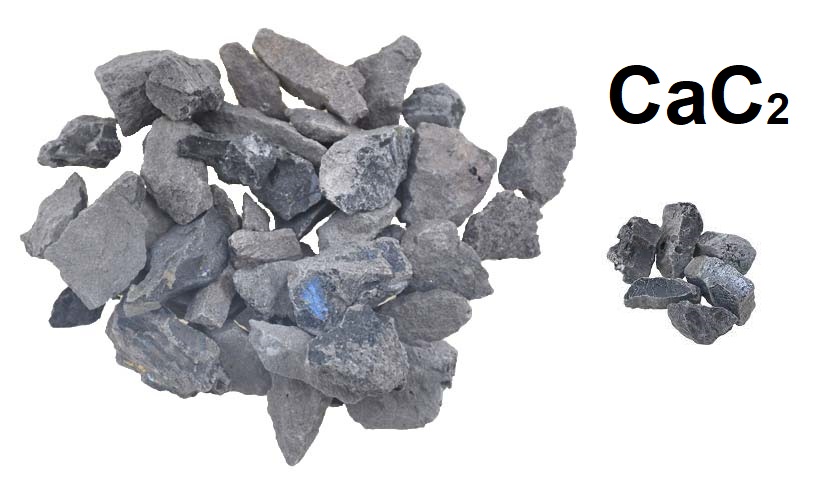
Cos’è il carburo di calcio?
Il carburo di calcio, noto anche come acetiluro di calcio, è un composto cristallino grigio-nero con formula chimica CaC2. A contatto con l’acqua genera acetilene, un gas altamente infiammabile un tempo ampiamente utilizzato per l’illuminazione e la saldatura.
Tra i carburi, il carburo di calcio si distingue come il più significativo a livello industriale. Rimane la spina dorsale dell’industria del gas di saldatura con acetilene, in particolare nelle regioni in cui le materie prime e l’energia sono facilmente disponibili e il petrolio è scarso.
Sommario
Il carburo di calcio viene prodotto in numerosi paesi come precursore di vari prodotti a base di acetilene, in particolare il polivinilcloruro (PVC) e nella produzione di calciocianammide.
Trova inoltre impiego nella desolforazione di metalli fusi come ferro e acciaio, nonché nelle pratiche di fonderia, dove fa parte degli additivi per il trattamento dei metalli.
La composizione chimica del carburo di calcio fu identificata per la prima volta da Wöhler nel 1862, ottenuta dalla reazione di una lega di calcio-zinco e carbone. Prima di allora, diversi ricercatori avevano preparato il composto in laboratorio, spesso utilizzando archi elettrici su prodotti di carbone o coke in presenza di composti di calcio.
La fine del XIX secolo vide lo sviluppo della produzione su scala industriale in forni elettrotermici. Moissan in Francia e Morehead e Willson negli Stati Uniti gettarono le basi indipendentemente per questo balzo tecnologico tra il 1885 e il 1895. Il primo forno industriale al carburo operativo, costruito dalla Willson Aluminum Company a Spray, negli Stati Uniti, emerse nel 1895.
Bertolus propose l’uso di correnti elettriche multifase per forni industriali nel 1897. Helfenstein seguì l’esempio nel 1904 con un forno a corrente trifase dotato di tre elettrodi. Questi primi forni, che vantavano capacità che andavano da 3000 a 7500 kW, incorporavano persino sistemi di recupero dei gas di scarico (barriera di Helfenstein). Nel giro di un secolo, i forni da 40 MW divennero comuni.
I moderni grandi forni elettrici, in grado di gestire fino a 60 MW, impiegano elettrodi Soderberg e sono completamente chiusi, consentendo il recupero dei sottoprodotti del monossido di carbonio. I recenti progressi si sono concentrati sullo sviluppo di forni chiusi affidabili e di medie dimensioni, più adatti alle richieste del mercato e alle materie prime disponibili.
Il processo carbotermico, impiegato dalla BASF in Germania tra il 1940 e il 1960, forniva un metodo alternativo per la produzione di carburo di calcio, ma nel frattempo è stato abbandonato.
1. Proprietà fisiche del carburo di calcio
Il carburo di calcio, CaC2, è un composto ionico binario con una massa molare di 64,10 g/mol. Nella sua forma pura, è incolore e inodore. Tuttavia, il materiale di grado tecnico spesso presenta varie tonalità di grigio fino al nero brunastro, occasionalmente con tonalità viola o rosso-marrone, a causa delle impurità.
Il caratteristico odore di fosfina del carburo di calcio di grado tecnico deriva da tracce di fosfuro di calcio che reagisce con l’umidità.
Il carburo di calcio puro possiede un punto di fusione elevato di 2160 °C, decomponendosi completamente sopra i 2500 °C. Esistono quattro distinte modifiche cristallografiche:
- Fase I: tetragonale, stabile tra 25 e 440 °C (dominante nel carburo commerciale)
- Fasi II e III: simmetria inferiore, stabile al di sotto di 440 °C
- Fase IV: cubico a facce centrate, stabile al di sopra di 440 °C
Il calore di trasformazione a 440 °C è 8,68 J/g. In particolare, il diagramma di fase CaC2-CaO mostra un semplice comportamento eutettico, senza formazione di composti o soluzioni solide allo stato solido. I componenti diventano completamente miscibili solo al di sopra della linea di liquidus. Le impurità nel carburo di grado tecnico abbassano la sua temperatura di liquidus.
Il carburo di calcio ha una capacità termica specifica media di 1047 J kg⁻¹ K⁻¹ tra 20 e 440 °C e un calore di fusione di 1470 J/g per materiale puro. La sua entalpia standard di formazione da elementi a 298 K è -59,4 kJ/mol e l’entropia standard è 70,3 J mol⁻¹ K⁻¹.
La conduttività elettrica del carburo di calcio varia da 100 a 1000 S.m⁻¹ e dipende fortemente dalla purezza e dalla temperatura.
2. Proprietà chimiche del carburo di calcio
Il carburo di calcio, CaC2, subisce una serie di importanti reazioni chimiche:
Sintesi di calciocianammide: questa reazione esotermica (ΔH298 = -289 kJ/mol) converte il carburo di calcio e l’azoto gassoso in calciocianammide e carbonio: CaC2 + N2 → CaCN2 + C.
Idrolisi ad acetilene: la reazione con acqua produce facilmente acetilene, idrossido di calcio e calore (ΔH298 = -128,4 kJ/mol): CaC2 + 2 H2O → C2H2 + Ca(OH)2.
Una produzione efficiente di acetilene avviene al di sotto dei 300 °C, con carburo di calcio puro che produce 346,89 L/kg (secco) a 0 °C e 101,3 kPa (leggermente superiore a 15 °C con vapore acqueo presente). Le alte temperature producono invece ossido di calcio, idrogeno e anidride carbonica.
Reazione con lo zolfo: il carburo di calcio reagisce con lo zolfo nel ferro fuso per formare solfuro di calcio e rilasciare carbonio: CaC2 + [S]Fe → CaS + 2 [C]Fe.
Idrogenazione: sotto pressione, l’idrogenazione del carburo di calcio produce non solo idruro di calcio e metano, ma anche altri idrocarburi.
il carburo di calcio si dissolve in vari sali fusi, consentendo diverse reazioni di riduzione.
Elettrolisi: l’elettrolisi del carburo di calcio disciolto in sali fusi produce calcio al catodo e carbonio all’anodo.
3. Produzione di carburo di calcio
Mentre la preparazione del carburo di calcio puro ha un interesse accademico, la sua produzione industriale dà priorità al materiale di grado tecnico per applicazioni pratiche. Ciò si basa in gran parte sulla reazione ad alta temperatura della calce viva (CaO) con fonti carboniose come coke e antracite:
CaO + 3 C → CaC2 + CO (ΔH298 = +465 kJ/mol)
La velocità di reazione diventa significativa solo oltre i 1600 °C. Tuttavia, superando i 2000 °C si introducono reazioni collaterali indesiderate, in particolare:
CaC2 → Ca + 2 C
CaC2 + 2 CaO → 3 Ca + 2 CO
Pertanto, i processi industriali operano nell’intervallo 1800-2100 °C, producendo carburo di calcio di grado tecnico con un contenuto di CaC2 di circa l’80%. Il resto è composto principalmente da CaO, con impurità aggiuntive come SiO2 e Al2O3 dalle materie prime.
Le alte temperature sono cruciali per la produzione di carburo di calcio, e richiedono due possibili approcci:
- Forno a pozzo elettrotermico: fonde il materiale carbonioso con CaO in un forno corto, introducendo direttamente energia elettrica.
- Forno a pozzo con combustione di ossigeno: brucia il materiale carbonioso con ossigeno puro o arricchito in presenza di CaO.
Mentre quest’ultimo metodo offriva gas di sintesi come sottoprodotto, fu infine abbandonato dopo 50 anni a causa della produzione più economica dello stesso gas dal petrolio. Oggi, tutta la produzione commerciale di carburo di calcio utilizza il primo approccio elettrotermico.
3.1. Materie prime
Le materie prime per la produzione di carburo di calcio, note come “carico” nel forno elettrotermico, svolgono un ruolo cruciale nell’efficienza e nella qualità del prodotto. Questi materiali sono costituiti da due componenti principali: una fonte carboniosa e un componente contenente calce.
Dimensioni delle particelle, resistenza e conduttività influiscono in modo significativo sulle prestazioni del forno e sulla stabilità operativa. I forni aperti più piccoli offrono flessibilità nella regolazione manuale o meccanica di queste proprietà, mentre i forni chiusi ad alta capacità richiedono specifiche più severe per il funzionamento senza supervisione.
I volatili e il contenuto di ceneri influenzano l’efficienza della reazione e la generazione di rifiuti. I moderni forni chiusi consentono materiali a grana fine iniettandoli direttamente attraverso elettrodi cavi. Le impurità come gli ossidi metallici possono causare reazioni collaterali indesiderate e richiedono una gestione attenta.
Fonte di carbonio
- Coke: derivato dal carbone bituminoso o dalla lignite, il coke è il principale materiale carbonioso utilizzato a livello globale per la sua disponibilità e le sue proprietà adatte. La granulometria varia in genere da 3 a 25 mm, con frazioni più fini iniettate tramite elettrodi. Il contenuto di umidità deve essere inferiore al 2% e il contenuto di ceneri inferiore al 15% per una produzione ottimale.
- Altre opzioni: l’antracite non calcinata e il coke di petrolio possono essere utilizzati parzialmente in forni chiusi, ma richiedono la calcinazione per ridurre i volatili al di sotto del 2% per uso esclusivo. Il carbone vegetale trova applicazione solo in piccole fornaci aperte.
Componente contenente calce
- Calce viva: La scelta predominante, con grandi fornaci chiuse che richiedono una granulometria di 6-50 mm e l’iniezione di frazioni più fini. Il contenuto di magnesio dovrebbe essere inferiore al 2% per un funzionamento efficiente. La calce deve essere morbida ma resistente, ottenibile tramite forni moderni e avere un contenuto di CO2 inferiore al 2%.
- Idrossido di calcio riciclato: questo sottoprodotto della generazione di acetilene può essere utilizzato come materia prima economica dopo la granulazione o la bricchettatura, ma l’accumulo di impurità ne limita il potenziale di riciclaggio.
I rifiuti di plastica vengono sempre più esplorati come fonte di carbonio secondaria, con specifiche rigorose sul contenuto di cloro (max. 12%) a causa della sua indesiderata vaporizzazione e reazione con il calcio.
Le tabelle 1 e 2 forniscono esempi di tipiche composizioni di materie prime per la produzione di carburo di calcio.
Materiale | Carbonio fisso | Carbonio volatile | Umidità | Zolfo | Cenere |
---|---|---|---|---|---|
Coke metallurgico | 89,0 | 0,8 | 0,8 | 0,8 | 9,4 |
Antracite | 80,0 | 6.0 | 8.0 | 0.8 | 6.0 |
Coke di petrolio | 81.6 | 9.0 | 8.0 | 1.9 | 0.3 |
Componente | Calce nuova | Calce riciclata |
---|---|---|
CaO totale | 93,8 | 89,0 |
CaO libero | 93,6 | - |
CaSO4 | 0,4 | - |
SiO2 | 1,3 | 2,9 |
Fe2O3 | 0,4 | 0,4 |
Al2O3 | 0,5 | 2,4 |
MgO | 0,8 | 0,8 |
CO2 | 2,7 | 3.0 |
P2O5 | 0.015 | 0.01 |
Perdita all'accensione (CO2) | 0.5 | 0.5 |
3.2. Riduzione elettrotermica
La miscela di materie prime per la produzione di carburo di calcio viene sottoposta a lavorazione ad alta temperatura in un forno elettrico a albero corto. Le indagini suggeriscono un meccanismo di reazione in due fasi:
- Calcinazione: CaO + C → Ca + CO
- Formazione del carburo: Ca + 2 C → CaC2
La zona di reazione primaria all’interno del forno si trova in una fase fusa CaC2-CaO. Tuttavia, la complessa interazione di corrente elettrica, fornitura di calore, temperatura e reazioni chimiche rimane poco compresa.
La fase limitante la velocità probabilmente comporta il trasporto di CaO disciolto nella fusione alla superficie del grano di coke, dove avviene la formazione di CaC2. Questo CaC2 appena formato si dissolve facilmente nella massa fusa.
Infine, il carburo di calcio fuso viene estratto dal fondo del forno.
3.3. Forni
I forni al carburo di calcio possono essere classificati in base a tre aspetti chiave:
- Alimentazione elettrica: monofase o trifase.
- Disposizione degli elettrodi: configurazioni seriali, simmetriche o di altro tipo.
- Esclusione dell’aria: aperta, semicoperta o chiusa.
1. Forni monofase
Sviluppati nel 1928, questi forni funzionano ad alta corrente e bassa tensione, raggiungendo fattori di potenza fino a 0,95. Tuttavia, sono meno efficienti e sono caduti in disgrazia rispetto ai modelli trifase.
2. Forni trifase
Il tipo dominante oggi, classificato in base alla disposizione degli elettrodi:
- Seriale: Offre vantaggi nell’alimentazione e nella distribuzione, ma limitazioni nel recupero del gas e nel consumo di energia.
- Simmetrico: Design ad alte prestazioni con fattori di potenza bilanciati e zone fuse sovrapposte a potenza più elevata.
3. Forni semi-coperti
I primi forni scaricavano direttamente la CO, causando inquinamento. I modelli moderni impiegano cappe di raccolta del gas, sebbene i forni chiusi offrano il miglior controllo ambientale.
4. Forni chiusi
Questi forni moderni forniscono il recupero del gas al 100% e un impatto ambientale minimo. I componenti chiave includono:
- Focolare: costruito con acciaio e materiali refrattari per resistere alle alte temperature.
- Elettrodi: gli elettrodi Soderberg sono preferiti per la loro convenienza e il funzionamento continuo. Gli elettrodi cavi consentono l’iniezione diretta delle materie prime.
- Alimentazione: trasformatori con raffreddamento a olio e uscita controllabile per gestire le fluttuazioni.
- Diagramma di potenza: rappresenta la complessa interazione di resistenze e reattanze all’interno del forno.
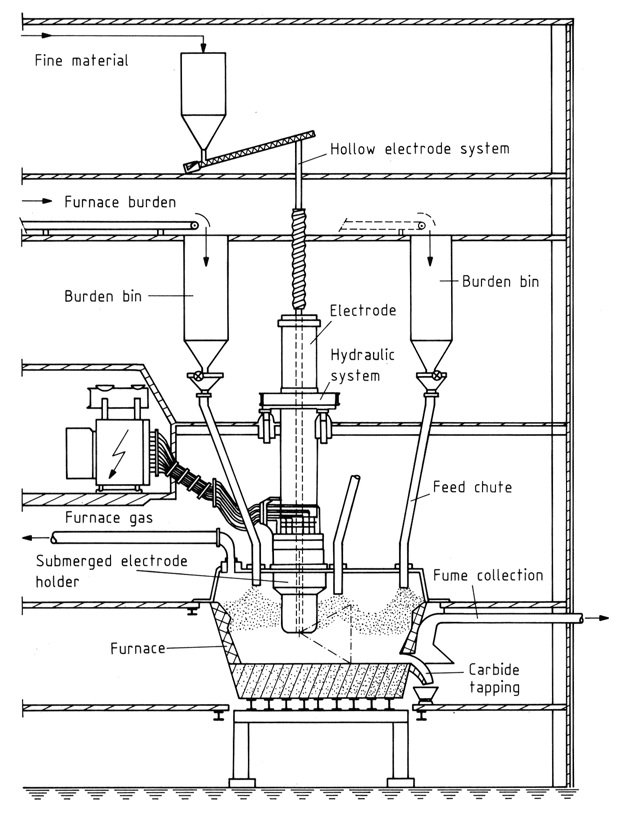
Controllo e funzionamento
I forni trifase richiedono il controllo dell’impedenza regolando la profondità di immersione dell’elettrodo per gestire potenza e resistenza del forno. Le cappe chiuse possono consentire la manipolazione degli scivoli di alimentazione per regolare ulteriormente la resistenza.
3.4. Processo industriale
La produzione di carburo di calcio inizia con una base di coke grossolano stratificato all’interno del forno. Gli elettrodi vengono meticolosamente abbassati verso il coke fino a quando gli archi elettrici segnalano il contatto. Quando il coke raggiunge il calore rosso, il fondo del forno viene gradualmente alimentato con il carico e la potenza viene aumentata gradualmente per adattarsi alla temperatura crescente.
Un’alimentazione costante del carico è essenziale per il funzionamento ottimale del forno. Piccole variazioni di composizione possono essere mitigate tramite aggiunte di calce, che richiedono un’immersione più profonda dell’elettrodo a causa della minore conduttività della calce.
Un’altezza eccessiva dell’elettrodo rischia la formazione di carburo negli strati superiori del carico, portando potenzialmente a pericolosi “spruzzi” di fusione. Mantenere la permeabilità al gas all’interno del materiale solido è essenziale per una produzione costante.
La pressione della cappa della fornace deve essere meticolosamente bilanciata con la pressione atmosferica per impedire l’intrusione di ossigeno o la fuoriuscita di monossido di carbonio. Le configurazioni di fornaci su larga scala spesso impiegano sale di controllo centralizzate per un funzionamento efficiente e un monitoraggio completo dei parametri ambientali.
La spillatura comporta l’apertura meccanica della fornace o l’uso di un arco elettrico per creare un foro di spillatura. Un elettrodo cotto dedicato facilita la fusione del carburo, che scorre a temperature comprese tra 1700 e 2100 °C a seconda della purezza, in siviere in ghisa raffreddate appositamente progettate.
Grazie al suo elevato punto di fusione e alla rapida perdita di calore, il carburo di grado tecnico (80% CaC2) si solidifica rapidamente, rendendo necessaria una manutenzione continua del foro di spillatura con barre di acciaio.
Tende a catena, reti metalliche e scudi in acciaio proteggono gli operatori da gas caldi, polvere e schizzi di carburo potenzialmente pericolosi durante il processo di spillatura. Equipaggiamento protettivo specializzato, tra cui camici ignifughi rivestiti in alluminio, occhiali scuri e visiere protettive, è obbligatorio per tutto il personale coinvolto nelle operazioni di spillatura.
I sistemi di estrazione dei fumi rimuovono efficacemente le particelle di aerosol nocive, riducendo l’impatto ambientale.
I moderni manipolatori idraulici dotati di utensili intercambiabili hanno rivoluzionato le procedure di spillatura, riducendo al minimo la necessità di un coinvolgimento umano diretto e migliorando la sicurezza.
La riduzione di impurità come Fe2O3 e SiO2 mediante carbonio produce ferrosilicio, che, a causa della sua maggiore densità, si deposita sotto la fusione di carburo e in genere fuoriesce durante la spillatura. Tuttavia, il suo punto di fusione più basso rispetto al carburo richiede una vigilanza costante e misure preventive per evitare perdite attraverso crepe nel rivestimento del forno.
4. Utilizzi del carburo di calcio
Il carburo di calcio viene utilizzato nella produzione di acetilene, nella reazione con l’azoto per formare calciocianammide e nella desolforazione di metalli caldi.
Sebbene il suo utilizzo come precursore per prodotti chimici pesanti sia diminuito a causa del predominio dei prodotti petrolchimici a partire dagli anni ’60, l’acetilene derivato dal carburo di calcio rimane importante nella saldatura a gas. La sua adattabilità e portabilità lo rendono indispensabile per attività come la costruzione di condotte, anche in mezzo ai progressi nelle tecniche di giunzione dei materiali.
L’acetilene continua a trovare applicazioni di nicchia nella sintesi di sostanze chimiche specifiche, come il butynediolo per materie plastiche e fibre e l’acetilene nero per batterie a secco.
La reattività del carburo di calcio con lo zolfo lo rende uno strumento prezioso nella metallurgia. Gli standard rigorosi di qualità dell’acciaio richiedono un contenuto minimo di zolfo e la desolforazione con carburo di calcio prima del convertitore di produzione dell’acciaio si rivela il metodo più economico.
L’iniezione di carburo di calcio finemente macinato (< 100 mm) nel metallo fuso riduce efficacemente il contenuto di zolfo, in genere dallo 0,2% fino allo 0,001%. Le combinazioni di carburo di calcio con magnesio sono sempre più esplorate per migliorare la reattività all’interno del metallo caldo.
Nelle pratiche di fonderia, il carburo di calcio a grana grossa, spesso combinato con additivi come la fluorite, trova impiego nella desolforazione. La miscela viene mescolata nella siviera dopo la spillatura e prima della fusione, contribuendo a migliorare la qualità del metallo.
5. Tossicologia del carburo di calcio
Il carburo di calcio è classificato come grave irritante per gli occhi e per la pelle, con basso potenziale di sensibilizzazione.
Il carburo di calcio di qualità commerciale può causare gravi danni da inalazione a causa delle sue proprietà corrosive/irritanti.
Sono disponibili dati limitati sul carburo di calcio stesso, ma alcuni componenti in tracce sollevano preoccupazioni:
- Fosfina: esistono prove genotossiche, ma la sua bassa concentrazione nel carburo di calcio (< 0,1%) riduce al minimo il rischio.
- Arsenico: sebbene presente a < 0,1%, questo potenziale cancerogeno può generare arsina a contatto con l’acqua. Tuttavia, gli attuali criteri CLP non richiedono la classificazione come cancerogeno.
In base ai bassi livelli di arsenico e alla sua limitata conversione in arsina, la classificazione come cancerogeno non è giustificata.
A causa della sua rapida decomposizione in acqua, l’ecotossicità del composto puro è trascurabile.
Studi su pesci, Daphnia e alghe forniscono informazioni sulla tossicità dei prodotti di decomposizione e dei costituenti minori.
L’elevata LC50 per i pesci (>50 mg/L) e EC50 per Daphnia (4,42 mg/L) riflette probabilmente la tossicità dell’idrogeno solforato, prodotto dall’impurità solfuro di calcio.
Nel complesso, gli studi sulla biodegradazione suggeriscono proprietà facilmente biodegradabili per il carburo di calcio e i suoi prodotti di decomposizione.
Riferimento
- Calcium Carbide; Ullmann’s Encyclopedia of Industrial Chemistry. – https://onlinelibrary.wiley.com/doi/10.1002/14356007.a04_533.pub2