Il caprolattame, l’ingrediente chiave del Nylon-6, può essere prodotto tramite diverse vie. Il metodo più comune è la conversione del cicloesanone in cicloesanone ossima tramite processi di ammossimazione o perossido di idrogeno. Questa ossima subisce quindi un riarrangiamento di Beckmann per formare il caprolattame.
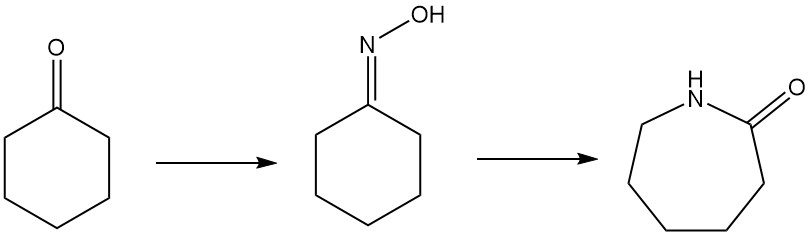
Altri processi includono la produzione tramite fotoossimazione e via basata sul toluene o viene recuperato dai rifiuti di Nylon-6. Stanno emergendo processi innovativi, tra cui la via ALTAM che utilizza metodi basati su butadiene o adiponitrile derivati da risorse rinnovabili come furfurolo o biomassa.
I moderni impianti di caprolattame sono operazioni complesse e multistadio, con capacità attuali a linea singola che raggiungono un’impressionante cifra di 200.000 tonnellate all’anno per la tecnologia Fibrant HPO ampiamente autorizzata.
Mentre il cicloesanone domina come materiale di partenza (>98%), possono essere utilizzati anche cicloesano e toluene. In particolare, l’idrogenazione del fenolo e vari percorsi di ossidazione del cicloesano vengono impiegati per ottenere l’intermedio chiave. L’efficienza combinata della conversione del cicloesanone in caprolattame è di circa il 98%.
Sommario
1. Produzione di caprolattame tramite processo di cicloesanone
La moderna produzione di caprolattame si basa sul benzene estratto da flussi di BTX come materia prima primaria. Tutti i processi commerciali tranne uno utilizzano l’ossima di cicloesanone come intermedio. Questa ossima si forma tramite la reazione del cicloesanone con idrossilammina, generata tramite vari metodi come:
- Processo Raschig
- Processo di idrogenazione dell’ossido nitrico in acido solforico
- Processo HPO fibrante
- Processo di ammossimazione
1.1. Cicloesanone ossima mediante processo Raschig
In questo processo, la cicloesanone ossima viene prodotta dalla reazione di cicloesanone e solfato di idrossilammina, e l’ammoniaca viene utilizzata per neutralizzare il sale di ossima. Il solfato di ammonio viene prodotto come sottoprodotto di questa reazione.
Sono stati implementati diversi miglioramenti, noti come processi Raschig, per aumentare la resa di cicloesanone ossima e ridurre al minimo la produzione di sale di solfato. I processi Raschig modificati, gli unici ancora in funzione, generano esclusivamente solfato di ammonio come sottoprodotto.
Nel processo Raschig modificato, prima le materie prime (ammoniaca, CO2, SO2, acqua e aria) reagiscono per formare solfato di idrossilammina tramite Equazione (1). Quindi, il solfato di idrossilammina reagisce con il cicloesanone per produrre ossima di cicloesanone (Equazione (2)).
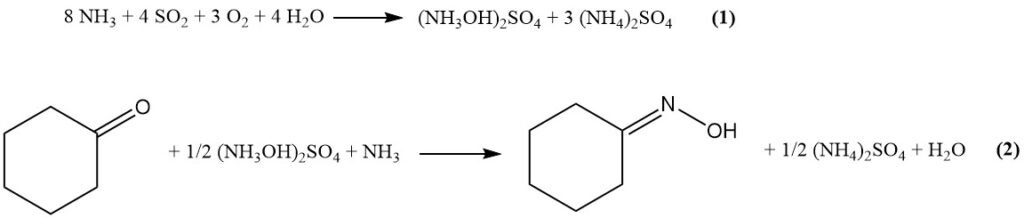
Di seguito sono elencati i principali passaggi del processo:
L’ammoniaca assorbe CO2 in acqua per formare una soluzione di carbonato/bicarbonato di ammonio.
L’ammoniaca brucia con aria (catalizzatori Pt/Rh) a ~850 °C per generare NOx e acqua. I gas caldi vengono raffreddati, recuperando il calore di ossidazione esotermica e condensando l’acido nitrico diluito del sottoprodotto.
La miscela di gas nitroso e la soluzione di carbonato/bicarbonato di ammonio reagiscono a <10 °C e pH 15 per formare nitrito di ammonio.
La combustione dello zolfo produce SO2 (10–20 vol%), con recupero di calore per la generazione di vapore.
- SO2 reagisce con una miscela acquosa di nitrito di ammonio e idrossido di ammonio per formare acido idrossiimmidodisolforico. La temperatura e il rapporto NH4OH/NH4NO2 sono parametri importanti per ridurre al minimo i sottoprodotti.
L’acido idrossiimmidodisolforico subisce idrolisi e neutralizzazione per formare solfato di idrossilammina tramite N-idrossisolfamato di ammonio.
L’ossimazione del cicloesanone con solfato di idrossilammina a pH 4,5 e 50–100 °C produce cicloesanone ossima.
L’ammoniaca acquosa neutralizza l’acido solforico liberato e il solfato di ammonio coprodotto viene recuperato tramite cristallizzazione evaporativa.
Altri sottoprodotti del processo Raschig sono i gas nitrosi nei gas di scarico della formazione di nitrito, il gas azoto dalla decomposizione del nitrito di ammonio e il gas N2O da varie reazioni di decomposizione.
1.2. Idrogenazione dell’ossido nitrico nel processo dell’acido solforico
Per ridurre al minimo la coproduzione di solfato di ammonio, BASF, Cyclopol e Inventa hanno sviluppato processi che prevedono la riduzione catalitica dell’ossido nitrico con idrogeno a solfato di idrossilammina in acido solforico diluito. L’ossido nitrico stesso viene generato tramite ossidazione catalitica dell’ammoniaca con ossigeno puro e vapore.
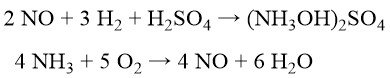
La successiva produzione di ossima è simile al processo Raschig (Equazione (2)). Questo percorso, con la neutralizzazione dell’eccesso di H2SO4, genera ancora ~0,7 kg di solfato di ammonio per kg di cicloesanone ossima. I rischi di esplosione sono mitigati dalla composizione controllata del gas durante la sintesi del solfato di idrossilammina. Sono necessarie un’ampia purificazione delle materie prime e complesse elaborazioni del catalizzatore.
Un ~14% di ammoniaca, un ~1,34 rapporto O2/NH3 e una miscela di vapore passano su un catalizzatore Pt/Rh a ~850 °C per formare principalmente NO e altri ossidi di azoto. Il gas caldo si raffredda in una caldaia a recupero di calore (generando vapore), quindi si raffredda ulteriormente per condensare l’acqua e diluire l’acido nitrico.
Il restante NO2 viene lavato via in torri consecutive con acido nitrico diluito e soluzioni di soda caustica, ottenendo una purezza di circa il 95%.
La sintesi dell’idrossilammina comprende più linee di 5-7 reattori ben agitati da 20 m3 azionati in continuo. Ogni reattore riceve una soluzione di acido solforico purificato al 20% in peso con circa 35 g/L di catalizzatore di grafite-Pt finemente disperso (circa 0,5% in peso). Tutti i reattori ricevono NO purificato e idrogeno in eccesso. La temperatura di reazione è di circa 45 °C.
Mentre viene utilizzata la pressione atmosferica, una pressione elevata può essere vantaggiosa. Una soluzione di solfato di idrossilammina al ~25% in peso contenente il catalizzatore esce dall’ultimo reattore e viene sottoposta a filtrazione. La sospensione concentrata del catalizzatore viene riciclata nel primo reattore.
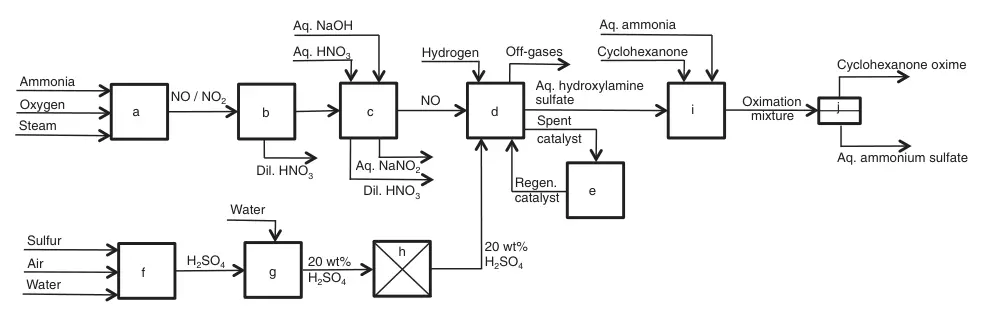
a) Combustione dell'ammoniaca; b) Condensazione; c) Lavaggio di NO; d) Riduzione di NO; e) Rigenerazione del catalizzatore; f) Combustione dello zolfo; g) Diluizione; h) Purificazione; i) Cicloesanone ossima; j) Separazione cicloesanone ossima/solfato di ammonio acquoso
Le miscele di reazione estremamente corrosive e la sensibilità del catalizzatore richiedono un’attenta selezione dei materiali. Inventa ha proposto rivestimenti in gomma/resina sintetica e BASF ha suggerito tipi speciali di acciaio senza rame.
La soluzione di solfato di idrossilammina prodotta reagisce con il cicloesanone a una temperatura (85–90 °C) superiore al punto di fusione dell’ossima acquosa di cicloesanone. La fase di solfato di ammonio acquoso risultante si separa dalla fase organica contenente circa il 7% in peso di acqua ed entrambe vengono elaborate separatamente.
L’ossima di cicloesanone viene estratta dalla fase di solfato di ammonio con cicloesanone, successivamente recuperata tramite distillazione. La cristallizzazione evaporativa della soluzione rimanente produce circa 0,7 kg di solfato di ammonio cristallino per kg di cicloesanone ossima. Dopo l’essiccazione parziale, l’ossima contenente acqua è pronta per il riarrangiamento di Beckmann per produrre caprolattame.
1.3. Processo Fibrant HPO®
Sviluppato da Fibrant negli anni ’60, il processo HPO (idrossilammina fosfato ossima) offre un approccio unico alla produzione di cicloesanone ossima basato sull’idrogenazione selettiva di ioni nitrato/ossido di azoto.
Questo percorso combinato di sintesi di idrossilammina e ossima elimina il sottoprodotto di solfato di ammonio. Il processo HPO consente un ciclo chiuso tra sintesi di idrossilammina e ossima evitando la liberazione di acido solforico durante la formazione di ossima,
Ruota attorno al riciclo di due flussi: un tampone di acido fosforico acquoso e una fase di processo organica. Diverse reazioni e operazioni chiave si verificano all’interno di questo sistema.

L’idrogenazione catalitica selettiva degli ioni nitrato con gas idrogeno nella soluzione tampone di acido fosforico genera idrossilammina. Al pH ~2 della reazione, l’idrossilammina risultante diventa protonata, formando fosfato di idrossilammonio. Pd/Pt supportato su carbonio o allumina è utilizzato come catalizzatore.
Un esclusivo sistema di reattori a colonna a bolle trifase combina un contatto ottimale gas-liquido-solido con un’efficiente rimozione del calore. L’idrogeno non reagito viene riciclato dopo la separazione dalla sospensione del catalizzatore. La soluzione tampone di acido fosforico di idrossilammonio procede alla sezione di ossimazione.
Il tampone acquoso di idrossilammina-acido fosforico viene fatto reagire con una fase organica di toluene-cicloesanone converte il cicloesanone in cicloesanone ossima e libera acido fosforico. Questa fase di ossimazione funziona a pH ~2, ottenendo conversioni quasi quantitative sia di idrossilammina che di cicloesanone.
La fase organica formata (cicloesanone ossima-toluene) viene separata dal tampone acquoso, lavata con acqua e quindi il toluene viene distillato. L’ossima secca viene trasferita alla sezione di riarrangiamento di Beckmann, mentre il toluene distillato viene riciclato al reattore di ossimazione.
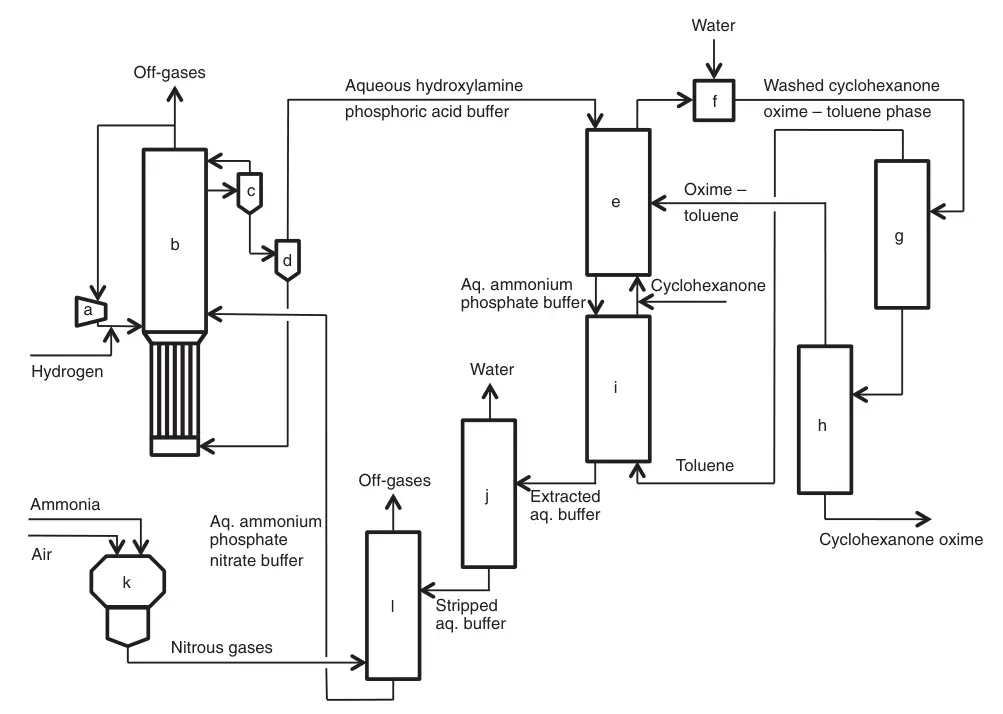
a) Compressore; b) Reattore di idrogenazione del nitrato; c) Separatore gas-liquido; d) Filtrazione del catalizzatore; e) Ossimazione; f) Lavaggio; g) Distillazione del toluene; h) Purificazione dell'ossima cicloesanone; i) Estrazione; j) Strippaggio con vapore; k) Combustione dell'ammoniaca; l) Decomposizione dell'ammoniaca e assorbimento dei gas nitrosi
Lo sviluppo continuo del processo HPO ha portato al processo HPOplus intensificato, caratterizzato da flussi di processo concentrati, consumo ridotto di materie prime/energia e capacità di ossima a linea singola notevolmente aumentata (>200.000 t/a).
1.4. Processo di ammossimazione
La reazione del cicloesanone con ammoniaca e perossido di idrogeno offre una via alternativa alla sintesi dell’ossima del cicloesanone in fase liquida senza generare sottoprodotti di solfato di ammonio.

Il successo iniziale di questo approccio arrivò nel 1960 con l’uso di catalizzatori di tungsteno e stagno in ammoniaca acquosa a 10–30 °C, ottenendo elevate rese di ossima (>90%). Tuttavia, le sfide di estrazione e recupero del catalizzatore ostacolarono la commercializzazione.
Alla fine degli anni ’70, fu sviluppato un materiale sintetico poroso (silicalite di titanio (TS-1)), che portò a nuovi processi di ossidazione catalitica. Nel 1987, Montedipe implementò TS-1 per l’ammossimazione del cicloesanone, seguita da processi simili da Sinopec.
L’ammoniaca reagisce con il perossido di idrogeno sui centri di titanio del catalizzatore, formando l’idrossilammina intermedia, che successivamente reagisce con il cicloesanone per dare l’ossima desiderata.
Il rapporto di alimentazione molare di H2O2/cicloesanone è 1,0-1,1 e un alcol terziario stabile (ad esempio, alcol terz-butilico) a 2-4 volte il peso del cicloesanone viene utilizzato come solvente.
La reazione viene eseguita a una temperatura di ~85 °C e una pressione di >0,25 MPa per circa 1,5 ore per ottenere una conversione del cicloesanone in ossima fino al 98%.
Il primo impianto commerciale basato su questa tecnologia è stato costruito da Sumitomo Chemical nel 2003. Diversi impianti cinesi di caprolattame utilizzano questa tecnologia, alcuni con varianti TS-1.
Una descrizione semplificata del processo è mostrata nella Figura3:
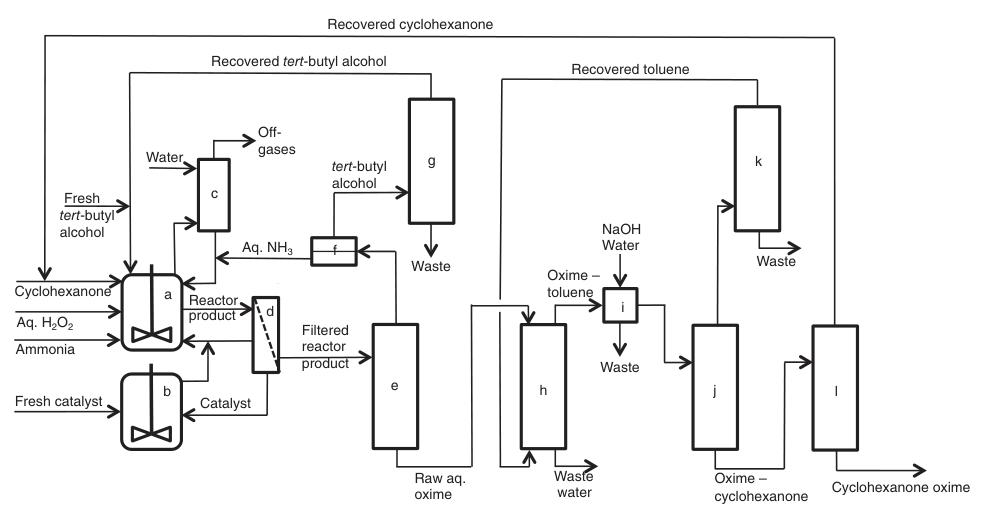
a) Reattori di ammossimazione; b) Preparazione/purificazione del catalizzatore; c) Lavaggio dei gas di scarico; d) Filtrazione; e) Recupero di ammoniaca/alcol terz-butilico; f) Separazione L/L; g) Distillazione dell'alcol terz-butilico; h) Estrazione; i) Lavaggio; j) Recupero del solvente; k) Distillazione del solvente; l) Recupero del cicloesanone
Il processo inizia con un flusso continuo di materia prima contenente perossido di idrogeno diluito, cicloesanone, ammoniaca, alcol terz-butilico (sia fresco che riciclato) e catalizzatore (fresco o riciclato) che entra nei reattori di ammossimazione agitati.
I gas di scarico generati durante questa fase, che contengono ammoniaca non reagita, vengono lavati con acqua per recuperare e riciclare l’ammoniaca.
La miscela di prodotti risultante viene quindi sottoposta a filtrazione e inviata a una colonna di recupero per la separazione e la purificazione. In questa fase, possono essere impiegati due percorsi alternativi:
1. Estrazione del toluene:
L’ammoniaca non reagita e l’alcol terz-butilico contenente acqua vengono recuperati e purificati per il riutilizzo. L’ossima del cicloesanone e il cicloesanone non reagito vengono estratti utilizzando toluene, seguito da lavaggio con acqua e ulteriore separazione per distillazione.
2. Riestrazione controcorrente:
Una fase di riestrazione controcorrente continua utilizza acqua demineralizzata per formare fasi separate di ossima acquosa e cicloesanone. Queste fasi vengono quindi sottoposte a ulteriore purificazione tramite distillazione.
1.5. Riarrangiamento di Beckmann dell’ossima di cicloesanone in caprolattame
Il caprolattame, un precursore chiave del nylon-6, è prodotto principalmente dall’ossima di cicloesanone tramite il riarrangiamento di Beckmann. Questa reazione altamente esotermica si verifica sia in fase liquida che in fase gassosa.
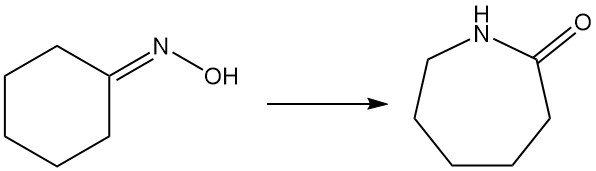
La conversione dell’ossima in caprolattame comporta il tradizionale riarrangiamento di Beckmann in fase liquida con acido solforico fumante, generando solfato di ammonio come coprodotto. Sumitomo Chemical, tuttavia, utilizza un esclusivo processo di riarrangiamento di Beckmann in fase vapore.
Un prezzo basso del solfato di ammonio rende la sua coproduzione indesiderabile, motivando lo sviluppo di processi che lo riducano al minimo o lo eliminino. Tuttavia, il solfato di ammonio può anche favorire la produzione di caprolattame quando utilizzato come fertilizzante in specifiche condizioni del terreno, fornendo azoto, zolfo e regolazione del pH.
1.5.1. Riarrangiamento di Beckmann in fase liquida
Il metodo industriale dominante utilizza acido solforico fumante o oleum come catalizzatore e solvente. Raggiunge un’elevata conversione dell’ossima e la resa del caprolattame è quasi del 100%, ma genera solfato di ammonio come sottoprodotto.
I parametri di reazione come temperatura, concentrazione acida e miscelazione hanno un impatto significativo sulla purezza e sul colore del prodotto. La riorganizzazione multistadio con alimentazione di oleum distribuita riduce la produzione di solfato di ammonio.
La purificazione finale del caprolattame prevede estrazione con solvente, distillazione e lavaggio.
1.5.2. Riorganizzazione in fase gassosa (riorganizzazione catalitica eterogenea)
La riorganizzazione in fase gassosa è stata sviluppata per evitare la generazione di solfato di ammonio associata ai metodi in fase liquida. I primi tentativi di utilizzare catalizzatori che eliminano l’acqua hanno avuto difficoltà con la bassa selettività e la disattivazione del catalizzatore.
Sumitomo Chemical ha ottenuto un successo industriale con zeoliti ad alto contenuto di silice in presenza di acqua e metanolo.
Questo processo comporta l’evaporazione di una miscela umida di ossima/metanolo. L’ossima viene quindi convertita in caprolattame su catalizzatore zeolitico MFI a 350-380 °C. Il catalizzatore viene rigenerato continuamente con aria a 500 °C in un sistema a letto fluido.
Le impurità dal caprolattame risultante vengono rimosse tramite distillazione. Un’ulteriore purificazione del caprolattame tramite cristallizzazione da un solvente misto e tramite idrogenazione e distillazione multifase fornisce un prodotto altamente puro.
Sumitomo Chemical è l’unico produttore commerciale che utilizza la riorganizzazione in fase gassosa senza generare solfato di ammonio.
2. Produzione di caprolattame tramite fotoossimazione
Negli anni ’50, Toray ha sviluppato un processo fotochimico unico per produrre caprolattame. Questa metodologia, chiamata Fotonitrosazione (PNC), bypassa la sintesi convenzionale dell’ossima mediante conversione diretta del cicloesano in dicloridrato di cicloesanone ossima, seguita da successiva riorganizzazione di Beckmann in caprolattame.
Il cicloesano viene fatto reagire con cloruro di nitrosile per dare cloridrato di cicloesanone ossima, seguendo le reazioni sottostanti:
1. Formazione di acido nitrosilsolforico: i gas nitrosi ottenuti dalla combustione dell’ammoniaca vengono fatti reagire con acido solforico per produrre acido nitrosilsolforico (NOHSO4).
2 H2SO4 + NO + NO2 → 2 NOHSO4 + H2O
2. Produzione di NOCl: NOHSO4 reagisce con acido cloridrico (HCl) per produrre NOCl, con rigenerazione simultanea di acido solforico.
NOHSO4 + HCl → NOCl + H2SO4
3. Conversione fotochimica:

Il processo PNC si basa sulla reazione fotochimica del cicloesano con NOCl in presenza di HCl in eccesso. Questa trasformazione è facilitata da lampade LED ad alte prestazioni che emettono luce attinica e porta alla formazione selettiva di dicloridrato di ossima di cicloesanone come strato di fondo oleoso.
In particolare, le lampade LED offrono un’efficienza energetica superiore (0,4 kg di ossima per kWh) e una selettività molare (86%) rispetto alle precedenti alternative di lampade al mercurio.
Il dicloridrato di ossima recuperato subisce un riarrangiamento di Beckmann utilizzando oleum, producendo caprolattame. Il cicloesano non reagito viene riciclato, mentre l’acido cloridrico sviluppato viene recuperato tramite un processo di assorbimento e concentrazione acquosa.
La soluzione grezza di caprolattame viene neutralizzata con ammoniaca e sottoposta a ulteriore purificazione tramite trattamento chimico, essiccazione e distillazione. Questo processo genera 1,55 tonnellate di solfato di ammonio per tonnellata di caprolattame.
3. Recupero di caprolattame da rifiuti di nylon-6
I rifiuti di nylon-6, generati durante tutto il loro ciclo di vita dalla produzione allo smaltimento del prodotto finale, rappresentano un’opportunità per il recupero delle risorse. I processi di depolimerizzazione recuperano il prezioso caprolattame da questi flussi di rifiuti, offrendo vantaggi sia ambientali che economici.
I rifiuti solidi di nylon-6 vengono depolimerizzati in caprolattame in un reattore a bollitore ad alta pressione utilizzando vapore surriscaldato con un catalizzatore di cracking (tipicamente acido fosforico). Questa conversione può avvenire anche senza catalizzatore sotto elevata pressione del vapore.
La miscela di vapore e caprolattame risultante subisce una condensazione e concentrazione parziali. Quindi, un agente ossidante purifica il concentrato, seguito dalla purificazione finale del caprolattame tramite distillazione.
L’acqua di lavaggio dalla produzione di chip di nylon-6 contiene oligomeri di caprolattame insieme al monomero. La preconcentrazione tramite evaporazione a film sottile precede la depolimerizzazione utilizzando la stessa metodologia dei rifiuti solidi.
La soluzione acquosa di caprolattame risultante viene sottoposta a purificazione chimica e distillazione per produrre acqua, frazioni bassobollenti e il prodotto caprolattame desiderato.
Metodi alternativi affrontano anche la depolimerizzazione degli oligomeri. Un approccio prevede la concentrazione dell’acqua di lavaggio per mantenere la solubilità degli oligomeri e l’alimentazione della soluzione caprolattame-oligomeri in un reattore a letto fisso o a letto fluidizzato.
Un catalizzatore di ossido di alluminio specializzato cracca gli oligomeri a 275-350 °C, ottenendo una resa del 95% rispetto all’alimentazione. I metodi di purificazione convenzionali recuperano successivamente il caprolattame.
Diverse tecnologie consolidate si occupano di rifiuti di nylon-6 post-consumo, in particolare tappeti scartati. Questi processi richiedono la raccolta, la selezione e la triturazione meccanica prima della depolimerizzazione in caprolattame di grado vergine.
Esempi degni di nota includono il programma “6ix Again” di BASF, che utilizza un reattore semicontinuo con acido fosforico e vapore surriscaldato per la depolimerizzazione ad alta temperatura (250-300 °C). La successiva purificazione con un agente ossidante e la distillazione sotto vuoto recuperano il caprolattame dal distillato.
Un altro processo è Evergreen Nylon Recycling, un metodo di depolimerizzazione non catalizzata a due stadi che impiega un sistema di reattori ad alta pressione e vapore surriscaldato per idrolizzare il materiale triturato. Recupera il 90-95% del nylon-6 iniziale come caprolattame, adatto per la produzione di tappeti.
4. Processo a base di toluene
Sviluppato da Snia Viscosa nel 1960 e utilizzato in Italia fino ai primi anni ’90, questo processo a base di toluene offre un percorso alternativo alla produzione di caprolattame. Il processo comprende tre fasi chiave:
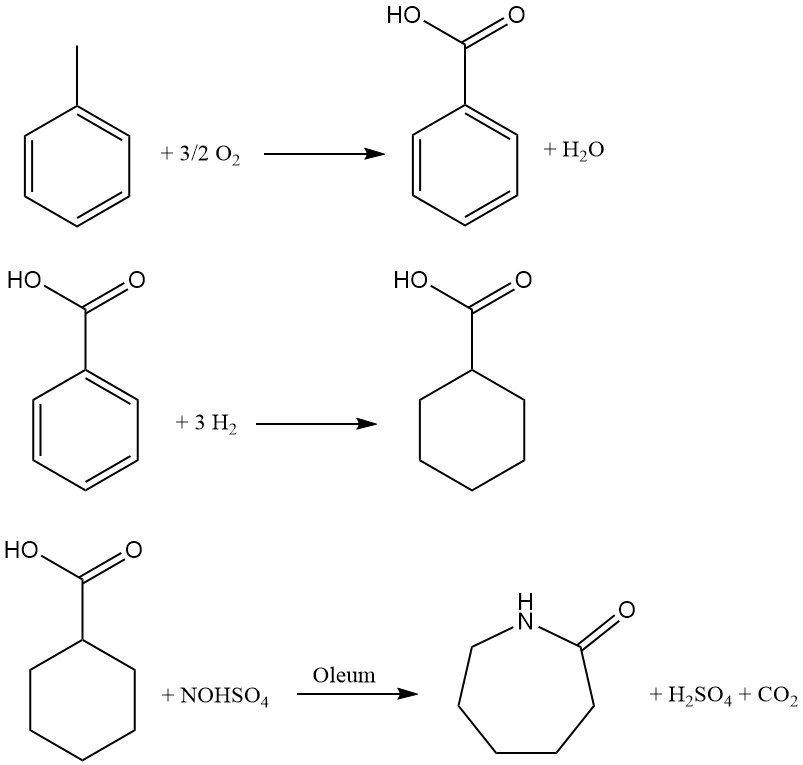
1. Ossidazione catalitica: il toluene subisce un’ossidazione dell’aria nella fase liquida utilizzando un catalizzatore al cobalto a 160-170 °C e una pressione di 0,8-1 MPa. Il recupero del toluene non reagito tramite raffreddamento garantisce una resa ottimale. Il prodotto liquido risultante, contenente circa il 30% di acido benzoico insieme a intermedi e sottoprodotti, necessita di una distillazione multistadio per la purificazione.
2. Idrogenazione: l’acido benzoico viene convertito in acido cicloesancarbossilico tramite idrogenazione nella fase liquida utilizzando un catalizzatore Pd/C. Una serie di reattori agitati che operano a circa 170 °C e una pressione di 1-1,7 MPa facilitano una trasformazione efficiente. La successiva distillazione a pressione ridotta purifica l’acido risultante.
3. Nitrosodecarbossilazione e riarrangiamento: questo passaggio cruciale combina la nitrosazione dell’acido cicloesancarbossilico con il riarrangiamento di Beckmann per generare direttamente caprolattame. Una soluzione di acido nitrosilsolforico al 73% in acido solforico, preparata tramite assorbimento convenzionale di NO in oleum, viene utilizzata nella reazione all’interno di un reattore multistadio.
Mantenere il tasso di conversione intorno al 50% richiede che il processo avvenga in cicloesano bollente a pressione atmosferica. Gli acidi solfonici si formano come inevitabili sottoprodotti.
A seguito della nitrosazione-riarrangiamento combinata, il flusso di prodotto subisce idrolisi con acqua a basse temperature. L’estrazione dell’acido cicloesancarbossilico non reagito consente il suo riciclo nel processo.
La soluzione acida di caprolattame, contenente acido solforico in eccesso, passa quindi alla fase di neutralizzazione. La cristallizzazione a pressione ridotta con ammoniaca produce due distinti strati liquidi: una soluzione di solfato di ammonio e una soluzione acquosa di caprolattame. Un’ulteriore purificazione comporta:
- L’estrazione con toluene separa il caprolattame dai sottoprodotti solubili in acqua.
- L’estrazione controcorrente con acqua recupera il caprolattame dalla soluzione di toluene.
- La distillazione produce caprolattame puro dalla soluzione acquosa concentrata.
5. Processi alternativi
Oltre al processo convenzionale di ammossimazione del cicloesanone, sono emersi diversi percorsi alternativi per il caprolattame:
5.1. Processi con perossido di idrogeno
- Processo Inventa: L’ossidazione della cicloesilammina con perossido di idrogeno genera cicloesanone ossima.
- Processo 1,1´-perossidicicloesilammina: Il cicloesanone e il perossido di idrogeno reagiscono per formare un perossido, che poi si converte in caprolattame e rigenera il cicloesanone.
5.2. Ossidazione della cicloesilammina con ossigeno elementare:
L’ossidazione diretta della cicloesilammina con ossigeno produce cicloesanone ossima.
5.3. Ossimazione diretta del cicloesanone:
Ammoniaca, aria e cicloesanone reagiscono direttamente su vari catalizzatori per formare cicloesanone ossima.
5.4. Processo del bis(nitrosocicloesano):
La scarica elettrica innesca la reazione del cicloesano con ossido nitrico o composti correlati, formando bis(nitrosocicloesano), che si riorganizza in cicloesanone ossima.
5.5. Processo acido ε-idrossicaproico/ε-caprolattone:
L’ossidazione del cicloesanone con aria genera acido ε-idrossicaproico e acido adipico (sottoprodotto). Entrambi possono essere convertiti in caprolattame tramite percorsi diversi.
5.6. Processo 2-nitrocicloesanone:
Una sequenza unica di reazioni che coinvolgono acetilazione, nitrazione, scissione dell’anello, idrogenazione e ciclizzazione converte il cicloesanone in caprolattame senza sottoprodotti.
5.7. Processo 3,3-pentametilenoxaziridina:
L’ipoclorito reagisce con il cicloesanone in ammoniaca acquosa per formare cicloesanone isossima, che poi si riorganizza in caprolattame sotto calore.
5.8. Deacetilazione catalitica di N-acetilcaprolattame:
L’ossima di O-acetilcicloesanone subisce una deacetilazione sui catalizzatori per produrre caprolattame.
5.9. Processi basati sul butadiene:
- Processo ALTAM: sviluppato da DSM e altri, questo processo multi-step utilizza il butadiene per produrre caprolattame con elevata selettività.
- Processi basati sull’adiponitrile: BASF e Rhone-Poulenc hanno sviluppato processi indipendenti per la produzione di caprolattame dall’adiponitrile, ottenuto da vari percorsi, incluso il butadiene.
5.10. Percorsi biorinnovabili:
Con le crescenti preoccupazioni sulla sostenibilità, le risorse di origine biologica stanno guadagnando terreno come materie prime per la produzione di caprolattame. Sono in fase di sviluppo diverse vie promettenti, incentrate su:
- Prodotti chimici drop-in: Benzene bioderivato, fenolo, acrilonitrile o HMF possono essere facilmente integrati nei processi caprolattame esistenti.
- Vie chimiche: L’acido levulinico o il furfurale, ottenuti dalla biomassa, possono essere convertiti in intermedi che portano al caprolattame.
- Vie (parzialmente) fermentative: Sintesi microbica di lisina o fermentazione dei carboidrati offre potenziali percorsi per i precursori del caprolattame.
Sebbene attualmente non siano economicamente competitivi con i metodi tradizionali, i processi biorinnovabili promettono una futura produzione sostenibile di caprolattame.
Riferimento
- Caprolactam; Ullmann’s Encyclopedia of Industrial Chemistry. – https://onlinelibrary.wiley.com/doi/10.1002/14356007.a05_031.pub3