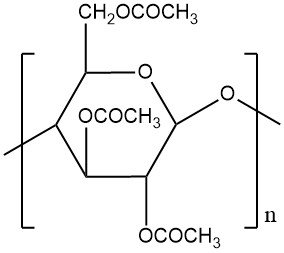
L’acétate de cellulose est un thermoplastique d’importance commerciale, formé à partir de l’acétylation de la cellulose (un polymère naturel). Cette réaction convertit tous les groupes hydroxyle primaires et secondaires de la chaîne cellulosique en triacétate de cellulose, un intermédiaire entièrement estérifié, qui peut être isolé ou traité ultérieurement.
Après l’acétylation, une étape d’hydrolyse contrôlée régénère une proportion souhaitée de groupes hydroxyle, personnalisant le degré de substitution acétyle (DS) par unité glucose sur la structure cellulosique. DS, exprimé en degré d’estérification ou de substitution, va de 0 au maximum théorique de 3.
Des altérations chimiques supplémentaires lors de la préparation de l’acétate de cellulose comprennent la sulfatation et la désulfatation des groupes hydroxyle, ainsi que la scission contrôlée de la chaîne, toutes facilitées par l’action catalytique du catalyseur d’acétylation prédominant, l’acide sulfurique.
Table des matières
Il existe plusieurs réactifs d’acétylation potentiels, notamment l’acide acétique, le chlorure d’acétyle, le cétène et l’anhydride acétique. L’acide acétique présente une réactivité lente, ce qui donne des produits à très faible teneur en acétyle. Le chlorure d’acétyle, bien qu’étudié en combinaison avec des catalyseurs, manque de viabilité commerciale.
Le cétène, bien qu’il ne produise aucun sous-produit, n’a pas connu le succès en tant qu’agent commercialement efficace. En conséquence, l’anhydride acétique est le plus efficace, réagissant avec trois groupes hydroxyle par unité de glucose pour produire trois molécules d’acide acétique comme sous-produit.
La première application de l’anhydride acétique en 1869 impliquait une réaction directe avec la cellulose à 180°C, provoquant probablement une dégradation importante du produit. La découverte des avantages catalytiques par Franchimont en 1879 a facilité le traitement à basse température avec une dégradation réduite.
De nombreux catalyseurs d’acétylation ont été identifiés, mais l’acide sulfurique est commercialement important. L’acide perchlorique, bien qu’utilisé commercialement, entraîne des risques de corrosion des équipements et des problèmes de sécurité en raison de l’instabilité de ses sels neutralisés.
D’autres acides minéraux manquent d’acidité suffisante dans le milieu typique acide acétique-anhydride acétique pour être efficaces. Le chlorure de zinc, autrefois utilisé commercialement, a été abandonné en raison des exigences de dosage élevées et des coûts de récupération.
L’un des principaux avantages de l’acide sulfurique réside dans son absorption rapide à la surface des fibres de cellulose lors du prétraitement, avant l’ajout d’anhydride acétique. Ce gonflement et cette répartition uniforme du catalyseur améliorent la réactivité ultérieure de la masse cellulosique.
Il est important de noter que l’acide sulfurique catalyse également la scission contrôlée des chaînes par l’hydrolyse des liaisons glycosidiques, permettant ainsi d’obtenir les réductions souhaitées du poids moléculaire.
Lors de l’ajout d’anhydride acétique en excès stoechiométrique à la cellulose prétraitée, l’acide sulfurique forme un intermédiaire acide ester sulfate de cellulose. De plus, l’acide sulfurique réagit avec l’anhydride acétique pour produire de l’acide acétylsulfurique, tous deux jouant probablement un rôle important dans la réaction d’estérification.
L’intermédiaire acide ester sulfate de cellulose réagit ensuite avec le milieu acide acétique-anhydride acétique environnant, remplaçant le groupe ester sulfate par acétyle. Cette réaction exothermique doit être équilibrée avec le taux de scission de chaîne catalysée (acétolyse) pour atteindre le poids moléculaire du produit souhaité.
L’hydrolyse des groupes acétyle, contrôlée par la concentration en acide sulfurique et en eau, se produit après estérification complète. Le degré souhaité de substitution acétyle est atteint en ajustant la teneur en eau et le temps d’hydrolyse. Enfin, le catalyseur est neutralisé avec un sel d’acétate pour terminer le processus.
Il est à noter qu’une partie des groupes sulfate introduits lors du prétraitement reste liée à la cellulose sous forme d’ester sulfate combiné même après acétylation. Cependant, ces groupes sont largement hydrolysés lors de l’étape suivante d’ajout d’eau, contribuant ainsi à une scission contrôlée de la chaîne et à la personnalisation des propriétés finales du matériau.
1. Matières premières pour acétate de cellulose
La production d’acétate de cellulose est réalisée en faisant réagir deux matières premières principales : la cellulose de haute pureté et l’anhydride acétique. L’obtention de performances post-traitement optimales dépend de la sélection de ces ingrédients cruciaux.
1.1. Cellulose
Les linters de coton offrent une matière première de qualité supérieure avec une pureté supérieure à 99 % d’α-cellulose. Après l’élimination des fibres de coton filables, deux coupes supplémentaires du linter sont réalisées.
La première coupe (4 %), principalement utilisée pour le coton et le feutre médicaux, donne des fibres plus longues. La deuxième coupe (8 %), plus riche en fibres plus courtes et en couches, est idéale pour le traitement chimique.
Les linters bruts subissent une purification rigoureuse : nettoyage mécanique, ébullition dans de la soude diluée et blanchiment acide-alcalin. Un séchage contrôlé est crucial, car un séchage excessif local (au-delà de la fenêtre d’humidité de 3 à 8 %) atténue considérablement la réactivité. Le tableau 1 résume les valeurs analytiques typiques des linters de haute qualité.
Composant | Contenu |
---|---|
α-cellulose | 99,7 % |
β-cellulose | 0,2 % |
γ-Cellulose | 0,1 % |
Groupes carboxyles | <0,02 % |
Cendres totales | 0,02 % |
Degré de polymérisation | 1 000 – 7 000 |
La pâte de bois est la matière première dominante et englobe à la fois les sources de résineux et de feuillus. Historiquement, la teneur limitée en α-cellulose (90 à 95 %) limitait l’utilisation de la pâte de bois en raison d’une production d’acétate de moindre qualité.
Cependant, les progrès des techniques de fabrication de pâte au sulfite et kraft ont permis une élimination efficace de la lignine et de l’hémicellulose, augmentant la teneur en α-cellulose au-dessus de 95 %.
Depuis les années 1950, la rentabilité de la pâte de bois de plus grande pureté a progressivement supplanté les linters de coton. Remarquablement, les acétates de cellulose à base de pâte de bois présentent une résistance à la traction, une couleur, une clarté de solution et une stabilité à la lumière et thermique comparables à celles de leurs homologues en linter.
1.2. Anhydride acétique
La plupart des fabricants optent pour la conversion sur site de l’acide acétique sous-produit en anhydride acétique, en ajustant les concentrations (90 à 95 %) en fonction de leurs processus spécifiques.
2. Processus de production industrielle d’acétate de cellulose
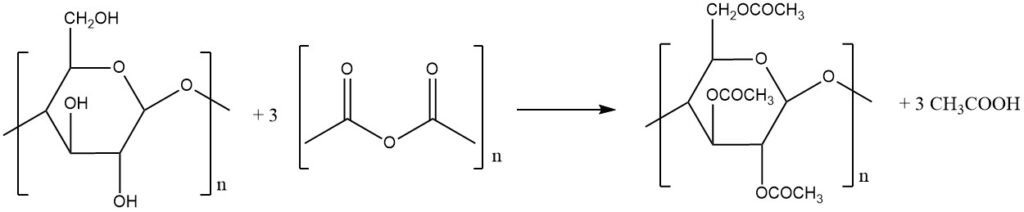
Bien que de nombreuses voies de production d’esters de cellulose aient été proposées, seules quelques-unes sont utilisées industriellement. Bien que les méthodologies spécifiques varient d’un fabricant à l’autre, deux grandes catégories existent :
1. Acétylation homogène (procédé à l’acétate en solution) :
Procédé à l’acide acétique glacial : Utilisant l’acide acétique glacial comme solvant, cette méthode permet une acétylation et une hydrolyse contrôlées, atteignant les niveaux de substitution souhaités. tout au long de la chaîne polymère.
Procédé au chlorure de méthylène : Le remplacement de l’acide acétique par du chlorure de méthylène comme solvant donne un résultat similaire, avec l’avantage de temps de réaction plus rapides.
2. Acétylation hétérogène (procédé à l’acétate de fibres) :
Cette méthode forme directement des fibres de triacétate de cellulose, imitant la nitration de la cellulose. Cependant, il n’a pas la capacité d’hydrolyser uniformément les groupes acétyle, ce qui limite sa polyvalence par rapport aux processus en solution.
Le processus de solution d’acide acétique glacial :
La figure 1 montre un organigramme typique de cette technique largement utilisée. En bref, le processus implique :
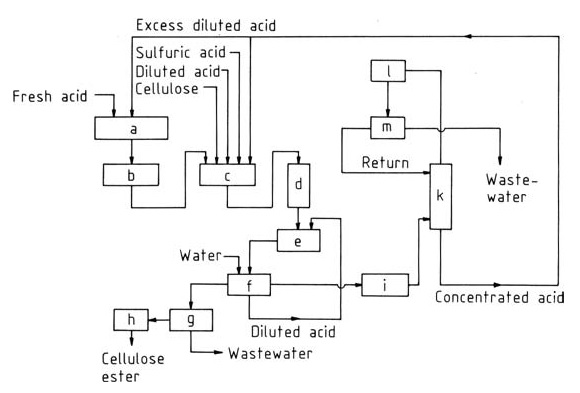
a) Reconditionnement acide ; b) Anhydride acétique ; c) Estérification ; d) Hydrolyse ; e) Précipitations ; f) Lavage ; g) Centrifugeuse ; h) Séchoir ; i) Évaporateur ; k) Distillation azéotropique ; l) Refroidisseur ; m) Carafe
- Prétraitement : la cellulose est purifiée et gonflée de manière appropriée, généralement dans de l’acide acétique et de l’acide sulfurique, pour une acétylation efficace.
- Acétylation : la cellulose réagit avec l’anhydride acétique en présence d’un catalyseur d’acide sulfurique, convertissant les groupes hydroxyle en liaisons ester et formant du triacétate de cellulose.
- Hydrolyse : pour atteindre le degré de substitution souhaité, une étape d’hydrolyse contrôlée élimine certains groupes acétyle à l’aide d’eau et d’un contrôle de température approprié.
- Neutralisation : le catalyseur est neutralisé, généralement avec de l’acétate de calcium, pour stabiliser le produit final.
- Filtration et lavage : la solution d’acétate de cellulose est filtrée, lavée et concentrée avant d’être transformée en films, fibres ou autres formes souhaitées.
2.1. Prétraitement de la cellulose
D’un point de vue purement chimique, l’estérification des groupes hydroxyles de la cellulose puis l’hydrolyse de ces esters peuvent sembler simples. Cependant, l’architecture unique des fibres de cellulose présente des défis pratiques qui nécessitent des techniques de traitement spécialisées.
Une étape cruciale est le prétraitement, également appelé activation. Cela implique de gonfler les fibres pour faciliter une diffusion efficace des produits chimiques d’acétylation lors de la réaction d’estérification suivante.
Bien que divers agents gonflants comme l’eau, les alcools et les amines soient théoriquement possibles, l’acide acétique est le plus couramment utilisé dans la production commerciale d’acétate de cellulose. Les options sans acide acétique nécessitent un remplacement par de l’acide acétique avant l’acétylation.
Idéalement, la cellulose contient 4 à 7 % d’humidité. Cette valeur dépend fortement des pratiques de séchage du producteur et de l’humidité ambiante avant utilisation. Bien que l’humidité inhérente facilite l’activation, elle entraîne des coûts supplémentaires en réagissant avec l’anhydride pendant l’estérification. À l’inverse, une faible humidité inhibe l’activation et ralentit la réaction d’estérification.
Les ratios acide acétique/cellulose, les temps d’activation et les températures varient selon les fabricants. Souvent, une petite quantité d’acide sulfurique est ajoutée au milieu d’activation. Cela améliore encore le gonflement des fibres et permet une distribution uniforme du catalyseur avant l’acétylation.
De plus, le catalyseur induit une scission contrôlée des chaînes dans la cellulose en hydrolysant les liaisons glycosidiques. L’étendue de la scission de la chaîne dépend de facteurs tels que la température, l’uniformité du catalyseur et la teneur en eau. Une humidité plus élevée de la pâte retarde la scission de la chaîne en solvatant le catalyseur acide fort.
2.2. Estérification de la cellulose
L’estérification des groupes hydroxyles de la cellulose est réalisée par deux voies dominantes : le procédé à l’acide acétique et le procédé au chlorure de méthylène.
1. Processus à l’acide acétique
Un mélange hétérogène composé d’acide acétique glacial, d’anhydride acétique (10 à 40 %), de cellulose activée et d’un catalyseur d’acide sulfurique à 2-15 % initie la réaction. La réaction commence par une interaction exothermique rapide entre l’eau contenue dans la cellulose activée et une partie de l’anhydride acétique.
Les fibres de cellulose non estérifiées et partiellement estérifiées restent dispersées dans tout le milieu réactionnel. Le contrôle de la température via le refroidissement de la cuve et les réactifs pré-refroidis est utilisé pour atteindre 50 °C.
L’estérification complète induit la dissolution des fibres, formant une solution très visqueuse. La scission de chaîne contrôlée, médiée par les niveaux de catalyseur, la température, la durée et le rapport acide/anhydride, optimise la solubilité dans le milieu réactionnel et les propriétés du produit final.
Si la réaction peut se dérouler vers le triacétate de cellulose entièrement substitué via le remplacement des groupes ester sulfate restants par des groupes acétyle, la viscosité de la solution augmentera considérablement jusqu’à ce que la masse réactionnelle se gélifie.
Après dissolution complète des fibres, l’eau ou l’acide acétique dilué éteint la réaction, consommant l’excès d’anhydride et préparant l’hydrolyse ultérieure.
Les malaxeurs refroidis dotés de capacités de mélange intensives garantissent un mélange et une distribution efficaces du catalyseur et sont importants pour le contrôle de la réaction. (Figure 2)
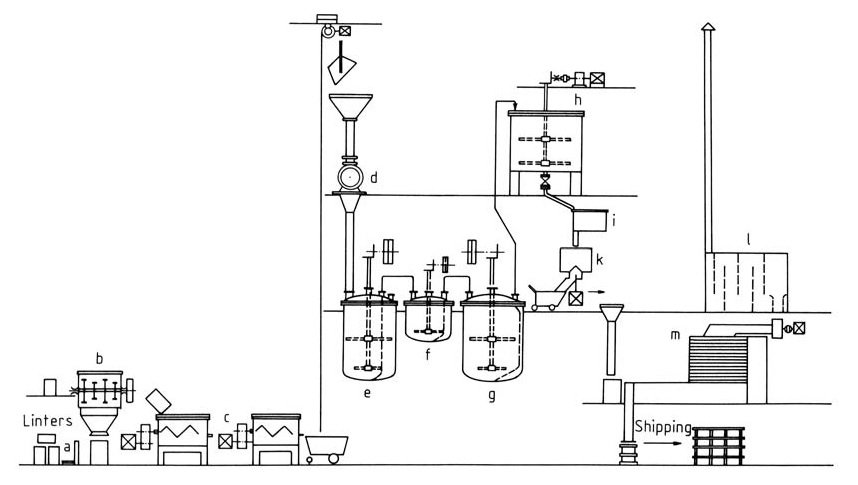
a) Balance ; b) Cuve d'arrosage ; c) Pétrin ; d) Moulin ; e) Rinçage de la cuve ; f) Bac de stabilisation ; g) Cuve de blanchiment ; h) Flotteur ; i) Casserole à bouillon ; k) Centrifugeuse ; l) Chambre à poussière ; m) Plus sec
2. The Methylene Chloride Process
Methylene chloride offers several benefits over acetic acid, including lower catalyst requirements, effective heat removal via vaporization (facilitating reaction control), and reduced recycle volume. However, higher esterification temperatures are employed compared to the acetic acid process, while catalyst concentrations decrease to 1% sulfuric acid.
Rotating drums or horizontal containers with stirrers are commonly used due to their suitability for viscous solutions. Corrosion resistance is imperative in this process.
To maintain the fibrous structure during esterification, nonsolvents like carbon tetrachloride, benzene, or toluene are used as the reaction medium. However, uniform hydrolysis is difficult in this heterogeneous system, limiting its application to specific uses like triacetate foils and films.
Perforated drums with rotating capabilities efficiently handle mixing and processing in this process.
2.3. Hydrolysis
The solution esterification process yields a solubilized cellulose triacetate, commercially known as primary acetate, with an approximate acetyl degree of substitution (DS) of 2.9. However, cellulose diacetate (secondary acetate, acetyl DS ~2.5) constitutes the most prevalent commercially available hydrolyzed cellulose acetate product.
Following esterification, water is added and its content adjusted to 5-10%, affecting the final ratio of primary and secondary hydroxyl groups. Typical hydrolysis temperatures vary between 40 and 80°C, primarily dictated by catalyst concentration and temperature. Higher water concentrations can reduce excessive chain scission during hydrolysis.
Hydrolysis progress is monitored by tracking the solubility of the secondary acetate. Upon completion, the sulfuric acid catalyst is neutralized with magnesium, sodium, or calcium acetate. This neutralization also targets the remaining trace sulfate groups bound to the polymer, enhancing stability during isolation and subsequent processing steps.
2.4. Precipitation and Processing
Following hydrolysis, transforming the viscous cellulose acetate solution into a solid form for further processing involves precipitation. Two methods are available:
- Direct Precipitation: Pouring the solution into water (optionally with diluted acetic acid) induces immediate precipitation, resulting in flake-like particles.
- Controlled Precipitation: Gradually adding a diluted acetic acid solution to the stirred solution allows finer control over particle formation, typically yielding a powder-like product.
The chosen method and specific precipitation conditions, including acid concentration, agitation intensity, and temperature, critically influence the final particle morphology. Careful optimization ensures an open pore structure, facilitating efficient removal of residual acids and salts during subsequent water washing.
For the methylene chloride process, solvent must be completely removed via distillation before precipitation. The resulting precipitate is then washed, with the recovered dilute acetic acid recycled back into the production cycle.
Continuous countercurrent washing systems are preferred for thorough purification. High-quality plastic applications may require additional stabilization and bleaching steps. Residual combined sulfate groups can be eliminated by pressure boiling or treatment with dilute mineral acids during stabilization.
Following further rinsing and water removal (e.g., suctioning, centrifugation, pressing, or thrust extraction), the cellulose acetate is carefully dried, ideally in a vacuum shovel drier, to achieve a final moisture content less than 1-3%. An efficient process can achieve a cellulose acetate yield exceeding 95% of the theoretical maximum.
3. Utilisations de l’acétate de cellulose
Des exemples d’acétate de cellulose dans les produits du quotidien comprennent les montures de lunettes, les filtres de cigarettes, certains textiles des vêtements et même les réservoirs d’encre des feutres.
L’acétate de cellulose est utilisé dans divers secteurs commerciaux, principalement sous forme de films, de fibres, de plastiques et de revêtements. Bien que le triacétate et le diacétate de cellulose aient des utilisations distinctes, cette section se concentre sur le diacétate de cellulose, souvent simplement appelé acétate de cellulose à des fins commerciales.
Le triacétate de cellulose est utilisé dans :
- Support de film : Depuis les années 1950, le triacétate de cellulose sert de support de film transparent et lisse pour les émulsions photographiques en raison de son isotropie optique, clarté, solidité et résistance aux rayures et à l’humidité.
- Écrans à cristaux liquides (LCD) : récemment, le triacétate de cellulose a trouvé une niche dans la protection des films polarisants des écrans LCD pour divers appareils comme les téléviseurs, les moniteurs et les téléphones portables, en raison de son taux de transmission élevé de vapeur d’humidité.
Le diacétate de cellulose est utilisé dans :
- Films : En raison de sa plus grande compatibilité avec les solvants et les plastifiants, le diacétate de cellulose excelle dans diverses applications de films. Les rubans sensibles à la pression, les fenêtres d’emballage et les stratifiés de protection bénéficient de sa transparence, de sa stabilité dimensionnelle et de sa résistance à la déchirure. De plus, il peut être coulé dans des porosités spécifiques pour les membranes d’osmose inverse lors de la purification de l’eau.
- Revêtements : Remplacement des nitrocellulose, l’acétate de cellulose est utilisé dans les revêtements depuis la Première Guerre mondiale. Les revêtements à base d’acétone sèchent rapidement, tandis que d’autres solvants et plastifiants sont ajoutés pour obtenir la rhéologie et les propriétés du film souhaitées. Les applications incluent les laques pour isolants, le verre, le carton, les emballages alimentaires, etc.
- Produits pharmaceutiques : fabriqué à l’aide de techniques cGMP, l’acétate de cellulose est utilisé dans les médicaments osmotiques et les systèmes à libération prolongée.
- Biodégradabilité : Dans des conditions spécifiques, notamment une faible substitution acétyle, une morphologie appropriée et des plastifiants choisis, l’acétate de cellulose peut se biodégrader dans certains environnements.
Référence
- Cellulose Esters; Ullmann’s Encyclopedia of Industrial Chemistry. – https://onlinelibrary.wiley.com/doi/10.1002/14356007.a05_419.pub2