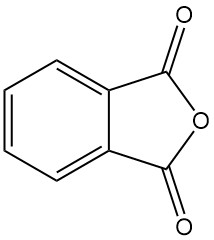
What is Phthalic Anhydride?
Phthalic anhydride [85-44-9], also known as isobenzofuran-1,3-dione, is an organic compound with the formula C6H4(CO)2O. It is a colorless to white, solid in the form of needles with a mild, distinctive odor that is formed by the dehydration of phthalic acid.
Phthalic anhydride was the first anhydride of a dicarboxylic acid to be used commercially. It is an important industrial chemical used for the large-scale production of plasticizers for plastics.
A. Laurent first discovered phthalic anhydride in 1836, and since 1872, it has been produced by BASF using the naphthalene oxidation process.
Table of Contents
1. Physical Properties of Phthalic Anhydride
Phthalic anhydride exists as colorless needles or platelets with monoclinic or rhombic crystalline forms. The physical properties of phthalic anhydride are listed in Table 1.
Property | Value |
---|---|
CAS number | [85-44-9] |
Chemical formula | C8H4O3 |
Molecular weight | 148.12 g/mol |
Density (solid at 4 °C) | 1.527 g/cm3 |
Specific Vapor Density (1013 mbar) | 6.61 kg/m3 |
Melting Point | 131.6 °C |
Boiling Point (1013 mbar) | 295.1 °C |
Heat of Fusion | 159.1 J/g |
Heat of Combustion | 22,160.7 J/g |
Heat of Formation (naphthalene) | 12,058 J/g |
Heat of Formation (o-xylene) | 8,625 J/g |
Heat of Sublimation | 601 J/g |
Heat of Evaporation | 441.7 J/g |
Flash Point | 152 °C |
Ignition Temperature | 580 °C |
Flammability Limits (1013 mbar) | Upper: 10.5 vol% Lower: 1.7 vol% |
Lower Dust Explosion Limit | 25 g/m3 |
The density of liquid phthalic anhydride between 140 and 240 °C can be determined using the following equation:
ρ/kg.m-3 = 1321.55-0.6697 (t/°C)-0.000905 (t/°C) 2
The solubility data of phthalic anhydride in various solvents is presented in Table 2.
Reported data on explosion hazards of phthalic anhydride in air show significant variations. Explosions can occur at concentrations below 100 g/m³, influenced by impurities present in the sample. Recent industrial incidents suggest that exceeding 35 g/m³ of phthalic anhydride in reaction product gas can lead to ignition upon contact with heat-transfer salt due to broken reactor tubes.
Solvent | Temperature (°C) | Solubility (g/100 g) |
---|---|---|
Water | 20 | 1.64 |
Water | 50 | 1.74 |
Water | 100 | 19.0 |
Carbon disulfide | 20 | 0.7 |
Formic acid | 20 | 4.7 |
Pyridine | 20 | 80 |
Benzene | - | soluble |
Ethanol | 20 | soluble |
Diethyl ether | 20 | slightly soluble |
2. Phthalic Anhydride Reactions
Phthalic anhydride shows the reactivity of cyclic anhydride and aromatic compounds.
The reaction of phthalic anhydride with alcohols or diols yields esters or polyesters. For example, phthalic anhydride reacts with ethylene glycol to form polyester, a polymer with repeating ester units.
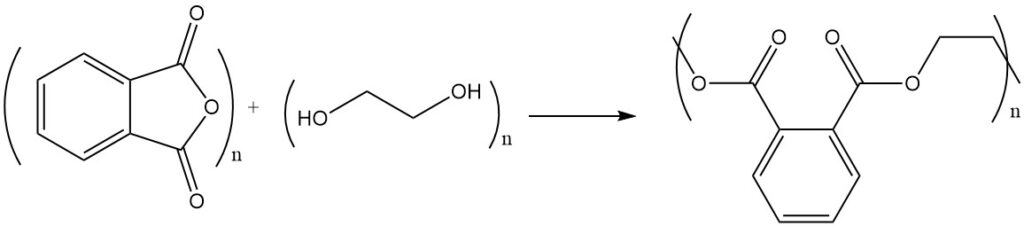
Unsaturated polyester resins are formed by polycondensation with maleic anhydride or fumaric acid.
One or both carboxy groups of phthalic anhydride can react with ammonia to produce phthalimide or phthalonitrile.
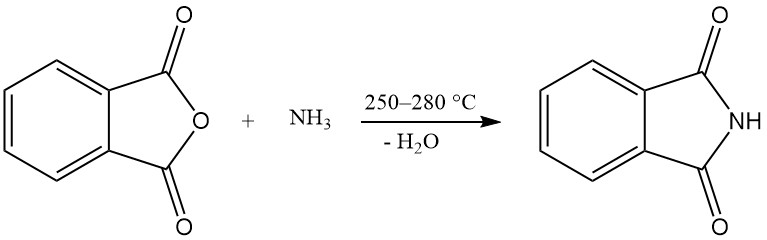
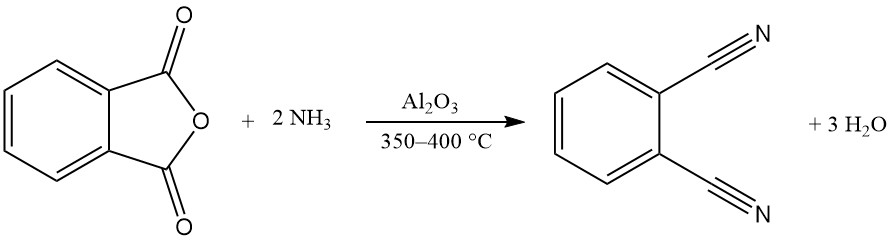
Phthalein and rhodamine dyes, some with over a century of production history, are obtained by the reaction of phthalic anhydride with phenols, aminophenols, or quinaldine derivatives. Fluorescein is synthesised from phthalic anhydride and resorcinol using acid catalysts.
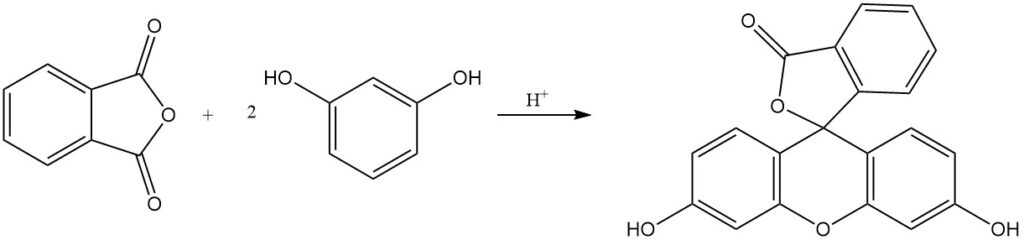
The reaction of phthalic anhydride with phenol produces phenolphthalein in the presence of an acid catalyst.
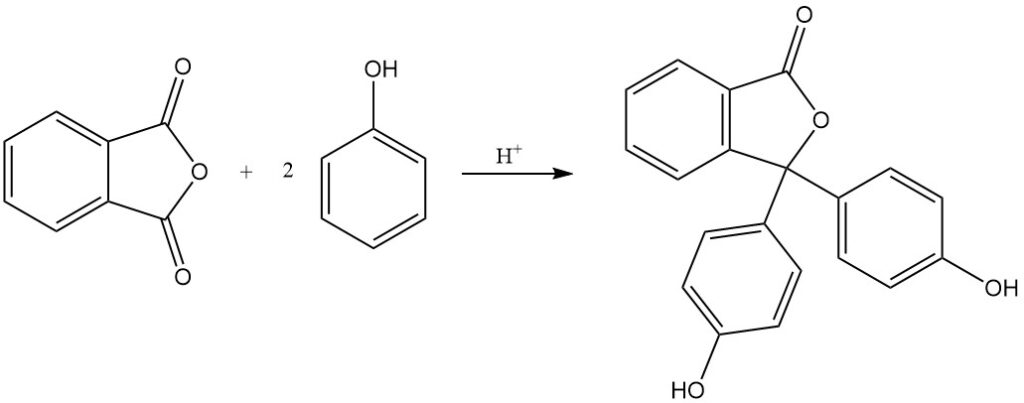
When phthalic anhydride is reacted with 4-aminophenol, it yields N-(4-hydroxyphenyl)phthalimide.
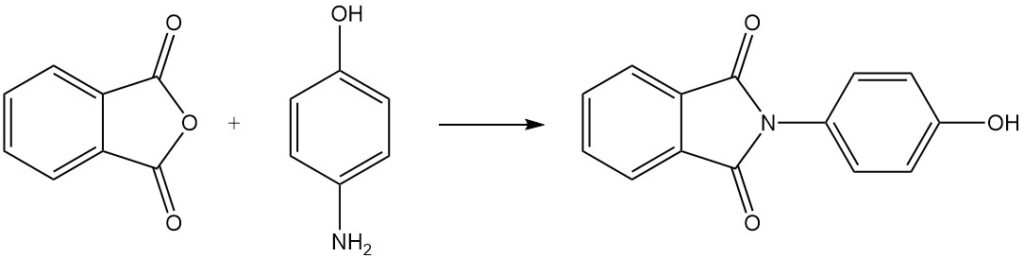
The Friedel-Crafts reaction of phthalic anhydride with benzene derivatives, followed by ring closure, forms anthraquinone derivatives, which are used to make anthraquinone dyes.
The industrial synthesis of anthranilic acid from phthalic anhydride involves two steps. First, phthalic anhydride reacts with ammonia in the presence of sodium hydroxide to form phthalimic acid salt, and then the sodium salt of phthalamic acid undergoes Hofmann rearrangement and decarboxylation when treated with hypochlorite to give anthranilic acid.
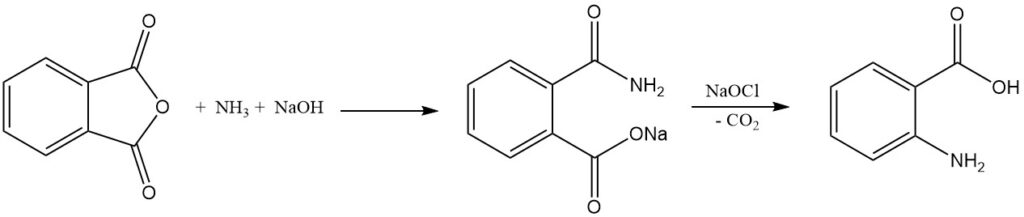
Terephthalic acid can be produced by rearrangement of dipotassium phthalate, but technical challenges have made this process obsolete.
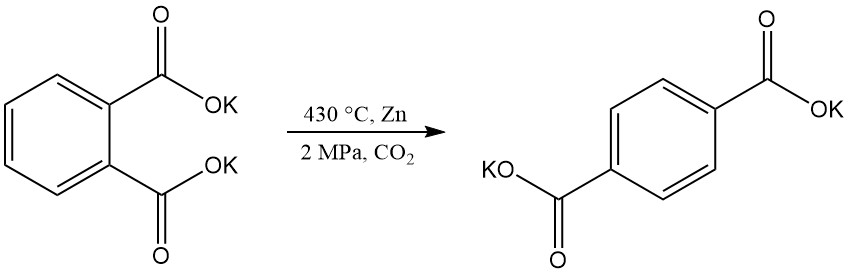
Electrochemical hydrogenation of phthalic anhydride yields 3,5-dihydrophthalic acid, while hydrogenation with a nickel catalyst produces phthalide.
3. Production of Phthalic Anhydride
Phthalic anhydride is predominantly produced on an industrial scale by the gas-phase oxidation of o-xylene or naphthalene. It can also be prepared by fluidized-bed oxidation of naphthalene or by liquid-phase oxidation of o-xylene.
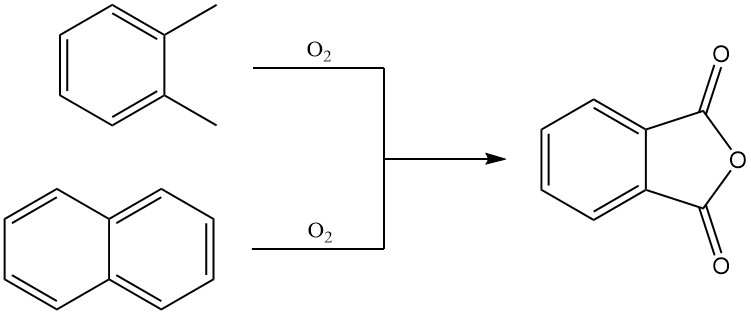
3.1. Production of Phthalic Anhydride by gas-phase Oxidation of o-Xylene or Naphthalene
Preheated o-xylene is mixed with hot air and fed into a tubular reactor containing a highly selective catalyst. The oxidation reaction is exothermic, and the generated heat is used to produce steam, with excess steam available for external use.
The reactor effluent gases are precooled. At high phthalic anhydride concentrations, some liquid phthalic anhydride can be directly collected in a condenser, and the remaining product gas stream enters a switch condenser system.
Finned tubes within the switch condensers are cooled by heat-transfer oil in a cyclic process. During the cooling cycle, phthalic anhydride condenses as a solid on the tubes, and a subsequent heating cycle melts the deposited phthalic anhydride, which is then collected in a storage tank.
After phthalic anhydride separation, exhaust gases containing byproducts require cleaning by water scrubbing, catalytic incineration, or thermal incineration.
Water scrubbing allows for the concentration of maleic acid (a byproduct) from the scrubbing solution, which can be further processed to yield fumaric acid or maleic anhydride.
The combination of scrubbing with maleic anhydride production eliminates the discharge of polluted wastewater.
The crude phthalic anhydride is transferred to a continuous thermal/chemical treatment system that converts any phthalic acid byproduct back into phthalic anhydride. Finally, the treated crude phthalic anhydride is purified by a continuous, two-stage distillation system.
3.1.1. Commercial Processes
The BASF process operates with a wide range of o-xylene loadings (up to 105 g/m³) and employs a finishing reactor for byproduct reduction and quality improvement.
This process offers flexible operation for optimized yield, reduced waste, and extended catalyst life and doesn’t require SO2 activation or a pre-condenser for crude phthalic anhydride collection.
The crude phthalic anhydride produced contains a low byproduct, which makes it optimized for low energy consumption and high net energy export.
The Wacker Process accommodates o-xylene, naphthalene, or their mixtures. It uses o-xylene loadings of 90–100 g/m³ (STP) and focuses on process modifications for energy savings.
The Nippon Shokubai VGR Process is distinguished by vent gas recycling, reducing oxygen concentration to <10 vol% for safe operation with high o-xylene loading (up to 85 g/m³ STP). This process achieves high yields attributed to a specialized catalyst system, and it can also use naphthalene as feedstock.
The Alusuisse-Ftalital LAR Process proposes o-xylene loadings up to 134 g/m³ (STP) for potential energy and equipment size reduction. It commercially uses loadings up to 80 g/m³ (STP) and employs ring- or half-ring shaped catalysts capable of processing both o-xylene and naphthalene or their mixtures.
The Rhône-Poulenc Process uses o-xylene as a feedstock and subjects the crude product to chemical post-treatment before the two-stage distillation. It treats waste gas through incineration.
The ELF Atochem/Nippon Shokubai Process leverages the Nippon Shokubai catalyst for processing o-xylene or naphthalene and uses industrial feed loadings of up to 75 g/m³ (STP) for o-xylene.
3.1.2. Catalyst and Reaction Mechanism
Modern plants predominantly use ring-shaped catalysts in tubular reactors cooled by molten salt for energy efficiency. Half-shell supports are also available.
Typical catalysts consist of an inert ceramic support (silicate, silicon carbide, etc.) coated with a thin layer of vanadium and titanium oxides. Antimony, rubidium, cesium, niobium, and phosphorus can be added to enhance the selectivity towards phthalic anhydride.
Two-zone catalysts that combine low and high activity zones are common, with some processes using three zones for high o-xylene loadings, and certain catalysts require SO2 activation for extended life.
The exact reaction pathway for phthalic anhydride formation is not fully understood and depends on measurement methods and experimental setups.
A redox mechanism involving oxygen atoms in the catalyst lattice is generally accepted. While the intermediate alcohol hasn’t been definitively observed, its presence is likely in the conversion of o-xylene to phthalic anhydride.
Industrial o-xylene conversion achieves yields exceeding 80% of the theoretical maximum (around 110–112 kg phthalic anhydride per 100 kg o-xylene). However, naphthalene conversion yields are typically lower (around 85% of the theoretical maximum, or 98 kg phthalic anhydride per 100 kg naphthalene), due to additional byproducts like naphthoquinone.
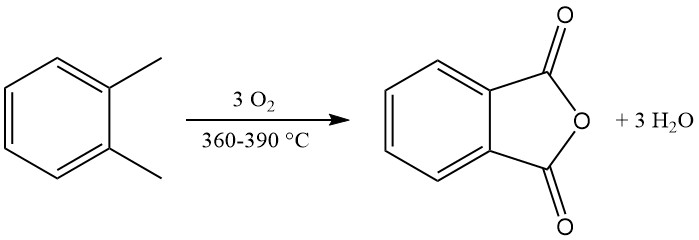
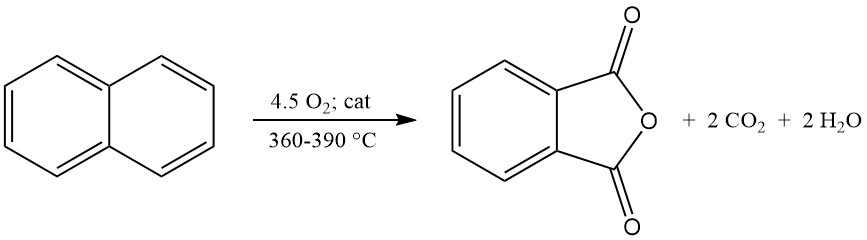
The exothermic oxidation reaction generates significant heat: 1300–1800 kJ/mol for o-xylene and 2100–2500 kJ/mol for naphthalene. This heat is often harnessed for steam production.
The main byproducts of o-xylene oxidation include maleic acid and phthalide, and the naphthalene oxidation additionally produces naphthoquinone, which requires more purification.
3.1.3. Purification of Phthalic Anhydride
To obtain high-purity phthalic anhydride after the initial reaction stage, the crude product often undergoes thermal treatment before distillation to remove impurities.
Simple heat treatment (100–400 °C) is suitable for low-impurity products made from o-xylene. Treatment aims to eliminate water, low-boiling contaminants (maleic anhydride, o-tolualdehyde), and phthalide.
Phthalic anhydride produced by the oxidation of naphthalene needs additional chemical treatment due to the presence of naphthoquinone as a byproduct.
Various chemicals can be used for naphthoquinone elimination, including sulfuric acid, sodium hydroxide, boric acid/sulfuric acid mix, potassium disulfide, sodium carbonate, potassium maleate, and aliphatic polydienes.
Distillation is used as the final purification stage for crude phthalic anhydride.
The distillation process (Figure 1) typically involves a continuous system with multiple columns.
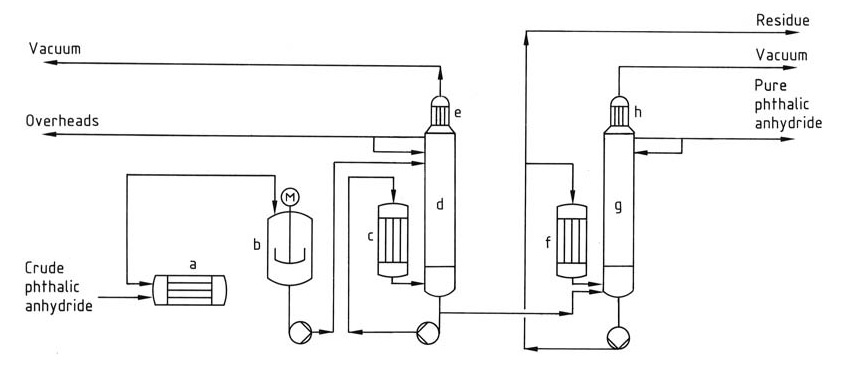
a) Crude phthalic anhydride heater; b) Predecomposer; c) Reboiler; d) Stripper column; e) Condenser; f) Reboiler; g) Distillation column; h) Condenser
First, the predecomposer converts residual phthalic acid in the crude product to phthalic anhydride, and then the first column concentrates and removes low-boiling impurities like maleic anhydride and benzoic acid from the head. Finally, the second column purifies phthalic anhydride by distilling it while leaving the high boiling residue behind.
3.2. Production of Phthalic Anhydride by Fluidized-Bed Oxidation of Naphthalene
Phthalic anhydride can be produced by fluidized-bed oxidation of naphthalene. One example is the Badger process, which is still in use, and plants employing this process can increase their production capacity by injecting both oxygen and air, allowing for a higher naphthalene concentration.
The liquid naphthalene is directly injected and vaporized at the bed bottom to ensure even distribution throughout the catalyst and the atmospheric oxygen is fed through a distributor plate to facilitate the reaction.
Vigorous mixing within the fluidized bed maintains uniform temperature (345–385 °C), and the heat generated by the reaction is used for high-pressure steam production via cooling tubes.
Cyclones and ceramic filters are used to separate and recycle the catalyst, which can be regenerated using SO2.
Up to 60% of phthalic anhydride is recovered as a liquid condensate, with the rest obtained by desublimation in switch condensers and finally distilled under vacuum to produce pure product.
3.3. Production of Phthalic Anhydride by Liquid-Phase Oxidation of o-Xylene
Phthalic anhydride can be produced by liquid-phase oxidation of o-xylene. In this process a mixture of acetic acid, o-xylene (>99% ortho isomer content required for high yield), and a cobalt, manganese, and bromine-based catalyst is fed to a cascade reactor system.
The reaction starts under pressure with air injection and progresses through subsequent vessels. Water generated as a byproduct is removed in the first vessel by azeotropic distillation with o-xylene.
Phthalic acid isomers are separated, and phthalic anhydride is obtained by crystallization. Due to the presence of bromine in the catalyst, the crude product requires special pre-treatment before final purification by distillation.
Sisas Process is a two-step process that involves liquid-phase oxidation of o-xylene to crude o-toluic acid and unreacted o-xylene is recycled. Then the separated o-toluic acid is oxidized in gas-phase to yield phthalic anhydride.
The overall molar yield of phthalic anhydride based on o-xylene can reach up to 88%.
The liquid-phase oxidation process is an alternative to traditional methods, but hasn’t achieved widespread industrial adoption compared to fixed-bed catalytic oxidation.
4. Uses of Phthalic Anhydride
The most important application of phthalic anhydride is the production of plasticizers. The main uses of phthalic anhydride are the production of plasticizers (55 %), unsaturated polyester resins (14 %), alkyd resins (15 %) and other chemical products such as dyes and pigments, detergents, herbicides and insecticides, fire retardants, saccharin and polyester resin cross-linking agents.
It is widely used worldwide for an extremely broad range of applications, spanning from the plastics industry to the synthesis of resins, agricultural fungicides and amines.
5. Toxicology of Phthalic Anhydride
Phthalic anhydride exhibits low acute toxicity but it can induce respiratory irritation and sensitization upon inhalation. Chronic exposure studies suggest no carcinogenic potential and limited data on reproductive toxicity requires further investigation.
Acute toxicity
Phthalic anhydride exhibits low acute toxicity based on LD50 values:
- Oral (rat): 1500–4000 mg/kg
- Inhalation (rat): >210 mg/m³ h (dust)
- Dermal (rabbit): >10000 mg/kg
Skin contact with phthalic anhydride may cause slight irritation, while eye contact is irritating. It can also induce dermal sensitization.
Subacute toxicity
Dietary exposure in rats (up to 3800 ppm) for 28 days showed no significant effects.
Gavage studies in rats revealed kidney and gastric mucosal toxicity at doses exceeding 1200 mg/kg/day.
Inhalation studies demonstrated respiratory irritation in various animals at high concentrations (10000 mg/m³).
Repeated inhalation exposure (8.5 mg/m³) caused respiratory tract irritation and frequent pneumonias in rats.
Genotoxicity
No mutagenic or chromosomal effects were observed in in vitro tests with and without metabolic activation.
Chronic toxicity and carcinogenicity
Long-term dietary studies in rats and mice at high doses (up to 3600 mg/kg/day) did not show increased tumor formation compared to controls.
Reproductive toxicity
Limited studies involving intraperitoneal injection in mice suggest potential malformation risks at high doses (≥55.5 mg/kg/day) during gestation. However, the route of exposure and animal strain limit the conclusiveness of these findings.
References
- Phthalic Acid and Derivatives, Ullmann’s Encyclopedia of Industrial Chemistry. – https://onlinelibrary.wiley.com/doi/10.1002/14356007.a20_181.pub2
- Phthalic anhydride (PA): a valuable substrate in organic transformations. – https://pubs.rsc.org/en/content/articlehtml/2023/ra/d3ra03378c
- Process for the production of phthalic anhydride. – https://patents.google.com/patent/US4435580A/en