
Nitrobenzene is an organic chemical compound with the molecular formula C6H5NO2. It is a pale yellow liquid with a distinctive odor similar to bitter almonds.
Table of Contents
1. Physical Properties of Nitrobenzene
Nitrobenzene is known as oil of mirbane. it have the chemical formula C6H5NO2 and a molar mass of 123.1 g/mol. This pale yellow liquid emits an aroma reminiscent of bitter almonds and exhibits high solubility in various organic solvents.
It shows complete miscibility with benzene in all proportions. Notably, nitrobenzene serves as an effective solvent for aluminum chloride, making it a valuable component in Friedel-Crafts acylation and alkylation.
The compound displays slight water solubility, being approximately 0.19% at 20 °C and 0.8% at 80 °C. Furthermore, it is readily volatile with steam.
Various other physical properties of nitrobenzene are as follows:
Property | Value |
---|---|
melting point | 5.85 °C |
boiling point at 101 kPa | 210.9 °C |
boiling point at 13 kPa | 139.9 °C |
boiling point at 4 kPa | 108.2 °C |
boiling point at 0.13 kPa | 53.1 °C |
density (solid) | 1.344 |
density (liquid) 25°C | 1.199 |
Viscosity (15 °C) | 2.17 × 102 mPa · s |
Surface tension (20 °C) | 43.35 mN/m |
Dielectric constant at 20 °C | 35.97 |
Dielectric constant at 170 °C | 18.15 |
Specific heat (30 °C) | 1.418 J/g |
Latent heat of fusion | 94.1 J/g |
Latent heat of vaporization | 331 J/g |
Flash point (closed cup) | 88 °C |
Autoignition temperature | 482 °C |
Explosive limit in air (93 °C) | 1.8 vol% |
Vapor density | 4.1 |
Refractive index (15 °C) | 1.55457 |
2. Chemical Reactions of Nitrobenzene
Nitrobenzene undergoes various chemical reactions due to the presence of the nitro group (-NO2) attached to the benzene ring. The nitro group is an electron-withdrawing group, which affects the reactivity of the benzene ring.
It withdraws electron density from the ring, deactivating it towards electrophilic aromatic substitution reactions (EAS). This means that the ring is less reactive towards the substitution of an electrophile in place of another electrophile, such as hydrogen.
Chemical reactions involving nitrobenzene encompass electrophilic meta substitution of the aromatic ring through processes like nitration, sulfonation, or halogenation.
Nitrobenzene can act as a mild oxidizing agent in the synthesis of compounds like quinoline and fuchsin.
Conversely, reduction of the nitro group leads to a diverse array of products, as presented in the following Table:
Reducing Agent | Product |
---|---|
Fe, Zn, or Sn/HCl, H2–catalyst | aniline |
Zn – H2O | N-phenylhydroxylamine (rearranges with acid to 4-aminophenol) |
Na3AsO3 | azoxybenzene |
Zn – NaOH | azobenzene, hydrazobenzene (rearranges with acid to benzidine ) |
LiAlH4 | azobenzene |
Na2S2O3– Na3PO4 | sodium phenylsulfamate (C6H5NHSO3Na) |
Electrolytic reduction | 4-aminophenol |
The primary products of reduction are nitrosobenzene, N-phenylhydroxylamine, and aniline, whereas other products arise from subsequent interactions and rearrangements.
It is essential to employ highly specific reduction conditions to obtain pure products, and intermediate stages, such as nitrosobenzene, are typically challenging to isolate.
3. Production of Nitrobenzene
The traditional batchwise nitration procedure involves adding mixed acid (nitric acid/sulfuric acid/water) (consisting of 27 – 32/56 – 60/8 – 17 wt %) to a slight excess of benzene (to prevent nitric acid presence in the spent acid). The reaction is controlled at a temperature of 50 – 55 °C and then completed by heating to 80 – 90 °C.
However, continuous processes have replaced this approach, operating under similar conditions. These continuous processes offer enhanced economy and safety due to improved mixing and higher reaction rates achievable in smaller reactors.
Remarkably, a 120-L continuous reactor can yield the same amount of nitrobenzene as a 6000-L batch reactor. The reactor configurations vary, but one typical example is a stirred cylindrical reactor operating at 50 – 100 °C.
The reuse of spent acid is important, achieved through continuous concentration and the addition of fresh acid. This contrasts with the batchwise reuse concept, but both approaches result in the same disadvantage of generating an equivalent amount of spent acid for disposal.
Many of today’s production facilities are package units based on years of design experience. For instance, Meissner units, with capacities up to 12 t of nitroaromatics per hour, come equipped with nitrogen blanketing for added safety.
Purging steps are applied to each output stream; thus, spent acid is extracted along with incoming benzene to remove residual nitrobenzene and nitric acid. Also, residual waste gases are scrubbed by a mixed acid loop to meet environmental regulations.
Another innovative development is the pump nitration circuit introduced by Nobel Chematur. This process allows nitration to take place in the pump itself, leading to reaction times of less than a second due to intense mixing and numerous associated advantages.
The concept of an adiabatic process that utilizes the heat of reaction for spent acid concentration has been in existence since 1941. The American Cyanamid adiabatic process, developed jointly with CLR, forms the foundation for one of the world’s largest nitrobenzene plants, rated at 159,000 t/a.
This process involves co-current streams of benzene (1.1 mol per mole of HNO3) and mixed acid (6 – 8/62 – 68/24 – 32 wt %) passing through a vigorously agitated tubular reactor, with entry at 60 – 80 °C (below the boiling point of benzene) and exit at around 120 °C, ensuring a residence time of approximately 4 minutes.
The requirement for much weaker sulfuric acid makes acid recycling much more cost-effective, especially because the process heat is almost sufficient for evaporation, particularly under vacuum.
Another option to avoid the need for separate sulfuric acid re-concentration is to carry out the nitration at higher temperatures (120 – 160 °C) with excess water distilled from the nitrator as an azeotrope with benzene.
In a duplex process, the benzene azeotrope resulting from the high-temperature first-stage partial reaction is utilized in a lower temperature second stage to complete the reaction. While azeotropic nitration offers significant energy savings, it is not considered as competitive as adiabatic nitration.
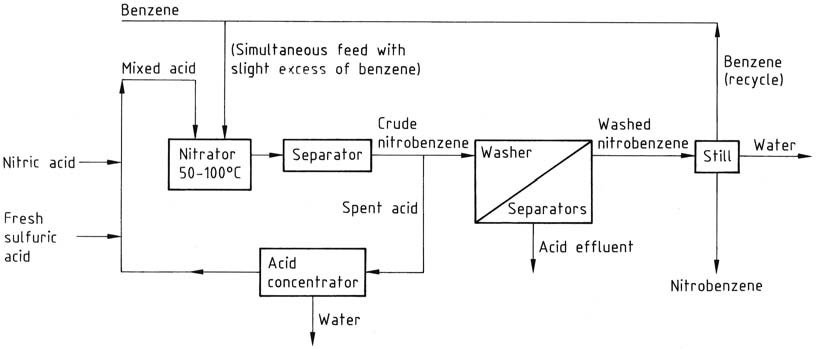
All these processes share similar work-up streams. The reaction mixture moves from the nitrator to a separator or centrifuge, and the aqueous spent acid is fed back to the recycle loop via a concentrator or strength adjustment stage, as appropriate.
The crude nitrobenzene, as the top layer, passes through a series of washer-separators where residual acid is washed away first with dilute alkali and then with water. The washed product is subjected to a still to remove water and benzene (recycled).
If needed, the product is finally vacuum distilled to obtain pure product with an overall yield of approximately 96%. The washing stages create an effluent issue, necessitating wastewater treatment, mainly to remove nitrobenzene.
In 1985, the global capacity for nitrobenzene production was approximately 1.7 millions t/a, with around one-third located in Western Europe and another third in the United States.
4. Uses of Nitrobenzene
The utilization of nitrobenzene as a solvent in specific chemical reactions holds a minor, yet significant, role. The majority (approximately 95% or more) of the produced nitrobenzene is converted to aniline, which serves as a precursor to numerous downstream products.
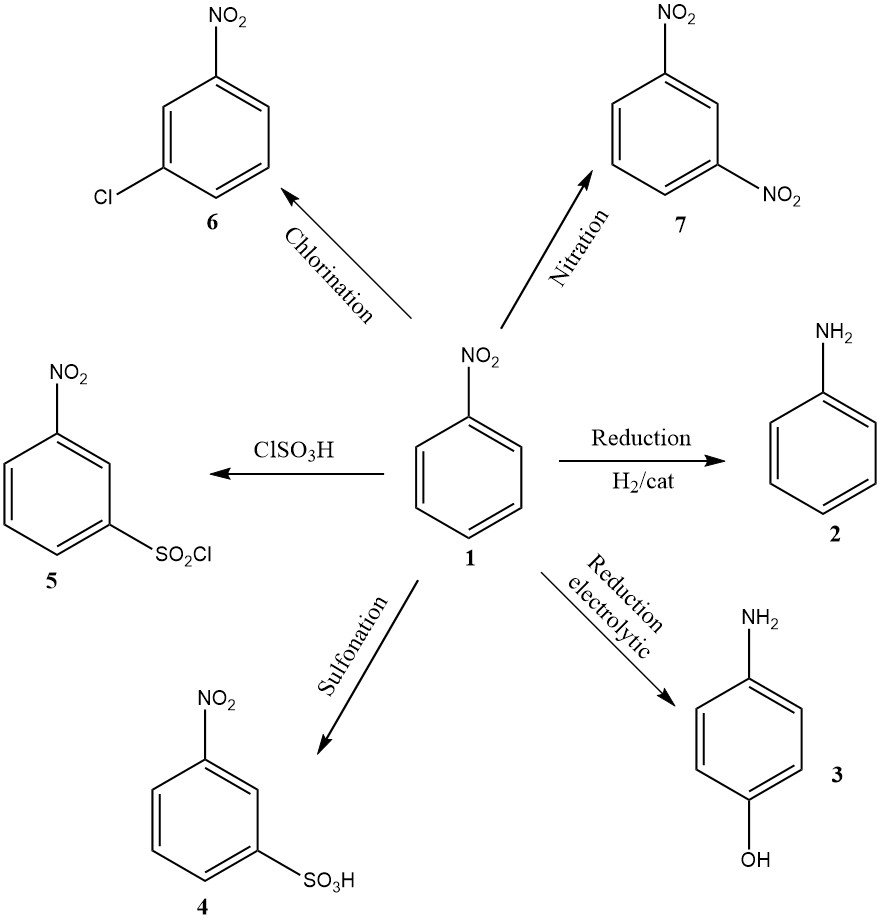
While lower in volume, other industrially relevant applications include electrolytic reduction to produce 4-aminophenol, nitration resulting in 1,3-dinitrobenzene (7), chlorination leading to 3-chloronitrobenzene (6), sulfonation yielding 3-nitrobenzenesulfonic acid (4), and chlorosulfonation giving 3-nitrobenzenesulfonyl chloride (5).
The latter three products are primarily used as precursors for their reduction products: 3-chloroaniline, metanilic acid, and 3-aminobenzenesulfonamide, respectively.
Aniline finds applications in the manufacturing of urethane polymers, rubber chemicals, pesticides, dyes (particularly azo dyes), explosives, and pharmaceuticals. It is a versatile compound with a wide range of uses across different industries.
In addition to its role as an aniline precursor, nitrobenzene is also utilized as a solvent in certain laboratory and industrial processes. It can be used to dissolve various substances, especially those that are not soluble in water.
Nitrobenzene’s solubility in organic solvents makes it a useful tool in certain experimental procedures.
Additionally, Nigrosin (C.I. Solvent Black 5) is obtained as a crude mixture resulting from the reaction of nitrobenzene with aniline and aniline hydrochloride at a temperature of 200 °C in the presence of iron or copper.
5. Toxicity of Nitrobenzene
Nitrobenzene, with a Threshold Limit Value (TLV) of 5 mg/m³, is highly toxic and can result in acute poisoning due to its easy absorption through the skin or respiratory tract.
The main effects of exposure include a reduction in hemoglobin levels, methemoglobinemia, cyanosis, and breathlessness. Prolonged exposure can lead to damage to the spleen and liver, jaundice, and anemia.
It’s important to note that the consumption of alcohol can accelerate and intensify these effects. Therefore, stringent and well-defined working conditions must be established and maintained to ensure proper control and safety.
Reference
- Nitro Compounds, Aromatic; Ullmann’s Encyclopedia of Industrial Chemistry. – https://onlinelibrary.wiley.com/doi/10.1002/14356007.a17_411
FAQ
Nitrobenzene is an organic chemical compound with the molecular formula C6H5NO2. It is a pale yellow liquid with a distinctive odor similar to bitter almonds.
The chemical formula of nitrobenzene is C6H5NO2.
Nitrobenzene is commonly synthesized through a process called nitration. In this process, benzene is reacted with nitric acid or a mixture of nitric acid and sulfuric acid to introduce a nitro group (-NO2) onto the benzene ring.
Nitrobenzene finds various industrial applications, such as being used as a precursor in the production of aniline, which is further utilized to produce a wide range of products, including dyes, pharmaceuticals, and rubber chemicals. Additionally, it serves as a solvent in some chemical reactions.
Nitrobenzene is reduced to aniline using reducing agents such as iron, zinc, or tin in the presence of hydrochloric acid (HCl) or using other catalysts like hydrogen gas (H2).
Yes, nitrobenzene is considered highly toxic and can pose severe health risks to humans. Exposure to nitrobenzene can lead to acute poisoning, causing effects like methemoglobinemia, cyanosis, breathlessness, and damage to organs such as the liver and spleen.
No, nitrobenzene itself is not commonly used as an explosive. However, it is a precursor in the synthesis of other compounds that can be utilized in the production of explosives.
Nitrobenzene is also known by its common name “Oil of Mirbane” due to its use as an aromatic oil in the past.