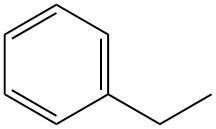
Qu’est-ce que l’éthylbenzène ?
L’éthylbenzène, également connu sous le nom de phényléthane, est un hydrocarbure alkylaromatique monocyclique de formule C8H10. C’est un liquide incolore et hautement inflammable avec une odeur aromatique caractéristique.
Il est principalement utilisé (> 99 %) comme intermédiaire dans la production de monomère de styrène, l’un des produits chimiques de base à volume élevé les plus importants au monde.
La production à l’échelle commerciale d’éthylbenzène a commencé dans les années 1930 par Dow Chemical (États-Unis) et BASF (Allemagne). L’industrie de l’éthylbenzène/styrène est restée relativement peu importante jusqu’à la Seconde Guerre mondiale.
La forte demande de caoutchouc styrène-butadiène synthétique (SBR) pendant les années de guerre a accéléré les progrès technologiques rapides et l’expansion significative des capacités. Cet effort de guerre a conduit à la construction de nombreuses usines à grande échelle, et la production de styrène est rapidement devenue une industrie majeure.
En 1999, la capacité de production annuelle mondiale d’éthylbenzène a atteint près de 25 millions de tonnes. Les années 1990 ont été particulièrement marquées par la croissance des capacités dans les pays d’Extrême-Orient (hors Japon), où les industries pétrochimiques fondamentales ont connu un développement et une expansion considérables.
Table des matières
1. Propriétés physiques de l’éthylbenzène
Dans des conditions normales, l’éthylbenzène est un liquide incolore à l’odeur aromatique. Il est insoluble dans l’eau mais très soluble dans l’éthanol et l’éther éthylique. L’éthylbenzène est un irritant pour la peau et les yeux et est modérément toxique par ingestion, inhalation et adsorption cutanée.
Certaines propriétés physiques de l’éthylbenzène sont répertoriées dans le tableau suivant.
Propriété | Valeur |
---|---|
Numéro CAS | [100-41-4] |
Formule chimique | C6H5CH2CH3 |
Masse moléculaire | 106,168 g/mol |
Densité |
|
Point de fusion | -94,949 °C |
Point d'ébullition (101,3 kPa) | 136,2 °C |
Indice de réfraction |
|
Densité de vapeur | 3,66 |
Pression critique | 3609 kPa (36,09 bar) |
Température critique | 344,02 °C |
Point d'éclair (vase clos) | 15 °C |
Température d'auto-inflammation | 460 °C |
Limite d'inflammabilité |
|
Chaleur latente |
|
Pouvoir calorifique |
|
Cinématique viscosité |
|
Tension superficielle | 28,48 mN/m |
Capacité thermique massique |
|
Facteur acentrique | 0,3026 |
Compressibilité critique | 0,263 |
2. Réactions chimiques de l’éthylbenzène
La réaction commerciale la plus importante de l’éthylbenzène est sa déshydrogénation en styrène. Cette réaction se produit à haute température (600–660 °C) et utilise généralement un catalyseur à base d’oxyde de fer activé par le potassium avec de la vapeur comme diluant.
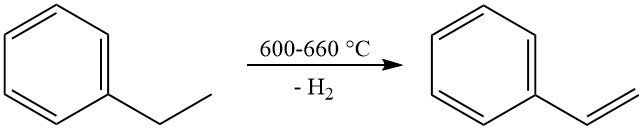
La production industrielle permet d’obtenir des sélectivités en styrène allant de 90 à 97 % en moles avec des conversions par passe de 60 à 70 %. La principale réaction secondaire est la désalkylation de l’éthylbenzène en benzène et en toluène.
Une autre réaction qui prend de l’importance commerciale est l’oxydation à l’air de l’éthylbenzène en hydroperoxyde d’éthylbenzène. Il s’agit d’un processus non catalysé qui se produit en phase liquide. Cependant, en raison de l’instabilité inhérente des hydroperoxydes, l’exposition à des températures élevées doit être minimisée pour réduire le taux de décomposition.
L’hydroperoxyde est ensuite traité avec du propylène pour coproduire du styrène et de l’oxyde de propylène. En 1999, environ 15 % de la production mondiale d’éthylbenzène a été consacrée à la coproduction de monomère de styrène et d’oxyde de propylène par cette voie.

Tout comme le toluène, l’éthylbenzène peut être désalkylé en benzène par des procédés catalytiques ou thermiques. De plus, l’éthylbenzène subit diverses autres réactions caractéristiques des composés alkylaromatiques, telles que l’alkylation, l’acylation, la nitration et la sulfonation.
3. Production industrielle d’éthylbenzène
Historiquement, pendant plusieurs décennies, la méthode dominante de production d’éthylbenzène était l’alkylation de Friedel-Crafts du benzène avec de l’éthylène en utilisant des acides de Lewis dissous, principalement du chlorure d’aluminium, comme catalyseurs en phase liquide. Cette méthode reste utilisée pour environ 40 % de la production mondiale d’éthylbenzène.
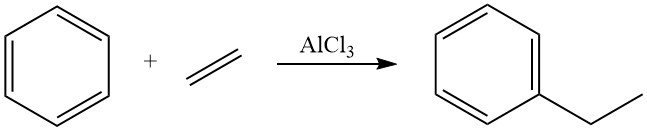
Bien que la méthode au chlorure d’aluminium puisse être compétitive sur le plan économique, ce procédé génère des flux de déchets dont l’élimination est de plus en plus coûteuse en raison des réglementations environnementales. De plus, le chlorure d’aluminium est hautement corrosif, ce qui entraîne des besoins importants en matière de maintenance des équipements et des canalisations.
Depuis le début des années 1980, les catalyseurs à base de zéolite hétérogène sont devenus la technologie préférée des nouvelles usines de production d’éthylbenzène. La technologie initiale à base de zéolite fonctionnait en phase vapeur, ce qui offrait une efficacité de processus améliorée par rapport au chlorure d’aluminium en phase liquide.
Plus récemment, des procédés à base de zéolite en phase liquide ont été développés, offrant une flexibilité supplémentaire. Cette technologie génère moins de déchets dangereux que la voie au chlorure d’aluminium.
Les préoccupations environnementales croissantes et les progrès de la technologie à base de zéolite ont incité de nombreux producteurs utilisant des unités au chlorure d’aluminium à moderniser leurs usines avec la technologie à base de zéolite. Entre 1997 et 1999, environ 106 tonnes de capacité ont été converties du chlorure d’aluminium aux procédés à base de zéolite.
En 2000, d’autres conversions étaient en phase d’ingénierie et la construction de nouvelles usines utilisant la technologie du chlorure d’aluminium a pratiquement cessé au cours de la dernière décennie.
Quelques usines produisent une quantité mineure d’éthylbenzène par superfractionnement de flux aromatiques mixtes en C8.
3.1. Production d’éthylbenzène à l’aide de chlorure d’aluminium et d’autres catalyseurs à base d’acide de Lewis
Pendant plusieurs décennies, les procédés au chlorure d’aluminium en phase liquide ont dominé la production d’éthylbenzène. Plusieurs entreprises, dont Dow, BASF, Shell et Monsanto, ont développé des variantes de cette technologie. Aujourd’hui, environ 40 % de la production mondiale d’éthylbenzène utilise encore AlCl3.
L’alkylation du benzène avec l’éthylène est hautement exothermique, libérant une quantité importante de chaleur (ΔH = -114 kJ/mol). L’utilisation du chlorure d’aluminium comme catalyseur dans cette réaction favorise une réaction rapide avec des rendements d’éthylbenzène presque stœchiométriques.
D’autres acides de Lewis comme AlBr3, FeCl3, ZrCl4 et BF3 peuvent également être utilisés. Les procédés utilisant AlCl3 intègrent souvent des promoteurs comme le chlorure d’éthyle ou le chlorure d’hydrogène. Ces promoteurs réduisent la quantité d’AlCl3 nécessaire à la réaction.
Le procédé AlCl3 classique (Figure 1) utilise trois phases dans le réacteur : liquide aromatique (benzène), gaz éthylène et une phase complexe de catalyseur à base d’huile rouge. La réaction se produit près de l’équilibre thermodynamique, nécessitant un seul réacteur pour l’alkylation et la transalkylation.
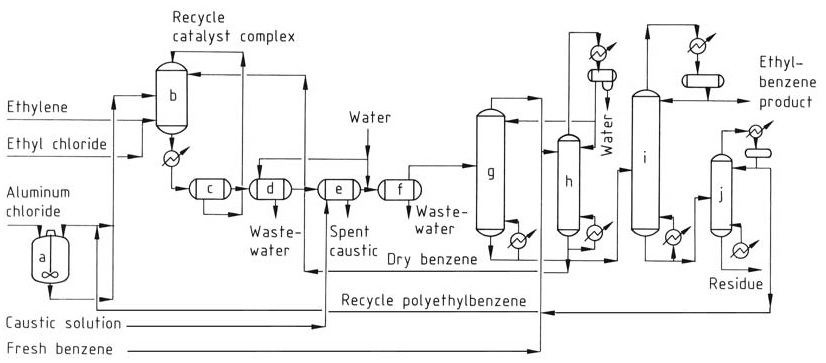
a) Cuve de mélange de catalyseurs ; b) Réacteur d'alkylation ; c) Cuve de décantation ; d) Séparateur d'acide ; e) Séparateur caustique ; f) Séparateur d'eau ; g) Colonne de récupération de benzène ; h) Colonne de déshydratation de benzène ; i) Colonne de récupération d'éthylbenzène ; j) Colonne de polyéthylbenzène
Le mélange complexe de catalyseur, le benzène sec et les polyalkylbenzènes recyclés sont introduits en continu dans le réacteur. De l’éthylène et un promoteur de catalyseur (par exemple, du chlorure d’éthyle) sont injectés dans le mélange réactionnel.
Les températures de fonctionnement sont limitées à 130 °C pour éviter la désactivation du catalyseur et la formation de sous-produits, et une pression suffisante est maintenue pour maintenir les réactifs en phase liquide.
Le procédé Monsanto amélioré (Figure 2) offre des avantages par rapport aux procédés AlCl3 classiques et a été mis en œuvre dans de nombreuses usines plus anciennes.
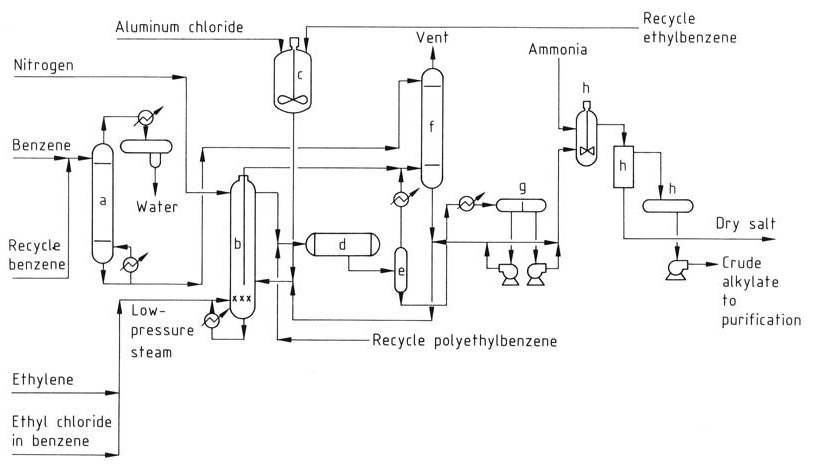
a) Colonne de séchage du benzène ; b) Réacteur d'alkylation ; c) Cuve de préparation du catalyseur ; d) Transalkylateur ; e) Tambour de détente ; f) Système de lavage des gaz d'échappement ; g) Décanteur ; h) Système de neutralisation
Ce procédé fonctionne à des températures plus élevées (160–180 °C) et utilise une phase liquide homogène. La température plus élevée permet de récupérer la chaleur perdue sous forme de vapeur. Cependant, un réacteur de transalkylation séparé est nécessaire en raison de la concentration plus faible du catalyseur.
En optimisant la température et l’ajout d’éthylène, le procédé réduit considérablement la quantité de catalyseur AlCl3 requise, minimisant ainsi les problèmes d’élimination des déchets et, comme il fonctionne dans une seule phase liquide homogène, il élimine la phase catalytique complexe présente dans les méthodes traditionnelles.
Les procédés conventionnels et Monsanto utilisent des étapes de purification similaires impliquant plusieurs colonnes de distillation pour séparer les fractions de benzène, d’éthylbenzène et de polyalkylbenzène non converties. Le résidu organique (huile de flux) est généralement utilisé comme combustible.
Le procédé Alkar, développé par UOP, utilise du trifluorure de bore comme catalyseur acide de Lewis. Bien qu’il offre des avantages tels qu’un produit d’éthylbenzène de haute pureté et la possibilité d’utiliser une charge d’éthylène diluée, le procédé n’est pas favorable en raison des coûts de maintenance élevés et de la sensibilité du catalyseur à une petite quantité d’eau.
3.2. Production d’éthylbenzène par alkylation en phase vapeur sur zéolites
La technologie en phase vapeur Mobil-Badger, qui s’appuie sur le catalyseur zéolite synthétique ZSM-5 de Mobil, est apparue dans les années 1970. Cette technologie a été proposée dans diverses configurations.
La conception de première génération, commercialisée en 1980, effectuait l’alkylation et la transalkylation dans un seul réacteur, de manière similaire aux procédés au chlorure d’aluminium. La dernière technologie de troisième génération sépare ces procédés, offrant des avantages en termes de rendement, de pureté et de coût d’investissement.
Le procédé à base de zéolite en phase vapeur est particulièrement adapté aux flux d’éthylène dilués, tels que ceux dérivés des unités de craquage catalytique fluide dans les raffineries.
Jusqu’à l’introduction des technologies à base de zéolite en phase liquide dans les années 1990, ce procédé dominait les nouvelles installations en raison de sa capacité à éviter les flux de déchets aqueux générés par la technologie au chlorure d’aluminium.
Mobil-Badger a obtenu des licences pour 31 unités depuis 1980 et la technologie reste pertinente pour les matières premières d’éthylène dilué.
Le catalyseur ZSM-5 à lit fixe favorise la même réaction d’alkylation que les autres procédés. Cependant, l’adsorption de l’éthylène sur les sites acides de Brønsted de la zéolite active la molécule d’éthylène, facilitant sa liaison avec le benzène. Ce mécanisme conduit à un sous-produit différent de celui des procédés Friedel-Crafts.
L’acier au carbone est le principal matériau de construction en raison de l’absence de composants hautement corrosifs. La conception de troisième génération est illustrée dans la Figure 3.
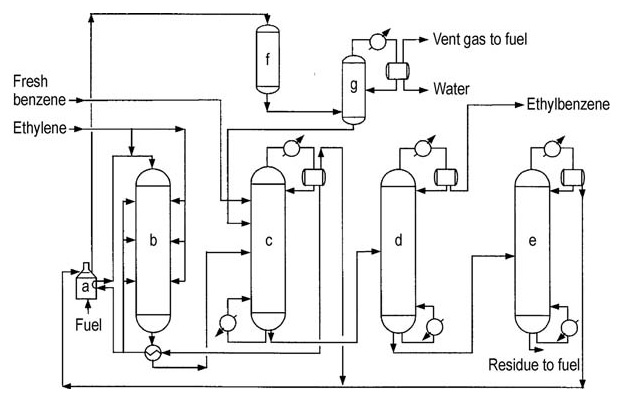
a) Réchauffeur d'alimentation du réacteur ; b) Réacteur d'alkylation ; c) Colonne de récupération du benzène ; d) Colonne de récupération de l'éthylbenzène ; e) Colonne de récupération du polyéthylènebenzène ; f) Réacteur secondaire ; g) Stabilisateur
Le réacteur d’alkylation fonctionne à 350–450 °C et 1-3 MPa, ce qui permet de récupérer la majeure partie de la chaleur du procédé sous forme de vapeur. Le réacteur utilise une configuration à lits multiples avec un réchauffeur à combustion et un équipement de récupération de chaleur.
L’excès de benzène est maintenu par rapport à l’éthylène. Le catalyseur se désactive progressivement en raison de la formation de coke, ce qui nécessite une régénération périodique in situ (environ tous les 18 à 24 mois), ce qui prend environ 36 heures.
Par rapport aux zéolites en phase liquide et aux catalyseurs à base d’acide de Lewis, cette technologie présente une plus grande tolérance à l’eau, au soufre et à d’autres poisons potentiels.
L’effluent vaporisé du réacteur subit une purification. Le benzène est récupéré par distillation dans la première colonne et recyclé. La deuxième colonne sépare l’éthylbenzène du flux de fond, qui est ensuite dirigé vers une colonne finale pour la séparation des fractions d’alkylbenzène et de polyalkylbenzène recyclables des résidus lourds non recyclables.
Ce résidu de faible viscosité, principalement composé de diphénylméthane et de diphényléthane, est utilisé comme carburant. Les alkylbenzènes supérieurs et les polyalkylbenzènes recyclables séparés sont introduits dans le transalkylateur en phase vapeur, où ils réagissent avec l’excès de benzène sur un catalyseur zéolithique.
Le transalkylateur fonctionne à une pression plus basse mais à une température plus élevée que l’alkylateur, favorisant la désalkylation des alkylbenzènes supérieurs tout en transalkylant le diéthylbenzène en éthylbenzène. Cette capacité de désalkylation minimise la production globale de résidus.
Les premiers procédés de première et de deuxième génération différaient principalement par l’emplacement du flux de recyclage de polyéthylbenzène, ce qui entraînait des performances inférieures par rapport à la conception de troisième génération.
3.3. Production d’éthylbenzène par alkylation en phase liquide sur zéolithes
La technologie de la zéolithe en phase liquide pour la production d’éthylbenzène est apparue au début des années 1990. La première usine commerciale, exploitée à Oita, au Japon, utilisait des catalyseurs ultrastables à base de zéolite Y ou de zéolite bêta, sous licence d’ABB Lummus Global et d’Unocal (plus tard acquis par ABB).
Un autre procédé, EBMax de Mobil-Badger, utilisait le catalyseur Mobil MCM-22. En 1999, douze usines étaient opérationnelles dans le monde.
Par rapport aux technologies antérieures utilisant de l’éthylène de qualité polymère, les procédés à base de zéolite en phase liquide nécessitent moins d’investissement et produisent un produit à base d’éthylbenzène de meilleure qualité.
La technologie en phase vapeur est désormais principalement sous licence de Mobil-Badger pour les applications impliquant des charges d’alimentation en éthylène dilué.
Les procédés en phase liquide nécessitent des zéolites à pores plus larges, par rapport à la ZSM-5 utilisée dans les procédés en phase vapeur, pour surmonter les limitations de diffusion. La régénération du catalyseur hors site est généralement recommandée en raison des temps de cycle du catalyseur prolongés, réduisant les besoins en équipement sur site et les coûts d’investissement.
Les deux principaux concédants de licence (ABB Lummus et Mobil-Badger) proposent des schémas de processus similaires (Figures 4 et 5).
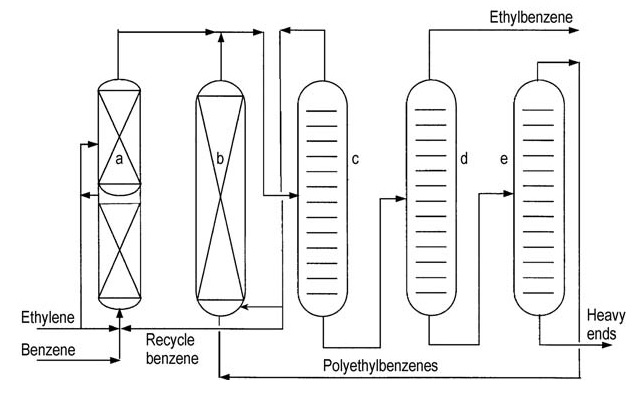
a) Réacteur d'alkylation ; b) Réacteur de transalkylation ; c) Colonne de benzène ; d) Colonne d'éthylbenzène ; e) Colonne de polyéthylbenzène
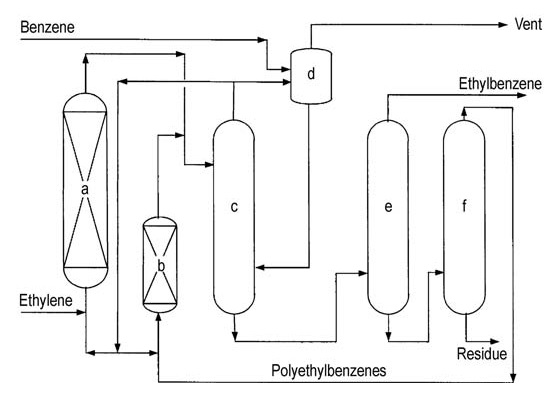
a) Réacteur d'alkylation ; b) Réacteur de transalkylation ; c) Colonne de benzène ; d) Colonne de gaz d'échappement ; e) Colonne d'éthylbenzène ; f) Colonne de polyéthylbenzène
L’éthylène est introduit dans un réacteur à lit fixe à plusieurs étages contenant un excès de benzène. Les températures du réacteur sont maintenues en dessous de la température critique du benzène (289 °C). Des pressions élevées d’environ 4 MPa sont nécessaires pour maintenir les gaz légers en solution.
L’excès de benzène est séparé de l’effluent du réacteur et recyclé vers l’étape d’alkylation.
Une série de colonnes de distillation purifie l’éthylbenzène brut. La distillation du benzène élimine l’excès de benzène pour le recyclage. La distillation de l’éthylbenzène sépare le produit souhaité et la distillation du polyéthylbenzène récupère les alkylbenzènes supérieurs et les polyéthylbenzènes des résidus.
Les alkylbenzènes supérieurs et les polyéthylbenzènes récupérés sont introduits dans un réacteur de transalkylation pour une conversion ultérieure. Les principales impuretés dans l’éthylbenzène final peuvent inclure des composés non aromatiques, du toluène et des alkylbenzènes supérieurs, provenant soit de l’alimentation soit des processus de production.
3.4. Production d’éthylbenzène par un procédé à base de zéolite en phase mixte
CDTech, une collaboration entre ABB Lummus Global et Chemical Research and Licensing, a proposé un procédé de production d’éthylbenzène à base de zéolite en phase mixte. La première usine commerciale a commencé à fonctionner en 1994 et, en 1999, trois usines de ce type étaient en service.
La caractéristique innovante de ce procédé est le réacteur d’alkylation, qui intègre un catalyseur à base de zéolite dans une colonne de distillation réactive.
L’éthylène (gaz) et le benzène (liquide) sont tous deux introduits dans la colonne de distillation réactive. Cette capacité permet au procédé d’utiliser des flux d’éthylène dilués produits pendant la distillation du vapocraqueur. Ce procédé peut également être adapté à une charge d’éthylène de qualité polymère.
Le flux du procédé est illustré à la Figure 6.
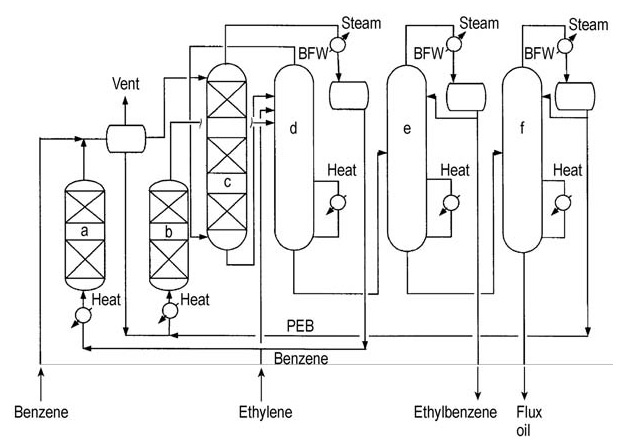
a) Réacteur de finition ; b) Transalkylateur ; c) Alkylateur ; d) Extracteur de benzène ; e) Colonne d'éthylbenzène ; f) Colonne de polyéthylbenzène. BFW = eau d'alimentation de la chaudière, PEB = polyéthylbenzène
L’alkylation et l’extraction du benzène se produisent simultanément dans la même colonne de distillation réactive. L’éthylène non converti et l’excès de benzène sont extraits comme produits de tête et dirigés vers un réacteur de finition pour un traitement ultérieur.
Le produit éthylbenzène est séparé du flux de fond dans la colonne de produits de tête. Le résidu restant est traité ultérieurement pour récupérer les polyéthylbenzènes transalkylables.
Les polyéthylbenzènes isolés sont ensuite envoyés dans un réacteur de transalkylation en phase liquide séparé avec l’excès de benzène. Le produit de cette étape de transalkylation est renvoyé vers le train de fractionnement pour une purification supplémentaire.
3.5. Séparation de l’éthylbenzène à partir de flux mixtes de C8
Moins de 1 % de la production mondiale d’éthylbenzène provient de la séparation de flux mixtes d’aromatiques de C8, qui se produit généralement parallèlement à la production de xylène à partir de reformat. Bien que des procédés d’adsorption comme l’EBEX d’UOP existent, la distillation reste la principale méthode de récupération de l’éthylbenzène à partir de cette source.
La difficulté de séparer l’éthylbenzène de ces flux nécessite un procédé connu sous le nom de superfractionnement. Mis au point par Cosden Oil & Chemical Company en 1957, il implique une série de trois colonnes de distillation, chacune comportant plus de 100 étages.
Plusieurs unités de superfractionnement ont été construites dans les années 1960 aux États-Unis, en Europe et au Japon. Cependant, la hausse des coûts de l’énergie et les coûts de construction élevés ont rendu cette méthode économiquement non compétitive. En conséquence, le superfractionnement a été largement abandonné au profit de méthodes plus efficaces.
4. Utilisations de l’éthylbenzène
Presque tout l’éthylbenzène produit commercialement est utilisé en interne dans les raffineries ou les usines chimiques pour la production de monomère de styrène, qui est un élément de base essentiel pour la production de polystyrène. Dans certains cas, l’éthylbenzène est coproduit avec de l’oxyde de propylène.
Moins de 1 % d’éthylbenzène est utilisé comme solvant de peinture ou comme intermédiaire pour la synthèse du diéthylbenzène, de l’acétophénone et de l’éthylanthraquinone.
5. Toxicologie de l’éthylbenzène
L’éthylbenzène est facilement absorbé après exposition par inhalation, par voie orale et par voie cutanée. Il subit un métabolisme primaire par oxydation de la chaîne latérale, avec des métabolites mineurs provenant de l’hydroxylation du cycle aromatique. Moins de 5 % sont excrétés sous forme inchangée dans l’urine sous forme de 2- et 4-éthylphénol.
Les principaux métabolites identifiés sont :
- 1-phényléthanol (métabolite urinaire majeur chez le rat)
- acide mandélique (métabolite urinaire majeur chez l’homme)
- acide phénylglyoxylique (métabolite urinaire majeur chez l’homme)
- acide benzoïque
- acide phénylacétique (métabolite mineur)
Les études expérimentales indiquent une faible toxicité aiguë chez les animaux. Les valeurs de DL50 orale chez le rat varient de 3,5 à 4,7 g/kg de poids corporel. Une valeur de DL50 cutanée d’environ 15 g/kg de poids corporel a été signalée.
L’exposition par inhalation chez le rat a entraîné une irritation des voies respiratoires à partir de 1 000 ppm. Des concentrations plus élevées ont provoqué une instabilité, une démarche chancelante et finalement une perte de connaissance et la mort à 5 000 ppm. Des volontaires humains exposés à 25 ppm pendant 7,5 heures ont signalé une légère irritation des muqueuses, qui est devenue plus prononcée à 100 ppm.
Un contact cutané répété avec de l’éthylbenzène non dilué peut entraîner un érythème, un œdème et une nécrose superficielle. Des effets similaires sont attendus chez l’homme en raison de la délipidation de la peau lors d’expositions répétées.
Des études examinant l’exposition à des doses répétées ont révélé que des effets indésirables significatifs chez les animaux ne se produisaient qu’à des doses relativement élevées d’éthylbenzène.
Aucun effet n’a été observé chez les rats à 100 ppm et les souris à 500 ppm au cours d’une étude d’inhalation de trois mois ; cependant, une augmentation du poids des poumons, des reins et du foie a été observée à partir de 250 ppm chez les rats et de 750 ppm chez les souris. Aucun changement histopathologique n’a été noté.
Des études d’inhalation de deux ans n’ont montré aucun effet chez les rats et les souris à 75 ppm. De légers changements ont été observés à 250 ppm, avec une augmentation des tumeurs hépatiques et pulmonaires chez les souris et des tumeurs rénales chez les rats mâles à 750 ppm (considérées comme spécifiques aux rats et non pertinentes pour les humains).
En ce qui concerne la toxicité reproductive de l’éthylbenzène, des résultats contradictoires ont été rapportés dans diverses études. Certaines études suggèrent une fœtotoxicité potentielle à des niveaux d’exposition élevés chez les souris et les rats gravides, mais aucun effet clair n’a été observé chez les lapins à 1 000 ppm avec une exposition quotidienne de 7 heures.
Le résultat global des différentes études suggère que l’éthylbenzène n’est pas un danger mutagène. Les données in vitro limitées disponibles pour la plupart des métabolites suggèrent également l’absence de potentiel génotoxique clair.
Une étude d’inhalation de deux ans a montré une augmentation de l’incidence des tumeurs chez les rats mâles (rein), les souris mâles (poumon) et les souris femelles (foie) au niveau d’exposition le plus élevé (750 ppm). Aucune tumeur liée à l’exposition n’a été observée dans une étude orale avec des rats et des souris exposés à des mélanges de xylène contenant 17 % d’éthylbenzène.
L’éthylbenzène n’est pas génotoxique in vivo, ce qui suggère un mode d’action non génotoxique pour les tumeurs observées dans l’étude d’inhalation à forte dose. La formation accrue de tumeurs peut être liée à la prolifération cellulaire induite par l’éthylbenzène dans les reins (rats) et les poumons/le foie (souris).
Des recherches plus approfondies sont nécessaires pour déterminer sa pertinence pour les humains et établir une limite d’exposition professionnelle sûre.
Le CIRC classe l’éthylbenzène comme « cancérogène possible pour les humains » (Groupe 2B) en raison de preuves suffisantes chez les animaux et de preuves insuffisantes chez les humains.
La commission allemande MAK classe l’éthylbenzène comme cancérogène de catégorie 3A en raison de données de cancérogénicité. Elle attend d’autres données mécanistiques avant d’établir une limite d’exposition professionnelle.
L’ACGIH classe l’éthylbenzène comme cancérogène A3 (« cancérogène confirmé pour les animaux avec une pertinence inconnue pour les humains ») et recommande une TLV-TWA de 100 ppm et une TLV-STEL de 125 ppm. Ils définissent également un indice d’exposition biologique (BEI) pour l’acide mandélique dans l’urine de 1,5 g/g de créatinine.
Dans l’UE, l’éthylbenzène est classé comme « hautement inflammable » (F) et « nocif par inhalation » (Xn).
Référence
- Éthylbenzène ; Encyclopédie de chimie industrielle d’Ullmann. – https://onlinelibrary.wiley.com/doi/10.1002/14356007.a10_035.pub2