Antioxidants are used in four primary categories of substrates: foods, fuels, lubricants, and polymers. Each category has its own specific antioxidant products, but some antioxidants can be used in multiple categories.
Cosmetics and pharmaceuticals are excluded from this article due to their specialized requirements. Coatings and adhesives are categorized under polymers.
Table of Contents
Distinct criteria must be met when using antioxidants in food or food packaging, especially when there is indirect contact with food. The FDA and EFSA regulate antioxidants in food.
Phenolic antioxidants are the most versatile and ubiquitous. They are naturally occurring in plants and animals and protect them from oxygen and radical degradation. Phenolic antioxidants are also widely used in synthetic organic materials.
Aromatic amines are primarily used in rubber materials, as they can cause discoloration. Aliphatic and cycloaliphatic amines are increasingly used as antioxidants in polymers. The other groups of antioxidants have more limited applications.
1. Use of Atioxidants for Stabilization of Food
Autoxidation in food can lead to degradation of quality, including changes in color, taste, and aroma, making the food inedible. A good example is the aging of butter, which produces the distinctive smell of butyric acid.
Food preservation using antioxidants is particularly challenging because food is a heterogeneous mixture of chemicals, including carbohydrates, fats, peptides, and vitamins, all of which are susceptible to oxidative aging.
Additionally, antioxidants added to food are ingested with it, so they must be rigorously tested and approved by national authorities. As a result, only a limited number of non-naturally occurring substances are used as food antioxidants.
In Europe, the European Food Safety Authority (EFSA) regulates the addition of additives to food, and maintains a list of permitted substances (the E-list, with codes starting with ‘E’). There are 316 permitted additives, of which 30 are specifically designated for use as food antioxidants.
Naturally occurring antioxidants are often preferred and widely used. The most important examples are ascorbic acid (1) (vitamin C; E300), which is very effective in aqueous systems, and tocopherol-based compounds, especially alpha-tocopherol (2) (vitamin E; E307), which are compatible with fats.
Other substances used as food antioxidants include gallic acid esters (such as n-propyl gallate (3); E310), phenol derivatives (such as butylated hydroxyanisole (4); E320), lecithin (E322), and citric acid (E330).
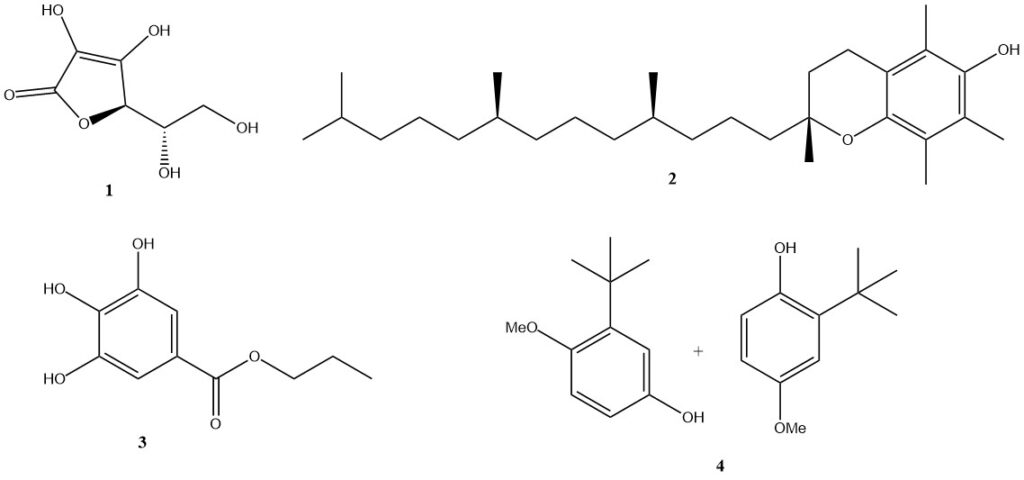
2. Use of Atioxidants for Stabilization of Fuels
Fuel stabilization is important because fuels are mostly hydrocarbons, which are a relatively homogeneous class of substances that are susceptible to oxidation during storage. This may change in the future with the increasing use of biofuels derived from natural sources, such as oils, fats, or ethanol.
For example, ethanol from sugarcane, vegetable oil, or its corresponding methyl ester is gaining importance, either in pure form or as blends with hydrocarbons.
The oxidation products of fuels can have two significant consequences. First, they can form deposits that can foul various components in contact with the fuel, such as carburetors or pumps. Additionally, acidic oxidation products can corrode metal parts in the fuel system.
Second, hydroperoxides generated by autoxidation are thermally unstable. Under combustion conditions, they can decompose uncontrollably, resulting in preignition, which can damage the entire engine.
Considering the typical storage conditions for fuels, which often involve dark environments, low temperatures, and limited durations, the concentration of antioxidants is typically kept low, typically around 10 parts per million (ppm).
Phenolic and amine-based antioxidants are commonly used for fuel stabilization. However, many companies develop proprietary stabilizer packages with tailored properties. Some of the phenolic antioxidants still in use are BHT (5), 2,4-dimethyl-6-tert-butylphenol (6) and 2,6-di-tert-butylphenol (7).
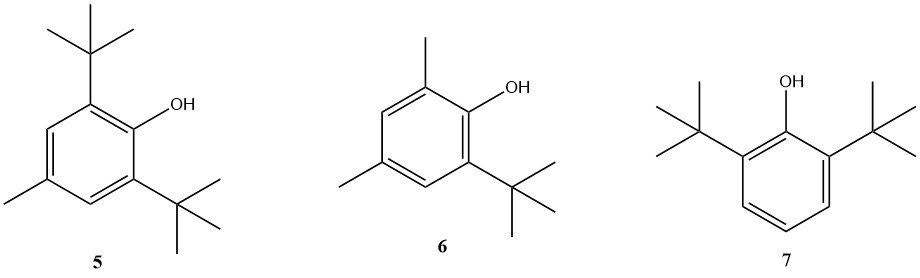
Among the amine-based antioxidants, N,N’-di-sec-butyl-p-phenylenediamine is significant, although other substituted p-phenylenediamines are also used.
3. Use of Atioxidants for Stabilization of Lubricants
Hydrocarbons are the main component of most lubricants, although other materials, such as synthetic esters, phosphoric acid esters, silicones, polyglycols, halogenated hydrocarbons, and other structural variants, are also used. Lubricants can be liquid, solid, or even gaseous, depending on the application.
Autoxidation is a significant challenge for hydrocarbon-based lubricants, as it deteriorates critical properties such as lubricating effectiveness and viscosity. Additionally, autoxidation can introduce adverse characteristics, such as increased corrosiveness due to the formation of acidic groups or the generation of sludge and deposits by oxidation byproducts.
Antioxidants play a vital role in maintaining the integrity of lubricants, often operating at elevated temperatures. Lubricants are primarily used to reduce friction between moving components, which can generate substantial heat.
Traditional antioxidants based on substituted phenols and amines are often sufficient for many applications. However, in cases where antioxidants must contend with highly oxidizing conditions, such as in engines or turbines, more potent solutions are required. This demand is met by the utilization of various compounds like zinc dialkyldithiocarbamates or zinc diaryldithiophosphates.
In addition to antioxidants, lubricants may also require supplementary additives, such as acid scavengers, viscosity regulators, or corrosion inhibitors. These additives are essential for stabilizing the lubricant over its extended service life. In particularly demanding applications, a relatively high dosage of antioxidants is warranted, typically falling within the range of 0.5 to 3%.
4. Use of Atioxidants for Stabilization of Polymers
The addition of antioxidants to polymers depends on several factors, including the type of polymer, environmental conditions, and the desired service life. In the case of thermoplastics, antioxidants are often necessary to protect the polymer during the shaping process, which occurs above its melting or glass transition point.
For demanding applications, such as high temperatures or extended service life (e.g., over 40 years for water pipes), up to 1% antioxidants may be needed.
The primary purpose of adding antioxidants to polymers is to protect them from oxidative processes, thus preventing changes in crucial properties for the intended application. These properties include mechanical characteristics, color, gloss, surface quality, and odor.
The efficacy and performance of antioxidants depend on various factors, including their compatibility and solubility within the polymer matrix, volatility, thermal stability, susceptibility to discoloration, and odor.
The selection of antioxidants must also consider additional parameters, such as:
- The form of the final product (e.g., thick injection-molded parts, thin films, or fibers)
- Other components in the composition, such as fillers and pigments
- Processing conditions
- Environmental conditions during the product’s use
These environmental factors may include chemical resistance, such as exposure to air pollution, or other media that could potentially degrade or leach out the additive, as observed in the case of water pipes.
Furthermore, obtaining the requisite approvals for specific applications, such as those involving food packaging, water pipes, or medical uses, is an important consideration in the antioxidant selection process.
4.1. Antioxidants in Elastomers
Elasticity is a key property of elastomers, which can be achieved through a variety of chemical structures. Elastomers can be divided into two subgroups: neat polymers (raw rubbers) and cross-linked (vulcanized) rubbers.
Many neat rubbers contain carbon-carbon unsaturation, making them susceptible to oxidation. This requires effective stabilization against oxidative processes. Examples of such rubbers include random styrene-butadiene-styrene copolymers (SBR), polybutadiene (PB), and acrylonitrile-butadiene copolymers (NBR).
Another class of elastomers is thermoplastic elastomers (TPEs), which are a wide range of block copolymers with soft segments (such as polyether), which provide elasticity, and hard segments (such as polyamides or polyesters).
Neat rubbers can be processed as thermoplastics and melted at elevated temperatures, unlike cross-linked rubbers. Cross-linking must be avoided to maintain the desired elastomeric properties.
The selection of antioxidants for elastomers is primarily determined by the final application, especially the desired color. Highly efficient but staining antioxidants based on aromatic amines are used for black elastomers, which are often achieved by incorporating carbon black.
These derivatives function as both antioxidants and antiozonants, protecting the elastomer from ozone damage. Prominent examples of such antioxidants include N-isopropyl-N’-phenyl-p-phenylenediamine (8) (IPPD), 4,4′-bis (α, α-dimethylbenzyl) diphenylamine (9), and phenyl naphthylamine (10). Efforts are underway to develop improved stabilizers.
Non-staining antioxidants are required for color-sensitive applications. Phosphites (11), phenols (BHT), or phenolic stabilizers with added sulfur functionalities, such as compounds 12 and 13, are preferred options in these cases.
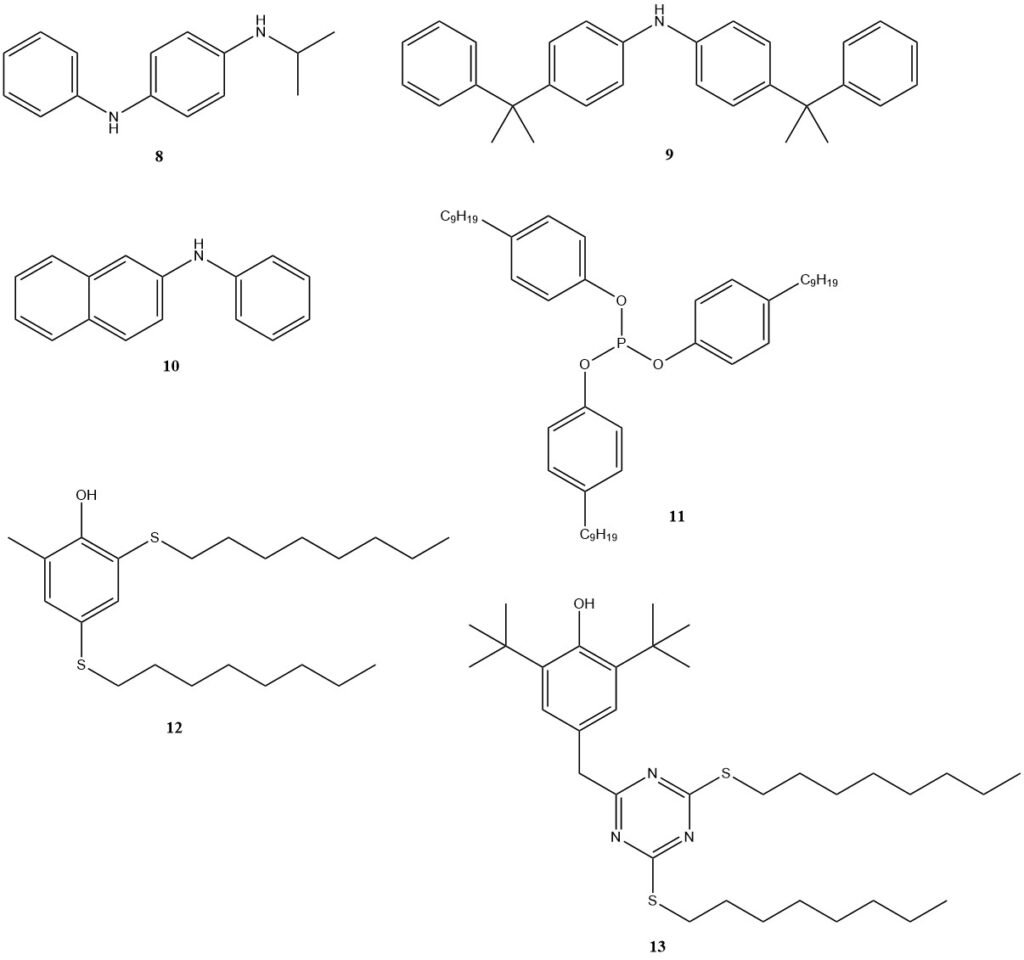
4.2. Antioxidants in Thermoplastics
Thermoplastics cover a wide range of chemical compositions, including bulk polymers (PE, PP, PVC), engineering plastics (PA, PET, PC), and high-end polymers (PEEK, PAI, PPS). Processing temperatures typically range from 180 to 330°C, but can be higher.
Long-term usage temperatures typically reach up to 100°C, but high-end thermoplastics can withstand 200°C or more. As a result, different antioxidants are needed for processing and long-term use, although phenols and phosphorus-containing compounds are still the most common. Antioxidants must prevent discoloration, loss of mechanical properties, and changes in gloss.
For high-temperature processing, phosphorus-based compounds (11, 14, 15) are still the main group, often used with phenolic antioxidants for synergistic effects. Benzofuranones were developed in the late 1990s, but are no longer commercially available.
Hydroxylamines (16) offer an interesting alternative, especially for polyolefins requiring phenol-free process stabilization. Typically, the dosage for process stabilizers is 0.05 to 0.1%.
For long-term stabilization, phenol-based products still dominate, with well-known options like 17 or 18. Various others have been developed for specific polymers, such as 19 for polyamide or 20, which has low migration tendencies and high stability against hydrolysis, making it suitable for water pipes or storage tanks.

Sulfur-containing cosstabilizers have been developed for long-lasting PP applications. While they have some antioxidative properties, they significantly improve PP’s service life when used with phenols.
Amine-based antioxidants, commonly associated with elastomers, are not typically used in thermoplastics due to color sensitivity. However, another group of amines, originally developed as light stabilizers for plastics, can serve as antioxidants: hindered amine stabilizers (HAS).
The need for antioxidants depends on the specific application and its demands. Short-term applications, like garbage bags made of LDPE or LLDPE, typically do not require antioxidants. For long-term stabilization, the typical dosage is 0.1 to 0.5%.
Some thermoplastics have a high intrinsic stability against oxidative degradation, making antioxidants unnecessary even for long-term use. Today, most thermoplastics can achieve service life times exceeding 30 years at room temperature.
Reference
- Antioxidants; Ullmann’s Encyclopedia of Industrial Chemistry. – https://onlinelibrary.wiley.com/doi/10.1002/14356007.a03_091.pub2