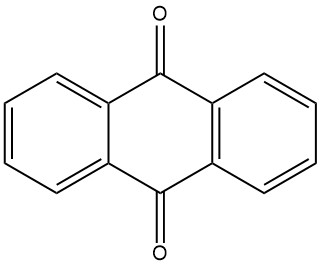
What is Anthraquinone?
Anthraquinone is an organic compound with the formula C14H8O2. It is a yellow, crystalline solid that is nearly insoluble in water and organic solvents at room temperature. Its solubility increases with temperature.
Anthraquinone is used as a precursor in the production of a wide range of dyes, as well as a catalyst in wood pulping.
It was first synthesized in 1835, but its pivotal role in the dye industry was not realized until 1868. Since then, anthraquinone chemistry has expanded rapidly, leading to the development of novel mordant dyes, acid dyes, vat dyes, disperse dyes, and reactive dyes.
In recent decades, the anthraquinone industry has undergone a global transformation. New synthesis procedures have been developed to meet the growing demand for anthraquinone, and processing methods have evolved to become more efficient and environmentally friendly.
One of the most groundbreaking applications of anthraquinone is its use as a catalyst in alkaline wood pulping. This branch of anthraquinone chemistry is rapidly developing and has the potential to surpass the demands of the dye industry.
The demand for anthraquinone has steadily increased since 1870, and the current annual demand exceeds 30,000 metric tons.
Table of Contents
1. Physical Properties of Anthraquinone
Physical properties of anthraquinone are listed in the following table:
Property | Value |
---|---|
CAS number | 84-65-1 |
Chemical formula | C14H8O2 |
Molar mass | 208.20 g/mol |
Appearance | Crystalline anthraquinone is delicate, light yellow to pale yellow needles. When finely divided or precipitated from sulfuric acid, it appears almost colorless. |
Melting point | 287 °C |
Boiling point | 377 °C |
Crystal class | Monoclinic |
Space group | P 21/a |
Unit cell dimensions |
|
Crystal density |
|
Vapor pressure |
|
Molar heat capacity at constant pressure (cp) | 265 J mol-1 K-1 |
Enthalpy of formation | -179 kJ/mol |
Enthalpy of combustion | 6449 kJ/mol at 25 °C |
Melting enthalpy | 32.57 kJ/mol at 287 °C |
Flash point | 185 °C |
Solubility |
|
Other |
|
2. Chemical Reactions of Anthraquinone
2.1. Oxidation
Anthraquinone is stable to oxidation under normal conditions, but can be oxidized to alizarin in harsh conditions with sodium hydroxide and sodium chlorate.
Anthraquinone can be oxidized to polyhydroxyanthraquinones with concentrated sulfuric acid and boric acid, persulfates, or metaarsenic acid at temperatures above 200 °C.
Oleum can also be used to oxidize anthraquinone to polyhydroxyanthraquinones at lower temperatures, depending on its SO3 content.
Concentrated nitric acid does not oxidize anthraquinone, but instead nitrates it. Some mixtures of anthraquinone and nitric acid can be explosive.
2.2. Reduction
Anthraquinone can be reduced to anthrahydroquinone with common reducing agents or hydrogen in the presence of a catalyst.
Sodium hyposulfite in an alkaline solution reduces anthraquinone to a blood-red sodium salt of anthrahydroquinone, which can rearrange to its tautomer oxanthrone in an acidic solution.
More vigorous reduction methods, such as tin-hydrochloric acid or catalytic hydrogenation under high pressure or temperature, yield anthrone, which exists in equilibrium with its tautomer anthrol (9-hydroxyanthracene) and subsequently transforms into anthracene and hydroanthracene.
When zinc or sodium hydroxide is used, dianthranol is produced via dimerization.
Under certain reaction conditions, the reduction process can be directed specifically to the two outer nuclei, leading to the formation of 1,2,3,4-tetrahydroanthraquinone or octahydroanthraquinone.
2.3. Condensation
Anthraquinone can be condensed with glycerol, iron powder, and sulfuric acid to produce benzanthrone.
2.4. Chlorination
Anthraquinone can be chlorinated in oleum, primarily at the alpha position.
Heating anthraquinone with antimony pentachloride or similar chlorine-releasing reagents yields chlorinated products ranging from monochloroanthraquinone to perchloroanthraquinone.
2.5. Sulfonation and hydroxylation
Sulfuric acid or oleum can sulfonate and/or hydroxylate anthraquinone. Concentrated sulfuric acid primarily sulfonates anthraquinone above 200 °C.
Oleum is typically used to sulfonate anthraquinone at temperatures between 140 °C and 160 °C, yielding major reaction products including β-sulfonic acids like anthraquinone-2-sulfonic acid, anthraquinone-2,6-disulfonic acid, and anthraquinone-2,7-disulfonic acid.
In the presence of mercury, sulfonation predominantly occurs at the alpha position, producing anthraquinone-1-sulfonic acid, anthraquinone-1,5-disulfonic acid, and anthraquinone-1,8-disulfonic acid.
2.6. Nitration
Nitrating anthraquinone requires rigorous conditions, resulting primarily in alpha-nitroanthraquinones alongside varying proportions of beta-nitro- and alpha,beta-dinitroanthraquinones.
Both mono- and dinitration processes occur, often yielding impure nitration products that require extensive processing for separation into 1-nitroanthraquinone, 1,5-dinitroanthraquinone, and 1,8-dinitroanthraquinone.
3. Industrial Production of Anthraquinone
Several processes are employed in the industrial production of anthraquinone. The most common method is the vapor-phase oxidation of anthracene using air. However, the naphthalene process and the synthesis from phthalic anhydride and benzene are also gaining prominence due to the scarcity of anthracene.
1. Oxidation of Anthracene
Anthraquinone is traditionally synthesized from anthracene, which is obtained from coal tar. This process involves the oxidation of anthracene with chromic acid in a solution of 48% sulfuric acid. The chromium(III) sulfate byproduct must be processed into tanning agents. This method requires high-purity anthracene with a minimum of 94% purity.
2. Vapor-Phase Oxidation of Anthracene
Approximately 85% of global anthraquinone production relies on the vapor-phase oxidation of anthracene using air. However, declining anthracene production has led to a supply shortage, promoting the naphthalene process. Naphthalene is readily available in coal tar and can also be extracted from residual oils obtained from gasoline reforming.
3. Naphthalene Process
This process is employed in Japan by Kawasaki and in Europe by Bayer. It involves a three-step synthesis of anthraquinone:
- Naphthoquinone is prepared by vapor-phase oxidation of naphthalene with air.
- Butadiene is introduced in a Diels-Alder reaction with the naphthoquinone.
- The resulting tetrahydroanthraquinone is subjected to oxydehydrogenation.
This process generates phthalic anhydride as a byproduct.
4. Synthesis from Phthalic Anhydride and Benzene
In regions where anthracene is insufficiently available from coal tar, anthraquinone can be synthesized from phthalic anhydride and benzene. This process involves the use of approximately 1.4 metric tons of aluminum chloride and 4-6 metric tons of sulfuric acid per ton of anthraquinone.
It has gained renewed importance due to the scarcity of anthracene. The availability of low-cost phthalic anhydride in sufficient quantities, achieved through the economical oxidation of naphthalene or o-xylene with air, has contributed to the resurgence of this synthesis route.
5. Styrene Dimerization Process
In the early 1970s, BASF introduced another intriguing anthraquinone production process. This method begins with the dimerization of styrene into 1-methyl-3-phenylindane, facilitated by an acid catalyst. Subsequently, 1-methyl-3-phenylindane is converted into anthraquinone in the vapor phase by oxidation with air.
3.1. Production of Anthraquinone by Oxidation of Anthracene with Chromic Acid
The industrial production of anthraquinone by chromic acid oxidation is a well-established and efficient process. It is relatively inexpensive and can be conducted in batch operations.

The process begins with the preparation of an anthracene paste by finely pulverizing pure anthracene (94-95% purity) and mixing it with water and a wetting agent in a mixing vessel. The anthracene paste is then oxidized by alternately adding portions of 48% sulfuric acid and 20% sodium dichromate solution. The reaction is controlled to avoid excessive foaming and temperature rise.
After the oxidation is complete, the reaction mixture is filtered and the filtered material is washed and suspended in water. The crude anthraquinone product is then filtered and has a purity of about 95%. The crude anthraquinone can be further processed by drying or recrystallization to achieve a purity level of up to 99%.
This process is often combined with the production of tanning agents, as it involves minimal expenses for the oxidizing agent.
3.2. Production of Anthraquinone by Vapor-Phase Oxidation of Anthracene with Air
The vapor-phase oxidation of anthracene with air is an efficient and well-controlled method for the production of high-purity anthraquinone.
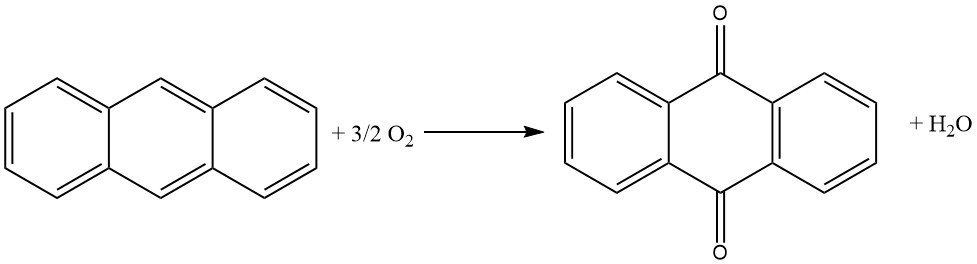
It is based on the use of catalysts similar to those used in the oxidation of naphthalene or o-xylene to phthalic anhydride. The process is characterized by high conversion of anthracene, minimal byproduct formation, and high product purity.
The process begins with the evaporation of anthracene using a preheated air-water vapor mixture. The gas stream is then carefully mixed with additional air to avoid the risk of explosion. This mixture is then directed into a catalytic furnace from the bottom, where the temperature is controlled.
The catalytic furnace consists of 1400 liters of catalyst material arranged in layers. The lower part, where the reaction takes place, is cooled to 390 °C, while the upper part is heated to 339 °C. The catalyst is typically iron vanadate, prepared from ammonium vanadate and iron(III) chloride.
The gases leaving the catalytic furnace are subjected to various cooling and filtering stages to separate the anthraquinone product from the byproduct gases.
The iron vanadate catalyst used in this process is prepared by dissolving red iron(III) oxide in hydrochloric acid and water. This solution is then mixed with ammonium vanadate in water and precipitated. The resulting solution is evaporated onto pumice in a heatable ball mill and subsequently calcined. The resulting catalyst should have a yellow-brown color.
Over time, the catalyst’s activity may decrease, leading to a decline in anthraquinone yield and an increase in phthalic anhydride production. To maintain or reactivate the catalyst’s activity, a small amount of ammonia can be added to the oxidation air, or the exhausted catalyst can be washed with a dilute alkali solution.
This process yields anthraquinone with a high purity of 99%.
3.3. Production of Anthraquinone by the Naphthalene Process
The naphthalene process, pioneered by Kawasaki Kasei Chemicals, is a three-step process for producing anthraquinone from naphthalene.
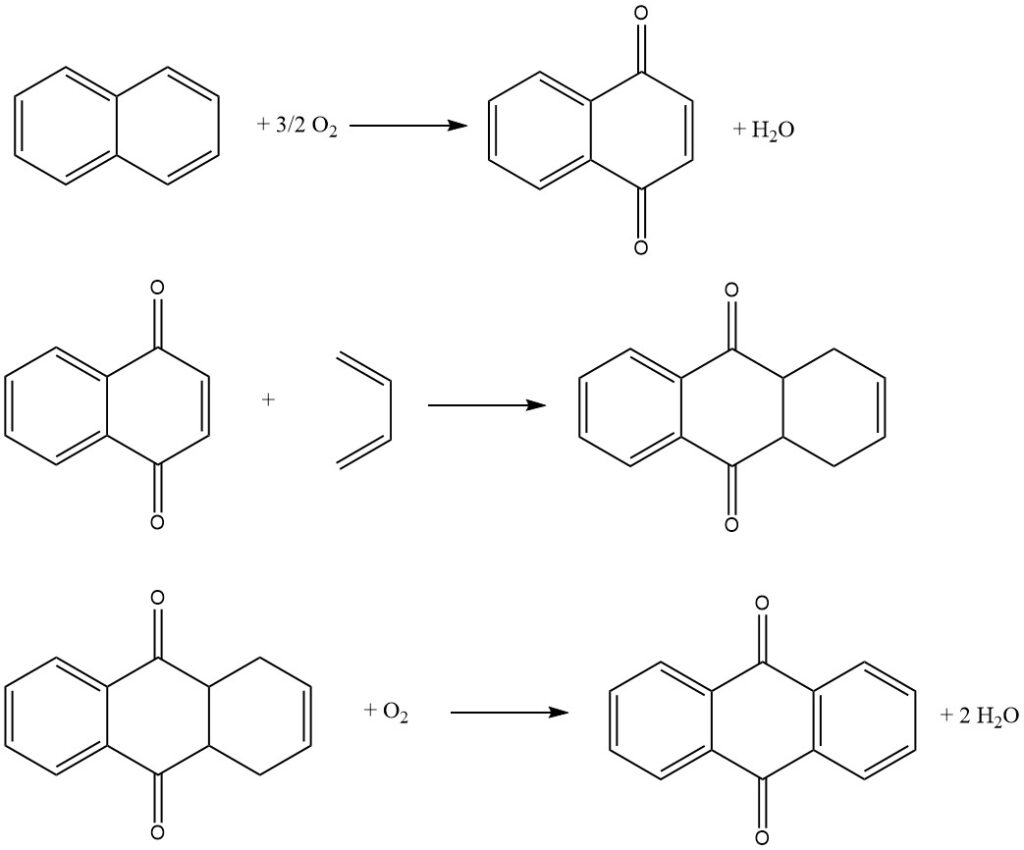
Step 1: Naphthalene Oxidation
In the first step, naphthalene is oxidized with air over a vanadium pentoxide catalyst to produce naphthoquinone and phthalic anhydride. The reaction is conducted in the gas phase at a high temperature.
Step 2: Diels-Alder Reaction with Butadiene
In the second step, naphthoquinone is reacted with butadiene in a Diels-Alder reaction to produce tetrahydroanthraquinone. The reaction is conducted in a liquid phase using an organic solvent such as xylene or tetrahydroanthraquinone.
Step 3: Oxydehydrogenation of Tetrahydroanthraquinone
In the third step, tetrahydroanthraquinone is oxidized with air to produce anthraquinone. The reaction is conducted in an aqueous phase using an alkali catalyst.
The phthalic anhydride produced in the first step can be recovered from the aqueous solution by crystallization and filtration.
Bayer’s Variant of the Naphthalene Process
Bayer’s variant of the naphthalene process differs from the Kawasaki Kasei process in the following ways:
- The naphthalene oxidation is conducted with a mixture of air and recycled reaction gas.
- The Diels-Alder reaction with butadiene is conducted without purifying the naphthalene oxidation products.
- The tetrahydroanthraquinone is oxydehydrogenated to anthraquinone in the presence of naphthalene.
- The anthraquinone and phthalic anhydride are separated by fractional distillation.
3.4. Synthesis from Phthalic Anhydride and Benzene
The synthesis of anthraquinone from phthalic anhydride and benzene is a two-step process:
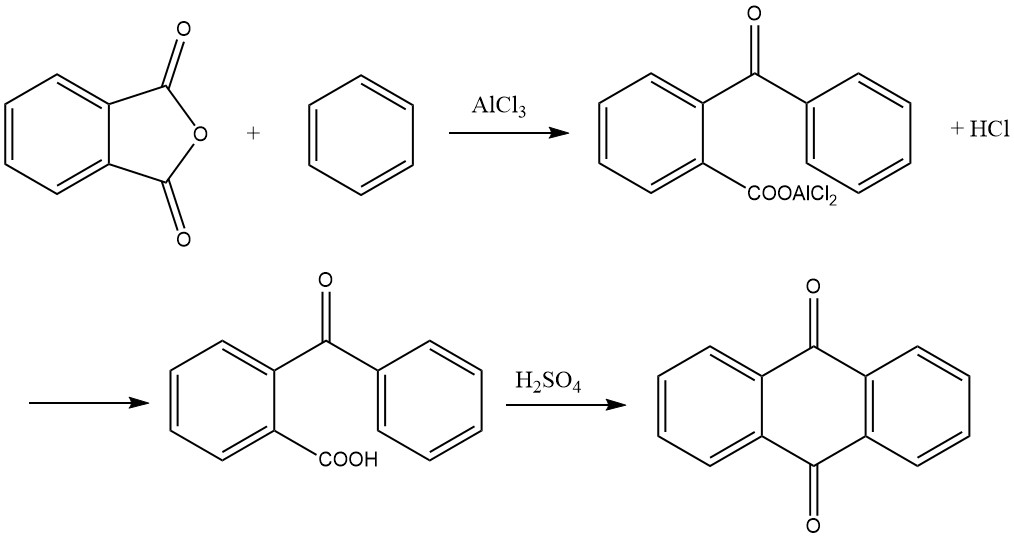
1. Formation of o-Benzoylbenzoic Acid
In the first step, o-benzoylbenzoic acid is formed through a Friedel-Crafts acylation using phthalic anhydride and benzene as starting materials. This reaction yields an aluminum chloride complex of o-benzoylbenzoic acid as a primary product, which can solidify within the reaction vessel.
To address this issue, various methods have been proposed, including:
- Conducting the reaction with excess benzene to achieve yields exceeding 95%.
- Performing the reaction in a solvent-free process in ball mills, using ethylene glycol or 1,4-butanediol to mitigate the solidification problem and reduce the required excess of benzene.
The reaction typically proceeds with a molar ratio of 1:1:2 for phthalic anhydride, benzene, and aluminum chloride. It takes place at temperatures below 45 °C and generates hydrogen chloride as a byproduct. Extensive foaming occurs during the reaction, increasing the volume several times, which must be accounted for when measuring the initial charge.
Completion of the reaction is indicated when 1 mole of hydrogen chloride per mole of phthalic anhydride has evolved. The resulting reaction product is then placed in a dilute acid solution, precipitating o-benzoylbenzoic acid. This precipitate is separated, washed, and dried, yielding more than 95% of the desired product.
2. Cyclization to Anthraquinone
In the second step, o-benzoylbenzoic acid can be further converted to anthraquinone. While it is possible to start with the aluminum chloride complex formed in the first step and cleave 1 mole of hydrogen chloride by heating to 200 °C to yield anthraquinone, the preferred method in practice is to condense the dried o-benzoylbenzoic acid with sulfuric acid.
The acid is dissolved in approximately three to four times its weight in 95–98% sulfuric acid and heated to a temperature ranging from 115 to 140 °C. The duration of heating depends on factors such as the quantity and concentration of the sulfuric acid and the temperature.
Once the reaction is complete, anthraquinone precipitates upon addition of water, and it can be subsequently filtered and dried. Alternatively, a portion of the product can be obtained in coarsely crystallized form by directly cooling the sulfuric acid solution. The yield in this step is nearly quantitative.
The condensation solution can also be directly utilized for the production of benzanthrone or anthraquinonesulfonic acids.
3.5. Production of Anthraquinone by Styrene Process
The styrene process, developed by BASF, is a multi-step process for producing anthraquinone from styrene. It is an efficient and versatile method that yields high-purity anthraquinone.
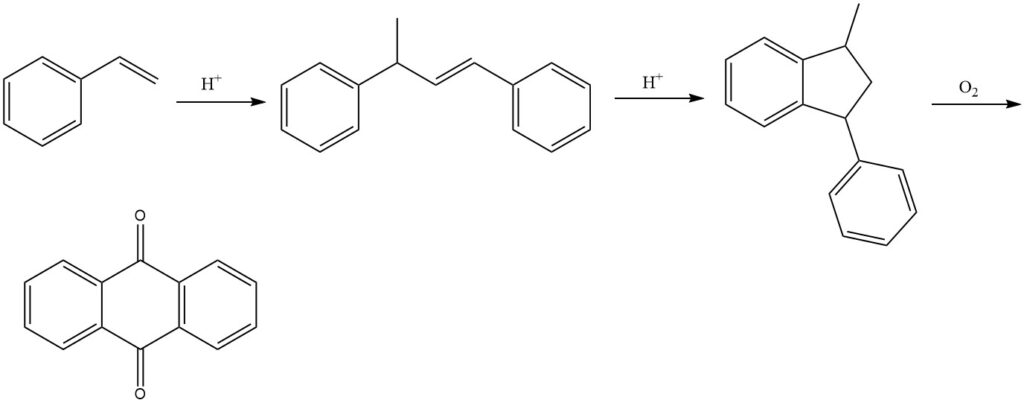
The process begins with the dimerization of styrene in the presence of acid catalysts to produce 1,3-diphenyl-2-butene. This is followed by the cyclization of 1,3-diphenyl-2-butene to form 1-methyl-3-phenylindane. Finally, 1-methyl-3-phenylindane is oxidized with air in the vapor phase to produce anthraquinone.
Various catalysts can be used in the oxidation step, such as vanadium compounds (primarily vanadium pentoxide), often in combination with other oxides such as thallium oxide and antimony oxide.
The styrene process results in yields of approximately 77% for the final product. However, the precipitated reaction product may still contain byproducts, necessitating further purification for the final isolation of pure anthraquinone.
4. Uses of Anthraquinone
Anthraquinone is a versatile and important chemical used in the production of a wide range of products, including dyes, plastics, pharmaceuticals, and paper.
Dye Production
Anthraquinone is used to produce a wide range of dyes, including acid dyes, base dyes, vat dyes, disperse dyes, and reactive dyes. These dyes are used in a variety of industries, including textiles, plastics, and printing.
Plastics Production
Anthraquinone is also used in the production of plastics, such as polyethylene terephthalate (PET) and polybutylene terephthalate (PBT). These plastics are used in a variety of products, including food packaging, beverage bottles, and electrical components.
Pharmaceutical Production
Anthraquinone is also used in the production of pharmaceuticals, such as laxatives and anti-inflammatory drugs.
Paper Production
Anthraquinone is used in the paper industry as a redox catalyst to facilitate the alkaline hydrolysis of polymeric lignin. This leads to increased pulp yield and reduced cooking time.
Other Applications
Anthraquinone is also used in a variety of other applications, such as the production of denaturants for seed protection, the modification of stand oils, and the improvement of colophony.
Recent Trends
In recent years, there has been a shift in the production of anthraquinone dyes from sulfonic acids to nitro compounds due to environmental concerns. The sulfonic acid process generates large amounts of wastewater, while the nitro compound process is more efficient and produces less waste.
5. Anthraquinone Toxicology
Anthraquinone is a relatively non-toxic chemical. It is considered biologically inert, meaning it is inactive in biological systems. This is likely due to its low solubility in both water and lipids.
There is a lack of toxicological data available for anthraquinone, but studies have shown that it is less irritating to the eyes than benzoquinone and has a similar level of inertness as inert dust.
An MAK value of 10 mg/m³ has been recommended for anthraquinone in occupational settings. This means that anthraquinone dust is considered to have a low health risk.
Reference
- Anthraquinone; Ullmann’s Encyclopedia of Industrial Chemistry. – https://onlinelibrary.wiley.com/doi/10.1002/14356007.a02_347