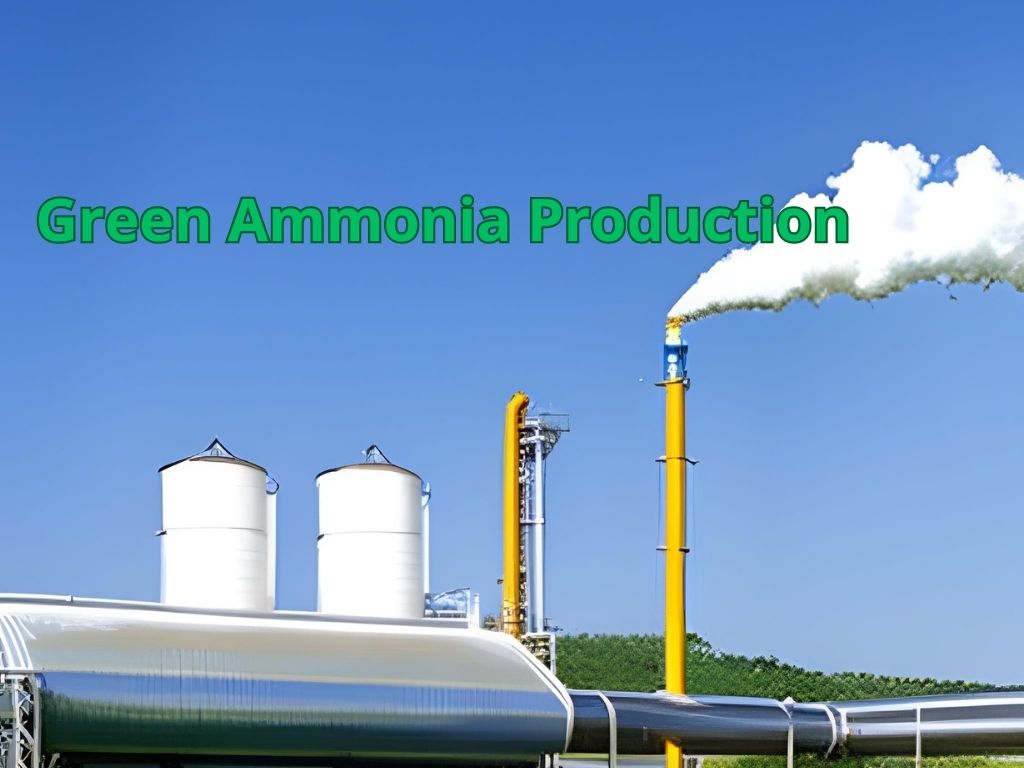
Green ammonia refers to ammonia that is produced without significantly contributing to carbon emissions. This can be achieved by employing traditional methods of ammonia synthesis coupled with electrolysis-based hydrogen generation, or by utilizing alternative techniques for ammonia synthesis.
Table of Contents
Prior to the widespread availability of inexpensive natural gas in the 1950s, electrolysis-based ammonia synthesis was widely adopted and only surpassed by coal gasification technology. Additionally, as an alternative approach to decentralized green ammonia synthesis, biomass-based hydrogen production integrated with carbon capture and storage (CCS) holds potential.
The initial implementation of the electrolysis-based Haber-Bosch process dates back to the 1920s, characterized by an energy consumption of approximately 46-48 gigajoules per metric ton of ammonia (GJ/tNH3).
Four key factors driving the production of green ammonia can be identified: the sustainability of raw materials involved, low energy consumption, the ability to scale production modularly, and economic viability.
Theoretical calculations indicate that the minimum amount of energy required for synthesizing ammonia from air and water is 22.5 GJ/tNH3.
1. Electrolysis-Based Hydrogen Production
Electrolysis is the primary method used to synthesize green hydrogen. Various commercially available electrolysis technologies can be integrated with ammonia synthesis, including alkaline electrolysis and proton-exchange membrane (PEM) electrolysis.
Solid oxide electrolysis (SOE) is currently in the demonstration stage, while anion-exchange membrane (AEM) electrolysis is being explored in academic research.
The efficiency and capital cost of these technologies depend on the scale of their application. Commercial systems exhibit load responses in the seconds range during hot standby, which is necessary for effective coupling with intermittent renewable electricity. However, only PEM electrolysis is capable of achieving ramping times in the range of seconds during cold standby.
There is also the possibility of combining electrolysis-based hydrogen with hydrogen derived from methane. For example, a hybrid plant that incorporates a solid oxide electrolyzer and an autothermal reformer (ATR) can be advantageous, as the ATR requires purified oxygen.
An ATR operates by partially combusting methane with purified oxygen and is particularly well-suited for large-scale ammonia synthesis due to the high cost of oxygen purification, which is economically viable only at large scales.
In a solid oxide electrolyzer, purified oxygen is produced regardless, making autothermal reforming feasible at smaller scales. It is estimated that such a configuration can lead to natural gas consumption savings of up to 22%.
2. Biomass-Based Hydrogen Production
For ammonia synthesis, biomass-based hydrogen production offers an alternative to electrolysis-based methods. However, typical biomass facilities face limitations in terms of logistics and biomass supply, resulting in plant capacities generally below 50 MW.
The cost of biomass is an important factor in determining the cost of hydrogen, which can vary significantly based on the type of biomass and its location. Biomass-based hydrogen can be produced through thermochemical or biochemical processes.
One advantage of biomass-based hydrogen production is its compatibility with conventional brown hydrogen production processes.
The outputs obtained from thermochemical or biochemical processing of biomass serve as the feedstock for the steam methane reforming (SMR) reactor used in brown ammonia synthesis. However, a drawback of biomass-based hydrogen production is the complex processing involved in handling biomass.
Additionally, the technical potential of biomass to meet hydrogen demand is considerably smaller compared to renewable electricity resources like solar, tidal, and wind, mainly due to limited biomass availability.
Common biomass sources include bagasse, crops, straw, switchgrass, wood, and wood chips. The typical products derived from biomass processing include biogas, bio-oil, and biochar. Municipal waste can also serve as an alternative feedstock for biomass.
An example of a waste-to-ammonia process is the utilization of recycled plastic, as demonstrated in Japan for selective catalytic reduction purposes.
Biogas derived from biomass can be combined with renewable electricity. One such system is the anaerobic digestion process for biogas production, coupled with electrified tubular steam reforming reactors. Another alternative is the integration of a biogas reactor with a solid oxide electrolyzer and an ATR.
3. Nitrogen Production
Nitrogen gas, which is purified from air, can be produced using several technologies: air separation unit (ASU) through cryogenic distillation, pressure-swing adsorption (PSA), membrane permeation, and hydrogen combustion.
In steam methane reforming (SMR), air separation is typically integrated with hydrogen production, and the oxygen obtained is combusted with a portion of the hydrogen. Similarly, hydrogen combustion can be utilized in a solid oxide electrolyzer to generate the heat necessary for hydrogen production from water.
The remaining three technologies (PSA, membrane permeation, and hydrogen combustion) can be combined with alkaline or PEM electrolyzers, where separate units are used to produce nitrogen and hydrogen.
The choice of the preferred technology depends on the desired purity of nitrogen and the scale of the application. Both PSA and membrane permeation require a deoxo system to eliminate residual oxygen.
To remove oxygen, catalytic combustion is performed with hydrogen, followed by water removal using a regenerative dryer. The removal of oxygen is crucial before entering the synthesis loop, as oxygen compounds can negatively impact the ammonia synthesis catalyst.
4. Ammonia Synthesis Loop
Regarding the ammonia synthesis loop, the fundamental structure remains unchanged regardless of the source of hydrogen and nitrogen, although impurity levels may vary. The choice of catalyst generally has minimal impact on the efficiency of the synthesis loop.
However, the operating temperatures and pressures may differ based on the chosen catalyst. This becomes particularly relevant in scaled-down and intermittent operations with renewable energy sources, as milder operating conditions can minimize heat losses when there is a reduced level of heat integration.
Furthermore, the production of green hydrogen introduces different heat and mass flows in the process, necessitating distinct heat integration schemes. Often, various catalysts are combined in a single reactor with different beds.
5. Economic Aspects of Green Ammonia Production
To provide a comparison, a biogas-based plant with a capacity of 22.5 tNH3/d (tons of ammonia per day) has an investment cost of approximately 14.4 million euros (M€). In contrast, an SMR-based plant with a capacity of 1800 tNH3/d has an investment cost of around 199 M€.
The operating costs of an electrolysis-based Haber-Bosch process can be divided into electricity costs and owner’s costs. The electrolyzer in a large-scale electrolysis-based Haber-Bosch process typically accounts for 75-95% of the electricity consumption. The electricity consumption and cost depend on the scale and location of the plant. The owner’s costs for a 3 tNH3/d plant are approximately 120,000 euros per year per ton of ammonia produced.
Hydrogen production is the major cost contributor in ammonia synthesis. Depending on the location, different alternatives can be considered. Brown hydrogen produced through SMR has a cost range of 845-1585 €/t (excluding carbon capture and storage [CCS]), while the cost increases to 1305-2145 €/t with CCS.
On the other hand, the cost of renewable hydrogen produced through electrolysis ranges from less than 1440 €/t to over 3605 €/t, depending on the cumulative solar and wind load hours at the specific location. Electrified SMR becomes attractive when the electricity cost is below 15-25 €/MWh, depending on the cost of natural gas at the given location. Electrified SMR offers the benefit of compatibility with existing SMR plants for hydrogen production and lower capital investment compared to electrolysis.
Biomass-based ammonia produced through thermochemical processing costs between 380 €/t and 1875 €/t, depending on the scale of application, biomass source, and location. The cost of ammonia derived from municipal waste can be as high as 2135 €/t.
Reference
- Ammonia, 4. Green Ammonia Production, Ullmann’s Encyclopedia of Industrial Chemistry. – https://onlinelibrary.wiley.com/doi/10.1002/14356007.w02_w02