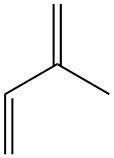
Isoprene, also known as 2-methyl-1,3-butadiene, is a five-carbon hydrocarbon that exists in nature at trace levels. It is a colorless, volatile liquid with the chemical formula C5H8.
Isoprene is used as a fundamental building block for numerous natural products. These include terpenes (natural rubber, camphor), vitamin A, and steroid sex hormones (adhering to the “isoprene rule” by Wallach and Ruzicka). It was first synthesized by the pyrolysis of natural rubber in 1860 by Williams.
Table of Contents
1. Physical Properties of Isoprene
Under normal conditions, isoprene is a colorless, volatile liquid that is insoluble in water at 20 °C. It is miscible with organic solvents such as ethanol, diethyl ether, acetone, and benzene.
Isoprene forms binary azeotropic mixtures with various compounds such as methanol, n-pentane, carbon disulfide, methyl formate, bromoethane, ethanol, dimethyl sulfide, acetone, propylene oxide, ethyl formate, isopropyl nitrite, methylal, diethyl ether, perfluorotriethylamine, acetonitrile, and isopropylamine.
Important physical properties of isoprene are detailed in Table 1.
Property | Value |
---|---|
Molecular Weight | 68.118 g/mol |
Melting Point (101.3 kPa) | -145.95 °C |
Boiling Point (101.3 kPa) | 34.059 °C |
Critical Temperature | 483.3 K |
Critical Pressure | 3.74 MPa |
Critical Volume | 266 cm3/mol |
Density (293 K) | 0.68095 g/cm3 |
Viscosity (293 K) | 0.216 mPa.s |
Surface Tension (293 K) | 18.22 mN/m |
Refractive Index | 1.42194 |
Vapor Pressure | |
-20 °C | 9.8 kPa |
0 °C | 26.4 kPa |
20 °C | 60.7 kPa |
34.059 °C | 101.3 kPa |
40 °C | 123.8 kPa |
60 °C | 229.1 kPa |
80 °C | 392.1 kPa |
100 °C | 629.5 kPa |
Specific Heat | |
Vapor (298 K) | 102.69 J mol-1 K-1 |
Liquid (298 K) | 151.07 J mol-1 K-1 |
Explosive Limits in Air (total pressure 13 kPa, 25 °C) | |
Upper Limit | 7 – 9.7 vol% (200 – 275 g/m3) |
Lower Limit | 1 – 1.5 vol% (28 – 40 g/m3) |
Maximal Explosion Pressure | 0.66 MPa |
2. Chemical Properties of Isoprene
Spectroscopic analysis indicates that at 50 °C, the majority of isoprene molecules exist in the s-trans conformation. Only 15% adopt the higher-energy s-cis form.
As a conjugated diene, isoprene exhibits characteristic behavior. The presence of a methyl group enhances its reactivity with electrophiles and Diels-Alder dienophiles compared to butadiene.
Isoprene is more reactive than butadiene due to its four unique hydrogen atoms compared to butadiene’s two. Isoprene participates in a diverse range of reactions, including substitution, addition, ring formation, complexation, and telomerization.
The reaction with hydroxyl radicals is the dominant pathway for isoprene degradation in the atmosphere. Hydroxyl radicals, highly reactive molecules, initiate a complex chain reaction that breaks down isoprene into various products. It can also be decomposed by ozone.
Under high temperatures and specific conditions, isoprene forms peroxides and free radicals, ultimately leading to the breakdown of isoprene into different products like dimethoxymethane and naphthalene.
Isoprene can undergo addition reactions similar to alkenes but is not selective and results in a mixture of products.
The only important chemical reaction of isoprene is its conversion to terpenes. Isoprene is primarily used in polymer synthesis.
3. Production of Isoprene
3.1. Production of Isoprene from Olefins
Isoprene is primarily produced by the acid-catalyzed Prins reaction of formaldehyde with isobutene, producing 4,4-dimethyl-1,3-dioxane, which is then cleaved in the gas phase (at 200 – 300 °C) to yield isoprene and recover half the formaldehyde.

Several companies refined this process due to readily available starting materials. Current production facilities of this type exist in Japan.
Efforts have focused on simplifying and improving the cost-effectiveness of isoprene synthesis from isobutene and formaldehyde. Takeda Chemical in Japan proposed a one-step gas-phase process using oxide catalysts.
Formaldehyde byproducts pose a challenge. Companies like Idemitsu and Sun Oil are using formaldehyde derivatives (methylal, dimethoxymethane) to avoid resin formation. Alternative methods involve integrating formaldehyde production directly into the process using methanol and oxygen or methyl tert-butyl ether (MTBE) and oxygen.
Japanese patents explored tert-butyl alcohol as a C4 source, while former Soviet publications described methods based on 1,3-dioxane cleavage.
The one-step gas-phase process is limited by the low catalyst space-time yield and rapid deactivation. It’s unclear if any of these variations have reached commercial production.
2-Methylbutanal is another raw material for producing isoprene. It is produced by hydroformylation of 2-butene using a rhodium catalyst.

The catalytic dehydration of 2-methylbutanal to isoprene has been extensively studied. While numerous catalysts have been proposed (β-phosphate, magnesium ammonium phosphate, molecular sieves, and zeolites), they all suffer from rapid activity loss.
However, zeolites modified with silane or cesium show improved lifetimes. Cleavage of 3-methylbutanal yielded poorer results. Currently, no industrial facilities use the synthesis of isoprene from 2-methylbutanal.
Codimerization of ethylene and propene leads to 2-methyl-1-butene, which can be dehydrogenated to isoprene, but this method remains at the experimental stage.
SNAM in Italy commercially produces isoprene by using acetylene and acetone, but the plant is no longer operational. A similar plant exists in South Africa. This method produces high-purity isoprene but is relatively expensive.
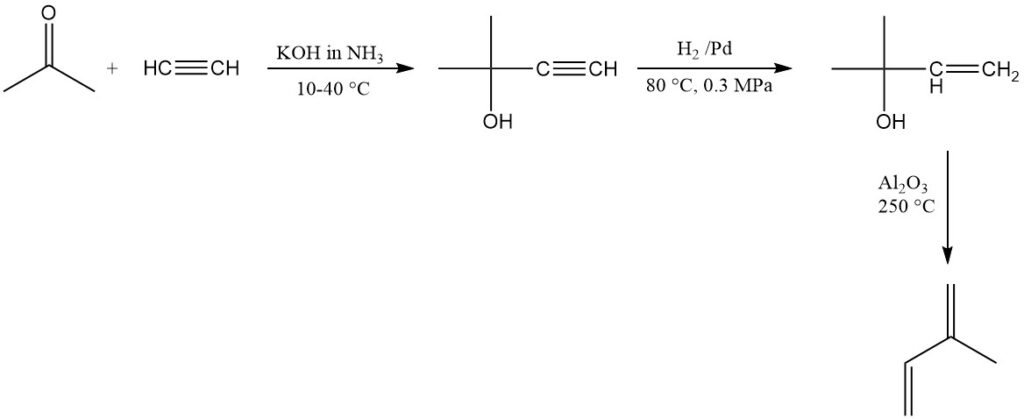
The Goodyear-Scientific Design process produced isoprene by propene dimerization to 2-methyl-1-pentene, followed by isomerization to 2-methyl-2-pentene and subsequent cracking. The first commercial isoprene synthesis used this approach (Beaumont, Texas), but production ceased in 1975 due to rising propene costs.

Olefin metathesis offers an attractive approach using readily available petrochemicals. A butene fraction is converted to 2-methyl-2-butene and propene, with subsequent dehydrogenation of 2-methyl-2-butene to isoprene. However, this method suffers from byproduct formation due to reactions between various olefins in the reactor.
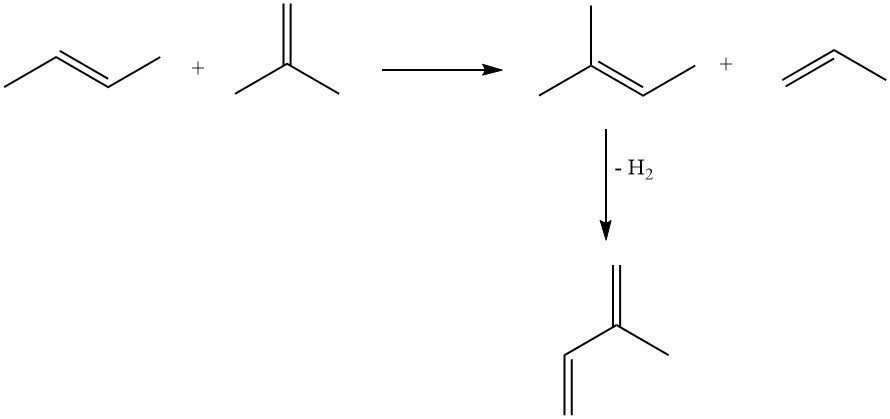
3.2. Production of Isoprene by Dehydrogenation of Isopentane or Methylbutenes
Isoprene can be produced by dehydrogenation of isopentane or methylbutenes (isopentenes). These reactions are similar to the dehydrogenation of n-butane and n-butenes to butadiene.
One-step dehydrogenation of isopentane to isoprene can be achieved using the Houdry-Catadiene process (Cr2O3/Al2O3 catalyst, ~600 °C, ~7 kPa), yielding 52% isoprene. This method was commercially used in the former Soviet Union.
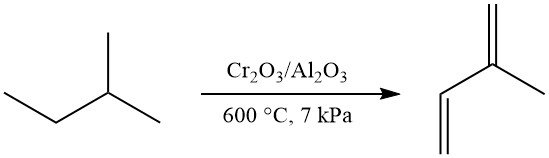
Isoprene production plants based on methylbutene dehydrogenation existed in the United States and the Netherlands but are not currently operational.
The starting material is typically extracted from cat-cracker off-gases using the Sinclair procedure (sulfuric acid extraction followed by back extraction with paraffins).
Dehydrogenation is done with a Shell catalyst (Fe2O3-K2CO3-Cr2O3) at 600 °C with steam dilution and achieves an 85% yield of isoprene.
Oxidative dehydrogenation of both isopentane and methylbutenes has been explored. Yields and selectivities of 60% and 95% for isoprene have been reported. Silicate catalysts doped with alkaline-earth oxides or oxides of nickel, iron, or cobalt are used for the oxidative dehydrogenation of methylbutenes to isoprene.
3.3. Recovery of Isoprene from C5 Cracking Fractions
Isoprene can be recovered from C5 byproducts from hydrocarbon pyrolysis in ethylene production. Naphtha cracking yields “crack gasoline” with low isoprene and other C5 hydrocarbons, primarily C6-C8 aromatics.
Distillation separates this mixture into C5 and aromatic fractions. Isoprene yield is typically 2–5 wt% based on ethylene, increasing with heavier feedstocks like gas oil. Isoprene yield decreases with higher cracking severity (temperature/residence time), but its concentration in the C5 fraction increases. Recovering isoprene from crack fractions is more energy-efficient than chemical synthesis.
Heavier cracker feedstocks for ethylene production will lead to more isoprene byproducts. Some crackers only recover an aromatic fraction from crack gasoline, while the C5 residue is often recycled with the C4 fraction in the cracker feed.
Pure isoprene isolation from the C5 fraction is not achievable by simple distillation due to the similar boiling points of the components and the formation of an azeotrope with n-pentane. Distillative enrichment to 25–50% is commercially used for reducing transportation and separation costs.
Separation techniques for producing pure isoprene are azeotropic distillation, chemical isolation, and extractive distillation using solvents such as N-methylpyrrolidone, dimethylformamide, and acetonitrile.
A simple isoprene isolation process is illustrated in Figure 1.
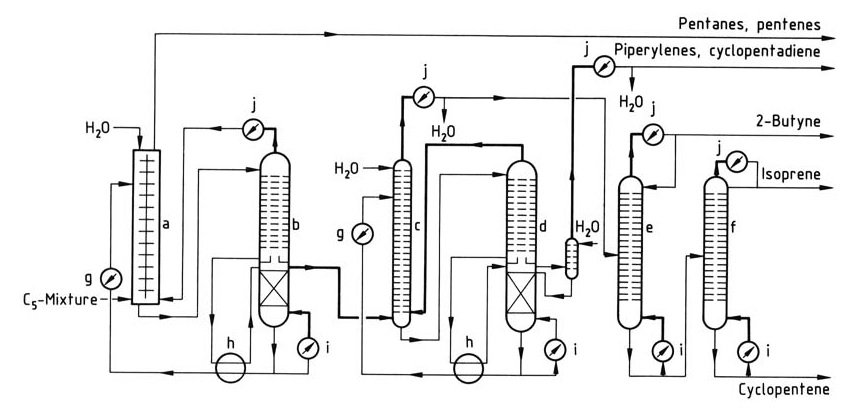
a) Liquid – liquid extraction column; b) – d) Columns for extractive distillation; e) Butyne column; f) Isoprene column; g) Cooler; h) Heat exchanger; i) Reboiler; j) Condenser
The first step is a combination of liquid-liquid extraction and extractive distillation, particularly suited for low-isoprene C5 fractions. Preconcentration of isoprene occurs in the extractor, followed by crude isoprene removal from the extractive distillation column.
Subsequent extractive distillation removes piperylenes and cyclopentadiene. Final purification for polymerization grade isoprene is achieved in additional distillation columns. This process allows the processing of C5 fractions containing cyclopentadiene, which is removed with piperylenes.
The process can be adapted to isolate cyclopentadiene or cyclopentene with additional equipment, and pure piperylenes can be recovered with a supplementary column.
4. Uses of Isoprene
4.1. Use of Isoprene in Polymer Synthesis
Poly(cis-1,4-isoprene) (isoprene rubber, IR), particularly the titanium-catalyzed type, is the primary application of isoprene. This synthetic rubber closely resembles natural rubber in structure and properties. Isoprene rubber is mainly used in vehicle tire production.
Poly(trans-1,4-isoprene) has properties similar to gutta-percha or balata, limiting its commercial applications primarily to cable insulation and golf balls.
The second largest market for isoprene is the production of styrene-isoprene-styrene (SIS) block copolymers, a type of thermoplastic elastomer. Around 0.79–0.88 tons of isoprene are consumed per ton of SIS polymer. These copolymers are used as thermoplastic rubbers and pressure-sensitive or thermosetting adhesives.
Smaller quantities of isoprene are used in the production of butyl rubber (isobutene-isoprene rubber, IIR), a copolymer with isobutene. The isoprene content in butyl rubber ranges from 0.5 to 3.0 mol%. IIR is known for its low gas permeability, making it suitable for hoses and liners in tubeless tires.
Finally, hydrocarbon resins (petroleum resins) can be produced by copolymerizing isoprene from cyclopentadiene-free C5 crack fractions with other unsaturated C5 compounds.
4.2. Use of Isoprene in Terpene Synthesis
While isoprene undergoes various chemical reactions, only terpene synthesis is of industrial importance and is actively researched.
In 1972, Rhodia began developing a process for C10 terpene and derivative synthesis from isoprene, acetone, and acetylene. Isoprene reacts with hydrochloric acid to form prenyl chloride, which is then converted to dehydrolinalool in two steps.
Rhodia used dehydrolinalool for various syntheses but discontinued production. However, Kuraray in Japan continues to produce these compounds, squalane, and others from isoprene.
Rhodia previously used a Grignard synthesis to produce the C10 terpene alcohol lavandulol from two isoprene molecules.
Isoprene reacts via oligomerization or telomerization to form terpenes. Examples include the scientifically and industrially relevant linear oligomerization of isoprene to myrcene and the telomerization with N,N-diethylnerylamine (both C10 terpenes).
Naturally occurring terpenes consist of “head-to-tail” arranged isoprene units with specific double bond positions. Producing terpenes from isoprene requires replicating this structure, making C10 terpene synthesis from isoprene generally less favorable than alternative routes. Catalyst composition can influence the structure of dimethyloctadienes synthesized from isoprene.
Takabe et al. reported myrcene synthesis by oligomerization of isoprene using a sodium/dialkylamine catalyst. Nissan Chemical Industries developed and announced the industrial production of myrcene using this method.
Isoprene telomerization occurs with various compounds, including ammonia or amines. The regioselectivity can be manipulated by varying the amount and concentration of Brønsted and Lewis acids in the catalyst.
Isoprene reacts with diethylamine to form N,N-diethylnerylamine via a butyl lithium-catalyzed telomerization reaction. Further reactions from N,N-diethylnerylamine yield linalool, geraniol, nerol, hydroxycitronellal, citronellal, and menthol (Figure 2).
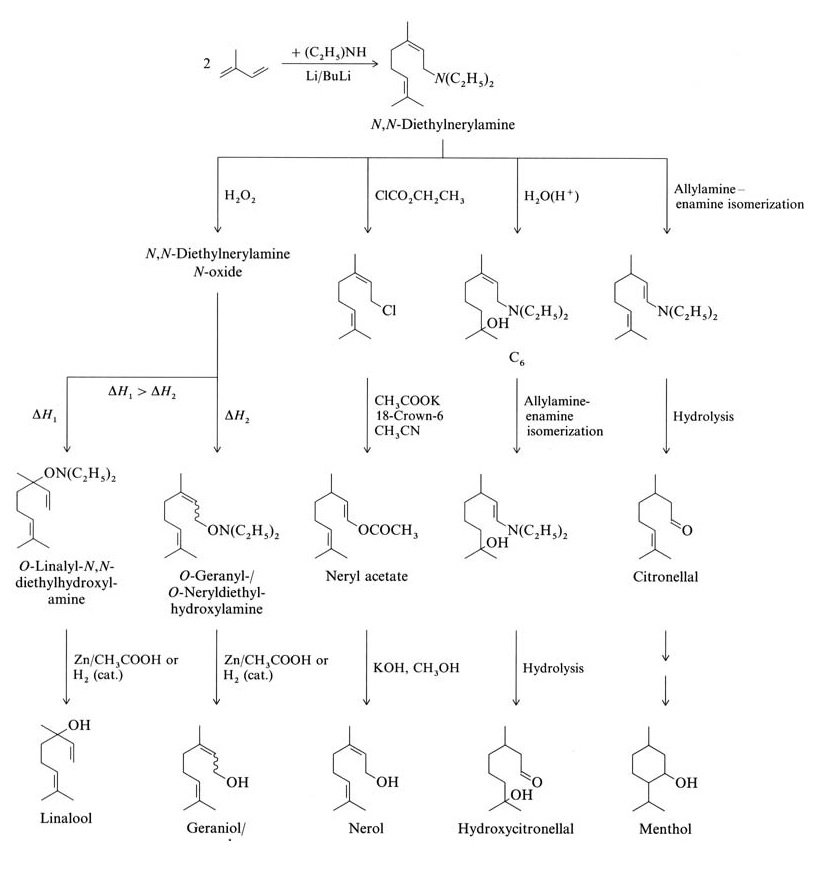
The Takasago Perfumery Company in Japan uses an industrial synthesis for enantiomerically pure L-menthol from optically active citronellal. This process involves the asymmetric allylamine-enamine isomerization of N,N-diethylgeranylamine or N,N-diethylnerylamine with a Rh-BINAP catalyst.
5. Toxicology of Isoprene
Acute Toxicity
High-level isoprene exposure causes anesthetic effects in animals, leading to paralysis and death. Single 2-hour inhalation exposures in mice (56,000 mg/m³) showed no adverse effects. Levels of 98,000–126,000 mg/m³ induced deep narcosis, and exposure to 140,000 mg/m³ for 2 hours caused mortality (LC50 = 180,000 mg/m³ for rats).
The threshold concentration for irritation in cats is reported as 800 mg/m³. Oral and intraperitoneal LD50 values in male rats were determined to be 2100 mg/kg and 1400 mg/kg, respectively, for liquid isoprene. Single dermal exposure (1 mL/kg) in rats caused no mortality or adverse symptoms.
Repeated Exposure Toxicity
Rats and mice were exposed to 0, 438, 875, 1750, 3500, and 7000 ppm isoprene for two weeks via inhalation. Rats showed no exposure-related changes.
Mice exposed to 7000 ppm showed lower body weight gain, while all groups displayed anemia, testicular atrophy, olfactory epithelial degeneration, and epithelial hyperplastic changes in the stomach. Similar to 1,3-butadiene, mice appear to be more susceptible than rats.
Repeated dermal exposure (500 mg x 2 applications/day for 5 days) on rabbit ears caused only mild, reversible irritation. Long-term inhalation exposure data is unavailable.
Mutagenicity
Isoprene and its monoepoxides are not mutagenic in the Ames test. However, isoprene dioxide (2-methyl-1,2,3,4-diepoxybutane) exhibited mutagenicity in this test system.
Due to potential similarities with 1,3-butadiene in generating mutagenic metabolites, further evaluation of isoprene’s carcinogenicity is warranted.
Inhalational exposure of mice to 438–7000 ppm isoprene for 6 h/day over 12 days resulted in increased sister chromatid exchange frequencies, indicating cytogenetic effects.
Data on reproductive or teratogenic effects is unavailable.
Metabolism
Rodent mitochondrial fractions convert isoprene to its monoepoxides (3,4-epoxy-3-methyl-1-butene and 3,4-epoxy-2-methyl-1-butene), leading to corresponding diols. Minor oxidation of the more stable metabolite (3,4-epoxy-2-methyl-1-butene) to a diepoxide has been reported.
Isoprene undergoes a significant metabolism in the respiratory tract. Up to 300 ppm atmospheric isoprene exposure displays a direct proportionality between exposure concentration and metabolism. Saturation effects occur above 300–500 ppm. Mice metabolize isoprene at a faster rate than rats.
Endogenous isoprene synthesis has been observed. Synthesis rates in unexposed mice and rats are estimated to be 0.4 mmol h⁻¹ kg⁻¹ and 1.9 mmol h⁻¹ kg⁻¹, respectively.
Human Effects
At very high exposure levels, isoprene acts as a narcotic in humans. It may also irritate the skin, eyes, mucous membranes, and respiratory tract.
Hygienic Standards
No threshold limit value (TLV) or maximum allowable concentration (MAK) has been established for isoprene. The former Soviet Union set a threshold of 40 mg/m³.
References
- Isoprene; Ullmann’s Encyclopedia of Industrial Chemistry. – https://onlinelibrary.wiley.com/doi/10.1002/14356007.a14_627
- https://www.nature.com/articles/s42004-019-0120-9
- https://bmcchem.biomedcentral.com/articles/10.1186/s13065-023-01016-y
- https://www.sciencedirect.com/science/article/abs/pii/S0045653519319812