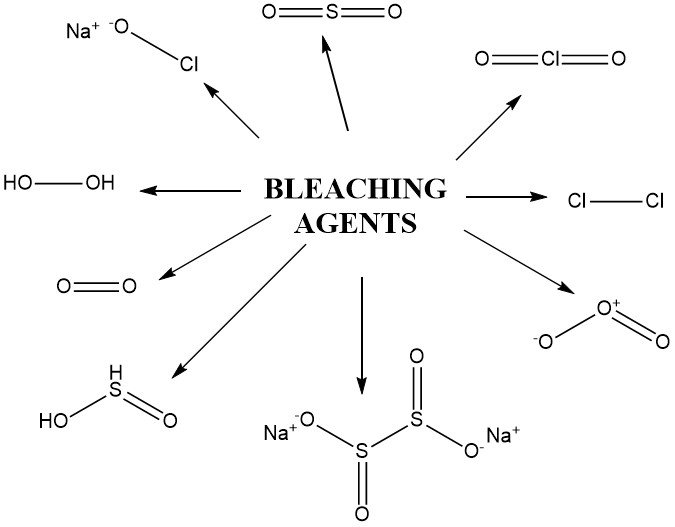
Introducción
El proceso para lograr un efecto blanqueador implica la eliminación de cromóforos. Esto se puede lograr adsorbiendo los compuestos coloreados sobre superficies activas como carbón activo o arcillas blanqueadoras.
Este método se emplea comúnmente a escala industrial para blanquear y purificar líquidos como el aceite vegetal. Otro enfoque comúnmente utilizado en entornos industriales es la destrucción química de cromóforos en compuestos orgánicos o inorgánicos, que a menudo se combina con procesos de purificación o limpieza.
Esto es especialmente importante en el caso de los productos naturales, que a menudo contienen impurezas. Por ejemplo, el algodón está contaminado con residuos de cápsulas de semillas, cera, componentes grasos y compuestos inorgánicos. Al blanquear el algodón se potencia su brillo y al mismo tiempo se eliminan las impurezas. El blanqueo también puede servir como continuación o complemento de los pasos de procesamiento anteriores.
Por ejemplo, en el contexto de la fabricación de pasta química, el blanqueo elimina la lignina de las fibras de madera, lo que da como resultado un mayor brillo y una mayor purificación de la celulosa. Lograr un blanqueamiento casi incoloro sin causar daños es un desafío y requiere experiencia. El objetivo del blanqueo desde el principio también puede ser crear una tonalidad más uniforme, como por ejemplo blanquear la chapa de madera.
En términos de volumen y valor del producto, el blanqueo de materiales fibrosos para la producción de papel y textiles tiene una importancia significativa.
Tabla de contenido
1. Mecanismo de blanqueo
El blanqueo se puede clasificar en blanqueo oxidativo y reductivo. El blanqueo oxidativo destruye irreversiblemente los cromóforos, mientras que el blanqueo reductivo puede ser reversible, como por ejemplo mediante la reoxidación por el oxígeno atmosférico.
En el caso de los productos naturales, a menudo se desconoce la composición química completa de los compuestos coloreados. Generalmente, estos compuestos contienen dobles enlaces carbono-carbono conjugados, como cadenas de polimetino, sistemas aromáticos o sistemas quinoides. El blanqueo oxidativo rompe los dobles enlaces, elimina la conjugación y genera compuestos químicos de menor peso molecular.
El blanqueamiento eficaz suele implicar un proceso de varios pasos. La repetición de la oxidación ácida y la extracción alcalina permite mantener condiciones moderadas y concentraciones químicas bajas.
El efecto blanqueador se mide por el aumento de brillo. Los fotómetros de remisión se utilizan para determinar el brillo relativo a un estándar en múltiples longitudes de onda, siendo BaSO4 el estándar más utilizado. Sin embargo, existen métodos alternativos disponibles para evaluar el brillo. La estabilidad del brillo también sirve como indicador de la calidad y eficiencia del proceso de blanqueo.
Una oxidación excesiva puede provocar la formación de nuevos cromóforos o un posible amarillamiento en el futuro. El color amarillento ocurre si los grupos auxocromos en un cromóforo pueden reoxidarse. La luz y el calor pueden provocar cambios de color en los materiales blanqueados.
La radiación ultravioleta rompe fácilmente los enlaces carbono-carbono y produce radicales. La recombinación de estos radicales con oxígeno u otras partes de la molécula puede generar nuevos cromóforos.
Durante los procesos de blanqueo, es importante asegurarse de que el grado de polimerización de los polímeros tratados no se vea afectado negativamente. Una disminución del peso molecular puede afectar la resistencia de la fibra y reducir el valor económico.
Por lo tanto, el blanqueo debe apuntar a los cromóforos preservando al mismo tiempo la estructura molecular. La complejidad de las materias primas ha llevado al desarrollo de diversos métodos de blanqueo.
Por ejemplo, blanquear algodón es diferente a blanquear lana. Si bien se pueden aplicar condiciones alcalinas fuertes para blanquear el polímero de carbohidratos de celulosa (algodón), la fibra de lana de queratina (proteína) es muy sensible a los álcalis. El blanqueo alcalino no se puede utilizar ya que provocaría la destrucción del polímero mediante la extracción de aminoácidos.
2. Agentes blanqueadores
2.1. Pretratamiento
La preparación para un proceso de blanqueo implica la eliminación de contaminantes. Un método de pretratamiento común es el lavado. La lana esquilada, por ejemplo, puede contener una cantidad significativa de arena y material graso (lanolina), hasta un 50 % en peso.
De manera similar, los compuestos que consumen o descomponen el agente blanqueador deben eliminarse antes del proceso de blanqueo propiamente dicho. El lavado con tensioactivos o compuestos quelantes es un procedimiento estándar para lograrlo.
Reduce la demanda de agentes blanqueadores y minimiza el potencial de reacciones secundarias negativas durante el blanqueo. En el caso del blanqueo químico de pulpa, esto suele ser un requisito crucial.
El lavado ácido a un pH inferior a 3 disuelve los iones metálicos. La presencia de agentes reductores como el dióxido de azufre, que reducen el estado de oxidación de los metales, puede potenciar este efecto. Agentes quelantes como las sales sódicas del ácido dietilentriaminopentaacético (DTPA) o del ácido etilendiaminotetraacético (EDTA) se utilizan en condiciones ligeramente ácidas (pH 5-6) para acelerar la eliminación de metales.
Este rango de pH permite la eliminación de metales de transición preservando los iones magnesio y calcio, que sirven como estabilizadores en el proceso de blanqueo. Para la pulpa química producida mediante pulpa alcalina, esta etapa de eliminación de metales es necesaria si se va a implementar un proceso de blanqueo totalmente libre de cloro (TCF).
En el blanqueo convencional o sin cloro elemental (ECF), los metales se eliminan durante las etapas de dióxido de cloro ácido. En la fabricación de pulpa con sulfito ácido, se solubilizan durante el proceso de fabricación de pulpa y se eliminan en el lavado del material pardo.
Durante la pulpa alcalina de madera dura, se generan dobles enlaces de polímero de xilano. Estos compuestos de hemicelulosa consumen productos químicos blanqueadores electrófilos. Se realiza un pretratamiento ácido a alrededor de 90 °C y un pH inferior a 3 para hidrolizar estos compuestos, produciendo ácido furancarboxílico. Esto ayuda a reducir la demanda de productos químicos blanqueadores.
Se pueden utilizar enzimas como la xilanasa como pretratamiento. Durante la pulpa alcalina, el xilano se disuelve pero puede precipitar nuevamente en las etapas finales del procedimiento de cocción, lo que plantea desafíos para el blanqueo. La enzima xilanasa elimina el precipitado y facilita el proceso de blanqueo. Para este fin se prefieren las enzimas extraídas de bacterias termófilas con tolerancia a altas temperaturas y pH.
En el blanqueo de textiles, pueden ser necesarios tratamientos con amilasa o peroxosulfato para eliminar el almidón.
2.2. Agentes oxidantes
En la antigüedad, los egipcios y fenicios practicaban el blanqueo oxidativo de textiles utilizando la luz solar combinada con un tratamiento alcalino suave que incluía carbonato de potasio lixiviado de las cenizas de madera.
En el siglo XVIII surgió un método de blanqueo conocido como «blanqueo holandés», que implicaba alternar tratamientos con carbonato de potasio, exposición a la luz solar en prados cubiertos de hierba y leche agria. Esta técnica alcanzó su apogeo cerca de Haarlem, Países Bajos.
Los avances en el conocimiento químico a finales del siglo XVIII llevaron al descubrimiento de un nuevo agente blanqueador, el hipoclorito. El hipoclorito de potasio (Eau de Javelle), el hipoclorito de sodio (Eau de Labarraque) y el hipoclorito de calcio se convirtieron en los agentes blanqueadores industriales más importantes durante casi 150 años.
El cloro se introdujo en el blanqueo químico de pulpa en la década de 1930, seguido por el dióxido de cloro y el peróxido de hidrógeno una década después.
El uso industrial del oxígeno como agente blanqueador de la pulpa química comenzó a finales de la década de 1960 y posteriormente se incorporó el ozono a las secuencias de blanqueo de la pulpa química.
Otros compuestos oxidantes empleados para el blanqueo incluyen derivados del peróxido de hidrógeno como el ácido peracético, el perborato de sodio, los peroxodisulfatos (persulfatos) y los peroxomonosulfatos (ácido de Caro). Estos compuestos se utilizan en condiciones específicas, incluido el permanganato de potasio.
2.2.1. Oxígeno
La utilización de oxígeno como agente blanqueador ha experimentado un aumento significativo desde principios de los años 1970. Se emplea en el blanqueo de pulpa química para mantener e intensificar la degradación de la lignina, que generalmente se inicia durante la elaboración de pulpa alcalina.
La deslignificación con oxígeno requiere condiciones alcalinas, generalmente con hidróxido de sodio (NaOH), para el proceso de oxidación. También requiere temperaturas relativamente altas (75-100 °C) y una presión de oxígeno de 0,3-0,5 MPa. Aumentar la temperatura, la presión o la concentración de la soda cáustica mejora la tasa de oxidación.
El proceso de deslignificación con oxígeno implica dos reacciones simultáneas: deslignificación deseada y degradación no deseada de carbohidratos. En consecuencia, existen límites prácticos para el aumento de temperatura y la cantidad de álcali. La reducción del grado de polimerización se ve parcialmente obstaculizada por las sales de magnesio.
Aunque el impacto del oxígeno sobre la pulpa química es limitado, su tratamiento reduce la demanda de otros químicos blanqueadores entre un 40% y un 50%. La deslignificación con oxígeno permite la recuperación combinada de los efluentes de la fabricación de pulpa y los pasos posteriores de deslignificación, reduciendo efectivamente la descarga total de material orgánico de la planta de blanqueo.
En los procesos de fabricación de pulpa a base de magnesio, tales como la fabricación de pulpa con sulfito de magnesio, la etapa de oxígeno se puede realizar usando hidróxido u óxido de magnesio como fuente de álcali. Normalmente, se añade peróxido de hidrógeno simultáneamente (a aproximadamente 90 °C) para acelerar la tasa de deslignificación.
2.2.2. Dióxido de cloro y clorito de sodio
El dióxido de cloro es un agente blanqueador excepcionalmente selectivo que se utilizó por primera vez en el blanqueo de pulpa química en 1946.
El dióxido de cloro posee un electrón desapareado, lo que lo convierte en un radical libre con estabilidad limitada. Existe como gas en condiciones estándar y puede explotar espontáneamente a presiones parciales superiores a 40 kPa, descomponiéndose en cloro y oxígeno.
Cuando se exponen al calor o la luz, concentraciones incluso más bajas de dióxido de cloro pueden explotar, aunque con menor violencia. En consecuencia, el dióxido de cloro puro no se puede transportar ni almacenar. En cambio, se genera in situ y normalmente se manipula como una solución acuosa diluida.
El principal método industrial para la generación de dióxido de cloro implica la reducción de clorato. Históricamente, el proceso Mathieson, que emplea dióxido de azufre para la reducción, jugó un papel importante. Como subproductos se producen ácido sulfúrico diluido y sulfato de sodio o hidrogenosulfato de sodio.
Los procesos alternativos con menos subproductos emplean ácido clorhídrico, metanol o peróxido de hidrógeno como agente reductor. El ácido clorhídrico ofrece la ventaja de un bajo coste, pero da como resultado una cantidad relativamente alta de cloro presente como subproducto en el dióxido de cloro, lo que conduce a una mayor formación de productos halogenados no deseados durante el blanqueo.
Hoy en día, los procesos de metanol y peróxido de hidrógeno son los métodos más destacados. Estos procesos generan dióxido de cloro gaseoso de gran pureza, que se diluye con aire o vapor de agua para evitar explosiones.
Luego, el gas se absorbe en agua fría para alcanzar una concentración de 6 a 12 g/l. Para las reacciones del dióxido de cloro con la pulpa, normalmente se mantiene un valor de pH entre 2 y 5. Dentro de este rango de pH, el dióxido de cloro no afecta el grado de polimerización de la celulosa.
La temperatura de reacción recomendada para el dióxido de cloro está entre 50 y 75 °C. En el blanqueo de pulpa de madera dura, iniciar el blanqueo a altas temperaturas (> 90 °C) es favorable ya que permite la oxidación simultánea de la lignina y la hidrólisis de los ácidos hexenurónicos.
En el blanqueo de textiles se emplea clorito de sodio como fuente de dióxido de cloro. Se utiliza ácido clorhídrico, ácido fórmico o ácido acético para liberar dióxido de cloro mediante la siguiente reacción:
5 NaClO2 + 4 HCl → 4 ClO2 + 2 H2O + 5 NaCl
2.2.3. Peróxido de hidrógeno y otros compuestos peroxo
El peróxido de hidrógeno ha servido como blanqueador industrial desde principios del siglo XX, principalmente en el blanqueo de fibras textiles.
El perborato de sodio, NaBO3·4 H2O, derivado del peróxido de sodio y el bórax, se ha utilizado como blanqueador en detergentes para ropa como Persil ya en 1907. Hasta el día de hoy, los perboratos y percarbonatos se utilizan ampliamente en detergentes para ropa debido a su suave efecto blanqueador. a temperaturas elevadas, que es más suave con las fibras en comparación con los hipocloritos más fuertes utilizados como blanqueadores fríos. Se aplican productos con recubrimiento especial para mejorar la estabilidad en almacenamiento del percarbonato puro.
Las soluciones acuosas de peróxido de hidrógeno están disponibles comercialmente en concentraciones de hasta el 90 % en peso. En el blanqueo se utilizan habitualmente soluciones con entre un 35 y un 70 % en peso.
La aplicación más importante del peróxido de hidrógeno es el blanqueo de pulpa para la producción de papel. La pulpa mecánica y la pulpa química se blanquean utilizando soluciones de peróxido alcalino. El peróxido de hidrógeno también se utiliza para blanquear fibras textiles como el algodón, el lino, la lana y las sintéticas.
Los procesos comerciales de blanqueo con peróxido de hidrógeno generalmente funcionan en condiciones de ligeras a fuertemente alcalinas. El hidróxido de sodio se utiliza comúnmente como fuente alcalina. La reacción inicial implica la adición nucleofílica de aniones hidroperóxido a grupos carbonilo. En consecuencia, la adición de álcali mejora la tasa de blanqueo:
HOOH+ OH- ↔ HOO- + H2O
Sin embargo, las condiciones alcalinas también favorecen reacciones secundarias como la desproporción del peróxido de hidrógeno en oxígeno y agua:
HOO- + H2O2 → H2O + OH- + O2
El resultado del blanqueamiento depende de la activación y la estabilización. La velocidad de reacción aumenta con la temperatura y la concentración de álcali.
Sin embargo, a altas temperaturas, se vuelven más probables reacciones secundarias como la descomposición térmica del peróxido de hidrógeno en radicales, lo que puede provocar pérdidas de rendimiento y solubilización del material que se está blanqueando. Por lo tanto, el rango de temperatura típico para el blanqueo con peróxido es entre 60 y 90 °C.
Puede ser necesaria la estabilización de la solución blanqueadora alcalina para minimizar la descomposición del peróxido. Los radicales hidroxilo, generados por la descomposición del peróxido, son agentes oxidantes altamente no selectivos que provocan reacciones secundarias no deseadas.
En el blanqueo químico de pulpa, la quelación de metales de transición sólo es necesaria en el blanqueo TCF (totalmente libre de cloro). En el blanqueo ECF (sin cloro elemental), normalmente se aplica peróxido de hidrógeno después de una etapa ácida, que elimina los metales de transición durante el paso de lavado.
Para el blanqueo mecánico de pulpa, la mejor manera de eliminar los metales perjudiciales es mediante un tratamiento previo con un agente quelante. Los agentes quelantes comúnmente utilizados son las sales de sodio del ácido dietilentriaminopentaacético (DTPA), del ácido etilendiaminotetraacético (EDTA) o fosfonatos similares con capacidades quelantes comparables o superiores.
También se emplean estabilizadores como silicato de sodio y sales de magnesio (principalmente sulfato de magnesio). Estos estabilizadores ayudan a precipitar o absorber compuestos perjudiciales sobre sílice coloidal o hidróxido de magnesio.
Durante el proceso de blanqueo, el peróxido de hidrógeno escinde las cadenas laterales y destruye irreversiblemente las estructuras quinoides. La oxidación y destrucción de las quinonas son cruciales para lograr una buena estabilidad del brillo. Los productos blanqueados con peróxido exhiben una menor reversión en comparación con otros oxidantes.
El ácido peracético se utiliza en pequeñas cantidades como paso de activación antes del tratamiento con peróxido de hidrógeno alcalino. Su aplicación permite un mayor aumento del brillo o un menor consumo global de productos químicos blanqueadores.
La reacción con la pulpa se lleva a cabo en condiciones ligeramente ácidas, implicando predominantemente la reacción de hidroxilación de la lignina residual. El ácido peracético se produce mezclando ácido acético y peróxido de hidrógeno.
En presencia de un ácido fuerte (p. ej., ácido sulfúrico), se establece un rápido equilibrio entre el ácido acético, el ácido peracético, el peróxido de hidrógeno y el agua. Como los otros compuestos de la mezcla no contribuyen a la reacción de blanqueo del ácido peracético, el uso de ácido peracético en equilibrio es costoso.
El ácido peracético destilado es una alternativa, que se obtiene mediante destilación al vacío del ácido peracético en equilibrio, lo que da como resultado una solución de ácido peracético relativamente pura en agua.
El ácido peracético destilado con un contenido de aproximadamente el 35 % en agua debe almacenarse por debajo de 4 °C para evitar el lento restablecimiento del equilibrio con el peróxido de hidrógeno y el ácido acético a temperaturas más altas.
Otra opción es la mezcla in situ, que produce una mezcla de ácido peracético/peróxido que puede usarse para una reacción inicial de ácido peracético seguida de una etapa posterior de blanqueo con peróxido. Esto se logra agregando suficiente álcali después de la etapa ácida.
El ácido peracético también se puede generar in situ a partir de peróxido de hidrógeno y tetraacetiletilendiamina (TAED) en condiciones débilmente alcalinas. Este procedimiento se aplica en agentes de lavado que utilizan percarbonato o perborato como fuente de peróxido y también es aplicable en blanqueamientos especiales.
El peroxosulfato de potasio (KHSO5) se utiliza para blanquear fibras de poliamida y celulosa, aunque se emplea principalmente para limpiar lana y reducir su encogimiento.
El peroxodisulfato de sodio (Na2S2O8) y el peroxodisulfato de amonio ((NH4)2S2O8) se utilizan en el desencolado del algodón y ocasionalmente como aditivos en el blanqueo con peróxido de hidrógeno.
2.2.4. Ozono
El ozono se genera mediante una descarga eléctrica silenciosa del oxígeno. En el blanqueo de pulpa, el ozono normalmente se produce utilizando oxígeno puro. Este método permite una alta concentración de ozono en el gas (hasta un 12 % en peso) y facilita el proceso de mezcla.
Para mantener un blanqueo eficaz, se utiliza ozono a un pH inferior a 4. Es importante mantener la temperatura por debajo de aproximadamente 50 °C para evitar reacciones secundarias con la celulosa causadas por su alto potencial de oxidación. Las temperaturas más altas pueden provocar un brillo menos estable y un fácil amarillamiento.
2.2.5. Cloro e hipocloritos
Históricamente, el cloro se utilizó ampliamente para la oxidación de la lignina (deslignificación) en el blanqueo químico de pulpa. La cloración implica la sustitución y oxidación de los anillos aromáticos de la lignina, lo que da como resultado la producción de ácido dicarboxílico y fragmentos de lignina clorada.
Alrededor del 10% del cloro aplicado se encuentra como compuestos halogenados en el efluente, incluidos fenoles clorados y dibenzodioxinas y dibenzofuranos polihalogenados.
Estos compuestos se analizan cuantitativamente mediante un método extractivo con carbón activado, y la medición se expresa como compuestos orgánicos halogenados adsorbibles (AOX).
Algunos de estos compuestos son mutagénicos, lo que lleva a la eliminación gradual de la aplicación de cloro en la mayoría de las regiones después de la identificación de estas sustancias en el efluente.
Actualmente, el hipoclorito se utiliza principalmente como quitamanchas, lo que se conoce como «lejía fría» en el lavado de ropa. En el blanqueo químico de pulpa, su aplicación se limita a pequeñas cantidades para la reducción controlada del grado de polimerización de la pulpa en disolución.
El ácido hipoclórico (HOCl) tiene un mayor potencial de oxidación (+1,50 V) en comparación con el cloro (+1,35 V) o el hipoclorito (OCl-) (+0,94 V). Para evitar reacciones secundarias, especialmente la despolimerización causada por el ácido hipoclórico agresivo, el blanqueo se realiza en soluciones alcalinas para minimizar la concentración de ácido hipoclórico no disociado.
Las condiciones alcalinas dan como resultado menos reacciones secundarias desfavorables ya que el anión hipoclorito es un nucleófilo débil incapaz de atacar sistemas aromáticos ricos en electrones. Sin embargo, el blanqueo con hipoclorito genera compuestos halogenados como subproductos, con una formación de AOX significativamente menor que con cloro. El principal subproducto es el cloroformo.
Se encuentran disponibles comercialmente soluciones de hipoclorito de sodio con concentraciones de cloro activo de 150-160 g/L. El término «cloro activo» se refiere a la cantidad de cloro liberado tras la acidificación de la solución de hipoclorito.
2.3. Agentes reductores
El principal agente blanqueador reductor es el ditionito de sodio, que se ha utilizado para el blanqueo de lana desde la antigüedad. Sin embargo, su importancia ha disminuido. Los derivados del ácido sulfínico se emplean principalmente para eliminar colorantes de tejidos textiles.
2.3.1. Ditionito de sodio
El ditionito de sodio (Na2S2O4), también conocido como hidrosulfito en Norteamérica (a pesar de la descripción incorrecta inicial), se produce actualmente a partir de formiato de sodio y dióxido de azufre. Anteriormente, el ditionito de zinc obtenido a partir de dióxido de azufre y polvo de zinc era más frecuente que la sal de sodio.
Sin embargo, las preocupaciones ambientales asociadas con el zinc han llevado a la interrupción de la producción in situ de ditionito de zinc utilizando polvo de zinc o amalgama de sodio. El ditionito de sodio se puede generar in situ en algunas fábricas de papel utilizando una solución alcalina de borohidruro de sodio, bisulfito de sodio y dióxido de azufre.
El ditionito de sodio está disponible en forma de polvo cristalino (90% Na2S2O4) o como una solución refrigerada de 150 g/L estabilizada con álcali. Las soluciones deben almacenarse muy por debajo de 10 °C para evitar que el ditionito se desproporcione con respecto al tiosulfato y al bisulfito.
La ditionita actúa reduciendo los grupos carbonilo a alcoholes y las quinonas a fenoles, destruyendo así los cromóforos. Se utiliza para blanquear pulpa mecánica, lana, seda, cerdas, cabello, paja, jabón, pegamento, caolín y diversos productos alimenticios como azúcar, melaza, gelatina y grasas comestibles.
El ditionito es susceptible a la oxidación por el oxígeno, convirtiéndolo en sulfito y sulfato. A temperaturas elevadas, la solución se descompone en tiosulfato, sulfito, sulfuro de hidrógeno o azufre, y los productos específicos dependen del pH. El pH elegido para el blanqueo con ditionito es un compromiso entre un blanqueo eficaz y una pérdida mínima de ditionito, normalmente alrededor de un pH de 5 a 6 a temperaturas de 50 a 80 °C.
En el blanqueo mecánico de pulpa, el blanqueo con peróxido de hidrógeno y ditionito a menudo se combinan en dos pasos secuenciales.
2.3.2. Dióxido de azufre
El dióxido de azufre se utiliza principalmente en forma de hidrogenosulfito de sodio (NaHSO3). Sin embargo, debido a su efecto blanqueador relativamente pobre, el SO2 ya no se utiliza ampliamente. Puede utilizarse como pretratamiento en la producción mecánica de pulpa antes del blanqueo con ditionita y también encuentra aplicación en el tratamiento de lana.
2.3.3. Derivados del ácido sulfínico
Los derivados importantes del ácido sulfínico incluyen el hidroximetanosulfinato de sodio y el ácido formamidinasulfínico.
Los hidroximetanosulfinatos se producen tratando ditionitos con formaldehído y son más estables que los ditionitos. Requieren temperaturas más altas para alcanzar su máximo poder reductor.
Estos derivados se emplean en procesos que operan por encima de 75 °C, donde el ditionito se descompondría rápidamente. Encuentran aplicación en el blanqueo de jabones, pegamentos, gelatinas, ácidos grasos y principalmente en procesos de teñido.
El ácido formamidinasulfínico, también conocido como dióxido de tiourea, se obtiene a partir de tiourea y peróxido de hidrógeno. Es un producto cristalino poco soluble en agua que se vuelve más soluble en condiciones alcalinas y exhibe su mayor poder reductor por encima de 80 °C.
Este ácido se utiliza para realzar el brillo de los textiles y eliminar tintes de las telas, de forma similar al ácido hidroximetanosulfínico. Su fuerte poder reductor a altas temperaturas lo hace adecuado para blanquear fibras secundarias durante la etapa de dispersión y es particularmente eficaz para destruir colorantes utilizados para papel coloreado.
3. enzimas
El uso técnico de enzimas en el blanqueo aún no está ampliamente adoptado y sigue siendo la excepción en los procesos industriales. Si bien el descubrimiento de enzimas que degradan la lignina en los hongos de la pudrición blanca ofreció potencial para la deslignificación y el blanqueo a escala industrial, hubo desafíos que limitaron su aplicación práctica.
La reacción catalizada por estas enzimas era lenta y no lo suficientemente selectiva, y las enzimas requerían coenzimas que degradaban la celulosa, lo cual era indeseable.
Uno de los problemas generales con la aplicación de enzimas es la necesidad de cepas de enzimas de alta pureza para evitar reacciones secundarias negativas causadas por otras enzimas. Además, muchos procesos industriales operan a temperaturas elevadas o niveles de pH extremos, lo que requiere el uso de enzimas adaptadas a estas condiciones.
Los organismos termófilos, que prosperan en ambientes de alta temperatura, suelen ser los preferidos como fuente para seleccionar enzimas con propiedades adecuadas.
Se han investigado enzimas específicas por su potencial en procesos de blanqueo. Las xilanasas, por ejemplo, se utilizan para eliminar una parte del xilano precipitado de las pastas kraft sin blanquear. Este tratamiento reduce la demanda de dióxido de cloro en el blanqueo sin cloro elemental (ECF) en aproximadamente un 10%.
Se cree que la lignina de las fibras está parcialmente cubierta por xilano precipitado y la eliminación del xilano facilita la eliminación de la lignina. Sin embargo, el efecto general de la aplicación de xilanasa es moderado y sigue siendo una opción de nicho para las fábricas de celulosa con acceso limitado al dióxido de cloro.
La lacasa es una enzima involucrada en la polimerización de unidades de fenilpropano en las plantas, contribuyendo a la formación del polímero de lignina. La lacasa se puede utilizar para la deslignificación de la pulpa con la ayuda de un mediador.
Los mediadores pueden convertirse fácilmente en cationes radicales mediante lacasa y oxígeno, y estos productos intermedios oxidan la lignina. En teoría, la enzima puede reoxidar el mediador varias veces, pero en la práctica, las reacciones repetidas son raras. Como resultado, la demanda del mediador, como el N-hidroxibenzotriazol, es alta, lo que hace que la aplicación industrial sea económicamente inviable.
Se han utilizado celulasas, un grupo de enzimas que descomponen la celulosa, para suavizar los tejidos de algodón. Se aplican en el lavado a la piedra de jeans como sustituto del efecto mecánico de la piedra pómez. La acción de las celulasas sobre la superficie del tejido provoca la decoloración del color ya que el colorante se encuentra principalmente en la capa exterior de las fibras.
También se han sugerido celulasas para mejorar la resistencia de la fibra de la pulpa de papel usado. Al disolver finos y fibrillas, las celulasas pueden aumentar la longitud promedio de las fibras y mejorar el potencial de resistencia.
Sin embargo, este proceso de solubilización reduce el rendimiento y aumenta la carga sobre el efluente, lo que hace que la aplicación a gran escala sea poco probable desde una perspectiva económica y ambiental.
Referencia
- Bleaching; Ullmann’s Encyclopedia of Industrial Chemistry. – https://onlinelibrary.wiley.com/doi/10.1002/14356007.a04_191.pub2