) (+0.94 V). To prevent side reactions, especially depolymerization caused by aggressive hypochloric acid, bleaching is conducted in alkaline solutions to minimize the concentration of undissociated hypochloric acid.
Alkaline conditions result in fewer unfavorable side reactions since the hypochlorite anion is a weak nucleophile incapable of attacking electron-rich aromatic systems. However, bleaching with hypochlorite does generate halogenated compounds as byproducts, with AOX formation significantly lower than with chlorine. The main byproduct is chloroform.
Sodium hypochlorite solutions with active chlorine concentrations of 150-160 g/L are commercially available. The term “active chlorine” refers to the amount of chlorine liberated upon acidification of the hypochlorite solution.
2.3. Reducing Agents
The primary reducing bleaching agent is sodium dithionite, which has been used for wool bleaching since ancient times. However, its significance has diminished. Sulfinic acid derivatives are mainly employed for removing colorants from textile fabrics.
2.3.1. Sodium Dithionite
Sodium dithionite (Na2S2O4), also known as hydrosulfite in North America (despite the initial incorrect description), is currently produced from sodium formate and sulfur dioxide. Previously, zinc dithionite obtained from sulfur dioxide and zinc dust was more prevalent than the sodium salt.
However, the environmental concerns associated with zinc have led to the discontinuation of on-site production of zinc dithionite using zinc dust or sodium amalgam. Sodium dithionite can be generated on-site in some paper mills by using alkaline sodium borohydride solution, sodium bisulfite, and sulfur dioxide.
Sodium dithionite is available in crystalline powder form (90% Na2S2O4) or as a refrigerated 150 g/L solution stabilized with alkali. Solutions should be stored well below 10 °C to prevent dithionite from disproportionating to thiosulfate and bisulfite.
Dithionite acts by reducing carbonyl groups to alcohols and quinones to phenols, thereby destroying chromophores. It is used for bleaching mechanical pulp, wool, silk, bristle, hair, straw, soap, glue, kaolin, and various food products such as sugar, molasses, gelatin, and edible fats.
Dithionite is susceptible to oxidation by oxygen, converting it to sulfite and sulfate. At elevated temperatures, the solution decomposes to thiosulfate, sulfite, hydrogen sulfide, or sulfur, with the specific products dependent on pH. The pH chosen for dithionite bleaching is a compromise between effective bleaching and minimal dithionite loss, typically around pH 5-6 at temperatures of 50-80 °C.
In mechanical pulp bleaching, hydrogen peroxide and dithionite bleaching are often combined in two sequential steps.
2.3.2. Sulfur Dioxide
Sulfur dioxide is predominantly used in the form of sodium hydrogensulfite (NaHSO3). However, due to its relatively poor bleaching effect, SO2 is no longer widely employed. It can be utilized as a pretreatment in mechanical pulp production before dithionite bleaching and also finds application in wool treatment.
2.3.3. Sulfinic Acid Derivatives
The important sulfinic acid derivatives include sodium hydroxymethanesulfinate and formamidinesulfinic acid.
Hydroxymethanesulfinates are produced by treating dithionites with formaldehyde and are more stable than dithionites. They require higher temperatures to achieve their full reducing power.
These derivatives are employed in processes operating above 75 °C, where dithionite would rapidly decompose. They find application in bleaching soap, glue, gelatin, fatty acids, and primarily in dyeing processes.
Formamidinesulfinic acid, also known as thiourea dioxide, is obtained from thiourea and hydrogen peroxide. It is a poorly water-soluble crystalline product that becomes more soluble under alkaline conditions and exhibits its highest reducing power above 80 °C.
This acid is used to enhance the brightness of textiles and remove dyes from fabrics, similar to hydroxymethanesulfinic acid. Its strong reducing power at high temperatures makes it suitable for bleaching secondary fibers during the dispersing step and is particularly effective in destroying colorants used for colored paper.
3. Enzymes
The technical use of enzymes in bleaching is not yet widely adopted and remains the exception in industrial processes. While the discovery of lignin-degrading enzymes in white rot fungi offered potential for industrial-scale delignification and bleaching, there were challenges that limited their practical application.
The reaction catalyzed by these enzymes was slow and not selective enough, and the enzymes required coenzymes that degraded cellulose, which was undesirable.
One of the general problems with enzyme application is the need for highly pure enzyme strains to avoid negative side reactions caused by other enzymes. Moreover, many industrial processes operate at elevated temperatures or extreme pH levels, which necessitate the use of enzymes adapted to these conditions.
Thermophilic organisms, which thrive in high-temperature environments, are often preferred as a source for selecting enzymes with suitable properties.
Specific enzymes have been investigated for their potential in bleaching processes. Xylanases, for example, are used to remove a portion of the precipitated xylan from unbleached kraft pulps. This treatment reduces the demand for chlorine dioxide in elemental chlorine-free (ECF) bleaching by approximately 10%.
It is believed that lignin on the fibers is partly covered by precipitated xylan, and removing the xylan makes it easier to wash off the lignin. However, the overall effect of xylanase application is moderate, and it remains a niche option for pulp mills with limited access to chlorine dioxide.
Laccase is an enzyme involved in the polymerization of phenylpropane units in plants, contributing to the formation of the lignin polymer. Laccase can be used for pulp delignification with the help of a mediator.
Mediators can be easily converted to radical cations by laccase and oxygen, and these intermediate products oxidize the lignin. Theoretically, the mediator can be reoxidized multiple times by the enzyme, but in practice, repeated reactions are rare. As a result, the demand for the mediator, such as N-hydroxybenzotriazole, is high, making industrial application economically unviable.
Cellulases, a group of enzymes that break down cellulose, have been used to soften cotton fabric. They are applied in the stone washing of jeans as a substitute for the mechanical effect of pumice stones. The action of cellulases on the fabric surface causes fading of the color since the colorant is primarily located on the outer layer of the fibers.
Cellulases have also been suggested for improving the fiber strength of wastepaper pulp. By dissolving fines and fibrils, cellulases can increase the average fiber length and enhance the strength potential. However, this solubilization process reduces yield and increases the load on the effluent, making large-scale application unlikely from an economic and environmental perspective.
Reference
- Bleaching; Ullmann’s Encyclopedia of Industrial Chemistry. – https://onlinelibrary.wiley.com/doi/10.1002/14356007.a04_191.pub2