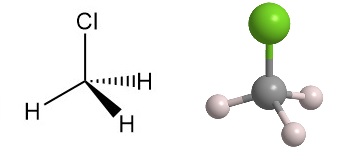
Chloromethane, also known as methyl chloride, is the simplest chlorinated derivative of methane with the chemical formula CH3Cl. It’s a colorless gas with a faint, sweet odor that occurs naturally in trace amounts but is primarily produced industrially.
Table of Contents
1. Physical Properties of Chloromethane
Chloromethane is a colorless and flammable gas with no odor. Its solubility in water depends on temperature, and it forms an azeotrope with water. The following table 1 represents its solubility at 0.1 MPa (1 bar):
T (°C) | Solubility (g of CH3Cl/kg of H2O) |
---|---|
15 | 9.0 |
30 | 6.52 |
45 | 4.36 |
60 | 2.64 |
The important physical properties of chloromethane are listed in the following table 2:
Property | Value |
---|---|
Molecular weight | 50.49 g/mol |
Boiling point at 1 bar | -24.0 °C |
Melting point | -97.7 °C |
Vapor pressure at 20 °C | 4900 mbar |
Enthalpy of vaporization | 21.67 kJ/mol |
Enthalpy of fusion at melting point | 6.4 kJ/mol |
Density of liquid (25°C) | 911 kg/m3 |
Density of vapor at boiling point | 2.558 kg/m3 |
Cubic expansion coefficient of liquid (0–40 °C) | 0.00209 K-1 |
Enthalpy of formation of vapor (25 °C, 1 bar) | -80.83 kJ/mol |
Gibbs free energy of formation of vapor (25 °C, 1 bar) | -57.37 kJ/mol |
Specific heat capacity of vapor (25°C, 1 bar) | 0.807 kJ kg-1 K-1 |
Critical temperature (Tc) | 143 °C |
Critical pressure | 65.9 atm |
Critical volume | 0.13645 mL/mol |
Thermal conductivity of vapor | 0.00841 W K-1 m-1 |
Thermal conductivity of liquid (20 °C) | 0.161 W K-1 m-1 |
Surface tension at 20°C | 16.2 mN/m |
Viscosity of liquid at 20 °C | 0.244 cP |
Dipole moment | 1.86 D |
Refractive index of liquid (25 °C) | 1.3712 |
Dielectric constant of vapor at 20°C | 1.01 |
Dielectric constant of liquid at 20 °C | 12.9 |
Ignition temperature | 618 °C |
Lower flammability limit in air | 7.1 vol% |
Upper flammability limit in air | 18.5 vol% |
Partition coefficient air/water (20 °C) | 0.3 |
Partition coefficient n-octanol/water (20 °C) (log Pow) | 0.91 |
2. Chemical Properties of Chloromethane
Chloromethane is a unique aliphatic chlorine compound that is thermally stable. Unlike many related compounds, it resists decomposition until exceeding 400 °C, even in the presence of most metals.
Its self-ignition temperature in air is a high 632 °C measured in a steel apparatus. While combustion primarily generates CO2 and HCl, traces of COCl2 and CO may also form. Photooxidation mainly yields carbon dioxide and phosgene.
Hydrolysis of chloromethane produces methanol and hydrogen chloride; however, under neutral or acidic conditions at room temperature, it is negligible. A strong alkali presence accelerates the process, reducing the half-life of chloromethane from decades to mere months.
Chloromethane readily participates in organometallic reactions with elements like lithium, magnesium, zinc, and aluminum, forming compounds like CH3MgCl and Al(CH3)3⋅AlCl3. These compounds have valuable applications in preparative organic chemistry and polymer production catalysis.
It has the ability to act as a methylating agent in numerous chemical reactions. It serves as a reageant in the Friedel-Crafts reaction with benzene for toluene synthesis and readily methylates hydroxyl groups to form ethers, including methylcellulose from cellulose and various phenol methyl ethers.
Monochloromethane also finds industrial use in producing quaternary methylammonium compounds by reaction with tertiary amines and various methylamines with ammonia.
The Grignard reagent methylmagnesium chloride is directly synthesized from chloromethane and magnesium, while the Wurtz reaction with sodium yields ethane.
A particularly significant reaction involves chloromethane and silicon, producing methylchlorosilanes (SiCl2(CH3)2) through the Müller-Rochow synthesis. These silanes, in turn, are important starting materials for silicone production by conversion to siloxanes intermediaires.
Finally, chloromethane can be converted to methyl mercaptan under pressure and elevated temperature using sodium hydrogen sulfide or transformed into tetramethyllead by reaction with a monosodium lead alloy.
3. Production of Chloromethane
Chloromethane is produced by two main methods: methanol hydrochlorination and substitution chlorination of methane.
In the methanol hydrochlorination process, methanol (CH3OH) reacts with hydrogen chloride (HCl) to produce monochloromethane (CH3Cl) and water (H2O).
CH3OH + HCl → CH3Cl + H2O
In the substitution chlorination, methane (CH4) reacts with chlorine (Cl2) to produce a mixture of chloromethanes and hydrogen chloride.
CH4 + Cl2 → CH3Cl + CH2Cl2 + CHCl3 + CCl4 + HCl
Many industrial plants combine both methods for optimized production. Substitution chlorination generates the chloromethane mixture and HCl. Methanol hydrochlorination consumes part of the HCl generated to produce more chloromethane and reduce overall HCl consumption.
3.1. Production of Chloromethane by Methanol Hydrochlorination
In the process of methanol hydrochlorination, the hydroxyl group (–OH) of methanol is substituted by a chlorine atom from hydrogen chloride (HCl). This exothermic reaction generates monochloromethane (CH3Cl) and water (H2O) with a heat release of 33 kJ/mol:
CH3OH + HCl → CH3Cl + H2O ⇔ ΔH = -33 kJ/mol
This reaction can be conducted in either the vapor or liquid phase. Both catalytic and noncatalytic methods exist in the liquid phase, while vapor-phase processes typically employ catalysts to enhance reaction rate. In most industrial settings, an excess of HCl relative to methanol is maintained in the reaction atmosphere to drive the conversion towards monochloromethane production.
3.1.1. Gas-Phase Hydrochlorination Process
The gas-phase hydrochlorination process uses a solid acid catalyst under controlled pressure (0.3–0.6 MPa) and temperature (280–350°C). This conversion of methanol to monochloromethane occurs through an Eley–Rideal mechanism, where chemisorbed methanol reacts with gas-phase HCl on the catalyst surface.
The high selectivity (0.2–1% dimethyl ether as byproduct) is attributed to the abundance of acidic sites promoting the desired reaction and suppressing competing dehydration to dimethyl ether.
Common catalysts include zinc chloride, copper chloride, and alumina, often supported on carriers like carbon or silica. γ-aluminum oxide is a common industrial choice. Studies have investigated the kinetics, aging, and regeneration of these catalysts.
The reaction exhibits first-order dependence on HCl but minimal dependence on methanol pressure. Notably, the rate constant correlates with surface area, and higher temperatures introduce limitations due to pore diffusion.
Fresh catalyst initially binds chlorine, forming acidic sites for methanol adsorption. Pore diffusion restricts chlorine uptake, leading to the presence of oxide and oxide hydrate sites.
Catalyst aging is mainly caused by carbon deposition from side reactions and pore blocking, while sintering reduces active surface area at high temperatures.
High-purity raw materials, including technically pure methanol and clean HCl, are crucial for minimizing side reactions and extending catalyst life. If HCl is sourced from an adjacent chlorination process, it requires rigorous purification to remove residual chloromethanes.
Typical gas-phase reactors employ numerous thin nickel tubes packed with catalyst. Efficient heat transfer is essential due to the exothermic nature of the reaction.
A simplified flow diagram (Figure 1) illustrates the process:
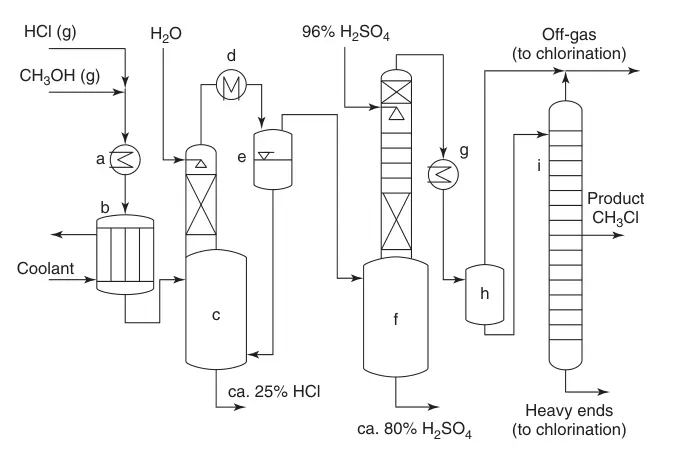
(a) Heat exchangers; (b) Multiple-tube reactor; (c) Cooling of the product stream with water and absorption of excess HCl; (d) Condensation; (e) Quench system; (f) Removal of water; (g) CH3Cl condensation; (h) Intermediate task; and (i) Monochloromethane purification
- Mixing and Heating: HCl and methanol are mixed, heated, and fed to the reactor.
- Conversion and Quenching: The catalyst bed drives the conversion, with excess HCl promoting desired product formation and suppressing dimethyl ether. The reaction gas is quenched with water, absorbing excess HCl.
- HCl Absorption and Cooling: The product stream passes through a cooler, condensing water and absorbing further HCl. The recovered HCl is recycled, while the water-HCl mixture undergoes downstream purification for methanol recovery.
- Dimethyl Ether Removal: The product stream enters a sulfuric acid column to remove dimethyl ether and residual water. The spent acid can be utilized in fertilizer production or sulfuric acid cleavage.
- Chloromethane Condensation and Distillation: Dry, crude chloromethane is condensed and further purified through a high-pressure distillation column. The gaseous overhead and distillation residue can be recycled.
This process achieves a high methanol-based yield of approximately 99%.
3.1.2. Liquid-Phase Hydrochlorination Process
Methanol hydrochlorination to chloromethane can occur in the liquid phase, either catalytically or noncatalytically. Both methods involve a bimolecular nucleophilic substitution mechanism:
- Protonation: The initial step involves protonation of the alcohol by HCl, generating a positively charged intermediate. (ROH + HCl → ROH2+ + Cl–)
- Nucleophilic Attack: In the second step, a chloride ion attacks the protonated alcohol, leading to bond cleavage and the formation of the desired product. (ROH2+ + Cl–) → [𝛿−Cl · · · R · · · 𝛿+OH2] → RCl + H2O
1. Catalytic Process
The typical catalytic method employs a stirred reactor filled with an aqueous metal chloride solution, often ZnCl2 (70–80 wt%), and then methanol and HCl gas or hydrochloric acid are fed into the reactor.
2. Noncatalytic Process
The noncatalytic process, developed by Shin-Estu and Dow, operates at lower temperatures and pressures compared to the catalytic method, thus minimizing dimethyl ether formation as a by-product. While gas-phase noncatalytic variants exist, the liquid-phase process dominates industrial applications.
Dow’s noncatalytic process utilizes a boiling bed reactor maintained under superatmospheric pressure (7–21 bar) to keep the reaction medium liquid at the desired temperature (≥ 50 °C, preferably 100–180 °C). Methanol and at least a 10% molar excess of HCl are fed into the reactor. The vaporous products then enter a rectifying tower, where:
- First, water vapor is bound to the reflux product, which is rich in HCl, effectively drying the product.
- Then, excess HCl reacts with any dimethyl ether generated in the reactor, minimizing this unwanted by-product.
3.2. Chloromethane as a Byproduct
Chloromethane is generated as a coproduct in silicone production by copper-catalyzed methanol hydrochlorination of SiCl2(CH3)2. It is recovered from Si(OH)2(CH3)2 and then reintroduced into the process of silane formation known as Müller-Rochow synthesis.
4. Uses of Chloromethane
Chloromethane is known for its use as a raw material for further chlorination to dichloromethane and trichloromethane. However, its primary industrial use is in the production of silicones, including fluids, elastomers, and resins.
These materials find widespread use in various sectors, from antifoaming agents in industrial processes to consumer products like coatings, sealants, and even personal care.
Chloromethane is used in the synthesis of cellulose ethers. These modified cellulose derivatives, such as methyl cellulose, hydroxypropyl methylcellulose (HPMC), and hydroxyethyl methylcellulose (HEMC), serve as thickening, emulsifying, and gelling agents in a multitude of applications. From construction materials and cosmetics to food and pharmaceuticals, they enhance product functionality and stability.
Monochloromethane’s methylating properties make it an essential reagent in the production of cationic polymers. These polymers are widely utilized in water treatment for various purposes, including flocculation, coagulation, and sludge dewatering.
It also contributes to the synthesis of quaternary ammonium compounds (quats), which are used as fabric softeners and organo-modified clays for oil and gas drilling, in plant protection products, and in cationic polymers used in water treatment.
While its use in refrigeration has been canceled in developed nations due to safety concerns, chloromethane remains essential in specific industrial processes. It serves as a cryogenic solvent in butyl rubber production and in laboratory settings.
It is important to note that reintroducing chloromethane into aluminum-based cooling units poses a significant safety risk. The slow Grignard-like reaction with aluminum can lead to explosions with potentially fatal consequences.
Similarly, the use of monochloromethane for the production of fuel anti-knock additives like tetraethyllead and tetramethyllead has been largely discontinued due to environmental and health concerns.
However, monochloromethane remains relevant in the production of organometallic compounds such as methyllithium, methylmagnesium chloride, trimethylaluminum, and methyl tin compounds.
These compounds are essential intermediates in fine chemical synthesis and potent catalysts in various polymerization reactions. Additionally, trimethylaluminum finds application in chemical vapor deposition, enabling the creation of thin films of highly resistant and dielectric aluminum oxide on various substrates.
5. Toxicology of Chloromethane
Chloromethane is an odorless gas, which means that the primary route of exposure is inhalation, posing unique safety concerns. Its impact on the central nervous system (CNS) is well-documented, with both animal studies and human exposure cases indicating potential for injury and even death.
Overexposure to chloromethane manifests symptoms similar to those of alcohol intoxication, including gait disturbance, incoherence, disorientation, and personality changes. These effects can be prolonged compared to alcohol, even permanent in severe cases. Interestingly, human volunteers exposed to 10 ppm for 2 hours experienced no irritation or CNS effects.
Reproductive and Developmental Toxicity: Excessive exposure in male rats affects the testes, while developmental toxicity and potential cardiac effects observed in animals are considered less relevant to humans due to higher exposure levels.
Chloromethane shows weak mutagenic properties in vitro; however, in vivo evidence for genotoxicity appears only at high, already toxic concentrations.
Two-year carcinogenicity studies in rodents revealed renal tumors only in male mice at the highest exposure level (1000 ppm); this is likely linked to repeated organ injury. The International Agency for Research on Cancer (IARC) classifies it as “not classifiable as to its carcinogenicity to humans (Group 3)”.
Exposure Limits and Safety: Repeated dose studies in animals suggest a No Observed Adverse Effect Concentration (NOAEC) exceeding 150 ppm. Occupational exposure limits (OELs) vary globally, typically ranging between 20 and 100 ppm.
Reference
- Chloromethanes; Ullmann’s Encyclopedia of Industrial Chemistry. – https://onlinelibrary.wiley.com/doi/10.1002/14356007.a06_233.pub4