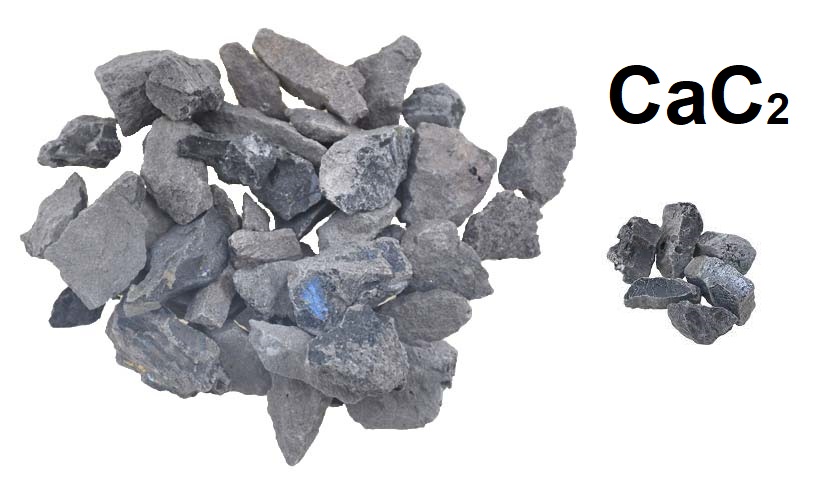
Le carbure de calcium, également connu sous le nom d’acétylure de calcium, est un composé cristallin gris-noir de formule chimique CaC2. Au contact de l’eau, il génère de l’acétylène, un gaz hautement inflammable autrefois largement utilisé pour l’éclairage et le soudage.
Parmi les carbures, le carbure de calcium s’impose comme le plus important sur le plan industriel (numéro CAS : 75-20-7). Il reste une matière essentiel de l’industrie du gaz de soudage à l’acétylène, en particulier dans les régions où les matières premières et l’énergie sont facilement disponibles et où le pétrole est rare.
Table des matières
Le carbure de calcium est fabriqué dans de nombreux pays comme précurseur de divers produits à base d’acétylène, notamment le poly(chlorure de vinyle) (PVC) et dans la production de cyanamide de calcium.
Il est également utilisé dans la désulfuration des métaux en fusion comme le fer et l’acier, ainsi que dans les fonderies, où il fait partie des additifs de traitement des métaux.
La composition chimique du carbure de calcium a été identifiée pour la première fois par Wöhler en 1862, obtenue par la réaction d’un alliage calcium-zinc et du charbon. Avant cela, plusieurs chercheurs avaient préparé le composé en laboratoire, souvent en utilisant des arcs électriques sur du charbon ou des produits à base de coke en présence de composés de calcium.
La fin du XIXe siècle a vu le développement de la production à l’échelle industrielle dans les fours électrothermiques. Moissan en France et Morehead et Willson aux États-Unis ont posé indépendamment les bases de ce saut technologique entre 1885 et 1895. Le premier four industriel opérationnel à carbure, construit par la Willson Aluminum Company à Spray, aux États-Unis, a vu le jour en 1895.
Bertolus proposa l’utilisation de courants électriques multiphasés pour les fours industriels en 1897. Helfenstein emboîta le pas en 1904 avec un four à courant triphasé équipé de trois électrodes. Ces premiers fours, d’une puissance allant de 3 000 à 7 500 kW, comportaient même des systèmes de récupération des gaz résiduaires (barrière Helfenstein). En un siècle, les fours de 40 MW sont devenus habituels.
Les grands fours électriques modernes, capables de traiter jusqu’à 60 MW, utilisent des électrodes Soderberg et sont entièrement fermés, permettant la récupération des sous-produits de monoxyde de carbone. Les progrès récents se sont concentrés sur le développement de fours fermés fiables de taille moyenne, mieux adaptés aux demandes du marché et aux matières premières disponibles.
Le procédé carbothermique, utilisé par BASF en Allemagne entre 1940 et 1960, offrait une voie alternative à la production de carbure de calcium, mais il a depuis été abandonné.
1. Propriétés physiques du carbure de calcium
Le carbure de calcium, CaC2, est un composé ionique binaire d’une masse molaire de 64,10 g/mol. Sous sa forme pure, il est incolore et inodore. Cependant, les matériaux de qualité technique présentent souvent diverses nuances de gris à noir brunâtre, parfois avec des teintes violettes ou rouge-brun, en raison d’impuretés.
L’odeur caractéristique de phosphine du carbure de calcium de qualité technique provient de traces de phosphure de calcium réagissant avec l’humidité.
Le carbure de calcium pur possède un point de fusion élevé de 2 160°C, se décomposant complètement au-dessus de 2 500°C. Il existe quatre modifications cristallographiques distinctes :
- Phase I : tétragonale, stable entre 25 et 440°C (dominante dans les carbures commerciaux)
- Phases II et III : symétrie inférieure, stable en dessous de 440°C
- Phase IV : cubique à faces centrées, stable au-dessus de 440 °C
La chaleur de transformation à 440°C est de 8,68 J/g. Notamment, le diagramme de phase CaC2-CaO présente un comportement eutectique simple, sans formation de composés ni de solutions solides à l’état solide. Les composants ne deviennent entièrement miscibles qu’au-dessus de la ligne du liquidus. Les impuretés contenues dans le carbure de qualité technique abaissent sa température de liquidus.
Le carbure de calcium a une capacité thermique spécifique moyenne de 1 047 J kg⁻¹ K⁻¹ entre 20 et 440°C et une chaleur de fusion de 1 470 J/g pour matière pure. Son enthalpie standard de formation à partir d’éléments à 298 K est de -59,4 kJ/mol et son entropie standard est de 70,3 J mol⁻¹ K⁻¹.
La conductivité électrique du carbure de calcium varie de 100 à 1 000 S m⁻¹ et dépend fortement de la pureté et de la température.
2. Propriétés chimiques du carbure de calcium
Le carbure de calcium, CaC2, subit une série de réactions chimiques importantes :
Synthèse du cyanamide calcique : Cette réaction exothermique (ΔH₂₉₈ = -289 kJ/mol) convertit le carbure de calcium et l’azote gazeux en cyanamide calcique et carbone : CaC₂ + N₂ → CaCN₂ + C.
Hydrolyse en acétylène : La réaction avec l’eau produit facilement de l’acétylène, de l’hydroxyde de calcium et de la chaleur (ΔH₂₉₈ = -128,4 kJ/mol) : CaC₂ + 2 H₂O → C₂H₂ + Ca(OH)₂.
La production efficace d’acétylène se produit en dessous de 300°C, avec un rendement de carbure de calcium pur de 346,89 L/kg (sec) à 0°C et 101,3 kPa (légèrement plus élevé à 15°C). C avec présence de vapeur d’eau). Les températures élevées produisent à la place de l’oxyde de calcium, de l’hydrogène et du dioxyde de carbone.
Réaction avec le soufre : Le carbure de calcium réagit avec le soufre dans le fer en fusion pour former du sulfure de calcium et libérer du carbone : CaC2 + [S]Fe → CaS + 2 [C]Fe
Hydrogénation : Sous pression, l’hydrogénation du carbure de calcium produit non seulement de l’hydrure de calcium et du méthane mais également d’autres hydrocarbures.
Le carbure de calcium se dissout dans divers sels fondus, permettant diverses réactions de réduction.
Électrolyse : L’électrolyse du carbure de calcium dissous dans des sels fondus produit du calcium à la cathode et du carbone à l’anode.
3. Production de carbure de calcium
Bien que la préparation de carbure de calcium pur présente un intérêt académique, sa production industrielle donne la priorité à des matériaux de qualité technique pour des applications pratiques. Cela repose en grande partie sur la réaction à haute température de la chaux vive (CaO) avec des sources carbonées comme le coke et l’anthracite :
CaO + 3 C → CaC2 + CO (ΔH₂₉₈ = +465 kJ/mol)
La vitesse de réaction ne devient significative qu’au-dessus de 1 600 °C. Cependant, dépasser 2000°C introduit des réactions secondaires indésirables, notamment :
CaC2 → Ca + 2 C
CaC2 + 2 CaO → 3 Ca + 2 CO
Par conséquent, les processus industriels fonctionnent dans la plage de 1 800 à 2 100 °C, produisant du carbure de calcium de qualité technique avec une teneur en CaC2 d’environ 80 % . Le reste comprend principalement du CaO, avec des impuretés supplémentaires comme SiO₂ et Al₂O₃ provenant des matières premières.
Les températures élevées sont cruciales pour la production de carbure de calcium, ce qui nécessite deux approches potentielles :
- Four à cuve électrothermique : fait fondre le matériau carboné avec du CaO dans un four court, introduisant directement de l’énergie électrique.
- Four à puits de combustion d’oxygène : brûle des matériaux carbonés avec de l’oxygène pur ou enrichi en présence de CaO.
Bien que cette dernière méthode offrait du gaz de synthèse comme sous-produit, elle a finalement été abandonnée après 50 ans en raison de la production moins coûteuse du même gaz à partir du pétrole. Aujourd’hui, toute la production commerciale de carbure de calcium utilise la première approche électrothermique.
3.1. Matières premières
Les matières premières pour la production de carbure de calcium, connues sous le nom de « fardeau » dans le four électrothermique, jouent un rôle crucial dans l’efficacité et la qualité du produit. Ces matériaux sont constitués de deux composants principaux : une source carbonée et un composant calcaire.
La taille, la résistance et la conductivité des particules ont un impact significatif sur les performances du four et la stabilité opérationnelle. Les fours ouverts plus petits offrent une flexibilité dans l’ajustement manuel ou mécanique de ces propriétés, tandis que les fours fermés de grande capacité nécessitent des spécifications plus strictes pour un fonctionnement sans surveillance.
Les matières volatiles et la teneur en cendres influencent l’efficacité de la réaction et la production de déchets. Les fours fermés modernes permettent d’obtenir des matériaux à grains fins en les injectant directement à travers des électrodes creuses. Les impuretés comme les oxydes métalliques peuvent provoquer des réactions secondaires indésirables et nécessitent une gestion prudente.
Source de carbone
- Coke : dérivé du charbon bitumineux ou du lignite, le coke est la principale matière carbonée utilisée dans le monde en raison de sa disponibilité et de ses propriétés appropriées. La taille des grains varie généralement de 3 à 25 mm, avec des fractions plus fines injectées via des électrodes. La teneur en humidité doit être inférieure à 2 % et la teneur en cendres inférieure à 15 % pour une production optimale.
- Autres options : L’anthracite et le coke de pétrole non calcinés peuvent être utilisés partiellement dans des fours fermés, mais nécessitent une calcination pour réduire les matières volatiles en dessous de 2 % pour la sole. utiliser. Le charbon de bois ne trouve d’application que dans les petits fours ouverts.
Composant contenant de la chaux
- Chaux vive : Le choix prédominant, avec de grands fours fermés nécessitant une granulométrie de 6 à 50 mm et une injection de fractions plus fines. La teneur en magnésium doit être inférieure à 2 % pour un fonctionnement efficace. La chaux doit être douce mais durable, réalisable dans des fours modernes, et avoir une teneur en CO2 inférieure à 2 %.
- Hydroxyde de calcium recyclé : ce sous-produit de la génération d’acétylène peut être utilisé comme matière première bon marché après granulation ou briquetage, mais l’accumulation d’impuretés limite son potentiel de recyclage.
Les déchets plastiques sont de plus en plus explorés en tant que source secondaire de carbone, avec des spécifications strictes sur la teneur en chlore (max. 12 %) en raison de sa vaporisation indésirable et de sa réaction avec le calcium.
Les tableaux 1 et 2 fournissent des exemples de compositions de matières premières typiques pour la production de carbure de calcium.
Matériel | Carbone fixe | Carbone volatil | Humidité | Soufre | Frêne |
---|---|---|---|---|---|
Coke métallurgique | 89,0 | 0,8 | 0,8 | 0,8 | 9.4 |
Anthracite | 80,0 | 6.0 | 8.0 | 0,8 | 6.0 |
Coke de pétrole | 81,6 | 9.0 | 8.0 | 1.9 | 0,3 |
Composant | Nouveau citron vert | Chaux recyclée |
---|---|---|
CaO totale | 93,8 | 89,0 |
CaO gratuit | 93,6 | - |
CaSO4 | 0,4 | - |
SiO2 | 1.3 | 2.9 |
Fe2O3 | 0,4 | 0,4 |
Al2O3 | 0,5 | 2.4 |
MgO | 0,8 | 0,8 |
CO2 | 2.7 | 3.0 |
P2O5 | 0,015 | 0,01 |
Perte au feu (CO2) | 0,5 | 0,5 |
3.2. Réduction électrothermique
Le mélange de matières premières pour la production de carbure de calcium subit un traitement à haute température dans un four électrique à arbre court. Les investigations suggèrent un mécanisme de réaction en deux étapes :
- Calcination : CaO + C → Ca + CO
- Formation de carbure : Ca + 2 C → CaC2
La zone de réaction principale à l’intérieur du four se trouve dans une phase CaC2 -CaO fondue. Cependant, l’interaction complexe entre le courant électrique, l’apport de chaleur, la température et les réactions chimiques reste imparfaitement comprise.
L’étape limitante implique probablement le transport du CaO dissous dans la masse fondue jusqu’à la surface des grains de coke, où se produit la formation de CaC2. Ce CaC2 nouvellement formé se dissout facilement dans la masse fondue.
Enfin, le carbure de calcium fondu est extrait du fond du four.
3.3. Fours
Les fours à carbure de calcium peuvent être classés en fonction de trois aspects clés :
- Alimentation électrique : Monophasée ou triphasée.
- Disposition des électrodes : Configurations en série, symétriques ou autres.
- Exclusion d’air : ouvert, semi-couvert ou fermé.
1. Fours monophasés
Développés en 1928, ces fours fonctionnent à courant élevé et basse tension, atteignant des facteurs de puissance allant jusqu’à 0,95. Cependant, ils sont moins efficaces et sont tombés en disgrâce par rapport aux conceptions triphasées.
2. Fours triphasés
Le type dominant aujourd’hui, classé par disposition des électrodes :
- Série : Offre des avantages en termes d’alimentation et de distribution, mais des limites en matière de récupération de gaz et de consommation d’énergie.
- Symétrique : Conception hautes performances avec des facteurs de puissance équilibrés et des zones fondues qui se chevauchent à une puissance plus élevée.
3. Fours semi-couverts
Les premiers fours évacuaient directement le CO, provoquant une pollution. Les conceptions modernes utilisent des hottes de collecte de gaz, bien que les fours fermés offrent le meilleur contrôle environnemental.
4. Fours fermés
Ces fours modernes permettent une récupération de gaz à 100 % et un impact environnemental minimal. Les composants clés incluent :
- Foyer : Construit en acier et en matériaux réfractaires pour résister à des températures élevées.
- Électrodes : les électrodes Soderberg sont préférées pour leur rentabilité et leur fonctionnement continu. Les électrodes creuses permettent l’injection directe des matières premières.
- Alimentation : Transformateurs avec refroidissement par huile et sortie contrôlable pour gérer les fluctuations.
- Diagramme de puissance : Représente l’interaction complexe des résistances et des réactances au sein du four.
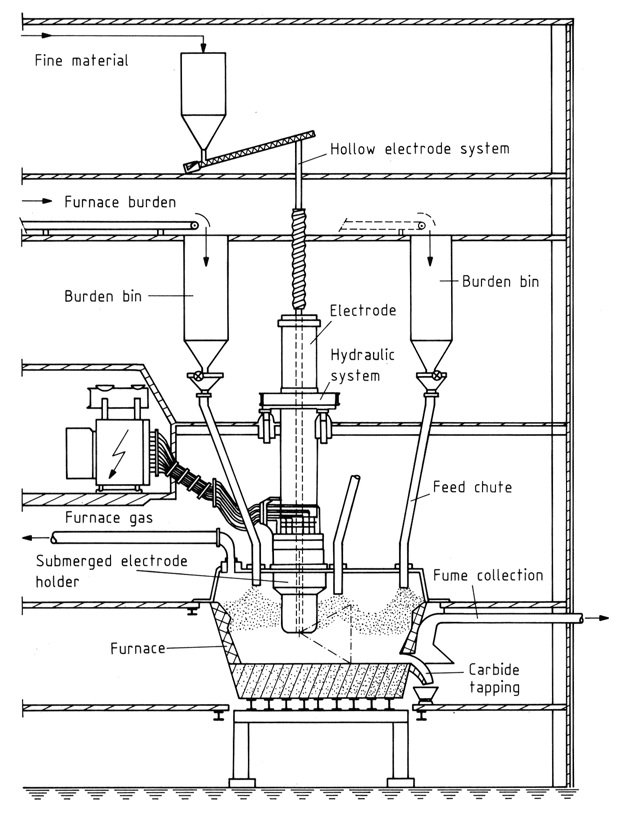
Contrôle et fonctionnement
Les fours triphasés nécessitent un contrôle d’impédance en ajustant la profondeur d’immersion des électrodes pour gérer la puissance et la résistance du four. Les capots fermés peuvent permettre la manipulation des goulottes d’alimentation pour réguler davantage la résistance.
3.4. Processus industriel
La production de carbure de calcium commence par une base de coke grossier déposée dans le four. Les électrodes sont méticuleusement descendues vers le coke jusqu’à ce que des arcs électriques signalent un contact.
À mesure que le coke atteint la chaleur rouge, le fond du four est progressivement alimenté en charge et la puissance est progressivement augmentée pour correspondre à l’augmentation de la température.
Une alimentation constante de la charge est essentielle pour un fonctionnement optimal du four. Des variations mineures de composition peuvent être atténuées grâce à l’ajout de chaux, nécessitant une immersion plus profonde de l’électrode en raison de la plus faible conductivité de la chaux.
Une hauteur d’électrode excessive risque la formation de carbure dans les couches supérieures de la charge, conduisant potentiellement à des « giclées » de fusion dangereuses. Le maintien de la perméabilité aux gaz au sein du matériau solide est essentiel pour une production cohérente.
La pression de la hotte du four doit être méticuleusement équilibrée avec la pression atmosphérique pour empêcher l’intrusion d’oxygène ou la fuite de monoxyde de carbone. Les installations de fours à grande échelle utilisent souvent des salles de contrôle centralisées pour un fonctionnement efficace et une surveillance complète des paramètres environnementaux.
Le taraudage consiste soit à ouvrir mécaniquement le four, soit à utiliser un arc électrique pour créer un trou de coulée. Une électrode cuite dédiée facilite la fusion du carbure, qui s’écoule à des températures allant de 1 700 à 2 100 °C selon la pureté, dans des poches en fonte refroidies spécialement conçues.
En raison de son point de fusion élevé et de sa perte de chaleur rapide, le carbure de qualité technique (80 % CaC2) se solidifie rapidement, nécessitant un entretien continu du trou de coulée avec des tiges d’acier.
Les rideaux de chaînes, les grillages et les boucliers en acier protègent les opérateurs des gaz chauds, de la poussière et des projections de carbure potentiellement dangereuses pendant le processus de taraudage.
Un équipement de protection spécialisé, notamment des manteaux ignifuges recouverts d’aluminium, des lunettes noires et des visières de protection, est obligatoire pour tout le personnel impliqué dans les opérations de taraudage.
Les systèmes d’extraction de fumée éliminent efficacement les particules d’aérosol nocives, réduisant ainsi l’impact environnemental.
Les manipulateurs hydrauliques modernes équipés d’outils interchangeables ont révolutionné les procédures de taraudage, minimisant le besoin d’intervention humaine directe et améliorant la sécurité.
La réduction des impuretés comme Fe2O3 et SiO2 par le carbone produit du ferrosilicium qui, en raison de sa densité plus élevée, se dépose sous la masse fondue de carbure et s’écoule généralement lors du taraudage.
Cependant, son point de fusion plus bas par rapport au carbure nécessite une vigilance constante et des mesures préventives pour éviter les fuites par les fissures du revêtement du four.
4. Utilisations du carbure de calcium
Le carbure de calcium est utilisé dans la production d’acétylène, la réaction avec l’azote pour former du cyanamide de calcium et la désulfuration des métaux chauds.
Bien que son utilisation comme précurseur de produits chimiques lourds ait diminué en raison de la domination des produits pétrochimiques depuis les années 1960, l’acétylène dérivé du carbure de calcium reste important dans le soudage au gaz. Son adaptabilité et sa portabilité le rendent indispensable pour des tâches telles que la construction de pipelines, même au milieu des progrès des techniques d’assemblage des matériaux.
L’acétylène continue de trouver des applications de niche dans la synthèse de produits chimiques spécifiques, tels que butynediol pour les plastiques et les fibres, et noir d’acétylène pour les piles sèches.
La réactivité du carbure de calcium avec le soufre en fait un outil précieux en métallurgie. Des normes strictes de qualité de l’acier exigent une teneur minimale en soufre et une désulfuration au carbure de calcium avant le convertisseur de production d’acier, qui s’avère être la méthode la plus économique.
L’injection de carbure de calcium finement broyé (< 100 mm) dans le métal en fusion réduit efficacement la teneur en soufre, généralement de 0,2 % à 0,001 %. Les combinaisons de carbure de calcium et de magnésium sont de plus en plus explorées pour améliorer la réactivité du métal chaud.
Dans les pratiques de fonderie, le carbure de calcium à gros grains, souvent associé à des additifs comme le spath fluor, est utilisé dans la désulfuration. Le mélange est agité dans la poche après le coulage et avant la coulée, contribuant ainsi à améliorer la qualité du métal.
5. Toxicologie du carbure de calcium
Le carbure de calcium est classé comme un irritant oculaire grave et un irritant cutané, avec un faible potentiel de sensibilisation.
Le carbure de calcium de qualité commerciale peut présenter des dommages aigus par inhalation en raison de ses propriétés corrosives/irritantes.
Des données limitées sont disponibles pour le carbure de calcium lui-même, mais des inquiétudes sont soulevées par certains composants traces :
- Phosphine : des preuves génotoxiques existent, mais sa faible concentration en carbure de calcium (< 0,1 %) minimise le risque.
- Arsenic : bien que présent à < 0,1%, ce cancérigène potentiel peut générer de l’arsine au contact de l’eau. Cependant, les critères actuels du CLP ne nécessitent pas une classification comme cancérogène.
Compte tenu des faibles niveaux d’arsenic et de sa conversion limitée en arsine, la classification comme cancérogène n’est pas justifiée.
En raison de sa dégradation rapide dans l’eau, l’écotoxicité du composé pur est négligeable.
Des études sur les poissons, les daphnies et les algues donnent un aperçu de la toxicité des produits de dégradation et des constituants mineurs.
La CL50 élevée pour le poisson (> 50 mg/L) et la CE50 pour la Daphnia (4,42 mg/L) reflètent probablement la toxicité du sulfure d’hydrogène, produit à partir de l’impureté sulfure de calcium.
Dans l’ensemble, les études de biodégradation suggèrent des propriétés facilement biodégradables pour le carbure de calcium et ses produits de dégradation.
Référence
- Calcium Carbide; Ullmann’s Encyclopedia of Industrial Chemistry. – https://onlinelibrary.wiley.com/doi/10.1002/14356007.a04_533.pub2