
Le disulfure de carbone, CS2, est un composé chimique important largement utilisé dans diverses applications industrielles. Sa découverte peut être attribuée à Lampadius en 1796, qui est tombé dessus en chauffant une combinaison de pyrite de fer et de carbone.
Le composé a suscité un intérêt industriel dès 1839 lorsque Schrötter l’a synthétisé avec succès en utilisant du charbon de bois et du soufre dans une cornue chauffée. Les remarquables capacités de solvant du disulfure de carbone ont été rapidement reconnues, ce qui a conduit à son utilisation généralisée dans l’extraction des graisses et des huiles pendant une période considérable.
Cependant, sa véritable signification en tant que produit chimique industriel à grande échelle est apparue avec l’avènement du procédé de rayonne viscose au début des années 1900. Ce processus reposait sur le disulfure de carbone pour dissoudre la cellulose, établissant ainsi son rôle central dans l’industrie.
Néanmoins, la croissance rapide de la rayonne a connu des revers à la fin des années 1960 en raison de la concurrence des fibres synthétiques à base de pétrole, entraînant un déclin ultérieur des marchés de la rayonne et du disulfure de carbone tout au long des années 1970. Cependant, ces derniers temps, l’utilisation du disulfure de carbone s’est stabilisée et une petite croissance du marché est prévue pour l’avenir.
En 1984, sur la production mondiale totale de 1,1 million de tonnes de disulfure de carbone, plus de 75 % étaient principalement consommés par l’industrie de la cellulose régénérée. La partie restante a trouvé son application dans la production de tétrachlorure de carbone et de divers composés organosoufrés, qui sont largement utilisés comme produits chimiques pour le caoutchouc, agents de flottation et pesticides.
Table des matières
1. Propriétés physiques du disulfure de carbone
Le disulfure de carbone est un liquide hautement volatil de densité importante, présentant une large plage d’inflammabilité en présence d’air, allant de 1 à 50 % en volume. Il possède notamment une température d’auto-inflammation exceptionnellement basse de 100 °C et un point d’éclair de -30 °C. Son taux d’évaporation dans l’atmosphère dépasse celui de l’éther diéthylique d’un facteur 1,6.
Ce composé sert de solvant exceptionnel pour de nombreuses substances organiques, dissolvant facilement le soufre, le phosphore, l’iode, les cires, le caoutchouc et les résines. La forme disponible dans le commerce dégage un arôme piquant, caractéristique des composés à base de soufre.
Certaines des propriétés physiques les plus utiles du disulfure de carbone sont les suivantes :
- Masse molaire = 76,13 g/mol
- Point de fusion = -111,6 °C
- Point d’ébullition = 46,23 °C
- Densité à 25 °C = 1,26 g/ml
- Température critique = 273 °C
- Pression critique = 7600 kPa
- Tension superficielle à 20 °C = 32,3 mN/m
- Indice de réfraction à 20 °C = 1,62546
- Viscosité à 25 °C = 0,36 mPa.s
2. Réactions chimiques du disulfure de carbone
Le disulfure de carbone présente un large éventail de réactions chimiques qui ont été largement étudiées et documentées.
Lorsque le disulfure de carbone réagit avec les sulfures, les alcools, l’ammoniac, les amines et le chlore, il génère des dérivés et des intermédiaires d’importance industrielle. En présence d’alcalis aqueux, le disulfure de carbone réagit lentement pour former des composés de trithiocarbonate et de carbonate, comme représenté par l’équation :
3 CS2 + 6 NaOH → 2 Na2CS3 + Na2CO3 + 3 H2O
Les sulfures métalliques forment des trithiocarbonates lorsqu’ils réagissent avec du disulfure de carbone, comme le montre la réaction :
K2S (aqueux) + CS2 → K2CS3
De plus, lorsque le disulfure de carbone réagit avec des alcalis alcooliques, il donne des xanthates, qui sont des sels de dithiocarbonates, selon le processus suivant :
ROH + NaOH → RONa + H2O
RONa + CS2 → ROCSSNa
Cette réaction sert de base au processus de viscose, dans lequel la cellulose est convertie en xanthate puis régénérée sous forme de fibres et de films, comme le montre la réaction :
(cellulose)ONa + CS2 → (cellulose)OCSSNa
2(cellulose)OCSSNa + H2SO4 → 2(cellulose)OH + 2 CS2 + Na2SO4
En présence d’ammoniac, le disulfure de carbone forme du dithiocarbamate d’ammonium (1), du trithiocarbonate d’ammonium (2) et du thiocyanate d’ammonium (3), en fonction de la concentration d’ammoniac et de la température :
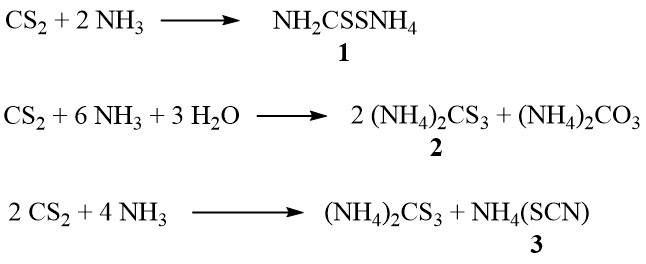
De plus, à des températures plus élevées en phase vapeur, le thiocyanate se décompose pour produire de la thiourée :
NH4(SCN) → SC(NH2)2
Les amines primaires et secondaires produisent principalement des sels de dithiocarbamate dans leur réaction avec le disulfure de carbone :
2 RNH2 + CS2 → RNHCSSNH3R
2 R2NH + CS2 → R2NCSSNH2R2
En présence d’alcalis, divers sels commercialement importants d’acide dithiocarbamique peuvent être obtenus :
R2NH+ CS2 + NaOH → R2NCSSNa + H2O
La réaction du disulfure de carbone avec la méthylamine et la soude caustique dans une solution aqueuse produit du méthyldithiocarbamate de sodium (CH3NHCSSNa), un fumigant de sol essentiel. De même, le disulfure de carbone réagit avec l’éthylènediamine pour donner le fongicide éthylène bis (dithiocarbamate) de sodium :

Les réactions d’aniline et de disulfure de carbone entraînent la formation de deux accélérateurs de vulcanisation importants. En l’absence de soufre, on produit du thiocarbanilide, tandis qu’en présence de soufre, on obtient du 2-mercaptobenzothiazole (MBT) :
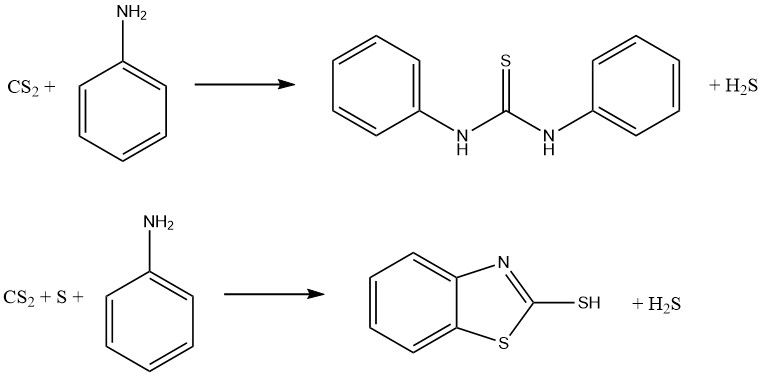
Les dithiocarbamates peuvent être oxydés pour former une famille de composés connus sous le nom de disulfures de thiurium, qui sont utilisés comme fongicides et accélérateurs de vulcanisation. La réaction implique l’équation suivante :
2 R2NCSSNa + H2O2 + H2SO4 → (R2NCSS–)2 + Na2SO4 + 2 H2O
La chloration du disulfure de carbone conduit à la formation de divers produits chlorés. Sous catalyse à l’iode, la chloration à des températures comprises entre 5 et 30 ° C produit du chlorure de trichlorométhanesulfényle, ainsi que du tétrachlorure de carbone, du dichlorure de soufre et du thiophosgène, selon le degré de chloration.
En présence de fer et de chlorures métalliques à des températures plus élevées (70 – 100 °C), on obtient exclusivement du tétrachlorure de carbone et des chlorures de soufre.
Le disulfure de carbone réagit facilement avec l’eau en présence de catalyseurs d’alumine et d’oxyde au-dessus de 150 °C, produisant du dioxyde de carbone et du sulfure d’hydrogène. Le sulfure de carbonyle agit comme intermédiaire dans cette réaction d’hydrolyse. À des températures allant de 200 à 300 °C, la conversion du disulfure de carbone en ces produits atteint l’équilibre.
Lorsqu’il est soumis à des températures élevées (supérieures à 150 – 200 ° C) en présence de catalyseurs de sulfure métallique comme les sulfures de molybdène et de nickel, le disulfure de carbone subit une réduction par l’hydrogène, ce qui donne des quantités variables de méthanethiol, de sulfure de diméthyle, de méthane et de sulfure d’hydrogène.
3. Production de sulfure de carbone
Le disulfure de carbone est produit par la réaction du soufre avec du charbon de bois ou du méthane. Bien que l’éthane, le propane et le propène aient été utilisés dans une mesure limitée, le procédé au méthane a acquis une importance significative depuis son introduction au début des années 1950.
Par conséquent, l’ancien procédé au charbon de bois n’est plus pertinent dans la fabrication de disulfure de carbone aux États-Unis, en Europe et au Japon. Cependant, dans les régions où le gaz naturel ou le méthane ne sont pas facilement accessibles ou lorsque la taille de l’usine est relativement petite, le procédé au charbon de bois est toujours utilisé pour répondre à la demande locale de production de rayonne viscose.
3.1. Production de disulfure de carbone à partir de charbon de bois et de soufre
Le processus fondamental de la réaction du charbon de bois avec le soufre a subi des changements minimes depuis sa création au milieu des années 1840. Des autoclaves chauffés de l’extérieur sont toujours utilisés, bien que la conception de l’équipement se soit considérablement améliorée grâce à la disponibilité de matériaux de construction de qualité supérieure.
Dans les usines d’autoclave, le soufre fondu est vaporisé et surchauffé avant ou après avoir été introduit dans l’autoclave. Dans la cornue, à des températures allant de 850 à 900 °C et légèrement au-dessus de la pression atmosphérique, la vapeur de soufre surchauffée réagit avec un lit fixe de charbon de bois.
Le gaz produit résultant, qui comprend du disulfure de carbone, du soufre, du sulfure d’hydrogène, du sulfure de carbonyle et des gaz inertes, passe à travers une série de condenseurs, d’épurateurs et d’absorbeurs d’huile pour récupérer le disulfure de carbone brut.
Un traitement ultérieur dans des colonnes de distillation donne le produit pur. Le gaz résiduaire, composé principalement de sulfure d’hydrogène, de sulfure de carbonyle et de gaz inertes, peut être soit incinéré et lavé avec une solution caustique, soit dirigé vers une usine de récupération du soufre.
Typiquement, chaque autoclave est capable de produire 1 à 3 tonnes métriques par jour de disulfure de carbone. La durée de vie utile des autoclaves en fonte est limitée à moins d’un an en raison de la corrosion à haute température. Pour minimiser le besoin de nettoyage du réacteur, les matières premières utilisées dans les autoclaves doivent avoir une faible teneur en cendres et en résidus. L’encrassement des cornues entrave le transfert de chaleur et réduit leur durée de vie.
La qualité du charbon de bois est cruciale, car les matériaux moins réactifs nécessitent des températures plus élevées pour un fonctionnement satisfaisant. Le charbon de bois dérivé de bois dur est préféré pour cette raison.
Le charbon de bois est généralement précalciné à 500 ° C pour éliminer les substances volatiles qui pourraient conduire à la formation de sous-produits indésirables. L’efficacité thermique des autoclaves est d’environ 25 %, avec des rendements en carbone et en soufre généralement inférieurs à 90 %.
Une source de chaleur alternative pour la réaction du charbon de bois avec le soufre est fournie par le chauffage par résistance électrique dans des réacteurs électrothermiques revêtus de briques. Lorsqu’une énergie peu coûteuse est disponible, la méthode électrique peut être plus rentable.
La consommation électrique par tonne métrique de sulfure de carbone produit est d’environ 1200 kWh. Les réacteurs électrothermiques offrent plusieurs avantages, notamment une plus grande capacité par réacteur (jusqu’à 10 tonnes métriques par jour) et une durée de vie prolongée du réacteur. De plus, une gamme plus large d’alimentation en carbone solide peut être utilisée car les réacteurs électrothermiques peuvent générer des températures plus élevées.
3.2. Production de disulfure de carbone à partir de méthane et de soufre
En raison de la demande croissante de disulfure de carbone dans les années 1940, les limites des procédés au charbon de bois ont incité le développement d’une méthode de fabrication à grande échelle plus efficace.
La réaction catalysée entre le méthane et le soufre, tirant parti du gaz naturel facilement disponible et rentable, est apparue comme une alternative réussie. De nombreux brevets ont été délivrés entre 1943 et 1965, couvrant divers aspects de ce procédé.
Le procédé commercial de méthane, principalement basé sur les brevets acquis par Pure Oil Co., a ensuite été repris par Food Machinery Corp. (FMC) et Stauffer Chemical Co.
En 1953, FMC a construit la première usine de traitement du méthane à South Charleston, en Virginie-Occidentale, suivie d’une usine Stauffer à LeMoyne, en Alabama, trois ans plus tard. Au milieu des années 1960, toute la production de disulfure de carbone aux États-Unis était réalisée par cette méthode, et des usines similaires ont rapidement émergé en Europe et dans d’autres régions.
Actuellement, plus de 85 % de la capacité de production mondiale de disulfure de carbone repose sur le procédé au méthane.
Un organigramme typique du procédé de méthane est illustré à la figure 1. Le gaz naturel purifié, contenant plus de 95 % de méthane et de faibles concentrations de propane et d’hydrocarbures plus lourds, est préchauffé à environ 250 °C dans la section de convection du four de réaction.
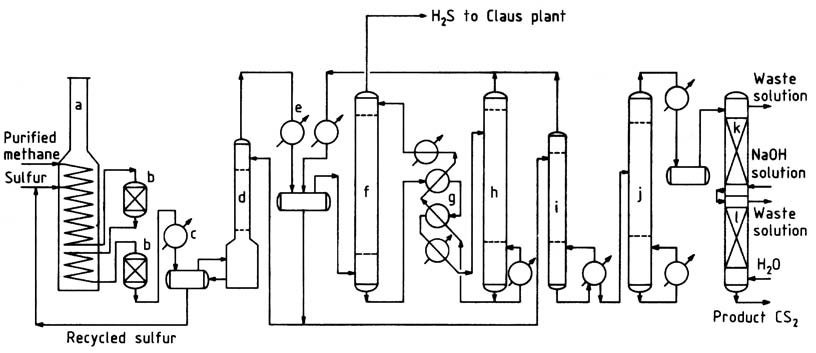
Le four, un four à pyrolyse de type boîte couramment employé dans l’industrie pétrochimique, est constitué de sections radiantes et de convection. Le gaz méthane chaud est mélangé avec du soufre liquide et introduit dans le serpentin de chauffage horizontal situé dans la section radiante.
Dans cette section, le soufre liquide se vaporise et la température du mélange monte à 550-650 °C. La pression de fonctionnement varie généralement de 400 à 700 kPa.
Alternativement, le méthane et le soufre peuvent être introduits séparément et à différents endroits dans le serpentin. Un léger excès de soufre (environ 5%) est utilisé pour assurer une conversion efficace du méthane et minimiser la formation de carbone et de goudron.
Pour résister à l’environnement corrosif à haute température, de l’acier inoxydable moulé fortement allié est utilisé comme matériau de tube, offrant une durée de vie d’environ 2 à 3 ans. Des réacteurs emballés et revêtus de briques sont connectés au serpentin de chauffage pour offrir un temps de séjour supplémentaire et un logement pour les lits de catalyseur.
La réaction a lieu à la fois dans les tubes et les réacteurs, assurant une conversion presque complète des hydrocarbures avant que le gaz ne sorte du dernier réacteur. Le gaz quittant le système de four de réaction passe à travers un condenseur de soufre, où la majeure partie du soufre en excès est séparée.
Ensuite, le gaz refroidi passe à un épurateur de soufre, puis à l’épurateur CS2, où le soufre restant est éliminé. Le gaz relativement exempt de soufre entre dans des condenseurs refroidis à l’eau pour la séparation en masse du disulfure de carbone.
Le disulfure de carbone restant est extrait du sulfure d’hydrogène gazeux dans l’absorbeur d’huile. Le sulfure d’hydrogène gazeux quittant l’absorbeur d’huile contient environ 1 à 2 % de méthane et moins de 1 000 ppm de disulfure de carbone.
Ce gaz est dirigé vers une usine de récupération de soufre Claus, où il subit une reconversion en soufre.
Le disulfure de carbone brut, y compris celui récupéré dans le stripper, est envoyé vers la colonne de stabilisation pour éliminer les impuretés à bas point d’ébullition.
Les fonds de la colonne de stabilisation subissent ensuite un traitement dans la colonne de purification pour séparer les contaminants à point d’ébullition élevé du produit. La purification du produit est complétée par des lavages caustiques et à l’eau, après quoi le produit fini est pompé pour vérifier les réservoirs et le stockage.
4. Utilisations du disulfure de carbone
Le principal consommateur de disulfure de carbone est l’industrie de la cellulose régénérée, qui représente plus de 65 % de la production mondiale. Plus précisément, la fabrication de la rayonne utilise une part importante de disulfure de carbone, avec environ 0,32 kg de disulfure de carbone consommé pour chaque kilogramme de rayonne produit.
Environ 10% du disulfure de carbone est utilisé dans la production de cellophane, tandis qu’un autre 10% est chloré pour produire du tétrachlorure de carbone. Cette méthode représente environ 25 % de la production mondiale de tétrachlorure de carbone.
Les 15% restants de disulfure de carbone sont répartis entre diverses applications, notamment les produits chimiques pour caoutchouc, les agents de flottation, les pesticides, divers réactifs chimiques, le solvant d’extraction, l’agent de présulfuration du catalyseur et le solvant pour puits de pétrole.
Cependant, l’industrie de la cellulose régénérée est confrontée à des défis en raison de la concurrence des fibres et des films synthétiques, ce qui limite la croissance de son marché. Pour favoriser le progrès, il est nécessaire d’améliorer progressivement l’utilisation du disulfure de carbone, en particulier grâce à une utilisation accrue dans la fabrication de produits chimiques agricoles et spécialisés.
Référence
- Carbon Disulfide; Ullmann’s Encyclopedia of Industrial Chemistry. – https://onlinelibrary.wiley.com/doi/10.1002/14356007.a05_185