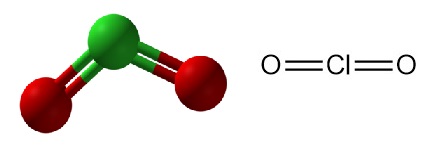
Chlorine dioxide is an inorganic chemical compound with the formula ClO2. It exists as a yellowish-green gas at room temperature, a reddish-brown liquid between 11 °C and −59 °C, and as bright orange crystals below −59 °C. It is usually handled as an aqueous solution and is produced on-site for industrial applications.
Chlorine dioxide is used primarily in the bleaching of chemical wood pulp. Historically, elemental chlorine was the dominant bleaching agent. However, due to significant environmental concerns associated with its use, chlorine dioxide has become the preferred alternative since the late 1980s.
Table of Contents
1. Properties of Chlorine Dioxide
Chlorine dioxide (ClO2) is a chlorine-oxygen compound with a chlorine atom that has a valence of four. It possesses a molecular weight of 67.45 g/mol, a melting point of -59 °C, and a boiling point of 11 °C.
This property makes chlorine dioxide a gas at room temperature. This gas has a distinct odor, similar to chlorine but with a pungent character. It is easily detected at low concentrations. However, inhalation at moderate concentrations can be hazardous, causing respiratory damage.
Due to safety and economic concerns, commercially available chlorine dioxide does not exist in pure gas, liquid, or solid forms. For small quantities, stabilized forms are available.
Chlorine dioxide readily dissolves in water, exhibiting a color ranging from pale yellow to dark greenish yellow depending on concentration (both in gas and solution phases). It is highly soluble in pure water, reaching approximately 60 g/L. Solubility is inversely proportional to temperature; it decreases as temperature rises. The dissolving process does not involve hydrolysis or dimerization.
Chlorine dioxide has an absorption maximum at 360 nm. While not particularly distinct, this peak can be used to measure chlorine dioxide concentration in gas, aqueous, and even organic solutions.
The chlorine dioxide molecule is inherently unstable from a thermodynamic perspective. Kinetic limitations allow for handling in the gas phase, but strict limitations exist. Vapor pressure must not exceed 10–12 kPa to prevent rapid decomposition with potentially explosive hazards.
Chlorine dioxide is relatively stable when absorbed in aqueous solutions (due to the heat of the solution), especially under cool and dark conditions. However, vapor pressure over such solutions necessitates concentration limitations (around 1 wt%) to avoid hazardous vapor pressure buildup. Additionally, the formation of crystalline ClO2·8 H2O can occur. Chlorine dioxide can also be dissolved in various other solvents.
The two chlorine-oxygen bonds possess a double-bond character with a bond angle of 117.5°. With 19 valence electrons, including one unpaired electron, chlorine dioxide has a radical-like behavior, enabling diverse reaction pathways.
Similar to all chlorine oxides, it presents a high explosion risk under thermal or physical shock. Compression of the gas phase must be strictly avoided.
Chlorine dioxide acts as a strong oxidizing agent, causing the spontaneous and sometimes explosive ignition of organic matter. In aqueous solutions, it oxidizes hydrocarbons to ketones and alcohols.
2. Industrial Production of Chlorine Dioxide
Chlorine dioxide (ClO2) is produced from either sodium chlorite (NaClO2) or sodium chlorate (NaClO3). Both of these starting materials are relatively stable, despite their oxidizing potential.
Production methods involve either the reduction of chlorate or the oxidation of chlorite. However, chlorate reduction remains the dominant method due to its cost-effectiveness, especially for large-scale applications exceeding 2,000 kg/day of ClO2. Smaller-scale operations can use either chlorite or chlorate.
The main reaction for chlorate reduction is:
ClO3– + reducing agent + acid → ClO2 + byproducts
This process occurs within a strong electrolyte medium containing a powerful acid (sulfuric or hydrochloric acid) and a reducing agent (typically methanol). The reducing agent selectively reduces the chlorine atom’s valence by one unit. Maintaining a stoichiometric excess of acid and reducing agent optimizes economics as chlorate is the most expensive raw material.
Cost-effectiveness is a crucial factor driving process selection. However, accessibility and safety of the ClO2 supply are equally important. Effective chlorine dioxide production processes minimize environmental impact and adhere to safety regulations.
Today, there are two major process arrangements for the reduction of chlorate:
- Vacuum processes offer a more complex approach but yield superior overall production economics for large-scale operations. These processes retain raw materials in the reactor while crystallizing and separating byproduct salts.
- Atmospheric processes use a reactor series to achieve a complete reaction. Spent acid effluent from these systems contains byproducts, residual chlorate, and significant amounts of acid.
The production process is not as simple as it seems; several competing and parallel reactions can exist, often involving 10–20 individual steps.
Careful control of reactant concentrations and purity is essential to achieve optimal yields and generator efficiencies. Process adjustments can be made to meet specific production capacity and minimal byproduct formation requirements without significant investment.
2.1. Production of Chlorine Dioxide from Chlorate Using Methanol as Reducing Agent
The reaction between sodium chlorate, methanol, and sulfuric acid represents the leading industrial route for chlorine dioxide production:
9 NaClO3 + 2 CH3OH + 6 H2SO4 → 9 ClO2 + 3 Na3H(SO4)2 + 0.5 CO2 + 1.5 HCOOH + 7 H2O
This equation seems straightforward, but it involves numerous competing reaction steps. Nevertheless, this process remains the most cost-effective and reliable method, accounting for roughly 75% of global ClO2 production. It offers several advantages:
- Economic Efficiency: The process has low operational costs.
- Reliability: Consistent and reliable production is achievable.
- Minimal Chlorine Formation: Elemental chlorine formation is minimal, typically below 0.1 g/L in a 10 g/L ClO2 solution.
- Byproduct Compatibility: The generated formic acid (HCOOH) does not inhibit downstream bleaching processes.
The most important processes employing this methodology are SVP-LITE (Eka Chemicals) and the related R8 (ERCO Worldwide).
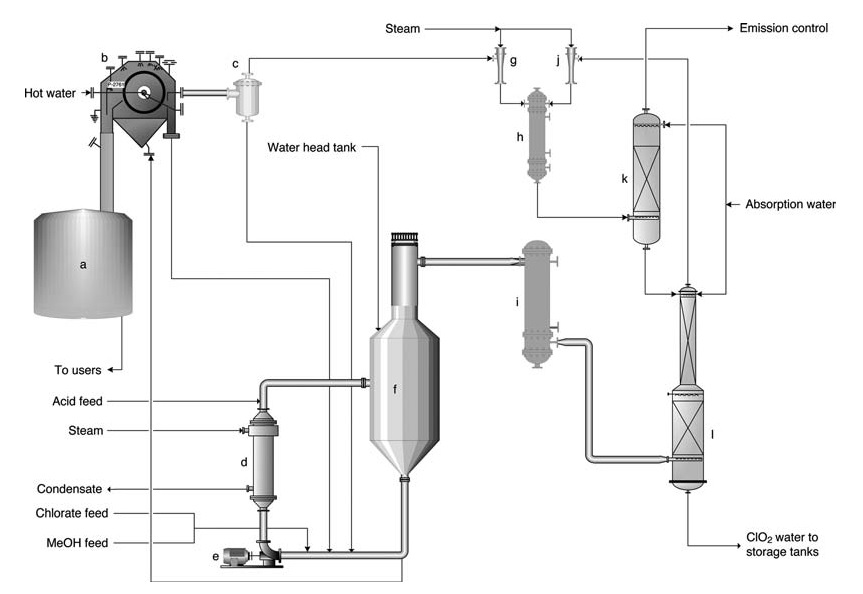
a) Salt cake dissolution tank; b) Salt cake filter; c) Filtrate receiving tank; d) Reboiler; e) Generator circulation pump; f) SVP Generator; g) Ejector for filter vacuum; h) Ejector steam condenser; i) Main injector for process vacuum; j) Gas cooler; k) Ventilation scrubber; l) Absorption tower
The SVP-LITE Process (Figure 1) uses a circulation system within a main reactor vessel maintained under vacuum. Reactants (chlorate, methanol, and sulfuric acid) are introduced into the reactor, where they react to form ClO2 and precipitate byproduct salts.
Heat is provided through a reboiler and from the dilution heat of the sulfuric acid. Chlorine dioxide exits the reactor alongside evaporated water and is subsequently absorbed in water within an absorption tower.
The resulting ClO2 solution is then pumped into storage. Tail gas from the absorber undergoes further scrubbing to minimize emissions. A portion of the reactor solution is diverted to a filter for byproduct salt removal before being recirculated back into the reactor.
For operational simplicity, the solid salt is typically redissolved and directed to the mill’s chemical system.
Production rates generally range from 5 to 60 tonnes per day. The final product contains 9–10 g/L ClO2 and is virtually free of elemental chlorine (Cl2 content typically below 0.1 g/L but guaranteed to be less than 0.2 g/L).
The unprocessed byproduct salt from the generator is typically an acidic sulfate salt known as sodium sesquisulfate (Na3H(SO4)2). However, the process can be modified to yield neutral sodium sulfate (Na2SO4).
This conversion is achieved by transforming sodium sesquisulfate within a dedicated plant unit (leading to the process names SVP-SCW and R10, respectively).
The sesquisulfate stream from the reactor system is directed to a mixing/metathesis tank, where it undergoes partial conversion to sodium sulfate, which is then separated by recrystallization and filtration. The acidic solution is then returned to the ClO2 reactor.
Converting the acidic salt to a neutral form offers significant advantages, such as reduced acid consumption and decreased salt cake volume.
2.2. Production of Chlorine Dioxide from Chlorate Using Hydrogen Peroxide as Reducing Agent
Hydrogen peroxide (H2O2) can also be used as a reducing agent in chlorate-based ClO2 production. This process generates oxygen (O2) as a byproduct, which is released to the atmosphere:
NaClO3 + 0.5 H2O2 + 0.5 H2SO4 → ClO2 + 0.5 Na2SO4 + 0.5 O2 + H2O
Despite its apparent simplicity, the actual reaction is more complex. The byproduct salt under vacuum conditions can be either sodium sulfate or sodium sesquisulfate depending on the reactor’s acidity. Although operating at higher acidity offers sodium sesquisulfate production, it comes at the cost of increased acid consumption and salt cake generation.
The advantages of hydrogen peroxide are as follows:
- Increased Capacity: Hydrogen peroxide’s faster reaction kinetics enable higher production capacity within existing ClO2 plants with minimal capital investment.
- Safer Reducing Agent: Hydrogen peroxide offers a safer alternative compared to other reducing agents like methanol, sulfur dioxide, or chloride.
- Potential for Neutral Salt Cake: Process modifications can yield a neutral salt cake, reducing environmental impact.
- Purer Chlorine Dioxide: Hydrogen peroxide use can contribute to a purer ClO2 product.
Similar to methanol-based vacuum processes (Figure 1), vacuum processes use the trade names SVP-HP or R11 (the latter employing a catalyst).
The most common process under atmospheric conditions is the Eka Chemicals HP-A process (Figure 2), also applicable to Solvay, Mathieson, and R2 processes. This process is typically implemented as an upgrade for older installations due to its similar design.
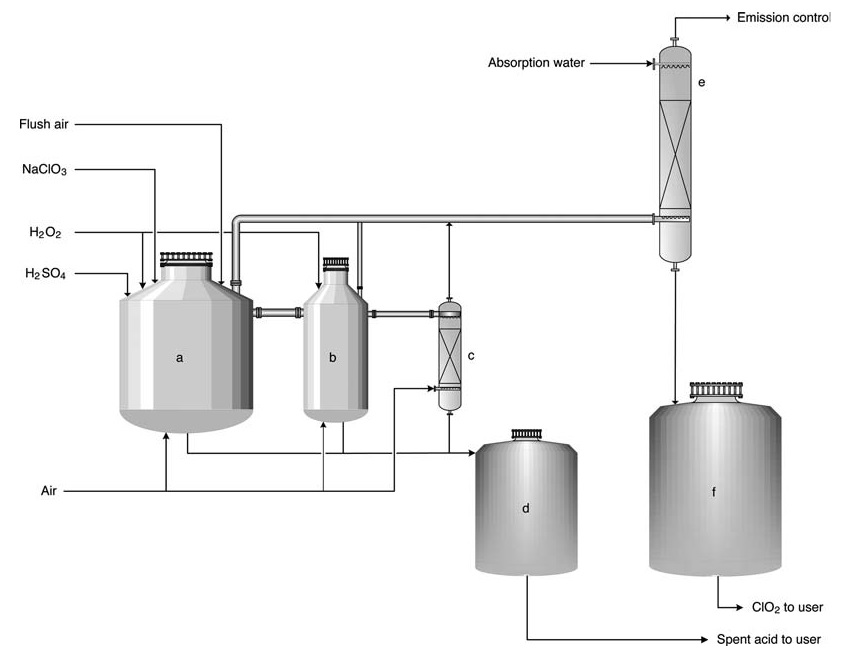
a) Primary reactor; b) Secondary reactor; c) Stripper; d) Spent acid tank; e) Absorption tower; f) ClO2 solution storage tank
In the HP-A process, reactants are fed into a series (usually 2-3) of open reactors. The process is essentially adiabatic, relying on the heat of dilution from sulfuric acid to maintain reaction temperature (typically 58 °C) and a slight sub-ambient pressure. Most of the chlorate conversion to chlorine dioxide occurs in the first reactor.
The byproduct salt remains in solution, while large air volumes are introduced to desorb ClO2 and maintain gas concentrations below the explosion limit (10–12 vol%). The gas is then directed to an absorption tower for ClO2 water production.
Spent acid can be utilized for mill acidification or makeup within the recovery boiler system. The product contains 8 g/L of chlorine dioxide and is virtually free of elemental chlorine (Cl2 concentration < 0.2 g/L).
For smaller-scale applications like water treatment or biocide production, the Eka Chemicals SVP-Pure process (Figure 3) offers a low-investment and simple solution. This process uses a pre-mixed chlorate and hydrogen peroxide solution along with sulfuric acid.
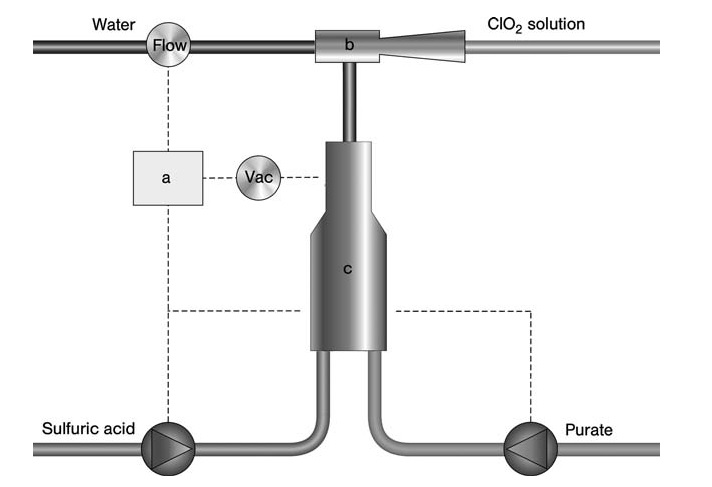
a) Controller; b) Eductor; c) Reactor
All reactants are fed simultaneously into a sub-atmospheric reactor using an eductor driven by a water stream. This water stream absorbs the generated ClO2 and byproducts to form the final product (chlorine dioxide in water).
The entire system is compact and controlled by a microprocessor, allowing for on-demand production with direct application of the product. The ClO2 content in this process typically ranges from 1–1.5 g/L, with variants reaching up to 7 g/L for bleaching applications.
2.3. Production of Chlorine Dioxide from Chlorate Using Sulfur Dioxide as Reducing Agent
Sulfur dioxide (SO2) can be employed as a reducing agent in chlorate-based processes. This integration offered economic and operational advantages, contributing to the popularity of the Mathieson process in the 1950s.
The Mathieson process, along with the Solvay and R2 processes, played an important role in producing chlorine dioxide for pulp bleaching applications. However, its importance has decreased in recent times.
The Mathieson process follows a slightly exothermic reaction, as represented by the equation:
2 NaClO3 + H2SO4 + SO2 → 2 ClO2 + 2 NaHSO4
While a competing reaction can lead to chlorine formation, it can be suppressed, and most of the generated chlorine reacts further. However, the reaction kinetics are relatively slow, resulting in incomplete chlorate conversion.
Adding 1–10 wt% sodium chloride relative to chlorate is a common practice to enhance reaction rate. However, this addition also increases byproduct chlorine formation, which may be undesirable in certain applications.
The Mathieson process layout closely resembles the HP-A process (Figure 2). The key difference lies in the absence of hydrogen peroxide inlets. Instead, sulfur dioxide is introduced through the sparger air.
2.4. Production of Chlorine Dioxide from Sodium Chlorite
Sodium chlorite (NaClO2) can also be used as a raw material for chlorine dioxide generation, primarily for small-scale applications. However, some drinking water treatment facilities may use this method for larger scale production (up to several tons per day). There are two main methods:
- By activation with an acid
In this process, chlorite reacts with an acid (hydrochloric acid, HCl), as shown in the following equation:
5 NaClO2 + 4 HCl → 4 ClO2 + 5 NaCl + H2O
Sulfuric acid can be a substitute, but it leads to lower production rates due to the absence of chloride catalysis. While more expensive, with a 25% higher production cost, this method offers a ClO2 product free of chlorine.
- By activation with chlorine
This method utilizes elemental chlorine in either the gas phase or dissolved in water (where it hydrolyzes to hypochlorous acid and hydrochloric acid). The overall reaction is illustrated in the equation:
2 NaClO2 + Cl2 → 2 ClO2 + 2 NaCl
The chlorine gas-activated process has been the industry standard for a long time. This two-feed system leverages the fast reaction between molecular chlorine and chlorite ions.
The Rio Linda method uses separate feeds of sodium chlorite solution and gaseous chlorine, allowing them to react before being drawn into the application by a water stream via an eductor that creates the necessary low pressure.
2.5. Production of Chlorine Dioxide by Electrochemical Processes
Chlorine dioxide can be produced by electrochemical methods from sodium chlorite, usually accompanied by sodium hydroxide production. Electrochemistry allows for accurate control over ClO2 production; however, electrodes and membranes are susceptible to impurities, necessitating deionized water for optimal operation.
The chlorite oxidation to chlorine dioxide occurs at the anode, and sodium ions migrate through a membrane to the cathode side, where water electrolysis produces hydrogen gas and hydroxide ions.
Electrolysis can also be used to generate the acid needed for the activation of chlorite in the sodium chlorite process.
The chlorine dioxide produced is separated from the chlorite solution by air stripping before being used.
Electrochemistry can also be employed to minimize salt cake production in large-scale chlorate-based processes. This method reduces sulfuric acid consumption by using electrochemically generated protons and removing sodium ions through co-produced caustic soda.
While environmentally beneficial, these electrochemical processes require high capital investment and significant electrical power consumption.
2.6. Stabilized Chlorine Dioxide Products
Various commercial vendors offer stabilized chlorine dioxide products. These products are all buffered solutions containing chlorite (or chlorate) ions that require activation to release chlorine dioxide.
These products come in two forms:
- Aqueous solutions are buffered solutions with chlorite or chlorate, requiring acid addition for chlorine dioxide release.
- Solids contain chlorite or chlorate incorporated into solid matrices (gels or absorbents) where chlorine dioxide is bound. Activation is achieved by heating or washing out the chlorine dioxide.
Stabilized chlorine dioxide products are used in various small-scale applications (less than 5 kg/day), such as odor control, air treatment, biocidal applications, disinfection, and water purification.
3. Uses of Chlorine Dioxide
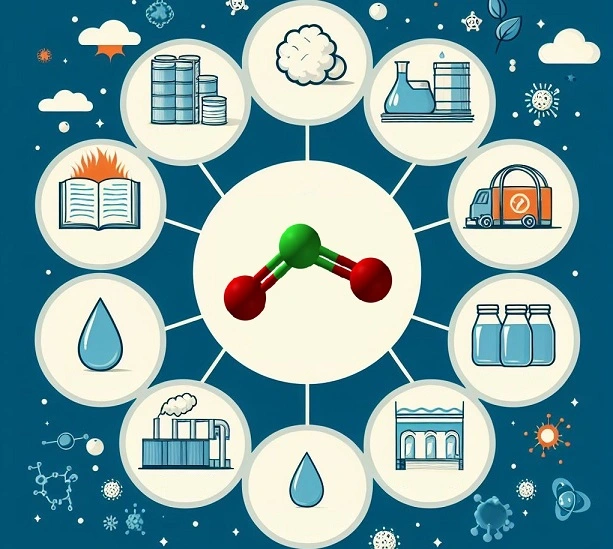
Chlorine dioxide is used in various sectors, with pulp bleaching being the dominant application. However, its economic viability often goes unnoticed due to the nature of marketing and trade press statistics.
Due to its unstable nature, ClO2 cannot be stored and must be generated at the point of use. Despite this limitation, it remains the most commercially valuable chlorine oxide or chlorine oxygen acid.
3.1. Uses in Pulp Bleaching
Over 90% of the world’s Kraft pulp (hardwood and softwood) production uses chlorine dioxide in Elemental Chlorine-Free (ECF) bleaching sequences. This is because ClO2 oxidizes lignin selectively, which enhances pulp yield and maintains mechanical properties.
While the bleaching potential of chlorine dioxide has been known for over 150 years, its widespread adoption occurred only in the 1980s. Safe and reliable large-scale production processes that emerged in the 1940s contributed to the modern continuous processes used today.
The primary driver for ClO2 adoption in pulp bleaching was to mitigate the environmental impact of chlorinated organic compounds formed during elemental chlorine bleaching. Since the late 1980s, ClO2 has largely replaced elemental chlorine.
Unlike elemental chlorine (a strong universal chlorinator), chlorine dioxide does not introduce chlorine atoms into aromatic rings during bleaching. This eliminates the formation of toxic, highly chlorinated organics like dioxins and polychlorinated phenols.
While some adsorbable organic halides (AOX) are still generated even with pure ClO2, they are more readily biodegradable, resulting in a lower environmental impact from pulp mill effluents.
Both ECF and Total Chlorine-Free (TCF) bleaching, when operated with best practices, are considered environmentally acceptable. Modern bleaching involves a combination of chemicals and processes to achieve cost-efficiency, high pulp quality, and low environmental impact.
High-performing mills can achieve bleaching with 8–16 kg of chlorine dioxide per ton of pulp.
3.2. Other Applications
Beyond pulp bleaching, chlorine dioxide is used in other sectors, often at a smaller scale.
- Textile fiber bleaching: Similar to pulp bleaching, chlorine dioxide allows for bleaching natural fibers (wool, cotton) with specific properties.
- Water treatment: Chlorine dioxide is used in thousands of drinking water treatment plants due to its effectiveness and selectivity compared to alternatives like elemental chlorine, hypochlorite, ozone, and UV light. It offers superior bacterial control, odor control, and taste control and does not generate trihalomethanes like chlorine and hypochlorite.
- Food industry: ClO2 finds application in microbial control in the food industry.
- Chlorine dioxide is used in wastewater disinfection and slime control in paper machines.
- Chlorine dioxide is used in oilfields for removing biofilms and neutralizing hydrogen sulfide and ferrous sulfide, which can cause backpressure in wells. Additionally, it finds use in odor control within the oil industry.
- An emerging application of ClO2 is in reducing nitrous gases from incineration processes (coal boilers, waste incinerators, and recovery boilers). This application offers high removal efficiencies (over 90%) for NOx and mercury with good economy.
4. Toxicology of Chlorine Dioxide
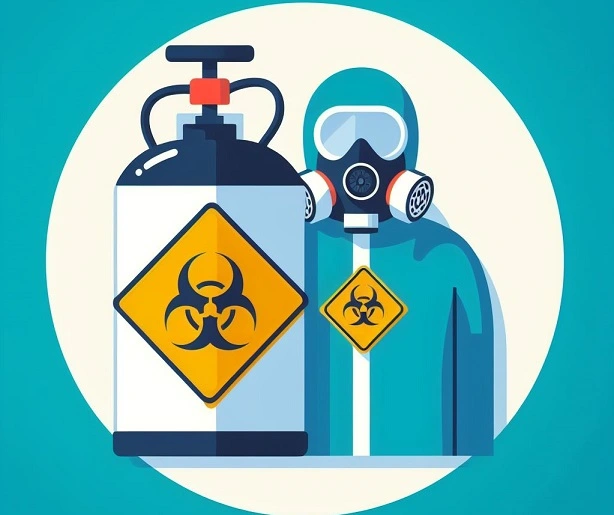
Chlorine dioxide poses specific hazards regarding human health and potential explosions. This section outlines the key safety considerations for handling ClO2.
Exposure Effects and Limits
- The release of chlorine dioxide gas or liquid is readily detectable due to its pungent odor, similar to that of chlorine.
- Low concentrations irritate the respiratory system and eyes.
- Higher concentrations can cause severe coughing, pulmonary edema (fluid buildup in the lungs), and even death.
- No human data exists on the carcinogenicity or genotoxicity of chlorine dioxide.
- Occupational exposure limits are:
- 8-hour Time-Weighted Average (TWA): 0.1 ppm
- Short-Term Exposure Limit (STEL): 0.3 ppm
Safe Handling Practices
- Conduct handling and storage in well-ventilated areas.
- Maintain cool storage temperatures and use minimal solution quantities.
- Implement process safety management practices.
- Provide training and proper safety equipment (respiratory protection, chemical splash goggles, gloves, and boots).
- Equip ClO2 plants and application points with gas leak detection alarms set at 0.1 ppm (TWA limit).
Explosion Hazards
- Gaseous chlorine dioxide is explosive at concentrations exceeding 10% in air (10 kPa partial pressure).
- Decomposition to chlorine and oxygen is exothermic and increases gas volume, leading to an increase in pressure and a potential shockwave.
- Decomposition can be initiated by metal oxide impurities, hot surfaces, rapid acid dilution, pressure shocks, heat, or sunlight.
References
- Chlorine Oxides and Chlorine Oxygen Acids; Ullmann’s Encyclopedia of Industrial Chemistry. – https://onlinelibrary.wiley.com/doi/10.1002/14356007.a06_483.pub2
- Halogens; Descriptive Inorganic Chemistry. – https://www.sciencedirect.com/science/article/abs/pii/B9780128046975000178
- The Chemistry of Chlorine Dioxide. – https://onlinelibrary.wiley.com/doi/10.1002/9780470166161.ch3