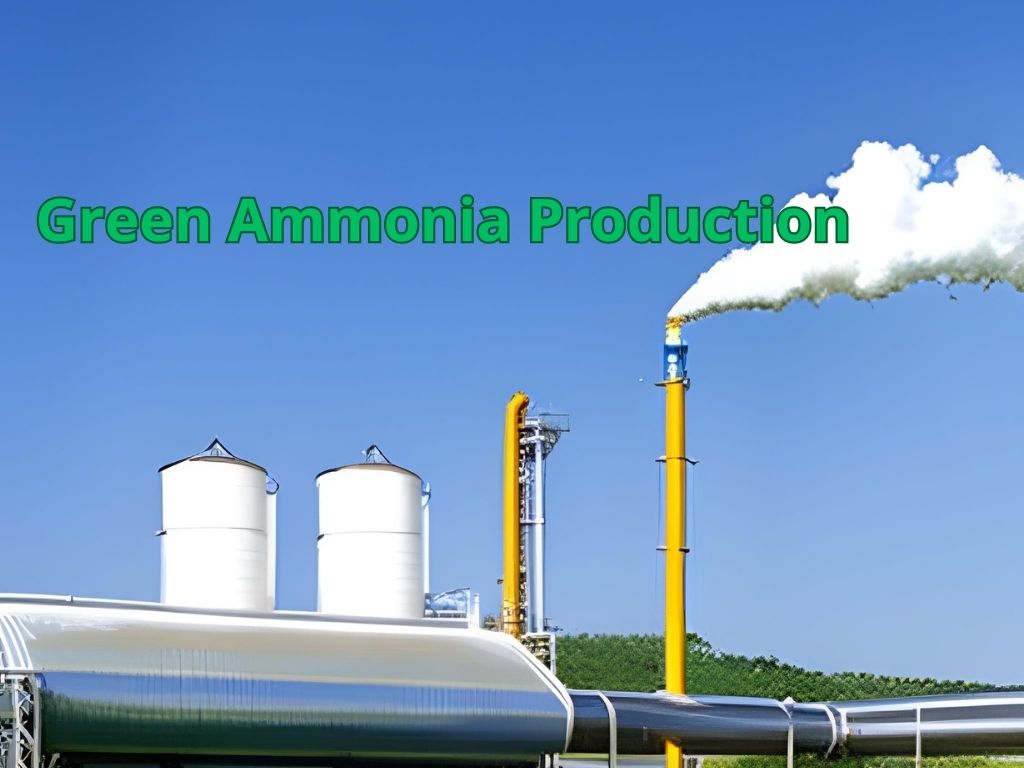
Unter grünem Ammoniak versteht man Ammoniak, das produziert wird, ohne wesentlich zu den Kohlenstoffemissionen beizutragen. Dies kann durch den Einsatz traditioneller Methoden der Ammoniaksynthese in Verbindung mit der elektrolysebasierten Wasserstofferzeugung oder durch den Einsatz alternativer Techniken zur Ammoniaksynthese erreicht werden.
Inhaltsverzeichnis
Bevor in den 1950er Jahren kostengünstiges Erdgas allgemein verfügbar war, war die Ammoniaksynthese auf Elektrolysebasis weit verbreitet und wurde nur von der Kohlevergasungstechnologie übertroffen. Als alternativer Ansatz zur dezentralen Synthese von grünem Ammoniak bietet darüber hinaus die biomassebasierte Wasserstoffproduktion in Kombination mit Kohlenstoffabscheidung und -speicherung (CCS) Potenzial.
Die erste Umsetzung des auf Elektrolyse basierenden Haber-Bosch-Verfahrens geht auf die 1920er Jahre zurück und zeichnete sich durch einen Energieverbrauch von etwa 46–48 Gigajoule pro Tonne Ammoniak (GJ/tNH3) aus.
Es lassen sich vier Schlüsselfaktoren für die Produktion von grünem Ammoniak identifizieren: die Nachhaltigkeit der verwendeten Rohstoffe, ein geringer Energieverbrauch, die Fähigkeit, die Produktion modular zu skalieren, und die Wirtschaftlichkeit.
Theoretischen Berechnungen zufolge beträgt der Mindestenergiebedarf für die Synthese von Ammoniak aus Luft und Wasser 22,5 GJ/tNH3.
1. Elektrolysebasierte Wasserstoffproduktion
Die Elektrolyse ist die wichtigste Methode zur Synthese von grünem Wasserstoff. Verschiedene kommerziell erhältliche Elektrolysetechnologien können in die Ammoniaksynthese integriert werden, darunter alkalische Elektrolyse und Protonenaustauschmembran-Elektrolyse (PEM).
Die Festoxidelektrolyse (SOE) befindet sich derzeit in der Demonstrationsphase, während die Elektrolyse mit Anionenaustauschmembranen (AEM) in der akademischen Forschung untersucht wird.
Die Effizienz und die Kapitalkosten dieser Technologien hängen vom Umfang ihrer Anwendung ab. Kommerzielle Systeme weisen im Hot-Standby Lastreaktionen im Sekundenbereich auf, was für eine effektive Kopplung mit intermittierendem erneuerbarem Strom notwendig ist. Allerdings ist nur die PEM-Elektrolyse in der Lage, im Kalt-Standby Rampenzeiten im Sekundenbereich zu erreichen.
Es besteht auch die Möglichkeit, elektrolysebasierten Wasserstoff mit aus Methan gewonnenem Wasserstoff zu kombinieren. Beispielsweise kann eine Hybridanlage mit einem Festoxid-Elektrolyseur und einem autothermen Reformer (ATR) von Vorteil sein, da der ATR gereinigten Sauerstoff benötigt.
Ein ATR funktioniert durch die teilweise Verbrennung von Methan mit gereinigtem Sauerstoff und eignet sich aufgrund der hohen Kosten der Sauerstoffreinigung, die nur im großen Maßstab wirtschaftlich ist, besonders gut für die Ammoniaksynthese im großen Maßstab.
In einem Festoxid-Elektrolyseur wird unabhängig davon gereinigter Sauerstoff erzeugt, wodurch die autotherme Reformierung in kleineren Maßstäben möglich ist. Es wird geschätzt, dass eine solche Konfiguration zu Einsparungen beim Erdgasverbrauch von bis zu 22 % führen kann.
2. Biomassebasierte Wasserstoffproduktion
Für die Ammoniaksynthese bietet die biomassebasierte Wasserstoffproduktion eine Alternative zu elektrolysebasierten Methoden. Allerdings stoßen typische Biomasseanlagen hinsichtlich Logistik und Biomasseversorgung auf Einschränkungen, was dazu führt, dass die Anlagenkapazitäten im Allgemeinen unter 50 MW liegen.
Die Kosten für Biomasse sind ein wichtiger Faktor bei der Bestimmung der Kosten für Wasserstoff, die je nach Art der Biomasse und ihrem Standort erheblich variieren können. Biomassebasierter Wasserstoff kann durch thermochemische oder biochemische Prozesse hergestellt werden.
Ein Vorteil der biomassebasierten Wasserstoffproduktion ist ihre Kompatibilität mit herkömmlichen Verfahren zur Herstellung von braunem Wasserstoff.
Die aus der thermochemischen oder biochemischen Verarbeitung von Biomasse gewonnenen Produkte dienen als Ausgangsmaterial für den Dampf-Methan-Reformierungsreaktor (SMR), der bei der Synthese von braunem Ammoniak verwendet wird. Ein Nachteil der biomassebasierten Wasserstoffproduktion ist jedoch die aufwändige Verarbeitung beim Umgang mit Biomasse.
Darüber hinaus ist das technische Potenzial von Biomasse zur Deckung des Wasserstoffbedarfs im Vergleich zu erneuerbaren Stromquellen wie Sonne, Gezeiten und Wind erheblich geringer, was hauptsächlich auf die begrenzte Verfügbarkeit von Biomasse zurückzuführen ist.
Zu den gängigen Biomassequellen gehören Bagasse, Feldfrüchte, Stroh, Rutenhirse, Holz und Hackschnitzel. Zu den typischen Produkten aus der Biomasseverarbeitung gehören Biogas, Bioöl und Pflanzenkohle. Auch Siedlungsabfälle können als alternativer Rohstoff für Biomasse dienen.
Ein Beispiel für einen Abfall-zu-Ammoniak-Prozess ist die Verwendung von recyceltem Kunststoff, wie in Japan für Zwecke der selektiven katalytischen Reduktion demonstriert.
Aus Biomasse gewonnenes Biogas kann mit erneuerbarem Strom kombiniert werden. Ein solches System ist der anaerobe Vergärungsprozess zur Biogasproduktion, gekoppelt mit elektrifizierten Rohrreaktoren zur Dampfreformierung. Eine weitere Alternative ist die Integration eines Biogasreaktors mit einem Festoxidelektrolyseur und einem ATR.
3. Stickstoffproduktion
Stickstoffgas, das aus Luft gereinigt wird, kann mithilfe verschiedener Technologien hergestellt werden: Luftzerlegungsanlage (ASU) durch kryogene Destillation, Druckwechseladsorption (PSA), Membranpermeation und Wasserstoffverbrennung.
Bei der Dampf-Methan-Reformierung (SMR) wird die Luftzerlegung typischerweise in die Wasserstoffproduktion integriert und der gewonnene Sauerstoff wird mit einem Teil des Wasserstoffs verbrannt. Ebenso kann die Wasserstoffverbrennung in einem Festoxid-Elektrolyseur genutzt werden, um die für die Wasserstoffproduktion aus Wasser erforderliche Wärme zu erzeugen.
Die verbleibenden drei Technologien (PSA, Membranpermeation und Wasserstoffverbrennung) können mit alkalischen oder PEM-Elektrolyseuren kombiniert werden, bei denen separate Einheiten zur Produktion von Stickstoff und Wasserstoff eingesetzt werden.
Die Wahl der bevorzugten Technologie hängt von der gewünschten Reinheit des Stickstoffs und dem Umfang der Anwendung ab. Sowohl PSA als auch Membranpermeation erfordern ein Deoxo-System zur Beseitigung von Restsauerstoff.
Um Sauerstoff zu entfernen, wird eine katalytische Verbrennung mit Wasserstoff durchgeführt, gefolgt von der Wasserentfernung mithilfe eines regenerativen Trockners. Die Entfernung von Sauerstoff ist vor Eintritt in den Synthesekreislauf von entscheidender Bedeutung, da Sauerstoffverbindungen den Ammoniaksynthesekatalysator negativ beeinflussen können.
4. Ammoniak-Synthesekreislauf
Was den Ammoniaksynthesekreislauf betrifft, so bleibt die Grundstruktur unabhängig von der Wasserstoff- und Stickstoffquelle unverändert, obwohl der Grad der Verunreinigung variieren kann. Die Wahl des Katalysators hat im Allgemeinen nur minimale Auswirkungen auf die Effizienz des Synthesekreislaufs.
Allerdings können die Betriebstemperaturen und -drücke je nach gewähltem Katalysator unterschiedlich sein. Dies ist insbesondere bei verkleinerten und intermittierenden Betrieben mit erneuerbaren Energiequellen relevant, da mildere Betriebsbedingungen bei geringerer Wärmeintegration Wärmeverluste minimieren können.
Darüber hinaus bringt die Produktion von grünem Wasserstoff unterschiedliche Wärme- und Massenströme in den Prozess ein, was unterschiedliche Wärmeintegrationsschemata erfordert. Häufig werden verschiedene Katalysatoren in einem einzigen Reaktor mit unterschiedlichen Betten kombiniert.
5. Ökonomische Aspekte der Produktion von grünem Ammoniak
Zum Vergleich: Eine Biogasanlage mit einer Kapazität von 22,5 tNH3/d (Tonnen Ammoniak pro Tag) hat Investitionskosten von ca. 14,4 Millionen Euro (M€). Im Gegensatz dazu hat eine SMR-basierte Anlage mit einer Kapazität von 1800 tNH3/d Investitionskosten von rund 199 Mio. €.
Die Betriebskosten eines elektrolysebasierten Haber-Bosch-Verfahrens lassen sich in Stromkosten und Eigentümerkosten unterteilen. Der Elektrolyseur in einem großtechnischen Haber-Bosch-Verfahren auf Elektrolysebasis ist typischerweise für 75–95 % des Stromverbrauchs verantwortlich.
Der Stromverbrauch und die Kosten hängen von der Größe und dem Standort der Anlage ab. Die Kosten für den Eigentümer einer 3 tNH3/d-Anlage belaufen sich auf ca. 120.000 Euro pro Jahr pro produzierter Tonne Ammoniak.
Die Wasserstoffproduktion ist der größte Kostenfaktor bei der Ammoniaksynthese. Je nach Standort können unterschiedliche Alternativen in Betracht gezogen werden. Durch SMR erzeugter brauner Wasserstoff hat eine Kostenspanne von 845–1585 €/t (ohne Kohlenstoffabscheidung und -speicherung [CCS]), während die Kosten mit CCS auf 1305–2145 €/t steigen.
Andererseits liegen die Kosten für erneuerbaren Wasserstoff, der durch Elektrolyse hergestellt wird, zwischen weniger als 1440 €/t und über 3605 €/t, abhängig von der kumulierten Sonnen- und Windlaststunde am jeweiligen Standort.
Elektrifizierte SMR wird attraktiv, wenn die Stromkosten unter 15–25 €/MWh liegen, abhängig von den Erdgaskosten am jeweiligen Standort. Elektrifizierte SMR bietet den Vorteil der Kompatibilität mit bestehenden SMR-Anlagen zur Wasserstoffproduktion und geringeren Kapitalinvestitionen im Vergleich zur Elektrolyse.
Biomassebasiertes Ammoniak, das durch thermochemische Verarbeitung hergestellt wird, kostet je nach Anwendungsumfang, Biomassequelle und Standort zwischen 380 €/t und 1875 €/t. Die Kosten für Ammoniak aus Siedlungsabfällen können bis zu 2135 €/t betragen.
Referenz
- Ammonia, 4. Green Ammonia Production, Ullmann’s Encyclopedia of Industrial Chemistry. – https://onlinelibrary.wiley.com/doi/10.1002/14356007.w02_w02